Einführung
Machining custom consumer parts plays a critical role in industries like electronics, automotive, and medical devices. In this article, we will explore the importance of machining in the production of custom consumer parts, the various techniques used, and how businesses can choose the right machining service. Whether you are manufacturing components for consumer electronics or designing unique parts for a new product, understanding how to machine custom parts efficiently will help you achieve precision, reduce costs, and improve product quality.

1. What Are Custom Consumer Parts in Machining?
Custom consumer parts refer to components specifically designed and manufactured to meet the unique specifications of consumer products. These parts are crucial in the creation of products such as smartphones, household appliances, automotive components, and medical devices. Custom machining is used to achieve high precision and tailor components to the exact needs of the product. But here’s the kicker – these custom parts are often the backbone of innovation, driving better performance and functionality in the products they’re integrated into.
For example, consider the case of a high-end audio system. The precision parts used in the internal components, such as custom circuit boards or speaker housings, ensure top-notch sound quality. Similarly, in the automotive industry, custom-machined engine parts are essential for performance optimization and safety.
Additionally, the demand for customized consumer parts has grown due to the increasing trend of personalization in consumer goods. People want products that reflect their individual needs, whether it’s a smartphone with specialized features or a kitchen appliance designed to save space.
Here’s where it gets interesting – as technology advances, the complexity of custom parts increases. With the evolution of 3D modeling and computer-aided design (CAD), manufacturers can create parts that fit into highly specialized applications. This shift has led to the rise of custom machining as an indispensable process in modern manufacturing.
Material Type | Anwendungen | Machining Process |
---|---|---|
Metalle | Automotive, Aerospace | CNC Milling, Turning |
Kunststoffe | Electronics, Medical | Injection Molding, CNC |
Composites | Sports Equipment, Aerospace | CNC Milling, Laser Cutting |
2. Why Is Machining Crucial for Custom Consumer Parts?
Machining is crucial for custom consumer parts because it provides precision, flexibility, and cost-efficiency. Ready for the good part? It’s the only method that can achieve the required tolerances and design complexities that consumer products demand. Unlike other manufacturing methods, machining can be used on a wide variety of materials and is capable of producing components with minimal waste.
Consider the creation of a custom part for a smartphone – it’s not just about getting the dimensions right. The part needs to fit perfectly into the assembly, ensuring that the final product works flawlessly. CNC (Computer Numerical Control) machines provide that level of precision, with the ability to handle intricate designs and achieve tight tolerances that are essential in high-performance consumer electronics.
Moreover, machining offers flexibility in production. With CNC machines, manufacturers can produce low-volume runs of custom parts without the need for expensive molds, making it a preferred method for businesses that want to test new designs or create limited-edition products. But here’s the kicker – machining also allows for faster prototyping, which means products can reach the market much quicker than with other methods.
In addition to flexibility and speed, machining ensures consistency and quality control, with the ability to replicate parts with high accuracy. This is particularly important in industries where product failure can have serious consequences, such as medical devices or automotive parts.
Machining Method | Vorteile | Häufige Anwendungen |
---|---|---|
CNC-Fräsen | High precision, Versatility | Electronics, Automotive |
CNC-Drehen | High-quality finish, Speed | Aerospace, Medical Devices |
Laserschneiden | Detailed cuts, Speed | Consumer Goods, Packaging |
3. What Types of Machines Are Used for Custom Consumer Parts?
When machining custom consumer parts, the types of machines used are critical to achieving the desired results. What’s the real story? The machines selected depend on the material, the design of the part, and the required precision. CNC milling machines, CNC turning machines, and laser cutters are some of the most commonly used machines in custom machining.
CNC milling machines are the backbone of the machining process. They use rotary cutters to remove material from a workpiece, creating the desired shape. These machines are highly versatile, making them suitable for a wide range of applications, from simple parts to highly intricate components. The precision they offer is essential for custom parts like circuit boards or housings in consumer electronics.
