مقدمة
CNC machining has revolutionized the manufacturing industry, offering precision and efficiency across a wide range of applications. Among the various types of CNC machines, the 4-axis CNC machine stands out for its ability to create intricate and highly detailed parts with exceptional precision. But what exactly makes 4-axis CNC machining unique? By adding an extra axis of movement to the traditional three-axis setup, it allows for more complex geometries and fewer setup changes. In this article, we’ll explore the ins and outs of 4-axis CNC machining, how it works, its key benefits, and why it’s a crucial tool in modern manufacturing.
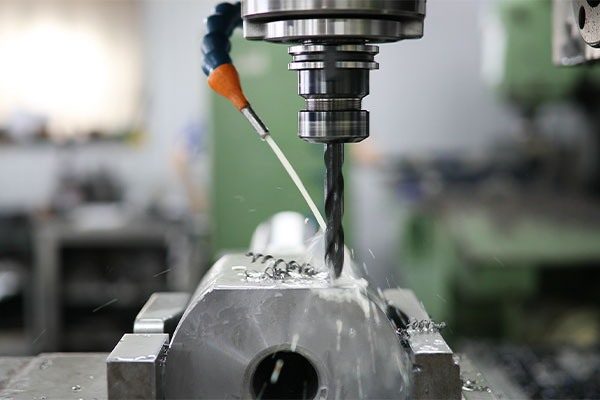
Understanding CNC Machining Basics
ما هي الآلات ذات التحكم الرقمي؟
CNC machining, or Computer Numerical Control machining, is a manufacturing process that uses computer-controlled machines to perform precise tasks like cutting, drilling, milling, and turning. The core idea behind CNC machining is the automation of tasks that would otherwise require manual labor, providing greater accuracy, speed, and repeatability.
CNC machines are equipped with motors and sensors that interpret a computer program to move the cutting tool along specified paths. These machines work by following predetermined designs to create products in various industries, from automotive to medical devices. The precision of CNC machining means that parts are made to exact specifications, ensuring consistency and reliability.
أنواع آلات CNC
There are several types of CNC machines, each designed for specific applications. The most common types include:
- مخرطات سي إن سي: Used for turning operations, these machines rotate a part while a cutting tool shapes it.
- ماكينات الطحن CNC: These machines use rotating cutters to remove material from a workpiece in various directions.
- أجهزة التوجيه CNC: Similar to milling machines but often used for cutting softer materials such as wood, plastics, and composites.
- CNC EDM (Electrical Discharge Machines): These use electrical discharges to remove material, particularly useful for hard metals.
Each of these machines operates under the same basic principles but differs in terms of their movements, tools, and material capabilities.
How 4 Axis CNC Machining Works
Basic Working Principle of 4 Axis CNC Machines
The main distinguishing feature of a 4-axis CNC machine is the addition of a fourth axis, which allows for more advanced operations. Unlike 3-axis machines, which operate along the X, Y, and Z axes, 4-axis CNC machines introduce the A-axis. The A-axis typically rotates around the X-axis, providing the machine with the ability to make complex cuts and shapes that are not possible with a standard 3-axis system.
This additional axis of rotation allows the machine to access different sides of a part without the need for multiple setups. It enhances the machine’s ability to create more intricate designs by allowing for continuous rotation during the cutting process.
The Role of Each Axis
- X, Y, and Z Axes: These are the basic three axes in CNC machining. The X and Y axes control the horizontal and vertical movements, while the Z axis controls depth.
- A-Axis (Rotating Axis): The A-axis enables the workpiece to rotate, allowing the cutting tool to approach the part from different angles. This is particularly useful for creating complex geometries that would otherwise require reorientation or multiple operations.
The integration of the A-axis significantly increases the versatility of CNC machines, enabling operators to perform more complex and detailed machining tasks in a single step.
How the A-axis Enhances Movement and Accuracy
The A-axis provides greater flexibility in machining by allowing parts to be rotated continuously. This means that parts can be machined on multiple faces without the need to remove them from the machine. It improves accuracy by eliminating the potential for misalignment during multiple setup changes, ensuring that the final product is consistent and precise.
