מָבוֹא
Custom titanium parts are essential for industries that require durable, lightweight, and corrosion-resistant components. With the increasing demand for high-performance materials, titanium has become a go-to option for various industries, including aerospace, medical, and automotive. In this article, we will explore what custom titanium parts are, why they are used, and how CNC machining plays a vital role in producing these high-quality parts. Ready to dive in? Let’s explore the specifics.
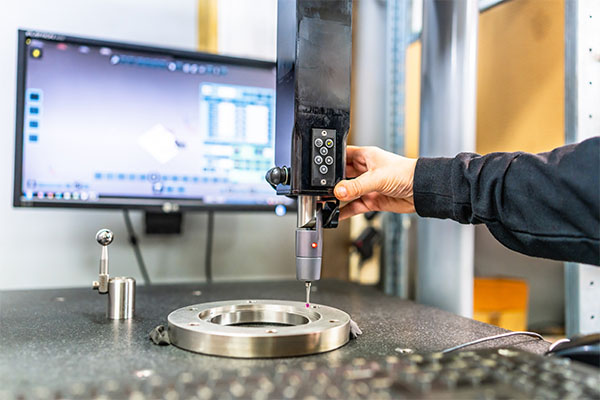
1. What Are Custom Titanium Parts?
Custom titanium parts are specially manufactured components tailored to meet the specific needs of various applications. Titanium is known for its incredible strength-to-weight ratio, corrosion resistance, and high melting point, making it ideal for parts that need to withstand extreme conditions. But here’s the kicker: titanium’s properties make it essential in industries that require precision, reliability, and performance, such as aerospace and medical equipment.
For instance, in aerospace, custom titanium parts are used for aircraft components like landing gear and wing structures. In the medical field, titanium is a preferred material for implants and surgical tools due to its biocompatibility. Custom parts are designed and manufactured based on specific requirements, which could range from a unique shape, size, or functionality to meeting industry-specific standards.
To create these parts, CNC machining is often used. This process allows manufacturers to produce parts with exceptional accuracy and tight tolerances. So, how does CNC machining help achieve this level of precision? Keep reading.
תכונה | Titanium Properties | Common Applications |
---|---|---|
Strength-to-weight ratio | Excellent | תעופה וחלל, רכב |
Corrosion resistance | Superior | Marine, medical |
Biocompatibility | גָבוֹהַ | Medical implants |
Heat resistance | גָבוֹהַ | Industrial components |
2. Why Choose CNC Machining for Titanium Parts?
CNC machining is a preferred method for producing custom titanium parts due to its precision, versatility, and ability to work with tough materials like titanium. What’s the real story behind CNC machining’s popularity? Simply put, it enables manufacturers to create parts that meet tight tolerances and complex geometries that other manufacturing methods cannot achieve.
CNC (Computer Numerical Control) machines use pre-programmed computer software to control machining tools. These tools cut, mill, drill, and shape the titanium into the required design. What makes CNC machining so effective for titanium is its ability to remove material slowly and precisely, which reduces heat buildup and prevents warping. This is important because titanium is a tough material that can be prone to tool wear if not handled correctly.
By using CNC machining, manufacturers can ensure that each custom titanium part is produced to exact specifications, with high repeatability and accuracy. The result is a component that performs at its best in critical applications. So, how does this process compare to traditional machining methods? Keep reading for the full comparison.
CNC Machining Process | Key Benefits |
---|---|
High precision | Tight tolerances for custom parts |
Automated control | Reduced human error |
Versatility | Suitable for complex designs |
3. What Are the Different Types of Custom Titanium Parts?
When it comes to custom titanium parts, there is no one-size-fits-all solution. Instead, there are various types of parts that can be tailored to meet specific requirements. Ready for the good part? Let’s break down the main categories of custom titanium parts produced through CNC machining.
One of the most common types of custom titanium parts are aerospace components, such as turbine blades and engine casings. These parts must withstand extreme temperatures and stresses, making titanium an excellent choice. Another popular category is medical implants, including hip and knee replacements, dental implants, and surgical tools. Titanium’s biocompatibility ensures these parts will not be rejected by the body, making them the material of choice for medical professionals.
Other types of custom titanium parts include fasteners, fittings, and connectors used in industries like automotive, military, and oil and gas. These parts are crucial for ensuring the integrity and reliability of larger systems. The versatility of titanium makes it suitable for a wide range of applications. But there’s more. Let’s explore how the properties of titanium influence the design and production of these parts.
