Introduction: Understanding 5 Axis Machining
5-axis machining is an advanced manufacturing process that allows for more intricate, precise, and efficient production of parts. Unlike traditional 3-axis machining, 5-axis machining uses five different movements to create complex geometries with extreme precision. This technology plays a crucial role in industries like aerospace, automotive, medical devices, and more. With its ability to handle complex shapes and reduce production times, 5-axis machining provides a significant competitive edge for manufacturers. By optimizing production workflows and enhancing the quality of finished products, this process is becoming increasingly essential in modern manufacturing.
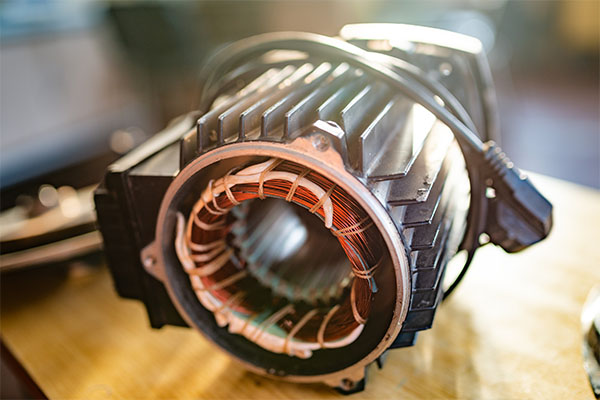
What Is 5 Axis Machining?
Explanation of 5 Axis Machining
5-axis machining is a computer-controlled process that utilizes five different axes to create precision parts. In simpler terms, the machine tool moves in five directions simultaneously, providing a level of accuracy and flexibility unmatched by traditional 3-axis machines. The first three axes refer to the standard X, Y, and Z axes that control horizontal and vertical movements. The remaining two axes allow rotation of the workpiece, enabling the machine to approach the material from multiple angles. This capability opens up new possibilities for creating intricate and complex geometries with fewer setups.
The Difference Between 3-axis, 4-axis, and 5-axis Machining
While 3-axis machining is suitable for simple, straightforward parts, 5-axis machining offers advanced capabilities for more complex tasks. A 3-axis machine moves only along the X, Y, and Z axes, while a 4-axis machine adds rotation on one axis, typically around the X-axis. The key advantage of 5-axis machining lies in the additional two axes of rotation, enabling the tool to access virtually every surface of the workpiece. This increased flexibility allows for faster production of highly detailed parts with greater precision.
How 5 Axis Machines Work
The operation of a 5-axis machine involves rotating the workpiece along two additional rotational axes while the cutting tool moves along the X, Y, and Z axes. This combination allows for continuous cutting without the need to reposition the material or tool manually, which significantly speeds up production. The movement of the cutting tool is controlled through advanced Computer Numerical Control (CNC) programming, ensuring optimal tool paths and precision throughout the process.
The Basics of CNC (Computer Numerical Control) Technology
What is CNC Technology?
CNC technology refers to the use of computers to control machine tools, such as mills, lathes, routers, and grinders, for precise manufacturing operations. CNC machines can operate automatically, guided by programmed instructions fed into the system. These machines provide higher precision, repeatability, and flexibility compared to manual operation, making them ideal for modern manufacturing.
CNC vs. Manual Machining
Unlike manual machining, where operators use physical tools to manipulate workpieces, CNC machining uses computer programs to guide the machine’s movements. This automation not only enhances accuracy but also speeds up the production process. CNC machines can perform multiple operations without human intervention, reducing the risk of human error and improving consistency. The transition from manual to CNC machining has revolutionized industries, offering faster lead times and more complex designs.
The Key Benefits of 5 Axis Machining
Improved Precision and Accuracy
One of the standout features of 5-axis machining is its ability to achieve exceptional levels of precision. The simultaneous movement along five axes allows for highly intricate parts to be manufactured with tight tolerances. This capability is particularly crucial in industries like aerospace and medical devices, where even the smallest error can result in costly defects or safety concerns. The precision offered by 5-axis machining minimizes human error and provides a higher level of repeatability in mass production.
Reduced Setup Time and Increased Efficiency
With traditional machining, each time a part requires a different angle of approach, the operator needs to manually reposition the workpiece. This results in multiple setup times and potential for errors. However, 5-axis machining eliminates the need for repositioning, as the machine can approach the workpiece from virtually any angle in a single setup. This reduction in setup time leads to faster turnaround times and increased overall efficiency. By minimizing human intervention and manual adjustments, manufacturers can achieve greater throughput and higher productivity.
