מָבוֹא
Manufacturing parts for functional prototyping is a critical step in product development. It’s a process that allows businesses to test and validate their designs before they move to full-scale production. By producing functional prototypes, manufacturers can ensure that the final product meets all the required specifications and functions properly under real-world conditions. This article will walk you through the different methods, materials, and challenges involved in functional prototyping.
1. What is Functional Prototyping?
Functional prototyping is the creation of a model that closely mimics the intended functionality of the final product. The goal is to produce a prototype that not only looks like the final product but also behaves like it in terms of performance, durability, and usability. This is different from aesthetic prototypes, which are typically created for visual design purposes only. Functional prototypes are crucial in testing how a design performs under real conditions. Ready for the good part? This means that manufacturers can identify and solve issues early in the development process, saving time and money in the long run.
The need for functional prototyping arises when a product is too complex for traditional testing methods or when the stakes are high, such as in industries like aerospace or medical device manufacturing. With functional prototypes, designers can test moving parts, electronic components, or structural features that are pivotal to the product’s success. It also allows for testing under stress, providing crucial data about durability, safety, and usability.
Here’s a quick breakdown of the functional prototyping process:
- Conceptual Design: The idea is conceptualized and developed into a digital model.
- Prototype Creation: A prototype is fabricated using various methods.
- Testing and Iteration: The prototype undergoes rigorous testing to check if it meets all functional requirements.
Table: Key Steps in Functional Prototyping Process
שָׁלָב | תֵאוּר |
---|---|
Conceptual Design | Creating a digital model based on initial ideas |
Prototype Creation | Fabricating a working prototype |
Testing and Iteration | Testing functionality and refining design |
2. Why is Functional Prototyping Important in Manufacturing?
You might be wondering why functional prototyping is so important for manufacturing. Well, the answer lies in its ability to streamline product development, reduce risks, and ensure product quality. One of the main reasons functional prototyping is used is to validate design concepts before committing to mass production. Imagine spending months developing a product, only to find out it doesn’t function as expected. That’s a huge setback, not only in time but also in costs.
But here’s the kicker: functional prototypes can help avoid this problem by providing real-world feedback early on. They allow manufacturers to spot flaws, test product durability, and ensure that all components are working together as they should. With this level of validation, manufacturers can confidently move forward with the production process, knowing that they’ve addressed potential issues.
Moreover, using prototypes can significantly reduce the cost of final product development. If issues are discovered after mass production begins, the cost of rectifying them can be astronomical. Prototypes offer a chance to make adjustments without committing to large-scale manufacturing.
Table: Benefits of Functional Prototyping in Manufacturing
תוֹעֶלֶת | תֵאוּר |
---|---|
Cost-Effective Testing | Catching design flaws early can save significant money |
Risk Reduction | Minimizes the risk of production delays and costly mistakes |
Quality Assurance | Ensures the final product performs as expected |
3. How is Functional Prototyping Used in Product Development?
In product development, functional prototyping plays a key role in bridging the gap between design and manufacturing. By creating a functional prototype, manufacturers can see how a design will hold up in real-world conditions. It’s not just about testing the look of the product, but its functionality, performance, and usability.
What’s the real story here? Prototypes help identify issues with the product’s performance, usability, or user experience before going into mass production. For instance, in industries like automotive, a prototype can be used to test engine parts, aerodynamics, and safety features. This allows engineers to refine their designs and make necessary adjustments.
Functional prototypes are also used for testing physical properties like strength, flexibility, and heat resistance. For example, if you’re developing a new phone, a functional prototype allows you to test how the screen reacts to pressure, or how the battery performs under heavy usage. The results are invaluable and can lead to better overall product performance.
