ভূমিকা
When it comes to CNC machining, copper presents a unique challenge due to its soft, malleable nature and high thermal conductivity. As one of the most commonly used metals in industries like aerospace, automotive, and electronics, copper’s demand is high, but machining it to perfection requires a precise understanding of its characteristics. The wrong approach can lead to rapid tool wear, poor finishes, and increased production costs. In this article, we’ll explore the best techniques for CNC machining copper, covering everything from choosing the right alloy to finishing touches that result in high-quality products.
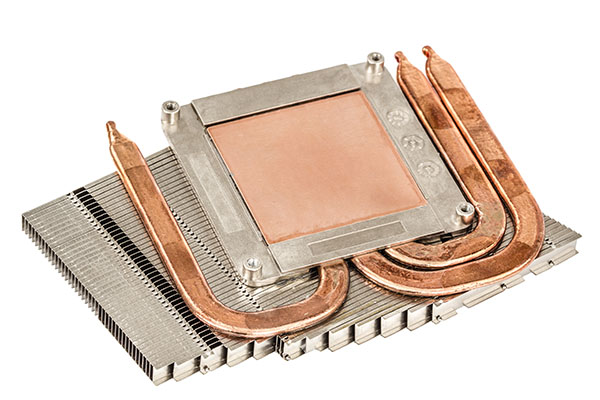
1. What is Copper CNC Machining?
Copper CNC machining is the process of using computer numerical control (CNC) machines to cut, shape, and finish copper and its alloys into precise components. The process is widely used in industries like electronics, automotive, aerospace, and more, due to copper’s excellent conductivity, resistance to corrosion, and malleability. CNC machines allow for highly accurate and repeatable production of copper parts, which is crucial for industries where precision is essential.
The importance of CNC machining lies in its ability to achieve complex shapes and intricate designs in copper components. Unlike traditional manual methods, CNC machining offers faster, more accurate results, reducing human error and increasing production efficiency. These benefits are critical for manufacturers who need to create high-precision parts such as electrical connectors, heat exchangers, and medical devices.
Copper machining is challenging due to its softness, which makes it prone to rapid tool wear. Additionally, its high thermal conductivity means that heat builds up quickly during the machining process, which can distort the material. Despite these challenges, CNC machining of copper remains essential for producing high-performance, durable parts that meet industry standards.
2. Understanding Copper’s Properties for CNC Machining
Copper is one of the most versatile metals used in CNC machining, but it also presents certain challenges. One of the primary characteristics of copper is its softness compared to materials like steel, which makes it more prone to tool wear. As a result, using the right tools and parameters is crucial for achieving optimal results.
Another key feature of copper is its excellent thermal conductivity, which allows it to dissipate heat quickly. This is beneficial in applications where heat dissipation is important, such as in electronic components. However, during the machining process, the high thermal conductivity can lead to excessive heat buildup, which may cause thermal distortion or part warping if not properly managed. As a result, precise cooling techniques are essential during machining to ensure that heat is effectively dissipated and the part remains intact.
Copper’s malleability also means that it can be easily shaped and formed, making it ideal for parts that require intricate designs. However, its softness requires adjustments in cutting tools, speeds, and feeds to avoid deforming the material during machining. Understanding these properties and how they affect the machining process is the key to achieving high-quality, durable copper components.
3. Choosing the Right Copper Alloy for Your Project
When machining copper, choosing the right alloy is crucial for ensuring both performance and machinability. While pure copper is commonly used in various applications, it is often alloyed with other metals like tin, zinc, and nickel to enhance its properties for specific use cases. The choice of alloy will depend on factors such as the required strength, corrosion resistance, and conductivity for the final product.
For example, brass, an alloy of copper and zinc, is often used for applications requiring a combination of strength and corrosion resistance, making it ideal for outdoor and marine environments. Bronze, another copper alloy, offers enhanced strength and wear resistance, making it suitable for applications in heavy machinery and automotive components. Each alloy will behave differently during the machining process, with varying degrees of hardness, thermal conductivity, and ease of cutting.
