ভূমিকা
ডান নির্বাচন করা CNC precision machining factory is critical for industries seeking high-quality and durable components. Whether you’re in the aerospace, automotive, or medical field, finding the ideal manufacturing partner can be the difference between a successful product launch and costly delays. This article will guide you through the essential factors to consider when selecting a top CNC machining factory, ensuring you make an informed decision. By understanding the importance of precision, quality control, and efficient operations, you can optimize your production and meet your business goals.
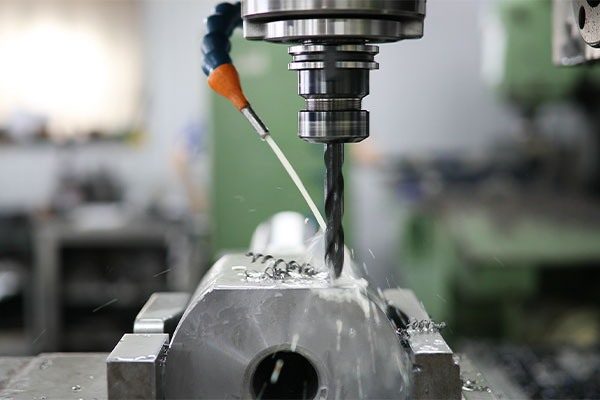
What is CNC Precision Machining?
Definition and Importance of CNC Machining
CNC precision machining refers to the process of using computer numerical control (CNC) machines to produce highly accurate and intricate components. Unlike traditional machining methods, CNC machining automates the production process, leading to higher precision, repeatability, and efficiency. These machines are programmed with specific commands to cut, mill, drill, or shape materials with extreme accuracy. The technology has become an industry standard due to its ability to produce parts that meet tight tolerances and complex geometries, often required in sectors like aerospace, automotive, and medical equipment manufacturing.
CNC machining is an indispensable tool in modern manufacturing, providing a significant advantage in terms of precision and scalability. With industries pushing for more complex designs, CNC machining enables manufacturers to meet these demands by offering high-quality, repeatable results. Whether it’s a small prototype or a large production run, CNC machines ensure that every part is identical in shape, size, and finish, making it a trusted method for creating critical components that require flawless execution.
Different Types of CNC Machining
There are several types of CNC machining processes, each suitable for different kinds of parts and materials. The most common methods include:
- সিএনসি মিলিং: Used to remove material from a workpiece, CNC milling is often used for creating intricate shapes and complex surfaces.
- সিএনসি টার্নিং: This method is used to produce parts with a cylindrical shape. A rotating piece of material is shaped using a stationary tool.
- CNC Grinding: Often employed for achieving a high surface finish, this method is ideal for parts that need precision finishing.
- CNC Drilling: This is used to make holes in materials with precision, a common process for many industrial parts.
Understanding these processes can help you choose the right CNC machining factory for your specific project needs, ensuring that your components are produced to meet high standards.
Why CNC Precision Machining is Important for Your Industry
Benefits Across Industries
CNC precision machining plays a critical role in a variety of industries, providing essential benefits such as reduced material waste, faster production times, and consistent part quality. The ability to work with a range of materials, from metals and plastics to ceramics, makes CNC machining an incredibly versatile solution for many manufacturing needs.
For industries like aerospace, where component precision is vital for safety, CNC machining offers the ability to manufacture parts that meet extremely tight tolerances. In automotive manufacturing, it helps create components that are both cost-effective and durable, ensuring that vehicles perform reliably over time. For the medical industry, CNC machining is indispensable for producing high-precision instruments that are essential for diagnostics and surgeries. Its versatility and precision help businesses in these sectors remain competitive, reduce errors, and minimize production downtime.
Precision and Repeatability
The key reason for adopting CNC precision machining across industries is its ability to produce parts with incredibly tight tolerances. The automated process eliminates the human errors often associated with traditional machining methods, ensuring that each part is produced with the same level of precision. This high level of repeatability is especially beneficial for industries that require large production runs or custom-made components, as it ensures consistency and quality across every item.
