Introduction: Understanding Milling Machines
Milling machines are essential tools in the manufacturing industry, used for cutting, drilling, and shaping materials. But when deciding on a milling machine for your production needs, it’s crucial to understand the differences between the two primary types: 3 Axis and 4 Axis milling machines. Both have distinct advantages and limitations, and choosing the right one depends largely on the complexity of the projects and the materials you’re working with. In this article, we’ll dive into the key differences between 3 Axis and 4 Axis milling machines, helping you make an informed decision based on your specific needs and business goals.
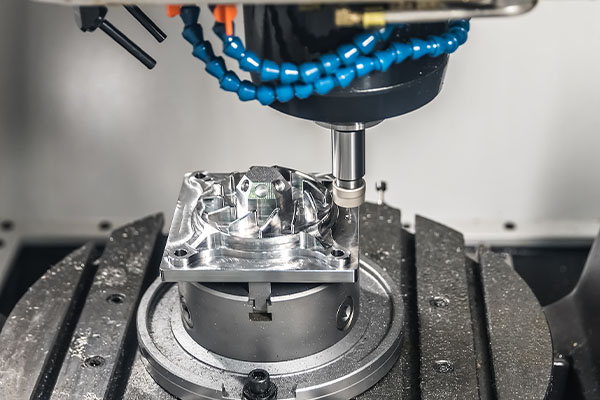
The Basics of 3 Axis Milling Machines
What is a 3 Axis Milling Machine?
A 3 Axis milling machine is a traditional type of CNC (Computer Numerical Control) machine that operates along three axes: X, Y, and Z. These machines are designed to move the cutting tool along these three axes to mill a workpiece. The X-axis moves the tool left and right, the Y-axis moves it forward and backward, and the Z-axis controls the vertical movement. This design allows for precise, straightforward machining tasks, making it the go-to option for most conventional manufacturing applications.
How a 3 Axis Milling Machine Works
In a 3 Axis machine, the workpiece is typically fixed on the machine bed, while the tool moves across the three axes to create the desired shape. The cutting tool remains stationary in relation to the workpiece, with the machine precisely controlling the tool’s position to ensure that each cut is made at the correct location and angle. The simplicity of this system makes it ideal for machining parts with flat surfaces or basic geometries.
Common Uses of 3 Axis Milling Machines
3 Axis milling machines are widely used for various applications, including drilling holes, cutting slots, and milling flat surfaces. They’re perfect for creating parts such as brackets, plates, and other relatively simple components. Their ability to execute detailed cuts with high precision makes them a staple in industries like aerospace, automotive, and electronics.
Advantages of Using 3 Axis Milling Machines
The primary advantage of 3 Axis milling machines is their cost-effectiveness. They are generally more affordable than more complex machines like 4 Axis models. Additionally, 3 Axis mills are easier to program, maintain, and operate, making them an excellent choice for smaller operations or companies just starting in CNC machining. They are also well-suited for tasks that don’t require complex geometries or multi-directional machining.
The Basics of 4 Axis Milling Machines
What is a 4 Axis Milling Machine?
A 4 Axis milling machine, as the name suggests, adds a fourth axis to the traditional three. This fourth axis is typically a rotary axis that allows the workpiece to rotate, enabling more complex movements and the ability to machine parts from different angles without needing to reposition the workpiece manually. This rotational movement opens up new possibilities for producing intricate and multi-faceted designs with higher precision.
How a 4 Axis Milling Machine Works
The 4 Axis milling machine operates similarly to a 3 Axis machine but includes an additional rotary axis that allows the workpiece to spin on one or more axes. This added dimension allows for continuous cutting on multiple sides of a part without manual intervention. It also enables the machine to perform undercutting, milling holes at unusual angles, and creating more complicated shapes.
Common Uses of 4 Axis Milling Machines
4 Axis machines are ideal for machining parts that require complex geometries or detailed features on multiple sides. Industries such as aerospace, medical device manufacturing, and automotive parts production often use these machines to create intricate components with high precision. For example, a turbine blade or a complex housing part would benefit from the capabilities of a 4 Axis milling machine.
Advantages of Using 4 Axis Milling Machines
The main advantage of a 4 Axis milling machine is its ability to perform more complex machining operations without requiring the part to be manually repositioned. This reduces setup time, increases production efficiency, and minimizes the chance of errors. Additionally, the ability to machine parts on multiple sides at once improves overall precision and reduces the need for secondary operations, ultimately leading to a faster production cycle.
