Introduction
The CNC machining industry has undergone significant transformation in recent years, and its growth continues to be driven by technological advancements, increased demand for precision, and automation. CNC machining, which stands for Computer Numerical Control machining, is at the heart of many industries, ranging from automotive and aerospace to healthcare and consumer electronics. The advent of Industry 4.0, automation, and smart manufacturing is reshaping the landscape of this sector, creating both challenges and opportunities for businesses. As companies strive to stay competitive, understanding these changes is crucial for navigating the evolving market. This article explores the key trends shaping the CNC machining industry, the opportunities it presents, and how businesses can leverage these to stay ahead in the market.
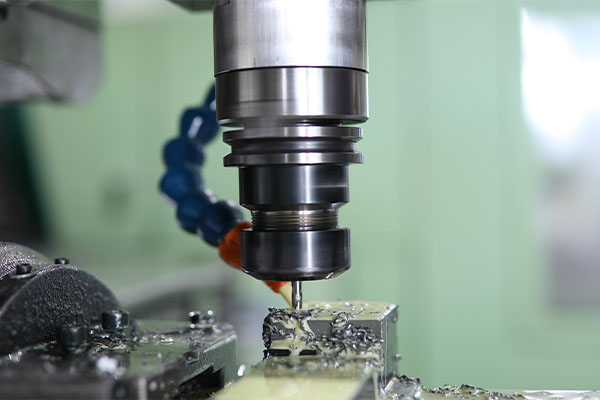
1. What is CNC Machining?
Comprendre les bases de l'usinage CNC
CNC machining is a manufacturing process that uses computers to control machine tools like lathes, mills, routers, and grinders. Unlike manual machining, where human operators directly control the machines, CNC machines operate with precision according to computer-generated programs. These programs are written using computer-aided design (CAD) software, which defines the exact movements and operations of the machine to produce complex parts. CNC machining is known for its ability to deliver high precision, repeatability, and consistency, making it essential in industries that demand intricate and accurate parts.
The Role of CNC Machining in Modern Manufacturing
CNC machining plays a critical role in today’s manufacturing processes. It is used to create parts for everything from consumer products like smartphones to industrial machinery, aerospace components, and medical devices. The flexibility of CNC machines allows manufacturers to create small batches, prototypes, and custom designs with ease. Moreover, the scalability of these systems means they can be adapted for mass production. Over time, the reliance on CNC machining has increased, as it helps reduce human error, speed up production, and improve overall product quality.
Why CNC Machining Matters
The importance of CNC machining cannot be overstated. As industries become more globalized and competition intensifies, manufacturers need to be able to produce high-quality products efficiently. CNC machining offers a solution to this challenge. It ensures consistent quality, minimizes waste, and cuts down on labor costs. By using automated systems, manufacturers can meet the ever-growing demand for faster production times while maintaining the standards of precision and accuracy.
2. The Growth of the CNC Machining Industry
How CNC Machining Has Evolved Over the Years
The history of CNC machining dates back to the 1940s, when the first numerical control (NC) machine was developed. Initially, these machines used punched paper tape to control their movements. Over time, advancements in technology led to the development of computer-controlled systems that allowed for more sophisticated designs and operations. The advent of personal computers in the 1980s revolutionized the CNC machining industry, making it more accessible and cost-effective for small and medium-sized businesses. With further innovations in software, automation, and materials, CNC machining has become an integral part of manufacturing processes across various sectors.
Current Market Size and Growth Projections
Today, the CNC machining industry is experiencing robust growth, driven by factors such as increasing demand for customized products, the rise of automation, and the integration of smart manufacturing technologies. According to market research, the global CNC machining market is expected to continue growing at a steady rate. Key regions contributing to this growth include North America, Europe, and Asia-Pacific, where technological advancements and manufacturing hubs are concentrated. As industries like aerospace, automotive, and healthcare continue to expand, the demand for CNC machining services will likely increase, presenting significant opportunities for businesses in the sector.