Table: Common Use Cases for Functional Prototypes
Industry | Application |
---|---|
רכב | Testing engine components, aerodynamics, safety features |
Electronics | Validating battery life, screen durability |
Consumer Goods | Testing usability, ergonomics, and design |
4. What Materials are Used in Functional Prototyping?
When it comes to functional prototyping, choosing the right materials is crucial. The materials used in the prototype must be able to mimic the properties of the final product to ensure accuracy in testing. The most commonly used materials in functional prototyping include plastics, metals, and composites.
Ready for the good part? Materials such as PLA, ABS, ו Nylon are commonly used in 3D printing for functional prototypes. These materials are versatile and cost-effective, providing a great balance between flexibility and strength. However, for more advanced prototypes, materials like aluminum, steel, או titanium may be used, especially when the prototype needs to undergo stress testing.
Let’s break down the material choices:
- Plastics (e.g., ABS, PLA): Great for general prototypes and functional testing, as they are lightweight and easy to mold.
- Metals (e.g., aluminum, steel): Used when the prototype must have high strength or be subjected to high stress.
- חומרים מרוכבים: These materials are a combination of two or more substances and are used when prototypes need to combine the best properties of both materials.
Table: Common Materials Used in Functional Prototyping
Material Type | Advantages | Common Uses |
---|---|---|
Plastics (ABS, PLA) | Lightweight, cost-effective | General prototyping, low-stress testing |
Metals (Aluminum, Steel) | High strength, durability | Parts that require high durability |
חומרים מרוכבים | Best of both materials, versatile | Complex or hybrid material requirements |
5. What Are the Different Methods for Functional Prototyping?
Functional prototyping can be accomplished through several methods, each with its own advantages and applications. The most common methods include 3D printing, CNC machining, ו injection molding.
Here’s where it gets interesting… each method has its own strengths depending on the type of prototype you need to create. 3D printing is great for rapid prototyping and is ideal for low-cost, low-volume production. CNC machining, on the other hand, offers high precision and is often used for metal prototypes. Lastly, injection molding is perfect for creating prototypes in high volumes, although the initial setup can be costly.
Each method also requires different types of materials, processes, and skillsets. It’s important to choose the right prototyping method based on the final product’s complexity and requirements.
Table: Comparison of Functional Prototyping Methods
שִׁיטָה | יתרונות | חסרונות |
---|---|---|
3D Printing | Fast turnaround, cost-effective | Limited by material options |
עיבוד CNC | High precision, ideal for metal parts | Higher cost, limited for small batches |
הזרקה | High-volume production, detailed parts | High initial setup cost, limited flexibility |
6. How Does 3D Printing Benefit Functional Prototyping?
3D printing is one of the most significant advancements in the field of functional prototyping. It provides manufacturers with the ability to quickly produce prototypes that are both functional and affordable. Ready for the good part? This method allows for rapid iteration, enabling designers to test and refine their ideas within hours or days, instead of waiting for weeks like traditional methods.
The beauty of 3D printing lies in its versatility. It supports a range of materials such as plastics, metals, and even composites, which means prototypes can be tested for various functional aspects like durability, flexibility, and heat resistance. The process is also highly customizable, meaning manufacturers can create complex geometries and intricate designs that would be difficult, if not impossible, to achieve with traditional methods.
Another key benefit of 3D printing is the cost-effectiveness it brings to small batch production. Unlike traditional manufacturing, which requires molds and tooling, 3D printing doesn’t involve expensive upfront costs. It’s a highly efficient method when prototypes are needed quickly and in small quantities.