Custom Titanium Part Type | Application |
---|---|
Aerospace components | Aircraft, spacecraft |
Medical implants | Surgical tools, joint replacements |
Fasteners and fittings | Automotive, military |
Connectors | Oil and gas, industrial |
4. How Is Titanium Machined for Custom Parts?
Machining titanium requires specialized tools and techniques due to its hardness and tendency to heat up during the cutting process. So, what’s the secret to machining titanium effectively? The key is controlling the heat and using the right tools to ensure a smooth and precise cut.
CNC machines are equipped with carbide or high-speed steel cutting tools that are designed to handle titanium’s toughness. The machining process begins with creating a detailed design or CAD (computer-aided design) model, which is then translated into machine instructions. This allows the CNC machine to follow precise paths, ensuring that the titanium part is cut to exact specifications.
The machining process includes several stages, such as rough cutting, fine milling, and finishing. Each stage is carefully controlled to maintain the integrity of the material and prevent issues like warping or cracking. The process may also include additional steps like heat treatment or surface finishing to improve the titanium part’s properties. But here’s the twist: knowing when to stop the cutting process is just as important as the cutting itself.
שָׁלָב | תֵאוּר |
---|---|
Rough cutting | Initial shaping of titanium part |
Fine milling | Precision cutting for tighter tolerances |
Finishing | Surface treatment and final adjustments |
5. What Industries Benefit from Custom Titanium Parts?
Custom titanium parts are crucial across various industries, offering solutions that other materials simply can’t match. What industries stand to benefit the most from using titanium? Let’s break it down.
In aerospace, custom titanium parts are used in everything from engines to structural components, where strength, weight, and durability are key. Titanium’s high strength-to-weight ratio makes it perfect for aviation applications, as it helps reduce the weight of aircraft without compromising performance. Similarly, the automotive industry relies on custom titanium parts for lightweight components that improve fuel efficiency and speed.
Medical devices are another major area where custom titanium parts are essential. Whether it’s in the form of implants, prosthetics, or surgical tools, titanium is preferred for its biocompatibility and ability to withstand bodily fluids without corroding. In military applications, titanium’s strength and resistance to harsh environments make it ideal for parts that need to withstand extreme conditions. And don’t forget about industrial applications, where custom titanium components are used in high-performance machinery and heavy-duty operations.
Industry | Application |
---|---|
תעופה וחלל | Aircraft components |
רכב | Lightweight parts |
רְפוּאִי | Implants, surgical tools |
Military | Defense components |
Industrial | Machinery, equipment |
6. What Are the Key Properties of Titanium for Custom Parts?
Titanium is a unique material known for its strength, light weight, and resistance to corrosion. So, what makes titanium the go-to choice for custom parts? Let’s dive into its key properties.
Titanium has an exceptional strength-to-weight ratio, meaning it is incredibly strong while still being light enough to be used in applications where weight is a critical factor, like aerospace and automotive. Its corrosion resistance is another key benefit, especially in marine or chemical environments. Titanium doesn’t rust or degrade when exposed to seawater or harsh chemicals, making it ideal for parts that need to withstand tough environments.
Another important property of titanium is its high melting point, which allows it to perform well under extreme temperatures. This makes titanium essential in industries like aerospace and defense, where high heat resistance is needed for components such as engines and turbines. And here’s the twist: titanium’s biocompatibility ensures it is safe for medical applications, like implants, without triggering an immune response.
Property | תוֹעֶלֶת |
---|---|
Strength-to-weight ratio | Lightweight yet strong |
Corrosion resistance | Ideal for harsh environments |
High melting point | Suitable for extreme temperatures |
Biocompatibility | Safe for medical applications |
7. How Do You Select the Right Grade of Titanium for Custom Parts?
Choosing the right grade of titanium is essential for ensuring the part’s performance and longevity. But here’s the deal: selecting the right titanium alloy depends on the specific requirements of the application.
There are several titanium alloys, with each offering distinct properties. Grade 1 titanium is known for its excellent corrosion resistance, while Grade 5 titanium offers a good balance of strength and weight. Grade 9 titanium is lighter and more flexible, making it ideal for industries like automotive and cycling. Each grade comes with its own set of advantages and trade-offs.
When selecting the right grade, factors like strength, corrosion resistance, and weight are all considered. For example, aerospace components typically require Grade 5 titanium due to its higher strength-to-weight ratio, while medical implants may require Grade 2 titanium for its higher biocompatibility. At the end of the day, choosing the right grade ensures that the part will perform optimally in its intended environment.