Factors Driving the Growth of CNC Machining
The primary drivers of growth in CNC machining include the increasing need for high-precision parts, the rise of automation, and the growing emphasis on customization. As industries demand faster production cycles with fewer defects, CNC machining offers a reliable solution. Additionally, advancements in automation technologies, such as robotics and artificial intelligence (AI), are enhancing the capabilities of CNC machines, allowing for even greater efficiency and accuracy. The ability to customize parts to meet specific customer needs further fuels the demand for CNC services, particularly in industries like medical devices, automotive, and aerospace.
3. Key Trends Shaping the CNC Machining Industry
Automation and AI in CNC Machining
The integration of automation and artificial intelligence (AI) in CNC machining has been a game-changer for the industry. CNC machines are increasingly being equipped with AI-driven software that can optimize machining processes in real time. These systems can monitor machine performance, predict failures, and adjust settings automatically to ensure optimal efficiency. Additionally, robotic arms are being integrated into CNC machining operations, allowing for faster production and reduced labor costs. Here’s the deal: automation is not just a trend—it is the future of CNC machining, and companies that embrace it will be able to stay competitive in a fast-evolving market.
The Rise of Industry 4.0
Industry 4.0 is the next phase of industrial revolution, characterized by the integration of cyber-physical systems, IoT (Internet of Things), and data analytics into manufacturing processes. CNC machining plays a critical role in Industry 4.0 by enabling machines to communicate with each other and with centralized control systems. This interconnected environment allows for real-time monitoring of production, predictive maintenance, and the optimization of manufacturing workflows. Vous vous demandez peut-être how this affects your business—well, Industry 4.0 ensures that manufacturers can produce parts more efficiently, reduce downtime, and gain insights into production processes that were once inaccessible.
Sustainability and Green Manufacturing
Sustainability has become a major focus in the CNC machining industry, as companies seek to minimize their environmental impact. CNC machines are now being designed with energy-efficient features that reduce power consumption, and manufacturers are adopting green practices such as recycling waste materials and using eco-friendly cutting fluids. The demand for sustainable manufacturing processes is being driven by both consumer preferences and regulatory requirements. You’re probably thinking: is CNC machining sustainable? Yes! By adopting sustainable practices, manufacturers can not only reduce their carbon footprint but also improve their bottom line by minimizing waste and lowering operational costs.
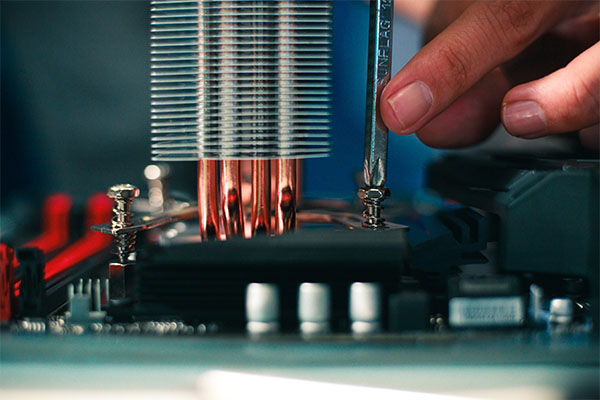
4. Technological Advancements in CNC Machining
3D Printing Integration with CNC Machines
As additive manufacturing (3D printing) technology has evolved, it is now being integrated with traditional CNC machining to create hybrid systems. These hybrid systems combine the strengths of both processes—subtractive manufacturing (CNC) and additive manufacturing (3D printing)—to produce complex parts with enhanced precision and material properties. The benefits include faster production times, reduced material waste, and the ability to produce parts with intricate geometries that would be difficult or impossible to achieve with traditional CNC machining alone.
Advanced CNC Software and Control Systems
CNC machining has become even more efficient with the development of advanced software and control systems. CAD (Computer-Aided Design) and CAM (Computer-Aided Manufacturing) software enable manufacturers to design and simulate machining processes before physical production begins. These systems allow for improved accuracy, reduced setup times, and faster turnaround times for custom parts. Autrement dit, the combination of sophisticated software with state-of-the-art CNC machinery ensures that manufacturers can produce high-quality parts faster and at lower costs.
