परिचय
Designing parts for CNC machining can be a challenging yet rewarding task. In this article, we’ll dive deep into the best practices, common mistakes, and practical tips for creating designs that optimize both performance and efficiency in CNC machining. Whether you’re designing for high-volume production or custom prototypes, understanding the ins and outs of CNC machining design will help you achieve better results.
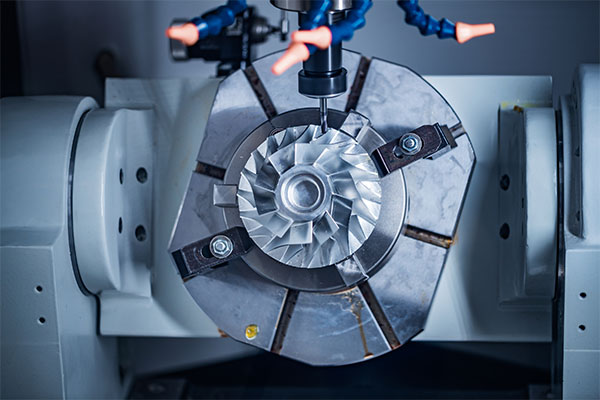
1. What Are the Key Considerations When Designing for CNC Machining?
When designing for CNC machining, several factors must be considered to ensure that the parts can be produced effectively and efficiently. यह रहा सौदा: without a solid understanding of CNC machining principles, even the best design can turn into a costly and time-consuming failure. To begin with, the material you choose plays a huge role. Different materials behave differently during the machining process, and choosing the right one is critical. Whether you’re working with metals, plastics, or composites, each material has its unique properties, such as hardness, machinability, and heat resistance.
Another critical factor is the tolerances. What’s the real story? Tight tolerances might be necessary for some parts, but these can drive up both cost and machining time. Balancing the required tolerances with the capabilities of your CNC machine ensures that your design can be executed within reasonable limits. Additionally, the complexity of the part itself is vital. This is where it gets interesting: complex geometries might require more advanced tools or multiple setups, increasing both time and cost.
Lastly, think about the ease of machining. Parts with simple geometries that are easy to clamp and machine will be more cost-effective than intricate designs. In many cases, incorporating symmetry into your design can simplify the machining process, reducing setup time and cutting down on costs.
कारक | सोच-विचार | Impact on Design |
---|---|---|
सामग्री | Hardness, machinability, cost | Influences machining time and tool wear |
Tolerances | Tight or loose tolerances | Affects cost and accuracy |
Geometry | Simple vs. complex shapes | Impacts machining complexity and cost |
Symmetry | Symmetry vs. asymmetry | Affects ease of setup and machining |
2. How Do You Choose the Right Material for CNC Machining?
Material selection is crucial when designing parts for CNC machining. क्या आप अच्छे भाग के लिए तैयार हैं? Choosing the wrong material can lead to longer machining times, increased tool wear, and ultimately higher costs. Materials such as aluminum are often preferred for CNC machining due to their ease of machining and relatively low cost. However, materials like titanium or steel offer superior strength and durability, but they require more sophisticated machinery and increased machining time.
What’s the catch? Material properties such as strength, stiffness, and thermal conductivity play a significant role in the final product’s performance. For instance, if your part needs to withstand high temperatures, materials with higher heat resistance, such as Inconel or stainless steel, might be necessary. On the other hand, if you’re designing a lightweight component, materials like magnesium or certain composites would be more appropriate.
Another consideration is the cost of the material itself. While high-performance materials offer excellent durability and performance, they can also be much more expensive. For mass production, cost-effective materials are often the best choice, as they balance performance with price. Ultimately, selecting the right material for CNC machining comes down to understanding the trade-offs between performance, machinability, and cost.
सामग्री | पेशेवरों | Cons | Best Use Case |
---|---|---|---|
अल्युमीनियम | Light, easy to machine, cost-effective | Low strength | High-volume production of non-load-bearing parts |
टाइटेनियम | High strength, corrosion-resistant | Expensive, difficult to machine | Aerospace and medical industries |
Stainless Steel | Strong, corrosion-resistant | Expensive, tough to machine | Heavy-duty components like machinery parts |
प्लास्टिक | Cost-effective, easy to machine | Less durable, weaker | Consumer products, prototypes |
3. What Role Do Tolerances Play in CNC Machining Design?
Tolerances define the allowable variation in the dimensions of a part, and they can significantly impact both the design process and the machining process. But here’s the kicker: specifying the right tolerance is a balancing act. Too tight a tolerance can increase machining costs due to the additional precision required, while too loose a tolerance can lead to issues with fit and function.
