Introduction
In the rapidly evolving landscape of artificial intelligence, the demand for powerful GPUs has skyrocketed, bringing with it unprecedented cooling challenges. As organizations deploy increasingly dense clusters of high-performance GPUs to train and run complex AI models, the question of how to effectively cool these systems has become paramount. This comprehensive guide explores the various cooling solutions available for enterprise GPU deployments, comparing their effectiveness, efficiency, and suitability for different AI workloads.
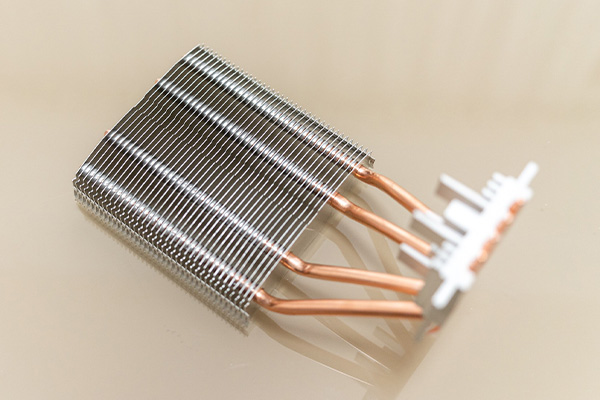
The Critical Role of Cooling in AI Infrastructure
The exponential growth of AI has fundamentally transformed data center cooling requirements, creating challenges that traditional approaches struggle to address.
Problem: Modern AI GPUs generate unprecedented heat loads that threaten performance, reliability, and operational efficiency.
Today’s high-performance AI accelerators like NVIDIA’s H100 or AMD’s MI300 can generate thermal loads exceeding 700 watts per device—more than double what previous generations produced just a few years ago. When deployed in dense configurations, these heat loads can overwhelm traditional cooling systems.
Aggravation: AI workloads typically drive GPUs to sustained maximum utilization, eliminating the thermal “recovery periods” common in other computing workloads.
Unlike traditional computing tasks that create variable loads with periods of lower utilization, AI training workloads often maintain GPUs at 95-100% utilization for days or weeks at a time. This sustained thermal output eliminates the “recovery periods” that cooling systems typically rely on to maintain equilibrium.
Solution: Understanding the critical role of cooling in AI infrastructure enables more effective system design and technology selection:
Thermal Impact on AI Performance
The relationship between temperature and GPU performance is direct and significant:
- Thermal Throttling Mechanisms:
- Modern GPUs automatically reduce clock speeds when temperature thresholds are exceeded
- Performance reductions of 10-30% are common during thermal throttling events
- Memory bandwidth may also be restricted during thermal events
- Throttling can occur at the chip, board, or system level
- Performance impact is often non-linear with temperature increases
- AI-Specific Performance Implications:
- Training convergence can be affected by performance inconsistency
- Batch processing throughput directly correlates with sustained performance
- Inference latency increases during thermal throttling
- Distributed training synchronization issues can arise from uneven cooling
- Reproducibility challenges emerge with variable thermal conditions
- Economic Impact of Thermal Limitations:
- Extended training times increase operational costs
- Reduced inference throughput affects service capacity
- Hardware utilization efficiency decreases
- Competitive disadvantage from slower development cycles
- Diminished return on expensive GPU investments
Here’s what makes this fascinating: Research indicates that inadequate cooling can reduce the effective computational capacity of AI infrastructure by 15-40%, essentially negating much of the performance advantage of premium GPU hardware. This “thermal tax” means that organizations may be realizing only 60-85% of their theoretical computing capacity due to cooling limitations, fundamentally changing the economics of AI infrastructure.
Reliability and Longevity Considerations
Thermal conditions significantly impact hardware reliability:
- Temperature-Related Failure Mechanisms:
- Semiconductor degradation accelerates at higher temperatures
- Thermal cycling creates mechanical stress on components
- Solder joint fatigue increases with temperature fluctuations
- Memory errors become more frequent at elevated temperatures
- Power delivery components are particularly vulnerable to thermal stress
- Reliability Statistics:
- Each 10°C increase approximately doubles component failure rates
- GPUs operating consistently above 75°C show 2-3x higher failure rates
- Thermal cycling causes more damage than steady-state high temperatures
- Cooling system failures account for 30-40% of data center outages
- Mean time between failures (MTBF) decreases exponentially with temperature
- Economic Implications of Reliability:
- Replacement costs for premium AI GPUs ($10,000-40,000 each)
- Downtime costs during hardware replacement
- Data and model corruption risks
- Engineering resources diverted to maintenance
- Disruption to AI development and deployment timelines
But here’s an interesting phenomenon: The relationship between cooling quality and hardware longevity is non-linear. Research shows that improving cooling to maintain GPU temperatures below 65°C rather than 85°C can extend useful lifespan by 50-100%, potentially doubling the effective value of hardware investments. This “reliability multiplier” means that premium cooling solutions often pay for themselves through reduced hardware replacement costs alone, even before considering performance benefits.
Energy Efficiency Impact
Cooling approach significantly affects overall energy efficiency:
- Cooling Energy Requirements:
- Traditional data center cooling: 40-60% of IT energy consumption
- Advanced cooling approaches: 10-30% of IT energy consumption
- PUE (Power Usage Effectiveness) implications
- Total energy cost per AI computation
- Carbon footprint considerations
- Temperature Effect on GPU Efficiency:
- Semiconductor leakage current increases with temperature
- Higher temperatures reduce power efficiency
- Energy consumption for equivalent computation increases
- Compound effect with cooling energy requirements
- Total energy cost optimization opportunities
- Economic and Environmental Considerations:
- Energy represents 25-40% of AI infrastructure TCO
- Carbon regulations and reporting requirements
- Corporate sustainability commitments
- Public perception and ESG considerations
- Competitive advantage from efficiency
Impact of Cooling Approach on AI Infrastructure Efficiency
Cooling Method | Typical PUE | GPU Efficiency Impact | Total Energy Overhead | Relative Carbon Footprint |
---|---|---|---|---|
Legacy Air Cooling | 1.8-2.2 | -5 to -15% | 85-135% | Very High |
Optimized Air Cooling | 1.4-1.8 | -3 to -10% | 45-90% | High |
Direct Liquid Cooling | 1.1-1.4 | -1 to -5% | 15-45% | Moderate |
Immersion Cooling | 1.03-1.15 | 0 to -3% | 3-18% | Low |
Ready for the fascinating part? The most advanced cooling approaches don’t just reduce cooling energy—they fundamentally transform the energy economics of AI computing. By enabling higher GPU efficiency through lower operating temperatures while simultaneously reducing cooling overhead, technologies like immersion cooling can reduce total energy costs by 40-60% compared to traditional approaches. This dramatic efficiency improvement is creating a paradigm shift where cooling is increasingly viewed not as an infrastructure cost but as a strategic investment in computational efficiency.
Air Cooling Solutions for Enterprise GPUs
Air cooling remains the most widely deployed approach for GPU thermal management, though it faces increasing challenges with the latest high-performance AI accelerators.
