Introduction
Choisir le bon metal CNC machine can seem like a daunting task, especially with so many options available in the market today. With the advancements in technology and the wide variety of machines on the market, it’s easy to get lost in the details. This article will help you understand the essential factors you need to consider when selecting the best metal CNC machine for your needs. By the end of this guide, you’ll have a clear idea of how to choose the machine that will optimize your production capabilities and meet your business’s requirements.
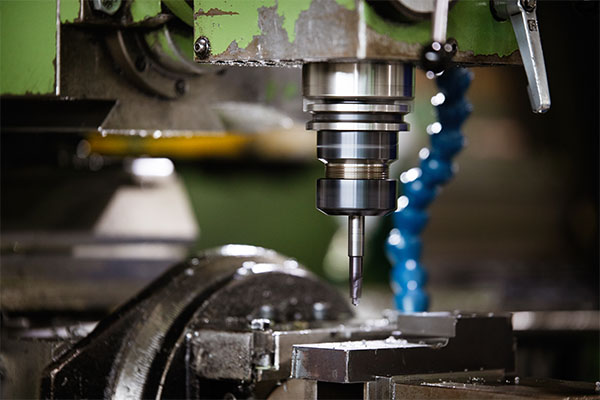
1. What is a Metal CNC Machine?
A Metal CNC machine is a precision tool used in the manufacturing industry to cut, shape, or carve metal materials. CNC, which stands for Computer Numerical Control, refers to the process where the machine’s movements are directed by a computer program. The most common types of metal CNC machines include lathes, mills, and grinders, all designed for specific tasks. These machines are used in various industries, including aerospace, automotive, and construction, due to their ability to produce highly accurate parts with minimal human intervention.
But here’s the kicker: choosing the right machine requires understanding its features and capabilities. There’s more to it than just picking a machine based on the material you want to cut. For instance, while a CNC lathe is perfect for turning operations, a CNC mill might be more suitable for complex multi-axis operations that involve cutting, drilling, and shaping metal parts.
Now, let’s break it down. Metal CNC machines are primarily used for shaping and cutting metals like aluminum, steel, and titanium. They work through subtractive machining, where material is removed layer by layer until the desired shape is achieved. The machines can handle a range of tasks, including boring, turning, and milling. This makes them versatile in a wide array of manufacturing processes, whether you’re producing automotive parts or intricate machinery components.
Table 1: Types of Metal CNC Machines
Type de machine | Function | Common Uses |
---|---|---|
Tour CNC | Turning operations, shaping parts | Automotive, Aerospace |
CNC Mill | Drilling, cutting, and shaping | Aerospace, Industrial |
CNC Grinder | Grinding metal surfaces | Toolmaking, Precision Work |
2. How Do Metal CNC Machines Work?
A metal CNC machine works by taking instructions from a computer program and translating them into precise movements. The program controls the machine’s motors, which move the tool in different directions along multiple axes. These movements can be very complex, with machines capable of operating on up to five axes simultaneously. The software that runs the CNC machine is programmed with detailed instructions on how the material should be cut, drilled, or shaped.
What’s the real story? The accuracy and precision of CNC machines are what set them apart from traditional manual machines. Thanks to their computer-controlled nature, CNC machines can replicate the same operation thousands of times with pinpoint accuracy. This level of consistency is critical in industries where precision is paramount, such as the production of aircraft parts or automotive components.
Metal CNC machines are often equipped with a range of tools that can perform different types of cuts and operations. Some machines feature tool changers, which allow the machine to automatically swap between tools, making it more efficient for larger production runs. Furthermore, CNC machines are highly programmable, which means you can set them up for a variety of tasks, whether you’re machining small components or larger, complex parts.
Table 2: CNC Machine Movements and Functions
Axis Movement | Description | Common Uses |
---|---|---|
X-axis | Left-right movement of the tool | Horizontal cuts |
Y-axis | Forward-backward movement | Vertical cuts |
Z-axis | Up-down movement | Depth cuts |
Additional Axes | Rotational or tilting movements | Complex operations |
3. What Are the Different Types of Metal CNC Machines?
When it comes to CNC machines, there are several different types, each designed for specific tasks. CNC lathes, for example, are used for turning operations, where a rotating piece of metal is cut by a stationary tool. CNC mills, on the other hand, are designed for cutting, drilling, and shaping materials in multiple directions.