In addition, CNC machines are capable of handling complex geometries and fine details, which are often required in industries like aerospace, automotive, and electronics. Parts that once would have been difficult to manufacture can now be produced efficiently and accurately.
Key Features of a Top CNC Precision Machining Factory
Quality Machinery and Technology
A top CNC machining factory must be equipped with advanced machinery capable of handling the specific needs of various industries. The quality of the machines plays a major role in the final product’s precision and consistency. Factories with state-of-the-art CNC machines can produce parts with micron-level accuracy, ensuring that even the most complex parts are manufactured to meet exact specifications. The use of high-end machinery also speeds up production time and reduces the likelihood of errors during the machining process.
Moreover, factories that incorporate automated systems and robotics in their operations are able to offer enhanced efficiency and higher throughput, providing quicker turnaround times for customers. This is especially critical in industries like automotive or aerospace, where production speed can directly affect overall business operations.
Skilled Workforce
A skilled workforce is another defining characteristic of a top CNC precision machining factory. While advanced machinery is vital, it’s the expertise of the operators that truly brings out the full potential of these machines. Skilled workers can ensure that CNC machines are running at optimal performance and can identify potential issues before they become major problems. Additionally, they are proficient in programming the machines to produce complex and customized parts according to the exact specifications provided by the customer.
Having an experienced team also ensures that the factory can handle a wide range of materials, from basic metals to high-performance alloys or even plastics. Workers with deep knowledge of machining processes can adapt to the demands of various industries, guaranteeing that each project is executed flawlessly.
Stringent Quality Control
A top CNC machining factory should have stringent quality control measures in place to ensure that each product meets high standards. This includes the use of precision measuring equipment like coordinate measuring machines (CMM) and laser scanners to verify part dimensions and tolerances. The factory should also have a robust inspection process to catch any defects before the product is shipped. Quality assurance is vital, especially in industries where safety and performance are paramount, such as aerospace and medical device manufacturing.
Additionally, certifications like ISO 9001 or industry-specific certifications such as AS9100 for aerospace or ISO 13485 for medical devices can help verify the factory’s commitment to maintaining high-quality standards. Factories with such certifications have demonstrated their dedication to producing top-quality parts and adhering to international standards.
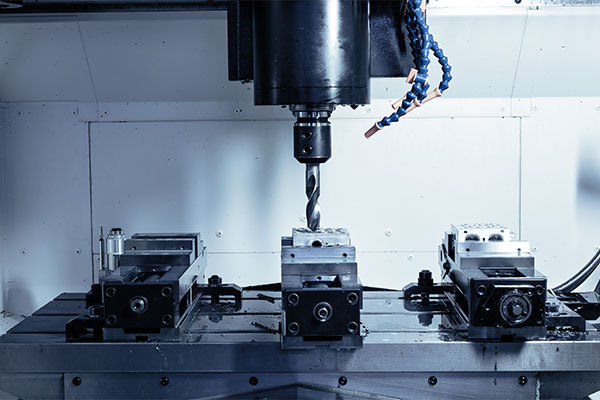
How to Choose the Best CNC Precision Machining Factory for Your Needs
Key Factors to Consider
When selecting a CNC precision machining factory, there are several factors to consider to ensure that it can meet your industry needs. First and foremost, evaluate the factory’s reputation. Look for reviews, testimonials, and case studies from past clients to gauge their reliability and the quality of their work. Additionally, assess the factory’s technical capabilities, including their ability to work with specific materials, production volumes, and the complexity of parts they can handle.
Location also plays a role in the decision-making process. While a local factory can provide easier communication and shorter lead times, international factories may offer cost advantages. Consider whether the factory has the capacity to scale production based on your future needs and whether it offers flexibility in meeting custom design requirements.
Assessing Communication and Support
Effective communication is essential in ensuring that the CNC machining factory understands your requirements and can deliver the desired product. A good factory should be able to provide clear communication regarding project timelines, cost estimates, and technical specifications. Consider whether the factory has dedicated customer support representatives who can answer questions promptly and help with any issues that may arise during the production process.