Table: Benefits of 3D Printing for Functional Prototyping
תוֹעֶלֶת | תֵאוּר |
---|---|
Speed | Rapid prototyping with quick turnaround times |
Customization | Can create complex geometries and intricate designs |
Cost-Effective | No need for molds or tooling, reduces production costs |
Versatility | Supports a wide range of materials for different prototype requirements |
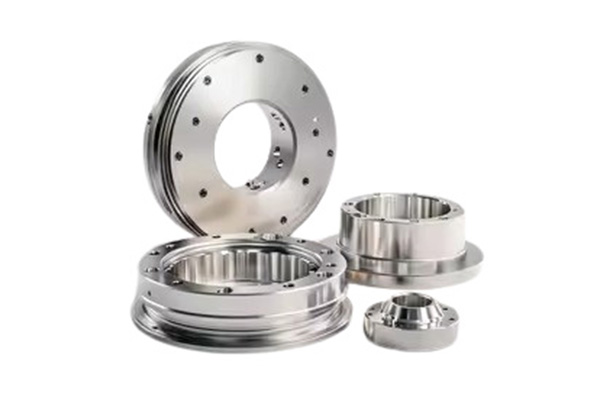
7. How Does CNC Machining Contribute to Functional Prototyping?
CNC machining is another popular method for creating functional prototypes, particularly for industries that require precision, such as automotive or aerospace. But here’s the kicker: CNC machining is ideal when you need prototypes that mimic the exact specifications of the final product, particularly when it comes to metal parts.
CNC machining involves the use of computer-controlled machines that cut, drill, and shape materials to create prototypes with high accuracy. It’s widely used because it delivers high precision and can create complex shapes in a variety of materials, including metals, plastics, ו composites. One of the key benefits of CNC machining is that it’s capable of producing parts that are virtually identical to the final product, ensuring the prototype undergoes rigorous functional testing.
However, CNC machining can be costly, especially for low-volume runs. The setup for each job requires time and resources, and while it’s ideal for precision, it may not always be the best choice for speed or cost-efficiency in smaller projects. Regardless, for prototypes that require high strength ו tight tolerances, CNC machining remains the go-to method.
Table: Advantages and Disadvantages of CNC Machining for Prototyping
Advantage | Disadvantage |
---|---|
High precision | Higher costs for small batches |
Can work with a variety of materials | Time-consuming setup |
Produces prototypes identical to final product | Limited design flexibility compared to 3D printing |
8. What Are the Challenges of Functional Prototyping?
Functional prototyping, though highly beneficial, comes with its own set of challenges. You might be wondering, “What’s the catch?” While the advantages of prototypes are numerous, the process isn’t always without complications.
One of the main challenges is עֲלוּת. While 3D printing and CNC machining have become more affordable over the years, they still require an investment in both equipment and materials. And, if you need to produce prototypes from higher-end materials or if the designs are more complex, the costs can quickly rise.
Another challenge is time constraints. Some prototyping methods require weeks to finalize, especially if the prototype involves intricate designs or is made of high-strength materials. For manufacturers working with tight deadlines, this can create scheduling issues and delays in the overall development timeline.
Lastly, material limitations can also pose a challenge. While there’s a wide range of materials available, not all of them may meet the specific requirements of a given prototype. For instance, some materials may not be able to withstand the same stresses as the final product, requiring additional adjustments and testing.
Table: Common Challenges in Functional Prototyping
אֶתגָר | Impact on Prototyping |
---|---|
Cost | High upfront costs for specialized equipment and materials |
Time Constraints | Prototyping methods can be slow, affecting product timelines |
Material Limitations | Some materials may not replicate final product performance |
9. How Do You Ensure Accuracy in Functional Prototypes?
Accuracy in functional prototypes is critical to the product’s success. Here’s where it gets interesting: the success of a prototype is directly tied to how accurately it represents the final product, both in terms of functionality and physical properties.
The first step in ensuring accuracy is to use precise design specifications. Engineers and designers must work together to ensure the prototype’s digital model is accurate down to the finest details. This digital model then serves as the blueprint for the prototype, whether it’s being produced through 3D printing, CNC machining, or injection molding.
During the prototyping process, manufacturers must also measure and test the prototype at various stages. This helps ensure that it aligns with the original design and performs as expected. Using advanced measuring tools such as coordinate measuring machines (CMM) אוֹ laser scanning technology, manufacturers can confirm that every part is within the specified tolerances.