Titanium Grade | Properties | Common Applications |
---|---|---|
Grade 1 | Excellent corrosion resistance | Medical, chemical |
Grade 5 | High strength, lightweight | תעופה וחלל, רכב |
Grade 9 | Lightweight, flexible | Sports equipment |
מַסְקָנָה
Custom titanium parts offer numerous benefits, including exceptional strength, lightweight properties, and superior resistance to corrosion. With the increasing demand for high-performance components in industries such as aerospace, medical, and automotive, titanium has become the go-to material for custom parts. CNC machining plays a crucial role in producing these parts with precision and accuracy, making it an ideal choice for high-quality manufacturing. Whether you are in need of aerospace components, medical implants, or industrial fittings, custom titanium parts offer a reliable solution to meet the most demanding needs.
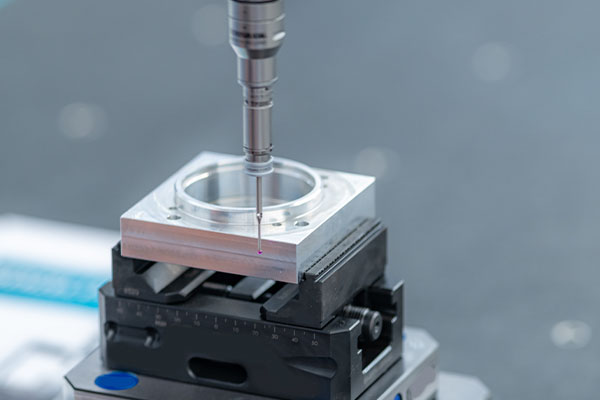
8. What Are the Challenges of CNC Machining Titanium Parts?
CNC machining titanium parts may seem straightforward, but there are a few challenges that manufacturers must navigate to ensure the process runs smoothly. What’s the real story here? Machining titanium is not like working with softer materials; it requires specialized skills, equipment, and knowledge to avoid costly mistakes.
The hardness of titanium presents a significant challenge during machining. Unlike aluminum or steel, titanium can cause excessive tool wear and is more prone to heat buildup. This means that the cutting tools used must be made of durable materials like carbide to withstand the stresses of machining. What’s the kicker? The material’s high strength also means that precision is key — any slight error can result in a part that doesn’t meet specifications, potentially rendering it unusable.
Another issue is the heat generated during the machining process. Titanium has a low thermal conductivity, which means it doesn’t dissipate heat as quickly as other metals. This can lead to thermal distortion, warping, or even tool failure if not properly managed. To combat this, manufacturers use techniques like coolant application and low cutting speeds to maintain temperature control. But here’s the twist: knowing when to stop the cutting process and preventing tool overuse is crucial for maintaining efficiency and quality.
At the end of the day, CNC machining titanium requires a careful balance of speed, precision, and heat management to produce high-quality custom parts.
אֶתגָר | פְּגִיעָה | פִּתָרוֹן |
---|---|---|
בלאי כלי עבודה | Increased costs and machine downtime | Use carbide tools, regular tool maintenance |
Heat buildup | Warping, thermal distortion | Low cutting speeds, coolant application |
דִיוּק | Inaccurate parts, scrapped products | Use CNC machines with tight tolerance control |
9. What Are the Benefits of Customizing Titanium Parts?
Customizing titanium parts brings several advantages, especially in industries where off-the-shelf components might not meet specific requirements. So, what’s the real value in customization? Custom parts are designed specifically to fit the needs of the project, resulting in more efficient and effective solutions.
One of the most obvious benefits of custom titanium parts is their ability to meet precise specifications. Whether it’s a complex aerospace component or a uniquely shaped medical implant, custom parts allow for the creation of solutions that are tailored to a specific function. This level of customization can improve the performance and longevity of the part, ensuring that it performs optimally under the given conditions.
Another benefit is cost savings. By opting for custom titanium parts, companies can eliminate the need for adapting existing parts, which may require costly modifications or even lead to performance issues. Custom parts are designed to reduce waste, enhance the functionality of the final product, and offer a more efficient manufacturing process. Ready for the good part? Custom titanium parts also help companies maintain a competitive edge by offering unique products that are not available elsewhere in the market.
