Introduction: Understanding CNC Machines
CNC machines are the backbone of modern manufacturing, offering a level of precision and automation that traditional machining methods simply can’t match. But have you ever wondered what makes these machines tick? The answer lies in the intricate, yet powerful, components that work together to deliver precise, high-quality parts every time. In this article, we’ll take you through the essential CNC machine parts and their functions, breaking down each part’s role in achieving seamless operation. By the end, you’ll have a deeper understanding of what makes CNC machines such a crucial part of the manufacturing process.
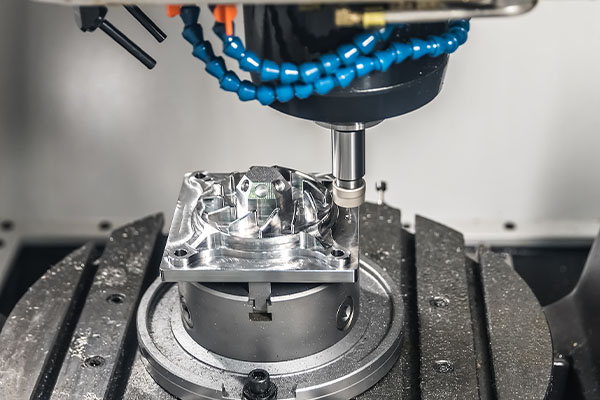
The Basic Structure of a CNC Machine
What Are the Key Components of a CNC Machine?
A CNC machine is a complex system with several interconnected parts, each serving a distinct purpose. At its core, it consists of the frame, motors, control panel, spindle, and various components that facilitate movement and precision. These parts work together to execute precise machining tasks. The frame is the foundation that holds all other components, ensuring stability during operations. Motors drive the movement of different parts, and the control panel serves as the interface between the user and the machine, enabling the entry of commands for the machine to follow.
How Do CNC Machines Operate?
The operation of a CNC machine revolves around the precise movement of the tool, driven by motors and guided by feedback systems. The control panel feeds instructions into the system, which then translates them into mechanical actions. For example, the spindle rotates the cutting tool, while the guideways ensure that the tool moves smoothly along the necessary path. The precision comes from the synergy between the frame, motors, sensors, and software that continuously adjust movements to maintain accuracy.
أنواع آلات CNC
CNC machines come in various types, each designed to handle different tasks. The most common include CNC mills, lathes, routers, and grinders. Each type has unique parts tailored for its intended use. For instance, CNC milling machines feature rotating cutters that move along multiple axes, while CNC lathes focus on rotating workpieces for precision cutting. Understanding the structure and function of each machine type can help manufacturers choose the right one for their specific needs.
The CNC Machine Frame: The Backbone of the Machine
What is the CNC Machine Frame?
The CNC machine frame is the foundational structure that supports all the other components. It holds everything in place, ensuring that all the parts are aligned properly for accurate machining. Made from sturdy materials like cast iron or steel, the frame must be able to withstand vibrations and forces without deforming. A solid frame ensures minimal movement and maximum precision during the cutting process.
Materials Used for CNC Frames
The materials used to build a CNC frame are critical to its stability and performance. Cast iron is a popular choice due to its durability and ability to absorb vibrations effectively. Steel is another option that provides strength and rigidity, though it may be more expensive. Some modern CNC machines even use aluminum for lighter, more portable models. Regardless of the material, the frame must maintain structural integrity to support the high precision required by CNC machines.
Why the Frame is Critical for Stability
The stability of the frame directly affects the accuracy and performance of the machine. A rigid frame minimizes vibrations that can cause deviations in the machining process. Any movement or flexing of the frame could result in imprecise cuts, leading to poor product quality. By ensuring a strong, stable foundation, the frame helps maintain consistency and reliability throughout the machining process.
The CNC Control Panel: The Brain of the Machine
What is the CNC Control Panel?
The CNC control panel is the interface that allows the user to communicate with the machine. It acts as the brain of the system, translating instructions into movements and operations. With a combination of buttons, touchscreens, and dials, the control panel provides an intuitive way for operators to input commands, adjust machine settings, and monitor performance. It is where all the decision-making happens, enabling seamless operation.
How Does the Control Panel Work?
The control panel is connected to the machine’s central computer, which processes the user’s input and translates it into commands for the machine to execute. Operators can enter detailed specifications for the machining process, including feed rates, tool paths, and cutting speeds. Advanced control panels also feature real-time monitoring, allowing operators to check the machine’s status, troubleshoot issues, and ensure the process runs smoothly.
