Einführung in die CNC-Bearbeitungstoleranzen
CNC-Bearbeitung ist eine der präzisesten Fertigungsmethoden und ermöglicht die Herstellung von Teilen mit hoher Genauigkeit und Wiederholgenauigkeit. Ein entscheidender Faktor bei der CNC-Bearbeitung sind jedoch die Toleranzen, die die zulässigen Abweichungen in den Teileabmessungen definieren. Toleranzen sind unerlässlich, um die Passung und Funktion der Teile in der Endmontage sicherzustellen, insbesondere bei Sonderanfertigungen. Das Verständnis der verschiedenen Toleranzarten und ihrer Auswirkungen auf den Bearbeitungsprozess ist für Hersteller und Kunden gleichermaßen entscheidend. In diesem Leitfaden untersuchen wir die wichtigsten Aspekte von CNC-Bearbeitungstoleranzen, einschließlich ihrer Typen, der sie beeinflussenden Faktoren und wie sie hinsichtlich Kosteneffizienz und Präzision optimiert werden können.
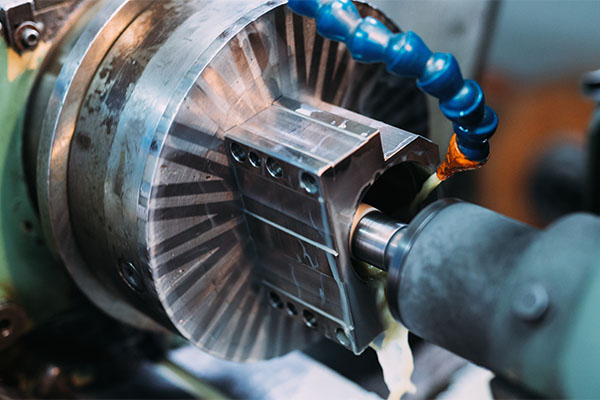
Was sind CNC-Bearbeitungstoleranzen?
Definition von Toleranzen bei der CNC-Bearbeitung
Toleranzen sind die zulässigen Abweichungen in den Abmessungen eines Teils. In der CNC-Bearbeitung bezeichnet dies, wie stark die tatsächlichen Abmessungen eines Teils von den vorgesehenen Konstruktionsmaßen abweichen können, ohne dass die Funktion beeinträchtigt wird. Im Wesentlichen definieren Toleranzen den Bereich, innerhalb dessen das Teil variieren kann, und stellen sicher, dass das Teil weiterhin korrekt in die vorgesehene Baugruppe passt.
Bei der CNC-Bearbeitung gibt es zwei Hauptarten von Toleranzen: Maßtoleranzen Und geometrische ToleranzenMaßtoleranzen bezeichnen die zulässige Abweichung von einem bestimmten Maß (wie Länge, Breite und Höhe), während geometrische Toleranzen die zulässigen Abweichungen in der Form eines Teils (wie Geradheit, Ebenheit oder Rundheit) beschreiben. Diese Toleranzen sind entscheidend für die korrekte Funktion und Kompatibilität von Teilen mit anderen Komponenten.
Warum Toleranzen bei der CNC-Bearbeitung entscheidend sind
Die Präzision einer CNC-Maschine wird maßgeblich durch ihre Fähigkeit bestimmt, enge Toleranzen einzuhalten. In Branchen wie der Luft- und Raumfahrt, der Automobilindustrie oder der Medizintechnik, wo Komponenten perfekt zusammenpassen müssen, sind Toleranzen besonders wichtig. Durch die Festlegung präziser Toleranzen können Hersteller sicherstellen, dass Teile die erforderliche Funktionalität erfüllen und unter Betriebsbedingungen zuverlässig arbeiten.
Sind die Toleranzen hingegen zu gering, erfüllt das fertige Teil möglicherweise nicht die gewünschten Leistungskriterien, was zu kostspieligen Fehlern oder Ausfällen führt. Zu enge Toleranzen wiederum können die Produktionskosten erhöhen und die Lieferzeiten unnötig verlängern. Das richtige Gleichgewicht ist entscheidend für Qualität und Kosteneffizienz.