For example, parts with critical fits or assemblies require tighter tolerances to ensure they fit together properly. However, achieving tight tolerances often requires more advanced equipment, skilled operators, and longer machining times, all of which increase the cost. What’s the real story here? In many cases, specifying tolerances that are tighter than necessary adds unnecessary expense.
A good rule of thumb is to use the least restrictive tolerances that will still meet the part’s functional requirements. If your part is a simple bracket that will only be bolted into place, you don’t need to demand a tolerance of ±0.001 inches. On the other hand, for components that need to interlock or engage precisely with other parts, tighter tolerances are essential. Balancing cost, time, and precision is key to effective CNC machining design.
Tolerance Type | Impact on Cost | उदाहरण |
---|---|---|
Tight Tolerances | Increases machining time and cost | High-precision parts like gears or connectors |
Loose Tolerances | Reduces cost and machining time | Non-critical components like brackets |
Standard Tolerances | Balanced cost and precision | General parts that do not need high accuracy |
4. How Do You Prepare CAD Models for CNC Machining?
Creating an accurate CAD model is the first step in designing parts for CNC machining. Now, let’s look at the details: CAD models allow you to visualize the part before any machining begins, which can help prevent errors and optimize the design. The first step in preparing your CAD model for CNC machining is to ensure that the design is manufacturable. What’s the catch here? A part that looks great in theory might be difficult or impossible to machine due to design flaws such as excessive undercuts or overly complex geometries.
To prepare your CAD model, ensure that it’s in the correct file format, such as .STEP, .IGES, or .STL, which CNC machines can interpret. Another critical step is verifying the design with a simulation tool. These tools simulate the machining process and can detect potential issues like collisions between the tool and the part. This is where it gets interesting: using simulation tools can save both time and money by identifying potential errors before machining begins.
Once the CAD model is complete and verified, it can be exported to CAM software, which generates the toolpaths for the CNC machine. These toolpaths define how the machine will move to carve the part, and they are based on the geometry of the part and the cutting tools available. The more accurate your CAD model, the more precise the resulting part will be.
कदम | कार्रवाई | Tool/Software |
---|---|---|
1 | Create CAD model | SolidWorks, AutoCAD |
2 | Verify design for manufacturability | CAMWorks, Fusion 360 |
3 | Run simulations to detect errors | Mastercam, Vericut |
4 | Export to CAM for toolpath generation | Fusion 360, Siemens NX |
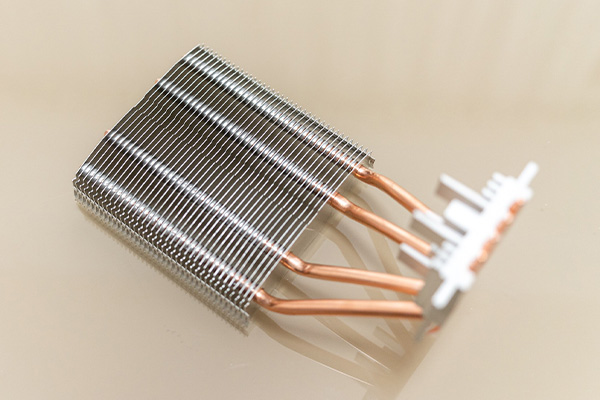
5. What Are Some Common Mistakes to Avoid in CNC Machining Design?
CNC machining is a precise and intricate process, and avoiding common mistakes is essential for producing high-quality parts. But here’s the kicker: even a small mistake in the design stage can result in costly errors down the line. One of the most common mistakes in CNC machining design is overcomplicating the geometry. क्या आप अच्छे भाग के लिए तैयार हैं? Complex shapes with intricate details often require advanced tooling or longer machining times, which increase both cost and lead time.
Another common mistake is failing to consider tool accessibility. Some designs make it difficult for the CNC machine’s tools to access certain areas of the part, requiring additional setups or tools, which can increase both time and cost. What’s the real story here? Ensuring that your design allows for easy access to all areas of the part will save time and reduce setup costs.
Lastly, overlooking the importance of part tolerances is a mistake many designers make. Tight tolerances should only be specified where absolutely necessary, as they can increase both the complexity of the design and the cost of machining. Understanding when to apply tight tolerances and when to use more generous ones is key to optimizing the design process.
