Introduction
CNC machining, or Computer Numerical Control machining, has transformed the manufacturing industry, allowing for faster, more precise production of parts and components across a variety of industries. As businesses move towards automation, understanding the key benefits of CNC machining is crucial for anyone looking to improve efficiency and reduce costs in manufacturing. In this article, we’ll explore the top 5 advantages of CNC machining that can make a significant impact on your production process. Whether you are involved in manufacturing for automotive, aerospace, medical, or any other industry, these advantages will help you recognize the importance of incorporating CNC technology into your operations.
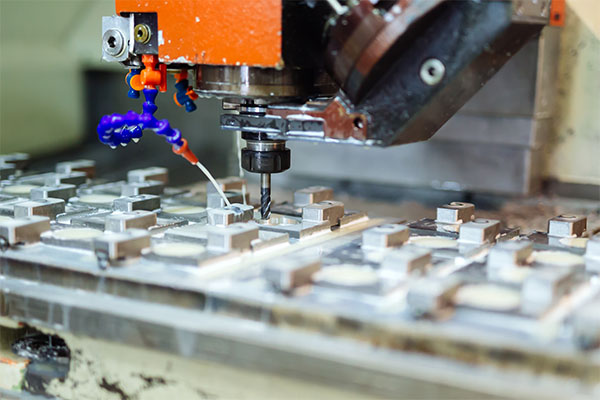
Qu'est-ce que l'usinage CNC ?
CNC machining is a manufacturing process where pre-programmed computer software controls the movement of tools and machinery. The term “CNC” stands for Computer Numerical Control, and it encompasses various machine tools like lathes, mills, routers, and grinders, which are used to cut, shape, and manipulate materials with high precision. The process operates by following instructions from a computer-generated design to produce parts that meet specific requirements. CNC machining is used to manufacture complex and intricate components that would be challenging or impossible to produce manually.
This technology began evolving in the mid-20th century and has since revolutionized industries such as aerospace, automotive, medical devices, electronics, and consumer goods. Unlike traditional manual machining methods, CNC machining eliminates the need for skilled operators to control machines, as the process is automated. The machines are programmed to produce parts quickly, with minimal human intervention. As a result, CNC machining has become the gold standard in modern manufacturing.
Why CNC Machining Matters in Modern Manufacturing
CNC machining plays an essential role in the modern manufacturing landscape. Its automated nature allows businesses to produce high-quality products at a faster rate and with fewer errors than manual processes. One of the most significant advantages of CNC machining is its precision. The automated tools are capable of making complex cuts and adjustments with extreme accuracy, allowing for consistent results every time. This is critical for industries like aerospace and medical device manufacturing, where safety and performance standards must be met with the utmost care.
In addition to its accuracy, CNC machining helps businesses save time and reduce production costs. By automating many of the tasks traditionally carried out by human workers, CNC machines can operate continuously with minimal downtime. This increases throughput, reduces labor costs, and ensures that products are produced on schedule. With CNC machining, businesses are able to meet growing demand without sacrificing quality.
Advantage #1: Precision and Accuracy
CNC machining is known for its exceptional precision and accuracy. The ability to manufacture parts with tight tolerances and intricate designs is one of the primary reasons businesses choose CNC technology over traditional methods. With CNC machines, every cut, hole, and shape is made based on highly specific measurements programmed into the system. This level of accuracy ensures that parts are consistently produced according to design specifications, with little to no deviation.
Precision is particularly important in industries such as aerospace, automotive, and medical device manufacturing, where even the smallest imperfection can have significant consequences. For example, an aerospace part that doesn’t meet precise specifications could fail during operation, leading to safety risks and costly recalls. CNC machines, however, can produce these components to within a few microns of the specified dimensions, minimizing the chances of error. This is why CNC machining is trusted by industries that require a high degree of precision.
Furthermore, CNC machines are capable of handling complex geometries and multi-axis cuts. This makes it possible to create parts with shapes that would be extremely difficult to achieve manually. With advancements in CNC technology, machines can now work with materials such as titanium, steel, and aluminum, all while maintaining a high level of precision throughout the manufacturing process.
Advantage #2: Efficiency and Speed
One of the key benefits of CNC machining is its ability to significantly improve production efficiency and speed. In traditional machining, parts often require multiple operations to be completed by different machines or human operators. CNC machines, however, can perform all of these operations in one continuous process, reducing the need for rework and manual intervention. This drastically reduces production time and increases throughput.
CNC machines are designed to run continuously, 24/7, without the need for breaks, sleep, or downtime, except during maintenance. As a result, businesses can ramp up their production capacity, fulfilling large orders in shorter time frames. This level of automation leads to a faster turnaround time for both prototype development and mass production, making it easier for businesses to meet customer demands and stay competitive in the marketplace.
