Einführung
Stainless steel CNC machining is crucial for creating durable, high-precision parts for a variety of industries. In this article, we’ll explore the methods, tools, and techniques involved in CNC machining stainless steel, along with the challenges manufacturers face. Whether you’re a beginner or an experienced professional, this guide will give you a deeper understanding of what it takes to master stainless steel CNC machining.
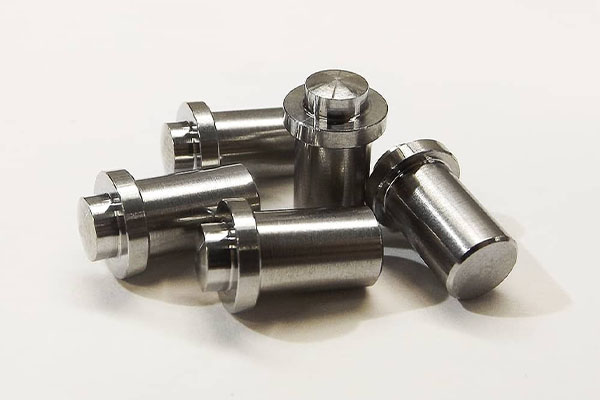
1. What is Stainless Steel Machining?
When we talk about stainless steel machining, we’re referring to the process of shaping stainless steel into specific parts using various machining methods. This involves high-precision techniques, often with the use of CNC machines, which are guided by computer programming to ensure accuracy.
But here’s the kicker—stainless steel is notoriously difficult to machine. Its hardness and resistance to corrosion make it a desirable material for many applications, but these same properties can make it challenging to work with. Unlike other metals, stainless steel requires specialized tools and techniques to maintain the quality of the finish and the durability of the parts.
CNC machining is a common method for stainless steel machining due to its precision and ability to handle the metal’s toughness. This process is highly adaptable and can create everything from simple parts to complex designs. By using computer-controlled machines, manufacturers can achieve intricate cuts, tight tolerances, and smooth finishes.
Table 1: Common Types of Stainless Steel Used in CNC Machining
Stainless Steel Type | Zusammensetzung | Häufige Anwendungen | Key Characteristics |
---|---|---|---|
304 Stainless Steel | 18% Chromium, 8% Nickel | Kitchen Equipment, Medical Devices | Corrosion resistant, durable, easy to machine |
316 Stainless Steel | 16% Chromium, 10% Nickel, 2% Molybdenum | Marine, Medical | Highly resistant to corrosion, especially in harsh environments |
410 Stainless Steel | 11.5% Chromium | Automotive, Fasteners | Strong, wear-resistant, but not as corrosion-resistant as others |
2. Why is CNC Machining Ideal for Stainless Steel?
CNC machining is ideal for stainless steel for one simple reason: precision. Stainless steel is a tough material, and achieving high-quality parts requires meticulous attention to detail. CNC machines offer the necessary precision to produce parts with very tight tolerances. They can also handle the intricate designs and sharp cuts that stainless steel requires without compromising on quality.
Ready for the good part? CNC machining also improves efficiency. Unlike manual machining, CNC machines can be programmed to work on multiple parts in a single cycle. This reduces the likelihood of human error and ensures that parts are consistently manufactured to the same standards.
Additionally, CNC machining eliminates the need for constant monitoring and adjustments during the process, which saves both time and resources. With automated machines, manufacturers can run jobs with minimal intervention, maximizing output and reducing labor costs.
Table 2: Benefits of CNC Machining for Stainless Steel
Nutzen | Beschreibung |
---|---|
Präzision | CNC machines can handle complex shapes with tight tolerances |
Effizienz | Automated systems lead to faster production and fewer errors |
Consistency | Repeatability in production ensures all parts meet the same standard |
3. What Are the Common CNC Machining Methods for Stainless Steel?
There are several CNC machining methods used for stainless steel, each suited for different types of parts and designs. The most common methods include milling, turning, drilling, and grinding.
What’s the real story here? Let’s dive into each method. Milling is a cutting process where a rotating tool removes material from a workpiece. This method is used to create flat surfaces, slots, and complex shapes. Turning is another method where the workpiece rotates while a cutting tool removes material. Turning is ideal for cylindrical shapes, like shafts or bolts.
Drilling, on the other hand, is used to create holes in stainless steel parts, while grinding is used for finishing surfaces to smooth out any rough edges or burrs. The choice of method depends on the final product and the complexity of the design.