CNC turning machines are used to create cylindrical parts by rotating the workpiece against a cutting tool. They are ideal for producing parts like shafts, rings, and bushings that need to be turned to a high degree of precision. This method is frequently used in the automotive and aerospace industries, where parts must meet strict tolerances.
Laser cutting machines, on the other hand, are used for parts that require fine, detailed cuts. These machines are excellent for cutting intricate shapes from materials such as metals, plastics, and composites. This technology is ideal for consumer goods like packaging, decorative parts, or intricate appliance components.
What’s the real story? By selecting the right machine for each job, manufacturers can ensure that custom consumer parts are produced efficiently and with a high degree of precision.
Machine Type | Use Case | Vorteile |
---|---|---|
CNC-Fräsen | Complex part production | High precision, Versatility |
CNC-Drehen | Cylindrical parts | High-speed, Excellent finish |
Laserschneiden | Detailed cuts | Precision, Fine detail cuts |
4. What Materials Are Commonly Used for Machining Custom Consumer Parts?
Selecting the right material for custom consumer parts is crucial in achieving both the functionality and durability of the product. Ready for the good part? Material choice can make or break a product’s performance. Metals, plastics, and composites are the most commonly used materials in custom machining, and each has its specific applications and benefits.
Metals like aluminum, steel, and titanium are widely used due to their strength and durability. Aluminum is often chosen for parts that need to be lightweight, such as automotive components and consumer electronics housings. Steel, on the other hand, is preferred for parts requiring higher strength and resistance to wear and tear, such as automotive engine components or tools.
Plastics are often used in the production of lighter, less expensive consumer parts. Materials such as ABS and polypropylene are common choices for parts like enclosures or housings in electronics. Plastics can be machined to fine tolerances and provide flexibility in design, but they are generally not as strong as metals.
Composites, which are made from a combination of different materials, are used in industries that require a combination of strength, lightweight, and heat resistance. Aerospace components, sports equipment, and high-performance automotive parts often use composite materials due to their unique properties.
Here’s where it gets interesting – as new technologies develop, the range of materials used for custom consumer parts is expanding. For example, 3D printing technology is making it possible to print parts in advanced materials like carbon fiber composites, which were once impossible to machine.
Material Type | Stärke | Häufige Anwendungen |
---|---|---|
Aluminium | Light, Durable | Automotive, Electronics |
Stahl | High strength | Engine parts, Tools |
Plastik | Lightweight, Flexible | Electronics, Appliances |
5. How Is the Machining Process for Custom Parts Managed?
Managing the machining process for custom consumer parts involves overseeing several key factors, from selecting materials to ensuring the final part meets the required specifications. But here’s the kicker – the goal is to strike a balance between quality, time, and cost. For manufacturers, efficient process management ensures that parts are made to precise specifications without exceeding budgets or timelines.
The machining process typically begins with the design phase, where CAD software is used to create a model of the part. Once the design is finalized, it is programmed into the CNC machine, which then begins the machining process. Factors such as speed, precision, and tool selection are critical to producing high-quality custom parts.
Quality control is another critical element in managing the machining process. In industries like aerospace and medical devices, even the slightest error can result in product failure. This is why quality checks are implemented throughout the machining process to ensure that every part meets the required standards. Inspections typically include visual checks, measurement with precision tools, and functional testing.
So, how can you ensure efficient machining? By closely monitoring each stage of the process, making adjustments as necessary, and using the right tools and equipment, manufacturers can deliver high-quality custom parts on time and within budget.
Process Step | Key Factor | Bedeutung |
---|---|---|
Design | CAD software | Precision, Accuracy |
CNC Programming | Machine setup | Speed, Efficiency |
Qualitätskontrolle | Inspections, Testing | Ensures part quality |
6. What Are the Challenges in Machining Custom Consumer Parts?
Machining custom consumer parts can be an intricate process, and there are several challenges that manufacturers face. What’s the real story? Even with the best machines and skilled operators, several factors can affect the outcome of the production process. These challenges range from material limitations to the intricacies of achieving the required tolerances.
