Einführung
CNC milling is an essential process in modern manufacturing, providing precision and accuracy across various industries. Whether you’re creating parts for automobiles, electronics, or medical devices, achieving the highest standards in CNC milling is crucial. The challenge many manufacturers face is ensuring that the parts they produce meet exact specifications every time. But with the right tools, techniques, and practices in place, you can significantly improve the precision and accuracy of your CNC milling operations. In this article, we’ll explore several tips and strategies to help you master CNC milling, avoid common mistakes, and produce high-quality parts consistently.
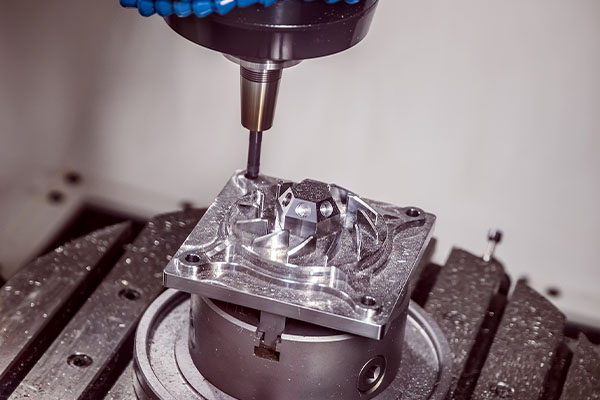
1. Key Concepts in CNC Milling
What Are CNC Milling Parts?
CNC milling parts are components that have been fabricated using a CNC (Computer Numerical Control) milling machine. These machines utilize rotary cutting tools to remove material from a workpiece to achieve the desired shape, size, and finish. CNC milling allows for highly intricate and precise cuts that would be impossible to achieve using manual methods. Parts produced through CNC milling are used across a wide range of industries, including automotive, aerospace, medical devices, consumer electronics, and more. The quality of these parts directly impacts the performance of the final product, which is why precision is crucial.
Precision vs. Accuracy: What’s the Difference?
Precision and accuracy are two critical terms often used in the context of CNC milling. However, they are not synonymous. Präzision refers to the ability of a CNC milling machine to produce the same result consistently, even if it isn’t necessarily correct. For example, a machine might produce a part that is slightly off-spec but identical every time. Accuracy, on the other hand, refers to how closely the part matches the intended dimensions or specifications. Ideally, CNC milling operations should achieve both high precision and high accuracy. However, many manufacturers focus on one more than the other, depending on the part and its application.
2. The CNC Milling Process Explained
How Does CNC Milling Work?
CNC milling involves using a rotating cutting tool to remove material from a workpiece, often a solid block of metal, plastic, or another material. The workpiece is mounted onto the machine, and precise movements are controlled by a computer program (often written in G-code). The cutting tool can move in various directions, typically along the X, Y, and Z axes, to create complex shapes with high accuracy. The key to effective CNC milling lies in proper machine setup, the choice of tools, and the right cutting parameters. Once the program is set, the machine can operate autonomously, producing parts with minimal human intervention.
Types of CNC Milling Machines
CNC milling machines come in various configurations, with the most common being vertical Und horizontal machines. Vertical milling machines have a spindle that moves vertically, allowing for the cutting tool to be positioned above the workpiece. These are ideal for operations like drilling and surface finishing. Horizontal milling machines, on the other hand, have a horizontal spindle that allows for more complex cutting, particularly when larger or deeper cuts are required. The choice between these types of machines depends on the part being produced and the desired outcome. For parts requiring high precision, choosing the right machine setup is essential to achieving accurate results.
3. Factors Affecting Precision in CNC Milling
Machine Calibration and Setup
Proper machine calibration is fundamental to achieving high precision in CNC milling. If the machine is not calibrated correctly, even the most sophisticated tools and software won’t guarantee accurate results. Calibration involves aligning the CNC machine’s axes, ensuring that the tool offsets are correctly set, and verifying that all parts of the machine are working within specified tolerances. Calibration should be done regularly and before each production run to ensure that your parts meet the exact specifications. Bucket Brigades like “Here’s the deal” and “You might be wondering” will help keep readers engaged when you discuss the importance of consistent calibration.
Tool Selection and Maintenance
The tools used in CNC milling have a significant impact on the precision of the finished parts. Choosing the right tool for the material being cut is crucial. For example, harder materials such as stainless steel require more robust cutting tools, while softer materials like aluminum may allow for faster cutting speeds. Regelmäßige Wartung is equally important. Worn-out tools can lead to inaccurate cuts, affecting the quality of the parts. Ensuring that tools are sharp, clean, and correctly installed helps maintain consistency throughout the machining process. Bucket Brigades such as “Let’s take a closer look at…” help guide the reader through the details of tool maintenance, reinforcing its importance in achieving accuracy.