Arten von CNC-Bearbeitungstoleranzen, die Sie kennen sollten
Maßtoleranzen
Maßtoleranzen geben an, wie stark die Abmessungen eines Teils vom Sollmaß abweichen dürfen. Dies sind die am häufigsten angegebenen Toleranzen in der CNC-Bearbeitung. Beispielsweise kann eine Welle eine Länge von 100 mm mit einer Toleranz von ±0,1 mm haben. Das bedeutet, dass die tatsächliche Länge zwischen 99,9 mm und 100,1 mm liegen kann und dennoch akzeptabel ist.
Maßtoleranzen können auf Längenmaße (wie Länge, Breite oder Höhe eines Teils) und Winkelmaße (wie Winkel zwischen Elementen) angewendet werden. Je enger die Toleranz, desto präziser muss die Messung sein. Dies erfordert oft moderne CNC-Maschinen und mehr Zeit für die Herstellung.
Geometrische Toleranzen
Geometrische Toleranzen dienen zur Steuerung der Form, Ausrichtung und Position von Bauteilmerkmalen. Diese Toleranzen sind entscheidend dafür, dass Teile wie vorgesehen zusammenpassen. Beispielsweise muss eine Bohrung perfekt rund sein oder sich an einer präzisen Position im Verhältnis zu anderen Bauteilmerkmalen befinden. Zu den geometrischen Toleranzen gehören:
- Geradheit: Stellt sicher, dass ein Merkmal, beispielsweise eine Kante oder Achse, vollkommen gerade ist.
- Ebenheit: Stellt sicher, dass eine Oberfläche innerhalb einer angegebenen Toleranz eben ist.
- Rundheit: Stellt sicher, dass ein Loch oder ein zylindrisches Element perfekt kreisförmig ist.
- Position: Definiert die genaue Position eines Features im Verhältnis zu anderen.
Durch die Angabe dieser geometrischen Toleranzen können Konstrukteure sicherstellen, dass die Teile die erforderlichen Funktionskriterien erfüllen.
Oberflächentoleranzen
Oberflächentoleranzen geben die Glätte der Oberfläche eines Teils an. In vielen Anwendungen kann die Oberflächenqualität entscheidend für die Leistung des Teils sein, insbesondere bei beweglichen oder mit anderen Teilen in Kontakt kommenden Komponenten. Die Oberflächengüte wird häufig anhand von Rauheitsmaßen wie Ra (durchschnittliche Rauheit), Rz (durchschnittliche maximale Höhe) und Ry (maximale Höhe des Profils) angegeben.
Warum Toleranzen wichtig sind: Die Auswirkungen auf Teilequalität und Funktionalität
Die Rolle von Toleranzen bei der Teilefunktionalität
Die während des Bearbeitungsprozesses angewendeten Toleranzen können die Funktionalität eines Teils erheblich beeinflussen. So können beispielsweise bei Automobil- oder Luftfahrtkomponenten kleine Abweichungen in den Abmessungen das Zusammenspiel der Teile beeinträchtigen und zu Problemen wie schlechter Passung, Ineffizienz oder sogar Versagen unter Belastung führen.
In manchen Fällen ist eine geringfügige Abweichung in Größe oder Form möglicherweise kein kritisches Problem. Bei Hochleistungsanwendungen wie Motorkomponenten, medizinischen Geräten oder hochpräzisen Instrumenten können jedoch selbst kleinste Toleranzverletzungen zu kostspieligen Fehlern und Produktausfällen führen. Daher ist es wichtig zu wissen, wie man für jedes Teil die richtige Toleranz wählt.
Toleranzen und Teilequalitätskontrolle
Toleranzen wirken sich direkt auf die Qualitätskontrolle aus. Enge Toleranzen erfordern anspruchsvollere Geräte und intensivere Prüfungen, um sicherzustellen, dass die Teile strengen Standards entsprechen. Qualitätskontrollmethoden wie Koordinatenmessgeräte (KMG) oder optische Messsysteme werden häufig eingesetzt, um zu überprüfen, ob die Teile innerhalb des vorgegebenen Toleranzbereichs liegen. Je höher die Toleranz, desto strenger ist der Prüfprozess.
