Introduction: What is CNC Injection Molding?
CNC injection molding is a precise and efficient method used to manufacture parts and components in various industries, from automotive to electronics. If you’re new to this technology, it can be a bit overwhelming, but don’t worry. In this beginner’s guide, we will walk you through the entire CNC injection molding process, explain the technology behind it, and show you why it’s essential in today’s manufacturing landscape. Whether you’re a business owner, engineer, or hobbyist, this article will provide you with a clear understanding of how CNC injection molding works and why it matters.
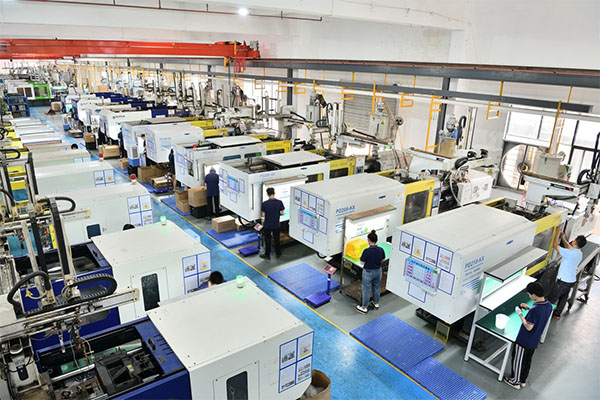
Understanding the Basics: What is Injection Molding?
Injection molding is a popular manufacturing process that allows for the production of complex and high-precision parts. The process involves injecting molten material, such as plastic, into a mold cavity where it solidifies into the desired shape. This method is widely used due to its ability to create large quantities of parts with high consistency and minimal waste.
The Injection Molding Process Explained
The process begins with the selection of the material, typically plastic pellets or granules. These materials are then heated until they melt and become liquid. The molten material is injected into the mold under high pressure, filling every cavity of the mold. Once the mold is filled, the material is cooled and solidified, and the finished part is ejected from the mold. The high precision of injection molding allows for the creation of complex shapes that would be difficult or impossible to achieve with other methods.
Applications of Injection Molding
Injection molding is used in various industries, including automotive, consumer products, medical devices, and electronics. It’s ideal for producing parts such as housings, gears, buttons, and more. This method is especially valuable for large-scale production runs, where efficiency and consistency are critical.
Key Components of an Injection Molding Machine
An injection molding machine consists of several key components, including the injection unit, mold, and clamping unit. The injection unit is responsible for heating and injecting the material, while the clamping unit holds the mold in place during the injection process. The mold itself is designed to form the part, and its design plays a crucial role in the final product’s quality and precision.
What is CNC (Computer Numerical Control)?
CNC (Computer Numerical Control) is a technology that uses computers to control machine tools. CNC machines can automate and precisely control the movement of tools during manufacturing processes, including machining, cutting, drilling, and molding. CNC systems replace manual controls with computerized programs, enabling higher precision and efficiency.
The Role of CNC in Injection Molding
In CNC injection molding, the CNC system is integrated into the mold and machine setup to enhance precision. It controls the movements of the machine, ensuring that the mold is positioned with extreme accuracy during the injection process. The result is more complex designs, faster production cycles, and fewer defects compared to traditional molding methods.
How CNC Injection Molding Works: Step-by-Step Process
CNC injection molding combines the principles of both CNC machining and injection molding. The process begins with the preparation of the material, which is typically a plastic pellet. These pellets are heated and melted into a liquid state before being injected into the mold cavity. The CNC machine controls the mold positioning, ensuring high accuracy and preventing defects. Once the mold is filled, the material is allowed to cool and harden before being ejected from the mold. The precision provided by CNC systems ensures that every part is produced with consistent quality.
Step 1: Preparing the Material
The material used in CNC injection molding typically starts in the form of small pellets or granules. These materials are chosen for their ability to melt and flow easily into the mold. Common materials include various types of plastics, such as ABS, polypropylene, and polystyrene. The material is fed into the hopper of the machine, where it is then heated to its melting point. This step is critical, as the material must reach the correct viscosity for proper molding.
Step 2: Heating and Melting the Material
Once the material enters the injection molding machine, it is heated in a barrel to reach its molten state. The heating elements inside the barrel ensure that the material reaches the appropriate temperature. The melted material is then forced into the injection chamber, where it is stored until it’s ready to be injected into the mold cavity. The temperature control in this step is vital to ensure the material flows properly and fills the mold correctly.
