Einführung
When it comes to manufacturing parts for industrial machinery, efficiency is key. Not only does it reduce costs, but it also ensures timely production and high-quality output. The manufacturing process for industrial machinery parts involves a series of steps, from selecting the right materials to ensuring that the final product meets stringent quality standards. In this article, we will explore how to manufacture parts for industrial machinery efficiently. We will discuss common types of industrial machinery parts, the importance of choosing the right manufacturing methods, the role of CNC machining, and much more. Let’s dive right in!
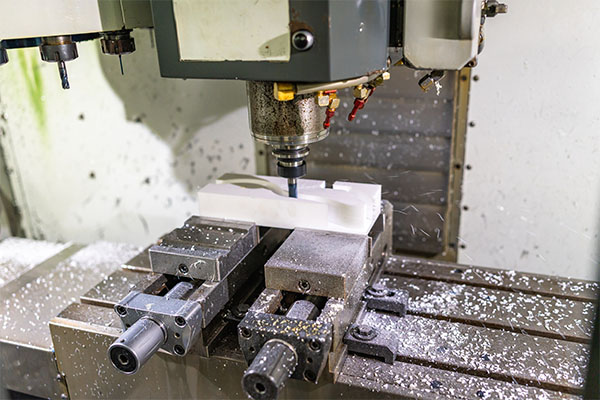
1. How Can You Efficiently Manufacture Parts for Industrial Machinery?
Efficiency in the manufacturing of industrial machinery parts is not just a buzzword; it’s a necessity. But here’s the kicker – manufacturing efficiency doesn’t just happen. It requires a well-planned process that minimizes waste, maximizes productivity, and ensures precision. Efficient manufacturing can lead to faster production cycles, reduced material waste, and ultimately, lower costs for your business.
The first step toward manufacturing efficiency is understanding the manufacturing processes available. Each process, such as casting, machining, or injection molding, has its own set of strengths and weaknesses. Choosing the right process for the job can significantly affect efficiency. For instance, CNC machining offers precision and speed, making it an ideal choice for parts that require tight tolerances. However, for bulk production of parts with less intricate designs, casting may be more efficient and cost-effective.
Another crucial factor is the use of advanced manufacturing technology. Automation, such as robotic arms for assembly or automated testing machines, helps streamline operations. Automation reduces the chances of human error, increases speed, and improves consistency across parts. This is where the real value lies – integrating technology to make your processes more efficient.
Table: Common Manufacturing Processes and Their Applications
Manufacturing Process | Am besten für | Vorteile | Nachteile |
---|---|---|---|
CNC-Bearbeitung | Precision parts | High precision, speed, and flexibility | Higher initial cost |
Casting | Bulk parts with simple designs | Cost-effective for large quantities | Limited to less complex designs |
Spritzguss | Complex, mass-produced parts | Fast production, suitable for plastics | High mold design cost |
2. What Are the Most Common Types of Industrial Machinery Parts?
When you think of industrial machinery, you likely picture large, complex machines built to perform heavy-duty tasks. But what about the individual parts that make these machines work? Here’s the real story – those parts are just as important, if not more, because they ensure that machinery operates smoothly and efficiently.
The most common types of industrial machinery parts include gears, shafts, bearings, and housings. Each part plays a crucial role in the functioning of the machinery. For example, gears are used to transfer motion and torque between machine components, while bearings reduce friction, allowing parts to move smoothly. Shafts are essential for transferring rotational motion, and housings protect other parts from external elements like dust and moisture.
When it comes to manufacturing these parts, precision is key. A gear that is even slightly off in terms of its teeth or dimensions can cause the entire machine to malfunction. Similarly, a bearing that doesn’t fit properly can lead to excessive wear and tear. That’s why it’s important to select the right manufacturing process for each type of part.
