Introduction
Usinage de grandes pièces is a crucial aspect of manufacturing in industries such as aerospace, automotive, and heavy equipment. The ability to machine large components with precision and speed can significantly impact the efficiency and quality of production. In this article, we will explore the challenges, techniques, and tools involved in machining large parts, along with best practices to achieve optimal results. By the end, you’ll have a comprehensive understanding of how to master the art of machining large parts with precision and speed.

1. What is Machining Large Parts?
Machining large parts refers to the process of shaping and manufacturing large-scale components that are used in various industries. These parts often require specialized equipment and techniques to ensure that they meet precise specifications. But here’s the kicker — large part machining isn’t as straightforward as standard machining. It involves a unique set of challenges that demand specific skills, equipment, and strategies.
Large parts can be anything from engine blocks for cars to large aircraft components, and they require machines capable of handling their size and weight. The material used in these parts varies widely, but often includes metals like steel, aluminum, and titanium, which require different approaches to achieve the desired results.
What’s the real story? The real story is that precision and speed are paramount. The larger the part, the more difficult it is to achieve tight tolerances, which means the stakes are higher. In addition to the challenges of size and weight, machinists also need to take into account the properties of the materials being used.
Here’s a quick breakdown of key aspects of large part machining:
Aspect | Importance |
---|---|
Size | Machines must accommodate larger components |
Matériel | Material properties impact cutting speeds |
Précision | Tight tolerances are essential for functionality |
Ready for the good part? Let’s dive deeper into the challenges of machining large parts and how to overcome them.
2. What Are the Challenges of Machining Large Parts?
Machining large parts comes with its own set of unique challenges. These challenges not only affect the machining process but also the final quality of the product. Understanding these challenges can help manufacturers find effective solutions to ensure quality results.
One of the biggest hurdles in large part machining is dealing with the size and weight of the components. The larger the part, the more difficult it is to handle. This adds complications in terms of setup, clamping, and even transportation between different stages of machining. But here’s the kicker — even slight imbalances in how a large part is handled can lead to distortions or inaccuracies.
Material variability is another challenge. When machining large parts, you are often working with materials that have varying properties. For instance, metals like titanium may require a different cutting speed and tool material compared to aluminum. This can complicate the machining process, as the tools and machines need to adapt to these changes.
Additionally, machine limitations come into play. Not all machines are built to handle such large parts. This requires manufacturers to invest in specialized equipment, like CNC machines with extended work tables or custom fixtures, to accommodate the size and ensure accuracy.
Here’s a comparison of common challenges when machining large parts:
Défi | Effect on Process | Solution |
---|---|---|
Taille et poids | Handling difficulties, potential distortions | Use specialized fixtures and machines |
Material variability | Varying cutting speeds and tool wear | Select tools based on material type |
Machine limitations | Equipment may not be suitable for large parts | Invest in larger, specialized machinery |
So, what’s the real solution? Let’s look at ways to mitigate these challenges and achieve precision in large part machining.
3. How Can You Ensure Precision in Large Part Machining?
Ensuring precision in large part machining is critical, as even the smallest error can lead to significant problems in the final product. So, what’s the secret? It’s all about the tools, techniques, and careful planning.
The first step in ensuring precision is selecting the right tools and equipment. CNC machines are commonly used for machining large parts because they offer a high level of accuracy and can handle complex geometries. However, selecting the right cutting tools is equally important. Cutting tools should be chosen based on the material being machined and the required tolerances. For example, carbide tools are often used for harder metals like titanium, as they offer longer tool life and better performance.
But wait, there’s more — machine calibration plays a huge role in maintaining precision. A machine that isn’t properly calibrated can lead to errors in positioning, causing parts to be cut incorrectly. Regular maintenance and calibration are essential for ensuring that the machine operates at optimal performance.
In addition to equipment, using CAD and CAM systems is a game-changer. These software tools allow for more accurate planning and simulation of the machining process. CAD (Computer-Aided Design) helps in designing the part with precise dimensions, while CAM (Computer-Aided Manufacturing) translates that design into machining instructions for the machine tools.
Here’s how these elements work together:
Element | Importance | Example Tools |
---|---|---|
CNC Machines | High precision, automated processes | Haas, Siemens |
Machine Calibration | Ensures accuracy, reduces errors | Regular machine check-ups |
CAD/CAM Software | Accurate design and machining instructions | AutoCAD, Mastercam |
So, now that you know how to ensure precision, let’s move on to selecting the right machines for the job.