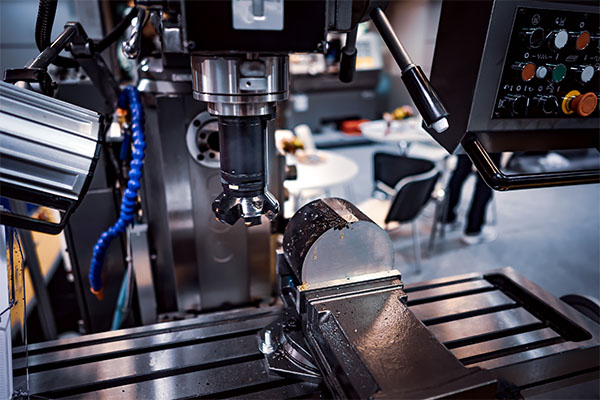
Faktoren, die die CNC-Bearbeitungstoleranzen beeinflussen
Materialeigenschaften und Toleranzen
Das für das Teil gewählte Material hat einen erheblichen Einfluss auf die erreichbaren Toleranzen. Manche Materialien, wie Metalle, sind stabiler und lassen sich leichter mit engen Toleranzen bearbeiten, während andere, wie Kunststoffe oder Verbundwerkstoffe, bei der Bearbeitung stärker verformen. Materialhärte, Wärmeausdehnung und Festigkeit spielen eine Rolle dabei, wie leicht ein Material enge Toleranzen einhalten kann.
Beispielsweise werden Metalle wie Edelstahl und Aluminium häufig für die CNC-Bearbeitung verwendet, da sie eine hervorragende Dimensionsstabilität bieten und enge Toleranzen ohne übermäßigen Werkzeugverschleiß erreichen können. Weichere Materialien wie Kunststoff oder Gummi erfordern jedoch möglicherweise besondere Überlegungen, um eine präzise Bearbeitung zu gewährleisten.
CNC-Maschinenfunktionen
Auch der Typ der verwendeten CNC-Maschine spielt eine entscheidende Rolle für die erreichbare Präzision. CNC-Maschinen haben unterschiedliche Genauigkeitsgrade, und jede Maschine hat ihre eigenen Grenzen, wenn es um die Einhaltung enger Toleranzen geht. Hochpräzise Maschinen, wie sie in der Luft- und Raumfahrtindustrie eingesetzt werden, können Toleranzen von ±0,001 mm oder sogar noch enger einhalten, während Allzweckmaschinen möglicherweise nur Toleranzen von ±0,05 mm erreichen.
Bei der Auswahl einer Maschine ist es wichtig, deren Leistungsfähigkeit an die Anforderungen des zu fertigenden Teils anzupassen. Wenn Sie die Grenzen Ihrer CNC-Maschine kennen, können Sie die richtige Toleranz für das Teil wählen und unnötige Anpassungen vermeiden, die die Kosten in die Höhe treiben könnten.
Werkzeuge und Verschleiß
Auch die Qualität der Werkzeuge und ihr Verschleiß können die Toleranzen bei der CNC-Bearbeitung beeinflussen. Verschleißende Werkzeuge können zu leichten Abweichungen in den Teilemaßen führen. Regelmäßige Wartung und Werkzeugwechsel sind entscheidend für die gleichbleibende Präzision.
Um den Werkzeugverschleiß zu reduzieren, verwenden viele Hersteller moderne Beschichtungen oder Hartmetallwerkzeuge, die langlebiger und scharfer sind. Darüber hinaus kann die Anpassung von Bearbeitungsparametern wie Drehzahl, Vorschub und Schnitttiefe zur Verbesserung der Präzision des fertigen Teils beitragen.
Gängige Toleranzbereiche bei der CNC-Bearbeitung für verschiedene Materialien
Toleranzen für Metallteile
Metallteile müssen oft sehr enge Toleranzen einhalten, insbesondere in Branchen wie der Luft- und Raumfahrt und der Automobilindustrie. Beispielsweise können Teile aus Edelstahl mit einer Toleranz von ±0,05 mm bearbeitet werden, während Teile aus Aluminium Toleranzen von bis zu ±0,025 mm erreichen können. Diese Toleranzen gewährleisten, dass Metallteile korrekt zusammenpassen und auch unter anspruchsvollen Bedingungen einwandfrei funktionieren.
Toleranzen für Kunststoffteile
Kunststoffteile hingegen lassen sich im Allgemeinen schwieriger mit den gleichen engen Toleranzen bearbeiten wie Metallteile. Die Toleranz für Kunststoffteile liegt typischerweise zwischen ±0,1 mm und ±0,5 mm, abhängig von der Kunststoffart und der Komplexität des Teils. Kunststoffe können sich aufgrund von Temperaturschwankungen verziehen, schrumpfen oder ausdehnen, was die Einhaltung gleichbleibender Toleranzen erschwert.