5. Key Materials Used in CNC Machining
Common Materials for CNC Machining
CNC machining is used to process a wide variety of materials, each with unique properties that make them suitable for different applications. Common materials include metals such as aluminum, steel, and titanium, which are frequently used in industries like automotive, aerospace, and medical device manufacturing. The truth is: the choice of material can significantly affect the machining process, as each material requires specific cutting tools, techniques, and machine settings to achieve the desired result.
Emerging Materials for CNC Machining
In recent years, new materials such as composites and ceramics have gained popularity in CNC machining. These materials offer superior strength, heat resistance, and wear properties, making them ideal for high-performance applications. What’s more, these advanced materials are becoming more accessible to manufacturers, opening up new opportunities for innovation in industries like aerospace and electronics. However, working with these materials often requires specialized machinery and expertise, which can increase the complexity of the machining process.
6. CNC Machining vs. Traditional Manufacturing Methods
The Advantages of CNC Machining Over Conventional Techniques
When compared to traditional manufacturing methods like casting, forging, or injection molding, CNC machining offers several key advantages. CNC machines are highly accurate and capable of producing complex shapes that would be difficult or impossible to achieve using conventional methods. For example, CNC machining allows manufacturers to produce custom parts in small quantities, making it ideal for industries where prototyping and low-volume production are essential. Additionally, CNC machines offer greater flexibility in design, as they can quickly adapt to different tasks without the need for expensive tooling changes.
Limitations and Challenges of CNC Machining
While CNC machining has numerous advantages, it also has its limitations. It’s worth noting that CNC machines typically require significant upfront investment, particularly for high-end models with advanced features. Moreover, CNC machining may not be the most cost-effective option for mass production runs, where other methods like injection molding may be more efficient. Additionally, CNC machining requires skilled operators who understand how to set up and maintain the machines properly, which can be a challenge for companies facing a shortage of qualified personnel.
7. CNC Machining Applications Across Various Industries
Industrie automobile
CNC machining plays a vital role in the automotive industry, where precision is critical for manufacturing components like engine parts, transmissions, and chassis. The ability to produce high-tolerance parts ensures that vehicles meet safety and performance standards. What makes CNC machining so valuable in the automotive industry is its ability to handle both large-scale production runs and custom parts, making it indispensable for everything from prototype development to mass production.
Industrie aérospatiale
In the aerospace industry, where safety and precision are paramount, CNC machining is used to create complex components such as turbine blades, aircraft wings, and landing gear. The benefits include the ability to produce lightweight, high-strength parts that can withstand extreme conditions. Aerospace manufacturers rely on CNC machining for its ability to produce parts with tight tolerances and high reliability, ensuring that each component meets stringent safety regulations.
Medical Devices and Healthcare
CNC machining is also widely used in the healthcare industry for producing medical devices like surgical instruments, implants, and diagnostic equipment. Voici l'affaire: precision and accuracy are crucial in healthcare applications, and CNC machining delivers the high-quality results needed for these critical components. Moreover, CNC machining’s ability to produce custom parts tailored to individual patient needs has opened up new possibilities in personalized medicine.
Electronics and Consumer Products
From smartphone components to computer parts, CNC machining is used extensively in the electronics industry. The ability to manufacture intricate, high-precision parts for electronics is essential for ensuring product performance and reliability. Vous vous demandez peut-être how this affects consumers—well, CNC machining helps produce the sleek, functional designs we rely on in our everyday devices.
8. Opportunities for Growth in CNC Machining
Emerging Markets and International Expansion
As the demand for CNC machining services continues to grow, emerging markets in Asia, South America, and Africa present significant opportunities for expansion. These regions are experiencing rapid industrialization, and businesses in developed countries are increasingly looking to outsource manufacturing to these regions to reduce costs. The truth is, these markets offer untapped potential for CNC machining businesses, particularly those that can provide high-quality products at competitive prices.
The Demand for Customization and Small-Batch Production
One of the driving forces behind the growth of CNC machining is the increasing demand for customized products and small-batch production. Industries such as medical devices, automotive, and aerospace often require bespoke parts that cannot be mass-produced using traditional methods. Autrement dit, CNC machining offers the flexibility to meet these demands, making it an essential tool for businesses that cater to niche markets and require high levels of customization.
