ভূমিকা
When designing custom aluminum parts for CNC machining, understanding the material’s unique properties and the machining process is crucial. Aluminum is a highly versatile material, making it a go-to choice for various industries such as automotive, aerospace, medical, and electronics. However, designing custom parts from aluminum requires careful attention to detail, as the characteristics of aluminum and the capabilities of CNC machines can significantly impact the final product. চুক্তিটি এখানে। – to ensure your custom aluminum parts meet performance and quality standards, a thoughtful design approach is necessary. In this article, we’ll explore essential design tips for CNC machining that will help you achieve precision and efficiency in your custom aluminum parts.
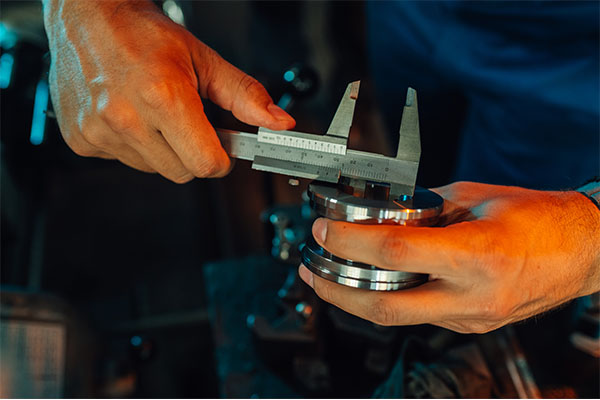
What Makes Aluminum a Popular Material for CNC Machining?
Aluminum has become one of the most commonly used metals in CNC machining due to its exceptional properties. Not only is aluminum lightweight, but it also boasts impressive strength-to-weight ratios, making it ideal for applications where weight reduction is crucial. Additionally, aluminum has excellent corrosion resistance, making it durable for outdoor and industrial environments. The material is also highly machinable, allowing for intricate designs to be produced with relative ease.
Bucket Brigade: তুমি হয়তো ভাবছো, why is aluminum so widely used in CNC machining? The answer lies in its flexibility and ease of processing. Common alloys such as 6061 and 7075 are popular choices for CNC machining, offering a balance of strength and lightweight characteristics. These alloys are not only easy to machine but also provide the necessary durability for a wide range of applications. Industries like aerospace, automotive, and consumer electronics rely on aluminum for its combination of performance and cost-effectiveness. By understanding the material’s versatility, you can better select the right aluminum for your CNC machining project.
Key Considerations When Designing Custom Aluminum Parts
Designing custom aluminum parts requires a detailed approach, as several factors influence the final outcome. One of the most important considerations is the selection of the appropriate aluminum alloy. Depending on the specific requirements of the part, such as its strength, weight, and resistance to corrosion, the right alloy can make a significant difference. For instance, 6061 aluminum is widely used for structural applications due to its good balance of strength, corrosion resistance, and weldability. In contrast, 7075 is stronger and often used in aerospace applications, although it is less resistant to corrosion and more difficult to machine.
Bucket Brigade: চুক্তিটি এখানে। – selecting the right alloy is just one part of the equation. It’s also essential to consider the specific application and performance needs of the custom aluminum part. Tolerances, surface finishes, and the final function of the part should also be factored into the design process. For instance, parts subjected to high-stress conditions must be designed with reinforced features to handle the load. Additionally, understanding the CNC machining capabilities and constraints will help you avoid unnecessary complexities that could increase costs or lead to production delays.
Design for CNC Machining: What You Need to Know
When designing parts for CNC machining, understanding the process is crucial. CNC machines are highly precise, but they have certain limitations. For instance, designing overly intricate or complex geometries can be difficult to machine and may lead to increased costs and production time. To optimize a design for CNC machining, it’s essential to consider factors like tool access, material removal rates, and machine capabilities. Avoid designs with sharp internal corners, as these can lead to tool wear and machining errors. Instead, opt for rounded edges and simple shapes that are easier for the CNC machine to produce efficiently.