Table 3: Comparison of Common CNC Machining Methods
Verfahren | Am besten für | Key Advantages |
---|---|---|
Mahlen | Flat surfaces, slots, complex shapes | High precision, can handle a variety of designs |
Drehen | Cylindrical parts, shafts | Efficient for producing round parts, minimal material waste |
Bohren | Löcher erzeugen | Fast and precise hole creation |
Schleifen | Surface finishing | Smooth finishes, accurate dimensions |
4. How Do CNC Machines Handle Stainless Steel’s Toughness?
Here’s where it gets interesting—stainless steel’s toughness presents unique challenges in machining. Its hardness means that CNC tools wear out more quickly, which can increase maintenance costs and reduce efficiency. Moreover, stainless steel generates heat during machining, which can lead to tool damage and poor surface finishes if not managed correctly.
So, how do CNC machines handle this? The key lies in selecting the right cutting tools and controlling the temperature during machining. Carbide tools, for example, are ideal for stainless steel because they are harder than steel and can withstand the high temperatures generated during machining. Using coolant and lubrication is also essential in preventing heat buildup, which could otherwise affect the performance of both the machine and the workpiece.
Table 4: Best Tools for CNC Machining Stainless Steel
Tool Type | Material | Vorteile |
---|---|---|
Carbide Tools | Tungsten carbide | High heat resistance, durability |
Cermet Tools | Ceramic and metal mixture | Excellent wear resistance, high-speed machining |
High-Speed Steel (HSS) Tools | Steel alloy | Cost-effective, versatile for general machining |
5. What Are the Benefits of Stainless Steel CNC Machining?
The benefits of stainless steel CNC machining go far beyond just producing precise parts. One of the key advantages is the material’s resistance to corrosion, making it ideal for applications in industries like healthcare, aerospace, and food processing. CNC machining allows manufacturers to create parts that maintain their structural integrity in harsh environments, whether exposed to chemicals, high temperatures, or moisture.
The versatility of stainless steel machining also stands out. With CNC machines, manufacturers can produce a wide range of components, from simple structural pieces to complex, custom parts. The precision and efficiency of the process ensure that parts are consistently made to exact specifications, reducing the need for manual adjustments and rework.
And, of course, let’s not forget the durability of stainless steel parts. They are built to last and can withstand wear and tear much longer than parts made from other materials. As a result, CNC machining of stainless steel is often more cost-effective in the long run due to the extended lifespan of the parts.
Table 5: Key Benefits of Stainless Steel CNC Machining
Nutzen | Beschreibung |
---|---|
Haltbarkeit | Stainless steel parts last longer and resist corrosion |
Präzision | CNC machining delivers high accuracy with tight tolerances |
Effizienz | Automated processes reduce time and labor costs |
Abschluss
In summary, stainless steel CNC machining is an essential process for producing high-quality, durable parts that can be used in a variety of industries. The combination of advanced CNC technology and the unique properties of stainless steel ensures that manufacturers can create precise, reliable components with excellent performance.
Whether you’re machining for the aerospace industry or producing medical components, understanding the methods, tools, and benefits of stainless steel CNC machining will help you optimize your production processes and achieve better results.
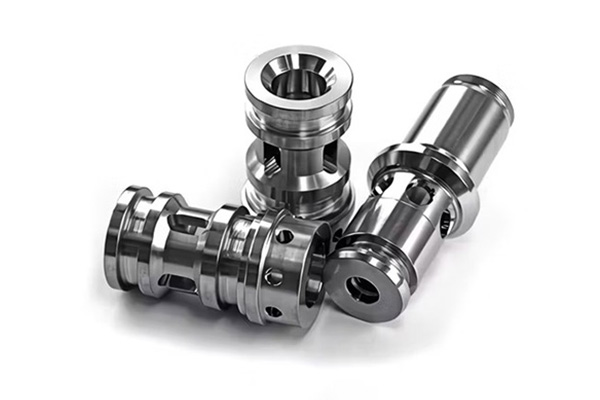
6. What Challenges Do Manufacturers Face with Stainless Steel Machining?
When machining stainless steel, manufacturers often encounter several challenges. Stainless steel is known for its strength and durability, which are two factors that make it difficult to machine. The material’s toughness leads to accelerated tool wear and tear, increasing maintenance costs and the frequency with which tools need to be replaced. This can reduce machining efficiency and add unnecessary expenses.
But here’s the kicker—heat generation is another challenge. Stainless steel tends to heat up quickly during machining, which can cause problems like tool deformation, poor surface finishes, and even part distortion. It’s critical to manage this heat to avoid damaging both the tools and the workpieces.