Ready for the good part? Let’s take a deeper dive into the different types of metal CNC machines, starting with CNC lathes. These machines are often used for creating cylindrical parts, such as shafts or wheels. They rotate the material, while a tool moves along its length to remove material. A CNC mill, in contrast, uses rotary cutters to remove material from a workpiece, and it can work in multiple axes simultaneously for more complex parts.
Other machines in the CNC family include CNC plasma cutters, which use high-powered plasma arcs to cut through metal, and CNC EDM (Electrical Discharge Machines), which use electrical discharges to remove material in very fine amounts. All these machines play an important role in the metalworking industry. Depending on the nature of your work, selecting the right type of CNC machine is crucial for efficiency, precision, and overall output.
Table 3: Comparison of CNC Machine Types
Type de machine | Capacités | Suitable Tasks |
---|---|---|
Tour CNC | Turning and shaping cylindrical parts | Shaft production, wheel shaping |
CNC Mill | Multi-axis cutting and drilling | Complex metal parts, gears |
CNC Plasma Cutter | High-power cutting of thick materials | Sheet metal cutting |
CNC EDM | Precision cutting with electrical discharges | Fine cutting, toolmaking |
4. Why Should You Invest in a Metal CNC Machine?
Investing in a metal CNC machine brings numerous benefits that can greatly enhance your business’s productivity and efficiency. One of the primary advantages is the increased precision it offers. CNC machines are capable of performing tasks with extremely tight tolerances, which is particularly valuable in industries that require high levels of accuracy.
But here’s the kicker: not only do metal CNC machines improve precision, but they also reduce human error, which can be costly and time-consuming. Once the machine is set up and programmed, it can work tirelessly, producing parts that meet the exact specifications without the need for constant oversight.
For example, consider a CNC machine used in the aerospace industry. The parts produced must meet strict safety and performance standards, which can only be achieved through the high accuracy that CNC machines provide. Furthermore, CNC machines are known for their ability to handle complex designs, enabling manufacturers to create intricate parts that would be impossible to achieve manually.
Table 4: Benefits of Investing in Metal CNC Machines
Avantage | Description |
---|---|
Précision | High accuracy and tight tolerances |
Efficacité | Faster production with fewer errors |
Complexité | Ability to handle intricate designs |
Consistency | Reliable performance, reducing human error |
5. How to Choose the Right Metal CNC Machine for Your Business?
Choisir le bon metal CNC machine for your business depends on several factors, such as your budget, the materials you plan to work with, and the type of projects you take on. But wait, there’s more: you also need to consider the machine’s capabilities, size, and the complexity of your tasks.
To begin, you should identify the type of metal you intend to machine. For example, if you’re working with softer materials like aluminum, a basic CNC machine may suffice. However, for harder metals like titanium, you may need a machine with more advanced features and capabilities. Size is another consideration; if you plan to produce large parts, you will need a machine that can accommodate these sizes.
Additionally, consider the number of axes the machine can handle. A three-axis machine might be sufficient for simpler tasks, but for more complex operations, a five-axis machine might be necessary. These machines allow for more flexibility in the types of operations they can perform, making them ideal for intricate projects.
Table 5: Choosing the Right CNC Machine
Facteur | Considération | Suitable Machine |
---|---|---|
Material Type | Type of metal being machined | CNC Lathe or CNC Mill |
Machine Size | Size of the parts being produced | Larger CNC Mills |
Complexity of Tasks | Number of axes needed for precision and detail | 5-axis CNC Machine |
Conclusion
Choosing the right metal CNC machine for your business is a decision that should not be taken lightly. It requires a careful assessment of your specific needs, including the materials you work with, the complexity of your tasks, and the budget available. By understanding the various types of CNC machines and their capabilities, you’ll be in a better position to make an informed choice that will optimize your manufacturing processes and improve your product quality.
As you move forward in selecting the best CNC machine, remember that precision, efficiency, and the ability to handle complex designs are key factors that should guide your decision. Investing in the right machine now will pay off in the long run, ensuring smoother operations and improved production quality for years to come.
