Einführung
Surface roughness is a critical factor in the manufacturing process and plays a key role in determining the performance and longevity of materials. Understanding the different parameters, measurement techniques, and engineering applications of surface roughness is crucial for manufacturers to ensure that their products meet the required standards. In this article, we will explore the various aspects of surface roughness, including key metrics, measurement methods, and how it affects material properties, all while diving into the engineering applications where surface roughness is most important.
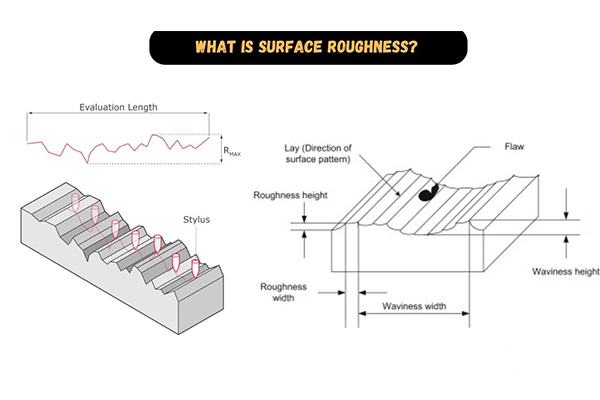
1. What is Surface Roughness?
Surface roughness refers to the irregularities that exist on the surface of a material, resulting from the manufacturing process. These irregularities are often microscopic and are measured by various roughness parameters. The roughness of a surface can be measured and quantified in multiple ways, including the arithmetic average roughness (Ra) and the root mean square (Rq). The significance of surface roughness lies in how it affects both the aesthetic and functional properties of the material.
But here’s the kicker: surface roughness is not just about looks; it has real implications for performance. From wear resistance to corrosion resistance, a rougher surface can have negative effects on how materials behave in real-world applications. It can lead to increased friction, faster wear, and even faster failure of parts in some cases.
One common parameter used to measure surface roughness is the arithmetic average roughness (Ra), which averages the height of surface irregularities. Another key parameter is root mean square (Rq), which tends to give a more weighted average compared to Ra. These parameters are essential in determining the functional performance of a material and ensuring that it is fit for purpose in industrial applications.
Surface roughness is a key consideration in industries like automotive manufacturing, aerospace engineering, and medical device production. These industries require precise control of surface quality to ensure that parts meet stringent performance standards.
Measurement Type | Parameter | Formula | Anwendungsbereich |
---|---|---|---|
Arithmetic Average | Ra | Average height of surface irregularities | Automotive, Aerospace |
Root Mean Square | Rq | Square root of the average squared heights | Medical devices, Machinery |
Peak-to-Valley | Rz | Difference between the highest peak and the lowest valley | Metalworking, Electronics |
2. Why is Surface Roughness Important in Engineering?
Surface roughness is crucial in engineering because it directly impacts the material’s functionality and longevity. While it’s easy to overlook the surface texture, roughness can significantly affect a product’s overall performance. Whether in reducing wear or ensuring tight fits between parts, the roughness of the surface determines how the material will behave under stress and friction.
Ready for the good part? The importance of surface roughness extends to more than just mechanical performance. It also influences aesthetics, heat transfer efficiency, and sealing capabilities. For instance, in heat exchangers, the roughness of surfaces can affect thermal conductivity, which in turn affects the system’s overall efficiency.
From a mechanical perspective, rough surfaces tend to increase friction, which can accelerate wear and lead to premature failure of parts, especially in applications where high precision is required. On the other hand, excessively smooth surfaces might not provide the necessary friction for components to function properly, such as in the case of braking systems. Therefore, a balance needs to be struck.
When it comes to aerospace engineering, the slightest difference in surface roughness can have a huge impact. Aerospace parts are typically subjected to extreme conditions, so controlling roughness is key to preventing failures. For instance, turbine blades must maintain a specific surface texture to endure high-speed rotations and heat.
Engineering Field | Surface Roughness Effect | Common Solutions |
---|---|---|
Automobilindustrie | Affects friction and wear | Control through lubrication |
Luft- und Raumfahrt | Impacts structural integrity | Precision machining techniques |
Herstellung | Influences sealing and durability | Surface finishing methods |
3. What are the Key Surface Roughness Parameters?
There are several parameters used to quantify surface roughness. Each parameter is suited for different applications and provides engineers with different insights into the surface’s quality. The most common parameters are Ra (arithmetic average roughness), Rq (root mean square roughness), and Rz (peak-to-valley height).