Step 3: Injecting the Molten Material into the Mold
Once the material has been melted and is under the correct pressure, the injection molding machine uses a screw or plunger to inject the molten material into the mold cavity. The mold is precisely positioned using the CNC system, ensuring that the molten material fills the cavity without any gaps or misalignment. The pressure at which the material is injected is carefully controlled to ensure optimal results and prevent defects.
Step 4: Cooling and Solidifying the Material
After the mold is filled, the material begins to cool and solidify. The cooling process is essential to ensure that the material hardens into the desired shape. During this stage, the mold is kept at a controlled temperature to allow the material to set properly. The cooling time can vary depending on the material used and the size and complexity of the part being molded.
Step 5: Ejecting the Final Product
Once the material has solidified, the mold is opened, and the finished product is ejected. The CNC system ensures that the mold opens and closes with precision, preventing any damage to the part. The part is then removed from the mold and inspected for quality. At this stage, any necessary post-processing, such as trimming or polishing, can be performed.
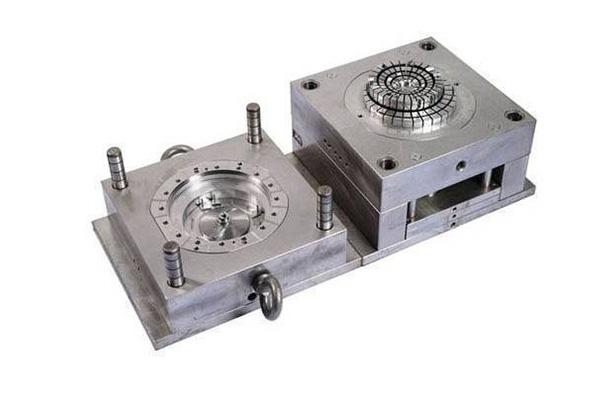
The Role of CNC in the Injection Molding Process
CNC technology plays a crucial role in the injection molding process by ensuring precise control over the mold’s movement and positioning. With CNC, manufacturers can achieve tighter tolerances and more complex designs that would be difficult to accomplish with traditional molding techniques. The CNC system allows for automated adjustments during production, which reduces the need for manual intervention and improves consistency.
How CNC Enhances Precision and Control
One of the main advantages of using CNC in injection molding is its ability to control mold positioning with high precision. This ensures that the mold cavities are filled evenly and that the parts produced meet exact specifications. CNC machines can also perform multiple tasks simultaneously, such as adjusting the temperature, pressure, and speed during the injection process, further enhancing the overall quality of the product.
Achieving Higher Precision and Complexity with CNC Injection Molding
CNC injection molding enables manufacturers to create parts with intricate designs and high precision. It also allows for tighter tolerances, which is especially important in industries like aerospace and medical device manufacturing, where even the slightest variation in size or shape can lead to product failure.
Customization and Precision in CNC Injection Molding
One of the main advantages of CNC injection molding is the ability to customize the process to meet specific requirements. Whether you need a part with unique features, such as undercuts or complex geometries, or require high-precision tolerances, CNC technology allows for precise adjustments to ensure your product meets all the necessary specifications.
Types of Injection Molding Machines
There are several types of injection molding machines, each designed for different types of parts and materials. The two most common types are horizontal and vertical injection molding machines. Horizontal machines are the most widely used, with the mold opening and closing in a horizontal direction. Vertical machines, on the other hand, use a vertical mold and are typically used for more specialized applications.
Horizontal Injection Molding Machines
Horizontal injection molding machines are the most common type and are used for a wide range of products. These machines are ideal for large-scale production runs, as they can inject large amounts of material at high speeds. The mold opens and closes in a horizontal direction, which allows for easy removal of the finished parts.
Vertical Injection Molding Machines
Vertical injection molding machines are less common but are used for specialized applications. These machines are ideal for producing small, intricate parts, as the vertical orientation allows for more precise molding. Vertical machines are also used for insert molding, where components such as metal inserts are placed into the mold before the injection process begins.
CNC Technology’s Adaptation in Different Machine Types
The integration of CNC technology into both horizontal and vertical machines has enhanced their precision and versatility. CNC systems ensure that the mold is positioned correctly, which is essential for producing high-quality parts. CNC systems also allow for adjustments during the injection process, ensuring that the material flows properly and that the part is created with the desired features.
CNC Injection Molding Materials: What Can Be Molded?