The Difference Between 3-Axis and 4-Axis CNC Machining
Comparing the Movements: 3 Axis vs 4 Axis
A 3-axis CNC machine operates by moving the cutting tool along three linear axes: X, Y, and Z. This setup works well for simpler parts with flat surfaces. However, as parts become more complex, with features like holes on multiple sides or intricate angles, 3-axis machines start to fall short.
In contrast, a 4-axis CNC machine adds the A-axis, a rotational movement that allows for more flexibility. While the X, Y, and Z axes move the cutting tool across the workpiece, the A-axis rotates the part, enabling the tool to cut from different angles. This allows for greater complexity and precision in part production.
Why 4 Axis Provides More Flexibility
The addition of the A-axis enables 4-axis machines to perform multi-side machining in a single operation. This reduces the need for operators to manually adjust the part or reposition it between steps, saving time and improving accuracy. The ability to rotate the part also means that it can be worked on at different angles without the need for additional tools or manual labor.
When to Choose 3-Axis Over 4-Axis and Vice Versa
The choice between 3-axis and 4-axis CNC machining depends on the complexity of the part being produced. For simple parts with flat surfaces or basic geometries, a 3-axis machine is sufficient. However, for more intricate designs with multiple features or detailed angles, a 4-axis machine is necessary. When precision and efficiency are critical, investing in a 4-axis CNC machine offers the best results.
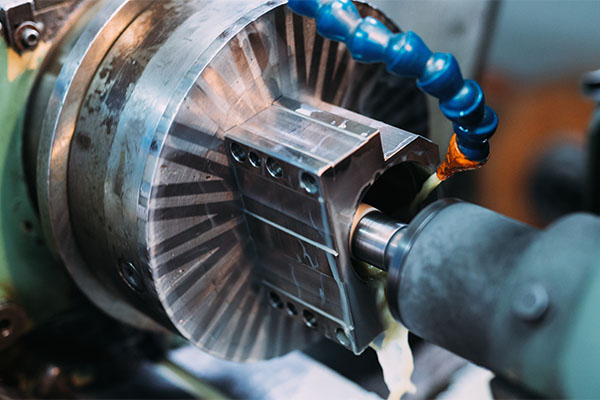
Key Benefits of 4 Axis CNC Machining
Enhanced Precision and Detail
One of the most significant advantages of 4-axis CNC machining is its ability to produce highly detailed parts with tight tolerances. The additional rotational axis allows the cutting tool to access areas that would otherwise be difficult or impossible to reach with a 3-axis machine. This ability to create precise angles and intricate shapes ensures that the final product meets exact specifications.
Improved Efficiency
4-axis CNC machines offer greater efficiency by reducing the number of setups required. In traditional machining, parts often need to be reoriented or repositioned to complete different stages of production. With the A-axis in 4-axis machining, parts can be rotated and worked on continuously, eliminating the need for multiple setup changes. This saves both time and labor costs, making the production process more streamlined and cost-effective.
Complex Shapes Made Easy
4-axis CNC machines excel at producing complex parts with multiple sides, such as those found in the aerospace or medical industries. These machines can create intricate shapes with high accuracy and minimal human intervention. This capability opens up new possibilities in design, enabling manufacturers to produce parts that would be difficult or even impossible to create with a 3-axis machine.
Increased Versatility
4-axis machines are highly versatile, able to work with a wide range of materials including metals, plastics, and composites. This makes them ideal for industries such as automotive, aerospace, and medical device manufacturing, where precision and material versatility are crucial. The ability to produce complex geometries on a variety of materials makes 4-axis CNC machining an invaluable tool for modern manufacturing.
What Industries Benefit Most from 4 Axis CNC Machining?
Aerospace and Aviation
The aerospace industry requires parts that meet the highest standards of precision and durability. 4-axis CNC machining allows for the production of complex components such as turbine blades, structural parts, and landing gear, all of which require precise machining from multiple angles. The ability to work on these parts in a single setup helps reduce production time and ensures that each component meets stringent quality standards.
Automotive Manufacturing
In automotive manufacturing, precision is critical for producing parts like engine components, transmission systems, and suspension elements. 4-axis CNC machines are particularly useful in this industry for creating complex, high-performance parts that must meet tight tolerances. The ability to machine multi-dimensional parts efficiently allows for better designs and faster production times.
