परिचय
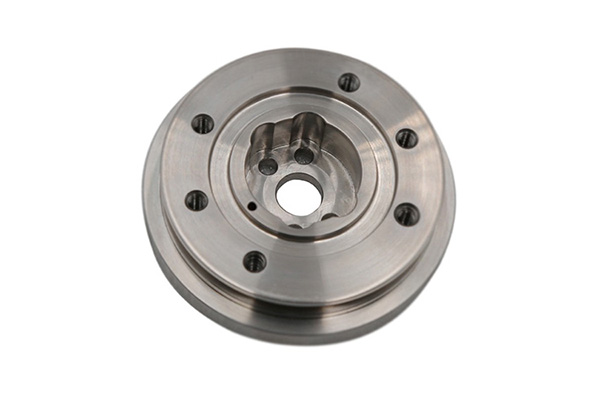
Design for CNC machining refers to the process of creating parts and components with a focus on optimizing them for CNC (Computer Numerical Control) machines. This process involves considering the capabilities and limitations of CNC machines to ensure that parts are manufacturable, cost-effective, and high quality. In other words, design for CNC machining helps businesses ensure that their designs can be efficiently produced using modern machining techniques.
Here’s the deal: CNC machining has become a staple in manufacturing because of its precision, repeatability, and ability to work with a variety of materials. But if you’re not careful during the design phase, it can lead to longer production times, higher costs, or even the need for redesigns. So, if you want to make the most of CNC machining, it’s essential to understand how to design parts that work seamlessly with these machines.
This article will cover everything you need to know about designing for CNC machining, from its importance to practical tips on how to optimize your designs. Let’s dive in!
1. Why is Design Critical for CNC Machining?
When it comes to CNC machining, the design of your part can make or break the entire production process. But why does design matter so much? Simply put, it determines how quickly, accurately, and cost-effectively a part can be produced.
What’s the real story? The key to effective CNC machining lies in understanding how design affects machining efficiency. Poorly designed parts can lead to longer machining times, more tool changes, or excessive waste, all of which increase costs. On the other hand, a well-designed part can streamline the machining process, reduce production times, and save money.
To give you a clearer picture, let’s break down some factors that highlight why design is so critical in CNC machining:
- Tooling and Setup: The more complex a design is, the more tools and setups are required during machining. This increases the time spent on the machine, as well as the cost.
- सामग्री अपशिष्ट: The design can significantly affect how much material is wasted during production. Complex geometries or inefficient shapes often lead to more scrap material.
- Production Speed: Simple designs tend to be faster to produce, as they involve fewer machine movements and less complex tool paths. The quicker you can produce a part, the lower your costs.
क्या आप अच्छे भाग के लिए तैयार हैं? A good design reduces the number of setups, simplifies the machining process, and minimizes material waste. All of these things directly contribute to lowering overall production costs. By focusing on creating designs that work well with CNC machinery, you can increase efficiency and improve your bottom line.
Table: Factors Influencing CNC Machining Efficiency
कारक | सीएनसी मशीनिंग पर प्रभाव | नतीजा |
---|---|---|
Tooling and Setup | More setups increase machining time | Higher costs, longer production |
सामग्री अपशिष्ट | Complex designs lead to more waste | Increased material costs |
Production Speed | Simple designs are faster to produce | Lower overall cost |
2. What Are the Key Principles of Design for CNC Machining?
When designing for CNC machining, there are several principles that should guide the design process. Here’s where it gets interesting… These principles are not just technicalities; they’re the foundation of successful CNC machining and can dramatically impact production time, quality, and cost.
Let’s break down the key principles:
- Design for Manufacturability: This principle focuses on designing parts that are easy to machine. The goal is to make sure the design can be efficiently and cost-effectively produced by CNC machines. This involves considering factors like tool access, part orientation, and the number of tool changes required during production.
- Minimize Complex Features: While CNC machines are capable of producing highly complex geometries, it’s often more cost-effective to design parts with simpler shapes. This can reduce machining time and tooling costs.
- Material Considerations: The material you choose impacts the machining process. Some materials are more difficult to machine, requiring specialized tooling or longer machining times. Understanding material properties and how they interact with CNC processes is critical for a successful design.
