Introduction
CNC machining, which stands for Computer Numerical Control machining, is transforming industries by providing precise and efficient manufacturing solutions. As technology advances, the role of CNC machining in driving innovation becomes more significant. It is no longer just a tool for mass production but a catalyst for creating complex designs, customizing products, and revolutionizing industries such as aerospace, automotive, and healthcare. In this article, we’ll explore how CNC machining capabilities are not only shaping the present but also paving the way for future innovations. Let’s dive into the world of CNC machining and see how it plays a crucial role in modern manufacturing and product development.
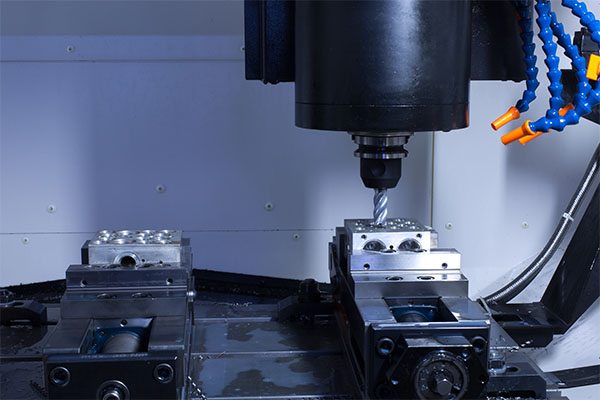
What is CNC Machining?
Understanding the Basics of CNC Machining
CNC machining is a manufacturing process where pre-programmed computer software dictates the movement of factory tools and machinery. It allows for automated, high-precision production of parts and components, making it a preferred method in industries requiring intricate designs and high tolerance levels. With CNC machines, manufacturers can produce everything from simple components to complex geometries with consistent accuracy and minimal human intervention. These machines can perform a variety of tasks such as milling, turning, drilling, and electrical discharge machining (EDM). This versatility allows CNC machining to be applied across diverse sectors, making it one of the most advanced and efficient technologies used today.
The process begins with designing a digital model of the desired part using CAD (Computer-Aided Design) software. This model is then converted into a CNC-compatible format, which directs the machine to cut, drill, or mill the material into the desired shape. One of the main advantages of CNC machining is its ability to produce consistent results, which is especially important for industries like aerospace, medical, and automotive, where even the slightest deviation from the specifications could lead to costly failures or unsafe products.
History and Evolution of CNC Technology
CNC machining has a rich history that spans back to the 1940s when the concept was first introduced to the manufacturing industry. Originally, machines were manually operated, which made them time-consuming and prone to human error. The first CNC machines were developed in the 1950s and were used primarily in the aerospace industry to manufacture aircraft parts. These early machines were huge and expensive, limited to highly specialized uses. However, over time, technological advancements and improvements in software have led to more affordable and compact CNC machines that are now widely available and used in many industries.
The evolution of CNC technology has also brought about the integration of advanced control systems, automation, and the use of multi-axis machines. This has allowed for more complex shapes to be cut and intricate patterns to be produced with far greater precision than ever before. In recent years, CNC machines have become even more sophisticated, with advancements in AI, robotics, and automation, making them even more adaptable to evolving manufacturing needs. Today, CNC machining continues to evolve, helping industries innovate faster and more cost-effectively.
CNC Machining Capabilities
Precision and Accuracy in CNC Machining
One of the standout capabilities of CNC machining is its ability to produce parts with extreme precision and accuracy. CNC machines can achieve tolerances as tight as ±0.0001 inches, which is crucial for industries like aerospace and medical device manufacturing where even a minor error could compromise safety or performance. The machines operate under the guidance of pre-programmed instructions that ensure each part is produced exactly as intended. This consistency means that large volumes of identical parts can be made without the variations that can arise with manual machining.
CNC machining excels in producing parts with intricate features, such as small holes, fine threads, and detailed surface finishes. Moreover, CNC systems can work with a variety of materials, including metals, plastics, and composites, which can further enhance the precision and performance of parts. For instance, titanium, which is commonly used in the aerospace and medical industries, can be machined to create components that are lightweight, durable, and able to withstand high stress without compromising on accuracy.
Another significant aspect of CNC machining is its capability to handle complex geometries. While traditional methods may struggle with parts that have unusual shapes or intricate features, CNC machines excel at creating custom parts with these specifications. This ability to manufacture highly customized, complex components has led to greater design freedom, which is often the catalyst for innovation in various industries.
