مقدمة
Medical CNC machining plays an essential role in the production of high-quality, precise components for the medical industry. Whether it’s creating intricate surgical instruments, customized prosthetics, or life-saving diagnostic equipment, precision is paramount. The medical industry relies on CNC machining for the consistent production of complex parts that adhere to the highest safety and regulatory standards. In this article, we will explore why CNC machining is integral to modern healthcare, the types of devices and materials used, and how manufacturers ensure the precision and reliability needed to improve patient outcomes. Keep reading to uncover the secrets behind this invaluable process.
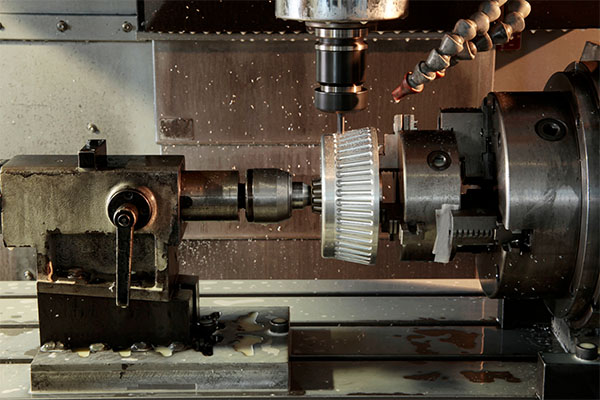
1. The Importance of CNC Machining in the Medical Industry
What Role Does CNC Machining Play in Healthcare?
CNC machining is a crucial technology in the medical field, ensuring that medical devices meet exacting standards. Precision is not just a nice-to-have; it’s a necessity in the medical world. A small deviation in measurements can lead to significant safety risks, making CNC machining essential for the creation of medical parts that require exact tolerances. Whether producing components for implants, diagnostic tools, or surgical instruments, the ability to work with incredibly tight tolerances ensures that these parts function as intended without fail. CNC machining’s ability to work with complex geometries and diverse materials also contributes to the development of innovative medical solutions.
Why CNC Machining is the Preferred Manufacturing Method
One of the reasons CNC machining is so prevalent in medical device manufacturing is its flexibility. CNC machines can create complex, high-precision parts from a wide range of materials, ensuring medical professionals get exactly what they need. Compared to other methods, such as injection molding or manual machining, CNC provides superior accuracy and repeatability. For example, the ability to make adjustments on the fly allows manufacturers to meet specific regulatory requirements, such as those set by the FDA and ISO standards, ensuring that medical devices are both safe and effective. The speed and reliability of CNC machining also make it ideal for fast-paced medical device production.
2. Key Advantages of CNC Machining for Medical Applications
Unmatched Precision
CNC machining offers unparalleled precision, which is a vital requirement in the medical industry. Each part must be manufactured to exact specifications, and CNC technology ensures that even the smallest details are accurate. Whether creating micro-sized surgical instruments or large prosthetic components, the machine’s precision remains consistent throughout the manufacturing process. This high level of accuracy is why CNC machining is the go-to method for producing medical parts that demand strict tolerances.
Customization and Flexibility
Another major advantage of CNC machining in the medical field is its flexibility in customization. The ability to create parts that fit specific patient needs or surgeon preferences is invaluable in medical applications. From custom implants to uniquely shaped surgical tools, CNC machining allows for rapid prototyping and design changes, enabling manufacturers to create one-of-a-kind solutions for individual patients. This adaptability also allows companies to produce limited runs of specialized devices or tools without sacrificing quality.
Consistency in Manufacturing
CNC machines excel in providing consistent results, even when producing large batches of medical components. Once a design is set, the machine can consistently produce parts that meet the same high-quality standards every time. This consistency is crucial for ensuring that each medical device performs reliably and safely. In a field where precision and uniformity are critical, CNC machining helps manufacturers maintain the highest quality standards.
Reduced Time-to-Market
CNC machining significantly reduces the time required to manufacture medical devices, which is essential in the competitive healthcare industry. Faster production times mean quicker time-to-market, which can lead to faster availability of critical devices for healthcare providers. This is especially important in emergency situations or when new medical technologies need to be rapidly developed and tested.
3. Types of CNC Machines Used in Medical Manufacturing
Vertical and Horizontal Milling Machines
Milling machines, both vertical and horizontal, are commonly used in the medical manufacturing process. Vertical milling machines are ideal for producing precise cuts on smaller parts, while horizontal mills are used for larger components that require a different cutting angle. These machines play a crucial role in shaping parts like orthopedic implants, surgical tools, and other medical devices. The flexibility of milling machines enables manufacturers to create complex designs with great accuracy, making them indispensable in the production of medical parts.
