מָבוֹא
The world of CNC machining is evolving rapidly, and staying on top of the latest technological advancements is crucial for businesses seeking efficiency, precision, and competitiveness. In this article, we’ll dive into the latest CNC machining technologies and how they can transform your operations. We’ll explore why adopting these innovations can give your business a significant edge, how to integrate them into your existing systems, and what challenges you might face along the way. Ready for the good part? Let’s dive into how these new technologies can propel your business forward.
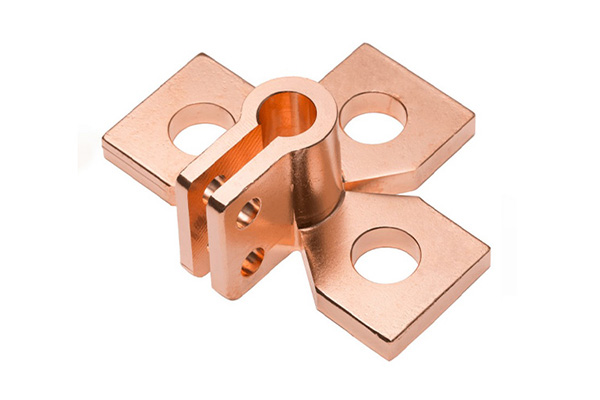
1. What are the latest CNC machining technologies?
To understand the significance of new CNC machining technology, we first need to explore the latest advancements. These technologies have revolutionized the industry, pushing boundaries of precision, speed, and efficiency. High-precision tools, multi-axis capabilities, and automation have raised the stakes in CNC machining.
The most notable development in recent years is the introduction of multi-axis machining. By allowing for more complex cuts, multi-axis machines enable manufacturers to create intricate designs with much greater accuracy. These machines move along multiple axes simultaneously, reducing the need for multiple setups and re-fixturing, which ultimately speeds up the manufacturing process.
Another major innovation is the rise of ייצור תוסף in CNC machining. While traditional CNC machining typically removes material from a workpiece, additive manufacturing builds objects layer by layer. This process has opened up new possibilities for creating complex geometries, rapid prototyping, and improving material usage efficiency.
Automation is also making waves in CNC machining. The integration of robots and artificial intelligence (AI) into machining processes not only improves consistency but also reduces labor costs. Machines now operate 24/7 with minimal human intervention, making the whole process faster and more reliable.
What’s the real story? These new technologies enable manufacturers to take on more complex projects with higher accuracy, all while reducing time and costs. The result is a more efficient and competitive manufacturing environment.
CNC Technology Innovations
טֶכנוֹלוֹגִיָה | תֵאוּר | תוֹעֶלֶת |
---|---|---|
Multi-Axis Machining | Machines that operate on multiple axes simultaneously | Reduces setup time and enhances precision |
ייצור תוסף | Builds objects layer by layer | Allows for complex designs and rapid prototyping |
Automation & AI Integration | Robots and AI-powered systems improve machining | Reduces labor costs and improves reliability |
2. Why should you care about new CNC machining technology?
The introduction of new CNC machining technology isn’t just about staying current—it’s about staying competitive. The modern business landscape demands increased efficiency, precision, and speed, and adopting these technologies ensures that your operations remain relevant.
One major benefit is cost reduction. The increased speed and precision of modern CNC machines significantly lower operational costs. With multi-axis machines and automation in place, you can produce more parts in less time, reducing both labor costs and machine downtime.
Another key benefit is improved quality. New CNC technologies are designed to produce parts with higher accuracy and fewer defects. For example, advanced software can monitor the machining process in real-time, ensuring that any potential issues are detected and corrected before they become costly problems.
But here’s the kicker: adopting new CNC technologies doesn’t just make you more efficient—it opens up new business opportunities. With the ability to produce more complex designs and handle a wider variety of materials, your business can attract a broader client base and take on more diverse projects. Whether it’s serving industries like aerospace, automotive, or medical manufacturing, you’ll be able to meet the specialized demands of each.