Table: Common Types of Industrial Machinery Parts and Their Functions
Part Type | Funktion | Materials Used | Common Manufacturing Methods |
---|---|---|---|
Gears | Transfer motion and torque | Steel, alloy | CNC machining, casting |
Shafts | Transfer rotational motion | Steel, titanium | CNC machining, forging |
Bearings | Reduce friction and support rotating parts | Steel, ceramic, plastic | CNC machining, injection molding |
Housings | Protect machine components from the environment | Aluminum, steel | Casting, CNC machining |
3. How Do You Choose the Right Manufacturing Method for Parts?
Choosing the right manufacturing method is where efficiency starts to shine. Ready for the good part? The decision you make on the method can make or break the quality and cost-effectiveness of the final product.
There are many different methods for manufacturing parts, each with its own advantages and disadvantages. The choice of method depends on several factors, including the complexity of the part, the materials used, and the required production volume.
For complex parts that require tight tolerances and high precision, CNC machining is usually the best option. CNC machines can create intricate designs with great accuracy, ensuring that each part meets the required specifications. On the other hand, for high-volume production, methods like injection molding or casting may be more suitable as they can produce large quantities at a lower cost per unit.
But wait, there’s more. When deciding on a manufacturing method, it’s also essential to consider the material being used. Some materials, like aluminum, are easier to machine and mold than others, like titanium, which is much harder and requires specialized equipment. Understanding the interaction between material properties and manufacturing methods can prevent delays and reduce waste.
Table: Comparing Manufacturing Methods Based on Material and Complexity
Manufacturing Method | Am besten für | Materialverträglichkeit | Complexity Level |
---|---|---|---|
CNC-Bearbeitung | Hochpräzise Teile | Metals, plastics, ceramics | Hoch |
Spritzguss | Mass production of complex parts | Plastics, some metals | Medium |
Casting | Simple parts in bulk | Metals, alloys | Niedrig |
4. What Role Does CNC Machining Play in Industrial Machinery Manufacturing?
You might be wondering, why is CNC machining so popular in industrial machinery manufacturing? The answer lies in its ability to provide unmatched precision and flexibility. This is where it gets interesting – CNC machining allows manufacturers to create parts that meet exact specifications, which is crucial for machinery that needs to perform in demanding environments.
CNC (Computer Numerical Control) machines are used to automate the process of machining. The process involves using pre-programmed computer software to control the movement of machinery, allowing for precise cutting, drilling, and shaping of materials. This makes CNC machining ideal for parts that require tight tolerances and intricate designs, like gears and bearings.
But here’s the kicker – CNC machines can be used with a variety of materials, including metals, plastics, and ceramics. This makes them incredibly versatile and suitable for different types of industrial machinery. Whether you need to produce a small batch of custom parts or large quantities of standard components, CNC machining can handle it all.
Table: Materials Compatible with CNC Machining
Material | Vorteile | Häufige Anwendungen |
---|---|---|
Stahl | Strong, durable, corrosion-resistant | Gears, shafts, frames |
Aluminium | Lightweight, corrosion-resistant | Housings, brackets |
Titan | High strength, corrosion-resistant | Aerospace, medical parts |
Plastik | Lightweight, easy to mold | Casings, enclosures |
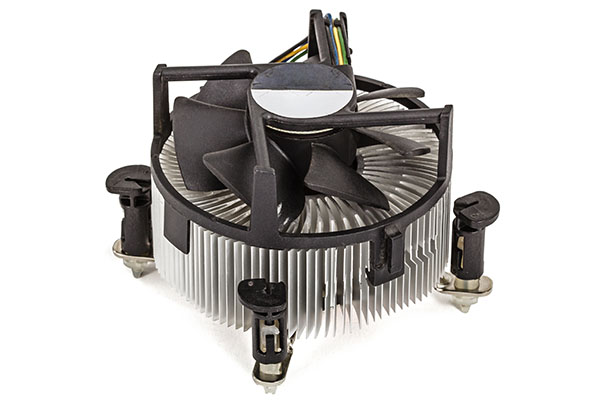
5. What Are the Key Steps in the Manufacturing Process for Industrial Machinery Parts?
Manufacturing industrial machinery parts involves several key steps, each crucial for ensuring the final product meets the required specifications. These steps, when done correctly, ensure that your parts are produced efficiently and to the highest quality standards.