Pure copper is still widely used for applications where high electrical and thermal conductivity is paramount, such as in electrical wiring and heat exchangers. However, it is softer and more prone to wear, which can increase tooling costs over time. The right alloy choice depends on the specific needs of the part and the environment in which it will be used, which is why it’s essential to understand the characteristics of each copper alloy before starting the machining process.
4. Essential CNC Machining Techniques for Copper
CNC machining copper involves a variety of techniques to ensure that the material is cut, shaped, and finished correctly. The most common methods for machining copper include milling, turning, drilling, and grinding. Each technique requires specific parameters to ensure the best results while maintaining tool life and minimizing material distortion.
মিলিং is the most commonly used method for machining copper parts. This technique involves using a rotating cutting tool to remove material from the workpiece. Since copper is a soft material, it requires slower speeds and lower feed rates than harder metals to avoid excessive tool wear. It’s important to use carbide or high-speed steel (HSS) tools with the correct geometry to achieve clean, precise cuts.
বাঁক is another key technique used for machining copper. This process involves rotating the workpiece while a stationary tool removes material from the surface. For copper, it’s essential to use tools with sharp edges to prevent material deformation. Copper’s softness requires turning at a lower speed with high feed rates to prevent the formation of burrs and achieve a smooth finish.
তুরপুন copper parts requires careful attention to the speed and feed rates to prevent the material from tearing or distorting. It’s essential to use high-quality drill bits that can withstand the soft nature of copper without causing significant wear.
নাকাল is used for finishing copper parts and achieving a smooth surface. However, since copper is prone to heat buildup, it’s essential to use proper cooling techniques during grinding to avoid thermal distortion.
5. Best Cutting Tools for Copper CNC Machining
Selecting the right cutting tools is one of the most important steps in achieving optimal results when CNC machining copper. Copper’s soft and malleable nature means that standard cutting tools may not perform well, leading to faster wear and less precise results. For copper machining, it’s important to use tools made of materials that can withstand the material’s properties without excessive wear or overheating.
Carbide tools are often the best choice for copper machining, as they are harder and more durable than high-speed steel (HSS) tools. They are particularly effective when machining larger quantities of copper parts, as they maintain their sharpness for longer and are more resistant to heat. Coated carbide tools, such as those with a titanium nitride (TiN) coating, can further extend tool life by reducing friction and heat buildup.
HSS tools are another option, especially for small runs or intricate parts. They tend to be less expensive than carbide tools but may wear out faster when cutting copper. It’s also essential to use tools with the correct geometry, such as those with positive rake angles, to minimize cutting forces and improve the quality of the finished part.
Coating the cutting tools with materials like diamond or ceramic can also help improve performance by increasing tool hardness and reducing wear. This is particularly useful when machining tough copper alloys or when high-speed machining is required.
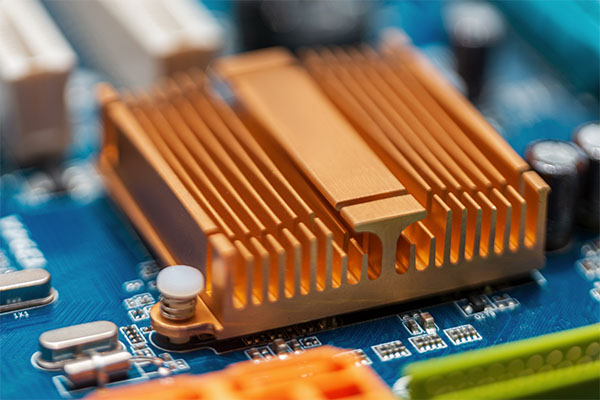
6. Optimal Machining Speeds and Feeds for Copper
One of the most critical factors in CNC machining copper is selecting the right speeds and feeds. Copper’s softness means that cutting speeds can be higher than for harder materials, but the feed rates must be carefully adjusted to avoid overloading the tool. Choosing the right balance between speed and feed rate is crucial for achieving a smooth finish while maintaining tool life.