Cost and Quality Benefits
טֶכנוֹלוֹגִיָה | Cost Reduction | Quality Improvement |
---|---|---|
Multi-Axis Machining | Reduces material waste and labor costs | Enhances part accuracy |
ייצור תוסף | Minimizes material waste and tool usage | Increases design flexibility |
Automation & AI Integration | Lowers labor costs and operational expenses | Ensures consistent product quality |
3. How do new CNC technologies improve machining accuracy?
CNC machining has always been valued for its precision, but the latest technologies take this to a whole new level. The introduction of real-time data monitoring, enhanced controls, and more advanced cutting tools has made modern CNC machines incredibly accurate.
Closed-loop systems, for instance, allow CNC machines to monitor and adjust their operations on the fly. These systems use sensors to detect deviations in the machining process and make real-time adjustments to ensure the final product meets the required specifications. This level of real-time feedback has dramatically reduced the likelihood of human error and inconsistencies in the finished product.
Additionally, advanced tool-path algorithms are optimizing machining strategies, enabling tools to perform smoother cuts with fewer passes. This not only improves accuracy but also extends tool life and reduces wear, leading to more consistent production over longer periods.
But wait, there’s more: automated calibration further enhances accuracy by ensuring that all machine components are properly aligned before each job begins. This means fewer misalignments and faster setups, which translate into better overall machining performance.
Accuracy Enhancements
טֶכנוֹלוֹגִיָה | Accuracy Improvement | Additional Benefits |
---|---|---|
Closed-Loop Systems | Real-time error detection and correction | Reduces defects and downtime |
Tool-Path Algorithms | Smoother cuts and fewer tool passes | Extends tool life and reduces wear |
Automated Calibration | Precise machine alignment before each job | Ensures consistency and faster setups |
4. What are the benefits of adopting new CNC machining technology?
The benefits of adopting new CNC machining technology extend far beyond just operational efficiency. Let’s break down some of the most significant advantages you’ll experience by upgrading your equipment.
First and foremost, increased production speed is a major advantage. Modern CNC machines are capable of higher speeds while maintaining exceptional precision. This means that you can meet deadlines faster and take on more projects without sacrificing quality.
Moreover, reduced downtime is another critical benefit. With automated processes and better monitoring systems, new CNC technologies allow for predictive maintenance, meaning that issues are detected and addressed before they cause delays. This predictive capability helps ensure machines are always running at peak efficiency, minimizing downtime and maximizing productivity.
Here’s the good part: adopting these technologies also future-proofs your business. By integrating advanced systems, you’re not just keeping up with the competition—you’re positioning yourself as a leader in your industry. Your business will be ready to take on new challenges and meet the evolving demands of your clients.
Benefits of Adoption
תוֹעֶלֶת | פְּגִיעָה | Example |
---|---|---|
מהירות ייצור מוגברת | Faster turnaround times and higher output | Meet tight deadlines with ease |
Reduced Downtime | Predictive maintenance improves machine uptime | Fewer interruptions during production |
Future-Proofing | Stay ahead of competitors with cutting-edge technology | Position your business as an industry leader |
5. How do you integrate new CNC technologies into your existing workflow?
Adopting new CNC technology is not just about purchasing new machines—it’s about seamlessly integrating them into your existing workflow. This can be a daunting task, but with careful planning and execution, it’s entirely achievable.
One of the first steps in integration is training your team. Your employees must be equipped with the skills necessary to operate the new technology effectively. This means investing in training programs that cover everything from basic machine operation to troubleshooting and advanced programming techniques.
Another crucial step is upgrading your software. Modern CNC machines often require more sophisticated software to function properly. If your current software is outdated or incompatible with the new machines, you’ll need to upgrade or switch to a more advanced system. This ensures that you can fully utilize the capabilities of the new technology and that your machines are communicating seamlessly with your existing workflow.
This is where it gets interesting: phased implementation is often the best approach. Instead of overhauling your entire operation at once, consider gradually integrating new technologies into your workflow. This minimizes disruption and allows you to refine processes over time.