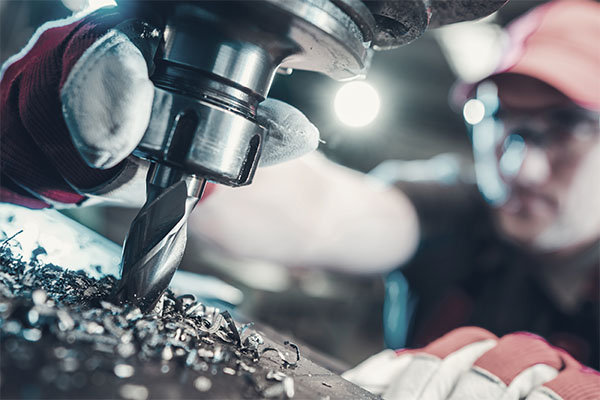
6. What Factors Should You Consider When Selecting a Metal CNC Machine?
Choosing the right metal CNC machine is not just about looking at the specs or the price tag—it’s about understanding the unique requirements of your business. Let’s break it down. One of the primary factors to consider is your budget. Metal CNC machines can vary in price significantly depending on their size, functionality, and the complexity of the tasks they perform. But here’s the kicker: it’s important to balance your needs with your budget. While you may be tempted to go for the most expensive option, you should assess whether the features justify the cost.
Another critical factor is the machine’s complexity. You need to understand the level of control and programming knowledge required. For example, a machine with advanced features, like multi-axis capabilities, may require more expertise in programming. If your team is not well-versed in these types of machines, it might be a better idea to start with a simpler CNC machine and gradually upgrade as needed.
The material you work with plays an equally important role. For instance, a machine that is excellent for cutting softer metals like aluminum may not be effective for harder materials such as titanium. Understanding the material requirements helps in narrowing down the choices.
Table 1: Key Factors When Selecting a CNC Machine
Facteur | Considération | Impact on Machine Selection |
---|---|---|
Budget | Price range of machines | Determines machine complexity and features |
Complexité | Ease of programming and usage | Affects training time and machine selection |
Material Type | Type of metals you intend to machine | Influences the machine’s capabilities |
After-Sales Support | Availability of service and maintenance | Ensures smooth operations post-purchase |
7. What Are the Common Materials Processed by Metal CNC Machines?
Metal CNC machines are versatile tools capable of processing a wide variety of materials. The most common materials include metals like aluminum, steel, and titanium. But here’s the kicker: the choice of material you need to work with will directly influence the type of machine you need. For instance, while aluminum is a relatively soft metal and can be machined with a basic CNC mill, materials like titanium require a more robust machine with higher tolerance levels.
Aluminum is one of the most commonly used materials because it’s lightweight, corrosion-resistant, and relatively easy to machine. For industries like aerospace and automotive manufacturing, aluminum’s strength-to-weight ratio makes it the go-to material for many applications. Steel, particularly stainless steel, is another widely used material. Known for its strength and durability, steel is commonly processed by CNC machines in industries that require parts with high mechanical properties.
Titanium is a high-strength material that requires specialized CNC machines due to its hardness and tendency to generate heat during cutting. Many high-performance parts, particularly in aerospace and military applications, are made from titanium, so CNC machines for titanium need to be specifically designed to handle these challenges. There are also other metals like brass, copper, and alloys used for more specialized machining.
Table 2: Common Materials Processed by CNC Machines
Material Type | Caractéristiques | Common Uses |
---|---|---|
Aluminium | Lightweight, corrosion-resistant | Aerospace, Automotive, Electronics |
Acier inoxydable | Strong, corrosion-resistant | Automotive, Medical Devices, Construction |
Titane | High strength, heat-resistant | Aerospace, Military, Medical Devices |
Cuivre | Excellent electrical conductivity | Electrical Components, Heat Exchangers |
Laiton | Malleable, corrosion-resistant | Electrical Components, Plumbing |
8. How to Maintain a Metal CNC Machine for Longevity?
CNC machines represent a significant investment, and proper maintenance is essential for maximizing their lifespan and ensuring they perform at their best. Regular maintenance involves checking the machine’s parts for wear and tear, ensuring proper lubrication, and cleaning out debris that can affect performance. The most important part? Regular inspection. If you don’t monitor your machine’s condition, even the smallest malfunction can snowball into bigger issues, leading to costly repairs or downtime.