For starters, one of the biggest challenges is material constraints. Certain materials can be difficult to machine due to hardness, brittleness, or the tendency to deform under heat. For example, machining high-strength alloys like titanium can be more complex than working with softer metals such as aluminum. It requires special tools, slower speeds, and more precise techniques, which increases production time and costs.
Precision is another critical issue. While CNC machines are highly accurate, ensuring that every part adheres to strict tolerances can be difficult. For instance, consumer products like smartphones or medical devices require parts with tight dimensional specifications. If a component doesn’t fit perfectly, it can result in a malfunction or failure of the final product.
Here’s where it gets interesting – even when the tolerances are met, there’s still the challenge of achieving the desired surface finish. Poor surface finishes can affect not only the aesthetics but also the functionality of the part. For example, parts that are not finished properly can have issues with fitment or may cause unnecessary wear and tear over time.
Despite these challenges, the benefits of precision machining often outweigh the difficulties, as it allows manufacturers to create custom parts that fit perfectly into highly specialized applications.
Herausforderung | Potential Issue | Lösung |
---|---|---|
Material Constraints | Difficult to machine certain materials | Use specialized tools, slower speeds |
Precision Requirements | Tight tolerances needed for fit | Regular calibration of CNC machines |
Surface Finish | Inconsistent finishes | Polishing, advanced tooling |
7. How Do You Choose a Machining Service for Custom Consumer Parts?
Selecting the right machining service is a critical step in ensuring that your custom consumer parts are produced efficiently, accurately, and within budget. Ready for the good part? The right partner will help streamline the entire process, from design to production, ensuring that quality standards are met and your parts fit perfectly into the final product.
First, you’ll want to evaluate the service provider’s capabilities. Does the machining service have experience with the materials and types of parts you need? It’s important to choose a service that specializes in the particular type of machining required for your custom parts, whether it’s CNC milling, turning, or laser cutting.
Another key factor is their ability to meet deadlines. Delays in part production can significantly slow down the overall manufacturing process, so finding a machining service with a proven track record of on-time delivery is crucial. Ask for references and past case studies to see if the service provider has worked on similar projects.
But here’s the kicker – cost is always an important consideration. While you don’t want to compromise on quality, it’s also important to find a machining service that provides competitive pricing. Be sure to get multiple quotes and compare them, keeping in mind that the cheapest option may not always be the best in terms of quality.
Criteria | Bedeutung | Questions to Ask |
---|---|---|
Funktionen | Ensures expertise in your project | Do you specialize in CNC milling or turning? |
Timeliness | Avoids project delays | Can you meet my production deadlines? |
Pricing | Ensures cost-efficiency | Can you provide a competitive quote? |
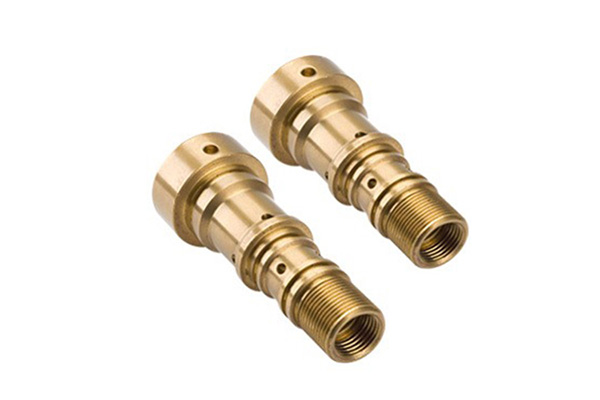
8. What Role Does CNC Programming Play in Custom Part Machining?
CNC programming plays a vital role in the machining process, as it determines how the machine will cut, shape, and finish the custom part. The process involves converting a part design into a machine-readable format, which then controls the CNC machine’s movements. But here’s the kicker – the quality of the CNC program directly affects the precision, accuracy, and efficiency of the machining process.
At the core of CNC programming is the use of G-code, which is a standardized language that tells the machine exactly how to move. The program defines key parameters such as cutting speed, tool path, and machine direction. A well-written CNC program ensures that the part is produced according to the exact specifications, reducing errors and improving overall production speed.