But wait, there’s more! While these are the most commonly used parameters, surface roughness can also be described using several other specialized metrics, such as Rt (total height) and Rsk (skewness). These parameters give additional insight into the surface profile and help engineers make more precise adjustments.
Let’s break it down a bit further. Ra measures the average height of surface irregularities, making it useful for general purposes and widely used in manufacturing. Rq, on the other hand, is more sensitive to extreme peaks and valleys, making it useful when more precision is required.
Rz is often used in applications that involve sealing or mating surfaces. This parameter helps engineers understand how well two surfaces will interact when pressed together. A higher Rz can mean more irregularities, which may affect the sealing performance of gaskets or joints.
To make sure you’re getting the best surface roughness parameters for your needs, it’s important to understand the nuances of each and choose accordingly. Engineers often need to use a combination of parameters to fully assess surface quality.
Parameter | Definition | Anwendung |
---|---|---|
Ra | Average height of surface irregularities | General manufacturing |
Rq | Root mean square roughness | Precision engineering |
Rz | Peak-to-valley height | Sealing, mating surfaces |
Rt | Total height of the profile | Harsh environments |
Rsk | Skewness of the profile | Aerospace, high-performance parts |
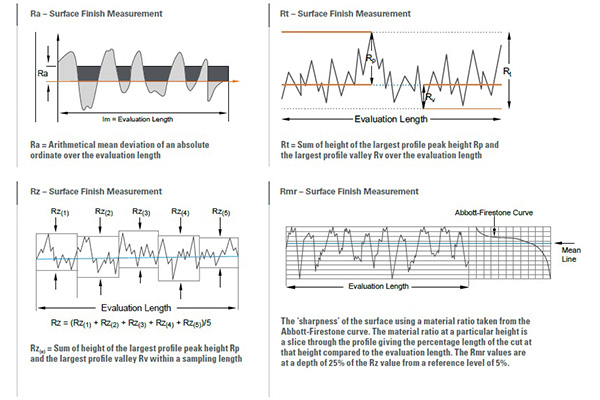
4. What Are the Different Methods for Measuring Surface Roughness?
There are a variety of methods available for measuring surface roughness, each suitable for different applications. The most commonly used methods include contact profilometry, optical methods, Und non-contact laser scanning.
Here’s the deal: each method has its pros and cons, and the choice of method depends largely on the level of precision required and the material being measured. Contact profilometers are the most traditional method and are often used in industries like automotive and metalworking. These devices physically touch the surface to measure roughness, making them highly accurate for certain materials.
Non-contact methods, such as laser scanning, are becoming more common in industries where delicate or very small parts need to be measured without causing any wear. Laser scanning uses light to measure the surface texture and is ideal for more fragile materials, or when you need to avoid potential damage from contact.
Optical methods are also frequently used in research settings and when measuring highly detailed surfaces. These methods provide quick measurements and are non-invasive. The downside is that they may not always be as accurate as contact methods for rougher surfaces.
Measurement Method | Vorteile | Nachteile | Anwendungsbereich |
---|---|---|---|
Contact Profilometry | High accuracy, reliable | Can damage sensitive surfaces | Metalworking, Automotive |
Optical Methods | Fast, non-contact, non-invasive | Lower accuracy on rough surfaces | Research, fine materials |
Laser Scanning | Precise, non-contact | Expensive equipment | Aerospace, delicate parts |
5. How Does Surface Roughness Affect Material Properties?
Surface roughness can significantly impact various material properties, including friction, wear resistance, and fatigue strength. When surfaces are rough, they typically experience higher levels of friction, which can lead to faster wear and a decrease in the material’s lifespan. Additionally, rough surfaces often have micro-cracks that can serve as initiation points for fatigue, causing the material to fail earlier than a smoother surface would.
What’s the real story? The relationship between surface roughness and material properties goes beyond just wear resistance. Surface roughness can affect other properties like corrosion resistance. A rough surface tends to trap moisture and other corrosive agents more easily, which accelerates the degradation of materials, particularly metals.