Key Differences Between 3 Axis and 4 Axis Milling Machines
The Number of Axes: What Does it Really Mean?
The most obvious difference between a 3 Axis and a 4 Axis milling machine is the number of axes they operate on. While a 3 Axis machine works along three planes (X, Y, and Z), a 4 Axis machine adds a fourth axis that provides rotational movement. This extra axis allows the 4 Axis machine to handle more complex tasks that would require manual repositioning in a 3 Axis system.
The Difference in Motion: How They Operate Differently
3 Axis machines move the cutting tool along three directions—left to right, forward and backward, and up and down. On the other hand, 4 Axis machines introduce a fourth motion, typically a rotary function that moves the workpiece along an additional axis. This extra degree of freedom allows the 4 Axis machine to create parts with features that would be difficult, if not impossible, for a 3 Axis machine to replicate.
Impact on Precision and Complexity
While 3 Axis machines are well-suited for simple tasks, 4 Axis machines offer greater versatility and precision when dealing with more intricate designs. The rotary axis of a 4 Axis machine enables more precise cutting and the ability to handle undercuts, which would be challenging for a 3 Axis machine to achieve. This added complexity allows for higher-quality results, especially when working with multi-sided components.
Speed and Efficiency: How They Compare
In terms of speed and efficiency, 4 Axis machines typically outperform 3 Axis machines for tasks involving complex geometry. Because the workpiece rotates automatically, a 4 Axis machine can work on multiple surfaces in one setup, reducing the time spent repositioning the part. This can lead to faster turnaround times and more efficient production, especially in high-volume environments.
Complexity of Setups and Programming
Programming a 3 Axis machine is relatively simple compared to a 4 Axis system. The latter requires more complex software and programming techniques due to the additional rotary axis. Operators need to account for the part’s rotation, which adds an extra layer of complexity in terms of toolpath generation. This complexity, however, is compensated by the machine’s ability to complete more intricate tasks in one go.
Design and Structure: Comparing 3 Axis vs 4 Axis Milling Machines
What Does a 3 Axis Milling Machine Look Like?
A 3 Axis milling machine has a straightforward design with a fixed workpiece and a cutting tool that moves along three linear axes. The machine typically has a stable, rigid frame that allows for accurate machining of flat or basic geometries. These machines are often compact, making them suitable for shops with limited space.
What Does a 4 Axis Milling Machine Look Like?
The design of a 4 Axis milling machine is slightly more complex. In addition to the standard three linear axes, it incorporates a rotary axis that moves the workpiece. This addition requires a more intricate setup, and the machine’s structure may be larger or require more robust components to support the added rotational function. The design allows for continuous cutting from multiple angles, making it ideal for complex parts.
Design Flexibility: Which Machine Offers More Options?
When it comes to design flexibility, the 4 Axis milling machine outperforms the 3 Axis machine. The rotary axis enables the creation of parts with angles and undercuts that would be difficult to achieve with a 3 Axis machine. This increased versatility makes the 4 Axis machine the preferred choice for industries dealing with complex and detailed parts.
Space Considerations: Which One Takes Up More Space?
While both machines require significant floor space, a 4 Axis machine may take up more room due to its larger structure and additional components. However, the ability to work on multiple sides of a part in one setup can ultimately reduce the amount of space needed for additional equipment, making the 4 Axis machine more efficient in the long term.
Machining Capabilities: What Can Each Machine Do?
Types of Parts You Can Machine with 3 Axis Machines
3 Axis milling machines are ideal for simpler machining tasks, such as cutting basic shapes, drilling holes, and milling flat surfaces. Common parts include brackets, plates, and other straightforward components. For industries that don’t require complex geometries, 3 Axis machines are often sufficient for creating high-quality, precise parts.
Types of Parts You Can Machine with 4 Axis Machines
4 Axis milling machines excel at machining more intricate parts. They are well-suited for components that require multi-sided machining or undercuts. This includes turbine blades, medical implants, and aerospace parts, which require the precise control and rotational movement offered by the 4 Axis system. These machines can handle tasks that would otherwise require multiple setups or secondary operations.
When to Choose 3 Axis and When to Choose 4 Axis for Your Projects
The choice between a 3 Axis and 4 Axis machine depends on the complexity of the parts you need to produce. If you’re working with simple components that don’t require multi-angle machining, a 3 Axis machine is sufficient. However, if your projects involve complex shapes, undercuts, or multi-sided machining, a 4 Axis machine will provide the flexibility and precision you need.