To combat these issues, manufacturers often rely on advanced cooling techniques. Coolants and lubricants help reduce the heat generated during machining, preserving the integrity of both the machine and the part. Additionally, careful planning of machining operations, such as adjusting speeds and feeds, can help manage tool wear and prevent excessive heat buildup.
Table 6: Common Challenges in Stainless Steel Machining
Herausforderung | Beschreibung | Lösung |
---|---|---|
Werkzeugverschleiß | High hardness leads to quicker tool wear | Use carbide tools and coatings |
Heat generation | High heat can cause tool damage and poor finishes | Employ coolant and control speeds |
Material deformation | Stainless steel can distort under stress | Adjust machining parameters to reduce strain |
7. How Does Stainless Steel Machining Affect the Environment?
The environmental impact of stainless steel machining is an often-overlooked aspect of the manufacturing process. While stainless steel is a highly durable and corrosion-resistant material, the machining process itself can have significant environmental implications. Waste management is one of the biggest concerns in machining, as it involves cutting metal that can produce waste materials like chips and swarf.
What’s the real story here? Proper recycling and disposal of these materials are essential to reduce waste and lower environmental impact. Many machining facilities now implement recycling programs that allow them to reuse metal scraps, which can be melted down and repurposed for future use, minimizing waste in the long term.
Additionally, energy consumption during CNC machining is another area for improvement. The high power requirements for running CNC machines and tools can result in significant energy consumption. However, some manufacturers are shifting toward more energy-efficient systems to reduce their carbon footprint. By investing in energy-saving technologies and improving operational efficiency, companies can lower their environmental impact.
Table 7: Environmental Impact of Stainless Steel Machining
Environmental Issue | Auswirkungen | Minderungsstrategien |
---|---|---|
Abfallaufkommen | Metal scraps and swarf create waste | Implement recycling programs and reuse materials |
Energieverbrauch | CNC machines consume significant energy | Invest in energy-efficient machines and practices |
Pollution | Coolants and lubricants can pollute | Use environmentally friendly coolants and proper disposal methods |
8. What Tools Are Best for CNC Machining Stainless Steel?
Selecting the right tools for CNC machining stainless steel is critical to achieving high-quality results. Stainless steel is a tough material, and using the wrong tools can lead to increased wear, longer machining times, and lower precision. So, what tools are best suited for this job?
Ready for the good part? Carbide tools are commonly used for machining stainless steel because they are harder and more wear-resistant than regular high-speed steel (HSS) tools. They can withstand the heat generated during machining, which is essential when working with stainless steel. In addition, tools with coatings such as titanium nitride (TiN) can further increase durability and reduce friction.
However, tool selection doesn’t end with carbide. Cermet tools, a mixture of ceramic and metal, are also ideal for high-speed machining of stainless steel. These tools offer excellent wear resistance and maintain their sharpness longer, making them particularly useful in high-volume production.
Table 8: Recommended Tools for CNC Machining Stainless Steel
Tool Type | Am besten für | Vorteile |
---|---|---|
Carbide Tools | Allgemeine Bearbeitung | High heat resistance, long tool life |
Cermet Tools | Hochgeschwindigkeitsbearbeitung | Excellent wear resistance, sharpness retention |
High-Speed Steel (HSS) Tools | Low-volume machining | Cost-effective, versatile |
9. How Do You Maintain Precision During Stainless Steel CNC Machining?
Precision is key when machining stainless steel. The material’s hardness means that even minor variations in tool alignment or machine settings can lead to significant errors. To maintain high precision, manufacturers need to focus on regular machine calibration and careful control over machining parameters.
But here’s the kicker—temperature fluctuations and vibrations can also affect the accuracy of the CNC machine. Even slight changes in temperature can cause the machine’s components to expand or contract, leading to precision loss. To manage this, many manufacturers implement temperature-controlled environments and use vibration-damping systems.
Regular machine calibration is essential to ensure that CNC machines are working at their optimal performance. Regularly checking the alignment of the machine and ensuring that cutting tools are sharp and free from defects will help keep the process running smoothly and reduce errors.
Table 9: Best Practices for Maintaining CNC Machine Precision
Üben | Beschreibung | Vorteile |
---|---|---|
Regular Calibration | Ensure machines are calibrated to exact specifications | Maintains accuracy, prevents errors |
Vibration Control | Use dampers or isolation tables to reduce machine vibrations | Enhances precision, minimizes tool wear |
Tool Maintenance | Regularly check and replace tools | Prevents errors, ensures consistent results |
10. What Are the Different Grades of Stainless Steel Used in Machining?
Stainless steel comes in various grades, each offering different characteristics depending on the intended application. The most common grades used in machining include 304, 316, and 410 stainless steel, among others. Each grade has its unique properties, which influence how it should be machined.