تصنيع الأجهزة الطبية
The medical device industry requires parts that are both accurate and reliable. Components such as surgical instruments, implants, and prosthetics require a high level of detail and precision. 4-axis CNC machines are ideal for producing these parts, as they can handle complex shapes and ensure that each component is manufactured to exact specifications.
Tool and Die Making
4-axis CNC machining plays a vital role in tool and die making, where molds and dies must be created with extreme precision. The ability to rotate the workpiece allows for complex mold designs that can produce intricate parts used in mass production. The versatility of 4-axis machines also allows for the production of tools and dies with complex geometries that would be difficult to achieve with a 3-axis machine.
Types of 4 Axis CNC Machines
Vertical 4 Axis CNC Machines
Vertical 4-axis CNC machines are typically used for smaller to medium-sized parts. These machines are designed with the spindle on top and the workpiece held in a vertical position. They are ideal for parts that require precise machining along multiple sides but are not overly large. Vertical 4-axis machines are often found in industries such as automotive, aerospace, and electronics.
Horizontal 4 Axis CNC Machines
Horizontal 4-axis CNC machines feature a horizontal spindle, with the workpiece positioned horizontally on the machine. These machines are well-suited for larger and heavier parts, as they provide better stability and access to the workpiece. Horizontal 4-axis machines are commonly used in high-volume production and industries that require large, complex parts, such as aerospace and heavy machinery.
Specialized 4 Axis Machines
Some industries, such as medical device manufacturing and the production of complex molds, may require specialized 4-axis machines. These machines are designed to meet the specific needs of the industry, whether it’s for the creation of delicate medical components or highly detailed molds for industrial applications. These machines are often customized to suit the unique requirements of the parts being produced.
Applications of 4 Axis CNC Machining in Manufacturing
Complex Geometries and Parts
4-axis CNC machines are particularly valuable in the production of parts with complex geometries. For example, turbine blades, engine components, and molds often require precise machining on multiple surfaces. The ability to rotate the part during machining allows for a higher degree of accuracy and the creation of intricate designs that would be difficult to achieve with 3-axis machines.
Multi-Part Machining
One of the key advantages of 4-axis CNC machining is its ability to machine multiple parts simultaneously. This reduces setup time and increases throughput, which is especially beneficial in high-volume production. By using fixtures and multiple workpieces, manufacturers can efficiently produce large quantities of parts without compromising on quality.
High-Volume Production
For manufacturers producing large quantities of parts, 4-axis CNC machines offer significant advantages. The ability to perform complex machining operations in a single setup allows for faster production times, reducing cycle times and improving overall efficiency. This makes 4-axis machines ideal for industries such as automotive, aerospace, and medical device manufacturing, where high-volume production is common.
Improved Surface Finish
4-axis CNC machining also excels in creating parts with superior surface finishes. The ability to machine a part from multiple angles and remove material more evenly results in a smoother surface. This is particularly important in industries where the appearance and functionality of the part depend on its surface finish, such as in medical devices or high-performance automotive components.
Challenges in 4 Axis CNC Machining
Programming Complexity
One of the primary challenges of 4-axis CNC machining is the complexity of programming. The addition of the A-axis requires more advanced programming skills and expertise. Operators must be able to create programs that take full advantage of the machine’s capabilities, ensuring that the part is machined accurately and efficiently from all sides.
Machine Cost
4-axis CNC machines are generally more expensive than their 3-axis counterparts due to the added complexity of the design and functionality. This can make them a significant investment for manufacturers, especially smaller businesses. However, the increased efficiency and ability to handle more complex parts can justify the initial cost over time.
Part Size and Setup Considerations
While 4-axis CNC machines are capable of handling more complex parts, there are limitations in terms of size. Some machines may have size constraints that limit the types of parts that can be machined. Additionally, the setup process for 4-axis machining can be more time-consuming, particularly for larger parts or those that require multiple fixture changes.
Training and Skill Requirements
To maximize the potential of 4-axis CNC machines, operators must undergo extensive training. The complexity of the machines and the need for precise programming and setup mean that operators must have a higher level of expertise. Ensuring that staff are properly trained is essential for getting the most out of a 4-axis CNC machine.
