مقدمة
Many people interested in machining may find the process intimidating due to its complexity and the array of machines available. However, CNC machining has become an essential part of modern manufacturing, with its capabilities to create precise and complex components. If you’re looking to get started with CNC machining, whether as a hobbyist or someone planning a career, this guide will help you understand everything you need to know, from the basic concepts to the practical aspects of getting hands-on with a CNC machine. وهنا الصفقة—we’ll break it all down into easy-to-understand steps so you can jump into the world of CNC machining confidently.
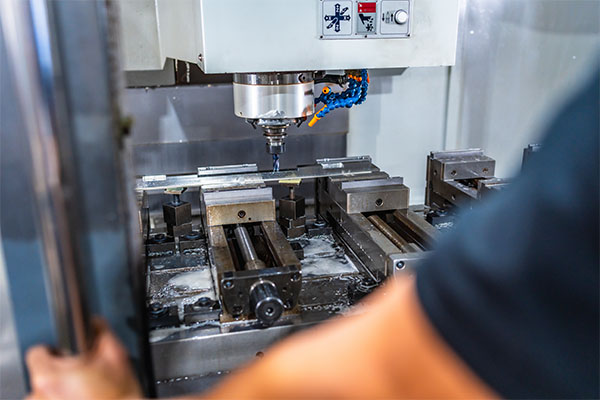
What Is CNC Machining?
Definition of CNC Machining
CNC machining stands for Computer Numerical Control machining, a technology that uses computers to control machine tools. Unlike traditional machining, where an operator physically manipulates the machine, CNC machining uses pre-programmed computer software to automate these tasks. This provides unparalleled precision, reduces human error, and increases efficiency, making it the preferred choice for many industries today. CNC machines are versatile and can create complex shapes by cutting, grinding, milling, and drilling materials. The precision achieved through CNC machining has made it a key process in industries like automotive, aerospace, medical device manufacturing, and even consumer electronics.
Overview of CNC Machining Process
The CNC machining process typically involves creating a design on CAD (Computer-Aided Design) software, converting it into a set of instructions via CAM (Computer-Aided Manufacturing) software, and then sending those instructions to a CNC machine. The machine interprets the code and executes the movement of cutting tools on a piece of material. Whether it’s cutting metal, plastic, or wood, CNC machining can produce parts with incredible accuracy, often within fractions of a millimeter. As a result, CNC machines have become essential in industries that demand high-quality, precision parts. ربما تتساءل, how does this all come together? Well, in the next sections, we’ll explore why this process is so important for modern manufacturing.
Key Benefits of CNC Machining
CNC machining offers several advantages that make it a valuable tool for industries across the globe. First off, it delivers extreme precision—something that traditional methods can’t always match. CNC machines are also highly automated, reducing the need for human labor and minimizing the risk of errors. This leads to increased production speeds and efficiency. Moreover, the versatility of CNC machines allows them to work with a wide variety of materials, making them suitable for numerous applications. Whether you’re designing small components for electronics or large aerospace parts, CNC machining can deliver the quality and precision required for even the most demanding jobs.
Why Should You Learn CNC Machining
Career Opportunities
Learning CNC machining can open doors to numerous career opportunities in industries like automotive, aerospace, medical devices, and more. These fields rely heavily on precise manufacturing processes, and CNC machinists are always in demand to operate these sophisticated machines. In fact, as technology advances, the demand for skilled CNC operators is expected to continue growing. By learning CNC machining, you are not just gaining a skill; you’re entering a field with many prospects, from operating CNC machines in manufacturing facilities to designing and programming the machines themselves.
Skill Development
CNC machining allows individuals to develop a broad set of skills, from technical proficiency in operating and programming machines to a deep understanding of materials and how they interact with various tools. Plus, learning how to interpret complex blueprints and CAD files will enhance your problem-solving abilities, which can be valuable in many engineering and manufacturing roles. The hands-on experience you’ll gain while learning CNC machining also provides transferable skills that are applicable to other sectors within the broader manufacturing and design industries.