Lathes and Turning Centers
Lathes and turning centers are used to create round or cylindrical medical components, such as prosthetics, shafts, and surgical handles. CNC lathes use a rotating workpiece and a stationary cutting tool to shape components, ensuring that each part is turned to the desired specifications. Turning centers offer increased flexibility and automation, allowing for more intricate designs and improved efficiency. These machines are commonly used in the production of medical tools and implants that require high durability and precision.
EDM (Electrical Discharge Machining)
Electrical Discharge Machining (EDM) is often used in medical device production when parts require extremely intricate designs or tight tolerances. EDM uses electrical sparks to shape conductive materials, making it ideal for cutting small, delicate parts. This method is especially useful for producing complex surgical instruments or precision diagnostic tools that require a high degree of accuracy, such as catheters, medical electrodes, and other sensitive components.
3-Axis vs 5-Axis CNC Machines
The difference between 3-axis and 5-axis CNC machines lies in their ability to move the cutting tool. 3-axis machines work along the X, Y, and Z planes, while 5-axis machines offer additional rotational movement. The increased movement capabilities of 5-axis machines allow for more complex geometries and improved precision, making them the preferred choice for high-complexity medical parts. With the ability to machine on multiple planes at once, 5-axis CNC machines can reduce production time and enhance accuracy for detailed medical components.
4. Materials Commonly Used in Medical CNC Machining
Biocompatible Materials
In medical CNC machining, biocompatibility is a crucial factor. Medical parts, such as implants, surgical instruments, and prosthetics, must be made from materials that are not only durable but also safe for use in the human body. Materials like titanium, stainless steel, PEEK, and certain plastics are commonly used in CNC machining because they do not cause adverse reactions when implanted or used in medical procedures. Using biocompatible materials ensures that the parts are safe for long-term use and reduce the likelihood of complications.
How Material Choice Affects Precision
The material used in CNC machining has a direct impact on the precision of the final product. Harder materials, such as titanium, require more advanced cutting techniques and higher-powered machines. Conversely, softer materials are easier to shape but may not provide the same durability or strength. Choosing the right material for a specific medical part ensures that it meets both the performance and precision requirements of the application.
Durability and Sterilization Requirements
In addition to biocompatibility, medical components must be durable and easy to sterilize. The materials chosen for CNC machining must withstand repeated sterilization processes without degrading or losing functionality. For example, surgical instruments and implants must be able to endure autoclaving, a common sterilization method that uses high-pressure steam. Durability is essential for ensuring that the medical device can perform effectively throughout its lifespan, especially when exposed to harsh medical environments.
5. Medical Device Categories Manufactured Using CNC Machining
Orthopedic Implants
CNC machining plays a vital role in the production of orthopedic implants, which are used to replace or repair damaged bones and joints. Parts such as hip replacements, knee implants, and spinal fusion devices all require a high degree of precision to fit properly and function effectively. CNC machining ensures that these parts are created with the exact dimensions required for successful implantation. The customizability and flexibility of CNC machining also make it possible to produce patient-specific implants for a perfect fit.
Surgical Instruments
The precision of CNC machining is crucial in the production of surgical instruments, where even the smallest flaw can have significant consequences. From scalpels and forceps to more complex tools like surgical drills, CNC machines allow for the accurate shaping of high-performance surgical tools. These instruments must not only be precise but also durable and easy to sterilize, making CNC machining the ideal method for creating reliable surgical instruments that meet stringent regulatory standards.
Prosthetics
CNC machining is increasingly used in the production of custom prosthetics, allowing for highly individualized solutions for patients. Whether it’s a custom limb, dental implant, or hearing aid, CNC machining offers the flexibility to create prosthetics that are perfectly tailored to a patient’s body. Advanced technology allows manufacturers to create personalized devices with exact specifications, ensuring that the prosthetic fits and functions optimally.
Diagnostic Equipment
Medical diagnostic equipment, such as imaging machines, blood analyzers, and diagnostic probes, also relies on the precision of CNC machining. These devices require highly accurate parts that must function properly under stringent conditions. CNC machining ensures that the components used in diagnostic equipment are crafted with the highest degree of precision and reliability, which is critical for accurate diagnosis and patient care.
