परिचय
PEEK CNC Machining is revolutionizing industries by providing a high-performance solution for creating precise and durable parts. In this article, we will explore the benefits, applications, and intricacies of PEEK CNC machining. From its outstanding properties to its versatility in various sectors, this article will guide you through everything you need to know about PEEK CNC machining. Let’s dive into how PEEK is changing the game in manufacturing.
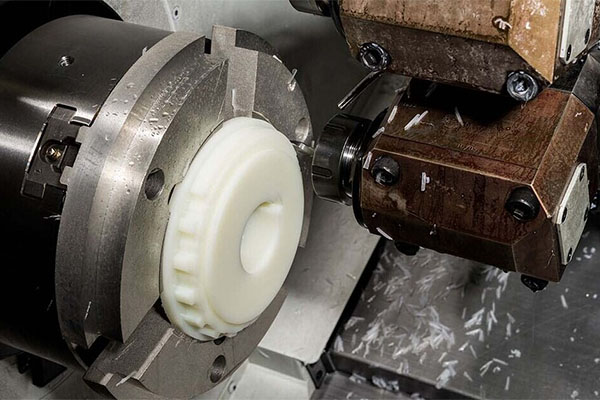
1. What is PEEK CNC Machining?
Polyetheretherketone (PEEK) is a high-performance thermoplastic that boasts remarkable strength, durability, and resistance to high temperatures and chemicals. But here’s the kicker: PEEK CNC machining takes these already impressive material qualities and elevates them by allowing manufacturers to create complex, precision parts that meet strict industry standards. This machining process involves using CNC (Computer Numerical Control) machines to precisely cut, drill, and finish PEEK parts, creating intricate components that would be impossible to achieve with traditional methods.
You might be wondering, why choose PEEK for CNC machining over other materials? The answer lies in PEEK’s unique combination of properties. It’s resistant to high temperatures, making it ideal for industries like aerospace and medical, where components are exposed to extreme conditions. Additionally, PEEK maintains its strength even at elevated temperatures, making it an excellent choice for high-stress applications. As the manufacturing industry seeks materials that offer both performance and efficiency, PEEK’s value becomes undeniable.
Let’s explore the essential benefits that make PEEK CNC machining stand out in the manufacturing world.
विशेषता | PEEK CNC Machining |
---|---|
Temperature Resistance | उत्कृष्ट |
Chemical Resistance | उत्कृष्ट |
Durability | उच्च |
Strength-to-Weight Ratio | उच्च |
2. What are the Key Benefits of PEEK CNC Machining?
Ready for the good part? PEEK CNC machining offers a host of benefits that make it a go-to material for manufacturers looking for precision, reliability, and performance. Here are some of the key advantages:
First off, PEEK’s strength-to-weight ratio is exceptional. This makes it an ideal choice for industries like aerospace and automotive, where lightweight materials are essential without sacrificing strength. Take the aerospace sector, for instance. PEEK parts are often used in aircraft components that need to be strong yet lightweight. This characteristic directly impacts fuel efficiency, making it an excellent choice for modern aircraft designs.
PEEK’s resistance to extreme temperatures is another game-changer. When exposed to high heat, PEEK maintains its mechanical properties, unlike other plastics that might deform. This property is crucial for industries like medical equipment manufacturing, where components often need to withstand sterilization processes that involve high temperatures.
Next, let’s talk about chemical resistance. PEEK doesn’t react with a wide range of chemicals, oils, and solvents, making it ideal for use in chemical processing equipment. This resistance not only improves the lifespan of components but also ensures reliability under harsh working conditions.
PEEK also boasts biocompatibility, making it an ideal material for medical applications, such as implants and prosthetics. Its ability to withstand harsh sterilization processes while remaining non-reactive with the human body is a significant advantage.
संपत्ति | फ़ायदा |
---|---|
Strength-to-Weight Ratio | Excellent for lightweight yet strong components |
Temperature Resistance | Maintains mechanical properties under high heat |
Chemical Resistance | Durable in harsh environments |
जैव | Ideal for medical implants and devices |
3. How Does PEEK CNC Machining Work?
What’s the real story behind PEEK CNC machining? The process begins with preparing the PEEK material, typically in the form of rods or sheets, which are then placed into CNC machines for precise shaping. CNC machines are programmed with exact specifications for the part being produced, ensuring that every cut, drill, and finish is executed with pinpoint accuracy.
The process involves several stages. First, cutting the PEEK material to the required size, followed by milling और drilling to create complex shapes and holes. The high precision of CNC machining ensures that even intricate designs can be replicated consistently, making it perfect for industries that require complex parts, such as aerospace or medical fields.
But wait, there’s more. The key to successful PEEK CNC machining lies in using the right cutting tools. PEEK is a tough material, so specialized tools are used to prevent wear and tear on the machinery. Coolants are often employed to manage heat during machining, ensuring that the PEEK material doesn’t melt or deform due to the heat generated by cutting tools.
Finally, the parts undergo finishing processes to enhance surface quality. This may include polishing or coating to achieve the desired finish and improve wear resistance. The result? A high-quality, precision-engineered part that meets industry standards.
कदम | Process |
---|---|
1 | Cutting the PEEK material to size |
2 | Milling and drilling for precision |
3 | Specialized cutting tools and cooling methods |
4 | Finishing processes for enhanced surface quality |
4. What Are the Common Applications of PEEK CNC Machining?
So, where does PEEK CNC machining fit in? PEEK’s versatility makes it an excellent material for a variety of industries. For example, in the aerospace industry, PEEK is used in the manufacture of parts that need to endure extreme temperatures and stress. Its lightweight yet durable nature is crucial for improving fuel efficiency and safety in aircraft.