Improving Productivity
CNC machining is widely known for its ability to improve productivity. وهنا الصفقة—machines can operate 24/7, which means fewer human labor hours are required, and products can be made much faster than through traditional methods. This increased speed can result in cost savings and faster turnaround times for manufacturers. Additionally, CNC machines are highly precise, which reduces the chances of mistakes, ensuring fewer errors and better-quality products. Whether you’re running a business or looking to expand your skill set, the knowledge of CNC machining can give you a competitive edge.

Common CNC Machines and Their Functions
ماكينات الطحن CNC
CNC milling machines are one of the most commonly used types of CNC machines. They work by rotating a cutting tool while the material is held in place, allowing the tool to move along multiple axes to carve out the shape of the desired part. Milling machines can be used for a wide range of applications, including drilling, contouring, and slot cutting. For beginners, it’s important to start with a basic milling machine to grasp the essential concepts of CNC machining before moving on to more advanced machinery.
مخرطات سي إن سي
CNC lathes are another type of machine that is widely used in various industries. Unlike milling machines, lathes work by rotating the material itself while the cutting tool stays stationary. This method is ideal for creating cylindrical or round parts. Lathes are commonly used to produce products like shafts, tubes, and gears. When choosing your first CNC machine, it’s essential to understand the differences in machine functions. Lathes are particularly useful when working with round materials and can provide excellent results when the proper cutting tools are used.
أجهزة التوجيه CNC
CNC routers are primarily used for cutting softer materials like wood, plastic, and foam. They can also work with metals such as aluminum and brass, making them versatile machines. Routers are commonly used in woodworking and sign making, and they offer a great option for those interested in working with large, flat materials. CNC routers use a similar principle to milling machines but are optimized for these softer materials.
CNC Plasma and Laser Cutters
These machines are designed to cut materials using high-powered plasma or lasers. Plasma cutters work by using an electrically charged gas stream, while laser cutters use a focused beam of light to melt or vaporize the material. These machines are particularly popular in the sheet metal industry and are used to produce precise cuts in a variety of metals. Laser cutters offer extremely fine cuts and can be used for intricate designs, while plasma cutters are better suited for thicker materials.
Choosing the Right CNC Machine for Beginners
Factors to Consider
Choosing the right CNC machine for your needs depends on several factors. First off, you need to consider your budget. CNC machines can range from a few hundred dollars for basic hobby machines to tens of thousands of dollars for industrial-grade machines. Second, think about the materials you’ll be working with. Some machines are better suited for specific materials, such as metal or plastic. It’s also important to consider the size of the workpieces you plan to produce, as some CNC machines are designed for larger parts, while others are better suited for smaller, more intricate designs.
Best CNC Machines for Hobbyists and Beginners
If you’re just starting, you’ll want to invest in a beginner-friendly CNC machine. Desktop CNC routers and small milling machines are great options for hobbyists and those just getting their feet wet. These machines are affordable, compact, and capable of handling smaller-scale projects. They can work with a variety of materials, including wood, plastics, and metals like aluminum, making them ideal for experimentation and learning.
Used vs. New CNC Machines
وهنا الصفقة—buying a used CNC machine can save you money, but it also comes with risks. Secondhand machines may have wear and tear, which could lead to expensive repairs down the road. However, purchasing a new CNC machine can be a significant investment, although it often comes with warranties and customer support. Beginners may prefer buying new machines to ensure reliability and avoid the hassles of maintenance right from the start.
Essential Skills You Need to Start CNC Machining
Understanding Blueprints and CAD Files
One of the most important skills in CNC machining is understanding technical blueprints and CAD files. Blueprints and CAD files contain the detailed instructions needed for creating a part. As a machinist, you’ll need to interpret these files to know how to position tools, what angles to use, and how to achieve the desired measurements. Don’t worry if this sounds complicated—with time, you’ll become proficient in reading and understanding these files, which will be essential to your success as a CNC machinist.