Problem: Traditional air cooling struggles to effectively dissipate the thermal output of modern AI GPUs, particularly in dense deployments.
The fundamental physics of air cooling—limited thermal capacity of air and constraints on airflow volume—create inherent limitations that are increasingly challenged by GPUs generating 400-700+ watts of heat.
Aggravation: Density requirements for AI clusters exacerbate air cooling challenges by limiting airflow and creating compound heating effects.
Further complicating matters, AI deployments typically cluster multiple high-power GPUs in close proximity, creating thermal interaction effects where the heat from one device affects others, further reducing cooling effectiveness.
Solution: Advanced air cooling approaches and appropriate deployment architectures can extend the viability of air cooling for many AI applications:
Traditional Air Cooling Approaches
Understanding conventional air cooling methods and their limitations:
- Passive Heatsink Cooling:
- Heat spreader and heatsink designs
- Fin density and surface area considerations
- Material selection (copper, aluminum, composites)
- Thermal interface materials
- Effective TDP range: up to 150-200W
- Active Fan Cooling:
- Fan types and airflow characteristics
- Push vs. pull configurations
- Static pressure vs. airflow volume
- Noise and reliability considerations
- Effective TDP range: up to 250-350W
- Ducted and Directed Airflow:
- Airflow channeling and management
- Inlet and exhaust considerations
- Recirculation prevention
- Pressure differential management
- Effective TDP range: up to 300-400W
Here’s what makes this fascinating: The physics of air cooling creates a non-linear relationship between cooling capacity and energy consumption. Doubling the cooling capacity typically requires more than triple the fan power due to the cubic relationship between fan speed and power consumption. This diminishing return means that beyond certain thermal densities (approximately 350-400W per GPU), air cooling becomes prohibitively inefficient, creating a practical ceiling that the latest AI accelerators have already exceeded.
Advanced Air Cooling Technologies
Innovative approaches extending air cooling capabilities:
- Heat Pipe and Vapor Chamber Technologies:
- Operating principles and thermal physics
- Implementation in GPU cooling solutions
- Performance characteristics and limitations
- Integration with traditional heatsinks
- Effective TDP range: up to 350-450W
- High-Performance Air Coolers:
- Multi-fan configurations
- Advanced fin designs and materials
- Optimized airflow patterns
- Integration with server chassis design
- Effective TDP range: up to 400-500W
- Synthetic Jet Cooling:
- Pulsed air technology principles
- Boundary layer disruption benefits
- Implementation in confined spaces
- Combination with traditional approaches
- Effective TDP range: up to 400-500W
But here’s an interesting phenomenon: The effectiveness of advanced air cooling technologies varies significantly with altitude. At sea level, these solutions may effectively cool 450-500W devices. However, at data center locations above 3,000 feet elevation, cooling capacity can decrease by 10-15% due to lower air density. At elevations above 6,000 feet, capacity may decrease by 20-30%, creating situations where cooling solutions that work perfectly in coastal data centers may fail in mountain or high-plateau locations.
Deployment Architectures for Air Cooling
System-level approaches to maximize air cooling effectiveness:
- GPU Spacing and Arrangement:
- Minimum spacing requirements by TDP
- Linear vs. matrix arrangements
- Thermal interaction considerations
- Airflow path optimization
- Trade-offs between density and cooling
- Server and Rack Design Considerations:
- Front-to-back vs. top-to-bottom airflow
- GPU orientation options
- Fan placement and redundancy
- Inlet temperature management
- Hot/cold aisle implementation
- Facility-Level Optimizations:
- Raised floor vs. overhead cooling
- Containment systems (hot/cold aisle)
- Supplemental cooling approaches
- Airflow management best practices
- Temperature setpoint optimization
Air Cooling Deployment Density Guidelines by GPU TDP
GPU TDP Range | Maximum GPUs per 1U | Recommended GPUs per 2U | Minimum Spacing | Maximum Rack Density |
---|---|---|---|---|
200-250W | 4 | 8 | 15mm | 40-48 GPUs |
250-350W | 2 | 4-6 | 25mm | 24-32 GPUs |
350-450W | 1 | 2-4 | 35mm | 16-24 GPUs |
450-550W | Not recommended | 2 | 50mm | 10-16 GPUs |
550W+ | Not viable | Not recommended | N/A | N/A |
Limitations and Practical Considerations
Understanding the boundaries of air cooling for AI applications:
- Physical and Practical Limitations:
- Thermal capacity of air (specific heat capacity)
- Volumetric constraints on airflow
- Fan power and noise limitations
- Temperature delta requirements
- Practical upper limit around 450-500W per GPU
- Operational Challenges:
- Dust accumulation and maintenance requirements
- Filter replacement schedules
- Fan failure detection and redundancy
- Airflow monitoring and management
- Temperature variation across devices
- Economic Considerations:
- Initial capital cost advantages
- Higher operational costs at scale
- Energy efficiency disadvantages
- Density and space utilization impact
- Total cost of ownership calculations
Ready for the fascinating part? The most sophisticated air-cooled AI deployments are now implementing dynamic workload scheduling based on thermal conditions. These systems continuously monitor temperature across GPU clusters and intelligently distribute workloads to maintain optimal thermal conditions. This “thermally-aware scheduling” can improve effective cooling capacity by 15-25% compared to static approaches, extending the viability of air cooling for higher-TDP devices. However, this approach introduces computational overhead and complexity that must be balanced against the cooling benefits.
Liquid Cooling Technologies
Liquid cooling has emerged as the preferred solution for high-density AI deployments, offering superior thermal performance and efficiency compared to air cooling.
Problem: The thermal output of modern AI accelerators exceeds the practical capabilities of air cooling, necessitating more effective heat transfer methods.
With thermal densities exceeding 0.5-1.0 W/mm² and total package power reaching 400-700+ watts, modern AI GPUs generate heat beyond what air cooling can effectively dissipate, particularly in dense deployments.
Aggravation: The trend toward higher GPU power consumption shows no signs of abating, with next-generation AI accelerators potentially exceeding 1000W.
Further complicating matters, the computational demands driving GPU power increases continue to grow exponentially with larger AI models, creating a thermal trajectory that will further challenge cooling technologies in coming generations.
Solution: Liquid cooling technologies offer significantly higher thermal transfer efficiency, enabling effective cooling of even the highest-power AI accelerators:
Direct Liquid Cooling Fundamentals
Understanding the principles and implementation of direct liquid cooling:
- Operating Principles:
- Direct contact between cooling plates and heat sources
- Liquid circulation through cooling plates
- Heat transfer to facility cooling systems
- Closed-loop vs. facility water implementations
- Temperature, flow, and pressure management
- Thermal Advantages:
- Water’s superior thermal capacity (4x air)
- Higher heat transfer coefficients
- More efficient transport of thermal energy
- Reduced temperature differentials
- Effective cooling of 600W+ devices
- System Components:
- Cold plates (direct contact with GPUs)
- Manifolds and distribution systems
- Pumps and circulation equipment
- Heat exchangers
- Monitoring and control systems
Here’s what makes this fascinating: The thermal transfer efficiency of liquid cooling creates a non-linear advantage over air cooling as TDP increases. For 250W GPUs, liquid cooling might offer a 30-40% efficiency advantage. For 500W GPUs, this advantage typically grows to 60-80%, and for 700W+ devices, liquid cooling can be 3-5x more efficient than even the most advanced air cooling. This expanding advantage creates an economic inflection point where the additional cost of liquid cooling is increasingly justified by performance and efficiency benefits as TDP increases.