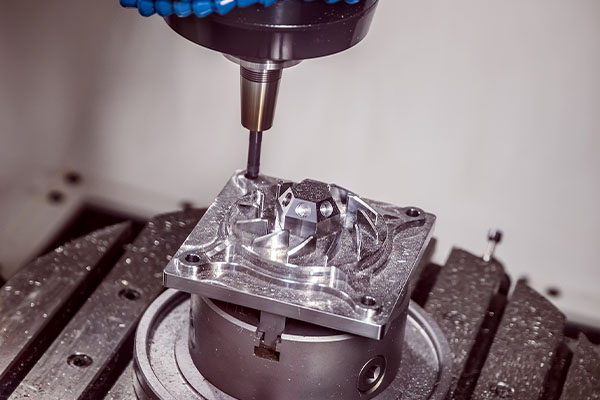
6. The CNC Machining Process in Medical Manufacturing
Step-by-Step Process of CNC Machining
CNC machining for medical devices follows a structured, methodical process that includes several key stages. The first step is the design phase, where engineers create the blueprint for the part using CAD software. Once the design is complete, it’s transferred to the CNC machine, which precisely cuts, shapes, and finishes the material based on the digital model. The final step involves quality control, where each part is inspected to ensure it meets the required tolerances and regulatory standards.
The Role of CAD/CAM in CNC Machining
Computer-Aided Design (CAD) and Computer-Aided Manufacturing (CAM) software are integral to the CNC machining process. CAD allows for the design of intricate parts, while CAM software converts these designs into machine instructions. This seamless integration of software and hardware enables manufacturers to create complex medical components with high precision and efficiency. By automating much of the process, CAD/CAM reduces human error and speeds up production.
Precision and Calibration in Every Step
Throughout the entire CNC machining process, precision is of the utmost importance. Calibration ensures that the CNC machine is set to the correct specifications before production begins. The machine’s cutting tools are also calibrated to maintain accuracy, and every step of the process is carefully monitored to ensure the part meets the required standards. Precision is maintained at each stage, ensuring that the final product will perform as intended in the medical setting.
7. Regulatory Standards and Compliance for Medical CNC Machining
لوائح إدارة الغذاء والدواء
In the medical industry, regulatory compliance is a critical aspect of CNC machining. The FDA (Food and Drug Administration) oversees the manufacturing of medical devices to ensure they are safe and effective for patient use. CNC machining companies must adhere to FDA regulations regarding the design, manufacturing, and testing of medical devices, including meeting specific requirements for material use, sterilization, and biocompatibility.
ISO Certifications
ISO 13485 is a global standard for quality management systems in the medical device industry. CNC machining companies that hold ISO certification demonstrate their commitment to producing high-quality, reliable products. This certification ensures that manufacturers follow stringent processes to meet the needs of the healthcare sector. Compliance with ISO standards provides an extra layer of assurance that the medical devices produced are safe, reliable, and of the highest quality.
CE Marking
In Europe, CE marking is required for medical devices sold within the European Economic Area. This mark indicates that the device meets all the necessary safety and performance requirements as defined by EU regulations. CNC machining companies that produce medical devices for the European market must ensure their products meet CE standards, which cover everything from material safety to performance testing.
Other Industry-Specific Compliance Requirements
In addition to FDA regulations, ISO certifications, and CE marking, there are other compliance requirements for medical device manufacturing. These include adherence to local regulations, as well as industry-specific standards that apply to different types of medical devices, such as dental implants or diagnostic equipment. Manufacturers must stay up to date on these requirements to ensure their products are market-ready and safe for patient use.
8. Challenges in Medical CNC Machining
Complexity of Medical Parts
Medical device designs often involve highly complex geometries, which can pose challenges for CNC machining. Parts must meet precise specifications while also fitting together perfectly within a larger assembly. The complexity of these designs means that CNC machines must be capable of handling intricate cuts and small tolerances, often requiring the latest technologies and highly skilled operators.
Achieving Consistency Across Batches
Another challenge in medical CNC machining is maintaining consistency across production batches. Even slight variations in parts can lead to performance issues or safety concerns. Manufacturers must invest in quality control systems and advanced CNC machines to ensure that every part, regardless of when it’s produced, meets the same high standards.
Cost and Time Constraints
While CNC machining offers numerous benefits, it also comes with challenges related to cost and time. The high cost of CNC machinery, along with the time required for setup and calibration, can be a concern for manufacturers. However, the benefits of precision and consistency often outweigh these costs, particularly in the medical industry where quality is paramount.
Maintaining Compliance in Production
The need to adhere to strict regulatory requirements also presents challenges for CNC machinists. Medical device manufacturers must continually monitor their processes to ensure compliance with regulations such as the FDA and ISO standards. This requires ongoing training, investment in new technologies, and rigorous testing, all of which can be time-consuming and costly.