4. What Types of Machines Are Used for Large Part Machining?
When it comes to machining large parts, choosing the right machine is essential. Not all machines can handle the size, weight, and complexity of these components. What’s the real story? There are specific machines built for large part machining that provide the precision and power needed to handle heavy-duty tasks.
CNC (Computer Numerical Control) machines are some of the most commonly used machines for machining large parts. These machines offer incredible precision, which is essential for large components that require tight tolerances. CNC machines can perform a variety of tasks, from drilling and milling to turning and grinding, making them highly versatile.
Horizontal and vertical milling machines are also crucial for machining large parts. Horizontal mills are particularly effective for large parts because they can handle heavier workpieces and have a larger table area. On the other hand, vertical mills are great for precision work and are commonly used for smaller components but can still handle parts up to a certain size.
But here’s the kicker — some specialized machines, such as gantry mills and boring mills, are designed specifically for large parts. These machines provide additional stability and larger work tables to accommodate hefty components.
Here’s a breakdown of common machines used for large part machining:
Type de machine | Avantages | Example Uses |
---|---|---|
CNC Machines | High precision, versatility | Aerospace, automotive parts |
Horizontal Milling | Larger worktables, better stability | Engine blocks, large brackets |
Vertical Milling | Precision work, flexible setup | Smaller large parts |
Gantry Mills | Large size capacity, greater stability | Heavy-duty components |
Ready to dive deeper? Let’s explore how material selection impacts large part machining.
5. How Do You Choose the Right Material for Large Parts?
Choosing the right material for large parts is a crucial decision that can affect everything from machining speed to tool wear and part durability. Here’s the thing — not all materials are created equal when it comes to machining.
Common materials used in large part machining include metals like steel, aluminum, and titanium. Each of these materials has its own set of challenges. For example, steel is tough and durable but can be difficult to machine due to its hardness. On the other hand, aluminum is easier to machine but may not be suitable for parts that need to withstand extreme temperatures or pressures.
Titanium is another material commonly used in high-performance industries like aerospace. It’s strong and lightweight, but it can be tricky to machine due to its tendency to work-harden. The key is selecting the material that best suits the part’s intended use while considering machinability factors such as tool wear, cutting speed, and finish quality.
Here’s a quick comparison of materials commonly used for large part machining:
Matériel | Avantages | Inconvénients |
---|---|---|
Acier | Strong, durable, versatile | Hard to machine, tool wear |
Aluminium | Lightweight, easy to machine | May not be suitable for high-stress applications |
Titane | Strong, lightweight, corrosion-resistant | Expensive, difficult to machine |
So, now that we understand material selection, let’s move on to how machining speeds affect large part production.
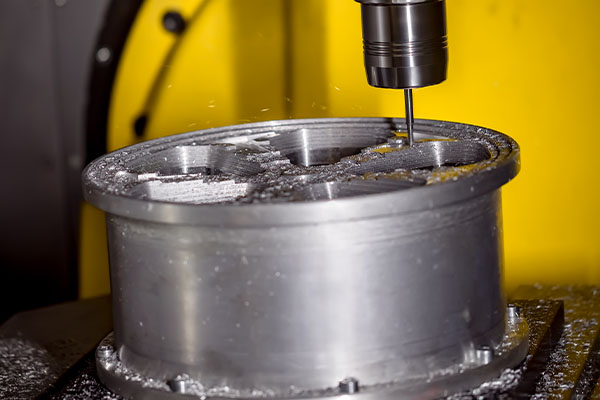
6. How Do Machining Speeds Affect Large Part Production?
Machining speed is an essential factor when it comes to producing large parts. It directly influences both production time and the final quality of the part. But here’s the kicker — going too fast or too slow can lead to unwanted outcomes.
For example, cutting speeds that are too high can cause excessive tool wear and poor surface finish, while cutting speeds that are too low can lead to longer production times. The ideal speed depends on the material being machined and the desired finish quality. Let’s look at how different materials react to speed changes.
For softer materials like aluminum, higher cutting speeds can be used without compromising the tool’s life or the part’s quality. However, for harder materials like titanium, slower cutting speeds are necessary to avoid damaging the tool or the part itself.
Here’s how machining speeds vary by material:
Matériel | Ideal Cutting Speed | Effect of Too Fast/Too Slow |
---|---|---|
Aluminium | High speed | Faster production, but risks tool wear |
Acier | Medium speed | Balanced speed ensures durability |
Titane | Low speed | Avoids tool damage, but slower production |
What’s the takeaway? Finding the right speed is crucial for achieving a balance between efficiency and quality.
7. What Are the Best Practices for Machining Large Parts Efficiently?
Usinage de grandes pièces efficiently requires careful planning and smart use of technology. So, what’s the secret? It’s about optimizing every step of the process, from initial design to final machining.