Bucket Brigade: তুমি হয়তো ভাবছো, how can you ensure your design is CNC-friendly? One of the best strategies is to simplify the design without sacrificing its functionality. Incorporating features like draft angles, which allow the tool to easily exit the material, can help speed up the machining process. Additionally, keeping wall thicknesses consistent and avoiding undercuts will reduce the likelihood of defects and improve the overall quality of the part.
The Role of CAD Software in Designing Custom Aluminum Parts
Computer-Aided Design (CAD) software plays an integral role in designing custom aluminum parts for CNC machining. CAD allows engineers and designers to create precise, detailed models of the parts before they are physically produced. Popular CAD software like AutoCAD, SolidWorks, and Fusion 360 provides tools for simulating the machining process, enabling designers to identify potential issues before manufacturing begins. CAD software also allows for easy adjustments to the design, ensuring that the final product meets both functional and aesthetic requirements.
Bucket Brigade: So, how do you get started with CAD? If you’re new to CAD software, start by familiarizing yourself with basic design principles such as dimensioning, tolerances, and material properties. With practice, you’ll be able to design complex custom aluminum parts with ease. CAD software not only helps streamline the design process but also enables collaboration between designers and CNC machinists to optimize designs for manufacturing.
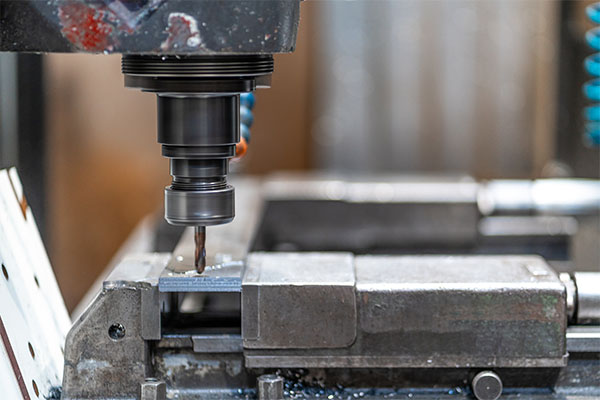
How Tolerances Impact the Design of Custom Aluminum Parts
Tolerances refer to the acceptable variation in dimensions and geometric characteristics of a part. In CNC machining, tight tolerances are essential for ensuring that the part fits and functions as intended. However, it’s important to strike a balance between precision and cost. Parts designed with very tight tolerances may require more time and effort to machine, increasing production costs. On the other hand, relaxing tolerances can lead to easier and cheaper production but might sacrifice performance in certain applications.
Bucket Brigade: Don’t make these common mistakes when setting your tolerances. One of the most critical aspects of designing for CNC machining is understanding which tolerances are necessary for the part’s performance and which ones can be relaxed. For example, a part that is purely decorative may not require tight dimensional tolerances, while a part used in a high-performance engine will demand more precise measurements. Work closely with your machinist to determine the best tolerance specifications based on the functionality and criticality of the part.
Optimizing Aluminum Part Design for Cost Efficiency
When designing custom aluminum parts, cost efficiency is always a key consideration. The complexity of a design directly impacts the machining time and, consequently, the cost. By simplifying your design and eliminating unnecessary features, you can reduce the overall production time and minimize material waste. Additionally, selecting the right aluminum alloy for your specific application can also affect the cost. Some alloys are more expensive due to their superior mechanical properties, while others are more affordable but may not meet the performance requirements of your part.
Bucket Brigade: Here’s how you can save money while still achieving a high-quality result. Start by evaluating the essential features of your part and determining if any can be simplified or eliminated. For example, removing decorative elements that don’t affect functionality or reducing the number of complex internal features can lead to significant cost savings. Also, consider using off-the-shelf aluminum alloys when possible, as these tend to be more affordable than specialized alloys.
Understanding Aluminum Part Finishing Options
Finishing plays a critical role in the overall quality and appearance of custom aluminum parts. Various finishing techniques, such as anodizing, polishing, and powder coating, can enhance the durability, corrosion resistance, and aesthetic appeal of your parts. Anodizing is particularly popular for aluminum parts as it creates a protective oxide layer that improves corrosion resistance while also offering a decorative finish. Polishing can give parts a high-gloss, shiny surface, while powder coating provides a durable, colored finish ideal for outdoor applications.