9. Challenges Facing the CNC Machining Industry
Skill Shortage and Training Needs
As the CNC machining industry continues to evolve, there is a growing need for skilled labor to operate and maintain advanced CNC machines. The shortage of trained professionals in the field has become a significant challenge, especially as older workers retire and fewer young people enter the trade. What can businesses do? Investing in training programs and partnerships with technical schools can help bridge the skills gap and ensure a steady supply of qualified workers for the future.
Supply Chain Disruptions and Material Shortages
Global supply chain disruptions, coupled with material shortages, have become a major challenge for CNC machining companies. The pandemic has highlighted the vulnerability of supply chains, and many manufacturers are facing delays in obtaining the raw materials they need to produce parts. Voici l'affaire: businesses that rely on timely deliveries must adopt more resilient supply chain strategies to mitigate the impact of these disruptions.
10. The Role of CNC Machining in Smart Manufacturing
The Integration of IoT in CNC Machining
As part of the broader trend toward smart manufacturing, CNC machining is increasingly being integrated with the Internet of Things (IoT). This allows CNC machines to communicate with each other, with central control systems, and with other equipment on the factory floor. The benefits include real-time monitoring, predictive maintenance, and more efficient production scheduling. IoT integration also allows manufacturers to collect data on machine performance, which can be used to optimize production and reduce costs.
Predictive Maintenance and Real-Time Analytics
CNC machining is becoming more intelligent with the use of real-time analytics and predictive maintenance tools. By monitoring machine performance continuously, manufacturers can predict when maintenance is needed before a breakdown occurs. Vous vous demandez peut-être how this affects productivity—well, predictive maintenance helps reduce downtime, ensuring that CNC machines are always performing at their best.
11. Cost Factors and Investment in CNC Machining
The Cost of CNC Machinery and Tools
Investing in CNC machines can be costly, especially for high-end systems that offer advanced features like multi-axis machining and automation capabilities. Voici l'affaire: businesses must weigh the costs of acquiring CNC machinery against the long-term savings generated by faster production times and reduced labor costs. Additionally, there are ongoing costs for tools, maintenance, and software updates, which can add up over time.
How to Reduce Operational Costs in CNC Machining
There are several strategies businesses can implement to reduce operational costs in CNC machining. For example, investing in energy-efficient machines and tools can help lower electricity bills. Autrement dit, businesses can also reduce material waste by optimizing cutting paths and using advanced software that simulates machining processes before physical production begins. Training employees to operate machines efficiently can also lead to significant cost savings.
12. Future Trends to Watch in CNC Machining
The Future of CNC Automation and Robotics
The future of CNC machining is increasingly linked to automation and robotics. The benefits include faster production cycles, reduced labor costs, and greater precision. As robots become more integrated into the CNC machining process, they will be able to perform tasks like material handling, assembly, and quality control. The increased use of robots in CNC machining will also help address the labor shortage that is affecting the industry.
Quantum Computing and Its Impact on CNC Machining
While it may sound like science fiction, quantum computing is poised to revolutionize CNC machining in the future. You’re probably thinking: how could this technology help? Well, quantum computers can process complex calculations at incredibly high speeds, enabling manufacturers to design parts with greater precision and efficiency. Although the technology is still in its infancy, its potential impact on the CNC machining industry is immense.
13. How Businesses Can Leverage CNC Machining for Competitive Advantage
Increased Efficiency and Shortened Lead Times
By incorporating CNC machining into their production processes, businesses can significantly improve efficiency and reduce lead times. Voici l'affaire: faster production means that companies can respond more quickly to customer demands, improving customer satisfaction and increasing their competitive edge. Additionally, CNC machining enables manufacturers to produce parts to tight tolerances, ensuring high product quality and consistency.
Customization and Innovation as Competitive Tools
Customization has become a key differentiator in many industries, and CNC machining offers the flexibility to meet these demands. Autrement dit, businesses that can provide customized products tailored to specific customer needs are more likely to stand out in a crowded market. Furthermore, CNC machining enables rapid prototyping, allowing companies to test new designs and innovations before committing to full-scale production.