In general, higher cutting speeds are recommended when machining copper, but feed rates should be kept moderate to prevent excessive tool wear. If the feed rate is too high, it can cause the copper to overheat and lead to poor surface finishes. On the other hand, if the cutting speed is too slow, it can increase machining time and decrease productivity.
For milling, the recommended cutting speeds for copper can range from 150 to 500 surface feet per minute (SFM), depending on the tool material and geometry. For turning, a typical cutting speed is between 300 and 800 SFM. It’s also important to adjust the depth of cut to ensure that the tool isn’t overloaded, as this can result in poor cutting performance and excessive heat generation.
Using high-quality coolant and proper tool coatings can also help achieve the optimal balance of speed and feed, ensuring smooth cuts and preventing heat buildup during machining.
7. Preventing Heat Build-up During Copper CNC Machining
Heat is one of the biggest challenges when CNC machining copper, as the material’s high thermal conductivity causes it to heat up quickly during the cutting process. If heat is not properly managed, it can cause thermal distortion, part warping, and reduced surface quality. Therefore, implementing effective cooling strategies is essential to prevent overheating and achieve high-quality results.
Using the right cooling method is critical when machining copper. Liquid coolant is often the preferred choice for maintaining a stable temperature during machining, as it helps dissipate heat away from the workpiece. Coolants that are specifically formulated for copper machining can help prevent overheating, tool wear, and part distortion.
এয়ার কুলিং is another option for copper CNC machining, particularly in high-speed operations. It’s less effective than liquid cooling, but when used in conjunction with proper tool geometry and cutting parameters, it can still help control temperatures during machining.
In addition to using the right coolant, it’s essential to use correct feed rates এবং cutting speeds to prevent excessive heat buildup. Slower cutting speeds and moderate feed rates allow heat to be dissipated gradually, reducing the risk of thermal distortion and maintaining the quality of the finished part.
8. Dealing with Chip Formation and Removal in Copper
Chip formation and removal are crucial factors in copper CNC machining. Copper tends to produce short, sticky chips that can easily clog tools or cause material build-up on the workpiece. Effective chip removal is necessary to maintain a clean working environment and avoid damage to the tool or part.
To deal with chip formation, it’s essential to use tools with the proper geometry and cutting angles to minimize chip formation. Tools with positive rake angles help ensure smooth chip formation and reduce the risk of chip welding, which can result in tool wear and poor surface finishes.
Coolant plays a key role in chip removal by helping flush away chips from the cutting zone. High-pressure coolant systems are particularly effective in copper machining, as they help clear chips from the cutting area and prevent them from interfering with the machining process. Additionally, maintaining proper cutting speeds and feeds ensures that chips are not overly compressed and can be effectively removed.
Proper chip management is also essential, as leaving chips on the workpiece can cause scratching and surface defects. Using a chip conveyor or air blast system can help remove chips and keep the machining process smooth and efficient.
9. How to Achieve Precision and Tight Tolerances in Copper CNC Machining
Achieving precision and tight tolerances in copper machining can be difficult due to the material’s softness and thermal conductivity. However, with the right techniques, it’s possible to produce highly accurate parts that meet strict dimensional requirements.
সরঞ্জাম পরিধান is one of the main factors that can affect precision during machining. Copper is a soft material, and without proper care, tools can wear quickly, leading to dimensional inaccuracies. To maintain precision, it’s essential to regularly monitor tool condition and replace worn tools as necessary.
Machine calibration is also crucial to ensure that CNC machines are working within the required tolerance limits. Ensuring that the machine’s axes are correctly aligned and that the cutting tool is positioned accurately can help achieve the desired tolerances. Additionally, using high-quality measuring instruments during the setup and inspection processes ensures that parts meet the required specifications.
To further improve precision, it’s important to select the right machining parameters, such as optimal cutting speeds, feeds, and depth of cuts. By adjusting these factors carefully, it’s possible to minimize material deformation and achieve the desired results without compromising part quality.
10. Finishing Techniques for Copper Parts
Once the primary machining operations are completed, the finishing process is essential for achieving the desired surface quality and ensuring the parts meet industry standards. Copper parts often require polishing and deburring to remove sharp edges, burrs, or excess material and achieve a smooth, high-quality finish.
