Introducción
Threads are integral components in manufacturing, commonly used to join and secure parts together in various industries. Whether you’re working with machinery, fasteners, or piping systems, understanding the different types of threads and how they function is crucial for ensuring your product’s performance and longevity. In this article, we will explore the various types of threads used in manufacturing, their key features, and their best applications.
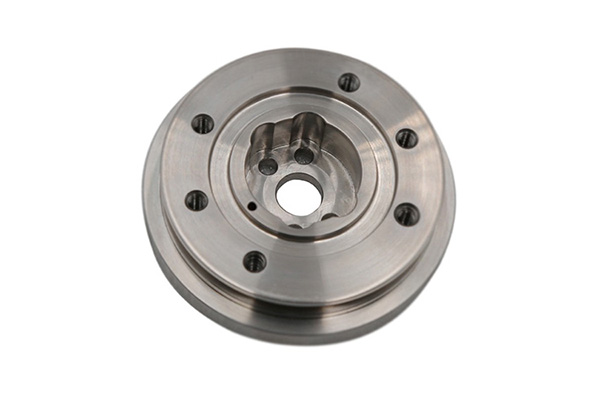
1. What are the different types of threads used in manufacturing?
Threads in manufacturing come in a variety of types, each serving a specific purpose based on their design and functionality. Threads are classified by their shape, size, material, and the way they are used in different industries. They are essential in mechanical operations, offering a means of fastening, alignment, or movement. So, what are the main types of threads you’ll encounter in manufacturing?
Here’s the deal: The most commonly used thread types include Unified Thread Standard (UTS), metric threads, Acme threads, and pipe threads. Each of these thread types has unique features that make them ideal for specific applications.
Unified Thread Standard (UTS) threads are widely used in the United States and are standardized for both external and internal threads. Metric threads, on the other hand, are globally recognized and are preferred in countries outside the U.S., particularly in Europe and Asia. Acme threads are perfect for power transmission applications due to their trapezoidal shape, offering more surface area for load-bearing. Meanwhile, pipe threads are specifically designed for creating airtight seals, making them ideal for piping systems in plumbing and gas systems.
Here’s the kicker: Each type of thread plays a unique role, and choosing the right one for the job ensures strength, durability, and safety in your manufacturing processes.
2. How are threads classified in manufacturing?
Threads are classified in manufacturing based on several factors, including their shape, size, material, and function. Understanding how threads are classified is key to selecting the appropriate type for any given application. Let’s break down the major classifications.
One of the primary ways threads are classified is by shape. The most common thread shapes are triangular, square, and trapezoidal. Triangular threads, for example, are typically seen in standard fasteners like bolts and screws. Square threads, often used in lead screws, are ideal for transmitting motion with minimal friction. Trapezoidal threads, such as Acme threads, are commonly used in power transmission systems due to their ability to bear heavier loads.
¿Listo para la buena parte? Threads are also classified by tamaño y material. Size is often denoted by pitch and diameter. Pitch refers to the distance between each thread, and the diameter indicates the width of the threaded part. Material choice affects a thread’s durability, corrosion resistance, and strength. Stainless steel threads, for example, offer excellent corrosion resistance, while carbon steel threads are chosen for their strength.
The classification of threads plays a significant role in the manufacturing process, helping engineers and manufacturers select the right type for the right application.
3. What are the most common types of threads in manufacturing?
There are several types of threads that are commonly used in manufacturing, each designed to meet specific needs in various industries. But what are these thread types, and how do they differ from one another?
Let’s take a deeper look at the most common ones: Unified Thread Standard (UTS), Metric Threads, Acme Threads, and Pipe Threads.
- Unified Thread Standard (UTS): UTS threads are primarily used in the United States and are the most common type of thread for fasteners. They come in both coarse and fine versions and are used in automotive, industrial, and construction applications.
- Metric Threads: Metric threads are commonly used outside the United States and are based on the International System of Units (SI). These threads are standard in Europe and Asia and are often used in everything from electronics to automotive applications.
- Acme Threads: Acme threads are designed with a trapezoidal profile and are used in applications where power transmission is critical. These threads are commonly found in lead screws, which convert rotational motion into linear motion.