Materials Used in CNC Machining
The materials used in CNC machining play a critical role in the performance and durability of the final product. CNC machines can handle a broad range of materials, from hard metals such as stainless steel, aluminum, and titanium, to plastics, composites, and even wood. Each material has its unique properties that make it suitable for specific applications. For example, metals are often chosen for their strength and durability, making them ideal for aerospace and automotive parts. Plastics, on the other hand, are preferred for products that need to be lightweight and cost-effective, such as consumer electronics housings or medical device components.
The ability to work with different materials also enables manufacturers to innovate and create parts that offer a combination of strength, weight, flexibility, and durability. CNC machines are equipped with various cutting tools that are specifically designed to handle the different properties of materials, ensuring that they are machined to the desired specifications without compromising their integrity.
In addition, newer materials, such as advanced composites and hybrid materials, are increasingly being used in CNC machining, particularly in the aerospace and automotive industries. These materials often offer superior performance characteristics, such as improved heat resistance or weight reduction, and CNC machining can be adapted to work with them effectively. This ability to manipulate a wide variety of materials has helped companies stay ahead of the curve by enabling them to manufacture cutting-edge products.
Speed and Efficiency of CNC Machining
CNC machining is known for its speed and efficiency, which are key benefits for manufacturers looking to reduce production times and costs. The automated nature of CNC machining eliminates the need for manual labor in repetitive tasks, allowing machines to work continuously without interruption. This significantly boosts productivity, especially in mass production environments where large quantities of identical parts need to be made quickly and consistently.
In addition to increased speed, CNC machining is also efficient in terms of material usage. Traditional machining methods often result in significant material waste, whereas CNC machines use precise cutting tools that maximize the use of raw materials, reducing waste and lowering costs. This efficiency is particularly valuable for industries that work with expensive materials, such as aerospace and medical manufacturing, where minimizing waste can lead to significant cost savings.
Moreover, CNC machines can work 24/7 without the need for rest or breaks, making them ideal for continuous production environments. The use of advanced CNC machines, combined with automation and robotics, allows for faster cycle times and more efficient workflows. These improvements in speed and efficiency have led to faster time-to-market for new products, giving manufacturers a competitive edge in an ever-evolving marketplace.
CNC Machining in Different Industries
CNC Machining in Aerospace and Defense
In the aerospace and defense industries, precision and reliability are paramount. CNC machining is indispensable in producing parts that meet the stringent quality standards required for aircraft, satellites, and defense equipment. CNC machines are capable of manufacturing complex parts such as turbine blades, engine components, and structural elements that require tight tolerances and high strength-to-weight ratios. The ability to work with advanced materials like titanium and high-performance alloys further enhances CNC machining’s suitability for aerospace applications.
The aerospace industry relies heavily on CNC machining for both prototyping and production. Prototyping is critical in aerospace as engineers need to test the design before committing to full-scale production. CNC machining allows manufacturers to produce high-precision prototypes quickly, allowing for design iterations and faster development cycles. Additionally, the customization capabilities of CNC machining allow for the production of specialized components that are unique to each aircraft or mission, supporting innovation in the field.
CNC Machining in Medical Device Manufacturing
In the medical industry, the need for precise and reliable components is even more critical, as these parts can directly impact patient health and safety. CNC machining is used extensively to manufacture medical devices, implants, surgical instruments, and diagnostic equipment. The precision and repeatability of CNC machining are essential in producing these devices with the exact specifications required for medical applications.
For instance, CNC machines are used to create custom orthopedic implants that must fit perfectly with a patient’s body. Similarly, surgical instruments such as scalpels, forceps, and drills require high levels of precision to ensure they function correctly and safely. In medical device manufacturing, the ability to work with a variety of materials, including bio-compatible metals and plastics, is crucial for ensuring that the devices are safe for use in the human body.
Furthermore, the customization capabilities of CNC machining have led to innovations in personalized medicine. With the ability to create custom-fitted implants and devices, CNC machining is helping to pave the way for more individualized treatments, which can improve patient outcomes and reduce recovery times.
CNC Machining in Automotive Manufacturing
The automotive industry has long relied on CNC machining for the production of parts that are both precise and durable. CNC machines are used to create engine components, transmission parts, brake systems, and other critical components that require exacting standards. The ability to machine complex shapes and intricate details ensures that these components fit together seamlessly, contributing to the overall performance and safety of the vehicle.
In addition to mass production, CNC machining also plays a key role in the customization of automotive parts. For high-performance vehicles and custom builds, CNC machining allows for the production of specialized components that enhance performance, such as custom pistons, turbochargers, and exhaust systems. This level of customization is essential for motorsport applications and other performance-driven industries where every fraction of a second counts.