Polishing copper parts involves using abrasive materials and polishing compounds to create a reflective surface. This process helps improve the appearance of copper parts, making them more aesthetically pleasing and increasing their corrosion resistance. Polishing is particularly important in industries like electronics, where the appearance of copper parts can impact product quality.
Deburring is another critical finishing step that removes any sharp edges or burrs left after machining. Burrs can affect the performance of copper parts, especially in applications like electrical connectors or heat exchangers. Using abrasive brushes, grinding wheels, or deburring tools helps ensure that parts are free of burrs and ready for further processing.
In some cases, electroplating অথবা anodizing can be used to further improve the appearance and performance of copper parts. Electroplating involves coating the copper part with a thin layer of another metal, such as nickel or gold, to enhance its corrosion resistance and conductivity. Anodizing can also be used to protect the surface of copper parts, although this process is less common with copper than with aluminum.
11. Common Challenges in Copper CNC Machining
Despite its widespread use, copper CNC machining comes with a variety of challenges that manufacturers must navigate to achieve optimal results. সরঞ্জাম পরিধান is one of the most significant issues when machining copper, as the material’s softness causes rapid tool degradation. To counteract this, it’s essential to use high-quality tools, adjust cutting speeds, and replace tools regularly to maintain machining precision.
Another challenge is material distortion, which occurs due to copper’s high thermal conductivity. Heat buildup during the machining process can cause the material to expand, leading to part warping or dimensional inaccuracies. Proper cooling techniques, slower feed rates, and optimized cutting speeds are necessary to minimize the risk of material distortion.
Finally, surface roughness is another common issue that arises when machining copper. Without careful control of cutting parameters, copper parts can exhibit unwanted surface imperfections like scratches or uneven finishes. Using appropriate cutting tools, proper feeds, and speeds, and employing effective finishing techniques can help overcome these challenges and achieve smooth, high-quality parts.
12. Safety Precautions When Machining Copper
Copper machining can pose certain risks to operators and equipment, making safety an important consideration. The high cutting speeds and heat generated during the machining process increase the risk of burns, flying debris, and tool breakage. Wearing personal protective equipment (PPE), such as gloves, goggles, and face shields, is essential to protect against injuries.
It’s also important to ensure that the machinery is in good condition and properly maintained. Regular checks and maintenance help prevent accidents caused by machine malfunctions. In addition, operators should be trained to understand the specific risks of copper machining, such as handling sharp tools and managing the cooling systems.
Another safety consideration involves the use of coolants. Proper disposal and handling of coolants are necessary to prevent contamination and ensure safe operating conditions. Using high-quality coolants designed for copper machining reduces the risks of accidents caused by overheating or improper fluid management.
13. Cost Considerations in Copper CNC Machining
Cost is an important factor in any manufacturing process, and CNC machining of copper is no exception. Several factors influence the overall cost of machining copper, including material costs, tool wear, and machine time. Copper is a relatively expensive material, and when combined with the cost of high-quality tools, the price of machining copper can add up quickly.
সরঞ্জাম পরিধান is one of the biggest cost factors when machining copper, as the material’s softness leads to rapid tool degradation. To offset this, it’s important to invest in durable cutting tools and regularly monitor their condition. High-speed machining and the use of high-quality coolants can also help reduce tool wear and improve machining efficiency.
যন্ত্রের সময় is another significant cost factor. Faster cutting speeds and optimized feed rates can help reduce production time and increase overall efficiency. However, it’s essential to balance speed with quality, as rushing the process can lead to poor finishes or defective parts. By carefully managing time and resources, manufacturers can reduce costs while still maintaining high-quality results.