9. The Future of Medical CNC Machining
Advancements in CNC Technology
As CNC machining technology continues to evolve, the medical industry stands to benefit from new innovations. Advancements such as multi-axis machines, laser machining, and improved automation are enabling manufacturers to create even more precise and complex medical devices. These innovations are reducing production times and improving the overall quality of medical components, making CNC machining even more integral to healthcare manufacturing.
3D Printing and CNC Hybrid Systems
One of the most exciting developments in medical CNC machining is the rise of hybrid systems that combine CNC machining with 3D printing technologies. These hybrid systems allow for the rapid production of both solid and complex geometries, offering manufacturers the flexibility to create custom medical components more efficiently. This integration could revolutionize the production of medical implants, prosthetics, and other highly specialized devices.
Personalized Medicine and Customization
Personalized medicine is a growing trend in healthcare, and CNC machining is playing a significant role in making customized medical solutions a reality. With CNC technology, manufacturers can create bespoke devices tailored to individual patients’ needs, improving outcomes and patient satisfaction. From custom implants to personalized surgical tools, CNC machining’s flexibility and precision are essential for supporting the personalized medicine movement.
10. The Cost of CNC Machining in the Medical Industry
Factors That Affect the Cost
The cost of CNC machining in the medical industry can vary depending on several factors. These include the material used, the complexity of the design, the quantity of parts being produced, and the machine setup time. Materials such as titanium or specialized plastics often come with higher costs, while simple components made from less expensive materials may be more affordable. The more complex the part, the higher the cost of machining, as additional time and precision are required.
How CNC Machining is Cost-Effective in Long-Term Manufacturing
Despite the initial high costs, CNC machining proves to be cost-effective in the long run. With its ability to produce large quantities of highly accurate parts with minimal waste, CNC machining allows manufacturers to keep costs down over time. Additionally, CNC machines can work around the clock, reducing labor costs and increasing production speed.
Price vs Quality in Medical CNC Machining
In the medical industry, quality should always take precedence over price. While CNC machining may seem expensive compared to other manufacturing methods, it provides superior precision and reliability, which are essential for the safety of medical devices. Cutting corners in CNC machining can result in faulty parts, which could compromise patient health. Thus, investing in high-quality CNC machining ensures that medical devices meet all safety and regulatory standards.
11. Quality Control in Medical CNC Machining
Inspection Methods
Quality control is critical in medical CNC machining. Parts are subjected to rigorous inspection methods, such as visual inspection, laser scanning, and coordinate measuring machines (CMM), to ensure they meet strict tolerance requirements. These inspections are crucial for verifying that each component will function as intended and that it adheres to all safety regulations.
Tolerances and Their Importance
In the medical industry, tolerances are incredibly tight, and even the smallest deviation can result in product failure. CNC machines must be capable of working within extremely precise tolerances, often measured in microns, to ensure the accuracy and reliability of medical devices. This level of precision is required not only for functional purposes but also to ensure patient safety.
Maintaining Quality Across Production Runs
Maintaining consistent quality across all production runs is a challenge for many industries, but CNC machining excels in this regard. By using the same programs and settings across each batch, CNC machines ensure that every part is identical. This consistency is crucial in the medical industry, where each device must meet the same high standards every time.
Advanced Technologies for Quality Assurance
Advancements in quality assurance technologies are helping manufacturers maintain the highest standards in CNC machining. New systems, such as automated in-line inspection tools and robotic arms, are reducing human error and increasing accuracy. These innovations are improving the efficiency and effectiveness of quality control, ensuring that medical devices continue to meet the required standards.
12. The Role of CNC Machining in Medical Innovation
Enabling New Medical Devices
CNC machining is not just a tool for manufacturing; it’s a driving force behind medical innovation. From the creation of cutting-edge implants to the development of life-saving diagnostic tools, CNC machining enables manufacturers to push the boundaries of what’s possible in healthcare. As medical technology continues to evolve, the precision and adaptability of CNC machining ensure that manufacturers can meet the growing demands of the industry. This capability to innovate is vital for bringing new medical devices to market that improve patient outcomes and enhance healthcare practices.
Rapid Prototyping for Medical Devices
One of the most valuable aspects of CNC machining in medical innovation is its ability to rapidly prototype new devices. In the past, prototyping medical devices was a slow and costly process, but CNC machining speeds up this stage significantly. Manufacturers can quickly create and test prototypes, make adjustments, and then move forward with production. This reduces development time and allows for faster testing and iteration, which is crucial in a field where speed can mean the difference between life and death.
Improving Surgical Techniques with Precise Tools
The precision of CNC machining also plays a pivotal role in improving surgical techniques. From surgical tools to robotic systems, the ability to create exact replicas and enhancements allows surgeons to operate with higher accuracy. The manufacturing of these precise tools helps doctors perform procedures with greater confidence and efficiency, leading to better patient outcomes. By providing the tools needed for advanced medical practices, CNC machining is an essential part of medical progress.