What’s the real story here? 304 stainless steel is the most commonly used grade due to its excellent corrosion resistance and ease of machining. It’s ideal for general applications like kitchen equipment, medical devices, and food processing. On the other hand, 316 stainless steel is more resistant to corrosion, especially in marine environments, but it’s more challenging to machine due to its toughness. Lastly, 410 stainless steel is commonly used in automotive and fasteners but is less resistant to corrosion.
Understanding the properties of each grade helps manufacturers select the right material for the job, ensuring the best performance and cost-effectiveness.
Table 10: Comparison of Common Stainless Steel Grades
Stainless Steel Grade | Hauptmerkmale | Best Uses |
---|---|---|
304 Stainless Steel | Corrosion-resistant, easy to machine | Kitchen equipment, food processing |
316 Stainless Steel | Highly corrosion-resistant, tougher | Marine environments, medical devices |
410 Stainless Steel | Wear-resistant, strong | Automotive parts, fasteners |
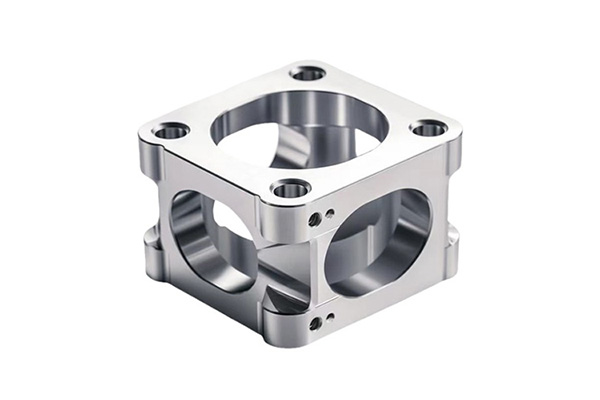
11. How Do Tolerances Work in Stainless Steel CNC Machining?
In stainless steel CNC machining, tolerances are critical. Tolerances define the allowable variation in a part’s dimensions. The tighter the tolerance, the more precise the machining must be. Understanding how tolerances work is key to producing parts that fit perfectly and perform reliably.
Ready for the good part? The type of tolerance required will depend on the application. For instance, parts that require a high degree of precision, such as those used in aerospace or medical applications, need tighter tolerances. This means that the machining process needs to be controlled carefully, with frequent checks to ensure the parts meet the required specifications.
It’s essential to select the right tools and techniques for achieving the desired tolerance. Advanced CNC machines with high precision, along with experienced operators, are crucial in producing parts that meet tight tolerance standards.
Table 11: Tolerance Ranges for Stainless Steel Parts
Tolerance Level | Type of Part | Suitable Applications |
---|---|---|
±0.005mm | Hochpräzise Teile | Aerospace, medical devices |
±0,1 mm | Allgemeine Bearbeitung | Automotive, general manufacturing |
±0,5 mm | Low-precision parts | Structural components, non-critical parts |
12. What Are the Applications of Stainless Steel Machining?
The versatility of stainless steel CNC machining makes it indispensable across various industries. From the automotive sector to medical devices, stainless steel machining plays a pivotal role in producing parts that need to withstand high stress, extreme temperatures, and corrosive environments.
What’s the real story? Stainless steel parts are used in industries where durability and reliability are paramount. For instance, in the medical industry, stainless steel is used to manufacture surgical tools and implants, thanks to its corrosion resistance and biocompatibility. In the aerospace sector, stainless steel is used for critical components that must perform under extreme conditions. It’s also common in the food and beverage industry, where hygiene and corrosion resistance are essential.
Table 12: Industries That Use Stainless Steel Machining
Industrie | Anwendungen |
---|---|
Medizinisch | Surgical tools, implants |
Luft- und Raumfahrt | Engine components, fasteners |
Food & Beverage | Processing equipment, storage tanks |
Automobilindustrie | Exhaust systems, structural parts |
13. What Are the Costs Involved in Stainless Steel CNC Machining?
The cost of stainless steel CNC machining varies depending on a number of factors, including the complexity of the part, the grade of stainless steel, and the volume of production. While the material itself is more expensive than other metals, its durability and resistance to corrosion make it a long-term investment.
But here’s the kicker—the type of machining method used also affects the cost. Milling and turning tend to be more cost-effective for simple parts, but more complex processes like grinding or EDM can increase the price. Additionally, tooling and maintenance costs must be factored into the overall cost.
To optimize costs, manufacturers can look into process improvements, such as increasing machine efficiency or reducing material waste. For high-volume production, investing in more advanced CNC equipment may pay off in the long run.