Cold Plate Design and Technology
The interface between GPUs and cooling liquid is critical to system performance:
- Cold Plate Materials and Construction:
- Copper vs. aluminum base materials
- Microchannel vs. jet impingement designs
- Surface finish and contact optimization
- Corrosion resistance considerations
- Manufacturing techniques and precision
- Thermal Interface Materials:
- Liquid metal vs. traditional thermal compounds
- Pad vs. paste applications
- Compression and mounting pressure
- Long-term stability and pump-out concerns
- Application techniques and coverage
- Flow Optimization:
- Serial vs. parallel configurations
- Flow rate requirements
- Pressure drop considerations
- Temperature rise calculations
- Turbulent vs. laminar flow dynamics
But here’s an interesting phenomenon: The design of cold plates has evolved from general-purpose to GPU-specific implementations. Early liquid cooling solutions used generic cold plates with limited contact with GPU components. Modern designs feature GPU-specific cold plates with tailored contact for dies, memory, and VRMs, improving cooling efficiency by 30-50%. The most advanced designs now include active flow control that dynamically adjusts cooling to different GPU regions based on workload characteristics, further improving efficiency and performance.
Distribution and Infrastructure
System-level considerations for liquid cooling implementation:
- Manifold and Distribution Systems:
- Server-level distribution
- Rack-level manifolds
- Quick-connect coupling technologies
- Leak prevention and detection
- Maintenance and serviceability
- Pumping and Circulation:
- Centralized vs. distributed pumping
- Redundancy and reliability
- Flow rate monitoring and control
- Pressure management
- Energy efficiency considerations
- Heat Rejection Options:
- Liquid-to-liquid heat exchangers
- Cooling distribution units (CDUs)
- Direct facility water integration
- Dry coolers and radiators
- Cooling towers and evaporative options
Liquid Cooling System Architectures Comparison
Architecture | Advantages | Disadvantages | Best For | Typical Efficiency |
---|---|---|---|---|
Direct Facility Water | Simplest, lowest cost | Facility water quality concerns | Small deployments | Very High |
CDU with Secondary Loop | Isolation from facility water | Additional cost and complexity | Medium deployments | High |
In-Row CDU | Reduced piping, simplified deployment | Higher per-rack cost | Small/medium clusters | High |
Centralized CDU | Economies of scale, centralized management | Extensive piping infrastructure | Large deployments | Moderate-High |
Rack-Level Closed Loop | Self-contained, minimal facility impact | Limited heat rejection options | Edge deployments | Moderate |
Implementation and Operational Considerations
Practical aspects of deploying liquid cooling for AI infrastructure:
- Facility Requirements:
- Water quality specifications
- Supply temperature and flow capacity
- Pressure requirements
- Backup and redundancy provisions
- Monitoring and control integration
- Operational Procedures:
- Commissioning and filling protocols
- Leak testing methodologies
- Maintenance schedules and procedures
- Water treatment and quality monitoring
- Emergency response planning
- Reliability and Risk Management:
- Leak detection and prevention systems
- Condensation monitoring and control
- Component reliability statistics
- Failure mode analysis
- Mitigation strategies and redundancy
Ready for the fascinating part? The operational reliability of modern liquid cooling systems now exceeds that of traditional air cooling in many deployments. While early liquid cooling implementations raised concerns about leaks and reliability, data from large-scale deployments shows that current enterprise-grade liquid cooling solutions experience 70-80% fewer cooling-related failures than equivalent air-cooled systems. This reliability advantage stems from fewer moving parts (elimination of multiple fans), reduced dust-related issues, and more consistent operating temperatures. This reversal of the traditional reliability assumption is fundamentally changing risk assessments for cooling technology selection.
Immersion Cooling Systems
Immersion cooling represents the frontier of thermal management for the most demanding AI workloads, offering unmatched performance and efficiency.
Problem: Even direct liquid cooling faces challenges with the highest-density AI deployments and next-generation accelerators.
As GPU power consumption approaches and potentially exceeds 1000W per device, even traditional liquid cooling approaches face increasing implementation challenges and efficiency limitations.
Aggravation: The trend toward specialized AI hardware with non-standard form factors creates additional cooling challenges.
Further complicating matters, the emergence of custom AI accelerators, specialized AI ASICs, and heterogeneous computing systems creates cooling requirements that traditional approaches struggle to address uniformly and efficiently.
Solution: Immersion cooling provides a comprehensive solution that addresses current extreme cooling requirements while offering headroom for future generations:
Immersion Cooling Fundamentals
Understanding the principles and implementation of immersion cooling:
- Operating Principles:
- Complete immersion of computing hardware in dielectric fluid
- Direct contact between fluid and all components
- Elimination of thermal interfaces for most components
- Convection-based heat transfer within the fluid
- Heat extraction through fluid circulation and heat exchangers
- Thermal Advantages:
- Elimination of hotspots through uniform cooling
- Superior cooling for irregular form factors
- Elimination of air as a thermal transfer medium
- Reduced temperature differentials across components
- Effective cooling regardless of component arrangement
- System Components:
- Immersion tanks and containment systems
- Dielectric cooling fluids
- Circulation and pumping systems
- Heat rejection equipment
- Filtration and fluid maintenance systems
Here’s what makes this fascinating: Immersion cooling fundamentally changes the relationship between component density and cooling efficiency. In traditional cooling, increasing density creates compound cooling challenges as components affect each other’s thermal environment. In immersion systems, cooling efficiency remains relatively constant regardless of component density, enabling theoretical density improvements of 5-10x compared to air cooling. This density advantage creates cascading benefits for facility space utilization, interconnect latency, and overall system performance.
Single-Phase vs. Two-Phase Immersion
Comparing the two primary approaches to immersion cooling:
- Single-Phase Immersion:
- Non-boiling fluid operation
- Circulation-based heat transfer
- Simpler implementation and management
- Lower cooling efficiency than two-phase
- More mature technology with broader adoption
- Two-Phase Immersion:
- Fluid boiling at component surfaces
- Phase-change heat transfer (highly efficient)
- Passive circulation through convection
- Higher cooling efficiency
- More complex fluid management
- Comparative Considerations:
- Cooling efficiency: Two-phase 20-40% more efficient
- Implementation complexity: Single-phase simpler
- Fluid cost: Two-phase typically higher
- Operational experience required: Two-phase more demanding
- Future scaling capability: Two-phase superior
But here’s an interesting phenomenon: The efficiency advantage of two-phase immersion over single-phase varies significantly with heat density. For moderate-density deployments (15-25 kW per rack equivalent), the efficiency difference might be only 10-15%. For extreme density deployments (50+ kW per rack equivalent), the advantage can grow to 30-50%. This variable efficiency delta creates deployment scenarios where single-phase is more economical for moderate deployments while two-phase becomes increasingly advantageous for the highest densities.