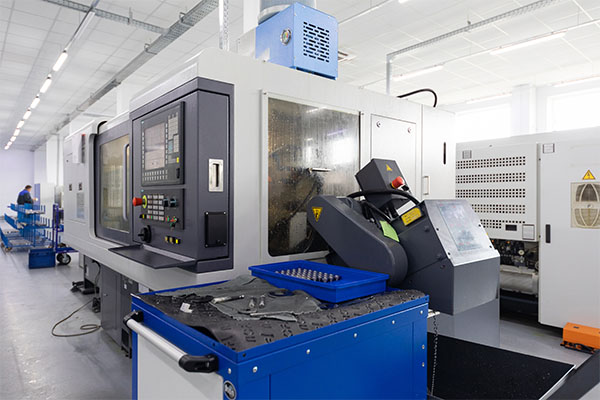
Programming and Setup: A Comparison
Ease of Programming for 3 Axis Machines
Programming a 3 Axis machine is relatively simple and can be accomplished with basic CAD/CAM software. The machine’s movements are predictable, and operators can easily generate toolpaths for simple tasks. For businesses with less experienced operators or smaller-scale operations, 3 Axis machines offer an easier learning curve and faster setup times.
Programming Complexity for 4 Axis Machines
Programming a 4 Axis machine is more complicated due to the additional rotary axis. Operators must account for the rotation of the workpiece and ensure that the toolpath is properly aligned for each side of the part. This requires more advanced CAD/CAM software and a deeper understanding of CNC programming, making 4 Axis machines better suited for businesses with more experienced operators.
Which Machine is Better for New Operators?
For new operators, a 3 Axis milling machine is generally easier to handle. The learning curve is less steep, and the setup and programming processes are simpler. As operators gain experience and require more complex machining capabilities, they can gradually transition to 4 Axis machines.
Common Software and Tools Used for Each Type of Machine
3 Axis milling machines typically use basic CAD/CAM software that can generate toolpaths for simple parts. In contrast, 4 Axis machines require more advanced software that supports multi-axis machining and the generation of complex toolpaths. This software often includes simulation tools that help ensure accuracy and avoid collisions during machining.
Cost Comparison: 3 Axis vs 4 Axis Milling Machines
Initial Purchase Price of Each Type
The initial cost of a 3 Axis milling machine is typically lower than that of a 4 Axis machine. This is because 3 Axis machines are simpler and require less advanced technology. However, 4 Axis machines provide greater capabilities and may be a more cost-effective option in the long run, depending on the complexity of the work.
Maintenance Costs: Which One is More Expensive to Maintain?
Maintenance costs for 3 Axis milling machines are generally lower due to their simpler design and fewer components. In contrast, 4 Axis machines require more frequent maintenance and can be more expensive to repair, as they involve additional moving parts and more complex technology.
Cost-Effectiveness Over Time: Which Offers Better ROI?
While the upfront cost of a 4 Axis milling machine may be higher, it can provide better return on investment (ROI) over time. This is because 4 Axis machines reduce setup times, minimize errors, and allow for more complex parts to be machined in a single operation. For businesses that deal with intricate components, the 4 Axis machine may ultimately prove to be more cost-effective in terms of efficiency and productivity.
Work Efficiency: How Much Faster is a 4 Axis Milling Machine?
Time Savings with 4 Axis Milling Machines
4 Axis milling machines save significant time during production because they eliminate the need for multiple setups. The ability to machine parts on multiple sides without repositioning reduces the total time required for machining. This leads to faster turnaround times and higher throughput, especially in high-volume production environments.
How 4 Axis Milling Machines Handle Complex Jobs More Efficiently
For complex jobs, a 4 Axis machine’s ability to work on different sides of a part in one setup dramatically improves efficiency. Complex geometries, undercuts, and multi-angle features can be created in fewer steps, reducing the need for additional machines or setups. This efficiency is critical in industries where time and precision are paramount.
The Importance of Time Management in Production
In competitive industries, time is a critical factor. By utilizing a 4 Axis milling machine, businesses can improve production speeds without compromising quality. This can lead to faster product delivery, improved customer satisfaction, and greater profitability.
Precision and Accuracy: Which Machine Provides Better Results?
Accuracy in 3 Axis Milling Machines
While 3 Axis milling machines are accurate, their design limits the ability to achieve certain complex features. The accuracy depends heavily on the setup and the operator’s skills. For basic tasks that involve simple cuts and drills, 3 Axis machines provide the precision required without much variation.