Table 13: Factors Influencing the Cost of Stainless Steel Machining
Faktor | Beschreibung | Impact on Cost |
---|---|---|
Material Grade | Higher grades like 316 are more expensive | Increases material costs |
Machining Method | Complex methods like EDM cost more | Increases labor and equipment costs |
Volume of Production | Larger quantities reduce per-part cost | Lower cost per unit in high volume |
14. How Can You Improve Your Stainless Steel Machining Process?
Improving your stainless steel machining process involves several strategies. The first step is to invest in high-quality tools and machinery. This will not only improve the precision of your work but also reduce the time and cost of production. Additionally, optimizing your CNC machine settings—such as feed rates and cutting speeds—can help you achieve a better finish and extend the life of your tools.
But here’s the kicker—regular maintenance is crucial for ensuring that your machines are operating at peak efficiency. Clean and well-maintained equipment reduces the risk of breakdowns and ensures that you can achieve consistent, high-quality results.
Another way to improve your machining process is by implementing advanced technologies such as automation and AI-based monitoring systems. These innovations can help reduce human error, increase productivity, and enhance quality control.
Table 14: Strategies to Improve Stainless Steel Machining Efficiency
Strategy | Beschreibung | Auswirkungen |
---|---|---|
Tool Quality | Invest in high-performance tools | Improves precision, reduces wear |
Machine Optimization | Adjust cutting speeds and feeds | Enhances productivity, reduces costs |
Automation | Implement automated systems for monitoring | Increases consistency, reduces error |
15. What Are the Key Trends in Stainless Steel CNC Machining?
Stainless steel CNC machining continues to evolve with the introduction of new technologies and methods. One of the key trends is the increased use of automation in the machining process. Automated systems can monitor production in real-time, making adjustments as needed to improve efficiency and reduce human error.
What’s the real story here? Another emerging trend is the use of additive manufacturing, or 3D printing, in combination with traditional machining methods. This allows manufacturers to create more complex parts that may be difficult or impossible to produce using conventional methods.
Finally, advancements in CNC machine tools, including the use of AI and machine learning, are helping to improve precision and reduce setup times. These innovations are enabling manufacturers to produce higher-quality parts at a faster rate, ultimately leading to lower costs and more competitive pricing.
Table 15: Trends in Stainless Steel CNC Machining
Trend | Beschreibung | Potential Benefits |
---|---|---|
Automation | Use of automated systems to monitor and adjust machining | Increased efficiency, reduced human error |
Additive Manufacturing | 3D printing combined with CNC machining | Allows for more complex designs, reduced waste |
KI-Integration | AI-driven CNC machines for improved precision | Faster production, reduced setup time |
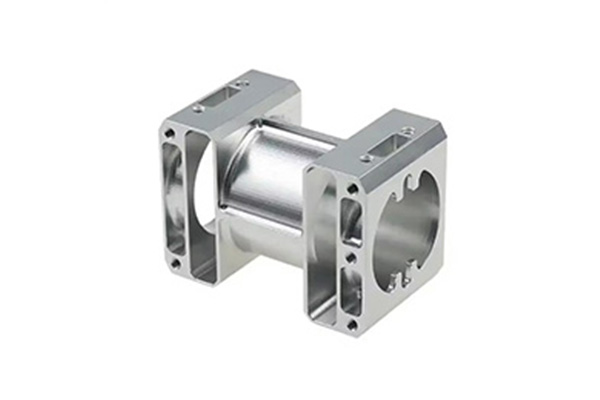
FAQ-Bereich
Frage 1: What is stainless steel machining?
Stainless steel machining is the process of using CNC machines to shape and form stainless steel into custom parts. It involves high-precision techniques and specialized tools to ensure that the final product meets exact specifications.
Frage 2: How does CNC machining work with stainless steel?
CNC machining works by using computer-controlled machines to cut, shape, and finish stainless steel parts. These machines offer high precision, allowing for intricate designs and tight tolerances to be achieved efficiently.
Frage 3: What are the common challenges in stainless steel machining?
Some of the common challenges include tool wear, heat generation, and the hardness of stainless steel, all of which can reduce machining efficiency and tool life if not managed properly.
Frage 4: How do you maintain stainless steel CNC machines?
Routine maintenance includes regular calibration, cleaning, and replacing worn-out parts to maintain accuracy and extend the life of the equipment.
Frage 5: What is the cost of stainless steel CNC machining?
The cost of stainless steel CNC machining depends on factors such as material grade, complexity of the part, tooling requirements, and production volume. However, optimized processes can reduce costs and improve efficiency.