आप सोच रहे होंगे कि how these principles apply in real life. Consider a company that designs a part with excessive undercuts or thin walls. These features might look great on paper but could require extra machining time or tooling, which ultimately increases costs. On the other hand, designing parts with rounded edges, fewer undercuts, and better tool access will ensure a quicker, more efficient production process.
Table: Design Principles for CNC Machining
Principle | विवरण | फ़ायदा |
---|---|---|
Design for Manufacturability | Parts should be easy to machine | Reduces machining time and costs |
Minimize Complex Features | Avoid overly complex shapes and features | Faster, cheaper production |
Material Considerations | Choose materials that are easy to machine | Lower tool wear, faster machining |
3. How Can You Optimize Your CNC Design for Efficiency?
Optimization is key when it comes to CNC machining. The goal is to design parts that are not only easy to machine but also reduce the time and resources required to make them. This is where it gets interesting… Proper optimization can drastically reduce both material and labor costs, making your production process more efficient.
Here are a few tips on how to optimize your CNC designs:
- Use Standardized Features: Whenever possible, use standard shapes and sizes. Standard tools are more readily available and typically less expensive to use. This also reduces setup time since the tools are already part of the machine’s regular operation.
- Minimize Tool Changes: Each time the machine needs to change tools, it adds time to the production process. Design parts in a way that minimizes the number of tool changes required.
- Consider Part Orientation: The orientation of your part on the CNC machine can have a significant impact on both machining time and accuracy. Proper part orientation ensures that the machine can access the entire surface without repositioning, which saves time and reduces errors.
So, how do these strategies work together? Let’s take the example of a complex part design that requires multiple tool changes. By redesigning the part to eliminate unnecessary features, you can reduce the number of tool changes, streamline the machining process, and lower production costs. The key here is balancing design complexity with efficiency—while still maintaining the part’s functionality and quality.
Table: CNC Design Optimization Tips
Tip | विवरण | Impact on Efficiency |
---|---|---|
Use Standardized Features | Use common shapes and sizes for easier machining | Reduces cost and setup time |
Minimize Tool Changes | Design parts to require fewer tool changes | Reduces machining time and cost |
Consider Part Orientation | Position parts to reduce machine movement | Increases accuracy and speed |
4. What Role Does Tolerances Play in CNC Design?
Tolerances are an important aspect of CNC machining because they determine how much variation is allowed in the finished part. What’s the real story? Tight tolerances might sound appealing, but they often come at a cost. Achieving tight tolerances typically requires more advanced machines, more time, and more effort, all of which drive up the cost of production.
Here’s how tolerances affect your CNC design:
- Material and Tooling Costs: Achieving tight tolerances often requires high-quality materials and specialized tools. This can drive up the cost of production significantly.
- Machining Time: The tighter the tolerance, the longer it may take to machine the part. Achieving precise measurements often requires additional steps in the machining process, increasing production time.
- गुणवत्ता नियंत्रण: With tighter tolerances, more quality checks are needed throughout the machining process to ensure the final part meets specifications.
क्या आप अच्छे भाग के लिए तैयार हैं? While tight tolerances are necessary for some applications, they can often be relaxed without compromising the functionality of the part. This allows you to reduce machining time and material costs, while still maintaining an acceptable level of quality.
Table: Tolerance Impact on CNC Design
Tolerance Type | Impact on Cost | Impact on Machining Time |
---|---|---|
Tight Tolerances | Higher material and tooling costs | Increased machining time |
Loose Tolerances | Lower cost | Reduced machining time |
Standard Tolerances | Balanced cost and time | Efficient production |
5. How Do You Choose the Right Materials for CNC Machining?
The material you choose for CNC machining has a significant impact on both the cost and the quality of your parts. But here’s the kicker… While it might seem like the strongest or most exotic material is always the best choice, that’s not always the case. The right material should be chosen based on the application, the machining process, and cost constraints.
Here’s how to choose the best material:
- Material Strength and Durability: Depending on the part’s intended use, you’ll need to select a material that has the appropriate strength and durability. For instance, parts that will be exposed to high stress or extreme temperatures may require stronger materials like titanium or hardened steel.
- Ease of Machining: Some materials, like aluminum, are easier to machine than others, reducing production time and cost. However, they may not be suitable for all applications.
- Cost Efficiency: While high-strength materials might be ideal for certain applications, they can also be very expensive. It’s important to balance material costs with performance needs.