CNC injection molding can be used with a wide variety of materials, each chosen based on the specific needs of the product. The most common materials used are plastics, but metals, ceramics, and rubber can also be molded using CNC technology.
Common Materials Used in CNC Injection Molding
Some of the most popular materials used in CNC injection molding include thermoplastics like ABS, polycarbonate, and polypropylene. These materials are chosen for their ability to melt and flow easily, allowing for a smooth molding process. Other materials, such as metal alloys and elastomers, are used for parts that require additional strength, flexibility, or heat resistance.
Choosing the Right Material for Your Project
Selecting the right material is crucial to the success of your project. Factors such as the part’s intended use, environmental conditions, and desired mechanical properties will influence your material choice. For example, ABS is often used for automotive parts due to its strength and impact resistance, while polycarbonate is used for electronic housings because of its transparency and durability.
Pros and Cons of Different Materials
Each material used in CNC injection molding has its pros and cons. Plastics are versatile and cost-effective, but they may not be suitable for high-stress applications. Metals and ceramics, on the other hand, provide greater strength and durability but are more expensive and may require specialized equipment.
Material Properties and Their Impact on the Final Product
The material used in CNC injection molding has a direct impact on the final product’s strength, appearance, and functionality. Understanding the properties of different materials, such as tensile strength, heat resistance, and flexibility, is essential to ensuring that your product performs as expected. For example, choosing the wrong material for a high-temperature application could lead to failure, while using an overly rigid material for a flexible part could cause it to crack or break.
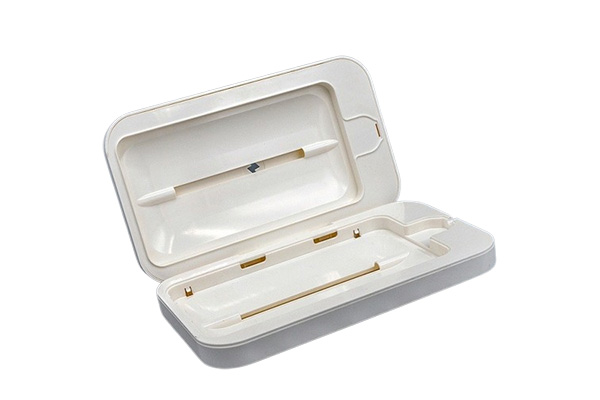
Mold Design for CNC Injection Molding
The design of the mold is one of the most critical factors in the success of the injection molding process. CNC technology allows for precise mold design and adjustment, ensuring that every part is produced to the correct specifications. The design of the mold affects factors such as cooling time, material flow, and part ejection, all of which impact the quality of the final product.
Key Considerations in Mold Design
Some key considerations in mold design include proper gating (the entry points where material flows into the mold), venting (allowing air to escape as the mold fills), and cooling channels (which help to cool the material during the solidification process). A well-designed mold will result in fewer defects, faster production times, and a higher-quality finished product.
Role of CNC in Mold Precision and Consistency
CNC machines play a crucial role in mold design by ensuring that the mold is manufactured with the highest level of precision. CNC machines can produce molds with extremely tight tolerances, which is essential for creating parts that fit together perfectly. This precision also helps to reduce defects such as sink marks and warping.
Examples of Successful Mold Designs
Successful mold designs vary depending on the application, but they all share a focus on precision and efficiency. For example, in the automotive industry, molds are often designed with complex geometries to create parts that fit perfectly within the vehicle’s assembly. Similarly, in the medical device industry, molds must be designed with precision to ensure that parts meet strict regulatory standards.
CNC Injection Molding vs Traditional Molding: What’s the Difference?
While both traditional and CNC injection molding involve injecting material into a mold, there are key differences between the two methods. Traditional injection molding relies on manual adjustments and control, which can lead to inconsistencies and longer production times. CNC injection molding, on the other hand, uses automated controls to ensure higher precision, faster production, and fewer defects.
Key Distinctions Between CNC and Traditional Methods
One of the key distinctions between CNC and traditional injection molding is the level of control that CNC provides. With CNC, the entire molding process can be monitored and adjusted in real-time, allowing for greater precision and faster cycle times. Traditional molding often involves more manual intervention, which can lead to slower production and higher error rates.
Benefits of CNC Over Conventional Molding
The main benefits of CNC injection molding include greater precision, faster production speeds, and fewer defects. CNC systems can make real-time adjustments to factors like temperature, pressure, and mold positioning, which improves overall efficiency. Additionally, CNC molding allows for more complex designs and tighter tolerances than traditional methods.
