Introduction
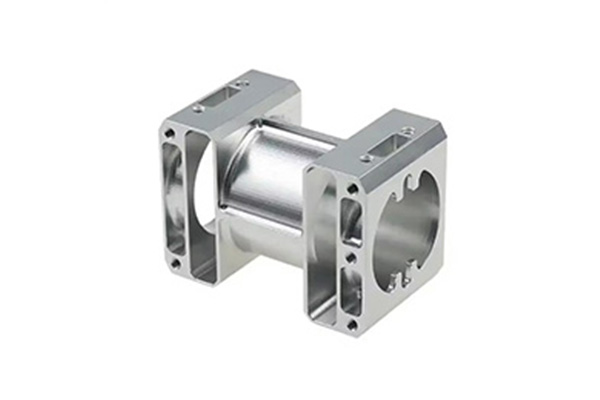
In this comprehensive guide, we will dive deep into the various materials used in manufacturing processes, exploring their significance, types, and the factors influencing material selection. Understanding the right materials is essential for producing high-quality products at an optimal cost. Whether you’re involved in manufacturing machinery, electronics, or consumer goods, this guide will equip you with the knowledge to make informed decisions about material choices in CNC machining.
1. Why Are Materials Important in Manufacturing?
Material selection is fundamental to the success of any manufacturing process. But here’s the kicker—the choice of material not only influences the functionality of the end product but also affects the efficiency of the entire production process. From raw materials to final products, everything hinges on the properties of the materials used. What’s the real story? Materials determine the cost-effectiveness of production, the durability of the final product, and how quickly it can be manufactured.
Manufacturers must consider multiple factors when selecting materials, including strength, weight, and resistance to wear. A wrong choice could lead to unnecessary expenses, production delays, or product failure. Ready for the good part? By understanding the types of materials available and their benefits, manufacturers can streamline their processes and deliver high-quality products consistently.
Material choice also impacts the product’s performance. For example, selecting the wrong material could affect the product’s resistance to extreme temperatures or its ability to withstand wear and tear. Moreover, it plays a crucial role in the cost of production, which can directly impact pricing strategies and market competitiveness.
Material Type | Impact on Production | Impact on Product Quality |
---|---|---|
Metals | High strength, versatile | Durable, high-quality finish |
Plastics | Lightweight, easy to mold | May lack strength, but cost-effective |
Composites | Lightweight, strong | High performance, complex to process |
2. What Are the Different Types of Manufacturing Materials?
Materials used in manufacturing can be broadly categorized into five main types: metals, plastics, composites, ceramics, and natural materials like wood. This is where it gets interesting… Each type has distinct properties that make it suitable for particular applications.
Metals like steel, aluminum, and titanium are commonly used in manufacturing due to their strength, durability, and ability to withstand extreme conditions. What’s the catch? While metals can be heavy, they offer exceptional performance in industries like automotive, aerospace, and construction. Steel is particularly prized for its strength, while aluminum is chosen for its lightweight properties, making it ideal for applications where weight reduction is critical.
Plastics and polymers are lightweight, corrosion-resistant, and cost-effective, making them popular in industries like consumer goods, packaging, and electronics. However, plastics often lack the strength of metals and may not perform well in high-temperature environments. But here’s the kicker—advances in polymer technology have led to the development of high-performance plastics that can rival metals in terms of strength and durability.
Composites, such as fiberglass and carbon fiber, are used when high strength-to-weight ratios are needed. These materials are commonly found in the aerospace and automotive industries. They’re incredibly strong, yet lightweight, making them ideal for applications where performance is crucial. However, they tend to be more expensive and difficult to process.
Material | Properties | Common Uses |
---|---|---|
Metals | Strong, durable, heavy | Automotive, aerospace, construction |
Plastics | Lightweight, cost-effective | Packaging, consumer goods, electronics |
Composites | Strong, lightweight | Aerospace, automotive, sports equipment |
3. How Do Material Properties Affect Manufacturing Processes?
Material properties are integral to the manufacturing process. What’s the real story? The characteristics of materials, such as strength, durability, and hardness, directly influence how they are processed, machined, and shaped into finished products.
Strength is perhaps the most critical property for manufacturing. Materials like metals and composites offer high strength, making them suitable for heavy-duty applications. On the other hand, soft materials like rubber and some plastics may be easier to mold or machine but don’t provide the same strength or durability.