Moreover, it’s important to assess the factory’s after-sales support. Will they be able to assist you with any post-production questions or concerns? The ability to maintain an ongoing relationship with your machining partner is crucial, particularly for long-term or large-scale projects.
Industries That Benefit the Most from CNC Precision Machining
Aerospace and Aviation
The aerospace and aviation industries require components that meet the highest standards of precision, as even the smallest error can have catastrophic consequences. CNC precision machining allows manufacturers to produce critical parts like turbine blades, engine components, and structural elements that are both lightweight and durable. These parts must adhere to strict safety and performance specifications, and CNC machining is the ideal solution for achieving this level of precision.
মোটরগাড়ি
In the automotive industry, CNC machining is used extensively for producing parts like engine blocks, transmission gears, and suspension components. These parts must meet strict quality standards while also being cost-effective. CNC machining ensures that each part is manufactured with tight tolerances, improving vehicle performance and safety. Moreover, the ability to mass-produce complex parts makes CNC machining an indispensable tool for automotive manufacturers.
চিকিৎসা সরঞ্জাম
The medical industry relies on CNC precision machining to produce parts like surgical instruments, diagnostic tools, and implants. Precision is critical in medical device manufacturing, as even the smallest deviation can compromise functionality or patient safety. CNC machining allows for the production of complex parts with the necessary tolerances, ensuring that they perform as intended. The ability to customize parts for specific medical applications is another significant advantage of CNC machining.
ইলেকট্রনিক্স
Electronics manufacturing also benefits from CNC precision machining, especially in the production of components like circuit boards, connectors, and housing for electronic devices. The tight tolerances required in electronics are easily achieved through CNC machining, ensuring the functionality and durability of critical components. Additionally, CNC machining can handle the small-scale production of intricate parts needed for high-performance electronics.
Common Materials Used in CNC Precision Machining
ধাতু
Metals are the most commonly used materials in CNC machining. Popular options include steel, aluminum, titanium, and brass, each of which has its unique properties that make it suitable for different applications. Steel is often used in automotive and industrial applications due to its strength and durability. Aluminum is preferred for aerospace and automotive parts due to its lightweight nature, while titanium is used in the aerospace and medical industries for its strength-to-weight ratio and resistance to corrosion.
Plastics and Composites
CNC machining is also capable of working with plastics and composites, making it versatile for industries like consumer electronics, medical devices, and automotive. Materials like polycarbonate, PTFE, and carbon fiber composites are commonly used in CNC machining for parts that require a balance of strength, flexibility, and lightweight properties. CNC machines can precisely cut and shape these materials, ensuring that parts meet the required tolerances.
Ceramics and Glass
CNC machining can also work with more specialized materials, such as ceramics and glass, which are often used in high-performance industries like medical devices and electronics. These materials require precision machining to achieve the desired shape and finish. CNC machines are equipped with specialized tools and techniques to work with these fragile materials without compromising their integrity.
Wood and Other Unconventional Materials
In addition to metals and plastics, CNC machining can also handle materials like wood, foam, and rubber. These materials are often used in prototyping and custom production runs, especially for industries like packaging or consumer goods. CNC machining allows for precise cutting and shaping, ensuring that even unconventional materials are processed with high accuracy.
CNC Precision Machining Capabilities: What to Look For
Precision and Tolerance Specifications
When selecting a CNC machining factory, it’s essential to consider the precision and tolerance specifications of the machines they use. CNC machines can offer incredibly fine tolerances, sometimes down to a fraction of a millimeter, depending on the type of machining and material being used. The ability to achieve such precise measurements is critical for industries like aerospace, medical, and electronics, where even the smallest deviations can lead to performance issues or safety concerns.
Range of Machining Operations
Another key consideration is the range of machining operations offered by the factory. Look for a factory that offers a variety of processes, including milling, turning, drilling, and grinding. This ensures that the factory can handle the production of complex parts with multiple features and geometries. Multi-axis machining is another important capability, as it allows for more flexibility and the ability to create intricate shapes in a single setup, improving efficiency and accuracy.