Ability to Machine Complex Parts
5-axis machining excels at producing parts with complex geometries that are impossible or time-consuming to manufacture using traditional methods. For instance, turbine blades for jet engines or intricate mold designs for the automotive industry can be produced with fewer steps and greater precision. The additional two axes of movement allow for machining hard-to-reach areas without requiring the part to be repositioned or re-clamped, providing more flexibility in design and manufacturing.
Enhanced Surface Finish
Achieving a high-quality surface finish is crucial in many industries, particularly in aerospace, medical devices, and automotive parts. 5-axis machining is capable of delivering smoother surfaces compared to traditional methods because it allows for continuous cutting and finer adjustments. This results in parts with superior finishes, reducing the need for post-processing steps like polishing or grinding. The ability to access different angles also ensures a more consistent surface across the entire workpiece.
Applications of 5 Axis Machining in Different Industries
Aerospace Industry
In the aerospace industry, precision and reliability are paramount. 5-axis machining is frequently used to produce complex, lightweight parts for aircraft, such as engine components, wing structures, and turbine blades. The process allows manufacturers to create parts with intricate details and tight tolerances while keeping the weight to a minimum. The ability to machine parts from multiple angles reduces the need for extensive manual handling, increasing productivity and reducing the risk of errors.
Automotive Manufacturing
The automotive industry relies heavily on 5-axis machining for producing a wide range of parts, from engine components to suspension systems. The ability to handle complex geometries makes it ideal for creating parts with high-performance requirements. Manufacturers also use 5-axis machining for prototyping, enabling faster iteration of new designs and reducing lead times in bringing new products to market. Furthermore, the precision and repeatability of 5-axis machining ensure that parts are consistently manufactured to exact specifications.
Medical Industry
In the medical field, 5-axis machining is used to produce highly precise instruments, implants, and prosthetics. The ability to manufacture custom parts tailored to individual patients is a significant advantage, particularly in orthopedics and dental applications. 5-axis machines allow for the creation of complex shapes with intricate details, ensuring that medical devices meet stringent safety and quality standards. Additionally, the reduced production time and improved accuracy help manufacturers meet the growing demand for medical devices.
Energy Industry
The energy sector benefits from 5-axis machining in various ways, including the production of components for power plants, oil rigs, and renewable energy systems. Components such as gas turbine blades, compressor housings, and specialized machinery require high precision and durability. 5-axis machining allows manufacturers to create parts with the necessary strength and tolerance while optimizing material use. The versatility of 5-axis machining also supports the production of custom parts for energy solutions, including wind turbines and solar panels.
Consumer Goods
5-axis machining plays a role in manufacturing high-quality consumer goods that require precision and durability. Items such as watches, consumer electronics, and custom automotive parts often require complex machining that traditional methods can’t efficiently provide. The ability to create detailed, intricate components with a high degree of accuracy makes 5-axis machining an invaluable tool in producing these types of consumer products.
Key Advantages Over Traditional Machining Methods
Higher Accuracy and Tight Tolerances
5-axis machining significantly reduces the risk of human error compared to traditional methods. Because the process involves computer-controlled precision, parts are made to exact specifications with minimal variance. This higher accuracy is particularly important in industries where precision is critical, such as aerospace and medical devices. Manufacturers can achieve tight tolerances consistently, reducing the need for costly rework and enhancing overall product quality.
Fewer Operations for Complex Parts
Traditional machining often requires multiple operations to achieve the final shape, with each operation potentially involving repositioning and realigning the workpiece. In contrast, 5-axis machining allows for the completion of these operations in a single setup. This not only reduces the number of steps in the production process but also minimizes the risk of mistakes caused by manual adjustments. By consolidating operations, manufacturers can save both time and resources while improving consistency.
Greater Flexibility
5-axis machining provides greater flexibility for producing custom or complex parts. The ability to work from multiple angles allows designers to create parts with intricate details that would otherwise require additional tools or setups. This flexibility makes 5-axis machining ideal for industries that require custom or low-volume production runs, such as prototyping or high-performance manufacturing.
Ability to Machine Difficult Materials
5-axis machining can handle materials that are difficult to machine with traditional methods, including hardened steels, titanium, and composite materials. These materials often require specialized tools and cutting techniques, which are made easier by the advanced capabilities of 5-axis machines. The precision and efficiency of 5-axis machining ensure that manufacturers can produce high-quality parts from these challenging materials without compromising on performance or quality.