Moreover, as the automotive industry shifts towards electric vehicles (EVs), CNC machining is becoming even more important. EVs often require specialized components such as battery enclosures, motor parts, and lightweight structural elements, all of which can be efficiently produced using CNC machining.
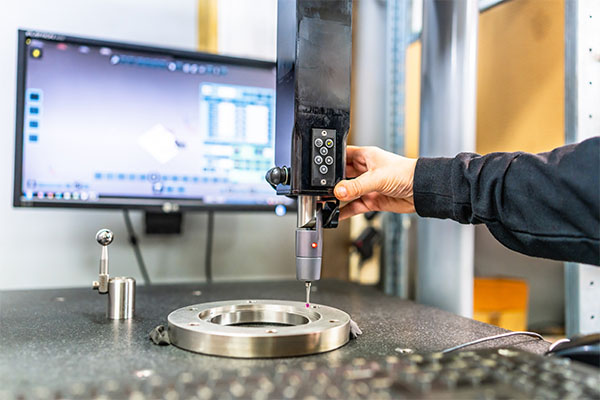
Innovative Applications of CNC Machining
Customization and Prototyping with CNC Machining
One of the major advantages of CNC machining is its ability to support customization and rapid prototyping. Here’s the deal, the flexibility of CNC machines makes them ideal for producing custom parts and prototypes for new products. Whether it’s a small batch of specialized components or a one-off custom design, CNC machining allows manufacturers to create parts with a high level of precision and minimal lead time.
Rapid prototyping with CNC machining helps companies test and refine their designs quickly, leading to faster product development cycles. Designers can create prototypes of their products in the same material they plan to use in mass production, ensuring that they are functionally and structurally sound. Once a prototype is created, adjustments can be made to the design, and the process can be repeated until the desired result is achieved. This iterative process fosters innovation by allowing designers to experiment with new ideas and concepts.
The ability to customize parts also supports innovation by allowing companies to develop unique solutions that are tailored to their specific needs. CNC machining enables the production of parts with complex geometries, intricate features, and specialized materials, opening up new possibilities for product design and manufacturing.
CNC Machining for Complex Geometries
One of the most exciting aspects of CNC machining is its ability to handle complex geometries that would be impossible with traditional machining methods. You might be wondering, how can CNC machines achieve such intricate shapes? The answer lies in the versatility of multi-axis CNC machines, which can move the workpiece and tool in several directions simultaneously, allowing for the creation of complex features such as curved surfaces, undercuts, and internal cavities.
These capabilities make CNC machining ideal for industries that require highly detailed and geometrically complex parts. Aerospace and automotive industries, for example, often require components with aerodynamically optimized shapes or intricate internal structures. CNC machines can easily produce these parts with exceptional precision, ensuring that they meet the required performance specifications.
Additionally, CNC machining’s ability to create detailed parts in a single setup reduces the need for multiple operations, which can help improve production efficiency. In other words, CNC machining enables the creation of parts that are not only complex but also high-performing, contributing to innovation across a variety of industries.
Integrating CNC with 3D Printing and Additive Manufacturing
As additive manufacturing (3D printing) technology continues to advance, CNC machining is increasingly being integrated with 3D printing to enhance the capabilities of both technologies. You might be thinking, how can these two technologies work together? The answer lies in the complementary strengths of CNC machining and 3D printing. While CNC machining excels at creating precise, high-performance parts from a variety of materials, 3D printing is perfect for rapid prototyping and creating parts with complex geometries that may be difficult or expensive to machine.
By combining the strengths of both technologies, manufacturers can produce parts that are not only highly functional but also innovative. For example, 3D printing can be used to quickly create prototypes or parts with intricate features, while CNC machining can be used to finish the parts, adding precision, strength, and a high-quality surface finish. This combination is especially useful in industries such as aerospace, automotive, and healthcare, where both performance and design complexity are essential.
Advancements in CNC Machining Technology
The Role of AI and Automation in CNC Machining
Here’s the deal—artificial intelligence (AI) and automation are becoming increasingly integrated into CNC machining systems, taking the technology to new heights. But wait, what exactly does AI have to do with CNC machining? AI enhances CNC machining by improving machine learning capabilities, predictive maintenance, and optimization of tool paths. These advancements allow CNC machines to work more efficiently, detect issues before they become problems, and continually improve their performance without human intervention.