In einigen Fällen können Hochleistungskunststoffe wie PEEK oder PTFE für kritische Anwendungen verwendet werden. Diese Materialien ermöglichen engere Toleranzen, erfordern jedoch anspruchsvollere Bearbeitungstechniken.
Toleranzen für Verbundwerkstoffe
Verbundwerkstoffe, die häufig in der Luft- und Raumfahrt sowie im Automobilbau eingesetzt werden, stellen bei der CNC-Bearbeitung besondere Herausforderungen dar. Verbundwerkstoffe sind oft geschichtet und können je nach Faserrichtung unterschiedliche Eigenschaften aufweisen, was zu Schwankungen in der Festigkeit und Dimensionsstabilität des Bauteils führen kann. Die Toleranzen für Verbundteile liegen typischerweise zwischen ±0,1 mm und ±0,3 mm, abhängig vom jeweiligen Material und der Teilegeometrie.
Auswahl der richtigen Toleranzen für Ihre individuell gefertigten Teile
Ermittlung der Toleranzanforderungen
Die Wahl der richtigen Toleranzen für Ihre kundenspezifischen Teile beginnt mit dem Verständnis der spezifischen Funktion des Teils. Beispielsweise erfordern Teile, die zusammenpassen oder mit anderen Komponenten interagieren müssen, engere Toleranzen, um eine korrekte Ausrichtung und Funktionalität zu gewährleisten. Andererseits können Teile, die keine präzise Passung erfordern, mit geringeren Toleranzen konstruiert werden, um die Fertigungskosten zu senken.
Um die optimale Toleranz für ein Teil zu bestimmen, müssen sowohl die Konstruktionsanforderungen als auch die Möglichkeiten des Herstellungsprozesses berücksichtigt werden. Zu enge Toleranzen können die Produktionszeit, die Werkzeugkosten und die Fehlerwahrscheinlichkeit erhöhen, während zu große Toleranzen die Funktion oder Qualität des Teils beeinträchtigen können.
Präzision und Kosten im Gleichgewicht
Es mag zwar verlockend sein, möglichst enge Toleranzen festzulegen, um höchste Präzision zu gewährleisten, doch dies ist oft mit höheren Kosten verbunden. Das Erreichen engerer Toleranzen erfordert in der Regel modernere Maschinen, längere Bearbeitungszeiten und höhere Prüfkosten. Für viele Teile ist es kostengünstiger, Toleranzen festzulegen, die der beabsichtigten Funktion des Teils entsprechen, ohne die Präzision zu übertreiben.
Das richtige Gleichgewicht zwischen Toleranz und Kosten zu finden, ist der Schlüssel zum Erreichen von Qualität und Effizienz bei der kundenspezifischen Bearbeitung.
Wie sich Toleranzen auf die Kosten der CNC-Bearbeitung auswirken
Die Beziehung zwischen Toleranzen und Herstellungskosten
Bei der CNC-Bearbeitung besteht ein direkter Zusammenhang zwischen der Genauigkeit der Toleranzen und den Gesamtproduktionskosten. Engere Toleranzen erfordern in der Regel fortschrittlichere Technologie, höhere Präzision und mehr Zeit, um sicherzustellen, dass das Teil den Spezifikationen entspricht. Infolgedessen steigen die Fertigungskosten tendenziell mit der Notwendigkeit engerer Toleranzen. Dies liegt daran, dass in jedem Prozessschritt – vom ersten Entwurf bis zur Endkontrolle – mehr Detailgenauigkeit erforderlich ist.
Beispielsweise muss die Maschine bei der Bearbeitung eines Teils mit einer Toleranz von ±0,1 mm möglicherweise mehr Durchgänge ausführen oder Spezialwerkzeuge verwenden, um die gewünschten Abmessungen zu erreichen. Dies kann die Bearbeitungszeit und den Materialverbrauch erhöhen, was wiederum zu höheren Kosten führt. Andererseits benötigt die Herstellung eines Teils mit einer Toleranz von ±0,5 mm möglicherweise weniger Zeit oder Spezialausrüstung, was die Produktionskosten senkt.