4. The Role of Materials in CNC Milling Precision
How Material Choice Affects Accuracy
The material you choose for CNC milling plays a significant role in determining the final part’s accuracy. Materials vary in hardness, density, and thermal properties, which can affect how they react during the cutting process. Harder materials like titanium and tool steel can be more challenging to mill, requiring specialized tools and slower feed rates. On the other hand, softer materials like aluminum and plastics are easier to machine but may not achieve the same level of durability. Bucket Brigades like “It’s important to understand” and “This is where” emphasize the need to select the right material to achieve high-quality, accurate results.
Dealing with Material Variations
Material inconsistencies can introduce errors into the CNC milling process. Variations in material thickness, density, or even grain structure can lead to parts that don’t meet the desired specifications. Handling these variations involves choosing high-quality materials from reputable suppliers, inspecting materials for defects before use, and adjusting the machine settings to compensate for material differences. Additionally, manufacturers should regularly monitor material properties during the milling process to ensure that the part remains within tolerance. Bucket Brigades like “Let’s be real here” can engage readers while addressing how material inconsistencies can be avoided or minimized.
5. CNC Milling Techniques for Improved Accuracy
Utilizing Multi-Axis CNC Milling for Precision
Multi-axis CNC milling machines have revolutionized the ability to produce complex, high-precision parts. While traditional 3-axis machines only move the cutting tool along the X, Y, and Z axes, multi-axis machines can also rotate the workpiece, enabling cuts from multiple angles. This results in greater flexibility and the ability to machine parts with more intricate geometries, which is ideal for industries such as aerospace and medical device manufacturing. Bucket Brigades such as “But wait, there’s more” and “This is a game-changer” can make the explanation of multi-axis machines more engaging for readers.
Reducing Tolerances for Tight Fitting Parts
Achieving tight tolerances is crucial for parts that need to fit together precisely. Tight tolerances refer to the allowable variation in a part’s dimensions, and reducing these tolerances is vital for the quality and functionality of the final product. Bucket Brigades like “Here’s the catch” can help highlight techniques such as using finer cutting tools, slower feed rates, and more advanced CNC programming to minimize tolerance variations. These techniques are essential when manufacturing high-performance parts that require a perfect fit, such as engine components or surgical devices.
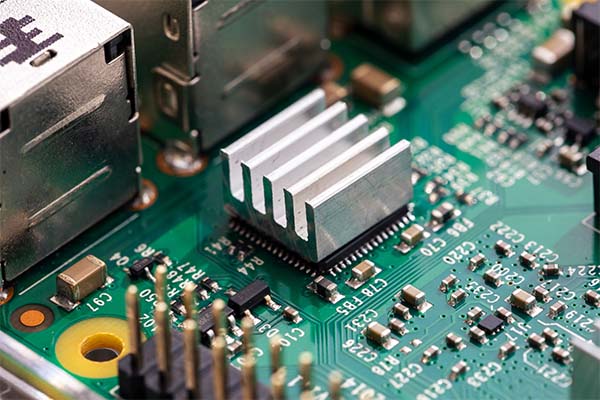
6. Common CNC Milling Mistakes and How to Avoid Them
Misalignment Issues and Their Impact on Accuracy
Misalignment is one of the most common mistakes in CNC milling that can lead to inaccurate parts. Misalignment can occur during machine setup, when the workpiece is not mounted correctly, or when the tool is improperly calibrated. The result is often parts that are out of spec and require reworking. To avoid this, always ensure that the machine and workpiece are properly aligned before starting the milling process. Bucket Brigades such as “This is how you fix it” and “Let me explain” can help guide the reader through simple steps to prevent misalignment.
Tool Wear and Its Effects on Precision
Tool wear is an inevitable part of CNC milling, but when not managed correctly, it can lead to significant inaccuracies. As tools wear down, they become less effective at cutting, leading to parts with rough surfaces, incorrect dimensions, or excessive tolerance variations. Regular tool inspection and timely replacement are essential in ensuring the parts continue to meet the required specifications. Bucket Brigades like “You might be wondering” and “So what can we do about it?” help engage the reader as they learn how to manage tool wear effectively to maintain accuracy.
7. Using CNC Milling for Complex Parts and Designs
How CNC Milling Handles Complex Geometries
CNC milling is ideal for creating parts with complex geometries that would be impossible or too time-consuming to produce with traditional methods. The ability to program precise movements of the cutting tool allows CNC machines to handle intricate designs, from gears to turbine blades. CNC milling can even handle parts with multiple layers or internal features, such as cooling channels or cavities. Bucket Brigades like “Here’s where the magic happens” help break down how complex parts are created with high accuracy using CNC milling.