What’s the real story? Materials like aluminum are a favorite in CNC machining because they are relatively easy to machine, have a good strength-to-weight ratio, and are cost-effective. However, for parts requiring higher strength or durability, more expensive materials like stainless steel may be necessary. The key is to choose a material that meets the part’s requirements while keeping costs in check.
Table: Material Selection for CNC Machining
सामग्री | ताकत | Machining Ease | लागत |
---|---|---|---|
अल्युमीनियम | मध्यम | आसान | कम |
Stainless Steel | उच्च | मध्यम | उच्च |
टाइटेनियम | Very High | Difficult | Very High |
6. How Does Design Affect CNC Machining Quality?
Design plays a pivotal role in determining the overall quality of a part produced via CNC machining. What’s the real story? A well-crafted design ensures that the final product is precise, meets functional specifications, and has a smooth, flawless finish. In contrast, poor design choices can lead to inconsistencies in product dimensions, rough surfaces, and additional post-production work.
Let’s break down the key ways design affects CNC machining quality:
- सतह खत्म: The geometry of a part can influence the surface finish achieved during machining. Sharp corners or complex features might require additional finishing processes such as polishing or grinding. Simple, smooth contours can help achieve a high-quality surface finish with fewer additional processes.
- Part Accuracy: Accurate designs help ensure that parts fit together as intended. Precision in dimensions and tolerances is critical, especially for parts that must be assembled or must fit into tight spaces. Poor design can lead to dimensional variations that require expensive corrections.
- Tool Wear: Parts with intricate geometries or hard materials can cause tools to wear out more quickly, affecting the machining process. This means the tools need to be replaced more often, increasing downtime and production costs.
But here’s the kicker… By designing with the machine’s capabilities in mind, you can minimize the potential for defects, improve part quality, and reduce rework. The better your design, the less likely you are to face post-production quality issues that can delay shipments or increase costs.
Table: Design Factors Impacting CNC Machining Quality
Design Factor | Impact on Quality | नतीजा |
---|---|---|
सतह खत्म | Affects the smoothness and finish of parts | Better finish, fewer rework cycles |
Part Accuracy | Ensures parts fit together as intended | Precision, reduced dimensional errors |
Tool Wear | Complex designs can lead to faster tool wear | Increased costs, frequent tool replacements |
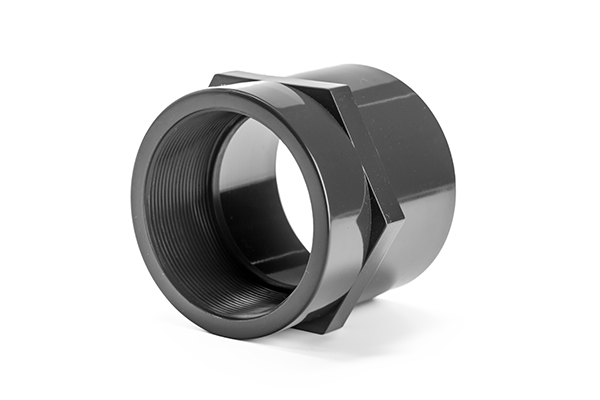
7. How Do You Choose the Right Materials for CNC Machining?
Choosing the right material for CNC machining is a critical step that can significantly impact both the quality and cost of a part. क्या आप अच्छे भाग के लिए तैयार हैं? Material selection influences the machining process, including tool choice, machining time, and production efficiency. Here’s how to go about selecting the best material:
- Material Strength and Durability: Depending on the intended application of the part, you’ll need to choose a material that offers the required mechanical properties. For high-stress applications, materials like titanium and stainless steel might be required, whereas lighter parts can be made from aluminum or plastics.
- Ease of Machining: Some materials are easier to machine than others. For example, aluminum is relatively easy to machine compared to harder materials like stainless steel. The machinability of a material affects how quickly the part can be produced and the wear on the cutting tools.
- Cost Considerations: Material costs can vary widely. While titanium might be ideal for specific applications, it is expensive and harder to machine. On the other hand, aluminum is less costly and easier to machine, but it may not offer the same strength or durability.
What’s the real story? The best material for a given part depends on balancing the material’s strength, machinability, and cost. Ideally, the material should be suited for both the functional requirements of the part and the capabilities of the CNC machine.