How to Choose the Right 4 Axis CNC Machine for Your Business
Evaluating Business Needs and Production Requirements
When choosing a 4-axis CNC machine, it’s essential to evaluate your business’s needs and production requirements. Consider the types of parts you need to produce, the materials you work with, and the level of precision required. For example, if you’re working with heavy parts, a horizontal 4-axis machine may be the best option, while vertical machines may be better for smaller components.
Cost vs. Benefit
While 4-axis CNC machines come with a higher upfront cost, they can deliver long-term savings by reducing production times and minimizing the need for multiple setups. Consider the potential return on investment (ROI) when evaluating whether a 4-axis machine is right for your business. For high-volume production, the benefits of speed and efficiency can outweigh the initial cost.
Choosing Between Vertical and Horizontal 4 Axis Machines
The choice between vertical and horizontal 4-axis machines depends on the size and shape of the parts being produced. Vertical machines are typically better for smaller, lighter parts, while horizontal machines are ideal for larger, heavier components. Consider the types of materials you work with, the complexity of the parts, and the volume of production when making your decision.
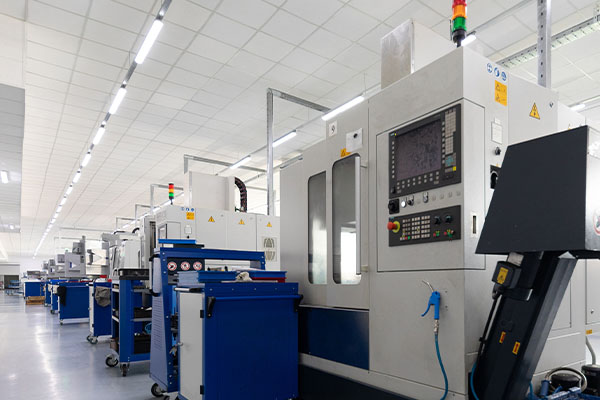
Common Materials Used in 4 Axis CNC Machining
Metals (Aluminum, Steel, Titanium, etc.)
Metals are some of the most common materials used in 4-axis CNC machining. The high precision and strength of metals like aluminum, steel, and titanium make them ideal for industries such as aerospace and automotive. These materials are often used for parts that require high durability and performance.
البلاستيك
Plastics are also widely used in 4-axis CNC machining, especially in industries such as electronics, medical devices, and consumer products. Plastics are versatile, lightweight, and can be machined with high precision, making them ideal for creating intricate components.
المركبات
4-axis CNC machining is well-suited for working with composite materials, which are often used in aerospace and automotive applications. Composites, such as carbon fiber and fiberglass, offer high strength-to-weight ratios and are ideal for parts that require durability without excess weight.
Wood
While 4-axis CNC machining is commonly associated with metals and plastics, it is also used in woodworking applications. CNC routers can precisely cut and shape wood, making them ideal for furniture, cabinetry, and architectural components. The ability to work with multiple surfaces in one setup improves efficiency in woodworking tasks.
Maintaining Your 4 Axis CNC Machine
Regular Inspection and Calibration
Maintaining your 4-axis CNC machine is essential for ensuring its continued performance. Regular inspections should be performed to check for any signs of wear or damage. Calibration is also important to maintain accuracy, as even minor misalignments can lead to defects in the parts being produced.
Lubrication and Cleaning
Proper lubrication and cleaning are critical for the smooth operation of a 4-axis CNC machine. Regularly lubricating the moving parts helps reduce friction and wear, while cleaning the machine ensures that no debris interferes with the machining process. Neglecting these tasks can lead to equipment failure and decreased performance.
Software Updates
Keeping your 4-axis CNC machine’s software up-to-date is also essential. Software updates often include improvements in functionality, efficiency, and compatibility with new tools and materials. Make sure your machine’s software is regularly updated to take full advantage of its capabilities.
How 4 Axis CNC Machining Enhances Quality Control
Precision and Consistency
The precision offered by 4-axis CNC machining ensures that parts are made to exact specifications. This consistency is particularly important in industries where even minor deviations can have significant consequences, such as medical device manufacturing or aerospace.
Reducing Human Error
By automating the machining process, 4-axis CNC machines reduce the potential for human error. Operators can program the machine to perform complex tasks with precision, eliminating mistakes that could occur during manual operations.
Real-time Monitoring and Adjustments
Many modern 4-axis CNC machines come with monitoring capabilities that allow operators to track the machining process in real-time. This enables quick adjustments if any issues arise, ensuring that the part is produced correctly and to the highest standards.