Mistake | प्रभाव | समाधान |
---|---|---|
Overcomplicating geometry | Increases machining time and cost | Simplify designs where possible |
Failing to consider tool accessibility | Requires additional setups and tools | Design for easy access to all areas |
Incorrect tolerances | Increases cost and complexity | Apply tight tolerances only when necessary |
निष्कर्ष
Designing for CNC machining requires careful consideration of material, tolerances, geometry, and machining methods. By following the best practices and avoiding common mistakes, you can ensure that your CNC machining designs are efficient, cost-effective, and high-quality. The key to success lies in balancing complexity with practicality, optimizing for both performance and cost.
6. How do you optimize the design for efficiency in CNC machining?
Optimizing design for efficiency is a critical aspect of CNC machining. It involves making design choices that reduce production time, minimize material waste, and enhance machine capabilities. But here’s the kicker: the more you optimize, the more you can reduce costs and increase production throughput. So, how do you achieve this optimization?
One strategy is to minimize the number of tool changes during machining. Each tool change not only takes time but also affects the precision of the final product. By designing parts that use fewer tools, you can speed up the machining process. Additionally, designing parts with simple geometries that are easy to machine is crucial. Complicated shapes or unnecessary curves can increase machining time and require more expensive tools.
Another way to improve efficiency is through reducing material waste. This can be done by optimizing the part layout on the material sheet to ensure maximum usage of available material. For instance, if you’re machining multiple parts from the same material block, arranging them in a way that minimizes unused spaces can significantly lower material costs.
Finally, designing parts that allow for the use of standard tools and fixtures can also streamline the machining process. Custom fixtures or special tooling may seem like a good idea, but they often add time to the setup and increase the overall cost. The fewer unique tools or setups you require, the more efficient the process becomes.
Incorporating these strategies into your design process not only saves time and money but also ensures that the final product is of the highest quality with the least amount of waste.
रणनीति | विवरण |
---|---|
Minimize Tool Changes | Reduce the number of tool changes to speed up production. |
Optimize Part Layout | Arrange parts efficiently to minimize material waste. |
Use Standard Tools and Fixtures | Design parts to use readily available tools and fixtures. |
Simplify Geometries | Avoid unnecessary curves and complex shapes to speed up machining. |
7. What are the best design practices for complex CNC machining parts?
When designing complex CNC machining parts, precision and careful planning are essential. Ready for the good part? By adhering to best practices, you can ensure that your designs are not only feasible but also cost-effective and high-quality.
One of the first considerations when dealing with complex parts is to break the design down into manageable components. Instead of designing one large, complex piece, divide it into smaller, more straightforward parts that can be easily machined and then assembled. This makes the manufacturing process more efficient and less prone to errors.
For multi-axis machining, a thorough understanding of the machining process is necessary. Multi-axis CNC machines can produce more complex geometries with greater accuracy. However, designing for multi-axis machining requires considering factors such as tool access and the part’s positioning relative to the machine’s axes. This can drastically improve the part’s precision and reduce the need for rework.
Additionally, it’s important to consider the tool paths. Optimizing the tool paths to minimize tool retractions and unnecessary movements will reduce machining time and wear on the tools. Toolpath optimization also contributes to better surface finishes and increased part accuracy.
Complex parts often require multiple setups during the machining process. To minimize setup times, design parts that allow for the efficient use of fixtures and jigs. This approach will not only reduce production time but also improve consistency across the production run.
Design Consideration | मुख्य घटक |
---|---|
Breaking Down Complex Parts | Divide into smaller parts for easier manufacturing and assembly. |
Multi-Axis Machining | Plan for multi-axis operations to improve precision and flexibility. |
Tool Path Optimization | Minimize tool retraction and movements for faster machining. |
Efficient Fixtures and Jigs | Design for fixtures that reduce setup time and increase consistency. |
8. How do you incorporate cost-effectiveness into CNC machining designs?
Cost-effectiveness is a priority in any manufacturing process, and CNC machining is no exception. What’s the real story here? CNC machining, while known for precision and versatility, can become expensive if not designed carefully. So, how do you ensure your design is cost-effective?
Start by choosing materials that offer a good balance between cost, durability, and machinability. While exotic materials may seem appealing, they can significantly increase production costs due to their hardness or the need for specialized tools. Opting for more commonly used materials can help reduce costs without sacrificing quality.