Basic Mathematics for CNC Machining
Basic math skills are essential for CNC machinists, especially in understanding measurements, scaling, and tolerances. You’ll need to be comfortable with fractions, decimals, and the metric system, as CNC machines often require precision to within thousandths of an inch. Understanding tolerances, which indicate the acceptable range of error in a part, is also crucial. Whether you’re measuring the diameter of a hole or the depth of a cut, you’ll need to apply math to ensure everything aligns perfectly.
Programming Basics
To truly master CNC machining, you’ll need to learn programming basics, specifically G-code و M-code. G-code is the language that CNC machines use to perform tasks like moving the cutting tool and controlling machine speed. M-code is used to handle machine functions such as turning the spindle on or off. Once you get the hang of G-code, you can program your CNC machine to produce virtually any design you can imagine.
Tool and Material Selection
Choosing the right tools and materials is critical for success in CNC machining. CNC tools come in various shapes and sizes, and each type of tool is suited for different tasks. End mills are used for cutting flat surfaces, while drills are ideal for making holes. It’s also important to understand material properties, such as hardness and flexibility, as these affect how the material will react to cutting tools. Choosing the right combination of tool and material ensures that you can achieve the desired result while minimizing tool wear and material waste.
The Role of CNC Software
CAD (Computer-Aided Design)
CAD software is the starting point for most CNC machining projects. Using CAD, you can create a 3D model of the part you want to make, including its dimensions, shape, and any intricate details. This model serves as a digital blueprint for the CNC machine, guiding it on how to cut the material. Popular CAD software includes AutoCAD, SolidWorks, and Fusion 360, each of which has unique features suited for different types of projects.
CAM (Computer-Aided Manufacturing)
CAM software takes the digital model created in CAD and converts it into instructions that CNC machines can follow. Using CAM, you generate tool paths that tell the machine how to move during the machining process. CAM software like Mastercam, Fusion 360, and SolidCAM can optimize tool paths to improve efficiency and reduce machining time, which is especially important for large-scale manufacturing.
Software Examples
Several software programs are available for CNC machining, each designed for different stages of the process. Fusion 360 is an all-in-one software that combines CAD, CAM, and even CAE (Computer-Aided Engineering). SolidWorks is known for its detailed 3D modeling capabilities and is often used by engineers and designers. Mastercam is a popular choice for creating CAM toolpaths, making it ideal for CNC operators looking to maximize efficiency.
Understanding CNC Machining Tolerances and Precision
What Are Tolerances?
Tolerances in CNC machining refer to the allowable deviation in the dimensions of a part. For example, if you need a hole to be 10mm in diameter, a tolerance might allow it to be between 9.98mm and 10.02mm. The tighter the tolerance, the more precise the part needs to be. ربما تتساءل, how do you ensure that tolerances are met? That’s where high-precision CNC machines come in—these machines are capable of making parts with tolerances down to fractions of a millimeter.
Precision vs. Accuracy in CNC Machining
In CNC machining, precision refers to how consistently a machine can reproduce a part, while accuracy refers to how close that part is to the intended design. بعبارة أخرى, a CNC machine can be precise but not accurate if it consistently produces parts that are slightly off from the target dimensions. The key is to calibrate and adjust the machine regularly to ensure both precision and accuracy are maintained throughout the production process.
How to Measure and Maintain Precision
To maintain precision, machinists use a variety of measuring tools, including micrometers, calipers, and gauges. Regular calibration of the CNC machine is also essential. By performing routine checks and adjustments, you can ensure that your machine is producing parts that meet the required specifications. Remember, even small changes in tool wear or environmental factors like temperature can affect the precision of your parts.
Setting Up Your CNC Machine
Installation Considerations
Setting up a CNC machine involves ensuring that it is securely installed, level, and properly connected to power and computer systems. وهنا الصفقة—you must ensure that the machine is placed in an area that offers both sufficient space and stability for accurate operations. The setup also includes installing necessary accessories such as tool changers and automatic tool measurement devices.