14. The Importance of Quality Control in CNC Machining
How CNC Machines Ensure Precision and Accuracy
CNC machines are built to operate with high precision, ensuring that each part meets strict quality standards. The truth is: this level of accuracy is achieved through the use of advanced control systems, sensors, and feedback loops that continuously monitor and adjust the machining process. By maintaining precise control over cutting speeds, tool paths, and machine movements, CNC machines can produce parts with a high degree of consistency.
Best Practices for Quality Assurance
To ensure the highest quality, manufacturers must implement robust quality control measures at every stage of production. Vous vous demandez peut-être: what are the best practices for achieving this? First, it’s essential to use calibrated measuring tools to verify dimensions during and after machining. Furthermore, using Statistical Process Control (SPC) allows manufacturers to track variations in the production process and identify potential issues before they lead to defects.
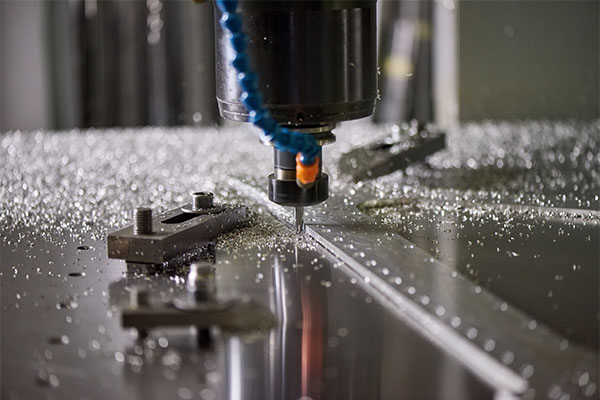
15. Conclusion
Summary of CNC Machining Trends and Opportunities
In conclusion, the CNC machining industry is poised for continued growth, driven by technological advancements, increasing demand for precision, and the rise of automation. Vous vous demandez peut-être how you can capitalize on these trends—well, embracing smart manufacturing practices, investing in automation, and expanding into emerging markets will position your business for success. As CNC machining continues to evolve, companies that stay ahead of the curve will be able to maintain a competitive advantage.
How Companies Can Position Themselves for Success
To succeed in this rapidly changing industry, businesses need to adopt a proactive approach. Voici l'affaire: invest in cutting-edge technology, train your workforce, and focus on quality and customer satisfaction. By staying adaptable and leveraging the power of CNC machining, businesses can thrive in this competitive market.
Call to Action
If you’re looking to take your manufacturing processes to the next level, now is the time to embrace CNC machining. What are you waiting for? Start exploring the opportunities that CNC machining offers today and position your business for long-term success in the evolving marketplace.
16. FAQ Section
What is CNC machining and how does it work?
CNC machining is a manufacturing process that uses computer-controlled machines to create parts from raw materials. The machine follows a pre-programmed sequence of operations to cut, shape, and finish parts with high precision.
How has CNC machining improved over traditional methods?
CNC machining offers increased accuracy, faster production times, and the ability to produce complex parts that would be difficult or impossible to create with traditional methods.
What industries benefit the most from CNC machining?
CNC machining is used across a wide range of industries, including aerospace, automotive, medical devices, and electronics, where precision and reliability are crucial.
Are there any environmental benefits of CNC machining?
Yes, CNC machining is a more sustainable manufacturing method as it minimizes material waste, improves energy efficiency, and can use recyclable materials.
What are the future opportunities for CNC machining?
The future of CNC machining includes advancements in automation, the integration of 3D printing and additive manufacturing, and expanding into emerging markets with growing demand for precision parts.
How can small businesses leverage CNC machining for growth?
Small businesses can use CNC machining to offer customized products, prototype new designs, and create high-quality parts on a small scale, allowing them to compete with larger manufacturers.
What is the cost of investing in CNC machining technology?
The initial investment in CNC machines can be high, but the long-term benefits, such as improved efficiency and reduced labor costs, often justify the investment. Additionally, smaller machines with fewer capabilities can be a more affordable option for startups.