Table: Material Selection for CNC Machining
सामग्री | ताकत | Machinability | लागत |
---|---|---|---|
अल्युमीनियम | मध्यम | आसान | कम |
Stainless Steel | उच्च | मध्यम | उच्च |
टाइटेनियम | Very High | Difficult | Very High |
8. What Are the Common Mistakes to Avoid in CNC Design?
Designing parts for CNC machining isn’t always straightforward. What’s the real story? Many engineers and designers make common mistakes that lead to increased costs, longer production times, and poor-quality parts. Here are some of the most frequent mistakes and how to avoid them:
- Overly Complex Features: Complex geometries or intricate features often lead to longer machining times, increased tool wear, and higher costs. While some complexity may be unavoidable, aim to design parts with simpler, more straightforward shapes to reduce machining time and cost.
- Ignoring Tool Access: Designing parts without considering the accessibility of cutting tools can result in tooling conflicts and added machining time. Ensure that all parts of the design are accessible by the machine tools.
- Not Accounting for Material Shrinkage: Materials, especially metals, can shrink slightly during the cooling process after machining. If this shrinkage isn’t accounted for during the design phase, it can result in dimensional inaccuracies.
Here’s the kicker… Avoiding these common mistakes is crucial for improving efficiency and lowering the risk of defects. By designing parts that are easy to machine, considering tool access, and accounting for material properties, you can optimize your designs for CNC machining.
Table: Common CNC Design Mistakes and Solutions
Mistake | प्रभाव | समाधान |
---|---|---|
Overly Complex Features | Longer machining times and increased costs | Simplify designs where possible |
Ignoring Tool Access | Tooling conflicts, longer setups | Ensure all areas are accessible by tools |
Not Accounting for Material Shrinkage | Dimensional inaccuracies | Factor in material shrinkage during design |
9. How Can You Improve Your CNC Design Skills?
Improving your CNC design skills takes time and practice, but there are several strategies you can follow to become more proficient. What’s the real story? As CNC technology continues to evolve, staying up-to-date with the latest tools and techniques is essential for creating optimal designs. Here are a few ways to improve your skills:
- Learn CNC Machine Capabilities: Understanding the capabilities of different CNC machines is critical. Knowing the limitations and advantages of the machines you’re working with allows you to create designs that are easier to manufacture.
- Master CAD/CAM Software: Computer-Aided Design (CAD) and Computer-Aided Manufacturing (CAM) software are essential tools for CNC design. Mastering these programs helps you visualize parts in 3D and simulate the machining process before actual production.
- Follow Best Practices: Keep learning about best practices in CNC machining design. Follow industry blogs, attend workshops, and connect with professionals to stay informed about the latest trends and techniques.
Here’s where it gets interesting… By continuously improving your CNC design skills, you not only enhance the efficiency of your designs but also contribute to better productivity and reduced production costs.
Table: Tools to Improve CNC Design Skills
औजार | उद्देश्य | फ़ायदा |
---|---|---|
CNC Machine Knowledge | Understanding machine capabilities | Ensures designs are machine-friendly |
सीएडी/सीएएम सॉफ्टवेयर | Design and simulate parts | Visualizes designs before machining |
Best Practices | Learn design and machining techniques | Increases efficiency and accuracy |
10. How Does 3D Modeling Help in CNC Machining Design?
3D modeling is an invaluable tool in CNC machining. But here’s the kicker… With the ability to create realistic, virtual prototypes of your design, you can catch potential issues before they become costly mistakes in production. Here’s how 3D modeling benefits CNC design:
- Previews and Adjustments: With 3D modeling software, you can visualize the design from every angle, making it easier to detect flaws or areas for improvement. This allows for adjustments before the design goes into production.
- Simulation of Machining Process: 3D modeling can simulate the actual CNC machining process, helping to identify potential problems like tool conflicts or machining inefficiencies.
- Reduced Prototyping Costs: Since you can virtually test the design, the need for physical prototypes is greatly reduced. This not only saves money but also speeds up the design-to-production timeline.
What’s the real story? 3D modeling enhances both the efficiency and accuracy of the design process. By catching errors early and simulating the machining process, you save time and money while improving product quality.