Another cost-saving design consideration is to simplify geometries. The more complex a design, the more time it will take to machine, leading to higher costs. By keeping designs simple, you can reduce machining time and, consequently, labor and tooling costs. Even minor changes in part design, such as adjusting the angle of a feature or changing the radius, can have a significant impact on cost reduction.
Using standard tooling and machine setups is also a smart way to cut costs. Custom tooling and fixtures are expensive and time-consuming to create. When possible, design parts that can be manufactured with off-the-shelf tools, reducing both the initial setup and long-term costs.
Finally, batch manufacturing can be a great way to reduce per-part costs. Producing multiple parts at once maximizes the use of the machine, material, and labor, lowering the cost for each individual part. This is especially beneficial for high-volume production runs where the same design can be repeated.
Cost-Saving Strategy | फ़ायदा |
---|---|
Material Selection | Choose materials that balance cost, strength, and machinability. |
Simplify Geometries | Reduces machining time, lowering labor and tooling costs. |
Use Standard Tools and Setups | Minimizes the need for custom tooling and reduces setup time. |
Batch Manufacturing | Reduces per-part costs in high-volume runs. |
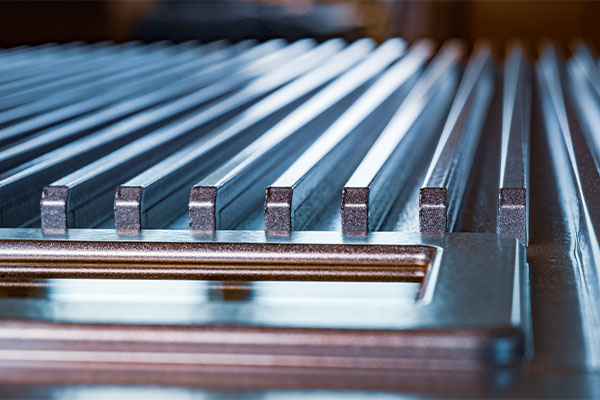
9. How does part geometry affect CNC machining?
Part geometry plays a crucial role in the efficiency and feasibility of CNC machining. This is where it gets interesting: understanding how geometry affects machining can lead to significant improvements in both production speed and part quality.
The first thing to consider is the complexity of the part geometry. Parts with intricate shapes or tight tolerances can take longer to machine, often requiring more specialized tools or additional setups. These added complexities increase the time and cost associated with the part. Therefore, simplifying the geometry whenever possible can result in faster machining times and lower costs.
Another factor to consider is the orientation of the part during machining. Geometries that require multiple angles of machining or that are difficult to position on the machine tend to slow down production. To avoid this, design parts with symmetry or that can be easily aligned during the machining process. This will reduce machine movement and minimize the need for complex setups.
Finally, the relationship between part geometry and tool access is critical. If certain features are designed in a way that makes them hard to reach with a cutting tool, it can lead to additional tool changes or more time spent repositioning the part. Proper tool access planning can significantly reduce the machining time and improve the overall quality of the part.
Geometry Factor | Impact on Machining |
---|---|
भाग जटिलता | Complex shapes increase machining time and cost. |
Part Orientation | Poor part positioning can slow down production. |
Tool Access | Limited tool access leads to longer machining times. |
10. How can you improve the durability of CNC-machined parts through design?
Durability is a critical factor in CNC machining, especially when parts are intended for harsh or high-wear environments. But here’s the kicker: improving the durability of your designs is not just about using tougher materials; it’s also about smart design choices.
One important design consideration for durability is the selection of appropriate materials. While stronger materials may seem like the obvious choice, it’s equally important to consider how the material will behave under stress, temperature fluctuations, or wear over time. Materials like stainless steel, for instance, offer excellent durability in corrosive environments, while materials like titanium are best suited for high-strength applications.
Another way to improve durability is through surface finishes. The surface of a part is often the first to suffer from wear and tear, especially in parts that experience friction or exposure to extreme conditions. By designing parts with surface finishes that enhance hardness, reduce friction, or provide corrosion resistance, you can significantly extend their lifespan. Common surface treatments like anodizing, plating, or coating can also be applied to further improve durability.
Finally, design features such as fillets, radii, and chamfers can help reduce stress concentrations on a part. Sharp corners and edges are more likely to crack under pressure, so adding a slight curve or chamfer to edges can help distribute the forces more evenly across the part, improving its overall longevity.