One of the best practices is to thoroughly plan the machining process. This involves selecting the right tools, calculating optimal cutting speeds, and considering how to handle the part during machining. Another key practice is minimizing setup time by using efficient fixtures and jigs that allow for quick changes between operations.
But wait, there’s more — tool wear can significantly impact efficiency. To minimize this, it’s important to use high-quality tools and maintain them properly. Regular tool inspection and replacement will ensure that machining speeds remain consistent and that quality is maintained.
Here’s a list of best practices to optimize machining efficiency:
Best Practice | Avantage |
---|---|
Thorough planning | Reduces mistakes, optimizes steps |
Quick setup times | Increases overall production rate |
Tool maintenance | Reduces downtime, improves consistency |
So, how do you handle large parts during machining? Let’s move on to the next section.
8. How Do You Handle Large Parts During Machining?
Handling large parts during machining is crucial to maintaining precision and preventing damage. So, how do you do it right? The key lies in using the right handling and fixturing techniques.
One of the most common methods is using special clamping fixtures that securely hold the part in place while allowing for precise cuts. The part needs to be carefully balanced and supported to avoid deflection or deformation. A common mistake is not securing the part properly, leading to vibrations that affect machining accuracy.
But here’s the kicker — oversized parts often need specialized equipment like cranes or overhead hoists for transportation between workstations. In some cases, rotating fixtures or even robotic arms are used to handle heavy or awkwardly shaped parts.
Here’s a table of common handling methods and their advantages:
Handling Method | Advantage | Example Use |
---|---|---|
Clamping fixtures | Securely holds parts, prevents vibration | CNC machines, milling machines |
Overhead hoists | Facilitates movement of large parts | Transporting parts between stations |
Robotic arms | Precision handling, reduces human error | Aerospace parts, large components |
Now that we know how to handle parts properly, let’s discuss how to improve the surface finish of large parts.
9. What Are the Key Techniques to Improve Surface Finish on Large Parts?
Achieving a smooth surface finish is essential for large parts, especially when they are used in applications where precision and aesthetics matter. What’s the real story? The key to a perfect finish lies in using the right cutting tools and techniques.
One method is to use finer cutting tools and slower feed rates to reduce the roughness of the surface. Additionally, using coolant during the machining process can help to keep the temperature down, preventing tool wear and ensuring a better finish.
But wait, there’s more — surface finishing can also be improved after machining through polishing or grinding. These post-machining processes can remove any remaining imperfections and achieve the desired smoothness.
Here’s a comparison of surface finishing methods:
Méthode | Avantages | Ideal Use |
---|---|---|
Fine cutting tools | Reduces roughness, improves finish | Precision parts, high-quality products |
Polishing and grinding | Removes imperfections, adds gloss | Final finishing, aesthetic requirements |
What’s the takeaway? To improve the surface finish, use fine tools, slow down the feed rate, and finish with polishing or grinding.
10. How Can You Minimize Waste in Large Part Machining?
Minimizing waste in large part machining is essential for both cost efficiency and environmental sustainability. But here’s the kicker — reducing waste doesn’t just mean saving material; it also means optimizing every step of the process to maximize productivity.
One of the first steps in reducing waste is selecting the right material. This includes using materials that are suited to the part’s function while ensuring the machining process results in minimal scrap. In some cases, recycling leftover material is possible, and advanced machines can even reuse scrap for future parts.
Another effective method is optimizing tool paths through software like CAD/CAM. These programs allow machinists to plan the cutting process in a way that reduces excess material removal. For example, they can specify the most efficient tool paths that require fewer passes or adjust the cutting depth to minimize scrap.
But wait, there’s more — using advanced cutting techniques like high-efficiency machining (HEM) can significantly reduce material waste. This technique uses optimized cutting parameters that allow for faster, more efficient machining, which also reduces the amount of material lost during the process.
Here’s a quick comparison of techniques to reduce waste:
Technique | Avantage | Example Use |
---|---|---|
Optimized tool paths | Reduces scrap, saves material | CAD/CAM software |
Material selection | Minimizes excess, ensures material is used efficiently | Aerospace, automotive parts |
High-efficiency machining | Reduces material loss and boosts speed | Large metal components, engine blocks |
So now that we know how to reduce waste, let’s dive into some advanced machining techniques for large parts.