Table: Benefits of 3D Modeling for CNC Design
फ़ायदा | विवरण | नतीजा |
---|---|---|
Previews and Adjustments | Visualize design flaws before production | Reduced design errors |
Simulation of Machining Process | Simulate the CNC machining process | Fewer tool conflicts and errors |
Reduced Prototyping Costs | Virtual testing eliminates the need for physical prototypes | Faster time-to-market |
11. What Are Some Design Guidelines for CNC Milling?
CNC milling involves cutting away material using rotary cutters, and certain design guidelines can make the process more efficient. क्या आप अच्छे भाग के लिए तैयार हैं? By following the right guidelines, you can design parts that are easier to mill, thus reducing machining time and costs. Here are some important design tips for CNC milling:
- Tool Access: Ensure that the milling machine can access all areas of the part. Avoid deep pockets or undercuts that might be difficult to machine.
- Use of Rounding: Rounding off sharp edges not only improves the appearance of the part but also reduces the likelihood of tool damage.
- Avoid Thin Walls: Thin walls may be difficult to mill accurately and can cause part distortion. If thin walls are necessary, ensure they are properly supported during machining.
What’s the real story? Following these guidelines will ensure that parts are milled more efficiently, with less downtime and fewer tool changes. The end result? A cost-effective, high-quality product.
Table: CNC Milling Design Guidelines
Guideline | विवरण | फ़ायदा |
---|---|---|
Tool Access | Ensure the design is easily accessible by tools | Faster machining times |
Use of Rounding | Round sharp edges to avoid tool wear | Increased tool life, better finish |
Avoid Thin Walls | Design parts with sufficient thickness | Prevents distortion and machining errors |
12. How Does Design Affect CNC Turning Operations?
CNC turning is a machining process where material is rotated and cut with a stationary tool. Here’s the kicker… Good design for CNC turning can make the difference between smooth, quick operations and costly, time-consuming delays. Here are some considerations when designing for CNC turning:
- Part Shape: When designing for turning, aim for symmetrical shapes. Parts with asymmetry or irregular geometries can complicate the turning process and increase setup time.
- Cutting Tool Access: Similar to milling, ensure that cutting tools can easily access all areas of the part. This reduces the number of tool changes needed and speeds up the process.
- Hole Design: Holes should be designed with proper entry and exit points to ensure smooth cutting and avoid tool interference.
What’s the real story? The key to effective CNC turning design is simplicity and symmetry. By designing parts with these principles in mind, you can streamline the turning process and reduce machining costs.
Table: CNC Turning Design Guidelines
Guideline | विवरण | फ़ायदा |
---|---|---|
Part Shape | Use symmetrical shapes | Reduces complexity and time |
Cutting Tool Access | Ensure tools can easily access the part | Faster, efficient machining |
Hole Design | Proper entry and exit points for holes | Reduces tool wear and time |
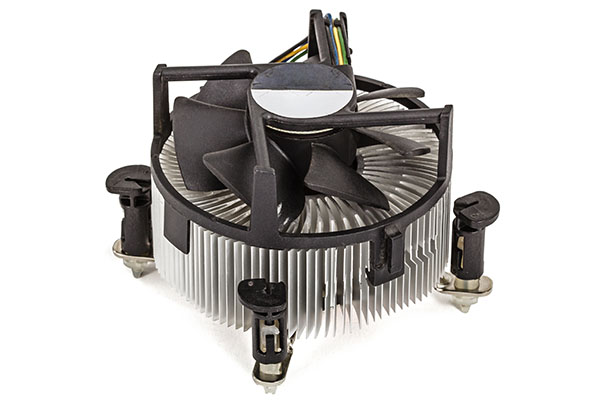
13. What is the Importance of Part Orientation in CNC Machining?
Part orientation is crucial in CNC machining, affecting both accuracy and machining time. What’s the real story? The orientation of a part on the machine can influence everything from the part’s surface finish to the ease of machining. Here’s how:
- Surface Quality: Proper orientation ensures that the cutting tool can work efficiently and smoothly across the entire surface of the part, improving finish quality.
- Machining Speed: Correct orientation minimizes the number of reorientations required during machining, which directly impacts machining speed.
- Tool Access and Reach: When designing the part orientation, ensure that all parts of the geometry are accessible by the CNC tool.
क्या आप अच्छे भाग के लिए तैयार हैं? The right part orientation not only reduces machining time but also improves part accuracy and surface finish.