However, rough surfaces are not always detrimental. In some cases, roughness is intentionally engineered to improve the material’s performance. For instance, in sealing applications, a rough surface may create better contact between mating parts, improving the seal’s effectiveness. This is why engineers must carefully control surface roughness to strike a balance between wear resistance and functional requirements.
Material Property | Effect of High Surface Roughness | Effect of Low Surface Roughness |
---|---|---|
Friction | Higher, increases wear | Lower, reduced wear |
Wear Resistance | Decreases due to more friction | Increases with lower friction |
Korrosionsbeständigkeit | Decreases due to moisture retention | Increases with smooth surfaces |
Fatigue Strength | Lowers due to crack initiation | Higher, less prone to cracking |
6. What is the Difference Between Surface Finish and Surface Texture?
Surface finish and surface texture are terms often used interchangeably, but they have distinct meanings in the context of engineering. Surface finish generally refers to the overall appearance or smoothness of a surface, while surface texture describes the fine details, such as the patterns and orientations of irregularities.
But here’s the kicker: the difference between the two is crucial in understanding how a material will perform. While surface finish is more about aesthetics and the “look” of the material, surface texture has a direct impact on how the material interacts with other surfaces.
In applications where friction is a concern, such as in bearing surfaces, understanding surface texture becomes critical. A smoother surface finish will lead to less friction, but it is the texture (such as grooves or patterns) that influences the material’s performance in sealing or bearing applications.
Surface finish is often measured by parameters such as Ra (arithmetic average roughness), while surface texture can be described in terms of wavelength Und amplitude. Understanding both aspects is crucial in manufacturing high-performance parts.
Parameter | Surface Finish | Surface Texture |
---|---|---|
Definition | Overall appearance or smoothness | Detailed surface patterns and irregularities |
Messung | Ra, Rz | Wavelength, amplitude |
Anwendungsbereich | Aesthetic, general use | Bearing surfaces, sealing components |
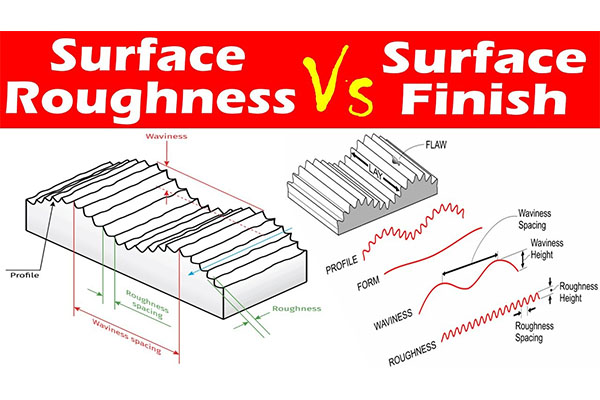
7. What is the Arithmetic Average Roughness (Ra)?
The arithmetic average roughness (Ra) is the most commonly used parameter to quantify surface roughness. It is calculated by averaging the absolute values of the height differences between the peaks and valleys of a surface. Ra provides a simple, easy-to-understand metric for surface roughness, making it useful across many industries.
Ready for the good part? The reason Ra is so widely used is that it provides a quick assessment of surface quality without requiring complex calculations. However, it’s important to note that Ra doesn’t capture extreme surface features as well as other parameters like root mean square roughness (Rq). Therefore, it’s often used in conjunction with other metrics to give a fuller picture of surface quality.
In manufacturing and machining, Ra is critical for ensuring that parts fit together properly and function as intended. For example, in automotive manufacturing, Ra is used to measure the roughness of metal parts, ensuring they can withstand wear and friction during use. However, in applications like medical device production, where smoothness is key, a lower Ra value may be required.
Parameter | Ra (Arithmetic Average Roughness) |
---|---|
Definition | Average height of surface irregularities |
Calculation | Average of absolute height differences |
Anwendung | Automotive, general manufacturing |
8. How is Root Mean Square Roughness (Rq) Used in Surface Measurement?
Root mean square roughness (Rq) is a more sensitive measure of surface roughness compared to Ra. Rq is calculated as the square root of the mean of the squares of the surface deviations. Because Rq emphasizes larger deviations more than Ra, it provides a more comprehensive understanding of surface quality, especially when dealing with highly irregular surfaces.