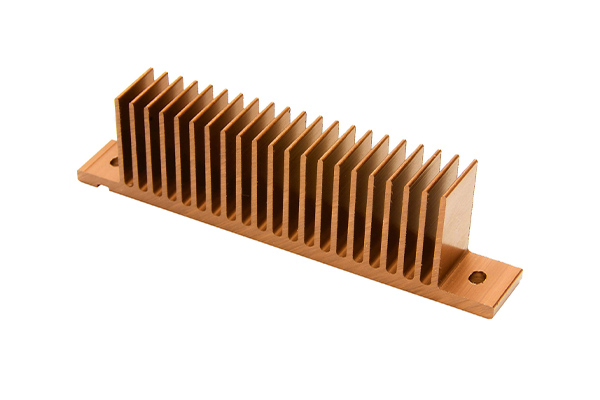
14. Copper CNC Machining in Different Industries
Copper CNC machining is used in a wide range of industries where its unique properties are required. In the automotive industry, copper is commonly used for electrical components, heat exchangers, and connectors. Its excellent conductivity and corrosion resistance make it ideal for automotive applications that require reliable performance and durability.
মধ্যে aerospace sector, copper is used in electrical systems, avionics, and heat exchangers. Its lightweight nature and high thermal conductivity are particularly beneficial in aerospace applications that require efficient heat dissipation and electrical reliability.
দ্য electronics industry also relies heavily on copper machining for components like circuit boards, connectors, and heat sinks. Copper’s high electrical conductivity makes it the material of choice for many electronic devices, ensuring efficient performance and heat management.
Finally, medical devices often require copper machining for components such as surgical instruments, connectors, and diagnostic equipment. Copper’s antimicrobial properties and resistance to corrosion make it a preferred choice for medical applications that require high-performance, hygienic materials.
15. The Future of Copper CNC Machining
The future of copper CNC machining is shaped by advancements in technology, automation, and sustainability. As manufacturers continue to seek more efficient and cost-effective methods for machining copper, automated machining systems এবং robotics are playing an increasing role in the process. Automation helps improve precision, reduce human error, and increase production speed.
Sustainability is also becoming a significant factor in copper machining, with a growing emphasis on using eco-friendly coolants and reducing material waste. Manufacturers are exploring ways to improve the efficiency of copper machining processes, such as using recyclable materials এবং energy-efficient machinery, to minimize the environmental impact of their operations.
Additionally, advances in machining technology এবং tool coatings are making it possible to achieve higher precision and longer tool life. As these technologies continue to evolve, the future of copper CNC machining looks promising, with greater efficiency, accuracy, and sustainability on the horizon.
উপসংহার
CNC machining copper presents unique challenges, but with the right techniques and tools, manufacturers can produce high-quality parts that meet the demands of various industries. By understanding copper’s properties, selecting the right alloy, and implementing the correct machining methods, it’s possible to achieve optimal results in copper machining. Start applying these strategies to your copper machining projects today, and watch your production efficiency and part quality improve.
প্রায়শই জিজ্ঞাসিত প্রশ্ন বিভাগ
- What is the best copper alloy for CNC machining?
Choosing the best copper alloy depends on the specific application. For electrical applications, pure copper is ideal, while alloys like brass and bronze are better for structural components due to their enhanced strength and durability. - How can I reduce tool wear when machining copper?
To reduce tool wear, it’s essential to use high-quality cutting tools, such as carbide tools, and maintain proper feed rates and cutting speeds. Regular tool inspection and replacement can also help extend tool life. - Why does copper need cooling during CNC machining?
Copper’s high thermal conductivity causes it to heat up quickly during machining, leading to part distortion and tool wear. Using coolants helps dissipate heat and maintain part quality. - How do I avoid surface roughness in copper parts?
To avoid surface roughness, use the correct cutting parameters, including speeds, feeds, and depths of cut. Additionally, employing proper finishing techniques, such as polishing and grinding, can help achieve smooth surfaces. - Can I use the same cutting tools for copper as I do for steel?
Copper requires different cutting tools than steel due to its softness. Carbide tools with the appropriate geometry are usually the best choice for copper, as they maintain sharpness longer than high-speed steel tools. - What are some common mistakes when CNC machining copper?
Common mistakes include using incorrect cutting speeds, improper tool selection, and inadequate cooling. These issues can lead to tool wear, part distortion, and poor surface finishes. Regular monitoring and adjustment can help avoid these problems.