Integration Strategy
Integration Step | פְּעוּלָה | Expected Outcome |
---|---|---|
Training | Invest in comprehensive training programs | Empower employees to operate new technology |
Software Upgrades | Update software to support new CNC machines | Improve machine compatibility and efficiency |
Phased Implementation | Introduce new technology gradually to reduce disruption | Streamline adoption without overwhelming the team |
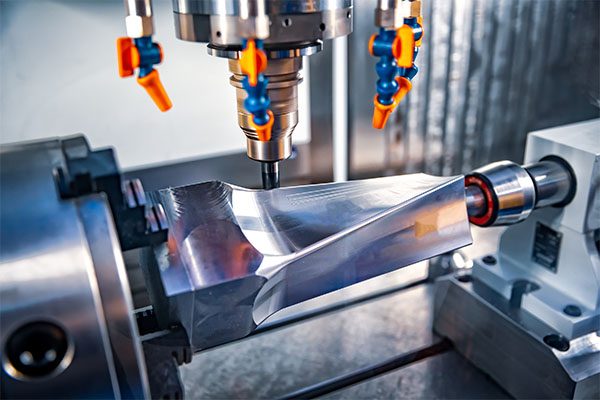
6. What are some common challenges when implementing new CNC technologies?
Implementing new CNC technology isn’t always smooth sailing. While the benefits are clear, there are challenges that businesses must be prepared to tackle.
The most immediate challenge is עֲלוּת. New CNC technologies can be expensive to purchase and integrate, and the initial investment may seem daunting. However, when you consider the long-term benefits, such as improved productivity and reduced labor costs, the investment begins to pay off.
Training is another hurdle. Employees will need to get up to speed with new systems and machinery, which can take time and resources. Some workers may also be resistant to change, making it essential to have a clear communication plan in place to ease any concerns and encourage buy-in.
What’s the bottom line? These challenges can be mitigated with proper planning and investment. By focusing on long-term goals and supporting your team throughout the transition, you can successfully navigate the implementation process and reap the rewards of cutting-edge CNC technology.
Implementation Challenges
אֶתגָר | פִּתָרוֹן | Result |
---|---|---|
Cost | Evaluate ROI and long-term benefits | Make the investment worthwhile |
Training | Provide ongoing training and support | Ensure a smooth transition to new technology |
Resistance to Change | Communicate benefits and address concerns | Build team support and readiness for change |
מַסְקָנָה
To wrap up, leveraging new CNC machining technology is an investment that can pay substantial dividends. From improved accuracy and faster production to cost savings and increased business opportunities, the benefits are undeniable. By embracing these advancements, your business can stay ahead of the competition, meet the evolving needs of clients, and future-proof your operations. The path to success in CNC machining is clear: adopt the latest technology, integrate it seamlessly into your workflow, and enjoy the rewards of a more efficient, profitable operation.
7. How does automation affect CNC machining processes?
Automation has revolutionized CNC machining by enabling continuous, high-speed production with minimal human intervention. This shift leads to faster manufacturing, reduced operational costs, and enhanced consistency in product quality.
Increased Production Rates: By integrating robots and automated systems, CNC machines can operate around the clock, reducing the need for human labor and eliminating downtime. These systems can handle repetitive tasks such as loading/unloading, tool changing, and even basic inspection, allowing the CNC machines to focus on their core tasks.
Consistency and Reliability: Automated systems help maintain a high level of consistency across production runs. Machines can perform the same operation multiple times with identical results, reducing variation and improving overall product quality.
חיסכון בעלויות: With automation, companies can lower labor costs and reduce the likelihood of errors caused by human operators. This allows businesses to stay competitive while producing high-quality products more efficiently.
Automation Benefits
Automation Benefit | פְּגִיעָה | Example |
---|---|---|
Increased Production Rates | Faster, continuous production with minimal human input | Machines running 24/7 with robots performing non-core tasks |
Consistency & Reliability | Maintains product uniformity across runs | Identical parts produced without variations |
חיסכון בעלויות | Reduces labor costs and operational inefficiencies | Fewer workers needed for repetitive tasks |
8. What materials can be processed with new CNC technologies?
New CNC machining technologies are compatible with a wide range of materials, making it easier for manufacturers to tackle complex projects across industries. These materials include metals, plastics, and even composite materials that were once difficult to machine.