Darüber hinaus erfordern Teile mit engeren Toleranzen oft eine strengere Qualitätskontrolle und -prüfung. Je nach Anwendung kann dies den Einsatz hochentwickelter Werkzeuge wie Koordinatenmessgeräte (KMGs), Laserscanner oder anderer hochpräziser Messgeräte erfordern. Die Kosten dieser Werkzeuge sowie der Zeitaufwand für die Prüfung jedes einzelnen Teils können sich bei der Herstellung von Komponenten mit sehr engen Toleranzen schnell summieren.
Wie Toleranzen die Vorlaufzeit beeinflussen
Toleranzen beeinflussen auch die Vorlaufzeit von CNC-Bearbeitungsprojekten. Teile mit engeren Toleranzen erfordern eine sorgfältigere Planung und mehr Zeit für den Bearbeitungsprozess. Beispielsweise kann die Bearbeitung eines Teils mit einer Toleranz von ±0,01 mm mehrere Stunden länger dauern als die eines ähnlichen Teils mit einer Toleranz von ±0,5 mm.
Der zusätzliche Zeitaufwand für die Einhaltung engerer Toleranzen kann den gesamten Produktionszeitplan verzögern, insbesondere bei Projekten mit mehreren Teilen oder komplexen Geometrien. Treten während des Prozesses Bearbeitungsfehler auf, müssen diese möglicherweise korrigiert werden, was zusätzliche Nacharbeit erfordert und die Vorlaufzeit weiter verlängert.
Um die Auswirkungen enger Toleranzen auf die Lieferzeit zu minimieren, müssen Hersteller den Bearbeitungsprozess oft sorgfältig planen und optimieren. Dies kann die Auswahl der richtigen Maschinen, die Anpassung der Schnittparameter und die Verwendung der effizientesten Werkzeugwege umfassen, um die termingerechte Fertigstellung des Teils zu gewährleisten.
Die Grenzen Ihrer CNC-Ausrüstung und -Werkzeuge verstehen
CNC-Maschinenpräzision und ihre Auswirkungen auf Toleranzen
Die Leistungsfähigkeit der eingesetzten CNC-Maschinen ist ein entscheidender Faktor für die erreichbare Präzision im Bearbeitungsprozess. Verschiedene CNC-Maschinentypen weisen unterschiedliche Genauigkeitsgrade auf. Es ist wichtig, die Grenzen der eingesetzten Maschinen zu kennen, um unrealistische Toleranzerwartungen zu vermeiden.
Beispielsweise können hochwertige CNC-Fräs- oder Drehmaschinen, die in der Luft- und Raumfahrt oder der Medizinbranche eingesetzt werden, Toleranzen von bis zu ±0,001 mm erreichen. Diese Maschinen nutzen fortschrittliche Technologien wie Mehrachsenfräsen, Laserkalibrierung und Echtzeit-Feedbacksysteme, um höchste Präzision zu gewährleisten.
Andererseits können herkömmliche CNC-Maschinen solche engen Toleranzen möglicherweise nicht einhalten, und die erreichbare Genauigkeit liegt möglicherweise nur bei ±0,05 mm oder ±0,1 mm. Um eine praktikable und kostengünstige Produktion zu gewährleisten, ist es wichtig, die erforderlichen Toleranzen des Teils an die Möglichkeiten der verfügbaren CNC-Maschinen anzupassen.
Auswahl der richtigen CNC-Maschine für den Job
Die Wahl der richtigen CNC-Maschine ist entscheidend für das Erreichen der gewünschten Toleranz. Bei engen Toleranzen und komplexen Geometrien kann beispielsweise die Investition in hochpräzise Maschinen wie CNC-Langdrehmaschinen oder 5-Achs-Fräsen erforderlich sein. Diese Maschinen ermöglichen die Bearbeitung komplexer Teile mit minimaler Fehlerquote, sind jedoch mit höheren Anschaffungskosten und längeren Produktionszeiten verbunden.
Für einfachere Teile mit geringeren Toleranzen kann jedoch eine Standard-CNC-Fräsmaschine ausreichen. Die Wahl der richtigen Maschine anhand der erforderlichen Toleranzen kann dazu beitragen, die Produktion zu rationalisieren, Kosten zu senken und sicherzustellen, dass das Teil den Qualitätsstandards entspricht.