Ready for the good part? Proper calibration is just as crucial for machine maintenance. Even the best-maintained machines can lose their precision over time. That’s why regular calibration checks are essential. By recalibrating the machine’s axes and settings, you can ensure that your metal parts are cut to the correct dimensions every time. If you’re working with high-precision parts, this is especially important to avoid costly errors.
Another critical aspect of maintenance is software updates. CNC machines are controlled by software that dictates their movements and operations. By keeping the software up to date, you ensure that the machine continues to operate optimally and benefits from improvements in efficiency and accuracy.
Table 3: Maintenance Checklist for CNC Machines
Maintenance Task | Frequency | But |
---|---|---|
Machine Cleaning | Weekly | Prevents dust and debris buildup |
Lubrication of Moving Parts | Monthly | Reduces wear and tear |
Calibration | Every 3-6 months | Ensures precision |
Software Updates | As available | Keeps the machine running smoothly |
9. What Are the Safety Considerations for Operating Metal CNC Machines?
Operating a metal CNC machine requires strict adherence to safety protocols. The first line of defense is protective gear. Operators should always wear safety glasses, gloves, and hearing protection to protect themselves from flying debris, loud noises, and other hazards. But here’s the kicker: safety goes beyond just wearing the right gear. It’s also about maintaining a safe working environment. Make sure that your CNC machine is properly grounded and that there’s no risk of electrical accidents.
One of the most critical safety concerns when using CNC machines is avoiding entanglement. Moving parts like the tool spindles and the workpiece itself can pose a serious risk if the operator is not careful. Always ensure that the area around the machine is clear of clutter and that safety shields are in place.
Training is another key component of CNC machine safety. Operators must understand how the machine works, what to do in the event of an emergency, and how to handle the machine’s controls. Proper training ensures that operators are aware of potential dangers and can avoid accidents.
Table 4: Safety Measures for CNC Machines
Safety Measure | But | Implementation |
---|---|---|
Safety Gear | Protects from debris, noise, and injury | Gloves, glasses, hearing protection |
Machine Grounding | Prevents electrical hazards | Regular checks of electrical systems |
Emergency Procedures | Prepares operators for accidents | Emergency stop buttons, training |
Safety Barriers/Guards | Prevents accidental contact with moving parts | Shields around rotating parts |
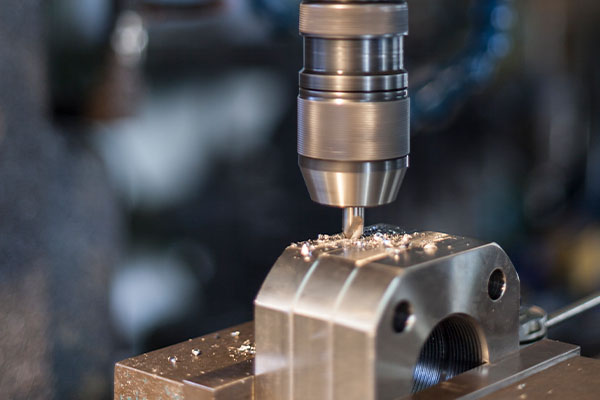
10. How to Set Up Your Metal CNC Machine for Optimal Performance?
Setting up your metal CNC machine for optimal performance involves more than just plugging it in and turning it on. First, you’ll need to load the appropriate software and ensure that it is compatible with the machine’s hardware. From there, you will input the program that tells the machine exactly how to cut, drill, or shape the metal.
What’s the real story? The setup process starts with selecting the correct tools and ensuring that they are properly secured. If the wrong tool is used or if the tool isn’t fastened correctly, the machine may produce inaccurate or defective parts. Once the tools are in place, the next step is to set up the workpiece on the machine bed, ensuring that it’s aligned perfectly. Even the smallest misalignment can lead to defects in the final product.
Once the machine is set up, it’s time to calibrate the axes and perform test cuts. By running a few tests, you can make sure that everything is aligned properly and that the machine is cutting accurately. Don’t skip this step—it’s essential to ensuring high-quality output.