Metals and Alloys: CNC machines have long been used to work with metals, including steel, aluminum, titanium, and various alloys. The latest CNC machines provide enhanced cutting capabilities, allowing for more precise and efficient metalworking.
Plastics and Composites: Modern CNC machines can now efficiently process engineering plastics and composite materials like carbon fiber and fiberglass. These materials require special tooling and machine settings, but recent advancements have made it easier to handle these tough, lightweight materials.
Innovative Materials: New CNC technologies also enable the processing of innovative materials such as ceramics and 3D-printable polymers. This opens up possibilities for industries like aerospace, automotive, and healthcare, where advanced material properties are essential.
Materials Processed with CNC Machines
Material Type | CNC Compatibility | Common Uses |
---|---|---|
Metals and Alloys | Steel, Aluminum, Titanium, etc. | Aerospace, Automotive, Industrial |
Plastics and Composites | Engineering plastics, carbon fiber, fiberglass | Consumer goods, Electronics |
Innovative Materials | Ceramics, 3D-printable polymers | Aerospace, Medical, Electronics |
9. How do you integrate new CNC technologies into your existing workflow?
Integrating new CNC technologies into your existing workflow is a strategic process that requires careful planning and execution. Here’s how you can ensure a smooth transition:
הדרכה ופיתוח מיומנויות: The first step in successfully implementing new CNC technologies is to train your workforce. Workers need to be proficient in operating the new systems, which may include learning new software, machinery, or automated processes. Training ensures that your team can operate the equipment to its full potential.
Software Integration: Modern CNC machines come with sophisticated software that may require updates or upgrades to your existing systems. Ensuring your CAD (Computer-Aided Design) and CAM (Computer-Aided Manufacturing) software are compatible with the new technology is essential for smooth operation.
Step-by-Step Implementation: Don’t rush the process. Begin by integrating one or two new machines or systems at a time. This phased approach allows you to troubleshoot any issues before scaling up.
Integration Strategy
Integration Step | פְּעוּלָה | Expected Outcome |
---|---|---|
הדרכה ופיתוח מיומנויות | Provide hands-on and theoretical training | Empower workers to effectively operate new technologies |
Software Integration | Update CAD/CAM software to support new CNC systems | Ensure seamless operation and data flow |
Step-by-Step Implementation | Integrate technologies gradually to minimize disruptions | Smooth transition with fewer challenges |
10. What are some common challenges when implementing new CNC technologies?
Implementing new CNC technology can present challenges, especially for companies that have relied on older systems for years. Here are the most common hurdles and how to address them:
Initial Costs: New CNC technologies often come with high upfront costs. Companies must evaluate whether the long-term savings in time, labor, and materials justify the investment. Understanding the return on investment (ROI) is crucial to making informed purchasing decisions.
Training and Knowledge Gaps: As new technologies evolve, so too must your workforce’s skill set. Employees need training to operate new machinery, software, and automation systems. In some cases, businesses may need to hire experts or consultants to bridge knowledge gaps.
Resistance to Change: Employees may be resistant to adopting new systems, especially if they are unfamiliar with the technology. To ease this transition, it’s important to clearly communicate the benefits of the new technology and involve workers in the decision-making process.
Common Challenges
אֶתגָר | פִּתָרוֹן | Result |
---|---|---|
Initial Costs | Calculate ROI and long-term savings | Justify the investment with cost-benefit analysis |
Training and Knowledge Gaps | Provide comprehensive training programs | Ensure team members are proficient and confident |
Resistance to Change | Communicate benefits and involve employees in the process | Foster a culture of acceptance and innovation |