Werkzeuge und Werkzeugverschleiß
Auch die Qualität und der Zustand der bei der CNC-Bearbeitung verwendeten Werkzeuge spielen eine wichtige Rolle für die Genauigkeit des Endprodukts. Mit der Zeit können sich Werkzeuge abnutzen, was zu Maßabweichungen und Abweichungen von den vorgegebenen Toleranzen führt. Daher sind regelmäßige Wartung und rechtzeitiger Werkzeugwechsel entscheidend für gleichbleibende Ergebnisse, insbesondere bei der Bearbeitung von Teilen mit engen Toleranzen.
Darüber hinaus können Material und Beschichtung des Werkzeugs dessen Langlebigkeit und Präzision beeinflussen. Hartmetallwerkzeuge beispielsweise behalten ihre Schärfe und Formstabilität über lange Zeit bei und eignen sich daher besonders für die hochpräzise CNC-Bearbeitung. Beschichtete Werkzeuge, beispielsweise mit Titannitrid (TiN) oder diamantähnlichem Kohlenstoff (DLC), tragen ebenfalls zur Verschleißreduzierung und Verlängerung der Werkzeuglebensdauer bei, was insbesondere bei der Bearbeitung schwieriger Materialien oder der Herstellung von Teilen mit engen Toleranzen wichtig ist.
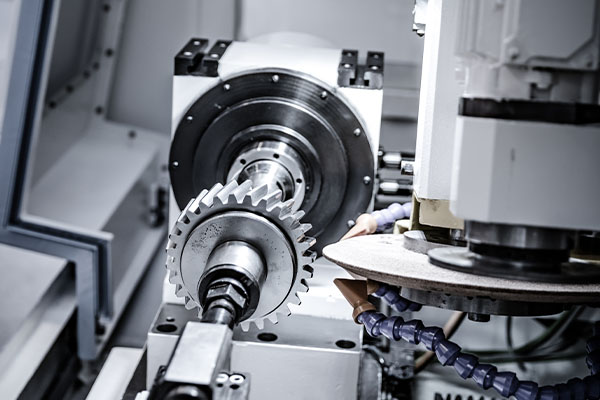
Toleranzoptimierung für schnellere Durchlaufzeiten und geringere Kosten
Präzision und Effizienz im Gleichgewicht
Enge Toleranzen sind zwar für bestimmte Anwendungen erforderlich, können aber zu längeren Lieferzeiten und höheren Produktionskosten führen. Eine der größten Herausforderungen bei der CNC-Bearbeitung besteht daher darin, das richtige Gleichgewicht zwischen Präzision und Effizienz zu finden. Das Erreichen der erforderlichen Toleranzen bei gleichzeitig niedrigen Produktionskosten und kurzen Durchlaufzeiten ist entscheidend, um die Kundenanforderungen zu erfüllen und wettbewerbsfähig zu bleiben.
Eine Möglichkeit, Toleranzen zu optimieren und gleichzeitig die Effizienz zu erhalten, besteht darin, sich auf die kritischen Abmessungen des Teils zu konzentrieren. Nicht alle Merkmale eines Teils müssen die engsten Toleranzen einhalten. Indem Hersteller die für die Funktionalität des Teils wichtigsten Abmessungen identifizieren und nur bei Bedarf engere Toleranzen anwenden, können sie Bearbeitungszeit und -kosten reduzieren, ohne die Leistung des Teils zu beeinträchtigen.
Rationalisierung des Bearbeitungsprozesses
Um die Bearbeitungszeit zu optimieren und Kosten zu senken, sollten Hersteller auch die Optimierung des Bearbeitungsprozesses in Betracht ziehen. Dies lässt sich durch die Wahl der richtigen Bearbeitungsstrategien erreichen, beispielsweise durch den Einsatz geeigneter Schneidwerkzeuge, die Anpassung der Vorschubgeschwindigkeiten und die Optimierung der Werkzeugwege. CNC-Maschinen mit erweiterten Automatisierungsfunktionen wie Werkzeugwechslern oder automatisierten Ladesystemen können ebenfalls dazu beitragen, den Zeitaufwand für unproduktive Aufgaben zu reduzieren und den Prozess weiter zu beschleunigen.
Eine weitere effektive Möglichkeit zur Optimierung von Toleranzen ist der Einsatz moderner Fertigungsverfahren wie der additiven Fertigung oder der Hybridbearbeitung. Diese Verfahren erreichen oft die gleiche Präzision wie die herkömmliche CNC-Bearbeitung und reduzieren gleichzeitig Materialabfall, Werkzeugverschleiß und Produktionszeit.