With CNC machines, manufacturers can also reduce the risk of human error, which is often a significant cause of production delays in traditional manufacturing processes. Once a part is programmed into the machine, it will consistently perform the same task with high precision, ensuring that every part produced is identical to the last. This consistency helps streamline the production process, making it easier to meet tight deadlines and reduce lead times.
Advantage #3: Flexibility and Customization
CNC machining offers unparalleled flexibility when it comes to customizations. With traditional methods, creating customized parts can be costly and time-consuming, especially if small changes to the design are needed during production. However, CNC machines allow manufacturers to make quick adjustments to the design by simply modifying the computer code, which is significantly faster and more affordable than manually changing the setup of traditional machines.
CNC technology is also highly adaptable to a wide range of materials. Whether you are working with metal, plastic, wood, or composite materials, CNC machines can handle them all with the same level of precision. This versatility makes CNC machining a go-to solution for industries that require different types of materials for custom products.
This ability to quickly adapt to changing designs and material requirements makes CNC machining a powerful tool for product development. Whether you are creating a prototype, designing a one-off custom part, or manufacturing a small batch of products, CNC machines can accommodate your specific needs. By reducing the time required for design changes and ensuring that modifications are carried out with minimal disruption, CNC machining makes customization easier and more cost-effective than ever before.
Advantage #4: Cost Efficiency in the Long Term
Although the initial investment in CNC machinery can be high, the long-term savings it provides are undeniable. CNC machines help reduce production costs in several key ways. First, they minimize the need for manual labor, cutting down on labor costs. By automating tasks, businesses can save money by reducing the number of skilled operators required on the shop floor. Additionally, CNC machines reduce material waste due to their precision, as parts are cut according to exact specifications with minimal scrap material.
Another cost-saving aspect of CNC machining is the speed at which machines can operate. By producing parts faster, businesses can take on more orders, meet tighter deadlines, and increase their overall output. The higher throughput and improved efficiency make it easier for businesses to scale their operations without investing heavily in additional workforce or resources.
CNC machining also reduces the likelihood of mistakes and defects, which can be costly to fix. In traditional manufacturing, parts that are off-spec must be scrapped or reworked, adding extra costs to the production process. With CNC technology, the likelihood of human error is minimized, ensuring that the first part produced is also the final, quality-assured part.
Advantage #5: Consistency and Repeatability
CNC machining ensures that every part produced is identical to the last, making it perfect for businesses that require high levels of consistency and repeatability in their production runs. Once a design is inputted into the CNC machine, it can be replicated thousands of times without variation. This is crucial for mass production and ensures that every item meets the same specifications, quality standards, and performance metrics.
In industries such as medical device manufacturing and electronics, the ability to produce consistent and reliable parts is critical. Even the smallest deviation in a part’s dimensions can result in malfunction or safety concerns. CNC machines ensure that these parts are produced with consistent quality, every time. This reliability also helps businesses build trust with their customers, as they can depend on receiving parts that meet exact specifications.
Repeatability is another benefit of CNC machining. When a machine produces a part once, it can replicate that same part repeatedly without deviation, ensuring uniformity across all units produced. This is especially important for manufacturers that produce large quantities of parts or components for complex assemblies.
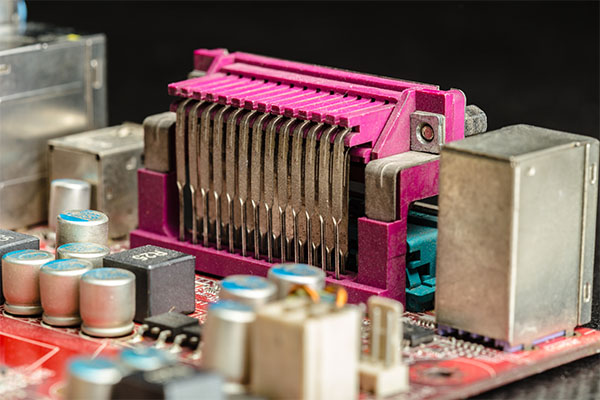
Material Variety and Compatibility
CNC machining is compatible with a wide range of materials, including metals, plastics, and composites, making it an ideal choice for businesses with diverse production needs. Whether you need to create complex metal parts for the aerospace industry or durable plastic components for consumer goods, CNC machining offers the flexibility to handle different materials with ease.
Each material has its own set of properties, and CNC machines are designed to work with these varying characteristics. For example, metal parts often require higher cutting speeds and more powerful machines, while plastic components may require softer tools and slower cutting speeds. CNC technology is versatile enough to handle all of these material requirements without compromising on precision or quality.