Table: Impact of Part Orientation on CNC Machining
कारक | Impact on Machining Process | नतीजा |
---|---|---|
Surface Quality | Proper tool access improves surface finish | Higher quality, fewer defects |
Machining Speed | Correct orientation reduces reorientations | Faster production times |
Tool Access and Reach | Ensure tool can reach all areas | Increased precision and speed |
14. How Do You Incorporate Assembly Requirements into CNC Design?
When designing parts for CNC machining, it’s important to consider how those parts will fit together during assembly. But here’s the kicker… Designing parts that fit together seamlessly can save time and cost during assembly, improving the overall production process. Here’s how to integrate assembly requirements into your CNC design:
- Interference Checking: During the design phase, check for potential interference points that could prevent parts from fitting together properly. Ensure that all parts have the necessary features for smooth assembly.
- Assembly Ease: Design parts in a way that minimizes the complexity of the assembly process. Consider things like ease of insertion and whether any parts will require additional tools or fixtures during assembly.
- Fasteners and Fittings: Include proper holes and threads for fasteners and fittings in the design. Avoid tight tolerances around these areas to make assembly quicker and more straightforward.
Here’s the kicker… By considering assembly requirements during the design phase, you can streamline production and reduce the risk of errors during the final assembly stage.
Table: Assembly Considerations for CNC Design
सोच-विचार | Impact on CNC Design | नतीजा |
---|---|---|
Interference Checking | Ensure parts fit together | Reduced assembly time, fewer errors |
Assembly Ease | Minimize complexity in assembly | Faster, more efficient assembly |
Fasteners and Fittings | Include proper holes and threads | Smoother, faster assembly |
15. How Can Design for CNC Machining Improve Overall Production?
Designing parts with CNC machining in mind can significantly improve overall production efficiency. What’s the real story? By optimizing your designs for CNC machines, you can reduce lead times, cut costs, and improve product quality. Here’s how design can impact the entire production process:
- Streamlined Processes: Optimized designs reduce the need for manual adjustments during machining, leading to faster production.
- Lower Costs: Efficient designs minimize waste, reduce tooling costs, and require fewer post-production processes, resulting in lower overall costs.
- Increased Profitability: By improving efficiency and reducing costs, manufacturers can increase profitability while still producing high-quality parts.
Here’s where it gets interesting… By focusing on design for CNC machining, businesses can enhance productivity, reduce waste, and ultimately improve their profit margins. In other words, design isn’t just about aesthetics—it’s about driving business success.
Table: Design for CNC Machining Impact on Production
कारक | Impact on Production | नतीजा |
---|---|---|
Streamlined Processes | Reduced need for adjustments | Faster production times |
Lower Costs | Fewer material wastes and tool changes | Reduced overall manufacturing costs |
Increased Profitability | More efficient production methods | Higher profit margins |
निष्कर्ष
In conclusion, design for CNC machining is an essential aspect of modern manufacturing. By focusing on design principles such as manufacturability, simplicity, and material compatibility, you can optimize production efficiency, reduce costs, and ensure high-quality outcomes. Through careful planning, choosing the right materials, and understanding the importance of tolerances, manufacturers can create products that not only meet performance standards but are also cost-effective to produce.
What’s the real story? If you take the time to design parts specifically for CNC machining, you’ll save time, reduce costs, and increase the quality of your final product. So, whether you’re designing for prototyping or large-scale production, always consider how your design will interact with CNC technology.
सामान्य प्रश्न
प्रश्न 1: What is design for CNC machining?
Design for CNC machining refers to the process of creating parts that are optimized for manufacturing using CNC machines. It involves considering the machining process, materials, and tolerances to ensure the part can be efficiently produced.
प्रश्न 2: How does design affect CNC machining work?
Design directly impacts CNC machining work by influencing efficiency, production time, and material waste. Well-designed parts are easier and quicker to produce, resulting in lower costs.
प्रश्न 3: What materials are best suited for CNC machining?
Materials like aluminum, stainless steel, and titanium are commonly used for CNC machining. The choice of material depends on factors such as strength, machinability, and cost.
प्रश्न 4: What are the most common design mistakes in CNC machining?
Common design mistakes include overly complex features, failing to account for machine limitations, and not considering material shrinkage or tool accessibility.
प्रश्न 5: Can design for CNC machining help reduce costs?
Yes, good design practices can reduce machining time, material waste, and the need for rework, all of which contribute to lowering production costs.