Fluid Technologies and Considerations
The cooling fluid is central to immersion system performance:
- Fluid Properties and Selection Criteria:
- Dielectric strength (electrical insulation)
- Thermal capacity and conductivity
- Viscosity and flow characteristics
- Chemical compatibility with components
- Environmental and safety considerations
- Common Fluid Types:
- Engineered hydrocarbons
- Synthetic esters
- Fluorocarbons
- Newer sustainable alternatives
- Application-specific formulations
- Operational Considerations:
- Fluid lifetime and degradation factors
- Replacement and top-off requirements
- Filtration and maintenance needs
- Handling and safety procedures
- Cost and availability factors
Immersion Cooling Fluid Comparison
Fluid Type | Thermal Efficiency | Environmental Impact | Cost Range | Lifespan | Best For |
---|---|---|---|---|---|
Engineered Hydrocarbons | High | Low-Moderate | $$ | 5-7 years | General purpose |
Synthetic Esters | High | Low | $$$ | 7-10 years | Environmentally sensitive |
Fluorocarbons | Very High | High | $$$$ | 5-8 years | Two-phase applications |
Mineral Oil | Moderate | Low | $ | 3-5 years | Budget-conscious |
Next-Gen Sustainable | High | Very Low | $$$$ | 8-10 years | Future-focused deployments |
Deployment and Infrastructure
System-level considerations for immersion cooling implementation:
- Tank and Containment Design:
- Open bath vs. sealed designs
- Materials and construction considerations
- Access and serviceability features
- Monitoring and safety systems
- Capacity and expansion capabilities
- Facility Integration:
- Floor loading requirements (significantly higher)
- Fluid handling and storage infrastructure
- Heat rejection integration
- Electrical and safety considerations
- Operational space requirements
- Hardware Compatibility Considerations:
- Component selection and qualification
- Server design modifications
- Connector and cabling adaptations
- Storage media considerations
- Warranty and support implications
Ready for the fascinating part? Immersion cooling is enabling entirely new approaches to system design that were previously impossible. With the elimination of traditional cooling constraints, some manufacturers are developing “cooling-native” hardware that abandons conventional form factors and thermal design limitations. These systems can achieve component densities 3-5x higher than traditional designs while simultaneously improving performance through shorter signal paths and more efficient power delivery. This fundamental rethinking of system architecture represents a potential inflection point in computing design, where thermal management becomes an enabler rather than a constraint for system architecture.
Hybrid Cooling Approaches
Hybrid cooling strategies combine multiple technologies to optimize performance, efficiency, and implementation complexity.
Problem: No single cooling technology is optimal for all components and deployment scenarios.
Different components within AI systems have varying thermal characteristics, form factors, and cooling requirements that may be better addressed by different cooling technologies.
Aggravation: The heterogeneous nature of modern AI infrastructure creates complex cooling requirements that single-technology approaches struggle to address optimally.
Further complicating matters, AI infrastructure increasingly combines different processor types, accelerators, memory technologies, and storage systems, each with unique thermal characteristics that may benefit from different cooling approaches.
Solution: Hybrid cooling strategies leverage the strengths of multiple technologies to create optimized solutions for complex AI infrastructure:
Targeted Liquid Cooling
Applying liquid cooling selectively to high-heat components:
- Implementation Approaches:
- GPU-only liquid cooling with air for other components
- CPU+GPU liquid cooling with air for supporting systems
- Component-specific cooling plate designs
- Integration with traditional air cooling
- Simplified liquid distribution compared to full liquid cooling
- Advantages and Limitations:
- Reduced implementation complexity vs. full liquid cooling
- Lower cost than comprehensive liquid solutions
- Addresses highest thermal loads directly
- Maintains compatibility with standard components
- Potential for uneven cooling across system
- Ideal Application Scenarios:
- Mixed-density AI infrastructure
- Retrofitting existing infrastructure
- Gradual transition strategies
- Budget-constrained implementations
- Moderate-density deployments
Here’s what makes this fascinating: Targeted liquid cooling often provides 80-90% of the benefits of comprehensive liquid cooling at 50-60% of the implementation cost and complexity. This favorable cost-benefit ratio makes it an increasingly popular approach for organizations transitioning from traditional infrastructure to AI-optimized cooling. The selective application of advanced cooling to only the highest-value, highest-heat components creates an efficient “cooling triage” that maximizes return on cooling investment.
Rear Door Heat Exchangers
Combining traditional air cooling with liquid-based heat capture:
- Operating Principles:
- Standard air-cooled servers and racks
- Water-cooled heat exchanger in rack door
- Hot exhaust air passes through heat exchanger
- Heat captured and removed via liquid
- Cooled air returned to data center
- Implementation Variations:
- Passive (convection-driven) vs. active (fan-assisted)
- Facility water vs. CDU implementations
- Varying cooling capacities (20-75kW per rack)
- Containment integration options
- Retrofit vs. new deployment designs
- Advantages and Limitations:
- Minimal changes to standard IT hardware
- Simplified implementation compared to direct liquid cooling
- Moderate improvement in cooling efficiency
- Limited maximum cooling capacity
- Potential for condensation in some environments
But here’s an interesting phenomenon: The effectiveness of rear door heat exchangers varies significantly with rack power density. At moderate densities (15-25kW per rack), they typically capture 80-90% of heat output. As density increases to 30-40kW, effectiveness often drops to 60-70% due to airflow constraints and heat exchanger capacity limitations. This declining efficiency with increasing density creates a practical ceiling that makes rear door heat exchangers ideal for transitional deployments but potentially insufficient for the highest-density AI clusters.