Challenges of 5 Axis Machining
Cost Considerations
While 5-axis machining offers numerous advantages, the initial investment in equipment and setup can be significant. High-end 5-axis machines can be expensive, and the costs associated with training personnel and maintaining the machines must also be considered. However, many manufacturers find that the long-term benefits, including increased efficiency, higher-quality parts, and reduced labor costs, outweigh the initial investment. Moreover, the ongoing advancements in technology are driving prices down, making 5-axis machining more accessible to a broader range of companies.
Skilled Workforce Requirement
Operating a 5-axis machine requires specialized knowledge and skills. Operators must be proficient in CNC programming and understand the intricacies of machine setup and operation. This need for skilled labor can be a barrier for companies that do not have the resources to train or hire qualified personnel. However, the demand for skilled CNC machinists is growing, and many training programs and resources are available to help workers acquire the necessary skills.
Complexity of Setup and Programming
Programming and setting up a 5-axis machine can be more complex than working with simpler machines. Designing the proper tool paths for intricate geometries requires specialized software and expertise. Additionally, ensuring that the machine is properly calibrated for each new job can take time and attention to detail. This complexity adds to the learning curve for operators and can make setup times longer compared to more straightforward machines.
Maintenance and Calibration
Regular maintenance and calibration are essential to ensure the machine operates at peak performance. Misalignments, worn tools, or debris in the system can compromise the quality of the finished part. Maintenance can be costly and time-consuming, but it is necessary to extend the life of the machine and ensure consistency in production. Additionally, calibration checks must be done regularly to maintain the accuracy of the machining process.
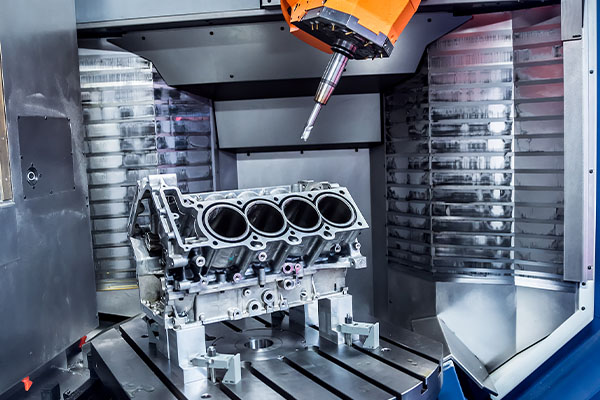
The Role of 5 Axis Machining in Prototyping
Rapid Prototyping Capabilities
5-axis machining is particularly advantageous in the field of prototyping. By reducing the need for multiple setups and allowing for the machining of complex geometries in a single operation, 5-axis machines accelerate the prototyping process. This capability is especially beneficial for industries like aerospace and automotive, where prototypes often undergo many iterations before the final design is approved. Manufacturers can quickly produce high-quality prototypes for testing and evaluation.
Precision in Prototyping
Prototypes often require high precision to ensure they meet design specifications. 5-axis machining excels at producing parts with tight tolerances and intricate features, making it an ideal choice for prototype production. The ability to handle complex designs with minimal human intervention ensures that prototypes are accurate and functional, reducing the need for expensive revisions.
Customization and Small Batch Production
For industries that require customized or small batch production, 5-axis machining offers the flexibility needed to create unique parts. The precision and speed of 5-axis machines make them ideal for low-volume runs, as they can produce a wide variety of designs without requiring additional tools or extensive setup changes. This capability is crucial for industries such as medical device manufacturing, where customized parts are often required for individual patients.
How to Choose the Right 5 Axis Machining Provider
Assessing Capabilities
When choosing a 5-axis machining provider, it’s important to assess their capabilities. Look for a provider with experience in machining the types of parts you need and who has access to the right equipment. Ideally, they should be able to demonstrate a track record of producing high-quality parts within your desired timelines.
Quality Assurance and Certifications
Quality assurance is key in any manufacturing process. Choose a 5-axis machining provider with certifications such as ISO 9001 or others relevant to your industry. These certifications indicate that the provider adheres to established quality standards and practices, ensuring that the parts produced will meet your specifications.