Working with Tight Tolerances
Tight tolerances are essential for many industries, including aerospace and medical device manufacturing. CNC milling can easily achieve tight tolerances when the right tools and techniques are used. The combination of high-quality materials, regular machine maintenance, and careful programming ensures that parts are produced with minimal variation. Bucket Brigades like “This is where it gets tricky” highlight the challenges of maintaining tight tolerances and provide actionable tips to achieve high precision in CNC milling.
8. Importance of Software and Programming in CNC Milling
The Role of CAD/CAM Software in Precision
CAD (Computer-Aided Design) and CAM (Computer-Aided Manufacturing) software play a critical role in ensuring CNC milling parts are precise. CAD software allows engineers to design parts with exact specifications, while CAM software generates the machine code that directs the CNC machine to create those parts. Both programs must be synchronized for accurate results. Bucket Brigades like “You’re probably wondering” and “Let’s dive into it” can engage readers while explaining the importance of software in maintaining accuracy during the CNC milling process.
Tips for Effective CNC Programming
Effective programming is essential to ensure that a CNC milling machine produces parts within the desired tolerances. Even a small error in the G-code or toolpath can result in a defective part. Proper programming requires an understanding of machine capabilities, cutting parameters, and the material being worked with. Bucket Brigades such as “Let’s break it down” and “Now here’s the trick” help explain programming best practices that contribute to milling precision.
9. Quality Control in CNC Milling
Inspection Methods for CNC Milling Parts
Quality control is a crucial aspect of CNC milling, especially when working with high-precision parts. Regular inspections during the milling process ensure that parts meet the required specifications. Common inspection methods include visual inspections, micrometer measurements, and the use of coordinate measuring machines (CMM). Bucket Brigades like “Let’s get technical” and “Here’s how it works” can keep readers engaged while explaining various inspection techniques used to check part accuracy.
Setting Up a Quality Control System
Setting up an effective quality control system involves establishing standards and procedures for checking parts at various stages of production. Regularly checking parts throughout the manufacturing process reduces the risk of defects and ensures that the final product is of the highest quality. Bucket Brigades like “This is how you do it” help guide the reader through setting up their own quality control system to improve precision in CNC milling operations.
10. Best Practices for Maximizing CNC Milling Precision
Optimizing Cutting Speeds and Feeds
Choosing the right cutting speeds and feeds is essential for maximizing CNC milling precision. Too fast or too slow feed rates can cause parts to be either too rough or imprecise. The optimal cutting speed depends on the material being milled and the type of tool used. Bucket Brigades like “Let’s talk about” and “Here’s the key” help keep readers engaged while explaining how adjusting cutting speeds and feeds can improve precision.
Temperature Control in CNC Milling
Temperature changes during milling can affect material properties, tool wear, and part accuracy. Managing temperature during the milling process ensures consistent results. Cooling systems, such as coolant jets or air mist systems, can be used to maintain the ideal temperature during cutting. Bucket Brigades such as “Why it matters” and “This is what you need to know” will help explain the impact of temperature on milling precision.
11. Troubleshooting Common CNC Milling Issues
Dealing with Over-Cutting and Under-Cutting
Over-cutting and under-cutting are common issues that can affect the precision of CNC milling. Over-cutting occurs when too much material is removed, leading to parts that are too small or not within tolerance. Under-cutting happens when not enough material is removed, resulting in parts that are oversized. Bucket Brigades like “Here’s how you fix it” guide readers through troubleshooting techniques to ensure parts are cut correctly.
Addressing Surface Finish Issues
Surface finish is another important aspect of CNC milling. A rough surface finish can lead to parts that are not suitable for their intended use, especially in industries like aerospace and medical devices. Bucket Brigades such as “This is what’s going on” help readers understand how to improve surface finishes by adjusting machining parameters and using specialized finishing tools.
12. The Future of CNC Milling Technology
Innovations in CNC Milling Machines
CNC milling technology is constantly evolving, with new innovations making machines faster, more efficient, and more precise. Bucket Brigades like “What’s next?” and “Here’s where the future lies” highlight how new developments, like AI-driven CNC machines, are transforming the industry. These innovations allow manufacturers to push the boundaries of precision and accuracy, opening up new possibilities for product design and functionality.
Emerging Trends in CNC Milling Precision
Emerging trends such as additive manufacturing integration Und smart manufacturing systems are helping improve precision in CNC milling. These trends enable manufacturers to produce even more complex parts with reduced lead times. Bucket Brigades like “What does this mean for you?” keep readers engaged as you explore how these trends will shape the future of CNC milling.