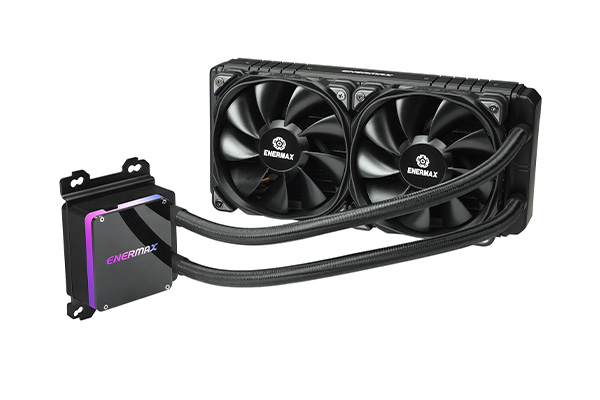
Evaporative and Adiabatic Approaches
Leveraging evaporative cooling principles for enhanced efficiency:
- Direct Evaporative Cooling:
- Adiabatic cooling of intake air
- Water evaporation for temperature reduction
- Integration with traditional air cooling
- Seasonal and climate-dependent operation
- Water consumption considerations
- Indirect Evaporative Approaches:
- Heat exchangers with evaporative secondary side
- Elimination of humidity introduction
- Reduced water consumption
- Higher efficiency than traditional cooling
- Climate-dependent effectiveness
- Hybrid Evaporative Systems:
- Combination with traditional cooling
- Seasonal operational modes
- Optimized for varying conditions
- Reduced mechanical cooling requirements
- Water and energy efficiency balance
Hybrid Cooling Approach Comparison
Approach | Implementation Complexity | Cooling Capacity | Energy Efficiency | Water Usage | Best For |
---|---|---|---|---|---|
Targeted Liquid Cooling | Moderate | High | High | None | High-density, mixed systems |
Rear Door Heat Exchanger | Low | Moderate | Moderate-High | None | Transitional deployments |
Direct Evaporative | Low | Moderate | Very High | High | Dry climates, moderate density |
Indirect Evaporative | Moderate | Moderate-High | High | Moderate | Various climates, mixed density |
Hybrid Evaporative | Moderate-High | High | Very High | Moderate | Large-scale, varying conditions |
Integration and Control Strategies
Optimizing performance across hybrid cooling systems:
- Unified Monitoring and Management:
- Integrated temperature monitoring
- Coordinated control systems
- Predictive analytics for optimization
- Failure detection and response
- Performance reporting and analysis
- Operational Mode Optimization:
- Weather and climate-based adjustments
- Workload-adaptive cooling strategies
- Energy price-responsive operation
- Maintenance-coordinated modes
- Emergency response configurations
- Efficiency Optimization Techniques:
- Machine learning for cooling prediction
- Dynamic workload placement
- Thermal-aware scheduling
- Adaptive setpoint management
- Continuous commissioning approaches
Ready for the fascinating part? The most sophisticated hybrid cooling implementations are now using AI techniques to optimize their own operation. These systems collect thousands of data points across cooling subsystems and use machine learning to predict thermal behavior, optimize resource allocation, and proactively adjust to changing conditions. These “AI-optimized cooling systems” have demonstrated 20-35% efficiency improvements compared to traditional control approaches while simultaneously improving cooling performance and reliability. This represents a fascinating case of AI technology being applied to solve challenges created by AI hardware itself.
Comparative Analysis of Cooling Technologies
Selecting the optimal cooling approach requires systematic comparison across multiple dimensions.
Problem: Organizations struggle to objectively compare cooling technologies with different strengths, limitations, and implementation requirements.
The diverse characteristics of cooling technologies—from performance and efficiency to implementation complexity and operational requirements—create challenges for direct comparison and selection.
Aggravation: Vendor claims and specifications often use inconsistent metrics and assumptions, further complicating objective comparison.
Further complicating matters, cooling technology vendors frequently use different testing methodologies, reference conditions, and performance metrics, making direct comparisons difficult without standardized evaluation frameworks.
Solution: A comprehensive, multi-dimensional comparison framework enables more objective technology evaluation and selection:
Thermal Performance Comparison
Evaluating raw cooling capabilities across technologies:
- Maximum Cooling Capacity:
- Air cooling: Up to 350-450W per GPU effectively
- Direct liquid cooling: Up to 1000W+ per GPU
- Immersion cooling: Essentially unlimited per GPU
- Hybrid approaches: Varies by implementation (400-700W)
- Practical deployment density limitations
- Temperature Management Precision:
- Air cooling: ±5-10°C typical variation
- Direct liquid cooling: ±2-5°C typical variation
- Immersion cooling: ±1-3°C typical variation
- Hybrid approaches: Varies by implementation
- Impact on performance consistency
- Thermal Response Characteristics:
- Air cooling: Slow response to load changes
- Direct liquid cooling: Moderate response time
- Immersion cooling: Excellent thermal stability
- Hybrid approaches: Varies by implementation
- Implications for variable workloads
Here’s what makes this fascinating: The thermal performance advantage of advanced cooling technologies increases non-linearly with GPU power. For 250W GPUs, the performance difference between air and liquid cooling might be 10-15°C. For 500W GPUs, this difference typically expands to 20-30°C, and for 700W+ devices, the difference can exceed 40°C. This expanding performance gap means that cooling technology selection becomes increasingly critical as GPU power increases, with advanced cooling shifting from optional to essential for the highest-power devices.
Energy Efficiency Comparison
Analyzing the energy implications of different cooling approaches:
- Cooling Energy Requirements:
- Air cooling: 25-40% of IT load
- Direct liquid cooling: 5-15% of IT load
- Immersion cooling: 3-7% of IT load
- Hybrid approaches: 10-25% of IT load
- Total energy cost implications
- PUE (Power Usage Effectiveness):
- Air-cooled AI clusters: 1.4-1.8 typical
- Liquid-cooled AI clusters: 1.1-1.3 typical
- Immersion-cooled AI clusters: 1.03-1.15 typical
- Hybrid approaches: 1.2-1.5 typical
- Annual energy cost differential
- GPU Efficiency Impact:
- Lower temperatures improve GPU power efficiency
- Reduced leakage current at lower temperatures
- Performance per watt improvements
- Compound effect with cooling efficiency
- Total energy consumption per computation
But here’s an interesting phenomenon: The efficiency advantage of advanced cooling varies significantly with climate and location. In moderate climates with year-round temperatures below 20°C, technologies like free air cooling with economizers can achieve efficiency comparable to liquid cooling for moderate-density deployments. In hot or tropical climates, the efficiency gap between air and advanced cooling expands dramatically, with liquid or immersion cooling potentially reducing energy costs by 50-70% compared to traditional approaches. This climate-dependent efficiency differential means that optimal cooling selection should vary by geographic location.