Bucket Brigade: You’ll be amazed at the difference a good finish can make. Choosing the right finishing technique depends on the intended use of the part. For example, anodizing is ideal for parts that will be exposed to harsh environments, while polishing is best for parts that need a sleek, polished appearance. Keep in mind that certain finishes may require additional machining steps, so be sure to factor this into your design and budget.
Designing for Strength and Durability in Aluminum Parts
While aluminum is inherently lightweight, it can also be designed to be extremely strong and durable. When designing for strength, it’s important to consider factors such as wall thickness, material choice, and the use of reinforcements. For parts that will be subjected to high stress or heavy loads, you may need to incorporate thicker walls or additional ribs and gussets to prevent deformation. Additionally, the design should account for stress concentration points, where cracks or failure are more likely to occur.
Bucket Brigade: তুমি হয়তো ভাবছো, how do you balance strength with weight? The key lies in understanding the forces your part will face during its service life and designing accordingly. For example, a structural component in an aerospace application may require extra reinforcement, while a consumer electronics part may focus more on lightweight and aesthetic features. Careful analysis and testing will ensure your part has the strength and durability needed without adding unnecessary weight.
How CNC Machine Settings Affect Aluminum Part Quality
CNC machine settings play a vital role in the final quality of your custom aluminum parts. Factors like spindle speed, feed rate, depth of cut, and coolant usage can significantly influence the machining process. For aluminum parts, it’s important to use the correct settings to achieve smooth surfaces and avoid issues such as burr formation, excessive tool wear, or material warping. By fine-tuning the machine settings, you can achieve a balance between speed and precision while maintaining high-quality standards.
Bucket Brigade: Are you using the right machine settings? Optimizing CNC machine settings is a critical step in producing high-quality aluminum parts. Collaborating closely with your machinist and understanding the specific requirements of your part will help ensure that the machine settings are properly adjusted for optimal results.
Common Design Mistakes to Avoid in Custom Aluminum Parts
Designing custom aluminum parts can be challenging, and several common mistakes can lead to production delays, increased costs, or quality issues. One of the most frequent mistakes is designing overly complex parts with intricate features that are difficult or costly to machine. Another common error is ignoring the material properties of aluminum, such as its tendency to expand when heated, which can lead to warping or deformation. Failing to properly communicate tolerances and requirements to the machinist can also result in parts that do not meet specifications.
Bucket Brigade: Don’t make these mistakes when designing custom aluminum parts. Keep your designs as simple as possible without compromising functionality. Work closely with your machinist to ensure that all critical dimensions and tolerances are clearly defined. And always account for material properties to avoid issues during machining and final production.
Quality Control in CNC Machining of Custom Aluminum Parts
Ensuring quality control throughout the CNC machining process is crucial for achieving precision and reliability in your custom aluminum parts. Several methods can be employed to inspect and test parts, including visual inspection, dimensional measurement using tools like calipers or CMMs (Coordinate Measuring Machines), and mechanical testing for strength and durability. Regular quality checks during production will help catch any defects early, preventing costly rework or product failure later on.
Bucket Brigade: Let’s talk about the checks and balances that guarantee top-quality parts. Quality control ensures that your custom aluminum parts meet all required specifications and performance standards. Working with experienced machinists and using advanced inspection equipment will help ensure that your parts are both functional and defect-free.
Prototyping Custom Aluminum Parts for Testing
Before proceeding with full-scale production, prototyping is an essential step in testing and refining the design of custom aluminum parts. Prototypes allow designers to evaluate the fit, form, and function of a part in real-world conditions, identifying any potential issues that could arise during production. Various prototyping methods, including 3D printing and small-batch CNC machining, are available to quickly produce functional models for testing and evaluation.