Design Feature | Effect on Durability |
---|---|
Material Selection | Choose materials based on strength, wear resistance, and environment. |
Surface Finishes | Enhance surface hardness and resistance to wear and corrosion. |
Stress Reduction Features | Use fillets and chamfers to reduce stress concentrations. |
11. What is the role of post-processing in CNC machining design?
Post-processing plays a vital role in CNC machining, often determining the final quality and finish of a part. So, how does post-processing impact your design? Let’s break it down.
Post-processing refers to any additional steps taken after the part has been machined to further refine its appearance, dimensions, or functionality. These steps can include grinding, polishing, coating, or heat treating. Each of these processes can have a profound effect on the final product’s performance, particularly in terms of surface finish, material properties, and overall precision.
The main advantage of post-processing is that it allows you to achieve the fine tolerances and high-quality surface finishes that might be difficult to achieve directly through CNC machining alone. For instance, grinding can be used to achieve a smooth surface, while heat treatment can be used to improve the hardness or durability of the material.
Moreover, incorporating post-processing into your design can help you account for certain imperfections that may occur during machining. By designing parts with post-processing steps in mind, you can ensure that any necessary corrections or improvements can be made without compromising the integrity of the design.
Post-Processing Step | Effect on Final Product |
---|---|
Grinding | Achieves smoother surfaces and fine tolerances. |
Heat Treatment | Increases material hardness and durability. |
Polishing | Enhances surface appearance and reduces surface defects. |
12. How can you improve part functionality through design?
Functionality is paramount when designing CNC-machined parts, as the final product must meet the intended performance standards. Ready for the good part? By integrating functional features directly into your design, you can ensure that your part performs optimally while minimizing manufacturing complications.
One key aspect of functionality is ensuring that the part fits and works as intended in the final assembly. For example, if you’re designing a mechanical component, it’s crucial that features like holes, threads, and mating surfaces are accurately designed to match the dimensions and tolerances required by the assembly.
Another critical consideration is designing for ease of use. Parts should be easy to handle, install, and maintain. For example, if you’re designing a part that will be exposed to frequent disassembly, consider adding features like chamfers to make handling easier or ensuring that fasteners are easily accessible for maintenance.
Finally, it’s essential to consider the part’s function in terms of stress distribution. By designing parts with evenly distributed loads, you can ensure they perform well under stress without failing prematurely. Features such as ribs, gussets, and fillets can help in distributing stress more evenly across the part.
Functional Design Consideration | Effect on Part Functionality |
---|---|
Accurate Features | Ensures proper fit and function in the final assembly. |
Ease of Handling and Maintenance | Makes parts easier to install, maintain, and service. |
Stress Distribution | Reduces the risk of premature failure under stress. |
13. What tools can help you design parts more effectively for CNC machining?
Designing parts effectively for CNC machining involves using the right tools and software. But wait, there’s more: choosing the right tools can make a huge difference in your design process, reducing errors and ensuring faster production times.
CAD (Computer-Aided Design) software is one of the primary tools used in CNC machining design. It allows designers to create detailed 3D models of parts, which can then be easily converted into machining instructions. Popular CAD tools include AutoCAD, SolidWorks, and Fusion 360. These tools provide precise control over dimensions and geometries, allowing designers to visualize and refine their designs before sending them off to the machine.
CAM (Computer-Aided Manufacturing) software is equally important. While CAD software is used to design the part, CAM software helps translate that design into machine instructions. It takes the 3D model and generates tool paths that tell the CNC machine how to cut the material. Fusion 360 and Mastercam are two examples of CAM tools commonly used in CNC machining.
Finally, simulators can be incredibly helpful for testing your design before machining. These tools simulate how the part will be produced, allowing you to detect errors, optimize tool paths, and ensure the final part will be free from defects.
Tool Type | Example Tools | उद्देश्य |
---|---|---|
सीएडी सॉफ्टवेयर | AutoCAD, SolidWorks, Fusion 360 | Create 3D models and detailed drawings of parts. |
CAM Software | Fusion 360, Mastercam | Generate machine tool paths from CAD designs. |
Simulators | CNC Simulator, Vericut | Test and optimize designs before actual machining. |
14. How do you ensure high-quality results when designing for CNC machining?
Ensuring high-quality results requires meticulous planning and attention to detail. This is where it gets interesting: by implementing certain design strategies, you can significantly improve the quality of your final product.