Implementation and Operational Comparison
Evaluating practical aspects of deployment and management:
- Implementation Complexity:
- Air cooling: Low complexity, standard practices
- Direct liquid cooling: Moderate-high complexity
- Immersion cooling: High complexity, specialized knowledge
- Hybrid approaches: Moderate complexity
- Expertise requirements and learning curve
- Facility Requirements:
- Air cooling: Standard data center design
- Direct liquid cooling: Significant plumbing infrastructure
- Immersion cooling: Specialized facility considerations
- Hybrid approaches: Moderate modifications
- Retrofit vs. new construction implications
- Operational Considerations:
- Maintenance requirements and frequency
- Monitoring complexity and requirements
- Specialized training and expertise needs
- Vendor ecosystem and support availability
- Operational risk profile
Comprehensive Cooling Technology Comparison
Factor | Air Cooling | Direct Liquid | Immersion | Hybrid |
---|---|---|---|---|
Max GPU TDP | 350-450W | 600-1000W+ | 1000W+ | 400-700W |
Density (GPUs/Rack) | 16-32 | 32-64 | 48-96 | 24-48 |
Energy Efficiency | Low | High | Very High | Moderate-High |
Implementation Complexity | Low | High | Very High | Moderate |
Capital Cost | $ | $$$ | $$$$ | $$ |
Operational Cost | $$$ | $ | $ | $$ |
Facility Impact | Moderate | High | Very High | Moderate-High |
Maintenance Complexity | Low | Moderate | High | Moderate |
Future Scalability | Limited | Good | Excellent | Moderate |
Noise Level | High | Low | Very Low | Moderate |
Economic Comparison
Analyzing the financial implications of cooling technology selection:
- Capital Expenditure Considerations:
- Initial hardware and infrastructure costs
- Installation and commissioning expenses
- Facility modification requirements
- Deployment timeline implications
- Financing and depreciation considerations
- Operational Expenditure Analysis:
- Energy costs over system lifetime
- Maintenance and support expenses
- Staffing and expertise requirements
- Consumables and replacement parts
- Insurance and risk management costs
- Total Cost of Ownership Calculation:
- 3-5 year TCO comparison
- Performance benefits monetization
- Reliability and downtime cost factors
- Scaling and expansion considerations
- Technology refresh implications
Ready for the fascinating part? The economic equation for cooling technology selection follows a distinct pattern based on deployment scale. For small deployments (under 100 GPUs), the implementation overhead of advanced cooling often outweighs efficiency benefits, making air cooling economically advantageous despite lower performance. For medium deployments (100-500 GPUs), hybrid approaches typically offer the best economics. For large deployments (500+ GPUs), the economies of scale fundamentally change the equation, making comprehensive liquid or immersion cooling increasingly economical despite higher initial costs. This “scale effect” means that optimal cooling technology selection should vary significantly based on deployment size.
Implementation Considerations
Successful cooling implementation requires careful planning and execution beyond technology selection.
Problem: Even the best cooling technology can fail to deliver expected results if implementation factors are not properly addressed.
Technology selection is only the first step in cooling optimization; implementation details, operational practices, and ongoing management significantly impact actual performance and reliability.
Aggravation: Many organizations focus primarily on technology selection while underestimating implementation and operational factors.
Further complicating matters, the gap between theoretical cooling performance and actual results is often wider than expected due to implementation details, creating performance shortfalls and operational challenges that could have been avoided with proper planning.
Solution: A comprehensive implementation approach that addresses all aspects of cooling deployment enables optimal results:
Planning and Assessment
Establishing a solid foundation for cooling implementation:
- Workload and Requirements Analysis:
- Current and future GPU types and TDPs
- Deployment density and scaling plans
- Performance and reliability requirements
- Budget and timeline constraints
- Facility capabilities and limitations
- Site and Facility Evaluation:
- Existing cooling infrastructure assessment
- Power availability and distribution
- Space and floor loading analysis
- Environmental conditions and constraints
- Regulatory and compliance considerations
- Technology Selection Process:
- Formal requirements documentation
- Multi-vendor evaluation framework
- Proof-of-concept testing
- Reference customer validation
- Total cost of ownership analysis
Here’s what makes this fascinating: The most successful cooling implementations typically spend 3-4x longer in the planning and assessment phase compared to average implementations. This extended planning process might seem excessive, but research shows it reduces implementation problems by 60-80% and typically results in 15-25% better performance and efficiency outcomes. This “planning multiplier effect” creates a compelling ROI for thorough assessment and planning despite the additional upfront time investment.
Deployment Best Practices
Ensuring optimal implementation of selected cooling technology:
- Phased Implementation Strategies:
- Pilot deployment and validation
- Scaling methodology and approach
- Migration planning for existing workloads
- Parallel operation considerations
- Testing and acceptance criteria
- Integration with Existing Infrastructure:
- Mechanical system connections
- Electrical integration requirements
- Control system coordination
- Monitoring system integration
- Operational handoff planning
- Quality Assurance Processes:
- Installation verification procedures
- Performance testing methodology
- Documentation requirements
- Training and knowledge transfer
- Commissioning and acceptance testing
But here’s an interesting phenomenon: The success rate of cooling implementations varies dramatically based on vendor experience with similar deployments. Vendors with 10+ similar implementations typically achieve 90-95% of projected performance in initial deployment. Vendors with fewer than 3 similar implementations often achieve only 60-75% of projected performance initially, requiring significant optimization to reach target levels. This “experience curve” effect means that vendor selection should heavily weight relevant experience, particularly for advanced cooling technologies.
Operational Optimization
Maximizing performance and efficiency through ongoing management:
- Monitoring and Management Systems:
- Comprehensive sensor deployment
- Real-time performance monitoring
- Predictive analytics implementation
- Alerting and response procedures
- Performance trending and analysis
- Operational Procedures Development:
- Standard operating procedures
- Emergency response protocols
- Maintenance schedules and procedures
- Staff training and certification
- Continuous improvement processes
- Performance Optimization Techniques:
- Setpoint optimization
- Flow balancing and adjustment
- Thermal mapping and hotspot identification
- Workload placement optimization
- Seasonal adjustment strategies
Cooling Implementation Success Factors
Success Factor | Impact Level | Best Practices | Common Pitfalls | Measurement Metrics |
---|---|---|---|---|
Requirements Definition | Very High | Detailed specification, stakeholder alignment | Incomplete requirements, unrealistic expectations | Requirement fulfillment percentage |
Vendor Selection | High | Experience-weighted evaluation, reference validation | Over-reliance on marketing claims, cost-only focus | Performance vs. specification |
Facility Preparation | Very High | Comprehensive assessment, adequate upgrades | Underestimating infrastructure needs | Infrastructure-related delays |
Implementation Planning | High | Detailed project plan, contingency provisions | Compressed timelines, inadequate resources | Schedule adherence, issue count |
Testing and Validation | Very High | Comprehensive testing protocol, performance verification | Inadequate testing, premature production deployment | Performance achievement percentage |
Operational Readiness | High | Staff training, procedure development | Inadequate knowledge transfer, missing procedures | Operational incident frequency |
Risk Management and Mitigation
Addressing potential challenges proactively:
- Risk Identification and Assessment:
- Systematic risk evaluation process
- Probability and impact analysis
- Risk prioritization methodology
- Stakeholder risk tolerance assessment
- Continuous risk monitoring
- Mitigation Strategy Development:
- Preventative measures implementation
- Contingency planning
- Redundancy and failover provisions
- Testing and validation of mitigations
- Response procedure development
- Business Continuity Considerations:
- Critical workload identification
- Recovery time objective definition
- Backup and recovery planning
- Alternative processing arrangements
- Regular testing and validation
Ready for the fascinating part? The most sophisticated cooling implementations now incorporate “digital twin” technology that creates a virtual replica of the entire cooling system. These digital twins enable scenario testing, predictive maintenance, and optimization without risking production systems. Organizations using digital twins for cooling management report 25-40% fewer operational incidents and 15-30% better efficiency compared to traditional approaches. This emerging practice represents a fundamental shift from reactive to predictive cooling management, enabling proactive optimization that was previously impossible.