Bucket Brigade: Rushing to full production without prototyping can lead to costly errors. Prototyping provides valuable insight into how the part will perform under actual conditions and allows you to make necessary adjustments before committing to larger-scale production. It’s an essential step in ensuring that your design meets all performance and quality standards.
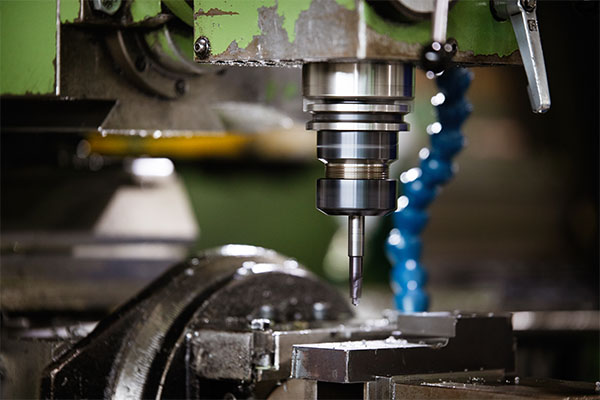
Collaborating with a CNC Machining Service Provider
When designing custom aluminum parts, collaborating with a reputable CNC machining service provider is essential. A skilled machinist will work closely with you to understand your design requirements and help optimize the part for CNC machining. It’s important to communicate your expectations clearly and provide all relevant details, such as tolerances, material specifications, and finishing requirements, to ensure that the final product meets your standards. Additionally, a CNC provider with OEM capabilities can offer added value by helping you scale production as needed.
Bucket Brigade: Here’s what you need to know before you partner with a CNC manufacturer. Choosing the right service provider is key to the success of your project. Make sure to review their track record, capabilities, and customer reviews to ensure that they can meet your specific design and manufacturing needs.
Conclusion: Final Tips for Designing Custom Aluminum Parts for CNC Machining
Designing custom aluminum parts for CNC machining requires a comprehensive understanding of material properties, machining techniques, and design principles. By selecting the right alloy, optimizing your design for machinability, and considering factors like tolerances and finishing, you can create high-quality, cost-effective parts that meet your specific requirements. Always remember that collaboration with an experienced CNC machinist is essential to ensure that your designs are manufacturable and meet your desired performance standards.
Call to Action: Ready to start designing your custom aluminum parts? Get in touch with a reliable CNC machining service provider today and take your project to the next level.
প্রায়শই জিজ্ঞাসিত প্রশ্ন বিভাগ
What are the most commonly used aluminum alloys in CNC machining?
The most commonly used aluminum alloys for CNC machining are 6061, 7075, and 2024. These alloys are known for their excellent machinability, strength, and durability. 6061 is a versatile alloy suitable for a wide range of applications, while 7075 is stronger and often used in aerospace and military applications. 2024, while not as commonly used as 6061, offers high strength and is ideal for structural components.
How do I choose the right CNC machining provider for custom aluminum parts?
When selecting a CNC machining provider, consider their experience with aluminum machining, their capability to meet your specific design requirements, and their reputation for quality and reliability. Ensure that they offer the necessary services, including material sourcing, prototyping, and finishing, to support your project. A provider with OEM capabilities can also help you scale production as needed.
What are the benefits of prototyping aluminum parts before full production?
Prototyping helps you test the fit, form, and function of your design before committing to full production. It allows you to identify any potential issues, such as machining difficulties or design flaws, and make necessary adjustments to avoid costly errors in the final product. Prototyping also ensures that the final part meets your performance and quality standards.
Can custom aluminum parts be machined with high precision?
Yes, CNC machining allows for high precision and accuracy when producing custom aluminum parts. The key to achieving tight tolerances and high-quality results is designing with manufacturability in mind and working closely with your CNC machinist to set the appropriate machine parameters.
What is anodizing, and why is it commonly used for aluminum parts?
Anodizing is a finishing process that creates a protective oxide layer on the surface of aluminum, enhancing its corrosion resistance and aesthetic appearance. It also allows for coloring the aluminum, making it an ideal choice for parts that will be exposed to harsh environments or for those that require a durable and attractive finish.