Types of Control Systems (Fanuc, Siemens, etc.)
There are several popular CNC control systems, each offering different features and compatibility. Fanuc is widely recognized for its user-friendly interface and reliability, while Siemens is known for its advanced technology and flexibility. Other systems, like Heidenhain and Mitsubishi, provide different features tailored to specific machining needs. Choosing the right control system can impact the ease of use and performance of the machine.
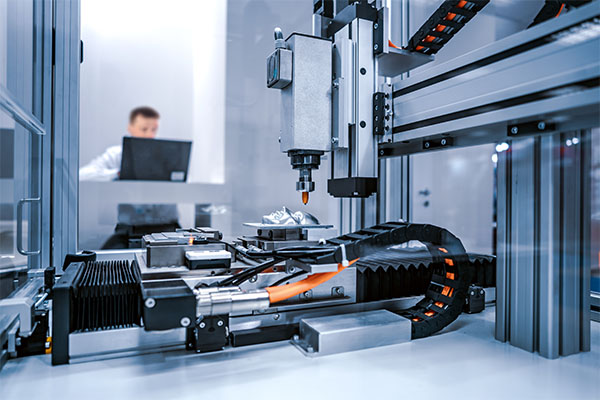
CNC Motors: Powering the Machine
What Are CNC Motors?
CNC motors are responsible for powering the movement of various components within the machine. These motors convert electrical energy into mechanical motion, enabling parts to move along precise paths. The type and size of motor used can significantly affect the machine’s performance, especially in terms of speed and precision.
Types of CNC Motors
There are several types of motors used in CNC machines, including stepper motors, servo motors, and brushless motors. Stepper motors are commonly used for tasks that require precise movements, while servo motors are better suited for high-speed, high-precision operations. Brushless motors are becoming increasingly popular due to their efficiency and long lifespan. The choice of motor depends on the specific requirements of the machining task.
How Motors Affect Machine Speed and Precision
The performance of CNC motors directly impacts the speed and accuracy of the machine. Stepper motors are excellent for precise control at lower speeds, while servo motors excel in high-speed applications. Motors with high torque ratings can also handle heavier workloads, ensuring the machine can operate effectively under different conditions. The type of motor selected affects not only speed but also the overall precision of the machine.
The Spindle: The Heart of Cutting Operations
What is the CNC Spindle?
The spindle is one of the most critical components of a CNC machine, as it is responsible for rotating the cutting tool. This allows the machine to perform tasks like drilling, milling, and turning. The spindle must be able to achieve high speeds and provide sufficient torque to cut through various materials effectively.
How Does the Spindle Work?
The spindle is powered by a motor and connected to the tool holder, which holds the cutting tool in place. When activated, the motor spins the spindle at a high rate of speed, which in turn rotates the cutting tool. This rotational motion, combined with precise movements along multiple axes, allows the CNC machine to perform detailed cutting operations with high precision.
Types of Spindles
There are several types of spindles used in CNC machines, each designed for specific tasks. Direct-drive spindles are the most efficient, as they eliminate the need for belts or gears. Belt-driven spindles, while less efficient, are more affordable and commonly found in less expensive machines. Integrated spindles combine the motor and spindle into a single unit, providing compactness and precision. Each type has its own set of advantages depending on the application.
CNC Guideways: Ensuring Smooth Motion
What Are CNC Guideways?
CNC guideways are linear rails that allow the movement of machine components along precise paths. They ensure that parts like the tool holder, workpiece, and spindle move smoothly and accurately during operations. Without proper guideways, the machine’s accuracy would be compromised, resulting in subpar cuts and a loss of precision.
Types of Guideways
There are several types of guideways used in CNC machines, including linear guideways, box guideways, and roller guideways. Linear guideways are the most common and are ideal for machines requiring high-speed movement. Box guideways are designed for heavy-duty operations and provide greater support for larger, heavier workpieces. Roller guideways offer a smooth, low-friction surface, ensuring high precision during operations.
How Guideways Impact Precision and Longevity
Guideways play a crucial role in maintaining the machine’s accuracy over time. Smooth, well-maintained guideways ensure that components move without any deviation from their intended path. Regular maintenance, such as cleaning and lubrication, helps preserve the guideways’ functionality and ensures the longevity of the machine. By investing in high-quality guideways, manufacturers can achieve consistent performance and avoid costly repairs down the line.
CNC Linear Rails: Supporting Precise Movement
What Are Linear Rails?
Linear rails are essential components of the CNC guide system that provide a stable, smooth path for moving machine parts. These rails allow for high precision during machining operations, guiding the movement of the worktable, spindle, and other parts.