When to Use CNC vs Traditional Methods
CNC injection molding is ideal for projects that require high precision, complex designs, or short production runs. Traditional molding may still be more cost-effective for large-scale production runs where precision is less critical. The decision to use CNC or traditional molding will depend on factors such as the complexity of the part, the materials used, and the desired production speed.
Advantages of CNC Injection Molding for Manufacturers
CNC injection molding offers numerous advantages over traditional molding methods, making it a popular choice for manufacturers across various industries. The primary benefits of CNC molding include increased precision, higher production efficiency, and reduced waste. CNC systems also enable manufacturers to create more complex and customized parts, which can be particularly valuable in industries like automotive, medical, and electronics.
Increased Precision and Consistency
CNC injection molding allows for more consistent and accurate results, even for complex and intricate parts. The high precision of CNC technology ensures that each part meets the required specifications, reducing the need for post-processing and minimizing defects. This precision is especially valuable in industries where even small variations in size or shape can lead to product failure.
Speed and Efficiency Benefits
CNC technology also increases production speeds by automating key aspects of the molding process. With CNC, manufacturers can optimize cycle times, reduce material waste, and improve overall throughput. These improvements lead to faster time-to-market and reduced costs, making CNC molding a more efficient option for many manufacturers.
Cost-Effectiveness in Large-Scale Production
While CNC injection molding may have higher upfront costs due to the need for specialized equipment and tooling, it is often more cost-effective in the long run. The improved precision and efficiency of CNC systems lead to fewer defects, less waste, and faster production speeds, all of which contribute to lower overall costs for manufacturers.
Customization and Flexibility in Designs
CNC technology offers unparalleled customization and flexibility, allowing manufacturers to produce parts with complex geometries and unique features. Whether you’re designing a part with undercuts, intricate patterns, or tight tolerances, CNC injection molding can meet your specific design requirements with ease.
Reduced Waste and Material Savings
One of the key benefits of CNC injection molding is its ability to minimize material waste. CNC systems can be programmed to optimize the flow of material, reducing excess and ensuring that only the required amount is used. This not only saves on material costs but also makes CNC molding a more sustainable option for manufacturers.
Minimizing Human Error in the Manufacturing Process
CNC systems eliminate much of the manual labor involved in the molding process, reducing the risk of human error. This leads to more consistent results and less downtime due to mistakes. Automated adjustments made by CNC machines further contribute to the reduction of defects and inconsistencies in the final product.
Applications of CNC Injection Molding
CNC injection molding is used in a wide range of industries, thanks to its versatility and precision. Industries such as automotive, medical devices, electronics, and consumer products rely heavily on CNC molding to produce high-quality, complex parts. Whether you need durable automotive components or precise medical equipment, CNC injection molding can meet your needs with accuracy and efficiency.
Industries That Benefit Most from CNC Injection Molding
Industries that require high precision and complex parts, such as aerospace, medical devices, and electronics, are particularly well-suited for CNC injection molding. CNC technology allows manufacturers in these industries to produce parts that meet stringent quality standards and regulatory requirements.
Examples of Real-World Products Made Using CNC Injection Molding
Some examples of products made using CNC injection molding include automotive components like dashboards and interior parts, medical devices such as surgical instruments and implants, and electronic housings for consumer gadgets like smartphones and computers.
How CNC Molding Meets Industry Standards and Requirements
CNC injection molding is highly beneficial in industries where quality and precision are paramount. The ability to create complex geometries, tight tolerances, and high-quality finishes ensures that CNC molding meets the exacting standards of industries such as medical and aerospace.
Challenges and Limitations of CNC Injection Molding
While CNC injection molding offers many advantages, it is not without its challenges and limitations. One of the biggest hurdles is the high initial investment in CNC equipment and tooling, which can be cost-prohibitive for small businesses or startups. Additionally, the complexity of mold design may require specialized expertise, and ensuring consistent material quality is essential for achieving optimal results.
High Initial Investment Costs
The cost of CNC injection molding equipment can be substantial, especially for businesses just starting out. However, these costs are often recouped over time due to the improved efficiency, accuracy, and production speeds that CNC systems provide.
Mold Wear and Maintenance Issues
Molds used in CNC injection molding are subject to wear over time, which can affect the quality of the final product. Regular maintenance and inspections are required to ensure that molds are functioning optimally. CNC technology helps by providing precise monitoring of mold conditions, reducing the likelihood of wear-related issues.