- Pipe Threads: Pipe threads are designed to create a tight seal for fluid or gas systems. These threads are commonly used in plumbing, HVAC systems, and other fluid-handling systems. They come in different standards, such as NPT (National Pipe Thread) for the U.S. and BSP (British Standard Pipe) for the U.K.
Each of these thread types plays an important role in ensuring the strength, precision, and reliability of the final product in various manufacturing processes.
4. What are the characteristics of Unified Thread Standard (UTS) threads?
The Unified Thread Standard (UTS) is one of the most widely used threading systems, particularly in the United States. UTS threads have several distinct characteristics that make them a reliable choice for a wide range of applications. But what exactly makes them stand out?
The UTS system is characterized by its uniformity y compatibility. These threads are designed to be interchangeable, meaning that any UTS-compliant bolt can fit into any UTS-compliant nut, regardless of the manufacturer. This universality simplifies the manufacturing process and reduces inventory complexity. Additionally, UTS threads come in both coarse y fine versions. Coarse threads are often used for fasteners that require quick assembly or disassembly, while fine threads offer better holding power and are ideal for applications requiring precision.
¿Cuál es la verdadera historia? UTS threads are standardized in terms of pitch and diameter, making them a dependable choice for fasteners and bolts in automotive, aerospace, and general industrial applications. Their compatibility with a variety of materials, including steel and aluminum, ensures they are versatile and reliable in different manufacturing settings.
5. How are metric threads different from other types of threads?
Metric threads, used primarily outside the United States, are another common type of thread found in manufacturing. So, how do these threads differ from other types, particularly UTS threads?
First, metric threads are based on the metric system, unlike UTS threads, which use the imperial system. Metric threads are measured in millimeters and use a pitch (distance between threads) and diameter to denote their size. This makes it easier to determine the thread’s size compared to UTS threads, which require more specific calculations to understand the pitch and diameter.
Here’s where it gets interesting: Metric threads are more common globally, particularly in Europe and Asia. They are often used in automotive, electronic, and mechanical applications, where precision is crucial. Because the metric system is universally recognized, using metric threads ensures compatibility in international manufacturing and distribution.
Metric threads are also often chosen for fine threads when a greater degree of precision is needed, and they offer better thread engagement compared to coarser threads, reducing the chance of stripping.
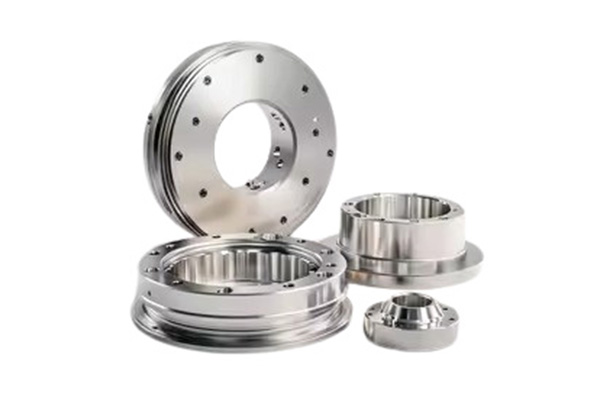
6. What are Acme threads, and when are they used?
Acme threads are a specific type of trapezoidal thread that are used in applications where power transmission and load-bearing capabilities are critical. So, what sets Acme threads apart from other types of threads?
El key feature of Acme threads is their trapezoidal shape, which provides more surface area for load distribution compared to the traditional V-shaped threads. This makes them ideal for mechanical power transmission systems that need to handle heavy loads, such as in lead screws or CNC machinery.
What’s the catch? Acme threads are often found in systems that require linear motion, such as adjustable machines or jacks. Their shape helps reduce friction, making them more efficient for converting rotary motion into linear motion. While they can be more expensive to produce than standard threads, the benefits they provide in terms of durability and performance often outweigh the additional costs.
These threads are highly sought after in industries that deal with heavy machinery, automation, and transportation.
7. What are buttress threads, and where are they applied?
Buttress threads are another specialized thread type used in specific applications that require high strength in one direction. So, what exactly are they, and why are they used in certain industries?
Buttress threads are unique due to their asymmetric profile, which gives them greater load-bearing capacity in one direction. This makes them particularly useful in applications where a high level of force needs to be applied in only one direction, such as in hydraulic systems, heavy-duty machinery, and military equipment.