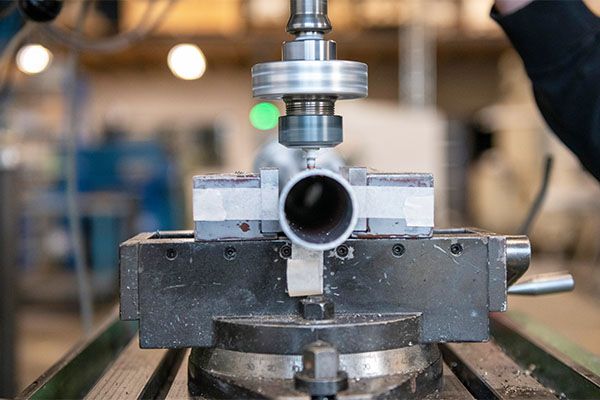
13. CNC Milling vs. Other Machining Methods
Comparing CNC Milling with CNC Turning
CNC turning and CNC milling are both critical machining processes, but they serve different purposes. CNC turning is primarily used for creating cylindrical parts, while CNC milling is ideal for parts with more complex shapes and features. Bucket Brigades like “Let’s compare” and “So why choose milling?” help readers understand when CNC milling is the best choice for achieving precision.
Why Choose CNC Milling Over Other Methods?
CNC milling offers unparalleled precision for creating complex parts with intricate details. While other machining methods may be quicker or cheaper, they often can’t achieve the same level of accuracy and fine detail as CNC milling. Bucket Brigades like “The main advantage is” and “This is why milling stands out” explain the benefits of choosing CNC milling for high-precision applications.
14. Cost Considerations in CNC Milling for Precision Parts
The True Cost of Precision CNC Milling
Precision CNC milling can be expensive due to factors like high-quality materials, advanced machines, and skilled labor. However, the cost of producing precise parts is often justified by the value they add to the final product, especially in high-performance industries like aerospace and medical devices. Bucket Brigades such as “Here’s the breakdown” and “Let me explain” can help readers understand the full cost of precision machining.
Cost-Saving Tips Without Sacrificing Quality
While achieving high precision in CNC milling often comes at a price, there are ways to optimize the process to reduce costs. Bucket Brigades like “So how can you save money?” guide readers through cost-saving tips, such as optimizing tool life, reducing waste, and streamlining machine setups, without compromising on quality.
15. Conclusion
Summary of CNC Milling Tips for Precision and Accuracy
Achieving precision and accuracy in CNC milling requires attention to detail at every stage of the process, from machine setup and tool selection to software and inspection. By following the tips outlined in this article, manufacturers can significantly improve the quality and consistency of their CNC milled parts.
Final Thoughts on Achieving Consistent Quality
Consistently high-quality, precise parts are achievable with the right equipment, materials, and techniques. By focusing on precision, regularly maintaining equipment, and utilizing the right software, manufacturers can improve their milling operations and produce parts that meet even the most demanding specifications.
Aufruf zum Handeln
Ready to improve your CNC milling precision? Implement the tips discussed in this article, or reach out to us for expert advice and high-quality CNC milling services tailored to your specific needs.
FAQs
- What are the best materials for CNC milling?
The best materials for CNC milling depend on the specific requirements of the project. For high-strength parts, metals like stainless steel, titanium, and aluminum are often used. For parts requiring high precision and minimal deformation, materials like brass, bronze, and plastics such as PEEK are ideal. The key is selecting a material that balances machinability with performance requirements. - How do I troubleshoot inaccuracies in my CNC milled parts?
If your CNC milled parts are coming out inaccurate, first check for common issues such as machine calibration, tool wear, and programming errors. Misalignment or errors in the G-code can lead to parts that don’t meet the specified dimensions. Inspect tools for wear and replace them if needed. Additionally, ensure the material is correctly aligned and that the machine is properly calibrated before starting the milling process. - What is the role of software in CNC milling precision?
Software plays a critical role in CNC milling precision. CAD (Computer-Aided Design) software helps design parts to the exact specifications, while CAM (Computer-Aided Manufacturing) software generates the tool paths and machine code required to produce the part. Both must be well-integrated to ensure accurate milling. Using the latest, most advanced software ensures that the machine operates efficiently and produces parts within tight tolerances. - How can I improve the surface finish of CNC milled parts?
To improve the surface finish of CNC milled parts, consider adjusting the cutting parameters such as feed rates, cutting speeds, and tool selection. Using a finer tool or using tools with coatings designed for smooth finishes can help. Additionally, implementing finishing operations such as polishing or honing can further enhance surface quality. Cooling fluids may also be used to reduce friction and heat buildup during milling, helping to improve the finish. - What’s the difference between 3-axis and 5-axis CNC milling?
The main difference between 3-axis and 5-axis CNC milling lies in the number of directions the tool can move. A 3-axis machine moves the cutting tool along the X, Y, and Z axes, which is ideal for simpler, flat parts. A 5-axis machine, however, adds rotational movement, allowing the tool to approach the part from multiple angles. This makes 5-axis milling more suitable for complex geometries and intricate parts requiring high precision and accuracy.