Durability and hardness are vital for products exposed to harsh environments. Materials with high hardness, such as titanium or ceramics, resist wear and tear, ensuring longevity in critical components like bearings or engine parts. Ready for the good part? On the flip side, these materials are often more difficult to process, requiring specialized tools and techniques.
Additionally, properties like thermal and electrical conductivity are essential when manufacturing components for electronics or power systems. Materials like copper and aluminum are excellent conductors of electricity, making them ideal for electrical wiring and connectors.
Material Property | Influence on Manufacturing | Examples |
---|---|---|
Strength | Affects machining techniques and product durability | Steel, Titanium |
Durability | Influences product lifespan and wear resistance | Ceramics, Composites |
Conductivity | Determines material use in electronics | Copper, Aluminum |
4. How Do Manufacturers Choose the Right Material?
Choosing the right material is more than just a selection process—it’s a balancing act between cost, quality, and performance. Here’s the kicker—manufacturers must carefully assess multiple factors to ensure that the material chosen aligns with both the production capabilities and the intended product’s requirements.
Cost vs. quality considerations are one of the first things manufacturers look at when selecting materials. High-quality materials like titanium or carbon fiber can be significantly more expensive than metals like steel or aluminum. However, if the performance of the end product is critical, opting for a higher-quality material might be necessary.
Availability and supply chain factors are also crucial. Manufacturers must ensure that the material is readily available in the quantities they need and at the right price. Sourcing materials from reliable suppliers helps minimize delays and ensures production schedules are met.
The right material choice also depends on manufacturing capabilities. If a manufacturer lacks the equipment to process a particular material, it may be more cost-effective to choose an alternative material that aligns better with their current resources.
Factor | Impact on Material Selection | Examples |
---|---|---|
Cost vs. Quality | Determines material affordability vs. performance | Steel (affordable), Titanium (premium) |
Availability | Affects production timelines and supply chain | Plastics (widely available), Rare metals (less availability) |
Manufacturing Capability | Affects material processability and efficiency | Wood (easy to process), Composites (complex processes) |

5. What Are Common Materials Used in CNC Machining?
In CNC machining, materials must be selected based on their machinability and ability to withstand the precision required in the process. This is where it gets interesting… CNC machining requires materials that are easy to cut, shape, and finish to tight tolerances.
Metals, especially steel, aluminum, and brass, are the most commonly used materials in CNC machining due to their strength and versatility. But here’s the kicker—these metals are not only durable but also provide the necessary hardness and strength for a wide range of mechanical applications.
Plastics and composites also play an important role in CNC machining. Plastics like polycarbonate, acrylic, and nylon are often chosen for their ease of machining and cost-effectiveness. On the other hand, composites, such as carbon fiber and fiberglass, offer high strength-to-weight ratios but are harder to machine.
Each material comes with its own set of benefits and challenges. Ready for the good part? When selecting a material for CNC machining, manufacturers must consider factors like material hardness, cutting speed, and tooling costs.
Material | Machinability | Common Applications |
---|---|---|
Steel | Hard, durable, challenging to machine | Automotive parts, structural components |
Aluminum | Easy to machine, lightweight | Aerospace, consumer electronics |
Plastics | Easy to machine, cost-effective | Consumer goods, packaging |
6. How Do Sustainability Concerns Affect Material Choices in Manufacturing?
Sustainability is becoming an increasingly important factor in material selection. What’s the real story? With rising environmental concerns, manufacturers are looking for ways to reduce waste, use renewable resources, and lower the carbon footprint of their production processes.
Recycled materials are gaining traction as an alternative to traditional materials. For example, recycled aluminum and plastics can be just as effective as new materials while significantly reducing environmental impact. But here’s the kicker—recycled materials often come at a lower cost, making them an attractive option for manufacturers seeking to cut costs while being more environmentally responsible.
Trends toward sustainable material sourcing also include the use of bio-based materials, which are derived from renewable sources like plants or algae. These materials are not only biodegradable but also help reduce reliance on fossil fuels, making them a more eco-friendly option for manufacturers.
Sustainable Material | Benefits | Common Uses |
---|---|---|
Recycled Aluminum | Reduces waste, lower environmental impact | Automotive, packaging |
Bio-based Plastics | Biodegradable, renewable | Packaging, consumer goods |
Recycled Plastics | Cost-effective, reduces landfill waste | Consumer electronics, textiles |
7. How Does Material Affect the Cost of Manufacturing?
When it comes to manufacturing, the material selection process plays a crucial role in determining the overall cost of production. But here’s the kicker—it’s not just the cost of raw materials that matters, but also the associated processing and production time.