Material Limitations and Processing Constraints
Some materials may not be suitable for CNC injection molding due to their specific properties or processing requirements. For example, some high-performance materials may require specialized equipment or more time-consuming processing steps. Understanding the limitations of your chosen material is crucial to achieving successful results.
Design Challenges Requiring Advanced Skills
The complexity of mold designs in CNC injection molding often requires advanced skills and experience. Designing molds with intricate features such as undercuts or tight tolerances can be challenging, and errors in the design phase can lead to significant production delays or defects in the final product.
Troubleshooting Common Problems in CNC Injection Molding
Common issues in CNC injection molding include material flow problems, air bubbles, sink marks, and flash. Troubleshooting these problems involves examining the mold design, adjusting machine settings, and making refinements to the process. CNC technology allows for real-time adjustments, making it easier to identify and address issues before they lead to defects.
Common CNC Injection Molding Problems and How to Solve Them
Defects in Molded Parts
Defects in CNC injection molding can range from minor cosmetic issues to major functional problems. Common defects include warping, sink marks, and inconsistent material flow. These issues can be mitigated by optimizing mold design, ensuring consistent material quality, and adjusting machine settings such as temperature and pressure.
Solutions for Improving Mold Design
Improving mold design can help solve many of the common problems faced in CNC injection molding. For example, adding proper venting to the mold can help prevent air pockets and improve material flow. Additionally, optimizing cooling channels and ensuring uniform thickness across the mold can reduce the likelihood of defects.
The Role of CNC in Troubleshooting and Precision Correction
CNC systems play a critical role in troubleshooting by providing real-time data on the molding process. Adjustments can be made to machine settings, mold positioning, and material flow to resolve issues before they affect the final product. This level of control ensures that production is efficient and that defects are minimized.
The Future of CNC Injection Molding: Trends and Innovations
The future of CNC injection molding looks bright, with continuous advancements in technology and techniques. One of the most exciting developments is the integration of automation and artificial intelligence (AI) into the molding process. AI-powered systems can analyze production data in real-time, optimizing the injection molding process and further reducing defects.
Emerging Technologies in CNC Molding
Emerging technologies, such as 3D printing integration, are opening up new possibilities for CNC injection molding. These technologies allow for faster prototyping and more complex designs, enabling manufacturers to create parts that were previously impossible or cost-prohibitive to produce.
How CNC Injection Molding is Evolving in Materials and Techniques
Advancements in material science are also driving the evolution of CNC injection molding. New materials with enhanced properties, such as higher strength and better heat resistance, are being developed and integrated into the process. These materials open up new opportunities for CNC molding in industries like aerospace and automotive.
Predictions for the Future of CNC Precision Manufacturing
As CNC technology continues to improve, we can expect even greater precision and efficiency in injection molding. The integration of smart systems, automation, and AI will further reduce production times and costs while improving the consistency and quality of molded parts.
Conclusion: Why CNC Injection Molding is Essential for Modern Manufacturing
CNC injection molding plays an essential role in modern manufacturing, offering precision, efficiency, and versatility across a range of industries. The ability to create complex, high-quality parts with minimal waste has made it a valuable tool for manufacturers worldwide. Whether you’re producing automotive components, medical devices, or consumer products, CNC injection molding offers the precision and customization needed to meet today’s manufacturing demands.

قسم الأسئلة الشائعة
- What types of products are best suited for CNC injection molding?
CNC injection molding is ideal for creating parts with intricate designs and high precision, such as automotive components, medical devices, and consumer electronics.
- How do I know which material to choose for my CNC injection molded product?
The material choice depends on factors such as the part’s intended use, environmental conditions, and required mechanical properties. Common materials include plastics like ABS and polycarbonate.
- Can CNC injection molding be used for prototyping?
Yes, CNC injection molding can be used for prototyping, offering high precision and the ability to create complex designs quickly.
- What are the typical costs involved in CNC injection molding?
While initial investment costs can be high, CNC injection molding is cost-effective for large-scale production due to its precision, speed, and ability to reduce waste.
- How do CNC machines enhance the speed of the injection molding process?
CNC systems allow for real-time adjustments to machine settings, improving the speed and efficiency of the injection molding process.
- What are some of the most recent advancements in CNC injection molding technology?
Recent advancements include the integration of AI and automation, which optimize the molding process and reduce defects. Additionally, new materials with enhanced properties are being developed for use in CNC injection molding.