Future Trends in GPU Cooling
The landscape of GPU cooling continues to evolve rapidly, with several emerging trends poised to reshape thermal management for AI infrastructure.
Problem: Current cooling technologies may struggle to address the thermal challenges of next-generation AI accelerators and deployment models.
As GPU power consumption potentially exceeds 1000W per device and deployment densities continue to increase, even current advanced cooling technologies will face significant challenges.
Aggravation: The pace of innovation in AI hardware is outstripping the evolution of cooling technologies, creating a growing gap between thermal requirements and cooling capabilities.
Further complicating matters, the rapid advancement of AI capabilities is driving accelerated hardware development cycles, creating a situation where cooling technology must evolve more quickly to keep pace with thermal management needs.
Solution: Understanding emerging trends in GPU cooling enables more future-proof infrastructure planning and technology selection:
Emerging Cooling Technologies
Innovative approaches expanding cooling capabilities:
- Two-Phase Cooling Advancements:
- Direct-to-chip two-phase cooling
- Flow boiling implementations
- Refrigerant-based systems
- Enhanced phase change materials
- Compact two-phase solutions
- Microfluidic Cooling:
- On-package fluid channels
- 3D-printed cooling structures
- Integrated manifold designs
- Targeted hotspot cooling
- Reduced fluid volume systems
- Solid-State Cooling:
- Thermoelectric cooling applications
- Magnetocaloric cooling research
- Electrocaloric material development
- Solid-state heat pumps
- Hybrid solid-state/liquid approaches
Here’s what makes this fascinating: The cooling technology innovation cycle is accelerating dramatically. Historically, major cooling technology transitions (air to liquid, liquid to immersion) occurred over 7-10 year periods. Current development trajectories suggest the next major transition (potentially to integrated microfluidic or advanced two-phase technologies) may occur within 3-5 years. This compressed innovation cycle is being driven by the economic value of AI computation, which creates unprecedented incentives for solving thermal limitations that constrain AI performance.
Integration and Architectural Trends
Evolving relationships between computing hardware and cooling systems:
- Co-Designed Computing and Cooling:
- Cooling requirements influencing chip design
- Purpose-built cooling for specific accelerators
- Standardized cooling interfaces
- Cooling-aware chip packaging
- Unified thermal-computational optimization
- Disaggregated and Composable Systems:
- Cooling implications of disaggregated architecture
- Liquid cooling for interconnect infrastructure
- Dynamic resource composition considerations
- Cooling for memory-centric architectures
- Heterogeneous system cooling requirements
- Specialized AI Hardware Cooling:
- Neuromorphic computing thermal characteristics
- Photonic computing cooling requirements
- Quantum computing thermal management
- Analog AI accelerator cooling
- In-memory computing thermal considerations
But here’s an interesting phenomenon: The boundary between computing hardware and cooling systems is increasingly blurring. Next-generation designs are exploring “cooling-defined architecture” where thermal management is a primary design constraint rather than an afterthought. Some research systems are even exploring “thermally-aware computing” where workloads dynamically adapt to thermal conditions, creating a bidirectional relationship between computation and cooling that fundamentally changes both hardware design and software execution models.
Sustainability and Efficiency Focus
Environmental considerations increasingly shaping cooling innovation:
- Energy Efficiency Innovations:
- AI-optimized cooling control systems
- Dynamic cooling resource allocation
- Workload scheduling for thermal optimization
- Seasonal and weather-adaptive operation
- Cooling energy recovery techniques
- Heat Reuse Technologies:
- Data center waste heat utilization
- District heating integration
- Industrial process heat applications
- Absorption cooling for facility air conditioning
- Power generation from waste heat
- Water Conservation Approaches:
- Closed-loop cooling designs
- Air-side economization optimization
- Alternative heat rejection methods
- Rainwater harvesting integration
- Wastewater recycling for cooling
Future GPU Cooling Technology Outlook
Technology | Current Status | Potential Impact | Commercialization Timeline | Adoption Drivers |
---|---|---|---|---|
Advanced Two-Phase | Early commercial | Very High | 1-3 years | Extreme density, efficiency |
Microfluidic Cooling | Advanced R&D | Transformative | 3-5 years | Integration, performance |
Solid-State Cooling | Research | Moderate | 5-7+ years | Reliability, specialized applications |
AI-Optimized Control | Early commercial | High | 1-2 years | Efficiency, performance stability |
Heat Reuse Systems | Growing adoption | Moderate-High | 1-3 years | Sustainability, economics |
Integrated Cooling | Advanced R&D | Very High | 3-5 years | Performance, density, efficiency |
Market and Industry Evolution
Broader trends reshaping the cooling technology landscape:
- Vendor Ecosystem Development:
- Consolidation among cooling providers
- Computing OEM cooling technology acquisition
- Specialized AI cooling startups
- Strategic partnerships and alliances
- Intellectual property landscape evolution
- Standards and Interoperability:
- Cooling interface standardization efforts
- Performance measurement standardization
- Safety and compliance framework development
- Sustainability certification programs
- Industry consortium initiatives
- Service-Based Models:
- Cooling-as-a-Service offerings
- Performance-based contracting
- Managed cooling services
- Integrated IT/cooling management
- Risk-sharing business models
Ready for the fascinating part? The economic value of cooling innovation is creating unprecedented investment in thermal management technology. Venture capital investment in advanced cooling technologies has increased by 300-400% in the past three years, with particular focus on AI-specific cooling solutions. This investment surge is accelerating the pace of innovation and commercialization, potentially compressing technology adoption cycles that previously took 5-7 years into 2-3 year timeframes. The result is likely to be a period of rapid evolution in cooling technology, creating both opportunities and challenges for organizations deploying AI infrastructure.
Frequently Asked Questions
Q1: How do I determine which cooling technology is most appropriate for my specific AI infrastructure requirements?
Selecting the optimal cooling technology requires a systematic evaluation process: First, assess your thermal requirements—calculate the total heat load based on GPU type, quantity, and utilization patterns, with particular attention to peak power scenarios. For deployments using high-TDP GPUs (400W+) in dense configurations, advanced cooling is typically essential, while more moderate deployments maintain flexibility. Second, evaluate your facility constraints—existing cooling infrastructure, available space, floor loading capacity, and facility water availability may limit your options or require significant modifications for certain technologies. Third, consider your operational model—different cooling technologies require varying levels of expertise, maintenance, and management overhead that must align with your operational capabilities. Fourth, analyze your scaling trajectory—future expansion plans may justify investing in more advanced cooling initially to avoid disruptive upgrades later. Fifth, calculate comprehensive economics—beyond initial capital costs, include energy expenses, maintenance requirements, density benefits, and performance advantages in your analysis. The most effective approach often involves a formal decision matrix that weights these factors according to your specific priorities. Many organizations find that hybrid approaches offer an optimal balance for initial deployments, with targeted liquid cooling for GPUs combined with traditional cooling for other components. This approach delivers most of the performance benefits of advanced cooling with reduced implementation complexity, while providing a pathway to more comprehensive solutions as density increases.