Precision in 4 Axis Milling Machines
4 Axis milling machines, on the other hand, offer superior precision when it comes to intricate and multi-sided parts. The additional rotary axis allows the machine to achieve finer details, complex angles, and undercuts that would be difficult for a 3 Axis machine to replicate. This makes them the go-to option for industries requiring extremely high tolerances.
The Role of the Operator in Achieving Precision
While both machines can achieve high levels of precision, the role of the operator is more significant in a 3 Axis machine. For 4 Axis machines, however, the additional complexity of the setup and programming means that an experienced operator is required to achieve optimal results.
Which Machine Offers More Consistent Results?
4 Axis milling machines typically provide more consistent results, especially when it comes to complex parts that require multi-angle machining. With fewer setups and more precise control over the cutting tool and workpiece, the 4 Axis machine is better equipped to produce parts with high precision and repeatability.
Versatility and Capability: Which Machine is Better for Custom Projects?
Versatility of 3 Axis Machines in Different Industries
3 Axis milling machines are versatile for industries that focus on basic parts and require simple machining tasks. These machines can handle a variety of materials and are particularly useful for creating flat components, such as brackets, plates, and other structural parts. However, they are less suitable for intricate or multi-sided parts.
Versatility of 4 Axis Machines and Complex Geometries
4 Axis milling machines are far more versatile when it comes to creating complex geometries. The rotary axis enables machining on multiple surfaces without repositioning, making it ideal for custom projects that require precise, multi-angle cuts. This added flexibility is invaluable in industries such as aerospace and medical device manufacturing.
Customizing Parts: What Each Machine Can Handle
For projects that demand detailed custom parts with undercuts or complex features, the 4 Axis milling machine offers unparalleled capability. Its ability to machine parts from multiple angles in one go ensures that even the most complex designs can be achieved with a high degree of accuracy. In contrast, 3 Axis machines are better suited for straightforward customizations that don’t require multi-sided machining.
Maintenance and Longevity: What You Need to Know
General Maintenance Requirements for 3 Axis Milling Machines
3 Axis milling machines are generally easier and less costly to maintain compared to 4 Axis machines. Their simpler design means fewer moving parts, which translates to less wear and tear. Routine maintenance includes cleaning, lubrication, and calibration, which are straightforward tasks that most operators can handle.
Maintenance Needs for 4 Axis Milling Machines
4 Axis milling machines have more complex systems, which require regular maintenance and inspection. The additional rotary axis and components add complexity to the maintenance process. However, with proper care, a 4 Axis machine can provide excellent performance and longevity, reducing the frequency of repairs.
Expected Lifespan of Both Machines
Both 3 Axis and 4 Axis milling machines can last for many years with proper maintenance. However, 4 Axis machines may experience more wear due to the added complexity and the additional components that move the workpiece. Ensuring proper lubrication, alignment, and calibration is essential to extending the lifespan of both types of machines.
How to Extend the Longevity of Your Milling Machines
Routine maintenance is the key to extending the lifespan of both 3 Axis and 4 Axis milling machines. By adhering to a proper maintenance schedule, operators can avoid common issues such as misalignment, excessive wear on parts, and decreased efficiency. Additionally, operators should invest in training to ensure that the machines are properly maintained and used.
Real-World Applications: Where Are These Machines Used?
Industries That Use 3 Axis Milling Machines
3 Axis milling machines are commonly used in industries such as automotive, electronics, and general manufacturing. They are ideal for producing parts like brackets, baseplates, and gears, as well as for operations such as drilling, tapping, and surface grinding. Their ability to handle basic parts efficiently makes them a popular choice for small to medium-sized manufacturers.
Industries That Use 4 Axis Milling Machines
4 Axis milling machines are favored by industries that require more intricate machining, such as aerospace, medical device manufacturing, and precision engineering. Complex parts like turbine blades, engine components, and medical implants are often machined with 4 Axis machines due to their ability to create multi-faceted shapes in a single operation.
Case Studies of 3 Axis vs 4 Axis Milling Machines in Action
In aerospace manufacturing, for example, a 3 Axis machine may be used to machine basic parts like brackets or mounting plates, whereas a 4 Axis machine would be used for machining intricate turbine blades. The 4 Axis machine’s ability to perform multi-angle cutting and undercutting makes it the preferred choice for more complex components in high-precision industries.
Specific Applications and Projects Best Suited for Each Machine
When deciding which machine is best suited for a specific project, consider the complexity of the part. For simple, flat components, a 3 Axis machine is sufficient. For parts with multi-sided geometries, undercuts, or intricate details, a 4 Axis machine is the better choice due to its increased flexibility and precision.