Capability for Custom Parts and Prototypes
A good CNC machining factory should be able to handle both custom parts and prototypes. Customization is often necessary when creating unique components for a specific application or when developing new products. CNC machining is highly adaptable, allowing for the production of parts with specific features or geometries that may not be possible with other manufacturing methods. Additionally, CNC machining is an excellent option for prototyping, as it allows for the creation of functional prototypes in a short period of time.
High-Speed Machining
High-speed machining (HSM) is a technique that involves using faster cutting speeds to produce parts more quickly while maintaining high precision. HSM is particularly useful when working with materials that are difficult to machine, such as high-strength alloys or composites. It can also help reduce production time and lower costs, making it an attractive option for manufacturers looking to improve their efficiency.
Multi-Axis Machining
Multi-axis CNC machining involves the use of machines with more than three axes, allowing for the production of more complex parts in a single setup. This eliminates the need for multiple operations, saving time and reducing the risk of errors. Multi-axis machining is particularly useful for producing parts with intricate geometries or tight tolerances, such as components used in aerospace or medical applications.
How Advanced Technology Enhances CNC Precision Machining
সিএনসি সফটওয়্যারের ভূমিকা
CNC precision machining is driven by advanced software that helps ensure the accuracy and efficiency of the production process. CAD (computer-aided design) and CAM (computer-aided manufacturing) software are used to design parts and generate toolpaths that guide the CNC machines. This integration allows for greater precision in the machining process, as the software can optimize the toolpaths to minimize errors and reduce material waste.
Automation and Robotics
Automation plays a key role in improving the efficiency and consistency of CNC machining. Robotic arms and automated material handling systems are used to load and unload parts, reducing manual labor and minimizing the risk of errors. These technologies help improve the throughput of CNC machining, allowing factories to meet tight deadlines and production quotas.
এআই এবং মেশিন লার্নিং
Artificial intelligence (AI) and machine learning are increasingly being incorporated into CNC machining operations. AI algorithms can predict maintenance needs, optimize toolpaths, and improve machine performance over time. Machine learning allows CNC machines to adapt to changing conditions, such as material variations or tool wear, ensuring consistent quality throughout the production run.
Quality Control and Assurance in CNC Machining
Importance of Rigorous Quality Control
Quality control is a cornerstone of CNC precision machining. Given the high stakes involved in industries like aerospace, medical devices, and automotive manufacturing, it’s essential that parts meet the highest standards. Rigorous quality control measures are in place to ensure that each part is produced to the required tolerances. These measures often include visual inspections, dimensional checks, and the use of precision measurement tools like coordinate measuring machines (CMM) to verify that parts are within spec.
Techniques Used for Quality Assurance
Common techniques used for quality assurance in CNC machining include visual inspection, in-process monitoring, and post-production testing. CMM machines are often used to measure the dimensions of parts with extreme accuracy, while surface finish measurements ensure that parts meet the required surface quality. Many factories also use statistical process control (SPC) to monitor the production process and ensure consistency across production runs.
Certifications to Look For
Certifications are a strong indicator of a CNC machining factory’s commitment to quality. ISO 9001 certification ensures that the factory adheres to internationally recognized quality management standards, while industry-specific certifications such as AS9100 (for aerospace) or ISO 13485 (for medical devices) demonstrate that the factory meets the stringent requirements of these specialized fields. Factories that hold these certifications are more likely to deliver consistent, high-quality results.
The Cost of CNC Precision Machining: What You Should Know
Pricing Factors
The cost of CNC precision machining depends on several factors, including the material being used, the complexity of the part, the volume of production, and the required tolerances. More complex parts that require specialized tooling or multi-axis machining will generally be more expensive than simpler components. Material costs also vary, with metals like titanium being more expensive to machine than aluminum or plastics.
Cost Comparison Between Different Machining Methods
When comparing CNC machining to other traditional machining methods, CNC often offers a more cost-effective solution in terms of precision and repeatability. While traditional methods may require more manual labor and multiple setups, CNC machines can produce parts in a single setup, reducing labor costs and minimizing errors. Additionally, the ability to run multiple parts simultaneously on a CNC machine further reduces production costs.