Finally, iterative testing plays a vital role in ensuring accuracy. By testing prototypes under real-world conditions and making necessary adjustments, manufacturers can fine-tune the design before mass production.
Table: Methods for Ensuring Accuracy in Prototyping
שִׁיטָה | תֵאוּר |
---|---|
Precise Design Specifications | Create an accurate digital model for the prototype |
Measuring Tools (CMM, Laser Scanning) | Ensure parts meet specified tolerances |
Iterative Testing | Test prototypes under real conditions and refine design |
10. What Are the Costs Involved in Functional Prototyping?
The cost of functional prototyping can vary greatly depending on the method and materials used. You might be wondering, “Why is it so expensive?” The reality is that prototyping often requires specialized equipment, skilled labor, and high-quality materials, all of which contribute to the overall cost.
For example, 3D printing, while cost-effective for small runs, still requires expensive 3D printers and high-quality materials, especially when dealing with advanced filaments or metals. CNC machining, on the other hand, can have high setup costs due to the need for custom tools and machinery, though it can be cheaper for higher volumes.
Other factors that contribute to cost include labor ו design complexity. The more complex a design, the more it will cost to produce, especially if multiple iterations are required. For manufacturers looking to reduce costs, selecting a prototyping method that balances speed and material costs is key.
Table: Cost Comparison of Prototyping Methods
שִׁיטָה | Cost Factors | Typical Use Case |
---|---|---|
3D Printing | Material cost, machine cost | Low-volume, rapid prototyping |
עיבוד CNC | Setup cost, machine time | High precision and metal parts |
הזרקה | Tooling cost, setup cost | High-volume production for detailed parts |

11. How Does Functional Prototyping Improve Product Design?
Functional prototyping significantly improves product design by providing tangible insights into how a product will function. Instead of relying solely on theoretical designs or computer simulations, prototypes offer a real-world testing platform that highlights flaws in the design or functionality.
But here’s the kicker: functional prototypes make it easier to refine designs. They allow engineers to test fit, function, ו performance in actual use conditions. This hands-on approach not only helps to spot design errors early in the process but also allows manufacturers to optimize performance, reducing the risk of product failure after mass production.
Moreover, prototypes enable design teams to validate user experience. Testing the product with real users provides invaluable feedback, ensuring the design aligns with customer expectations and usability standards.
Table: How Prototypes Improve Product Design
Improvement Aspect | תוֹעֶלֶת |
---|---|
Functionality Testing | Ensures product functions as intended in real-world conditions |
Design Optimization | Allows for the refinement of design flaws and performance issues |
User Experience Validation | Provides feedback on usability and design preferences |
12. What Role Does Functional Prototyping Play in the Automotive Industry?
The automotive industry relies heavily on functional prototyping to create safe, efficient, and innovative vehicles. Prototypes allow manufacturers to test everything from רכיבי מנוע אֶל safety features ו aerodynamics. Without functional prototypes, testing such complex systems would be near impossible.
In the automotive industry, functional prototyping is used to test components under extreme conditions. For example, prototypes are tested to withstand high heat, pressure, ו vibrations to ensure durability in actual use. Additionally, prototypes help engineers optimize fuel efficiency ו handling characteristics by testing different configurations before committing to full production.
Table: Automotive Use of Functional Prototypes
Component Tested | Test Purpose |
---|---|
Engine Components | Durability and performance under high stress |
Aerodynamics | Optimizing vehicle shape for speed and fuel efficiency |
Safety Features | Ensuring compliance with safety standards |
13. How is Functional Prototyping Used in Electronics Manufacturing?
In electronics, functional prototyping is crucial for testing everything from circuit boards אֶל electronic components. Engineers use prototypes to ensure that electrical systems perform as expected before full-scale production. Without functional prototypes, it would be nearly impossible to validate designs for things like battery life, signal strength, או user interfaces.