The process begins with design and prototyping. A CAD (Computer-Aided Design) model is created to visualize the part, and a prototype may be produced to test fit, function, and durability. Once the design is approved, the material selection process begins. Materials are chosen based on the part’s intended function, the conditions it will face, and its cost-effectiveness.
After material selection, the actual manufacturing process begins. Depending on the part, this could involve casting, machining, welding, or other methods. During this phase, precision is critical. Any deviation from the original design can result in parts that don’t fit or function as intended. Once the parts are manufactured, they undergo testing and quality control to ensure they meet the necessary standards.
Table: Key Steps in the Industrial Machinery Manufacturing Process
Schritt | Beschreibung | Verwendete Tools/Methoden |
---|---|---|
Design and Prototyping | Create CAD models and prototypes | CAD software, 3D printing |
Material Selection | Choose materials based on function and cost | Material testing, supplier evaluation |
Herstellung | Actual production of the part | CNC machining, casting, welding |
Qualitätskontrolle | Test and inspect parts for defects | Visual inspection, testing machines |
6. How Do You Ensure Quality Control in the Manufacturing of Industrial Machinery Parts?
Quality control is one of the most important steps in the manufacturing process for industrial machinery parts. The consequences of poor-quality parts can be severe – they can cause machinery breakdowns, reduce efficiency, and lead to expensive repairs. So, how do you ensure the highest standards of quality? Well, it starts with the right processes in place.
Quality control involves testing parts at various stages of the manufacturing process. First, raw materials are tested for consistency and strength. During the production process, the parts are checked for any defects, such as cracks, misalignments, or surface imperfections. After production, the final parts undergo rigorous testing to ensure they meet the required tolerances.
What’s the real story? The best manufacturers use advanced inspection techniques, such as non-destructive testing (NDT), to detect issues that might not be visible to the naked eye. These tests allow for the detection of cracks, inclusions, or other flaws that could affect the part’s performance.
Table: Common Quality Control Methods Used in Manufacturing
Quality Control Method | Purpose | Equipment Used |
---|---|---|
Visual Inspection | Identify surface defects | Magnifying glass, microscope |
Dimensional Inspection | Ensure parts meet size and tolerance | Calipers, micrometers |
Non-Destructive Testing (NDT) | Detect internal flaws | Ultrasonic testers, X-ray |
7. How Do You Manage Costs in Industrial Machinery Part Manufacturing?
Managing costs in industrial machinery part manufacturing is a delicate balance. You don’t want to sacrifice quality, but you also want to keep your operations cost-effective. Ready for the good part? There are strategies that can help you manage costs while still producing high-quality parts.
The first step is understanding the cost breakdown. This includes not only material costs but also labor, overhead, and machine maintenance. One way to reduce costs is by optimizing the production process to eliminate waste and improve efficiency. For example, using lean manufacturing principles can help identify areas where time or materials are being wasted.
Another way to manage costs is through technology. Investing in automation or advanced manufacturing technologies can lead to long-term savings. Automation reduces the need for manual labor, improves consistency, and speeds up production.
Table: Key Factors in Managing Manufacturing Costs
Faktor | How to Manage Cost | Strategies |
---|---|---|
Material Costs | Select cost-effective materials | Bulk purchasing, supplier negotiation |
Labor Costs | Reduce manual labor | Automation, process optimization |
Overhead Costs | Minimize energy and facility usage | Energy-efficient machinery, facility upgrades |
8. What Are the Challenges in Manufacturing Parts for Industrial Machinery?
Manufacturing parts for industrial machinery comes with its fair share of challenges. From production delays to quality control issues, these challenges can affect the entire manufacturing process. But wait, there’s more. Understanding these challenges and having strategies in place to address them can help ensure smoother operations.
One common challenge is supply chain disruptions. Delays in raw material delivery can halt production, leading to costly downtime. Another challenge is the complexity of some parts. As machinery becomes more advanced, the parts needed to assemble them become more intricate, which can lead to difficulties in production.