Cost vs. Quality Trade-off
While cost is always a consideration, it’s important to weigh it against quality. Opting for the cheapest provider may lead to compromises in quality, which can be more costly in the long run. Look for a provider who offers a balance between cost and quality, ensuring you get the best value for your investment.
Future Trends in 5 Axis Machining
Automation and Robotics
As automation continues to grow in manufacturing, 5-axis machining is poised to benefit from robotic integration. Robotic arms can assist with loading and unloading parts, improving overall efficiency. This automation will further reduce production times and increase precision, making 5-axis machining more cost-effective and accessible.
Integration with Additive Manufacturing
The future of 5-axis machining lies in its integration with additive manufacturing, such as 3D printing. Combining these technologies allows manufacturers to create even more complex parts with fewer steps and reduced material waste. Additive manufacturing will also allow for more customization, particularly in industries like healthcare and aerospace.
Machine Learning and AI in Machining
Artificial intelligence (AI) and machine learning are expected to revolutionize 5-axis machining by improving efficiency and predicting machine maintenance needs. AI can optimize cutting paths in real-time, ensuring that the machine is working at peak efficiency and minimizing material waste.
Material Innovation
5-axis machining will continue to evolve alongside material innovation. New materials, including advanced composites and alloys, will require more precise machining techniques. As new materials are developed, 5-axis machining will be critical in producing complex parts that meet the unique demands of these materials.
Case Studies: Successful Implementation of 5 Axis Machining
Case Study 1: Aerospace Industry Success
One example of 5-axis machining success is in the aerospace industry, where a leading company used this technology to manufacture complex turbine blades for jet engines. By utilizing 5-axis machining, the company was able to reduce production time and improve part accuracy, leading to better engine performance and fewer defects.
Case Study 2: Automotive Manufacturing Efficiency
An automotive manufacturer turned to 5-axis machining to streamline the production of engine components. By using fewer setups and reducing labor costs, the company significantly increased efficiency, allowing for faster production cycles and cost savings. The improved precision of the parts also led to better overall vehicle performance.
Case Study 3: Medical Devices Production
In the medical field, a manufacturer of custom implants implemented 5-axis machining to create highly detailed and precise parts. The technology allowed the company to produce customized implants with the exact specifications needed for each patient, ensuring better outcomes and reducing post-surgical complications.
Cost Breakdown of 5 Axis Machining
Initial Investment vs. Long-Term Savings
While the initial investment in 5-axis machinery can be substantial, it is important to consider the long-term savings it offers. With fewer setups required and faster production cycles, 5-axis machining can drastically reduce manufacturing costs over time. Furthermore, the precision it offers results in fewer defects and less waste, leading to additional savings.
Factors Affecting the Cost of 5 Axis Machining
The cost of 5-axis machining depends on several factors, including the complexity of the part, the material being used, and the machine time required. The more intricate the part, the longer it will take to machine, increasing the overall cost. Material choice also plays a role, with harder materials requiring specialized tools and processes that can raise costs.
How 5 Axis Machining Pays Off in the Long Run
Over time, the cost savings from faster production times, fewer mistakes, and higher-quality parts more than justify the initial investment in 5-axis machines. By improving efficiency and consistency, manufacturers can meet the growing demands of modern industries while maintaining competitive pricing.
Understanding the 5 Axis Machining Process
Step-by-Step Overview of a Typical Machining Process
The 5-axis machining process begins with the preparation of the material and the setup of the machine. Once the part is securely clamped into place, the cutting tool begins its journey along the five axes, following a pre-programmed tool path. The workpiece is rotated and moved simultaneously to achieve the desired shape, with real-time adjustments made to optimize the cutting process.
Programming the Machine
Programming the machine is a critical step in 5-axis machining. Using Computer-Aided Design (CAD) and Computer-Aided Manufacturing (CAM) software, engineers design the part and generate the necessary tool paths. These programs ensure that the cutting tool moves efficiently, avoiding unnecessary passes and optimizing material removal.
Post-Machining Process
Once the machining process is complete, the part undergoes finishing operations such as polishing or coating. These steps ensure that the part meets all required specifications for quality and performance. Quality checks are performed to confirm that the part adheres to the desired tolerances.
The Importance of Maintenance and Calibration in 5 Axis Machines
Routine Maintenance
Routine maintenance is essential for keeping 5-axis machines running smoothly. Regular inspections, cleaning, and lubrication help prevent wear and tear that can lead to costly downtime or poor-quality parts.