But here’s the kicker: prototyping allows for fast iteration and testing of circuit layouts, component integration, and software interfaces. This reduces the likelihood of costly errors during final production. Moreover, prototypes can be used to test miniaturization, which is especially important in consumer electronics, where compact designs are essential.
Table: Electronics Manufacturing with Functional Prototypes
Test Area | מַטָרָה |
---|---|
Circuit Boards | Test electrical flow, connectivity, and stability |
Miniaturization | Ensure components work in compact designs |
Battery Life Testing | Test real-world battery performance |
14. How Can Functional Prototyping Be Scaled for Production?
Scaling functional prototyping for mass production is an important step in the product development cycle. Once a functional prototype has been tested and refined, manufacturers can begin to transition the design to full-scale production.
This is where it gets interesting: scaling involves more than just replicating the prototype in larger quantities. It requires adapting the design to manufacturing processes that can handle larger volumes, such as injection molding or automated assembly lines. Prototypes help designers and manufacturers identify production bottlenecks early, allowing them to optimize workflows, materials, and assembly methods.
Table: Scaling Functional Prototyping to Production
Stage | תֵאוּר |
---|---|
Design Transition | Adjust design to fit mass production requirements |
Production Testing | Test mass-produced parts for quality and functionality |
Workflow Optimization | Streamline production processes for efficiency |
15. What Are the Future Trends in Functional Prototyping?
The future of functional prototyping is bright, with technological advancements pushing the boundaries of what’s possible. Ready for the good part? אוטומציה, AI, ו advanced materials are driving new innovations in the field.
For example, automation is expected to streamline prototyping processes, making it faster and more cost-effective. Additionally, new materials such as graphene ו bio-based plastics are offering more sustainable options for prototyping. AI-driven design software is also making it easier to create prototypes with optimized performance characteristics, reducing the trial-and-error process.
Table: Emerging Trends in Functional Prototyping
מְגַמָה | Impact on Prototyping |
---|---|
אוטומציה | Speeds up production and testing |
חומרים מתקדמים | Provides more sustainable and functional options |
AI-Driven Design | Optimizes design for performance and manufacturability |
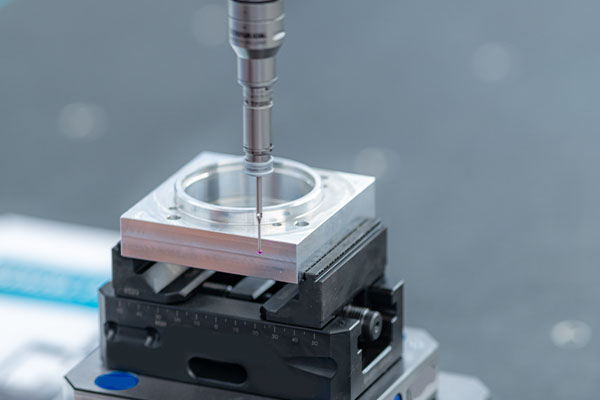
מדור שאלות נפוצות
Q1: What is functional prototyping?
Functional prototyping involves creating a prototype that mimics the final product’s functionality. This allows for real-world testing and validation before mass production.
Q2: How does 3D printing work for functional prototyping?
3D printing builds prototypes layer by layer from digital models, enabling quick production and the ability to test complex designs with a range of materials.
Q3: What materials are commonly used in functional prototyping?
Materials like ABS, PLA, and Nylon are commonly used for 3D printing functional prototypes, while metals such as aluminum and steel are used for high-strength prototypes.
Q4: How does functional prototyping improve manufacturing processes?
By allowing for early detection of design flaws and performance issues, functional prototyping helps manufacturers avoid costly mistakes during mass production.
Q5: What is the cost of functional prototyping?
The cost of functional prototyping depends on the method and materials used. 3D printing is usually cost-effective for small batches, while CNC machining and injection molding may be more expensive due to setup costs and material requirements.