Managing Costs Through Factory Selection
Choosing the right CNC machining factory can have a significant impact on the overall cost of your project. Factories with more advanced machinery and greater technical capabilities may charge higher rates, but they often deliver higher-quality parts with faster turnaround times. Conversely, factories that lack the necessary equipment or expertise may produce parts with errors or delays, leading to higher costs in the long run. It’s important to balance cost with quality and capabilities to find the best solution for your needs.
Managing Material Costs
Material costs are one of the most significant factors in CNC precision machining. Some materials, such as high-performance alloys or composites, can be expensive to machine. However, a top CNC machining factory can help you manage these costs by optimizing machining parameters to reduce material waste and improve production efficiency. Additionally, factories with established relationships with material suppliers may be able to offer discounts or pass on savings to their clients.
Lead Time and Delivery Considerations
The Importance of Fast Turnaround
In today’s fast-paced manufacturing environment, fast turnaround times are critical. CNC machining can offer quick production cycles, especially for prototypes or small production runs. However, lead times can vary depending on factors like the complexity of the part, the material being used, and the factory’s workload. It’s essential to communicate your timeline with the CNC machining factory to ensure that your project is completed on time.
Factors Affecting Lead Times
Several factors can affect lead times in CNC precision machining, including the availability of materials, machine setup times, and the complexity of the part. Simple parts with standard materials can typically be produced more quickly than complex parts that require specialized tooling or custom setups. Lead times can also be influenced by the factory’s capacity, with larger factories able to handle larger orders more efficiently.
Communicating Your Timeline
Clear communication is key when discussing lead times with a CNC machining factory. Make sure to provide detailed information about your project’s requirements, including any deadlines or time constraints. By setting realistic expectations and maintaining open communication, you can help ensure that your project is completed within the required timeframe.
Shipping and Logistics Considerations
Shipping and logistics also play a significant role in lead times. If you are working with an international CNC machining factory, consider factors like customs delays and international shipping times. When working with local suppliers, delivery can be faster, but always account for potential shipping delays, especially during peak seasons.
Prototyping vs. Mass Production: Understanding the Differences
CNC Machining for Prototyping
CNC machining is an excellent tool for rapid prototyping, allowing designers to test and refine their ideas before committing to mass production. Prototypes can be produced quickly and with high precision, enabling designers to identify potential issues early in the development process. CNC prototyping also allows for easy modifications, as changes can be made to the design without requiring significant retooling.
CNC Machining for Mass Production
In contrast, mass production requires CNC machining to be highly efficient and capable of producing large volumes of identical parts. For mass production, factories use automated systems to speed up the process, ensuring that parts are produced at a high rate without sacrificing quality. Multi-axis machines and other advanced technologies are often used to handle the high volume and complexity of mass production runs.
Transitioning from Prototyping to Mass Production
Once the prototype has been tested and finalized, CNC machining can seamlessly transition to mass production. The same machinery and processes are often used for both prototyping and large-scale production, ensuring consistency in quality across both phases. However, production runs typically require adjustments to machining parameters, tooling, and setup processes to accommodate the higher production volumes.
The Role of Customization in CNC Precision Machining
Tailoring CNC Machining for Specific Needs
Customization is a significant advantage of CNC precision machining. CNC machines can be programmed to produce parts that meet very specific requirements, whether it’s a particular shape, material, or finish. This flexibility makes CNC machining ideal for industries that require unique components, such as aerospace or medical devices.
Custom Tooling and Fixtures
To achieve the highest level of precision, CNC machining often requires custom tooling and fixtures. These tools are specifically designed for a particular project, allowing the factory to produce parts with the necessary precision and consistency. Custom tooling can be costly, but it ensures that parts are produced accurately and efficiently, especially when dealing with complex geometries.