What’s the deal here? The buttress thread design reduces the risk of wear and tear in high-stress environments, making them an excellent choice for applications where one-way force is predominant. The threads can handle high pressure and are often used in oil rigs, hydraulic presses, and other industrial machinery.
8. How do pipe threads differ from other types of threads?
Pipe threads are a specialized type of thread designed specifically for piping systems. These threads are used to create airtight seals in plumbing and fluid systems. So, what makes them different from other thread types?
Here’s the thing: Pipe threads have a unique design that helps ensure a secure seal for fluids or gases. The most common types are National Pipe Thread (NPT) y British Standard Pipe (BSP) threads. NPT threads have a tapered design, which ensures that the threads wedge together tightly as they are tightened, creating a seal. BSP threads, on the other hand, are typically straight and rely on a sealing mechanism like a gasket to ensure leak-proof connections.
Pipe threads are commonly used in industries like plumbing, oil and gas, HVAC systems, y piping systems for their reliability in containing liquids or gases under pressure. These threads are designed with safety and durability in mind, ensuring a long-lasting seal for piping connections.
9. What role does thread pitch play in manufacturing?
Thread pitch is a critical factor when selecting the right type of thread for a manufacturing application. So, why is thread pitch so important, and how does it impact performance?
Thread pitch refers to the distance between two adjacent threads and plays a significant role in how threads engage with each other. A fine pitch allows for more threads per inch, which provides greater surface contact and holding power. However, fine-pitched threads can be more prone to damage under high stress. On the other hand, coarse-pitched threads provide greater durability and are less likely to strip, making them ideal for quick assembly and high-torque applications.
¿Listo para la buena parte? When choosing a thread pitch, you need to consider the specific application and stress the threads will undergo. For instance, coarse-pitch threads are often used in fasteners that need to withstand vibration, while fine-pitch threads are better for precision tasks requiring a higher degree of alignment.
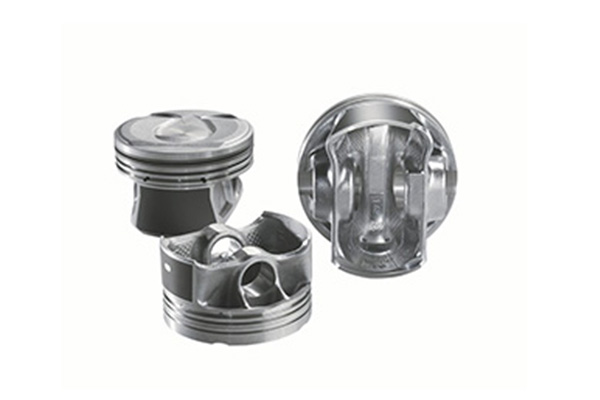
10. How do materials affect thread performance?
The material used to manufacture threads has a significant impact on their performance and durability. So, how does the choice of material affect thread quality and strength?
It’s simple: Different materials offer various benefits in terms of strength, corrosion resistance, and durability. Stainless steel threads are highly resistant to rust and corrosion, making them ideal for applications in harsh environments, such as marine or chemical industries. Carbon steel threads are known for their strength, while alloy steels provide improved wear resistance.
The material also influences how the threads are treated during the manufacturing process. For example, threads made from hardened steel are often coated with protective finishes to enhance their strength and longevity, making them ideal for heavy-duty applications.
11. What are the benefits of using precision threads in manufacturing?
Precision threads are used in applications where accuracy and tight tolerances are essential. But what makes precision threads so beneficial, and why should you use them?
Here’s the thing: Precision threads are designed to fit together with a high degree of accuracy, ensuring tight and secure connections. This is particularly important in industries like aerospace, electronics, and automotive, where even the smallest misalignment can cause significant issues. By using precision threads, manufacturers can achieve tighter tolerances, reduce the risk of failure, and ensure that parts perform optimally in their applications.
In addition, precision threads help improve the efficiency of manufacturing processes, as they reduce the need for rework and adjustments, ultimately leading to better product quality and cost savings.
12. How are threads created in manufacturing?
Thread creation in manufacturing involves a few critical steps that ensure the threads are formed correctly. So, how are these threads produced, and what processes are involved?