Table 5: CNC Machine Setup Checklist
Setup Task | Action | But |
---|---|---|
Tool Selection | Choose the correct cutting tool | Ensures accuracy |
Workpiece Alignment | Align the workpiece on the bed | Prevents defects |
Calibration | Test the machine’s axes | Confirms machine accuracy |
Test Cuts | Run test cuts on scrap material | Ensures proper machine setup |
11. What Are Some Advanced Features to Look for in Metal CNC Machines?
In today’s competitive manufacturing landscape, it’s important to look for CNC machines with advanced features that can help streamline your production processes and increase efficiency. One such feature is automation. CNC machines with automation capabilities can reduce the need for manual intervention, freeing up operators to focus on other tasks while the machine works.
Ready for the good part? High-speed capabilities are another key feature of modern CNC machines. Machines that operate at faster speeds can increase production rates, which is crucial for meeting tight deadlines and reducing overall manufacturing costs. Additionally, many CNC machines now come with advanced tool changers that allow for automatic switching between tools, reducing downtime and increasing productivity.
Another important feature to consider is multi-axis capabilities. While a standard three-axis CNC machine can handle basic tasks, machines with more axes (like five-axis CNC machines) offer increased flexibility for more complex operations. These machines can perform operations on multiple surfaces of the workpiece simultaneously, making them ideal for intricate parts that require more precision.
Table 6: Advanced CNC Machine Features
Fonctionnalité | Description | Avantage |
---|---|---|
Automation | Reduced manual intervention | Increases productivity |
High-Speed Operation | Faster cutting speeds | Reduces production time |
Tool Changer | Automatic tool switching | Minimizes downtime |
Multi-Axis Capability | Multi-axis machining capabilities | Allows complex, detailed parts |
12. How Do You Optimize the CNC Machining Process for Metal Parts?
Optimizing the CNC machining process for metal parts is crucial for improving both the quality and cost-effectiveness of your operations. It starts with choosing the right cutting tools and materials. For example, using high-quality carbide tools can improve cutting performance and extend tool life.
But wait, there’s more: optimizing feed rates and cutting speeds is just as important. If the feed rate is too slow, the process becomes inefficient. If it’s too fast, you risk damaging the tool or workpiece. By adjusting the feed rate based on the material being processed, you can ensure that you achieve the perfect balance between speed and precision.
Reducing waste is another essential part of optimization. CNC machines are capable of cutting metal with minimal material loss, but without the right setup and programming, material waste can increase. Using techniques like toolpath optimization, where the machine follows the most efficient cutting routes, helps minimize waste and save on raw material costs.
Table 7: Optimizing CNC Machining Process
Optimization Task | Action | But |
---|---|---|
Tool Selection | Use high-quality cutting tools | Increases efficiency and tool life |
Feed Rate Adjustment | Optimize feed rate based on material | Prevents tool damage and ensures accuracy |
Cutting Speed Adjustment | Match cutting speed to material type | Enhances precision and reduces waste |
Toolpath Optimization | Plan cutting routes efficiently | Reduces material waste and increases productivity |
13. How to Troubleshoot Common Metal CNC Machine Issues?
Even with the best machines, problems can arise. The first step in troubleshooting is identifying the issue. Is the machine producing inaccurate parts? Are there strange noises or vibrations during operation?
The common culprits often involve tool wear or improper calibration. If the machine isn’t cutting precisely, it may be time to inspect the tool and ensure it’s sharp enough for the material you’re working with. Another potential issue could be misalignment. Ensuring that the machine’s axes are properly calibrated will prevent deviations in the parts.
A third common problem is software errors. These can lead to unexpected machine behavior or incorrect cutting instructions. Regular software updates are essential for ensuring that the machine continues to function optimally. When troubleshooting, always check for these simple issues first before diving into more complex diagnostics.