תוֹעֶלֶת | פְּגִיעָה | Example |
---|---|---|
Tailored specifications | Improved performance | Aerospace components |
חיסכון בעלויות | Reduced waste and production costs | Automotive parts |
יתרון תחרותי | Unique, differentiated products | Medical devices |
10. How Are Custom Titanium Parts Used in Aerospace?
Custom titanium parts play a crucial role in the aerospace industry, where performance, strength, and weight are critical considerations. But here’s the kicker: titanium’s unique properties make it one of the best materials for aerospace components. From aircraft engines to structural components, titanium’s strength-to-weight ratio is unmatched.
In aerospace, titanium is used in components like turbine blades, landing gear, and airframes. These parts must endure extreme conditions, including high temperatures and pressure. Titanium’s resistance to heat and corrosion makes it the material of choice for parts exposed to harsh environments. Additionally, its lightweight nature ensures that aircraft can maintain fuel efficiency and speed without sacrificing safety.
What’s the real story in aerospace manufacturing? Custom titanium parts are vital for creating bespoke components that fit specific needs and requirements. By customizing titanium parts, manufacturers ensure that each component is tailored for optimal performance, which is crucial when safety is on the line. In short, custom titanium parts are indispensable in aerospace, and their continued use will likely drive innovation in the sector.
Aerospace Component | Function | Titanium Benefit |
---|---|---|
Turbine blades | Heat resistance | Withstand high temperatures |
Landing gear | Strength and durability | Resistant to wear and corrosion |
Airframes | Lightweight structure | Reduces overall aircraft weight |
11. What Are the Environmental Considerations When Manufacturing Custom Titanium Parts?
The environmental impact of manufacturing custom titanium parts is a growing concern, especially in an era focused on sustainability. What’s the kicker in titanium manufacturing? The process itself can be energy-intensive, but there are ways to mitigate these impacts and make the production process more sustainable.
One of the most significant environmental concerns with titanium production is the energy consumption required to extract and process titanium ore. This process, known as the Kroll process, is energy-intensive and releases greenhouse gases. However, efforts are being made to reduce the carbon footprint of titanium production, such as using renewable energy sources in manufacturing and improving efficiency in the Kroll process.
Another consideration is the recycling of titanium. Unlike other metals, titanium can be recycled without losing its properties, making it an environmentally friendly option for custom parts. Manufacturers can reuse titanium scrap to produce new parts, reducing waste and the need for new materials. Ready for the good part? Recycling titanium not only reduces environmental impact but also helps to lower material costs.
At the end of the day, while titanium production can have an environmental impact, it is a highly recyclable material, and efforts to reduce energy consumption and waste are making it more sustainable.
Environmental Concern | פְּגִיעָה | פִּתָרוֹן |
---|---|---|
Energy consumption | High carbon footprint | Use renewable energy in manufacturing |
Waste generation | Material waste | Recycle titanium scrap |
Carbon emissions | Contributes to climate change | Improve process efficiency |
12. How Do You Ensure Quality in Custom Titanium Parts?
Ensuring the quality of custom titanium parts is essential to meeting industry standards and ensuring the final product performs as expected. So, how can manufacturers ensure that their titanium parts are up to par? The answer lies in a combination of precision machining, rigorous quality control, and thorough testing.
One of the first steps in ensuring quality is using precise CNC machining processes. These machines are designed to work within very tight tolerances, ensuring that each part is produced to exact specifications. The machining process is carefully controlled to prevent defects, and manufacturers use advanced measurement tools like coordinate measuring machines (CMM) to verify accuracy.
Another critical aspect of quality assurance is testing. Custom titanium parts undergo various tests, including tensile strength, fatigue testing, and surface roughness assessments. These tests ensure that the parts can handle the stresses they will face in their respective applications, whether in aerospace, medical, or automotive fields. But here’s the twist: testing also provides valuable feedback, allowing manufacturers to fine-tune their processes and continually improve the quality of their parts.
Quality Assurance Step | תֵאוּר | Tools/Methods Used |
---|---|---|
עיבוד CNC | Precise cutting and shaping | CNC machines, CAD models |
Measurement | Verify part accuracy | Coordinate measuring machines |
Testing | Ensure part durability | Tensile strength, fatigue testing |
13. How Do Custom Titanium Parts Compare to Other Materials?
When considering custom parts for demanding applications, it’s essential to compare titanium to other materials to understand its advantages and limitations. What’s the real story here? Titanium has unique properties that make it superior to materials like steel and aluminum in certain applications, but it also comes with trade-offs.
Titanium is much lighter than steel, which makes it ideal for applications where weight is a significant factor. However, it is not as strong as steel, so it is generally used in applications where strength-to-weight ratio is more important than raw strength. On the other hand, titanium is far more corrosion-resistant than both steel and aluminum, making it ideal for harsh environments like marine or chemical industries.