Beispiele aus der Praxis für Toleranzherausforderungen und -lösungen
Fallstudie 1: Luft- und Raumfahrtkomponente mit engen Toleranzen
In der Luft- und Raumfahrtindustrie müssen Teile wie Triebwerkskomponenten und Strukturelemente extrem enge Toleranzen einhalten, um Sicherheit und Leistung zu gewährleisten. Ein Beispiel aus der Praxis betraf eine speziell gefertigte Aluminiumhalterung für das Fahrwerk eines Flugzeugs. Die für dieses Teil erforderliche Toleranz betrug ±0,01 mm, was aufgrund der thermischen Ausdehnung des Materials und der komplexen Geometrie des Designs eine Herausforderung darstellte.
Um die engen Toleranzanforderungen zu erfüllen, setzte der Hersteller eine hochpräzise 5-Achsen-CNC-Maschine mit Laserkalibrierung ein. Zusätzlich implementierte er einen mehrstufigen Bearbeitungsprozess, der Präzisionsschruppen, Vorschlichten und Schlichten umfasste. Das Teil wurde zudem mehreren Qualitätskontrollen mit einer Koordinatenmessmaschine (KMG) unterzogen, um sicherzustellen, dass es die geforderten Spezifikationen erfüllte.
Fallstudie 2: Medizingerätekomponente mit komplexen Geometrien
In der Medizintechnik erfordern Komponenten wie chirurgische Instrumente und Implantate hohe Präzision, um ihre korrekte und sichere Funktion zu gewährleisten. Ein Beispiel hierfür war die Bearbeitung eines Titan-Knieimplantats, für die komplexe geometrische Toleranzen erforderlich waren, darunter präzise Rundheits- und Positionstoleranzen für die Löcher, in denen die Schrauben untergebracht werden sollten.
Um diese Toleranzen zu erreichen, verwendete der Hersteller eine CNC-Drehmaschine mit angetriebenen Werkzeugen. Dadurch konnte das Teil in einer einzigen Aufspannung bearbeitet werden, was das Fehlerrisiko durch Neupositionierung reduzierte. Anschließend wurde das Teil mit einem hochpräzisen optischen Messsystem geprüft, um sicherzustellen, dass alle geometrischen Toleranzen eingehalten wurden.
Qualitätskontrolle: Sicherstellung von Genauigkeit und Konsistenz bei der CNC-Bearbeitung
Die Bedeutung strenger Inspektionen
Die Qualitätskontrolle spielt eine entscheidende Rolle, um sicherzustellen, dass die Teile die vorgegebenen Toleranzen einhalten und den geforderten Standards entsprechen. Bei der CNC-Bearbeitung beginnt die Prüfung bereits beim Einrichten und wird während des gesamten Produktionszyklus fortgesetzt. Viele Hersteller nutzen Koordinatenmessgeräte (KMGs) und Laserscansysteme, um Teile präzise zu vermessen und Abweichungen von den gewünschten Spezifikationen zu erkennen.
Je nach Verwendungszweck des Teils kann die Inspektion auch Sichtprüfungen, die Beurteilung der Oberflächenbeschaffenheit und Funktionstests umfassen. Bei Teilen mit besonders engen Toleranzen können zusätzliche Prüfschritte erforderlich sein, um sicherzustellen, dass während des Bearbeitungsprozesses keine Abweichungen auftreten.
Die Rolle automatisierter Inspektionssysteme
Mit dem technologischen Fortschritt setzen viele Hersteller heute auf automatisierte Prüfsysteme, um die Präzision CNC-gefertigter Teile zu überwachen. Diese Systeme nutzen Laser, Kameras oder andere Sensoren, um die Abmessungen der Teile während der Produktion kontinuierlich zu überprüfen. Die automatisierte Prüfung verbessert nicht nur die Genauigkeit, sondern beschleunigt auch die Qualitätskontrolle. So können Hersteller Fehler frühzeitig erkennen und kostspielige Fehler vermeiden.
Kontinuierliche Verbesserung und Feedbackschleifen
Neben formalen Inspektionen sollten Hersteller kontinuierliche Verbesserungsprogramme implementieren, um die Bearbeitungsleistung langfristig zu überwachen. Durch die Verfolgung wichtiger Kennzahlen wie Werkzeugverschleiß, Maschinenleistung und Produktionsgenauigkeit können Hersteller Verbesserungspotenziale identifizieren und notwendige Anpassungen vornehmen, um enge Toleranzen dauerhaft einzuhalten.
