مقدمة
تصنيع النحاس is a common practice across various industries, from manufacturing intricate components to producing durable parts. Whether you’re a seasoned professional or a newcomer to the world of machining, achieving high-quality results when working with brass requires a deep understanding of the material and the right techniques. This article explores the basics of machining brass, the tools required, common challenges, and how to improve your precision, along with expert tips for high-quality results. By the end, you’ll have a solid understanding of how to get the most out of your brass machining processes.
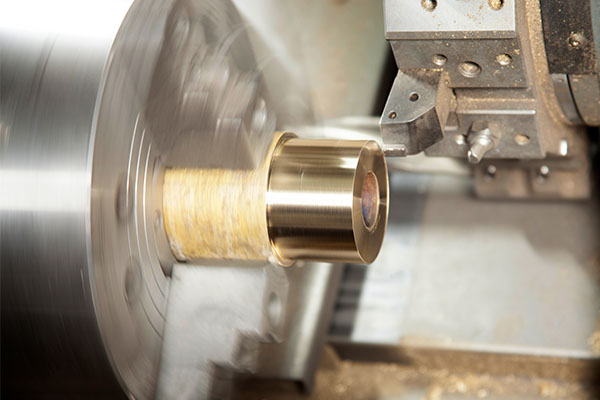
1. What Are the Basics of Machining Brass?
Brass is a versatile and widely used material in machining due to its ease of workability, corrosion resistance, and attractive appearance. It’s used in a range of applications, from creating fittings and valves to electrical connectors. But here’s the kicker—brass is an alloy of copper and zinc, and the ratio of these metals can significantly impact the material’s machinability.
Brass is soft, which makes it easy to machine, but it also comes with challenges, particularly when it comes to maintaining clean cuts and preventing material buildup. The material can work-harden quickly, which means that the machining process can generate excessive heat if not controlled properly. In turn, this heat can cause problems like tool wear, deformation, or distortion of the part. To prevent these issues, it’s essential to know the right machining techniques.
The ideal cutting tool for brass is one made of carbide, as it holds up better against heat and wear. Cutting speeds should be moderate to avoid excessive heat buildup. And, cutting fluid is an absolute must—it not only lubricates the tools but also helps cool the material.
2. What Tools and Equipment Are Used for Machining Brass?
Machining brass requires specific tools and equipment to achieve the best results. Ready for the good part? Understanding which tools and machinery work best with brass will elevate your precision and overall results.
A CNC lathe and milling machine are commonly used when machining brass, as these tools can precisely cut, drill, and shape the material. Additionally, specialized cutting tools such as carbide inserts, end mills, and drills are essential for efficient brass machining. Carbide tools are particularly useful because they provide longevity and can withstand the heat generated by cutting brass.
What’s the real story? The choice of tool material makes a significant difference when it comes to machining brass. While high-speed steel (HSS) is a popular option for many metals, carbide is preferred for brass due to its heat resistance and ability to maintain sharp edges.
Tool coatings are also worth mentioning. Some coatings, like TiN (Titanium Nitride) or TiAlN (Titanium Aluminum Nitride), help reduce friction and extend tool life by preventing material buildup on the cutting edge. A solid choice in tool coatings can significantly improve the speed and quality of brass machining operations.
3. What Are the Common Challenges When Machining Brass?
Despite its ease of machining, brass does come with its share of challenges. This is where it gets interesting—brass can present problems like work hardening, chip buildup, and poor surface finish if the right techniques aren’t followed.
Work hardening happens when the material becomes harder as it is worked, which makes further machining more difficult. This can lead to tool wear, excessive heat generation, and poor surface quality. A good practice to avoid work hardening is to ensure the cutting tool remains sharp and the cutting speed is adjusted appropriately to minimize heat buildup.
Chip buildup is another common challenge when machining brass. Brass chips can easily clog up the tool and machining area, making the process less efficient. To avoid this, manufacturers often use chip breakers, which are tools that help break the chips into smaller, manageable pieces that won’t block the cutting path.
Surface finish is often a concern, especially in industries where appearance matters. Improper tool selection, cutting speeds, or feed rates can result in a rough surface that needs additional finishing work. To tackle this, manufacturers usually implement finishing processes such as polishing or grinding, which smooth out any imperfections and give the part the desired aesthetic.