Direct material costs refer to the expense of acquiring the material itself, while processing costs include the costs for cutting, shaping, and assembling those materials. For instance, high-quality metals such as titanium may come at a premium price, but the processing cost might be lower due to their ease of machining. On the other hand, cheaper materials like certain plastics may be inexpensive upfront but require more time and labor to process, ultimately increasing overall production costs.
To illustrate this, consider the difference between low-cost and premium materials. Aluminum, a relatively inexpensive material, is often used for products requiring moderate strength and light weight. However, when compared to a material like carbon fiber, which is more expensive, manufacturers must weigh the performance benefits. Carbon fiber offers higher strength-to-weight ratios, making it ideal for applications where performance is prioritized over cost.
Ultimately, material choices can impact labor, processing time, and production complexity, which all tie back into the final cost of manufacturing.
Material | Direct Cost | Processing Cost | Example Applications |
---|---|---|---|
Aluminum | Low | Low | Aircraft, automotive parts |
Titanium | High | Moderate | Aerospace, medical implants |
Carbon Fiber | High | High | Sports equipment, aerospace |
8. What Are the Most Durable Materials for Manufacturing?
Durability is a key consideration when selecting materials for manufacturing, particularly for products that must withstand harsh environments or prolonged use. What’s the real story? Some materials are better suited for durability in extreme conditions than others.
Metals like steel, titanium, and Inconel alloys are among the most durable for high-stress applications. Steel, for example, is not only strong but also resistant to wear and fatigue, making it ideal for construction and machinery. Titanium, known for its excellent corrosion resistance, is widely used in aerospace and medical industries.
Ceramics and composites, while less common than metals, offer exceptional durability in specific contexts. Ceramics are often used in applications requiring high temperature resistance, such as in turbine blades or industrial furnaces. Composite materials like fiberglass and carbon fiber offer superior strength-to-weight ratios, making them ideal for industries like automotive manufacturing and sports equipment.
When selecting materials for durability, manufacturers must consider not only the inherent properties of the material but also how it will interact with the intended environment. Materials that perform well in one situation may fail in another due to different stressors like temperature extremes or chemical exposure.
Material | Durability Features | Example Applications |
---|---|---|
Steel | Strong, wear-resistant | Machinery, construction |
Titanium | Corrosion-resistant | Aerospace, medical devices |
Ceramics | High-temperature resistance | Industrial furnaces, turbine blades |
Composites (e.g., Carbon Fiber) | High strength-to-weight ratio | Aerospace, automotive |
9. How Do New Materials Impact the Future of Manufacturing?
Innovation in materials science has the potential to transform industries and lead to manufacturing breakthroughs. Ready for the good part? New materials such as nanomaterials and smart materials are setting the stage for advancements in manufacturing processes and product capabilities.
Nanomaterials, for instance, are engineered at the molecular level, offering properties like increased strength, conductivity, or flexibility that are not possible with traditional materials. These advances are already being applied in industries like electronics and healthcare, where high-performance materials are essential for smaller, more efficient products.
Smart materials are another exciting development. These materials can change their properties in response to environmental conditions such as temperature, pressure, or light. For example, materials that expand or contract with changes in temperature are being used in self-healing concrete for infrastructure projects. This type of material could revolutionize construction by reducing maintenance costs and increasing the lifespan of structures.
As these materials continue to evolve, manufacturers will have access to more versatile, sustainable, and cost-effective solutions, further pushing the boundaries of what is possible in manufacturing technology.
Material Type | Key Feature | Potential Applications |
---|---|---|
Nanomaterials | Enhanced strength, conductivity | Electronics, healthcare |
Smart Materials | Ability to change properties | Self-healing concrete, robotics |
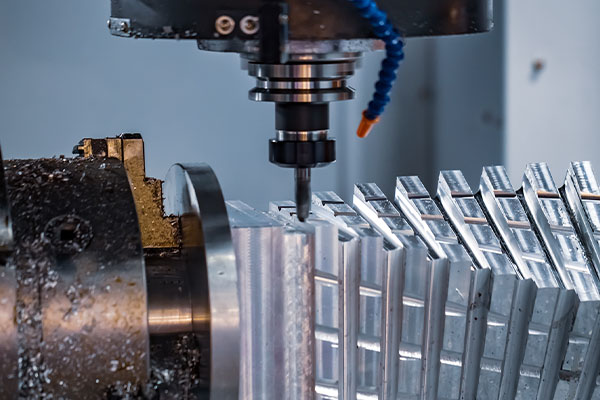
10. What Are the Best Materials for High-Precision Manufacturing?
High-precision manufacturing demands materials that can be manipulated with extreme accuracy and maintain their integrity under tight tolerances. This is where it gets interesting… Some materials excel in this arena, particularly those used in industries like aerospace, medical, and electronics.