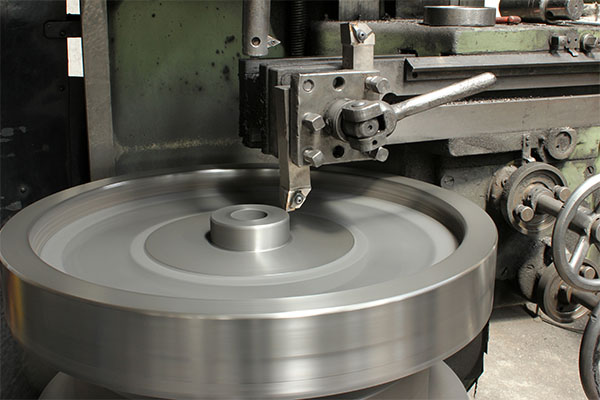
11. What Are Some Advanced Machining Techniques for Large Parts?
Advanced machining techniques can significantly improve the efficiency, precision, and capabilities of large part manufacturing. But here’s the kicker — using these techniques might require investment in new equipment and software, but the payoff can be substantial.
One such advanced technique is additive manufacturing, or 3D printing. While traditionally used for smaller parts, recent advancements have enabled 3D printing to be integrated with conventional machining processes. This hybrid approach allows for faster production of large, complex parts that would be difficult or expensive to machine entirely through traditional methods.
Another technique is robotic machining, where robots are used to automate certain aspects of the machining process. Robotic arms can handle repetitive tasks, such as material handling and part positioning, reducing human error and improving consistency.
Additionally, automated machining systems that combine CNC controls with robotics are gaining popularity. These systems can perform tasks like part clamping, part transport, and tool changes automatically, allowing for longer production runs with less downtime.
Here’s a breakdown of advanced techniques:
Technique | Avantages | Example Use |
---|---|---|
Fabrication additive | Faster production, complex geometries | Aerospace, custom parts |
Robotic machining | Reduces human error, automates tasks | Automotive parts, repetitive tasks |
Automated machining systems | Increases efficiency, reduces downtime | Large-volume production runs |
Now that we’ve covered advanced techniques, let’s talk about how to maintain large machining equipment.
12. How Do You Maintain Large Machining Equipment?
Maintaining large machining equipment is crucial to ensuring it operates efficiently and lasts for many years. But here’s the kicker — proper maintenance goes beyond routine check-ups. It involves keeping the machines in top condition to avoid costly downtime and repairs.
Regular maintenance schedules are essential for ensuring equipment performs at its best. This includes checking key components like the spindle, bearings, and tool holders. Machine operators should be trained to identify signs of wear and tear before they lead to failures.
Another important aspect of maintenance is lubrication. Proper lubrication reduces friction, which can cause parts to wear out faster. It also helps maintain the precision of the machine by ensuring that moving parts work smoothly.
But wait, there’s more — performing diagnostic tests can also help identify issues before they become major problems. Using sensors and monitoring systems to check for irregularities in temperature, vibration, or pressure can alert operators to issues early on.
Here’s a breakdown of essential maintenance practices:
Maintenance Task | Importance | Example Practice |
---|---|---|
Regular inspection | Identifies wear and tear, prevents failures | Check spindle, tool holders |
Lubrication | Reduces friction, maintains precision | Use high-quality lubricants |
Diagnostic testing | Detects potential issues early | Monitor temperature, vibration |
Ready to move on to the safety considerations for machining large parts? Let’s dive into the next section.
13. What Are the Safety Considerations for Machining Large Parts?
Machining large parts involves high-speed equipment and heavy machinery, so safety is always a top priority. But here’s the kicker — the bigger the part, the more dangerous it can be, which makes proper safety protocols essential.
One of the key safety considerations is ensuring that all workers are properly trained. This includes understanding how to operate machines safely, how to handle large parts, and how to recognize potential hazards. Ensuring that workers are familiar with safety equipment, such as protective gloves, goggles, and ear protection, is also crucial.
Handling large parts also requires specific safety measures. These parts can be heavy and awkward to move, so it’s important to use appropriate lifting equipment like cranes or hoists. Using proper clamping and fixturing techniques can also prevent the part from shifting during machining, which can cause accidents or machine damage.
But wait, there’s more — creating a safe work environment involves maintaining the machines and ensuring they are free from defects. Machines that are not properly maintained can malfunction, leading to accidents or injuries.
Here’s a quick checklist of safety considerations:
Safety Measure | Importance | Example Use |
---|---|---|
Worker training | Prevents accidents, ensures safety | Safety courses, machine operation training |
Proper handling | Prevents injuries from heavy parts | Use hoists, cranes, and fixtures |
Machine maintenance | Avoids malfunctions and injuries | Regular machine inspections |
With safety covered, let’s discuss how to improve the overall quality of large parts machining.