Table 8: Common CNC Machine Issues and Fixes
Issue | Possible Cause | Solution |
---|---|---|
Inaccurate Cuts | Tool wear or misalignment | Check tool sharpness, recalibrate machine |
Strange Noises/Vibrations | Loose parts or improper setup | Tighten all components, ensure proper setup |
Software Malfunctions | Outdated or incorrect programming | Update software, reprogram machine |
Machine Stops Unexpectedly | Electrical faults or emergency stops | Check electrical connections, reset emergency stop |
14. What Are the Top Brands of Metal CNC Machines?
There are several reputable brands in the CNC machining industry known for producing high-quality, reliable machines. These brands include Haas, Mazak, and DMG Mori. Each of these manufacturers offers a range of machines that cater to different needs, whether you’re working with smaller, simpler parts or larger, complex components.
But here’s the kicker: choosing the right brand is not just about the machine’s features, but also about after-sales service and support. Top manufacturers offer excellent customer service, which is critical when you face issues with your machine down the road. Additionally, a strong warranty and accessible parts replacement system are important considerations.
Haas is known for producing CNC machines that are user-friendly and come at a more affordable price point, making them a popular choice for small to mid-sized businesses. Mazak, on the other hand, is favored for its advanced multi-axis capabilities and high-speed machining options, while DMG Mori is known for offering state-of-the-art technology in high-precision machining.
Table 9: Comparison of Top CNC Machine Brands
Brand | Features | Idéal pour |
---|---|---|
Haas | User-friendly, affordable | Small to medium-sized businesses |
Mazak | Advanced multi-axis capabilities | High-speed, complex machining |
DMG Mori | High-precision, state-of-the-art technology | Aerospace, automotive industries |
15. How Do Metal CNC Machines Benefit Your Business in the Long Run?
Investing in a metal CNC machine offers long-term benefits that go beyond just improved productivity. One of the major advantages is scalability. As your business grows, your machining needs will likely become more complex. Metal CNC machines can be easily scaled up to handle larger production volumes and more intricate parts.
What’s the real story? CNC machines also contribute to consistent product quality. With automated processes, the risk of human error is greatly reduced, leading to higher precision and consistency in every part produced. This is especially important in industries like aerospace or medical devices, where part accuracy is critical.
Additionally, CNC machines reduce waste, which has both economic and environmental benefits. By using advanced programming techniques and optimizing cutting paths, CNC machines minimize material waste, leading to lower raw material costs and fewer emissions. This makes your operations not only more cost-efficient but also more environmentally friendly.
Table 10: Long-Term Benefits of CNC Machines
Avantage | Description | Long-Term Impact |
---|---|---|
Scalability | Easily adapts to higher production needs | Supports business growth |
Consistency | Reduces errors and improves product quality | Enhances customer satisfaction |
Waste Reduction | Optimizes material use | Lowers production costs |
Environmental Impact | Less waste and energy usage | More sustainable operations |
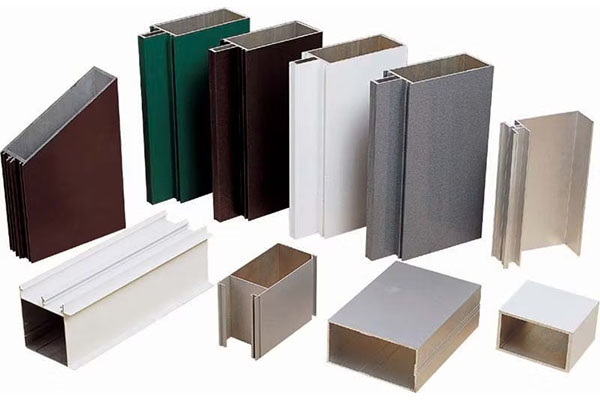
FAQ
Q1: What is a metal CNC machine?
A metal CNC machine is a computer-controlled tool used to cut, shape, or form metal parts with high precision.
T2 : How does a metal CNC machine work?
It works by receiving instructions from a computer program, which directs the machine’s movements to cut, drill, or shape metal.
T3 : What materials can be processed by a metal CNC machine?
CNC machines can handle materials like aluminum, stainless steel, titanium, and custom alloys.
T4 : How do I choose the right metal CNC machine for my needs?
Consider your budget, the materials you plan to machine, and the complexity of your tasks when choosing a CNC machine.
Q5 : What are the benefits of using a metal CNC machine?
The benefits include increased precision, reduced human error, improved efficiency, and the ability to handle complex designs.