With AI-powered systems, CNC machines can analyze data from previous machining operations to identify patterns and optimize future machining cycles. This reduces downtime and increases the overall productivity of the system. Additionally, predictive maintenance ensures that CNC machines are serviced before critical components fail, which reduces repair costs and extends the lifespan of the machine.
Furthermore, automation allows for lights-out manufacturing, where CNC machines can operate autonomously 24/7, without the need for constant human oversight. This ability to work continuously increases production capacity and drives efficiency, while also reducing labor costs. The integration of AI and automation is undoubtedly shaping the future of CNC machining, making it even more efficient and cost-effective.
The Future of CNC Machining: Trends and Innovations
The future of CNC machining looks incredibly promising, with continued advancements in machine capabilities, materials, and software. In other words, CNC machining is poised to remain at the forefront of manufacturing innovation. Some of the most exciting trends include the development of multi-axis machines that can handle even more complex geometries, the use of advanced materials such as composites and smart materials, and the continued integration of AI and robotics to further automate processes.
Another area of growth is the use of cloud-based systems for CNC programming and data analysis. By connecting CNC machines to the cloud, manufacturers can access real-time data, track machine performance, and make adjustments remotely. This connectivity allows for greater flexibility, efficiency, and collaboration in manufacturing processes.
As the demand for customized products and shorter production timelines continues to rise, CNC machining will continue to evolve to meet these needs. The combination of precision, flexibility, and innovation makes CNC machining an indispensable tool in the manufacturing world.
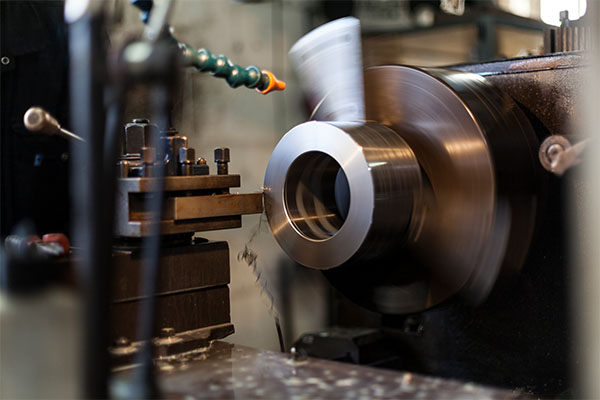
Challenges and Considerations in CNC Machining
Challenges in CNC Machining: Cost, Complexity, and Setup
While CNC machining offers many benefits, it does come with its challenges. You might be wondering, what are the major obstacles? First and foremost, CNC machining equipment can be expensive. The initial investment for high-quality CNC machines can be substantial, which can be a barrier for small businesses or startups. Additionally, the setup costs and time required to program CNC machines can also be considerable, especially when dealing with complex designs or new materials.
The complexity of operating CNC machines also requires skilled technicians. Although the machines themselves are highly automated, operators still need to have a deep understanding of programming, tool selection, and machine calibration to ensure that the parts are produced to the required specifications. For many companies, this means investing in employee training or hiring specialized personnel.
Despite these challenges, the long-term benefits of CNC machining often outweigh the initial costs, especially for businesses looking to scale their operations or produce highly customized products. By improving efficiency and reducing labor costs in the long run, CNC machining can offer a significant return on investment.
Conclusion
CNC machining plays a vital role in driving innovation across various industries. From precision parts in aerospace and medical devices to custom components in automotive manufacturing, CNC machining enables the production of high-quality, complex products with exceptional accuracy and efficiency. As technology continues to evolve, so too does the potential for CNC machining to revolutionize product design and manufacturing processes. If you’re looking to innovate, CNC machining offers the precision, speed, and versatility necessary to bring new ideas to life.
FAQ
What is the main advantage of CNC machining?
The main advantage of CNC machining is its ability to produce precise, high-quality parts with tight tolerances. This makes it ideal for industries that require accuracy, such as aerospace, automotive, and medical device manufacturing.
Can CNC machines work with any material?
Yes, CNC machines can handle a wide range of materials, including metals, plastics, and composites. The choice of material depends on the specific requirements of the part being produced.
How does CNC machining compare to traditional machining methods?
CNC machining offers greater precision, speed, and efficiency compared to traditional manual machining methods. It reduces human error, improves production consistency, and can operate continuously without the need for constant oversight.
Is CNC machining suitable for small batch production?
Yes, CNC machining is well-suited for both large and small batch production. It is particularly advantageous for custom parts and rapid prototyping due to its flexibility and precision.