13. The Importance of Trust in Medical CNC Machining
Choosing a Trusted CNC Machining Partner
Choosing the right CNC machining partner is essential for any medical device manufacturer. It’s critical to select a company that has the expertise, experience, and certifications to handle the stringent requirements of the medical industry. A trusted machining partner will have a strong track record of delivering high-quality, compliant parts. Working with an experienced provider ensures that your devices will be manufactured correctly, meet safety standards, and function as intended.
Why Quality and Precision Matter
In the medical industry, quality and precision are non-negotiable. Even minor deviations in a medical device can lead to catastrophic failures. Trusting a reputable CNC machining company ensures that the devices you rely on for healthcare will meet the highest standards of precision and reliability. Manufacturers who prioritize quality and invest in the best technology and talent are the ones that you can count on for your medical components.
Building Long-Term Relationships with Manufacturers
Long-term relationships with trusted CNC machining partners bring numerous benefits. Ongoing collaboration ensures that manufacturers are always aligned with the evolving needs of the medical industry. A long-term relationship also fosters better communication and a deeper understanding of the requirements for each project. By building these relationships, manufacturers can better anticipate challenges and provide timely solutions that meet both design and regulatory standards.
14. FAQs: Everything You Need to Know About Medical CNC Machining
What is the Difference Between Medical and Non-Medical CNC Machining?
The key difference between medical and non-medical CNC machining is the level of precision and the regulatory requirements. Medical devices require extremely tight tolerances and must adhere to strict safety standards, such as those set by the FDA and ISO. Non-medical parts may not require such high levels of precision or regulatory oversight, making CNC machining in the medical field a more specialized process.
How Long Does It Take to Manufacture Medical Parts via CNC Machining?
The time it takes to manufacture medical parts via CNC machining depends on the complexity of the part and the material used. For simple components, the process can take just a few hours, while complex parts may take several days to complete. Prototyping is usually faster than full production, but both stages benefit from the speed and precision of CNC machining.
What Certifications Should a Medical CNC Machining Company Have?
A reliable medical CNC machining company should hold certifications such as ISO 13485 and FDA compliance. These certifications ensure that the company follows strict guidelines for quality control and regulatory compliance. Companies that work with medical devices must also be able to meet other relevant standards, such as CE marking for the European market.
Is CNC Machining the Best Option for All Medical Devices?
CNC machining is an excellent choice for many types of medical devices, but it may not always be the best option. For some high-volume production needs, injection molding or casting might be more cost-effective. However, for devices requiring high precision, complex geometries, or custom designs, CNC machining is the ideal choice. Each medical device should be evaluated based on its specific requirements to determine the best manufacturing method.
How Do You Ensure the Parts Are Biocompatible?
Biocompatibility testing is essential for any medical device that will come into contact with the human body. Manufacturers ensure biocompatibility by selecting the right materials, such as titanium, stainless steel, or medical-grade plastics, which are known to be safe for implantation. Materials are also tested for compatibility with the human immune system to ensure there are no adverse reactions during use.
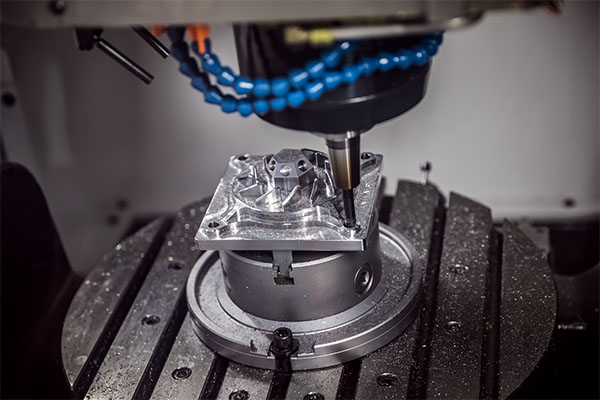
15. الخاتمة
In conclusion, CNC machining has become an indispensable part of the medical device manufacturing process. From producing precise surgical tools to crafting custom implants, the versatility and accuracy of CNC machining are critical in developing high-quality medical devices that improve patient outcomes. As technology continues to evolve, CNC machining will play an even more significant role in driving medical innovation and enhancing the quality of healthcare. By partnering with trusted manufacturers and ensuring rigorous quality control, the medical industry can continue to rely on CNC machining for safe and effective healthcare solutions. For any manufacturer or healthcare provider, investing in CNC machining ensures that the devices and instruments used in medical settings are reliable, effective, and safe for patients.