Safety First
CNC machining involves working with high-speed tools and powerful machines. That’s why safety should always be a top priority. Always wear protective gear, including goggles, ear protection, and gloves. It’s also crucial to ensure that you’re familiar with emergency shut-off buttons and other safety features on your CNC machine. Taking the time to follow safety protocols will help prevent accidents and injuries.
Machine Components and Functions
Understanding your machine’s components is critical to successful operation. At the core, the machine includes a motor that powers the tool movement, a controller that interprets instructions, and a spindle that holds the cutting tool. Plus, there are various other elements like linear guides, ball screws, and coolant systems that work together to ensure smooth and precise machining operations. Before starting your first project, take time to get familiar with the machine’s parts and functions.
G-Code: The Language of CNC Machines
Introduction to G-Code
G-code is the language that tells CNC machines exactly what actions to take. It contains a series of commands that define the tool path, spindle speed, feed rate, and other important factors that influence the machining process. ربما تتساءل, how do I learn G-code? Don’t worry—it’s simpler than it seems. You can start by learning some basic commands that control motion, and as you gain experience, you’ll learn more advanced commands for specific functions.
Basic G-Code Commands
Some of the most common G-code commands include G00 (rapid positioning), G01 (linear interpolation), and G02/G03 (clockwise and counterclockwise arcs). These commands tell the CNC machine how to move the tool along specific paths to shape the material. Understanding these commands is essential for programming your CNC machine to complete a task.
Practical G-Code Exercises for Beginners
To practice G-code programming, you can start with basic exercises like creating simple geometric shapes. For example, try programming the machine to cut a square or a circle. As you grow more comfortable with these basic commands, you can move on to more complex shapes and multi-tool operations. With practice, you’ll be able to create custom programs for more intricate designs.
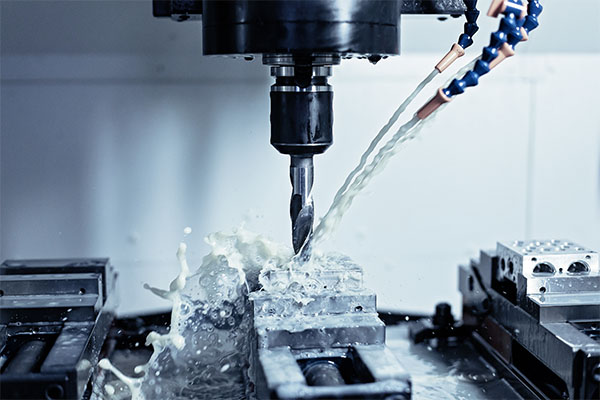
Choosing the Right Tools and Materials for CNC Machining
Tool Types
CNC tools come in various types, each suited for different applications. For example, end mills are used for cutting flat surfaces, while drills are ideal for making holes. Taps are used for threading, and special tools like ball end mills are used for creating rounded contours. The key is to choose the right tool for the job to achieve the desired finish and precision.
Material Choices
Choosing the right material is crucial to achieving the desired results. Materials like aluminum, stainless steel، و plastic are commonly used in CNC machining, but the specific material you select will depend on the application. Harder materials require specialized tools and more careful handling, while softer materials may be easier to machine but require different settings.
Tool Life and Maintenance
CNC tools are subject to wear over time, especially with materials that are harder to cut. Regular maintenance of your tools is essential for ensuring consistent results. Clean tools after every job, and regularly check them for signs of wear and tear. By keeping your tools in top condition, you can avoid costly replacements and keep your machine running smoothly.
CNC Machining Workflow: A Step-by-Step Process
Design Phase
Every CNC machining project starts with a design phase. First off, you’ll need to create a 3D model of the part using CAD software. This model will serve as the blueprint for the entire machining process, dictating how the machine will operate to create the part.
Tool Path Creation
Once the design is finalized, you’ll use CAM software to generate the tool paths. This is where the magic happens—the CAM software will create instructions for the CNC machine, detailing how the tools will move to cut the material.