What’s the real story? Poor CNC programming can lead to costly mistakes. For example, if the machine cuts too quickly or in the wrong direction, it could damage the part or even the machine itself. In industries like aerospace and medical devices, even minor mistakes can lead to catastrophic failures, which is why CNC programming requires precision and expertise.
To ensure optimal results, it’s important to use advanced software tools and invest in skilled programmers who can handle complex designs and machine setups. The right CNC programming is what makes custom machining so effective in producing high-quality, accurate parts.
Programming Aspect | Bedeutung | Potential Impact |
---|---|---|
Cutting Speed | Affects production time | Faster cutting speeds can reduce costs |
Tool Path | Determines machining accuracy | Incorrect paths lead to errors |
Maschineneinrichtung | Controls overall process | Poor setup can damage parts or machines |
9. How Does Prototyping Impact the Machining of Custom Consumer Parts?
Prototyping is a crucial step in the production of custom consumer parts. Ready for the good part? It allows manufacturers to test a design before committing to mass production, ensuring that any issues are addressed early in the process. Prototyping not only saves time and money but also helps in making design improvements that might otherwise go unnoticed until production starts.
One of the main benefits of prototyping is that it provides a tangible model of the part that can be physically inspected. This is particularly useful for detecting design flaws, checking for fit, and confirming that the part meets the required specifications. With rapid prototyping techniques like 3D printing, manufacturers can quickly produce models of their parts without the need for expensive molds or tooling.
But here’s the kicker – prototypes can be used to test the functionality of the part in real-world conditions. For instance, in the automotive industry, prototyping allows engineers to see how a new part fits within the engine assembly and performs under stress. This hands-on approach helps refine the design and ensures that the final part performs as intended.
Prototyping also reduces the risks associated with mass production. By catching potential issues early, manufacturers can avoid costly mistakes and revisions during the larger production run. This makes prototyping a critical step in the machining of custom consumer parts.
Prototyping Method | Vorteile | Use Case |
---|---|---|
3D Printing | Rapid production, Low cost | Electronics, Medical Devices |
CNC-Fräsen | High precision, Strong materials | Aerospace, Automotive |
SLA Printing | Detailed, Complex shapes | Consumer Goods, Jewelry |
10. What Are the Best Practices for Quality Control in Machining Custom Parts?
Quality control is essential when machining custom consumer parts. In industries where precision is critical, quality control processes ensure that the parts meet strict standards and function correctly in their final applications. But here’s the kicker – without a solid quality control plan, even the best machines and designs can produce faulty parts, leading to product failures.
The first step in quality control is inspection. Before the machining process begins, manufacturers use inspection tools to check the raw material’s dimensions and ensure it meets the required specifications. After machining, parts are subjected to further inspections to verify their shape, finish, and overall accuracy. Tools such as micrometers, calipers, and coordinate measuring machines (CMM) are commonly used in this process.
What’s the real story? In some cases, parts may undergo functional testing to ensure they perform as intended. For example, in medical devices, components must undergo rigorous testing to ensure they meet regulatory standards. Any deviation from the required standards can result in the rejection of the part, which could delay the entire production process.
To maintain consistency, manufacturers must implement a continuous feedback loop, where the machining process is regularly monitored and adjusted based on inspection results. By doing so, manufacturers can catch errors early, improve efficiency, and ensure the final product meets high-quality standards.
QC Process | Tools Used | Bedeutung |
---|---|---|
Rohstoffinspektion | Micrometers, Calipers | Ensures proper starting material |
Machining Inspection | CMM, Visual Checks | Guarantees correct dimensions |
Functional Testing | Stress Tests, Simulations | Validates part performance |
11. How Can You Reduce Costs When Machining Custom Consumer Parts?
Reducing costs in machining custom consumer parts is a common concern for manufacturers. Ready for the good part? There are several strategies that can help lower costs without compromising on quality. The key is to find ways to optimize the machining process and make it more efficient.
One of the most effective ways to reduce costs is by optimizing the material usage. Instead of cutting large blocks of material down to size, manufacturers can use techniques such as near-net shape manufacturing, where the part is designed to minimize material waste. This not only cuts costs but also reduces environmental impact.