To mitigate these challenges, manufacturers must be proactive. This includes maintaining strong relationships with suppliers, investing in predictive maintenance to avoid machine breakdowns, and continuously improving the manufacturing process.
Table: Common Challenges in Machinery Part Manufacturing
Herausforderung | Auswirkungen | Lösungen |
---|---|---|
Supply Chain Disruptions | Delayed production, increased costs | Build supplier relationships, diversify suppliers |
Complex Parts | Difficulty in production and quality control | Use advanced manufacturing techniques |
Machine Downtime | Production delays, increased costs | Predictive maintenance, regular machine checks |
9. How Do Technological Advancements Impact Industrial Machinery Part Manufacturing?
Technological advancements have revolutionized industrial machinery part manufacturing. From automation to 3D printing, new technologies have increased efficiency, reduced costs, and improved precision. But here’s the kicker – these advancements don’t just change how we make parts; they change what’s possible.
Automation, for example, has transformed the way parts are assembled. Robotic arms can now perform tasks like welding or painting with higher speed and accuracy than human workers. Similarly, 3D printing allows for the creation of highly customized parts with complex geometries that would be impossible to manufacture using traditional methods.
But here’s the real story – these advancements are not just about making parts faster. They’re also about making them better. With technologies like CNC machining and additive manufacturing, manufacturers can create parts with higher precision, ensuring that they perform better and last longer.
Table: Impact of Technological Advancements on Manufacturing
Technologie | Impact on Manufacturing | Vorteile |
---|---|---|
CNC-Bearbeitung | Increased precision and flexibility | Higher quality, faster production |
3D Printing | Allows for complex geometries | Custom parts, reduced waste |
Automation | Speeds up production, reduces errors | Lower labor costs, increased efficiency |
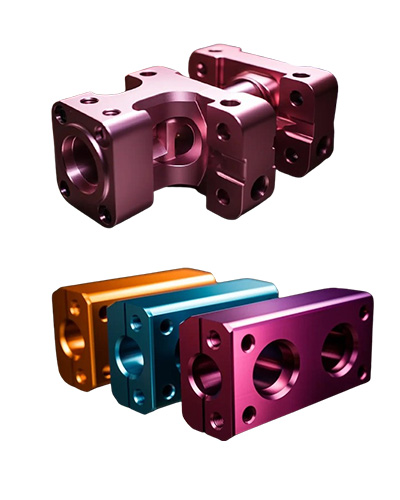
10. What Materials Are Best for Manufacturing Industrial Machinery Parts?
The material you choose for manufacturing industrial machinery parts plays a crucial role in the performance and durability of the part. Ready for the good part? Selecting the right material can drastically improve the lifespan of machinery and reduce the likelihood of failure.
Steel is one of the most commonly used materials for industrial machinery parts due to its strength, durability, and versatility. It’s perfect for parts that need to withstand heavy loads, such as gears and shafts. Aluminum, on the other hand, is lighter and corrosion-resistant, making it ideal for housings and brackets.
Other materials, such as titanium, are used in more specialized applications, like aerospace and medical machinery parts, due to their high strength-to-weight ratio and resistance to corrosion. The material choice directly affects the manufacturing process, so it’s important to consider the part’s requirements before making a decision.
Table: Common Materials Used in Industrial Machinery Parts
Material | Eigenschaften | Häufige Anwendungen |
---|---|---|
Stahl | Strong, durable, versatile | Gears, shafts, frames |
Aluminium | Lightweight, corrosion-resistant | Housings, brackets |
Titan | High strength, corrosion-resistant | Aerospace, medical parts |
Plastik | Lightweight, easy to mold | Casings, enclosures |
11. What Safety Measures Are Needed in Industrial Machinery Part Manufacturing?
Safety is paramount in industrial machinery part manufacturing. This is where it gets interesting – ensuring the safety of your workers not only protects them but also reduces the risk of production delays and costly mistakes. But how do you make sure that your manufacturing environment is as safe as possible?