4. How Do You Choose the Right Brass Alloy for Machining?
Choosing the right brass alloy is crucial for getting the desired results in machining. But wait, it’s not always straightforward! Brass alloys come in various compositions, each with its own properties, making it essential to understand what each type of brass is best suited for.
The most commonly used brass alloys in machining are 200 series and 300 series. The 200 series, often referred to as red brass, is known for its strength and corrosion resistance. It’s used in applications like plumbing fittings and electrical connectors. The 300 series is commonly used for applications that require higher corrosion resistance, like marine environments.
What’s the real story here? When selecting the right alloy, consider the application and desired mechanical properties. If the part requires high strength or the ability to withstand high temperatures, a higher zinc content (as found in 360 brass) might be necessary. For decorative or corrosion-resistant applications, a lower zinc content might be ideal.
Each alloy has different machining characteristics. For instance, alloys with higher zinc content are softer and easier to machine, while those with less zinc may require different techniques due to their harder nature. The key is to match the alloy with both your machining capabilities and the end-use of the part.
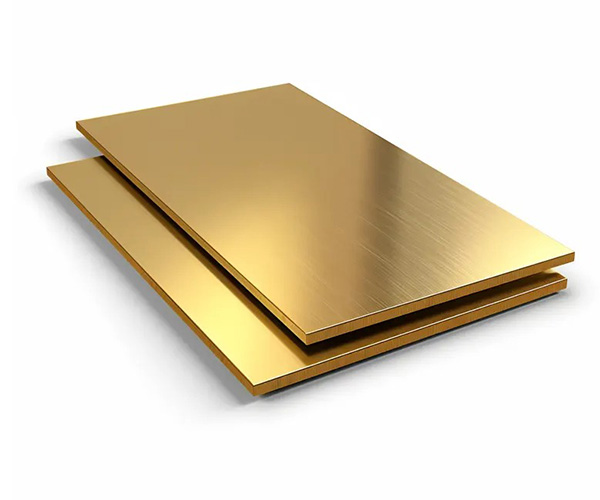
5. How Can You Improve Precision in Brass Machining?
Achieving precision is the name of the game when machining brass, and there are several ways to enhance the accuracy of your machining operations. Ready for the good part? Precision in machining brass requires both proper setup and careful operation.
The first step is ensuring that your CNC machine is well-calibrated. A misaligned machine can lead to inaccuracies and wasted material, so regular calibration checks are essential. Additionally, using high-precision equipment like fine-cutting tools and digital measuring instruments can help achieve tighter tolerances.
What’s the secret to improving precision? The right cutting tool setup plays a pivotal role. Choosing the right tool for the specific brass alloy you’re working with and setting it at the correct angle will enhance the overall precision of the cut. Additionally, minimizing vibration during the machining process is key. Vibration can lead to inconsistencies in the surface finish and lead to higher tool wear, affecting precision.
Maintaining the right feed rate and cutting speed is also vital. Too fast, and the part will become overheated and lose its dimensional accuracy; too slow, and you risk underperforming the cutting tool. Find the sweet spot between speed and efficiency, and you’ll be rewarded with highly precise brass parts.
6. What Speeds and Feeds Are Best for Machining Brass?
Speeds and feeds are critical components in brass machining, and getting them right can make or break your process. Here’s where it gets interesting—adjusting the cutting speed and feed rate is essential for maintaining tool life and achieving a smooth finish.
The ideal cutting speed for brass typically ranges between 100 and 200 surface feet per minute (SFM), depending on the specific alloy and the type of operation. For example, for softer brass alloys, higher cutting speeds can be used, whereas harder alloys require slower speeds to avoid excessive heat buildup.
Feed rate is equally important. The goal is to ensure that the cutting tool moves through the brass at a speed that prevents it from overheating while maintaining a consistent cut. A feed rate of around 0.002 to 0.005 inches per revolution (IPR) is standard for brass machining, but it may need to be adjusted based on the specific application and machine capabilities.
What’s the kicker here? Adjusting the speed and feed rate based on real-time observations during machining is critical. Factors such as temperature, tool wear, and material buildup can all affect the ideal settings. Keep an eye on these elements, and you’ll have better control over the machining process and achieve the best results.