One downside of titanium is its higher cost compared to other metals, which can make it a less economical choice for certain applications. However, when durability, strength, and resistance to corrosion are required, titanium proves to be worth the investment.
חוֹמֶר | Strength | Weight | Corrosion Resistance | Cost |
---|---|---|---|---|
טִיטָן | גָבוֹהַ | Lightweight | Superior | גָבוֹהַ |
פְּלָדָה | Very high | Heavy | Moderate | Moderate |
אֲלוּמִינְיוּם | נָמוּך | Very lightweight | נָמוּך | נָמוּך |
14. What is the Future of Custom Titanium Parts in Manufacturing?
The future of custom titanium parts is promising, with new innovations in materials, manufacturing techniques, and applications on the horizon. So, what’s the real story? Custom titanium parts will continue to play a vital role in industries requiring high-performance components, and advances in manufacturing technology are set to make them more accessible and affordable.
One area where custom titanium parts are likely to see significant growth is in additive manufacturing, also known as 3D printing. This technology allows for the production of complex parts with less material waste and at a faster pace. Ready for the good part? Titanium is already being used in 3D printing, and the combination of this technology with titanium’s unique properties could lead to breakthroughs in industries like aerospace, automotive, and medical devices.
Additionally, advancements in material science may lead to new titanium alloys with improved properties, such as greater strength, improved biocompatibility, or better corrosion resistance. These developments will open up even more possibilities for custom titanium parts in the future.
Innovation | תוֹעֶלֶת | Industry Application |
---|---|---|
3D printing | Faster production, reduced waste | Aerospace, medical |
New titanium alloys | Enhanced properties | Automotive, medical |
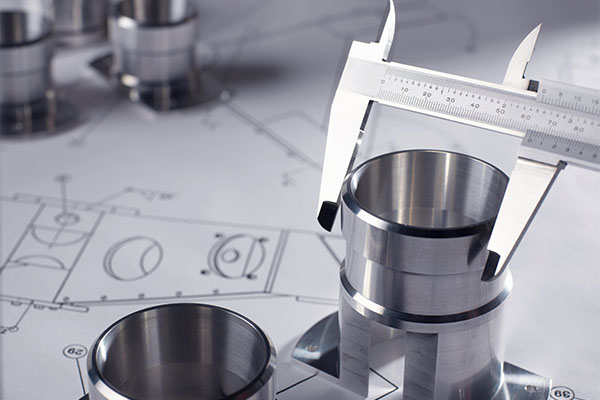
15. How Can You Order Custom Titanium Parts?
Ordering custom titanium parts involves a few straightforward steps, but it’s essential to choose a reliable CNC machining service provider. So, what’s the process like? Let’s break it down.
First, you’ll need to create or provide a detailed design of the part you need. This can be done using CAD software, which will allow manufacturers to understand the precise specifications of the part. Once you have the design, you can request a quote from a CNC machining company, which will factor in the material, labor, and machining time.
After receiving a quote, the manufacturer will begin production, using the appropriate grade of titanium and machining techniques to create the custom part. Ready for the good part? After production, the part will undergo quality checks and testing to ensure it meets your specifications before being delivered to you.
שָׁלָב | תֵאוּר |
---|---|
Design | Create or provide a CAD model |
Request quote | Get a quote based on specifications |
Manufacturing | Production using CNC machining |
Quality checks | Ensure part meets specifications |
Delivery | Receive your custom titanium part |
מדור שאלות נפוצות
שאלה 1: What are custom titanium parts?
Custom titanium parts are tailored components made from titanium that are designed to meet specific requirements for various industries such as aerospace, medical, and automotive.
שאלה 2: How does CNC machining work for custom titanium parts?
CNC machining uses computer-controlled machines to cut, shape, and form titanium into precise components based on CAD models, allowing for high precision and quality.
שאלה 3: What industries benefit from custom titanium parts?
Industries such as aerospace, medical, automotive, military, and industrial sectors benefit from custom titanium parts due to their strength, durability, and lightweight properties.
שאלה 4: How do you select the right titanium grade for custom parts?
The right titanium grade is selected based on factors like strength, corrosion resistance, and weight, with grades like Grade 5 for aerospace and Grade 2 for medical applications.
שאלה 5: What are the key properties of titanium for custom parts?
Titanium’s key properties include a high strength-to-weight ratio, corrosion resistance, heat resistance, and biocompatibility, making it ideal for demanding applications.