Threads can be created using cutting o rolling methods. In cutting, a single-point tool is used to cut the thread into the material. In thread rolling, the material is passed between two rollers, which press the material into the desired thread shape. Rolling is often preferred in high-volume manufacturing due to its efficiency and ability to produce stronger threads.
What’s the catch? The choice of method depends on the material and the required thread type. While thread cutting provides more flexibility, rolling is used for producing larger volumes of threads with better strength.
13. What tools and machinery are used for creating threads?
The tools and machinery used to create threads play a crucial role in determining the quality and precision of the threads. So, what tools are needed for the job?
Threading machines, such as máquinas de torno, thread mills, y tapping machines, are used to create various types of threads. These machines utilize a variety of cutting tools, including thread taps, dies, y cutting inserts, to shape the threads.
Here’s where it gets interesting: Thread rolling machines use rollers to compress the material into thread shapes, while CNC machines (computer numerical control) provide high precision and automation, making them ideal for creating complex thread designs.
14. What are the challenges of threading in manufacturing?
Threading in manufacturing comes with several challenges, and understanding these issues can help improve the process. So, what are the main challenges?
¿Cuál es la verdadera historia? One of the main challenges in threading is accuracy. Threads need to be precise to ensure proper fit and function. If the threads are too loose or tight, they may cause assembly issues or lead to product failure. Thread defects, such as burrs or misalignments, can also occur during production, which affects the overall quality of the threads.
Ensuring consistent quality across large batches can also be challenging, particularly when working with different materials and thread sizes. However, by using the right tools and quality control measures, these challenges can be minimized.
15. How do you ensure quality in thread manufacturing?
Ensuring quality in thread manufacturing is vital for the reliability of the final product. So, how can manufacturers guarantee thread quality?
Aquí está el trato: Thread quality is ensured through strict quality control measures y inspection. After production, threads are inspected using various methods, such as micrometers, calipers, y optical measuring devices. These tools help verify the thread’s diameter, pitch, and other critical dimensions.
Manufacturers also conduct destructive and non-destructive testing to check the strength and durability of the threads. Ensuring quality throughout the manufacturing process helps improve product performance and minimize defects.
Conclusión
Threads are essential components in manufacturing, and understanding their types, characteristics, and applications is critical for choosing the right one for any given task. From Unified Thread Standard (UTS) to Acme threads, each type offers unique benefits tailored to specific needs. By selecting the correct thread type, manufacturers can ensure their products are durable, reliable, and high-performing. Whether you’re designing machinery, fasteners, or piping systems, understanding the role of threads in manufacturing is key to success.
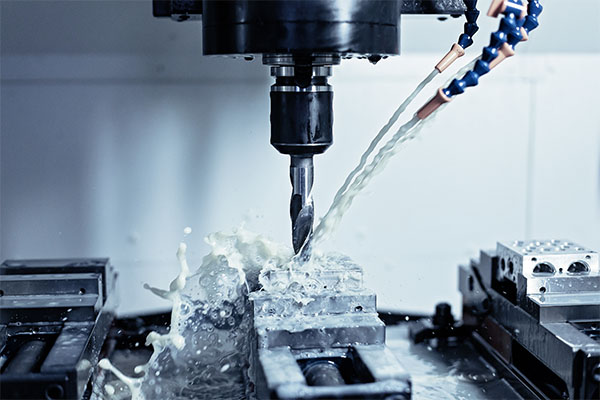
Preguntas frecuentes
Pregunta 1: What is a thread in manufacturing?
A thread is a helical ridge or spiral groove wrapped around a cylindrical or conical surface used for fastening, lifting, or mechanical movement.
Pregunta 2: How does thread pitch affect thread performance?
Thread pitch refers to the distance between the threads. A fine pitch provides better strength but is harder to manufacture, while a coarse pitch is more durable and easier to produce.
Pregunta 3: Why are Acme threads commonly used?
Acme threads are designed for applications requiring power transmission and load-bearing, commonly used in machinery and automation systems.
Pregunta 4: What is the difference between pipe threads and general threads?
Pipe threads are designed to create a tight seal for fluid or gas flow, while general threads are used primarily for fastening parts.
Pregunta 5: How are threads tested for quality in manufacturing?
Threads are tested for accuracy using calipers, thread gauges, and optical tools to check the alignment, pitch, and overall precision of the threads.