7. How Do You Prevent Brass from Overheating During Machining?
Overheating is a significant concern when machining brass, but here’s the kicker—by using the right methods, it’s entirely avoidable. Preventing overheating is essential for maintaining material integrity and ensuring that your tools last longer.
The first step to controlling heat is using cutting fluids. These fluids not only lubricate the cutting tool but also help dissipate the heat generated during machining. There are two main types of cutting fluids: water-based coolants and oil-based coolants. Water-based coolants are more effective in reducing heat, while oil-based coolants are better at providing lubrication and extending tool life.
What’s the real story? Another important factor is the cutting tool material. Carbide tools are excellent for brass machining because they are highly heat resistant. Additionally, controlling the cutting speed and feed rate, as well as using a tool with the right geometry, can minimize heat generation. In extreme cases, using an air blast to cool the workpiece can help reduce heat buildup during high-speed machining.
8. What Are the Best Practices for Surface Finishing Brass?
Surface finishing is crucial when machining brass, especially when aesthetics are important. Ready for the good part? Achieving a perfect finish on brass parts requires a combination of the right tools, techniques, and post-machining processes.
The first step is choosing the right cutting tool. For brass, using a high-quality carbide tool with a sharp edge is essential to achieving a smooth surface. As you machine the part, you may need to use multiple cutting tools to achieve a consistent surface finish.
What’s the real secret to finishing brass? After machining, polishing or grinding is often required to achieve a high-quality finish. Using a polishing wheel or abrasive belt can help remove any tool marks or rough spots left by the cutting process. Additionally, ultrasonic cleaning or sandblasting may be necessary for removing surface imperfections.
The right finishing process will ensure that your brass parts not only perform well but also look appealing, which is critical in industries like electronics, jewelry, and decorative items.
9. How Do You Manage Brass Chip Removal Effectively?
Chip removal plays a crucial role in brass machining, but here’s where it gets interesting—if not handled properly, chips can quickly become a serious problem. Brass chips are relatively soft, but their shape can easily clog the cutting area, leading to inefficient machining.
To prevent chip buildup, manufacturers often use chip breakers, which are specially designed tools that break large chips into smaller, more manageable pieces. These smaller chips can be easily removed by either manual methods or automated systems such as chip conveyors.
What’s the kicker here? Using a chip conveyor is an efficient way to manage brass chips, especially in high-volume machining operations. These conveyors collect chips and funnel them into a bin, making it easier to maintain a clean working environment. By keeping the work area free from chips, you can ensure that your machining process runs smoothly without interruption.
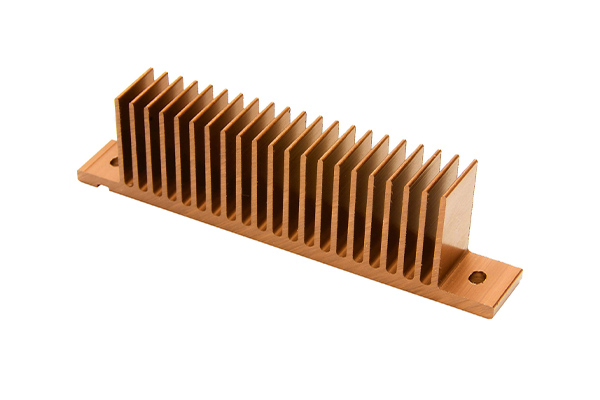
10. How Can You Achieve Consistency in Brass Machining?
Achieving consistency in brass machining is essential for ensuring that every part meets the required specifications. What’s the real story? There are several key factors that contribute to consistent brass machining, including regular equipment maintenance, machine calibration, and proper tool selection.
Regular calibration of your machines will help reduce the chances of dimensional inaccuracies. Additionally, routine maintenance ensures that your equipment is in top condition, preventing any sudden breakdowns or deviations from your desired results.
Precision cutting tools are also important for consistency. By using sharp tools with the right geometry, you’ll be able to maintain the same quality across multiple parts, ensuring a consistent output that meets your customers’ needs.
11. How Does Brass Machining Compare to Other Materials?
Brass is often compared to other materials like aluminum and steel in terms of machining. What’s the kicker here? Brass is more malleable and easier to machine than steel, but it’s also softer than aluminum, which can result in faster tool wear. However, unlike aluminum, brass offers better corrosion resistance, making it ideal for applications where durability is key.