First, proper equipment and machine safety is crucial. All machines should be fitted with safety guards, emergency stop buttons, and automatic shutoff mechanisms. Workers should be trained on how to properly use each piece of equipment to avoid accidents.
Additionally, personal protective equipment (PPE) is essential. Workers should wear gloves, safety goggles, and other protective gear to prevent injuries from flying debris, high temperatures, or chemicals. Regular safety audits and maintenance checks also help identify potential hazards before they cause problems.
Table: Essential Safety Measures in Machinery Part Manufacturing
Safety Measure | Beschreibung | Tools/Equipment Needed |
---|---|---|
Machine Safety Guards | Prevent accidents and injuries from moving parts | Safety guards, emergency stops |
PPE (Personal Protective Equipment) | Protect workers from hazards like debris and chemicals | Gloves, goggles, helmets |
Regular Safety Audits | Identify potential hazards early | Safety audit tools, checklists |
12. How Do You Handle Complex and Customized Parts for Industrial Machinery?
When it comes to industrial machinery, sometimes standard parts just won’t do. But here’s the kicker – handling complex and customized parts requires more skill, precision, and flexibility. Customized parts are often necessary for unique machinery or specific customer needs.
To create these parts, you need to collaborate closely with engineers and designers. Computer-aided design (CAD) software is typically used to design the parts, and then advanced manufacturing methods like CNC machining or 3D printing are used to produce them. These technologies allow manufacturers to create highly intricate and precise parts that wouldn’t be possible with traditional methods.
Custom parts also require a more personalized approach in terms of materials. Depending on the function of the part, you might need to select a material that provides specific strength, resistance to wear, or heat tolerance.
Table: Methods for Manufacturing Complex and Customized Parts
Verfahren | Am besten für | Vorteile |
---|---|---|
CNC-Bearbeitung | Hochpräzise Teile | Customizability, precision |
3D Printing | Complex, intricate designs | Speed, reduced waste |
Spritzguss | High-volume production of custom parts | Cost-effective for bulk production |
13. What Are the Environmental Considerations in Manufacturing Industrial Machinery Parts?
Environmental sustainability is a growing concern in industrial manufacturing. But wait, there’s more – addressing environmental impact is not just about being green, it’s also about optimizing your manufacturing process to reduce costs. Sustainable practices can lead to long-term savings, and in some cases, may even attract customers who prioritize eco-friendly businesses.
One of the main environmental considerations is waste management. Industrial machinery part manufacturers should focus on minimizing waste by recycling materials and using efficient cutting and molding techniques. Additionally, energy consumption is a major factor. By using energy-efficient machines and practices, manufacturers can reduce their carbon footprint while also cutting down on utility costs.
Sustainable material selection is another key factor. Materials that are recyclable or biodegradable are increasingly being used in manufacturing, especially for parts that will not be subject to heavy wear and tear.
Table: Environmental Considerations in Machinery Part Manufacturing
Consideration | Lösung | Vorteile |
---|---|---|
Waste Management | Recycling materials, efficient cutting | Reduces waste, saves resources |
Energy Consumption | Energy-efficient machinery, solar power | Lower energy costs, reduced carbon footprint |
Sustainable Materials | Use of recyclable or biodegradable materials | Eco-friendly, attracts environmentally-conscious clients |
14. How Can You Improve Efficiency in the Manufacturing Process?
Improving efficiency in the manufacturing process is an ongoing goal for every business. Ready for the good part? There are several strategies you can implement to boost efficiency while maintaining high-quality standards.
One of the most effective methods is lean manufacturing. This involves eliminating waste in the production process, improving workflow, and enhancing worker productivity. By identifying bottlenecks and eliminating them, you can speed up production times without sacrificing quality.
Automation is another key factor in improving efficiency. Automated machinery can perform repetitive tasks faster and with greater accuracy than humans. By incorporating robotics and automated systems into your production lines, you can achieve faster turnaround times and reduce the need for manual labor.