This is where it gets interesting. Rq is particularly useful in industries where extreme surface features could affect performance. For instance, in the aerospace sector, the performance of turbine blades relies on precise surface textures that can be accurately measured with Rq.
While Ra provides a general overview, Rq is used when more precision is necessary. In medical device manufacturing, for instance, Rq is essential for ensuring that surfaces are free from large imperfections that could affect patient safety.
Parameter | Rq (Root Mean Square Roughness) |
---|---|
Definition | Square root of the average squared deviations |
Calculation | More sensitive to extreme values than Ra |
Anwendung | Aerospace, medical devices, precision engineering |
9. What is the Role of Surface Texture in Manufacturing?
Surface texture is integral to the manufacturing process because it influences the functionality of parts in ways that are not immediately visible. It affects not only the appearance of a product but also how it interacts with other components in an assembly. For example, a rough surface can affect how well a component seals or how much friction it generates when in use.
Here’s the thing: engineers must control surface texture to meet specific functional requirements. Surface texture can be designed to control fluid flow, enhance or reduce friction, and improve material adhesion. In the case of gears, for example, the texture of the teeth will affect how efficiently they mesh and transfer power. Similarly, in sealing components, surface texture can influence how well seals maintain their integrity under pressure.
Surface Texture Type | Effect on Functionality | Häufige Anwendungen |
---|---|---|
Smooth | Low friction, aesthetic | Aerospace, automotive parts |
Rough | High friction, better seal | Bearings, gasket surfaces |
Textured | Controls fluid dynamics | Pumps, turbines |
10. How Are Surface Roughness and Surface Finish Used in Design?
In engineering design, surface roughness and finish are key factors that influence the performance, longevity, and cost-effectiveness of parts. Engineers consider these factors when selecting materials and manufacturing processes. For example, a part with a rough surface might require additional finishing processes to achieve the desired smoothness and functionality.
What’s the real story? Engineers need to balance surface roughness with other design considerations. For example, a surface that is too smooth may fail to generate sufficient friction for proper operation. On the other hand, excessively rough surfaces could cause unnecessary wear or failure.
In product design, surface roughness is used strategically to enhance the product’s performance. For example, a rough surface on a piston ring may be designed to increase friction for a better seal, whereas a smooth surface on a ball bearing helps reduce friction and wear.
Design Aspect | Desired Surface Finish | Example Applications |
---|---|---|
Friction | Smooth, low friction | Lager, Zahnräder |
Seal Integrity | Rougher surface | Gaskets, piston rings |
11. What Are the Engineering Applications of Surface Roughness?
Surface roughness plays a crucial role in several engineering applications, affecting the reliability and performance of parts used in various industries. In automotive engineering, for example, the roughness of engine parts like pistons, cylinders, and valves can impact the engine’s efficiency and wear resistance. Similarly, in aerospace, surface roughness is critical for ensuring that parts like turbine blades can withstand the high-stress conditions they face.
Surface roughness also impacts medical device production, particularly in implants and surgical tools. A smooth surface on surgical tools is essential to prevent damage to tissues, while surface roughness on implants can enhance the bond with bone or tissue.
Industrie | Wichtige Anwendungen | Impact of Surface Roughness |
---|---|---|
Automobilindustrie | Engine parts, suspension systems | Wear resistance, performance |
Luft- und Raumfahrt | Turbine blades, wings | Structural integrity, safety |
Medical Devices | Implantate, chirurgische Instrumente | Biocompatibility, performance |
12. How Do Surface Roughness Measurements Affect Product Quality?
Surface roughness measurements are essential for ensuring that products meet the required quality standards. By controlling surface roughness, manufacturers can produce parts that fit together seamlessly, function reliably, and withstand the test of time. For instance, in high-precision manufacturing, like the production of machine tools, surface roughness ensures that parts mesh properly and reduce friction.
What’s the catch? Poor surface roughness control can lead to poor-quality parts, resulting in higher rejection rates and increased costs. Manufacturers must use reliable methods to measure and control roughness to maintain high-quality standards and minimize waste.
Quality Control Method | Measurement Type | Industrielle Anwendung |
---|---|---|
Profilometry | Contact/Non-contact | Precision machining |
Optical Methods | Laser scanning | Automotive, aerospace |
13. How Can Surface Roughness Be Controlled in Manufacturing?
Manufacturers use several techniques to control surface roughness, including machining (e.g., grinding, milling), surface finishing, Und polishing. The choice of method depends on the material and the desired surface texture.