One of the first steps to ensuring high-quality results is to specify tolerances that match the requirements of the final application. For instance, parts that will be subjected to high stress or require precise fits should have tight tolerances. In contrast, parts used in less critical applications can afford looser tolerances.
Another way to ensure quality is through the use of proper design for manufacturability. This means designing parts with ease of production in mind. Features like fillets, radii, and chamfers not only help reduce stress concentrations but also make the part easier to machine, resulting in better surface finishes and fewer errors.
Additionally, it’s essential to conduct regular inspections during the manufacturing process. This can include measuring parts at various stages of machining to ensure they meet the required specifications. If any discrepancies are found, the design can be adjusted before proceeding to the next stage.
Quality Control Strategy | फ़ायदा |
---|---|
Tight Tolerances | Ensures precise fits and better performance in critical applications. |
Design for Manufacturability | Reduces machining errors and improves surface finishes. |
Regular Inspections | Identifies discrepancies early, preventing costly rework. |
15. How can you design for both CNC machining and 3D printing?
Hybrid manufacturing methods, such as combining CNC machining with 3D printing, offer flexibility and cost savings. What’s the real story? By designing parts that can be produced using both methods, you can achieve the best of both worlds.
When designing for both CNC machining and 3D printing, it’s important to understand the strengths and weaknesses of each method. CNC machining is excellent for high-precision parts and those requiring high strength, while 3D printing is better suited for creating complex geometries and prototypes quickly.
One of the key considerations is ensuring that the design can be easily modified for both methods. For example, the parts that are to be 3D printed should have features that can be produced layer by layer, such as lattice structures or overhangs that are difficult to achieve with traditional machining.
Conversely, when designing for CNC machining, you should avoid overcomplicating the part’s geometry, as machining complex shapes can increase time and cost. Instead, focus on designing the part in such a way that features that can be easily produced by both methods are prioritized.
Hybrid Manufacturing Factor | CNC Machining Advantages | 3D Printing Advantages |
---|---|---|
डिज़ाइन लचीलापन | High precision and strength | Complex geometries and prototypes |
Feature Complexity | Simpler shapes are easier to machine | Complex features can be printed faster |
Cost and Time Efficiency | Efficient for high-volume production | Excellent for low-volume or custom parts |
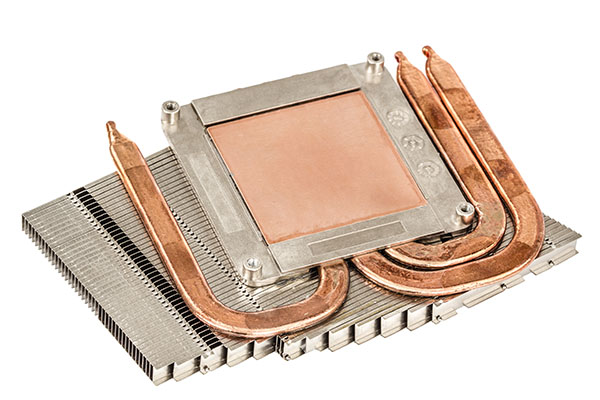
अक्सर पूछे जाने वाले प्रश्न अनुभाग
प्रश्न 1: What is CNC machining design?
CNC machining design involves creating detailed models of parts that can be efficiently manufactured using CNC machines. It requires an understanding of material properties, tolerances, and geometry to ensure the part can be accurately produced.
प्रश्न 2: How does material choice affect CNC machining design?
Material choice affects the machinability, cost, and performance of a part. Different materials have unique properties that impact tool wear, machining time, and final product quality.
प्रश्न 3: How do tolerances impact CNC machining?
Tolerances determine the acceptable variation in part dimensions. Tight tolerances require more precision and increase machining time and cost, while loose tolerances can reduce cost and time.
प्रश्न 4: How can you avoid common mistakes in CNC machining design?
Common mistakes include overcomplicating geometry, failing to consider tool accessibility, and specifying unnecessary tight tolerances. Simplifying designs and ensuring ease of machining can help avoid these errors.
प्रश्न 5: What are some tips for optimizing CNC machining designs for cost-effectiveness?
To optimize designs for cost-effectiveness, simplify geometries, choose the right material, apply appropriate tolerances, and ensure ease of tool access during machining. These steps help reduce time and cost.