Working with Manufacturers for Custom Orders
When requesting custom CNC machining, it’s essential to communicate your needs clearly to the factory. Providing detailed technical drawings and specifications will ensure that the factory can produce the exact parts you require. Collaborative discussions with the factory’s engineering team can also help refine the design and manufacturing process.
Global vs. Local CNC Precision Machining Factories: Which to Choose?
Benefits of Local CNC Machining
Local CNC machining factories offer several advantages, including quicker turnaround times and easier communication. Being able to visit the factory in person can help you better understand their capabilities and inspect the quality of their work. Additionally, shipping costs and lead times are generally shorter when working with a local supplier.
Advantages of Global CNC Machining
On the other hand, international CNC machining factories may offer cost savings due to lower labor or production costs. These factories may also have more extensive capabilities or specialized machinery that local suppliers cannot provide. Global CNC machining can be a great option for businesses looking to scale production or for industries that require highly specialized components.
Balancing Local and Global Options
Choosing between local and global CNC machining factories ultimately depends on your specific needs. Consider factors like production volume, required tolerances, and budget when making your decision. Some businesses may find it beneficial to combine both local and international suppliers, allowing them to leverage the strengths of each depending on the nature of the project.
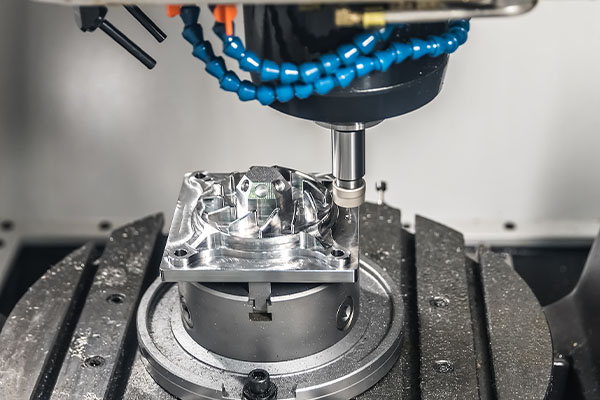
উপসংহার
Choosing the right CNC precision machining factory is crucial to ensuring the success of your projects. By understanding the key features of CNC machining, the different materials used, and the industries that benefit from these technologies, you can make an informed decision when selecting a factory that fits your specific needs. Remember, whether you’re producing prototypes or mass quantities, working with the right factory can help you achieve high-quality results with precision and efficiency. Reach out to a trusted CNC precision machining partner today to start optimizing your manufacturing processes.
প্রায়শই জিজ্ঞাসিত প্রশ্ন বিভাগ
- What industries use CNC precision machining the most? CNC precision machining is used in industries like aerospace, automotive, medical devices, and electronics, where precision is critical.
- What are the benefits of CNC over traditional machining methods? CNC machining offers higher precision, repeatability, and efficiency compared to traditional methods, leading to reduced errors and faster production times.
- How do I ensure the CNC machining factory I choose will meet my quality standards? Look for certifications like ISO 9001, AS9100, or ISO 13485, and ensure the factory has a robust quality control process.
- What materials can CNC machining handle? CNC machining can work with a variety of materials, including metals (steel, aluminum, titanium), plastics, composites, ceramics, and even wood.
- How does prototyping with CNC machining work? CNC machining allows for rapid prototyping, where parts are produced quickly and accurately to test designs before mass production.
- Can CNC machining be used for both small and large production runs? Yes, CNC machining is versatile and can be used for both small-scale prototyping and large-volume production runs.
- What is the typical lead time for CNC precision machining projects? Lead times vary depending on the complexity of the part and the factory’s capacity, but typical lead times range from a few days to several weeks.
- What are the main cost factors in CNC machining? Key cost factors include material type, part complexity, volume, and the required precision. More complex parts typically cost more to machine.
- How do I find a reliable CNC precision machining factory? Research potential factories, review client testimonials, assess their technical capabilities, and ensure they have the necessary certifications.
- What certifications should I look for when choosing a CNC machining factory? Look for ISO 9001 certification for quality management, as well as industry-specific certifications like AS9100 for aerospace or ISO 13485 for medical devices.