Machine Setup
The next step is setting up the machine itself. Make sure that the material is securely fixed in the machine, and the correct tools are installed. You’ll also need to input the tool offsets and test the program to ensure everything runs smoothly.
Execution
After all the setup, it’s time to run the machine. Monitor the process carefully to ensure that everything is going according to plan. If there are any issues, be prepared to stop the machine and make adjustments.
Troubleshooting Common CNC Machining Problems
Machine Failures
Machines can experience failures due to mechanical issues like misalignment or tool wear. When this happens, it’s important to diagnose the problem quickly to minimize downtime. Regular maintenance can help prevent some of these issues.
Material Defects
Sometimes the material you’re working with may have defects that affect machining quality. For instance, impurities or inconsistencies in the material can lead to an uneven surface or a part that doesn’t meet specifications. Always inspect your materials before you begin machining.
Programming Errors
Mistakes in the G-code or tool paths can lead to errors during machining. Common errors include incorrect tool movements or using the wrong tool for a job. To prevent mistakes, double-check your program before running the machine and test it with a dry run.
How Much Does It Cost to Get Started with CNC Machining?
Initial Investment
The initial cost of starting with CNC machining can vary widely. For beginners, hobby-grade machines can cost anywhere from a few hundred dollars to a few thousand dollars, while industrial machines can run into the tens of thousands. Additionally, you’ll need to invest in CAD and CAM software, which can add to the initial cost.
Ongoing Costs
Once you’ve made the initial investment, there are ongoing costs to consider. These include the cost of materials, tool replacements, and machine maintenance. It’s important to account for these expenses in your overall budget to ensure that you can continue operating efficiently.
Cost vs. Value
While CNC machines can require significant upfront investment, the value they provide in terms of precision, efficiency, and the ability to create high-quality products justifies the expense. Whether you’re starting a business or enhancing your skills, CNC machining can pay off in the long run through increased productivity and high-quality output.
How to Gain Experience and Practice CNC Machining
Apprenticeships and Online Courses
For beginners looking to gain hands-on experience, apprenticeships and online courses are great ways to learn. An apprenticeship allows you to work under the guidance of a professional machinist and gain practical skills, while online courses can provide foundational knowledge and hands-on exercises for practicing CNC programming and machine operation.
CNC Machining Communities
One of the best ways to gain experience is to join a CNC machining community. Online forums, local meetups, and industry events are great places to ask questions, share your experiences, and learn from others. ربما تفاجأ how helpful these communities can be, especially when you’re just getting started.
Experimenting at Home
If you’re working as a hobbyist, you can practice CNC machining at home with a smaller, more affordable machine. Try starting small, working with basic materials like wood or soft metals, and gradually progress to more complex projects. This hands-on practice will help you build confidence and improve your skills.
Conclusion: Your Next Steps in CNC Machining
CNC machining is a valuable skill that opens up numerous opportunities in various industries. Key takeaways from this guide include the importance of understanding machine types, programming, and tool selection, as well as the need to invest in training and practice. So, what’s next? If you’re ready to dive into CNC machining, take the first step by researching machines, learning CAD and CAM software, and starting small. With dedication and practice, you’ll soon be creating high-quality parts with ease.
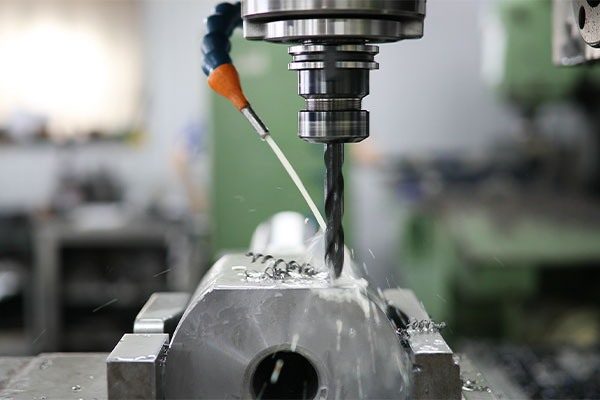
قسم الأسئلة الشائعة
- What is the best CNC machine for beginners? The best CNC machine for beginners depends on your needs and budget. For hobbyists and beginners, desktop CNC routers or small CNC milling machines are good options. They are affordable, user-friendly, and versatile enough to work with a variety of materials like wood, plastic, and soft metals such as aluminum. Popular choices for entry-level machines include the Shapeoko, X-Carve, or Tormach 440.