Materials used in aerospace, such as aluminum alloys and titanium, are known for their lightweight yet strong properties. These materials are often used in applications that require both precision and durability. Medical industries, particularly those focused on implants and prosthetics, often rely on titanium for its biocompatibility and strength.
In the electronics and micro-manufacturing industries, materials like silicon and various metal alloys are critical. These materials are precisely machined to create components for semiconductors and microchips, where even a tiny deviation in size can cause failure. The trade-off between precision and cost must always be considered. While some materials offer unparalleled precision, they may come with a higher price tag and processing cost.
Selecting the right material for high-precision manufacturing is crucial, as even the slightest material flaw or inconsistency can lead to a product failure.
Material | Precision Features | Example Applications |
---|---|---|
Aluminum Alloys | Lightweight, strong | Aerospace components |
Titanium | High strength, biocompatible | Medical implants, prosthetics |
Silicon | High precision, conductivity | Semiconductors, microchips |
11. How Can Manufacturers Optimize Material Usage?
Optimizing material usage is essential for improving production efficiency and reducing costs. But here’s the kicker… Material wastage not only increases costs but also impacts the environment, so manufacturers are looking for innovative ways to minimize loss and improve sustainability.
Reducing waste starts with making the right material choices. By selecting materials that are easier to process and require less finishing, manufacturers can cut down on waste during the production phase. For example, using metals that are easier to machine can significantly reduce scrap material.
Another way to optimize material usage is through advanced manufacturing techniques like additive manufacturing (3D printing). This allows manufacturers to use only the exact amount of material needed for each part, minimizing waste. Additionally, recycling and reusing scrap materials can further reduce the need for new raw materials.
Finally, the use of simulation software can help manufacturers design parts that use material more efficiently, ensuring minimal waste throughout the production process.
Technique | Impact on Material Usage | Example Applications |
---|---|---|
Additive Manufacturing | Minimal waste, custom designs | Aerospace, automotive |
Material Recycling | Reduces new material usage | Automotive, electronics |
Simulation Software | Optimizes material selection | Aerospace, medical devices |
12. What Is the Role of Material Testing in Manufacturing?
Material testing is a critical step in ensuring the final product meets the required standards for quality, safety, and performance. What’s the real story? Without proper testing, manufacturers risk producing products that may fail under use, leading to costly recalls and reputation damage.
Testing methods like tensile, fatigue, and hardness tests are commonly used to determine a material’s strength and durability. Tensile testing measures how much stress a material can handle before breaking, while fatigue testing assesses how a material responds to repeated stress over time. Hardness testing, on the other hand, measures a material’s resistance to deformation, which is especially important in high-wear environments.
By performing these tests before production, manufacturers can identify any potential issues early on and make adjustments to their material selection or manufacturing process. Material testing ensures that products are safe and durable, which is essential for maintaining quality standards.
Testing Method | Purpose | Application |
---|---|---|
Tensile Testing | Measures material strength | Aerospace, automotive |
Fatigue Testing | Assesses material durability | Medical devices, machinery |
Hardness Testing | Measures resistance to wear | Manufacturing, construction |
13. How Do Material Properties Affect Manufacturing Equipment?The properties of materials used in manufacturing have a significant impact on the equipment required to process them. Here’s the kicker—a material’s hardness, texture, and composition will determine the type of machinery and tools needed for production.
Harder materials, like steel and titanium, require cutting tools made from tougher materials, such as carbide or high-speed steel. In contrast, softer materials, such as plastics and certain alloys, can be machined with standard tools. The material’s compatibility with the machine and tool must be carefully considered to avoid excessive wear on the equipment and ensure high-quality results.