Ready for the good part? Surface roughness can also be controlled by choosing the right machining tools Und adjusting cutting parameters. For example, using a fine-grit tool can help produce a smoother finish, while adjusting speed and feed rates during milling can reduce surface imperfections.
Control Method | Effect on Surface Roughness | Common Uses |
---|---|---|
Schleifen | Reduces roughness to smooth level | Automotive, aerospace |
Polieren | Produces ultra-smooth finish | Medical devices, optics |
Oberflächenveredelung | Adjusts roughness for function | Seals, bearings |
14. What Are Common Challenges in Surface Roughness Measurement?
Measuring surface roughness is not without its challenges. One major issue is the variability of results due to the method of measurement and the material being tested. For instance, non-contact methods like laser scanning may struggle with very rough or uneven surfaces. Moreover, different materials respond differently to measurement techniques, which can lead to discrepancies in readings.
Here’s where it gets interesting: despite advances in measurement technologies, there’s still no one-size-fits-all solution. Manufacturers must consider the trade-offs between speed, accuracy, and material compatibility when choosing a surface roughness measurement technique.
Measurement Issue | Lösung | Anwendungsbereich |
---|---|---|
Surface Material | Choose compatible measurement method | Metalworking, plastics |
Werkzeugverschleiß | Regular calibration and maintenance | Luft- und Raumfahrt, Automobilindustrie |
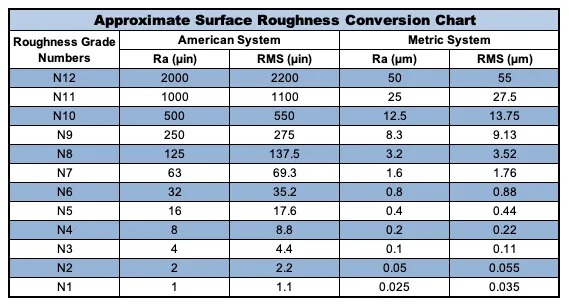
15. How is Surface Roughness Used in Product Testing?
Surface roughness is used in product testing to evaluate how materials will behave under stress, wear, and other operational conditions. By measuring surface roughness before and after product testing, manufacturers can determine how much wear a part has experienced and whether it will continue to perform at the required standards.
This is where it gets interesting: in real-world applications, surface roughness measurements can be a key indicator of product life. Parts that exhibit higher surface roughness after testing may be prone to premature failure, while parts that maintain a smoother finish are likely to last longer.
Test Method | Surface Roughness Change | Industrielle Anwendung |
---|---|---|
Wear Testing | Increased roughness indicates wear | Automotive, aerospace |
Fatigue Testing | Surface integrity shows durability | Medizinische Geräte |
Abschluss
In conclusion, surface roughness is a key consideration in manufacturing that affects everything from material properties to product quality and performance. Whether in automotive, aerospace, or medical device industries, controlling surface roughness is crucial for ensuring high-quality, durable products. By understanding and measuring surface roughness accurately, engineers can make informed decisions to optimize material performance and ensure that parts meet stringent industry standards.
FAQ-Bereich
Frage 1: What is surface roughness?
Surface roughness refers to the irregularities on the surface of a material caused by the manufacturing process. It is often quantified using parameters like Ra (arithmetic average roughness) and Rq (root mean square roughness).
Frage 2: How does surface roughness impact material performance?
Surface roughness can affect friction, wear resistance, and fatigue strength. A rougher surface often leads to higher friction and faster wear, while smoother surfaces can improve performance in certain applications.
Frage 3: What are the different methods for measuring surface roughness?
Surface roughness can be measured using contact methods (profilometers), non-contact methods (laser scanning), and optical methods. Each has its pros and cons depending on the application.
Frage 4: How does surface roughness affect the quality of a finished product?
Surface roughness affects the functionality and appearance of products. Rough surfaces can cause wear and early failure, while smooth surfaces may enhance performance in certain applications like bearings or seals.
Frage 5: What are some common challenges in surface roughness measurement?
Challenges include variability in measurement results, material compatibility issues, and the trade-offs between speed, accuracy, and material compatibility when selecting measurement methods.