Additionally, CNC machines can be programmed to work with a variety of finishes, textures, and surface treatments, adding another layer of customization to the production process. Whether it’s anodizing, painting, or polishing, CNC machining ensures that the finished product meets the desired aesthetic and functional qualities.
The Role of CNC Software in the Process
CNC software plays a crucial role in the machining process, enabling manufacturers to convert digital designs into machine-readable instructions. These software programs are responsible for controlling the movement of the CNC machine, determining the cutting path, and ensuring that every operation is performed according to plan.
Popular CNC software programs such as SolidWorks, AutoCAD, and Fusion 360 provide manufacturers with powerful tools for designing and simulating their projects before they are executed on the machine. With the right CNC software, engineers can optimize their designs for efficiency, performance, and cost-effectiveness. Additionally, CNC software can help streamline the production process by minimizing the need for manual adjustments, further reducing the likelihood of human error.
One of the key advantages of CNC software is its ability to accommodate complex geometries and multi-axis machining. By enabling the machine to move along multiple axes, CNC software makes it possible to produce parts with intricate shapes and designs that would be impossible to achieve with traditional methods.
CNC Machining for Small Batches vs Mass Production
CNC machining is versatile enough to handle both small-batch production and large-scale mass manufacturing. For businesses that require custom parts or prototypes, CNC machining offers a cost-effective and efficient solution. The ability to make adjustments to the design quickly and easily makes CNC machining perfect for creating one-off or low-volume parts.
However, CNC machining is equally capable of handling mass production. Once a design is finalized, CNC machines can replicate the same part thousands of times with consistent quality and precision. For manufacturers producing high volumes of parts, CNC machines provide the speed and reliability needed to meet demand while maintaining quality standards. The efficiency of CNC machines helps businesses scale their production to meet market needs without sacrificing consistency or precision.
Challenges and Limitations of CNC Machining
While CNC machining offers numerous advantages, there are some challenges and limitations to consider. One of the most significant challenges is the high initial investment cost of purchasing CNC machinery. These machines can be expensive, especially for small businesses or startups. However, the long-term benefits and cost savings often outweigh the upfront costs.
Another limitation of CNC machining is the need for skilled operators to program and maintain the machines. While CNC machines reduce the need for manual labor, having a knowledgeable team to oversee machine operations is essential to ensure smooth and efficient production.
Additionally, CNC machines are limited by their design and can only work with specific materials and sizes. For extremely complex or delicate designs, traditional manufacturing methods or alternative technologies like 3D printing may be more suitable.
Initial Investment Costs and Maintenance
The upfront cost of CNC machinery can be significant, and for smaller businesses, this can be a barrier to adoption. However, many businesses find that the investment pays off quickly due to increased productivity, reduced labor costs, and higher-quality output. Over time, the machine’s efficiency helps recover the cost of the initial purchase. Regular maintenance is also essential to ensure that the CNC machines continue to operate at peak efficiency.
Maintaining CNC machines involves routine checks and servicing, which may include calibrating parts, replacing worn tools, and cleaning the machine. Investing in proper maintenance schedules and training for staff can help minimize downtime and extend the lifespan of the machine. This makes CNC machines a reliable investment for businesses that rely on high production standards and efficiency.
Limitations in Complex Designs
CNC machining excels in producing parts with relatively simple or moderately complex designs. However, for designs that are extremely intricate or require delicate details, CNC machining may not always be the best solution. In these cases, additional techniques like 3D printing or traditional handcrafting might be more appropriate. CNC machines can be adapted to handle some level of complexity, but for extremely detailed or artistic designs, manual intervention may still be required.
Additionally, the size and scope of the CNC machine can limit the complexity of the design. Large parts or designs that require multi-dimensional components may exceed the capacity of standard CNC machines, requiring specialized equipment or different manufacturing methods.
Industries Benefiting from CNC Machining
CNC machining is widely used across various industries due to its precision, efficiency, and flexibility. Some of the key sectors benefiting from CNC machining include:
- Aérospatial: Manufacturing lightweight yet durable parts for aircraft and spacecraft.
- Automobile: Producing high-performance components for vehicles.
- Dispositifs médicaux: Creating precise parts for medical instruments and implants.
- Electronics: Fabricating small, intricate components for consumer electronics.
- Consumer Goods: Designing custom parts for everything from furniture to tools.
Each of these industries requires precision and consistency, making CNC machining an invaluable tool for their production needs.
Tendances futures de l'usinage CNC
As technology advances, CNC machining continues to evolve. The introduction of AI and machine learning has enhanced the capabilities of CNC machines, enabling them to optimize their processes autonomously. The integration of 5G technology and IoT (Internet of Things) allows for real-time monitoring and data analytics, improving decision-making and machine performance.