- Do I need special training to start CNC machining? While you don’t need formal training to get started, learning CNC machining requires a basic understanding of how machines work, CAD (Computer-Aided Design) and CAM (Computer-Aided Manufacturing) software, and G-code programming. Beginners can benefit from online courses, workshops, and hands-on practice to build confidence and improve their skills. Apprenticeships or community colleges also offer more structured training opportunities.
- Can I learn CNC machining online? Yes, you can learn CNC machining online through various courses, tutorials, and forums. Websites like Udemy, Coursera, and LinkedIn Learning offer courses on CNC machining fundamentals, including CAD, CAM, and G-code programming. Many CNC manufacturers also offer free resources, and forums like CNCZone allow you to ask questions and share experiences with other machinists.
- What is the average cost of CNC machining equipment? The cost of CNC machining equipment can vary widely depending on the type and size of the machine. Entry-level CNC machines can range from $500 to $5,000, with more advanced machines for professional use costing upwards of $20,000. In addition to the machine itself, there are costs for CAD/CAM software, tools, materials, and maintenance. For a beginner, starting with a lower-cost machine is advisable, and you can always upgrade as your skills grow.
- How do I get better at CNC programming? To improve your CNC programming skills, practice is key. Start by working on simple projects to familiarize yourself with G-code and machine operation. Hands-on practice with software like Fusion 360 or SolidWorks can help you create more accurate and efficient programs. You can also take online courses, participate in CNC machining communities, or attend workshops to deepen your understanding of programming concepts.
- What materials can be machined using CNC machines? CNC machines can handle a wide variety of materials, including metals (aluminum, steel, brass, titanium), plastics (acrylic, PVC, nylon), wood, and composites. Each material requires different cutting tools and machining techniques, so it’s essential to understand how the material behaves during machining. For instance, softer materials like plastic are easier to cut, while harder metals like steel require specialized tools and slower cutting speeds.
- How long does it take to become proficient at CNC machining? The time it takes to become proficient in CNC machining varies depending on your prior experience and dedication. With consistent practice, many beginners can expect to get comfortable with basic machine operation and G-code programming within a few months. Mastering more complex machining tasks, toolpath generation, and troubleshooting can take a year or more. Continuous learning and hands-on practice are key to improving your skills.
- What safety precautions should I take when operating CNC machines? Safety should always be your top priority when operating CNC machines. Always wear appropriate personal protective equipment (PPE) such as safety glasses, hearing protection, and gloves. Ensure the machine is properly set up and calibrated before running it, and never leave a running machine unattended. Familiarize yourself with emergency shut-off buttons and safety features on the machine. Additionally, regularly inspect your equipment for any wear or malfunction that could pose safety risks.
- Is CNC machining a good career? CNC machining is a highly rewarding career for individuals interested in precision manufacturing. With the growing demand for skilled machinists in industries like aerospace, automotive, medical devices, and electronics, CNC machining offers job stability and growth potential. Professionals in this field can advance to roles such as CNC programmer, machine operator, or even management. Additionally, the high level of skill required makes CNC machining a lucrative career with competitive wages.
- Can CNC machines be used for home-based businesses? Yes, CNC machines can be used for home-based businesses, particularly for small-scale manufacturing. Many hobbyists and entrepreneurs use smaller CNC routers, mills, and laser cutters to create custom products such as signage, jewelry, parts for model-making, and more. Starting a home-based CNC machining business is feasible with the right equipment, workspace, and understanding of machine operation. However, it’s important to check local zoning and business regulations if you plan to run a commercial operation from your home.