Calibration for Precision
Calibration ensures that the machine produces parts within the required tolerances. This process involves verifying that the machine’s axes are aligned and that the cutting tool is accurately positioned.
Troubleshooting Common Issues
Issues such as vibration, tool wear, or machine misalignment can negatively impact the machining process. Regular troubleshooting ensures that these issues are addressed promptly, minimizing the risk of defects and reducing the cost of repairs.
Conclusion: The Value of 5 Axis Machining in Modern Manufacturing
5-axis machining is an essential tool in the world of modern manufacturing. With its ability to produce complex parts with high precision, it has revolutionized industries ranging from aerospace to medical devices. While the initial investment can be significant, the long-term benefits, including reduced production times and improved quality, make it a valuable asset. As technology continues to evolve, the capabilities of 5-axis machining will only improve, making it an even more essential part of manufacturing processes in the future.
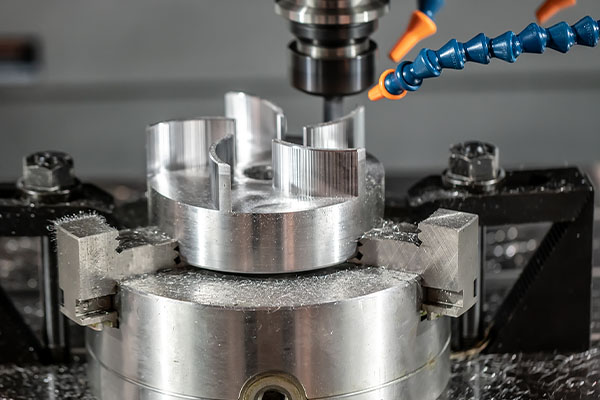
Frequently Asked Questions (FAQ)
How can I find the right 5-axis machining provider for my business?
To find the right 5-axis machining provider, assess their experience with the type of parts you need, their capabilities, and their track record in your industry. Look for providers with relevant certifications (like ISO 9001) and a commitment to quality assurance. Additionally, review their equipment to ensure they have up-to-date 5-axis machines capable of handling your specific requirements. Lastly, consider their customer service and communication, as strong partnerships are key for long-term success.
What makes 5-axis machining more accurate than 3-axis machining?
5-axis machining is more accurate than 3-axis machining because it allows the cutting tool to approach the workpiece from multiple angles simultaneously. This eliminates the need for multiple setups and reduces the chances of errors that can occur when repositioning the part. The continuous movement in five directions ensures greater precision, especially for complex parts with intricate features and tight tolerances.
How much does it cost to set up a 5-axis machining operation?
Setting up a 5-axis machining operation can be expensive, with costs primarily driven by the purchase of the machine itself, which can range from tens of thousands to several hundred thousand dollars. Additionally, there are costs related to software, training, and maintenance. However, the long-term benefits—such as increased production speed, higher precision, and reduced labor costs—can offset these initial expenses over time.
What materials can 5-axis machining handle?
5-axis machining can handle a wide range of materials, including metals such as aluminum, titanium, and stainless steel, as well as composite materials and plastics. This capability makes it ideal for industries such as aerospace, automotive, and medical device manufacturing, where hard and specialized materials are often required.
Is 5-axis machining suitable for small batch production?
Yes, 5-axis machining is particularly well-suited for small batch production. The flexibility and precision of 5-axis machines allow manufacturers to produce highly customized parts in low quantities. This is beneficial in industries like medical devices or aerospace, where specific parts need to be produced in limited runs or with individualized specifications.
Can 5-axis machining be used for prototyping?
Absolutely! 5-axis machining is highly effective for rapid prototyping. Its precision allows manufacturers to quickly create prototypes that closely resemble the final product, enabling more accurate testing and refinement. The reduced setup time and ability to handle complex geometries make 5-axis machines a popular choice for prototype production.
How does 5-axis machining improve surface finish quality?
The simultaneous movement along five axes allows the cutting tool to maintain a consistent angle and achieve a smoother finish, especially when working on complex shapes. This reduces the need for additional finishing processes such as polishing or grinding. The result is a high-quality surface finish directly from the machining process, improving part aesthetics and functionality.
What are the challenges of using 5-axis machines in manufacturing?
Some challenges of using 5-axis machines include the high initial investment, the complexity of machine programming, and the need for skilled operators. The machines themselves require regular maintenance and calibration to ensure consistent performance. Additionally, because of the high precision required, setup times can still be lengthy, especially for complex parts.