Another key strategy is to optimize machine time. This means selecting the right machine for the job, using automated systems to reduce labor costs, and ensuring that machines are running at their maximum efficiency. Machine downtime, for example, can lead to increased costs, so preventive maintenance is crucial in ensuring that the machinery operates smoothly.
What’s the real story? By improving processes and using technology, manufacturers can significantly reduce machining costs. Additionally, leveraging advanced software tools for CNC programming and part design can streamline production, minimize errors, and reduce material waste, all of which contribute to a more cost-effective machining process.
Cost Reduction Strategy | Action | Auswirkungen |
---|---|---|
Material Optimization | Near-net shape manufacturing | Reduces waste, Lowers costs |
Machine Time Efficiency | Maximize machine use, Prevent downtime | Reduces labor and operation costs |
Process Improvement | Implement automated systems | Enhances efficiency and reduces errors |
12. What Are the Environmental Considerations in Machining Custom Parts?
Environmental sustainability is becoming increasingly important in manufacturing processes, and custom machining is no exception. What’s the real story? Manufacturers need to adopt practices that minimize waste, reduce energy consumption, and lower their environmental impact while producing high-quality parts.
One of the most significant environmental considerations is material waste. Traditional machining processes can generate a lot of scrap material, which can end up in landfills if not properly recycled. To combat this, many manufacturers are implementing sustainable practices such as recycling metal scraps or using biodegradable lubricants in the machining process.
Another key factor is energy consumption. Machining can be an energy-intensive process, especially when running large machines for long hours. To reduce energy consumption, manufacturers can invest in energy-efficient machinery, improve workflow processes to minimize machine idle time, and utilize renewable energy sources where possible.
Finally, water usage in the machining process is another environmental consideration. Some machining processes require large amounts of coolant, which can contaminate water supplies. Manufacturers can adopt more sustainable practices by recycling coolant and using eco-friendly alternatives.
Environmental Factor | Lösung | Auswirkungen |
---|---|---|
Material Waste | Recycling, Waste reduction | Less landfill waste, Lower cost |
Energy Consumption | Energy-efficient machines, Automation | Reduced carbon footprint |
Water Usage | Coolant recycling, Eco-friendly fluids | Protects water resources |
13. How Do You Scale Up Production for Custom Consumer Parts?
Scaling up production for custom consumer parts can be challenging, but with the right strategies, manufacturers can expand their output without compromising quality. Ready for the good part? Scaling production involves balancing efficiency, quality control, and customer demands.
One of the first steps in scaling up is automating the machining process. By implementing automated CNC machines, manufacturers can produce parts faster and with fewer errors. Automated systems can also help reduce labor costs and improve consistency across larger production runs.
Another key strategy for scaling up is optimizing the supply chain. By streamlining sourcing and inventory management, manufacturers can reduce lead times and ensure that materials are available when needed. What’s the real story? An optimized supply chain ensures that production stays on schedule and prevents delays in the manufacturing process.
Scaling up also requires careful consideration of quality control. As production volumes increase, it’s crucial to maintain the same high standards of precision and accuracy. By using automated inspection systems and implementing continuous feedback loops, manufacturers can ensure that every part produced meets the required specifications.
Scaling Strategy | Action | Nutzen |
---|---|---|
Automation | Use automated CNC machines | Faster production, Lower costs |
Supply Chain Optimization | Streamline sourcing and inventory | Reduced lead times, Efficient production |
Qualitätskontrolle | Automated inspection systems | Consistent, high-quality parts |
14. What Are the Latest Trends in Custom Consumer Part Machining?
The machining industry is constantly evolving, and staying updated with the latest trends can give manufacturers a competitive edge. Ready for the good part? There are several exciting trends in the machining of custom consumer parts, from advanced materials to cutting-edge technology.
One trend gaining traction is the use of additive manufacturing (3D printing). While not traditionally associated with machining, 3D printing allows for the rapid creation of custom parts with complex geometries that would be difficult or impossible to machine using traditional methods. This technology is particularly useful for prototyping, low-volume production, and the creation of highly customized consumer products.