Additionally, CNC machining is becoming increasingly sustainable, with manufacturers incorporating eco-friendly practices into their operations. Innovations in material processing and recycling will continue to reduce waste and improve energy efficiency.
The future of CNC machining looks promising, with continuous advancements making it even more efficient and adaptable to the needs of various industries.
Conclusion
CNC machining has undeniably revolutionized the manufacturing world, offering numerous benefits that make it the go-to solution for businesses aiming to improve production efficiency, precision, and quality. The five key advantages—precision and accuracy, efficiency and speed, flexibility and customization, long-term cost savings, and consistency—are integral to industries ranging from aerospace to medical devices. By integrating CNC technology, businesses can meet growing market demands while maintaining the highest standards of quality.
While there are some challenges, such as high initial costs and the need for skilled operators, the long-term advantages far outweigh the drawbacks. The ability to produce complex parts with unparalleled accuracy, speed, and cost efficiency makes CNC machining a powerful tool for any manufacturer. As technology continues to evolve, CNC machines will only become more advanced, offering even greater capabilities and further solidifying their importance in modern manufacturing.
For businesses looking to stay ahead of the competition and ensure their products meet the highest standards, investing in CNC machining is a wise decision. Whether you’re producing small batches, prototypes, or mass production runs, CNC technology will enable you to achieve greater consistency, reduce waste, and improve overall efficiency. Don’t miss the opportunity to enhance your production process with CNC machining.
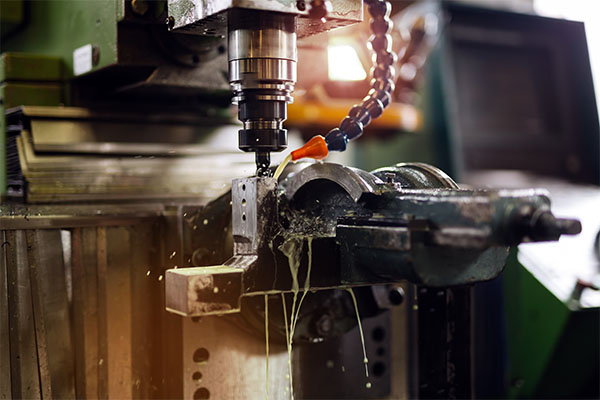
Section FAQ
- What are the most common types of CNC machines used? CNC machines come in several types, each designed for different tasks. The most common types include CNC mills, which are used to cut and shape materials, CNC lathes, which rotate materials to perform cutting tasks, and CNC routers, which are used for cutting softer materials like wood and plastic. Each machine type has its strengths and is used based on the specific requirements of the project.
- Is CNC machining only used for metal parts? No, CNC machining is not limited to metal parts. While it is widely used for metals such as steel, aluminum, and titanium, CNC machines can also work with plastics, composites, wood, and other materials. This versatility makes CNC machining suitable for a broad range of industries, including automotive, aerospace, medical, and consumer goods.
- What’s the difference between CNC machining and 3D printing? CNC machining and 3D printing are both used to create parts, but they operate differently. CNC machining involves subtracting material from a solid block using precision tools, while 3D printing adds material layer by layer. CNC is ideal for producing high-precision parts from a variety of materials, while 3D printing is often used for prototyping and producing complex geometries that may not be feasible with CNC machining.
- How do I choose the right CNC machine for my business? Choosing the right CNC machine depends on several factors, including the material you plan to work with, the complexity of the parts, and the volume of production. For small, intricate parts, a CNC mill or router may be ideal. For larger, cylindrical parts, a CNC lathe might be more suitable. It’s also important to consider the machine’s capacity, programming capabilities, and your business’s specific needs when making a selection.
- Can CNC machines handle large production runs? Yes, CNC machines are well-suited for both small and large production runs. Once a design is programmed, the machine can replicate the part thousands of times with high consistency and precision. This makes CNC machining ideal for mass production, especially when consistency and quality are critical. However, depending on the complexity of the design, some setups may require additional time for initial programming or tool changes.
Closing Thoughts
The incorporation of CNC machining into your production process opens up a world of possibilities for businesses of all sizes. By offering exceptional precision, increased efficiency, and the ability to handle complex designs with ease, CNC technology provides a competitive edge in today’s fast-paced manufacturing landscape. Whether you are a small business looking to optimize production or a large manufacturer aiming to improve consistency, CNC machining can help meet your goals.
As industries evolve, so too does the technology behind CNC machining. Investing in this technology today will help you stay ahead of the competition, ensuring that your products are not only high-quality but also produced in a timely and cost-effective manner. The future of manufacturing is here, and CNC machining is at the forefront of that revolution.
So, if you’re looking to take your manufacturing operations to the next level, now is the time to explore CNC machining’s potential. With its precision, speed, and flexibility, it’s the technology that can propel your business toward success in the global market.