Die Rolle von Toleranzen bei kundenspezifischen Bearbeitungsaufträgen
Kundenspezifische Bearbeitungs- und Toleranzspezifikationen
Bei der Auftragsvergabe für Sonderbearbeitungen sollten Kunden ihre Toleranzanforderungen klar kommunizieren, um Missverständnisse oder kostspielige Fehler zu vermeiden. Detaillierte Zeichnungen mit den gewünschten Toleranzen für jedes Bauteilmerkmal tragen zu einem reibungslosen Bearbeitungsprozess bei. Kunden sollten außerdem mit ihren Fertigungspartnern zusammenarbeiten, um zu prüfen, ob die angegebenen Toleranzen innerhalb des vorgegebenen Zeitrahmens und Budgets erreichbar sind.
Zusammenarbeit mit CNC-Bearbeitungslieferanten
Die Zusammenarbeit zwischen Kunde und Lieferant ist entscheidend, um sicherzustellen, dass Toleranzen klar verstanden und eingehalten werden. Dies kann die Besprechung der Materialauswahl, die Überprüfung der Leistungsfähigkeit der CNC-Anlage und die Sicherstellung einer optimierten Teilekonstruktion hinsichtlich Herstellbarkeit und Toleranzanforderungen umfassen.
Lieferanten können oft wertvolle Erkenntnisse liefern, wie Teiledesigns angepasst werden können, um die Bearbeitung zu erleichtern und gleichzeitig die Toleranzvorgaben einzuhalten. Durch die Zusammenarbeit können Hersteller und Kunden das optimale Gleichgewicht zwischen Präzision, Kosten und Lieferzeit erreichen.

FAQs
Was sind die gängigsten Toleranzen bei der CNC-Bearbeitung?
Die häufigsten Toleranzen für die CNC-Bearbeitung Die Toleranzen liegen je nach Komplexität und Material des Teils zwischen ±0,05 mm und ±0,5 mm. Für hochpräzise Anwendungen wie die Luft- und Raumfahrt oder medizinische Geräte sind in der Regel engere Toleranzen wie ±0,01 mm erforderlich.
Wie wirken sich Toleranzen auf die CNC-Bearbeitungskosten aus?
Engere Toleranzen erhöhen im Allgemeinen die Kosten der CNC-Bearbeitung, da sie modernere Ausrüstung, längere Bearbeitungszeiten und strengere Prüfungen erfordern. Engere Toleranzen können dazu beitragen, Kosten und Produktionszeiten zu senken.
Können durch CNC-Bearbeitung enge Toleranzen für alle Materialien erreicht werden?
Während viele Materialien, wie beispielsweise Metalle, mit CNC-Bearbeitung enge Toleranzen erreichen können, ist die hochpräzise Bearbeitung mancher Materialien, wie Kunststoffe und Verbundwerkstoffe, aufgrund ihrer inhärenten Eigenschaften schwieriger. Es ist wichtig, das richtige Material für die erforderliche Toleranz auszuwählen.
Wie kann ich die Kosten für die Bearbeitung von Teilen mit engen Toleranzen senken?
Um Kosten zu senken, konzentrieren Sie sich auf die Optimierung des Designs hinsichtlich der Herstellbarkeit. Geben Sie Toleranzen nur dort an, wo sie für die Funktion des Teils erforderlich sind, und wählen Sie das richtige Bearbeitungsverfahren und die passende Ausrüstung für die jeweilige Aufgabe. Die Zusammenarbeit mit dem Hersteller kann außerdem helfen, Bereiche zu identifizieren, in denen Kosten gesenkt werden können, ohne die Qualität zu beeinträchtigen.
Welche Werkzeuge eignen sich am besten, um bei der CNC-Bearbeitung enge Toleranzen zu erreichen?
Hartmetallwerkzeuge und beschichtete Werkzeuge, beispielsweise mit Titannitrid (TiN), eignen sich ideal zum Erreichen enger Toleranzen. Diese Werkzeuge bleiben länger scharf, wodurch das Risiko von Werkzeugverschleiß und Maßabweichungen reduziert wird.