What’s the real story? When it comes to choosing between brass and other metals for a project, the decision often depends on the application’s requirements. While brass may not be as strong as steel, its ability to withstand corrosion and its malleability make it an ideal choice for parts that need to be both functional and aesthetically pleasing.
12. What Are Some Common Mistakes to Avoid When Machining Brass?
There are several common mistakes to avoid when machining brass. Ready for the good part? One of the biggest mistakes is using the wrong cutting tool for the job. If your tool isn’t suited for brass, it can cause excessive wear, overheating, and poor surface quality.
Another mistake is using too high a cutting speed. Although brass is a soft material, using an excessively high speed can cause overheating and work hardening, making the machining process harder.
What’s the kicker here? Pay attention to tool maintenance—ensure your tools stay sharp and well-maintained. A dull tool can create heat, mess with tolerances, and result in a poor finish.
13. How Can You Reduce Costs While Machining Brass?
Machining brass can be costly, especially if the process isn’t optimized. But here’s the kicker—by making a few adjustments, you can significantly reduce costs while still maintaining quality.
The key to cutting costs is improving efficiency. By selecting the right tool for the job, reducing machine downtime, and ensuring proper feed rates and speeds, you can save both time and money. Automating certain aspects of the machining process can also help increase productivity and reduce labor costs.
What’s the real story? Using high-quality materials that last longer and require less maintenance can also lower costs in the long run. Ensuring that your machinery is properly calibrated and maintained will also help extend its lifespan and improve its performance.
14. What Safety Precautions Should You Take When Machining Brass?
Safety is paramount when machining any material, and brass is no exception. Ready for the good part? Proper safety protocols help minimize risks such as burns, cuts, or exposure to harmful fumes.
To stay safe, always wear the appropriate personal protective equipment (PPE), including gloves, safety glasses, and hearing protection. Additionally, ensure that all machines are properly shielded to prevent flying debris from causing injuries.
What’s the kicker here? Ensure your workspace is free from any hazards, and make sure to follow all safety guidelines provided by the equipment manufacturer. By maintaining a safe environment, you can avoid accidents and focus on achieving the best possible results.
15. How Can You Optimize Brass Machining for Mass Production?
When machining brass for mass production, consistency and efficiency are key. What’s the real story? One way to optimize mass production is to set up automated systems that can handle multiple parts simultaneously. By using multiple spindles, you can machine several parts at once, reducing the overall time per part.
Another key to efficiency is streamlining the machining process by choosing the best possible cutting tools and fluids to minimize wear and tear. By implementing a high-quality machining process, you can ensure that every part produced is accurate and up to spec.
خاتمة
In summary, machining brass involves a careful balance of selecting the right tools, techniques, and settings to achieve high-quality results. By understanding the material, adjusting cutting speeds, choosing the right alloy, and maintaining precision throughout the process, you can ensure that your brass machining operations run smoothly. Whether you’re facing challenges like overheating or seeking ways to improve your finish, the tips and techniques outlined above will help you achieve better results. Ultimately, optimizing your machining process will reduce costs, improve efficiency, and ensure consistent, high-quality output.
قسم الأسئلة الشائعة
س1: ما هي معالجة النحاس؟
Machining brass involves shaping, cutting, and finishing brass material to create parts or components used in various industries. Brass is often chosen for its corrosion resistance, appearance, and ease of machining.
س2: How does brass machining differ from other materials?
Brass is softer and easier to machine than metals like steel, which can make it simpler to work with. However, it can wear tools faster than materials like aluminum. Brass also offers superior corrosion resistance, making it ideal for applications that require durability.
س3: How can I prevent brass from overheating during machining?
To prevent overheating, use cutting fluids to cool both the cutting tool and the brass. Additionally, monitor the cutting speed and feed rate to avoid excessive heat buildup. Carbide cutting tools are also recommended due to their heat resistance.
س4: What are the best practices for surface finishing brass?
Achieving a smooth finish on brass involves using the right cutting tools, polishing, grinding, and sometimes sandblasting or ultrasonic cleaning. These techniques help remove tool marks and imperfections, improving both the functionality and appearance of the part.
س5: How can I improve precision when machining brass?
To improve precision, ensure your CNC machine is calibrated properly, use high-quality cutting tools, and minimize vibration. Regular machine maintenance and adjusting the feed rate and cutting speed based on the material’s response will also help achieve more accurate results.