How Do Linear Rails Work?
Linear rails work by providing a low-friction surface along which the moving parts of the CNC machine glide. They typically consist of a rail and a carriage, with ball bearings or rollers reducing friction and ensuring smooth movement. The precision of linear rails is critical to maintaining the accuracy of the machine.
Maintenance and Longevity of Linear Rails
Regular maintenance is essential for ensuring the longevity of linear rails. Proper lubrication reduces friction and wear, while periodic inspection helps identify any damage or misalignment. By keeping the rails clean and in good working condition, CNC machines can operate at peak efficiency for years to come.
CNC Ballscrews: Transmitting Motion Accurately
What Are Ballscrews?
Ballscrews are used in CNC machines to convert rotational motion into linear motion. These components play a crucial role in moving the machine’s tool holder or workpiece along precise paths. Ballscrews reduce friction and improve accuracy by utilizing ball bearings between the nut and screw.
How Do Ballscrews Work?
Ballscrews work by allowing the ball bearings to roll along the surface of the screw, creating smooth, precise movements. This reduces friction compared to traditional screws, resulting in more accurate motion. Ballscrews are highly effective at transmitting power with minimal backlash, making them ideal for high-precision applications.
Types of Ballscrews
There are two primary types of ballscrews: rolled ballscrews and ground ballscrews. Rolled ballscrews are produced by cold-rolling the material, which makes them more affordable but slightly less precise. Ground ballscrews are made by grinding the threads, offering superior precision at a higher cost. The choice of ballscrew depends on the required level of accuracy and the specific application.
CNC Tool Holders: Keeping the Tool in Place
What Are CNC Tool Holders?
Tool holders are critical for securely holding the cutting tool in place during machining operations. Without proper tool holding, there would be excessive vibrations, reduced tool life, and poor machining quality. Tool holders are designed to keep the tool steady and aligned, allowing for precise cutting.
Different Types of Tool Holders
There are several types of tool holders used in CNC machines, including collet chucks, end mill holders, and quick-change tool systems. Collet chucks are commonly used for smaller tools, while end mill holders are ideal for larger cutting tools. Quick-change systems allow for rapid tool swaps, reducing downtime between operations.
Choosing the Right Tool Holder
The right tool holder depends on the type of cutting tool being used, the material being cut, and the required precision. Proper tool holder selection can drastically improve machining performance and tool life, ensuring a smoother and more efficient operation.
CNC Chuck: Clamping Workpieces Securely
What is a CNC Chuck?
A CNC chuck is a clamping device used to secure the workpiece in place during machining operations. The chuck holds the workpiece tightly while the cutting tool operates, ensuring that it does not shift or move during the process.
Types of CNC Chucks
CNC chucks come in both manual and powered versions. Manual chucks are typically used in smaller machines, while powered chucks are used in larger, more advanced CNC systems for faster operation.
How Chucks Improve Precision
A tightly secured workpiece is essential for maintaining machining accuracy. By using high-quality chucks, manufacturers can reduce the chances of errors caused by workpiece movement, ensuring a higher level of precision in each cut.
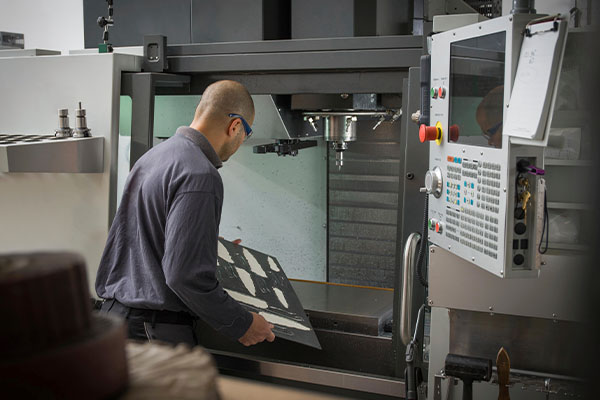
CNC Coolant System: Keeping Everything Cool
Why is a CNC Coolant System Important?
A CNC coolant system helps keep both the workpiece and the cutting tool cool during machining. This prevents overheating, reduces tool wear, and improves the finish of the workpiece.
How Coolants Are Applied in CNC Machines
Coolant is typically delivered to the cutting area through mist, flood, or through-tool systems. Flood coolant systems are the most common, providing a steady stream of coolant directly to the cutting area. Through-tool systems allow for more precise coolant application.
Types of Coolants Used in CNC Machines
Coolants can be either synthetic or oil-based. Synthetic coolants are water-based and often used for aluminum or softer materials, while oil-based coolants are more suitable for tougher metals like steel.