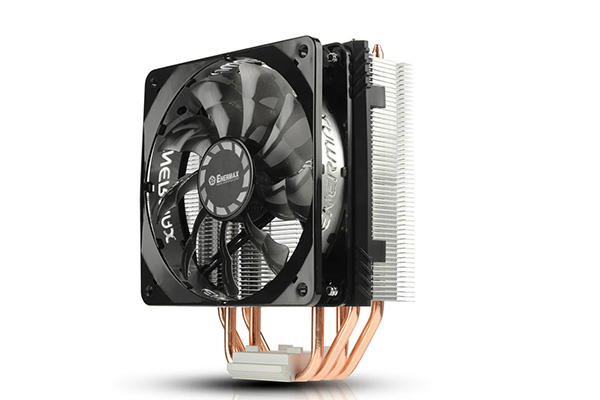
11. How do new CNC machining technologies improve product design?
New CNC technologies have dramatically changed how products are designed and manufactured. Here’s how these advancements impact product development:
Design Flexibility: Modern CNC machines allow designers to create more complex and intricate designs that were once difficult or impossible to produce. Multi-axis machining, for example, enables manufacturers to make complex cuts in all directions, creating parts with complex geometries.
Prototyping Capabilities: CNC machining speeds up prototyping, enabling businesses to quickly iterate and test new designs. This leads to faster product development cycles and the ability to test prototypes before mass production begins.
Integration with CAD/CAM: New CNC systems are seamlessly integrated with Computer-Aided Design (CAD) and Computer-Aided Manufacturing (CAM) systems, making it easier to transfer designs directly from the computer to the machine. This reduces the chance of errors and ensures that the final product matches the original design precisely.
Product Design Enhancements
Design Aspect | פְּגִיעָה | Example |
---|---|---|
Design Flexibility | Enables more complex, intricate parts | Multi-axis machines creating complex geometries |
Prototyping Capabilities | Speeds up design iterations and testing | Rapid production of prototypes for evaluation |
CAD/CAM Integration | Streamlines design-to-production workflow | Directly transferring CAD designs to CNC machines |
12. What role does AI play in CNC machining technology?
Artificial Intelligence (AI) has begun playing a major role in modern CNC machining technologies, driving efficiencies and precision. Here’s how AI is transforming the industry:
תחזוקה חזויה: AI-powered systems can analyze data from CNC machines to predict when maintenance is required. This helps avoid unplanned downtime and ensures that machines are always operating at peak performance.
Optimizing Tool Paths: AI is used to optimize tool paths, ensuring that the machine operates in the most efficient manner. By analyzing material properties, machine performance, and other factors, AI can reduce machining time and improve part quality.
בקרת איכות: AI algorithms can also monitor the quality of the machining process in real-time, detecting deviations from the desired specifications and making adjustments on the fly. This ensures that every part produced meets stringent quality standards.
AI Applications in CNC
AI Application | פְּגִיעָה | Example |
---|---|---|
תחזוקה חזויה | Prevents unexpected breakdowns and downtime | AI sensors predict when parts need servicing |
Optimizing Tool Paths | Improves machining efficiency and reduces time | AI-driven tools select the most efficient tool paths |
בקרת איכות | Ensures consistent product quality throughout production | AI detects errors and corrects them during machining |
13. How will the future of CNC machining evolve?
The future of CNC machining holds exciting possibilities, with technology continuing to push boundaries. Here’s what you can expect in the years ahead:
Integration with Industry 4.0: CNC machining will increasingly integrate with Industry 4.0 technologies such as the Internet of Things (IoT), big data, and smart factories. This will lead to even more connected systems and real-time data exchanges, allowing for better decision-making and optimization.
Further Automation: As technology advances, automation in CNC machining will become even more sophisticated. Autonomous robots, self-learning systems, and AI will continue to reduce human intervention and improve machine performance.
3D Printing Synergy: CNC machining will continue to blend with 3D printing technologies. This combination will open up new possibilities for rapid prototyping and manufacturing of complex parts, especially for industries like aerospace and healthcare.