Q2: What are the most important monitoring and management considerations for GPU cooling systems?
Effective monitoring and management of GPU cooling systems requires attention to several critical areas: First, comprehensive temperature monitoring—beyond basic GPU core temperatures, implement monitoring for memory temperatures, VRM temperatures, inlet and outlet temperatures for air or liquid, and ambient conditions. Temperature differentials and trends often provide earlier warning of developing issues than absolute values. Second, flow and pressure monitoring for liquid systems—measure and track flow rates, pressure differentials, and liquid temperatures at multiple points to detect restrictions, pump issues, or heat exchanger problems before they affect performance. Third, implement predictive analytics—modern cooling management should incorporate machine learning to establish normal operating patterns and identify anomalies before they become critical. These systems can detect subtle changes in thermal behavior that might indicate developing problems. Fourth, establish comprehensive alerting with appropriate thresholds—configure graduated alerts based on severity, with early warnings for trends and critical alerts for conditions requiring immediate action. Fifth, implement regular performance benchmarking—scheduled testing under standardized loads provides comparative data to identify gradual performance degradation that might otherwise go unnoticed. Sixth, maintain detailed historical data—long-term trend analysis enables correlation between environmental factors, workloads, and cooling performance. The most sophisticated operations implement “digital twin” modeling that simulates cooling system behavior under various conditions, enabling scenario testing and optimization without risking production systems. This approach transforms cooling management from reactive to predictive, significantly improving both performance and reliability.
Q3: How should organizations plan for the cooling requirements of future GPU generations with potentially higher TDP?
Planning for future GPU cooling requirements requires a forward-looking strategy: First, implement modular and scalable cooling infrastructure—design systems with standardized interfaces and the ability to incrementally upgrade capacity without complete replacement. This approach provides flexibility to adapt as requirements evolve. Second, build in substantial headroom—when designing new infrastructure, plan for at least 1.5-2x current maximum TDP to accommodate future generations. For organizations on aggressive AI adoption paths, 2.5-3x headroom may be appropriate. Third, establish a technology roadmap with clear transition points—develop explicit plans for how cooling will evolve through multiple hardware generations, including trigger points for technology transitions based on density, performance, and efficiency requirements. Fourth, create cooling zones with varying capabilities—designate specific areas for highest-density deployment with premium cooling, allowing targeted infrastructure investment where most needed. Fifth, develop internal expertise proactively—build knowledge and capabilities around advanced cooling technologies before they become critical requirements. The most forward-thinking organizations are implementing “cooling as a service” approaches internally, where cooling is treated as a dynamic, upgradable resource rather than fixed infrastructure. This approach typically involves standardized interfaces between computing hardware and cooling systems, modular components that can be incrementally upgraded, and sophisticated management systems that optimize across multiple cooling technologies. This flexible, service-oriented approach to cooling infrastructure provides the greatest adaptability to the rapidly evolving AI hardware landscape.
Q4: What are the most common failure points in GPU cooling systems, and how can they be mitigated?
The most common failure points in GPU cooling systems vary by technology, with specific mitigation strategies for each: For air cooling, fan failures represent the most frequent issue (30-40% of failures), mitigated through redundant fans, proactive replacement programs based on operating hours, and acoustic monitoring to detect bearing degradation. Dust accumulation causes 20-30% of air cooling problems, addressed through appropriate filtration, regular cleaning protocols, and monitoring for increasing temperature differentials that indicate restricted airflow. For liquid cooling, pump failures account for 25-35% of issues, mitigated through redundant pumps, vibration monitoring for early warning, and regular maintenance. Leaks cause 15-25% of liquid cooling failures, addressed through quality components, proper installation validation, comprehensive leak detection, and regular visual inspections. Corrosion and fluid degradation represent 10-20% of problems, mitigated through proper fluid selection, regular testing, scheduled replacement, and appropriate materials selection. For immersion cooling, fluid contamination causes 20-30% of issues, addressed through filtration systems, regular fluid analysis, and proper operational procedures. Heat exchanger fouling accounts for 15-25% of problems, mitigated through appropriate fluid treatment, temperature differential monitoring, and scheduled cleaning. Across all technologies, control system failures represent 10-15% of issues, addressed through redundant controllers, backup power supplies, and fail-safe designs. Organizations with the lowest failure rates implement comprehensive predictive maintenance programs that identify and address potential issues before they cause operational impact. These programs typically combine regular inspections, sensor-based condition monitoring, and trend analysis to transform maintenance from reactive to preventative, reducing cooling-related failures by 60-80% compared to reactive approaches.
Q5: How does the choice of cooling technology affect the overall reliability and lifespan of GPU hardware?
The choice of cooling technology significantly impacts GPU reliability and lifespan through several mechanisms: First, operating temperature directly affects failure rates—research indicates that every 10°C increase approximately doubles semiconductor failure rates. Advanced cooling technologies that maintain lower operating temperatures can potentially reduce failures by 50-75% compared to borderline cooling. Second, temperature stability matters as much as absolute temperature—thermal cycling creates mechanical stress through expansion and contraction, particularly affecting solder joints, interconnects, and packaging materials. Technologies that maintain more consistent temperatures (typically liquid and immersion) can reduce these stresses by 60-80% compared to air cooling with its more variable thermal profile. Third, temperature gradients across components create differential expansion and localized stress—advanced cooling typically provides more uniform temperatures, reducing these gradients by 40-60%. Fourth, humidity and condensation risks vary by cooling approach—properly implemented liquid cooling with appropriate dew point management can reduce humidity-related risks compared to air cooling in variable environments. The economic implications are substantial—for high-value AI accelerators costing $10,000-40,000 each, extending lifespan from 3 years to 4-5 years through superior cooling can create $3,000-15,000 in value per GPU. Additionally, reduced failure rates directly impact operational costs through lower replacement expenses, decreased downtime, and reduced service requirements. For large deployments, these reliability benefits often exceed the direct energy savings from efficient cooling, fundamentally changing the ROI calculation for cooling investments. Organizations increasingly recognize that premium cooling should be viewed not just as a performance enabler but as a critical reliability investment that directly impacts total cost of ownership.
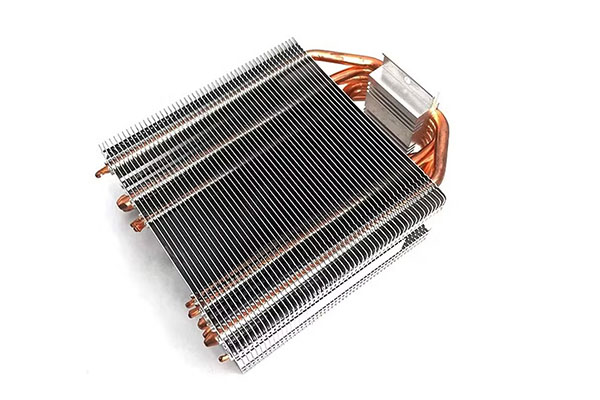