CNC Sensors and Feedback Systems: Monitoring Machine Health
What Are CNC Sensors?
CNC sensors monitor various machine parameters, such as temperature, vibration, and pressure. These sensors provide real-time feedback to the machine’s controller, ensuring optimal performance.
The Role of Feedback in CNC Machines
Feedback systems allow the machine to continuously adjust its movements based on real-time data. By receiving feedback from sensors, the machine can make small adjustments to maintain precision throughout the process.
Common Types of CNC Sensors
CNC machines utilize a variety of sensors, including position sensors, temperature sensors, and vibration sensors. Position sensors monitor the location of machine components, while temperature and vibration sensors detect potential issues like overheating or excessive wear.
CNC Electrical System: The Power Source
What is the CNC Electrical System?
The electrical system in a CNC machine provides the necessary power to operate various components, including the motors, control system, and cooling systems. This system is critical for ensuring stable power delivery during operation.
Types of Electrical Components in CNC Machines
The electrical system consists of several key components, such as power supplies, circuit boards, transformers, and cables. These components work together to deliver power and ensure the safe operation of the machine.
How Electrical Systems Ensure Machine Performance
A stable electrical system is essential for maintaining consistent machine performance. Power fluctuations or electrical issues can lead to inaccurate machining, inconsistent tool movements, or even machine failure.
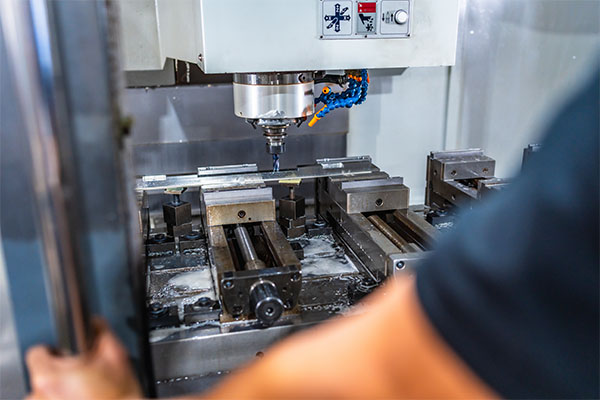
Conclusion: Maintaining CNC Machine Parts for Longevity and Accuracy
Why Regular Maintenance is Crucial
Regular maintenance is essential for ensuring the longevity and accuracy of CNC machines. By keeping all components in top condition, manufacturers can prevent costly repairs, minimize downtime, and ensure that machines continue to perform at their best.
Best Practices for CNC Machine Maintenance
Routine maintenance tasks include checking for wear and tear, cleaning the components, and ensuring proper lubrication. Maintaining a strict maintenance schedule can greatly extend the life of the machine and improve overall performance.
The Future of CNC Machines
تكنولوجيا التحكم الرقمي بالكمبيوتر continues to evolve, with new advancements in automation, materials, and precision. The future of CNC machines will likely involve greater integration of AI, machine learning, and real-time data analytics, offering even higher levels of performance and efficiency.
قسم الأسئلة الشائعة
What’s the Difference Between a CNC Milling Machine and a CNC Lathe?
A CNC milling machine uses rotating cutters to remove material from a stationary workpiece, while a CNC lathe rotates the workpiece itself while a cutting tool removes material. The choice between the two depends on the type of operation being performed.
How Can I Improve the Longevity of My CNC Spindle?
To extend the lifespan of your CNC spindle, regularly check for lubrication, monitor spindle speeds, and inspect for signs of wear. Keep the machine clean to prevent debris from affecting the spindle’s performance.
How Often Should I Replace My CNC Machine’s Ballscrews?
Ballscrews should be replaced when they show signs of wear, such as backlash or excessive noise. Regularly inspect them for any visible damage or signs of poor performance to determine the ideal replacement schedule.
What is the Role of the CNC Controller in Machine Operations?
The CNC controller acts as the brain of the machine, translating operator commands into precise actions. It controls the movement of the motors, the operation of the spindle, and monitors feedback systems to maintain accuracy.
How Do I Know Which CNC Machine Parts Need Replacement?
Regularly check parts like ballscrews, spindles, and motors for wear. Listen for unusual sounds, monitor performance inconsistencies, and inspect for visible signs of damage.
Why is CNC Coolant Necessary, and How Do I Choose the Right Type?
CNC coolant helps cool down the tool and workpiece, reducing wear and preventing overheating. The right coolant depends on the materials being cut and the type of machining being performed.