Making the Right Decision: Which Milling Machine is Best for Your Business?
Factors to Consider When Choosing Between 3 Axis and 4 Axis Milling Machines
When deciding between a 3 Axis and a 4 Axis milling machine, consider factors such as the complexity of the parts you need to machine, your budget, and your production volume. For businesses dealing with straightforward tasks, a 3 Axis machine may suffice. However, for those producing complex, multi-sided components, a 4 Axis machine is a more versatile and efficient choice.
How to Assess Your Business Needs and Equipment Requirements
Start by evaluating the types of parts you regularly produce. If your work primarily involves flat components, a 3 Axis machine is sufficient. However, if you often work with intricate designs or multi-sided parts, the additional capabilities of a 4 Axis milling machine may be worth the investment.
Tips for Small vs Large Businesses in Choosing the Right Milling Machine
For small businesses or startups, a 3 Axis milling machine offers a more affordable entry point into CNC machining. However, larger businesses or those with higher production demands might benefit from the speed and flexibility offered by a 4 Axis machine, which can handle more complex projects and deliver faster turnaround times.
Practical Considerations: Budget, Space, and Operator Skill
Finally, consider the total cost of ownership, including space requirements and operator skill. 3 Axis machines are generally easier and less costly to operate, but if your business handles high-precision or multi-faceted projects, the higher upfront cost of a 4 Axis machine could provide greater returns in the long run.
Conclusion: Final Thoughts and Key Takeaways
In summary, the choice between a 3 Axis and 4 Axis milling machine depends on the nature of your production needs. 3 Axis machines are ideal for straightforward tasks, offering an affordable and easy-to-use solution for businesses that don’t require complex geometries. On the other hand, 4 Axis machines provide the flexibility and precision needed for intricate designs, reducing setup times and improving overall efficiency for businesses that require multi-sided machining. When choosing between the two, consider your business goals, production volume, and budget to make an informed decision.
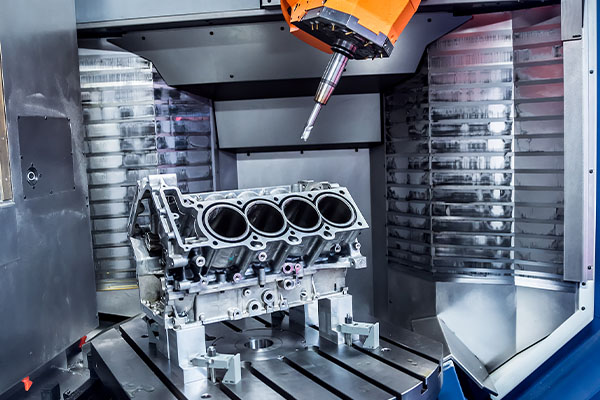
Frequently Asked Questions (FAQ)
What’s the difference between 3 Axis and 4 Axis milling machines?
The main difference is the number of axes they operate on. 3 Axis machines move along the X, Y, and Z axes, while 4 Axis machines add a rotary axis, allowing the workpiece to rotate for more complex machining.
Which one is better for precision work?
4 Axis milling machines are better for precision when it comes to intricate or multi-sided parts. Their ability to rotate the workpiece allows for finer detail and undercutting, which would be difficult for a 3 Axis machine.
Are 4 Axis machines harder to program than 3 Axis machines?
Yes, programming a 4 Axis machine is more complex because you have to account for the additional rotary axis. However, with advanced CAD/CAM software, it becomes manageable.
How much more expensive is a 4 Axis milling machine than a 3 Axis one?
4 Axis milling machines are generally more expensive due to their added complexity and capabilities. The price can vary depending on the machine’s features and size.
Can a 3 Axis machine perform tasks similar to a 4 Axis machine?
A 3 Axis machine can handle simple tasks but lacks the capability to machine multi-sided components or intricate geometries without repositioning the part.
Is a 4 Axis milling machine worth the extra investment?
If your business requires intricate parts or multi-sided machining, the additional cost of a 4 Axis milling machine is likely worth the investment, as it offers greater efficiency and precision.
What industries benefit most from 3 Axis milling machines?
3 Axis milling machines are ideal for industries that produce basic parts like automotive components, electronics, and general manufacturing parts.
What industries benefit most from 4 Axis milling machines?
Industries such as aerospace, medical device manufacturing, and precision engineering benefit most from 4 Axis milling machines, due to their ability to machine complex components with high precision.