Future Trends
מְגַמָה | פְּגִיעָה | Example |
---|---|---|
Industry 4.0 Integration | Full system connectivity for data exchange and optimization | IoT-enabled CNC machines working in sync with production lines |
Further Automation | More advanced AI and robotics for automated machining | Robots performing more complex tasks autonomously |
3D Printing Synergy | Combining CNC machining and 3D printing for advanced manufacturing | Producing complex, lightweight parts with both methods |
14. What industries benefit most from new CNC machining technologies?
New CNC technologies benefit a wide range of industries by enabling the production of highly complex parts with incredible precision. Some of the industries that stand to gain the most include:
תעופה וחלל: The aerospace industry demands precision and reliability in every part. CNC machining technologies allow for the production of high-quality components with intricate designs, such as turbine blades and structural components, meeting the stringent requirements of the industry.
רכב: CNC machining is widely used in the automotive sector for manufacturing parts like engine blocks, transmission gears, and suspension components. New technologies allow for faster production and more complex designs that improve vehicle performance and safety.
Medical Device Manufacturing: The medical industry relies on CNC machining to create precise, custom parts like implants and surgical instruments. Advanced CNC technologies allow for the manufacture of these high-precision components in a timely and cost-effective manner.
Industries Benefiting from CNC Technologies
Industry | CNC Technology Impact | Example |
---|---|---|
תעופה וחלל | High-precision, complex part production | Turbine blades, engine components |
רכב | Faster production of complex car parts | Engine blocks, transmission gears |
Medical Device Manufacturing | Precision in creating custom medical parts | Surgical tools, implants |
15. What should you look for when upgrading your CNC machinery?
Upgrading your CNC machinery is a significant investment, so it’s important to carefully consider your options. Here’s what to look for:
Technology Compatibility: Ensure that the new CNC machines are compatible with your existing systems, such as software and other equipment. This will minimize disruption and make integration easier.
Long-Term ROI: Evaluate the long-term return on investment. Consider how the new technology will reduce costs, increase productivity, and enhance product quality over time. Calculate the potential savings in both labor and materials.
Technical Support: Choose a machine supplier that offers strong after-sales support. Ensure that you have access to quick repairs, maintenance, and software updates.
Key Considerations for Upgrading
הִתחַשְׁבוּת | חֲשִׁיבוּת | Example |
---|---|---|
Technology Compatibility | Ensures smooth integration and operation | Verify software compatibility before upgrading |
Long-Term ROI | Ensures the investment will pay off over time | Evaluate savings in labor and materials |
Technical Support | Ensures minimal downtime and efficient operations | Choose suppliers with strong customer service |
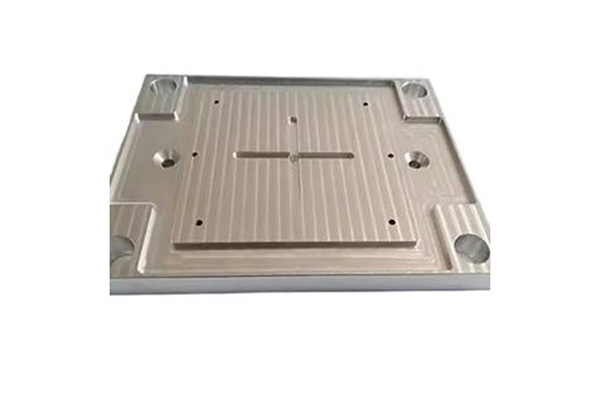
מדור שאלות נפוצות
שאלה 1: What is CNC machining technology?
CNC machining technology refers to computer-controlled machines used for manufacturing parts and products with high precision. These machines use software to automate machining processes like cutting, drilling, and milling.
שאלה 2: How does new CNC technology work?
New CNC technology integrates advanced sensors, AI-driven tools, and enhanced automation to increase efficiency, reduce human error, and improve the precision of machining processes.
שאלה 3: What are the benefits of adopting new CNC technologies?
Adopting new CNC technologies leads to faster production times, reduced costs, higher precision, and the ability to work with a broader range of materials, offering a competitive edge in manufacturing.
שאלה 4: How does automation impact CNC machining?
Automation in CNC machining allows for faster production with fewer errors, reduces labor costs, and ensures consistency in the quality of products.
שאלה 5: What are the latest trends in CNC machining?
The latest trends in CNC machining include increased use of multi-axis machines, automation, artificial intelligence, and real-time data integration to optimize production and improve precision.