Future Trends in 4 Axis CNC Machining
Advancements in Technology
As CNC machining continues to evolve, new technologies such as artificial intelligence, machine learning, and the Internet of Things (IoT) are being integrated into 4-axis machines. These technologies improve the machine’s ability to make adjustments in real-time, enhancing precision and reducing downtime.
Integration with 3D Printing
Another exciting trend is the integration of CNC machining with 3D printing. This combination allows for faster prototyping and the ability to create complex parts using both subtractive and additive manufacturing methods. This hybrid approach is becoming increasingly popular in industries like aerospace, automotive, and medical devices.
Automation and Industry 4.0
The future of 4-axis CNC machining lies in automation. As part of Industry 4.0, machines are becoming more connected, allowing for greater data collection and analysis. This data can be used to optimize the machining process, improve quality control, and predict maintenance needs before they become problems.
Cost Considerations: Is 4 Axis CNC Machining Worth the Investment?
Initial Setup and Machine Costs
4-axis CNC machines come with a higher upfront cost compared to 3-axis machines. The added complexity of the A-axis and additional components increase the price. However, the benefits in terms of efficiency and precision can make the investment worthwhile for many manufacturers.
Long-Term Savings and ROI
The ability to produce complex parts with fewer setups and less manual labor results in long-term savings. By reducing production time and increasing output, manufacturers can see a significant return on investment. Over time, the savings in labor and setup costs outweigh the initial cost of the machine.
Financial Support Options
For businesses looking to invest in 4-axis CNC machining, there are several financing options available. These may include equipment leasing, loans, or government grants for innovation and technology adoption. Exploring these options can help offset the initial cost and make the investment more manageable for smaller manufacturers.
خاتمة
4-axis CNC machining offers unmatched precision, efficiency, and versatility, making it a vital tool for manufacturers across various industries. By adding an extra axis of movement, this technology enables the production of more complex and detailed parts, all while reducing setup times and improving accuracy. While the initial investment may be higher, the long-term savings and potential for innovation make it a worthwhile addition to any manufacturing process. For businesses looking to stay ahead in a competitive market, investing in 4-axis CNC machines is a step toward enhanced quality and productivity.
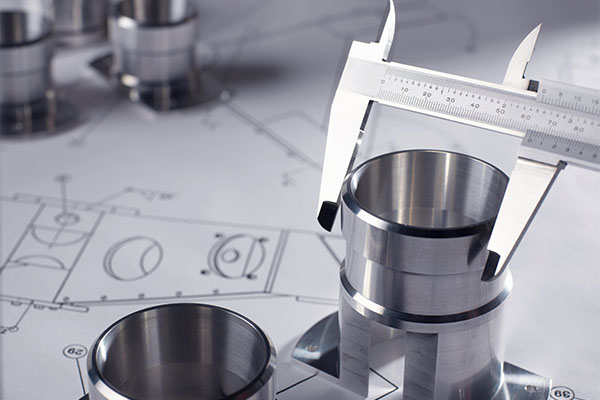
قسم الأسئلة الشائعة
What is the main difference between 3-axis and 4-axis CNC machining?
The main difference is that 4-axis CNC machining includes an additional rotational axis (the A-axis) which allows the machine to rotate the workpiece. This enables more complex shapes and multi-angle cutting without requiring additional setups.
Can 4-axis CNC machines be used for all materials?
Yes, 4-axis CNC machines can handle a wide variety of materials, including metals, plastics, composites, and wood. This makes them highly versatile and suitable for different industries.
How difficult is it to program a 4-axis CNC machine?
Programming a 4-axis CNC machine requires more expertise than a 3-axis machine due to the added complexity of the A-axis. However, with proper training and software, operators can efficiently program these machines for complex tasks.
What are some real-world applications of 4-axis CNC machining?
4-axis CNC machines are used in industries like aerospace, automotive, medical devices, and tool making. They are ideal for creating parts with complex geometries, such as turbine blades, engine components, and molds.
How can I reduce the cost of operating a 4-axis CNC machine?
To reduce operating costs, ensure that the machine is regularly maintained, keep programming and tool changes efficient, and utilize high-quality materials to avoid costly mistakes.