Table: Strategies for Improving Manufacturing Efficiency
Strategy | Beschreibung | Vorteile |
---|---|---|
Lean Manufacturing | Eliminate waste, improve workflow | Faster production, reduced costs |
Automation | Use of robots and automated systems | Increased speed, consistency |
Employee Training | Improve skills and knowledge | Enhanced productivity, fewer errors |
15. How Do You Ensure Timely Delivery of Industrial Machinery Parts?
Ensuring timely delivery of industrial machinery parts is critical for customer satisfaction and maintaining smooth operations. What’s the real story? Delays can have a domino effect, disrupting your customers’ schedules and causing ripple effects down the supply chain.
Effective scheduling and logistics management are key to ensuring timely delivery. By accurately estimating production times and planning ahead, you can avoid bottlenecks that might delay delivery. It’s also crucial to maintain strong relationships with suppliers and shipping partners to ensure a smooth flow of materials and finished parts.
Predictive analytics is becoming increasingly popular in manufacturing. By using data to forecast production needs and potential delays, manufacturers can proactively address issues before they become problems.
Table: Strategies for Timely Delivery of Industrial Machinery Parts
Strategy | Beschreibung | Vorteile |
---|---|---|
Accurate Scheduling | Plan production and shipping in advance | Avoid delays, maintain flow |
Strong Supplier Relationships | Ensure timely material supply | Minimized disruptions |
Prädiktive Analytik | Use data to forecast production needs | Proactive issue resolution |
Abschluss
In this article, we’ve explored how to manufacture parts for industrial machinery efficiently. We’ve covered the importance of choosing the right manufacturing methods, the role of CNC machining, and how technology impacts the industry. By focusing on precision, sustainability, and efficient processes, manufacturers can produce high-quality parts while reducing costs and increasing productivity. To stay competitive in this field, adopting the right tools and strategies is essential.

FAQs
In this article, we’ve explored how to manufacture parts for industrial machinery efficiently. We’ve covered the importance of choosing the right manufacturing methods, the role of CNC machining, and how technology impacts the industry. By focusing on precision, sustainability, and efficient processes, manufacturers can produce high-quality parts while reducing costs and increasing productivity. To stay competitive in this field, adopting the right tools and strategies is essential.
Frage 1: What is industrial machinery part manufacturing?
Industrial machinery part manufacturing refers to the production of components that are essential to the operation of industrial machines. These parts ensure that machinery performs its required tasks efficiently, reliably, and with minimal downtime. The process typically involves selecting appropriate materials, using precise manufacturing methods, and testing the finished parts for quality.
Frage 2: How does CNC machining work in manufacturing industrial parts?
CNC machining uses computer-controlled machines to perform precise operations like cutting, drilling, and milling on raw materials. This process allows for the high accuracy needed in industrial machinery parts, making it ideal for parts with complex shapes or tight tolerances. The use of CNC machines ensures consistency and speed, improving overall manufacturing efficiency.
Frage 3: What materials are commonly used for manufacturing industrial machinery parts?
Common materials include steel, aluminum, titanium, and plastics. Steel is used for high-strength components like gears and shafts, while aluminum is popular for lightweight parts like housings and brackets. Titanium is often selected for parts that require high strength-to-weight ratios, and plastics are used for components that need to be lightweight and easy to mold.
Frage 4: How can I reduce costs when manufacturing industrial machinery parts?
Cost reduction in industrial machinery part manufacturing can be achieved by optimizing the production process, minimizing waste, and selecting cost-effective materials without sacrificing quality. Automation and lean manufacturing practices can also help reduce labor costs and improve efficiency, while bulk purchasing of materials may lead to savings on raw materials.
Frage 5: What safety measures should be in place for industrial machinery part manufacturing?
Safety measures include proper training for workers on equipment usage, regular maintenance of machines, and safety protocols like the use of personal protective equipment (PPE), such as gloves, goggles, and helmets. Machines should be fitted with safety guards and emergency stop buttons to prevent accidents, and regular safety audits should be conducted to identify and mitigate potential risks.