Another key trend is the integration of artificial intelligence (AI) and machine learning in CNC programming. AI algorithms can analyze production data in real-time to optimize machine performance, predict maintenance needs, and improve overall efficiency. This means that custom consumer parts can be produced faster and more accurately, reducing downtime and costs.
What’s the real story? As technology continues to advance, new machining techniques and tools are constantly emerging, making it easier for manufacturers to produce high-quality custom parts with greater precision and efficiency.
Trend | Beschreibung | Auswirkungen |
---|---|---|
Additive Manufacturing (3D Printing) | Rapid prototyping, Complex designs | Faster production, More customization |
KI-Integration | Real-time data analysis, Predictive maintenance | Improved efficiency, Reduced downtime |
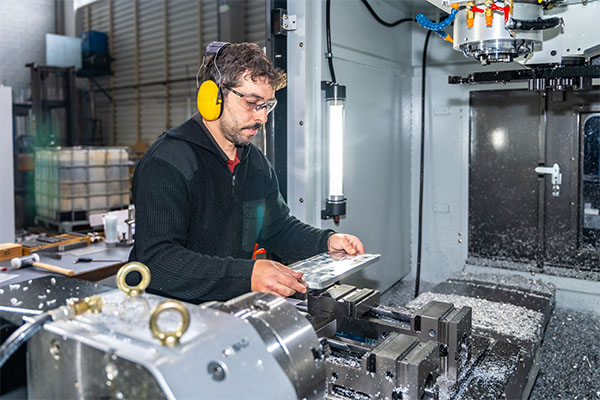
15. How Can You Ensure Long-Term Success in Machining Custom Consumer Parts?
Achieving long-term success in machining custom consumer parts requires a combination of continuous improvement, technological investment, and strong partnerships. What’s the real story? To succeed, businesses need to focus on innovation, customer satisfaction, and maintaining high standards of quality.
First, manufacturers should invest in the latest technologies, such as CNC machines with advanced capabilities and software tools for 3D modeling and simulation. By staying ahead of technological advancements, businesses can improve efficiency and keep up with the demands of modern production.
Another crucial aspect is building strong relationships with suppliers and machining partners. A reliable network of suppliers can help ensure the timely delivery of materials, while strong relationships with machining partners can help improve overall production quality and reliability.
Finally, fostering a culture of continuous improvement is key. Regular training, performance evaluations, and feedback loops can help employees stay up-to-date with the latest best practices, ensuring that the machining process remains efficient and that custom parts continue to meet customer expectations.
Success Factor | Action | Outcome |
---|---|---|
Technological Investment | Invest in advanced CNC machines | Improved precision, Faster production |
Strong Partnerships | Build reliable supplier and partner networks | Better quality, Timely deliveries |
Continuous Improvement | Ongoing training and performance reviews | Enhanced efficiency, High standards |
FAQ-Bereich
Frage 1: What is custom machining for consumer parts?
Custom machining for consumer parts involves using precision machines to create parts that fit specific designs and functions for consumer products. It ensures accuracy, durability, and high-quality finishes.
Frage 2: How does CNC machining work for custom consumer parts?
CNC (Computer Numerical Control) machining works by using computer programs to guide machines to cut, shape, and finish materials into custom parts. It allows for precise and repeatable results, making it ideal for consumer products.
Frage 3: What are the benefits of machining over other manufacturing methods?
Machining offers high precision, flexibility in material selection, and the ability to create complex designs that other methods, like injection molding, may not easily achieve.
Frage 4: How can I choose the right material for my custom consumer parts?
Choosing the right material depends on factors such as strength, weight, durability, and cost. Machining often uses metals, plastics, and composites, and the material choice impacts the performance and functionality of the part.
Frage 5: What steps can I take to ensure quality in custom part machining?
Ensuring quality involves regular inspections, precise CNC programming, using high-quality materials, and adhering to strict tolerance standards. Quality control measures are critical to achieving consistent, reliable parts.