14. How Can You Improve the Quality of Large Parts Machining?
Improving the quality of large parts machining is a continuous process that involves optimizing several factors. But here’s the kicker — it’s not just about precision; it’s about maintaining consistency across all parts, every time.
One way to improve quality is by implementing strict quality control systems. These systems ensure that each part is measured against predefined tolerances and that any discrepancies are detected early. This can be achieved through visual inspections or by using high-precision measuring instruments such as CMMs (Coordinate Measuring Machines).
Training employees is another critical aspect. Skilled workers are more likely to produce high-quality parts, as they understand how to handle equipment and materials properly. Providing continuous education and training ensures that employees stay up-to-date with the latest techniques and technologies.
But wait, there’s more — implementing continuous improvement practices can further enhance machining quality. Using feedback loops and reviewing production data allows manufacturers to identify areas where efficiency or quality can be improved.
Here’s a breakdown of key practices to improve machining quality:
Pratique | Importance | Example Use |
---|---|---|
Quality control systems | Ensures parts meet tolerances and specifications | Visual inspections, CMM testing |
Employee training | Ensures skilled workers produce better parts | Regular training sessions |
Continuous improvement | Improves overall efficiency and quality | Analyzing production data, feedback loops |
15. What Are the Future Trends in Large Part Machining?
The future of usinage de grandes pièces looks promising, with new technologies driving efficiency and precision to new heights. But here’s the kicker — staying ahead of the curve requires adopting these emerging trends to maintain competitiveness in the industry.
One trend that’s gaining traction is the use of additive manufacturing in combination with traditional machining. This hybrid approach allows manufacturers to create complex geometries that would be difficult or impossible to achieve with conventional methods. For instance, 3D printing can be used to create intricate internal structures, while traditional machining finishes the external surfaces.
Automation is another major trend. Automated machining systems, including robots, are being increasingly used to streamline production processes. These systems can perform tasks such as loading and unloading parts, tool changes, and even quality checks, reducing the need for manual labor and increasing overall efficiency.
But wait, there’s more — the integration of smart manufacturing and IoT (Internet of Things) technology is revolutionizing large part machining. Sensors embedded in machines provide real-time data on performance, which can be used to predict when maintenance is needed, optimize production schedules, and improve part quality.
Here’s a snapshot of future trends:
Trend | Impact | Example Use |
---|---|---|
Fabrication additive | Enables complex designs, faster production | Aerospace, automotive parts |
Automation | Reduces labor, increases efficiency | Robotic arms, automated systems |
Smart manufacturing | Real-time data improves performance and quality | IoT sensors, predictive maintenance |
As we’ve seen, the future of large part machining is about embracing innovation and leveraging new technologies to improve efficiency and quality.
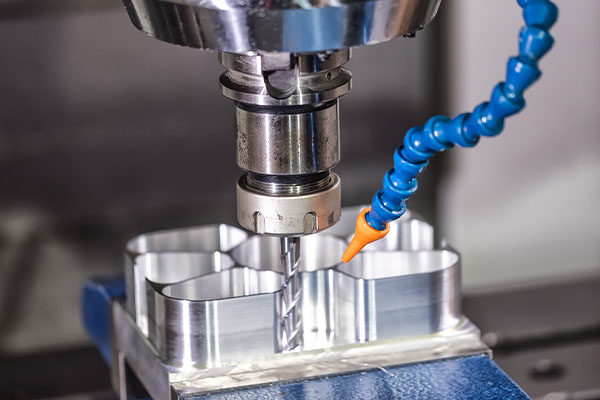
Section FAQ
Q1: What is machining large parts?
Machining large parts refers to the process of shaping and manufacturing large components, often for industries like aerospace, automotive, and heavy machinery. It requires specialized tools and techniques to achieve precision and efficiency.
T2 : How does large part machining work?
Large part machining works by using specialized equipment, such as CNC machines and milling machines, to cut and shape large components. The process involves careful planning, material selection, and machine calibration to ensure precision.
T3 : Quels sont les défis de l’usinage de grandes pièces ?
Challenges include managing the size and weight of components, handling material variability, and dealing with machine limitations. Special equipment is often needed to accommodate large parts and achieve the necessary precision.
T4 : How do I choose the right machine for machining large parts?
Choosing the right machine depends on the part’s size, material, and required precision. Common options include CNC machines, horizontal milling machines, and specialized equipment like gantry mills for larger parts.
Q5 : How can I ensure the efficiency of machining large parts?
Efficiency can be ensured by planning the machining process in detail, optimizing tool paths, minimizing setup time, and using high-quality tools. Additionally, maintaining equipment and reducing downtime is key to maximizing production.