Another factor to consider is the material’s thermal conductivity. Materials that heat up quickly, such as aluminum, may require specialized cooling systems during the machining process to prevent deformation. The right machine setup will ensure that both the material and the equipment are used efficiently, resulting in higher productivity and reduced maintenance costs.
Material | Equipment Requirements | Example Applications |
---|---|---|
Steel | High-speed cutting tools | Automotive, construction |
Aluminum | Standard tools, cooling system | Aerospace, consumer goods |
Titanium | Specialized tools, cooling | Aerospace, medical devices |
14. What Are the Challenges of Using Composite Materials in Manufacturing?
Composites have become increasingly popular in manufacturing due to their excellent strength-to-weight ratios and durability. This is where it gets interesting—though they offer significant advantages, working with composite materials presents several challenges.
The primary difficulty lies in the complexity of processing composites. Unlike metals, composites often require specialized equipment and techniques to cut, mold, and finish. The high cost of processing composites can make them prohibitive for certain industries, despite their superior properties.
Additionally, composite materials can sometimes be difficult to join with other materials due to their unique properties. Welding or bonding composite materials requires careful attention to the type of adhesive or process used, which can add to the production cost.
Despite these challenges, composites are increasingly being used in industries where performance is paramount, such as aerospace and automotive manufacturing, where weight reduction is critical.
Challenge | Impact on Manufacturing | Example Applications |
---|---|---|
Processing Difficulty | Requires specialized equipment | Aerospace, automotive |
Joining Issues | Difficult to bond with other materials | Aerospace, sports equipment |
High Costs | Expensive production process | Automotive, construction |
15. How Do Manufacturers Stay Updated on Material Trends?
The materials landscape is constantly evolving, and staying ahead of the curve is essential for manufacturers who want to remain competitive. Ready for the good part? Keeping up with material trends requires a multifaceted approach.
Manufacturers rely on industry journals, conferences, and online resources to stay informed about new materials and their applications. These resources provide valuable insights into the latest innovations and trends, allowing manufacturers to incorporate cutting-edge materials into their production processes.
Collaborating with material scientists and suppliers is also crucial. By working closely with experts, machining manufacturers can gain access to proprietary information about new materials and testing techniques. Additionally, ongoing research and development efforts in material science continue to push the boundaries of what’s possible, helping manufacturers stay at the forefront of technology.
Resource Type | Benefits | Example Uses |
---|---|---|
Industry Journals | Latest material innovations | Automotive, aerospace |
Conferences and Events | Networking, new product insights | Medical devices, electronics |
Collaboration with Experts | Access to proprietary information | Aerospace, sports equipment |
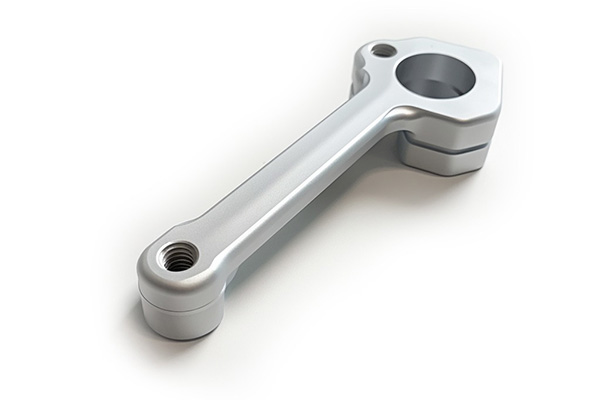
FAQ Section
Q1: What is a manufacturing material?
A manufacturing material is any substance or matter used in the production of goods. It could be metals, plastics, composites, ceramics, or any other material selected based on its properties and suitability for the intended product.
Q2: How does material selection impact manufacturing?
Material selection impacts every aspect of manufacturing, from production cost to product quality and durability. The right choice ensures efficiency, cost-effectiveness, and high-quality output.
Q3: What is the most common material used in manufacturing?
Metals such as steel and aluminum are among the most common materials used in manufacturing due to their strength, versatility, and availability. However, the best material depends on the specific application.
Q4: Why is material testing important in manufacturing?
Material testing ensures that the materials used meet quality standards, safety regulations, and performance requirements. It helps manufacturers avoid costly defects and ensures products function as intended.
Q5: How do new materials affect manufacturing industries?
New materials, such as advanced composites and nanomaterials, offer opportunities for lighter, stronger, and more cost-efficient products. They drive innovation and open new avenues in manufacturing industries like aerospace, electronics, and medical devices.