PEEK is also widely used in the medical field for applications such as surgical instruments, implants, and prosthetics. PEEK’s biocompatibility and resistance to sterilization processes make it an ideal material for components that come into contact with the human body.
Additionally, PEEK CNC machining finds applications in the automotive industry, particularly in the production of high-performance parts that need to withstand wear and tear, such as bushings, bearings, and seals. The chemical resistance of PEEK ensures that automotive parts remain reliable under challenging conditions.
What’s the takeaway here? PEEK CNC machining is critical for manufacturing high-performance components that serve demanding industries. With its ability to withstand high temperatures, chemicals, and mechanical stress, PEEK is the material of choice in numerous applications across various sectors.
उद्योग | Common Application |
---|---|
एयरोस्पेस | Aircraft components for lightweight and strength |
चिकित्सा | Surgical instruments, implants, and prosthetics |
ऑटोमोटिव | High-performance parts like bearings and bushings |
Chemical Processing | Components exposed to harsh chemicals and solvents |
5. Why is PEEK Ideal for Medical Applications?
Let’s get to the heart of the matter—why is PEEK such a game-changer in the medical industry? One of the primary reasons PEEK stands out is its biocompatibility. It’s a material that doesn’t react negatively when it comes into contact with the human body, which is critical for implants and prosthetics. For example, PEEK is often used in spinal implants, where it must interact with bone and tissue without causing adverse reactions.
Moreover, PEEK’s strength and durability are essential for medical devices that need to perform consistently over time. For instance, it is used in surgical tools that must maintain their integrity after repeated sterilization cycles. The ability to endure autoclaving and other sterilization methods without losing its strength makes PEEK an ideal choice for medical applications that require both reliability and longevity.
But here’s the kicker: PEEK also has an excellent radiolucent property. This means it doesn’t interfere with X-rays or other medical imaging techniques. As a result, doctors can easily assess the condition of a PEEK implant without the need to remove it. This property makes PEEK particularly useful in applications like bone fixation devices, where the implant must remain in place for a long time but still allow for clear imaging.
संपत्ति | फ़ायदा |
---|---|
जैव | Ideal for implants and prosthetics |
Strength and Durability | Resists wear over time, even in demanding applications |
Radiolucency | Does not interfere with medical imaging |
Sterilization Resistance | Can withstand repeated sterilization without degradation |
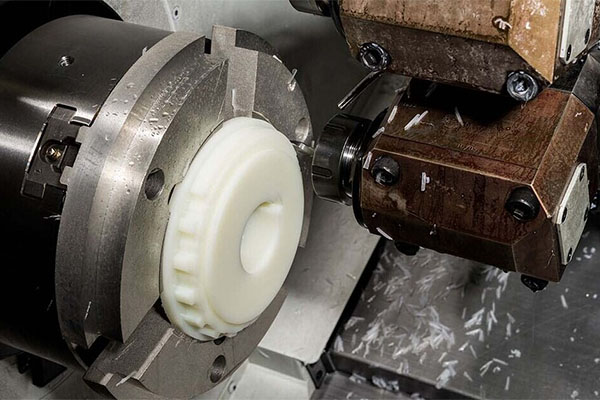
6. How Does PEEK CNC Machining Compare to Other Materials?
Ready to compare PEEK with other materials? PEEK stands out when compared to other plastics and metals due to its superior mechanical properties और resistance to extreme conditions. Take PTFE (Polytetrafluoroethylene), for example, which is also used in demanding applications. While PTFE is known for its excellent chemical resistance, it lacks PEEK’s mechanical strength and high-temperature resistance.
Similarly, अल्युमीनियम, a common metal used in CNC machining, might be lightweight and strong but cannot match PEEK in terms of heat and chemical resistance. This makes PEEK the material of choice when parts need to perform in environments where metals like aluminum would fail.
So, why choose PEEK over other materials? The combination of high strength, chemical resistance, temperature resistance, and biocompatibility makes PEEK the superior option for critical applications in industries like aerospace, medical, and automotive.
सामग्री | ताकत | Temperature Resistance | Chemical Resistance | जैव |
---|---|---|---|---|
PEEK | उच्च | उत्कृष्ट | उत्कृष्ट | Yes |
PTFE | मध्यम | कम | उत्कृष्ट | No |
अल्युमीनियम | मध्यम | कम | मध्यम | No |
टाइटेनियम | उच्च | उत्कृष्ट | मध्यम | No |
7. What Are the Challenges in PEEK CNC Machining?
PEEK CNC machining is not without its challenges, and understanding these difficulties can help manufacturers better prepare for the machining process. One major challenge is the tool wear that occurs when machining PEEK. PEEK is a tough material, and it can cause significant wear on traditional cutting tools. This can lead to increased maintenance costs and downtime if not managed properly. But here’s the kicker: using specialized cutting tools designed for high-performance plastics can help mitigate this issue. These tools, often made from carbide or ceramic materials, can withstand the demands of machining PEEK and extend tool life.
Another challenge is heat management. CNC machining generates a significant amount of heat, and PEEK, due to its high melting point, can deform if the heat is not controlled. To address this, manufacturers often use coolants or lubrication systems during the machining process. Cooling not only helps maintain the integrity of the material but also improves the quality of the finished product. However, choosing the right cooling system is critical, as some coolants can react with PEEK, potentially compromising its properties.
Lastly, machining accuracy can be challenging, especially when producing complex geometries. PEEK is a dense material, and small deviations in the machining process can lead to poor tolerances, affecting the final product’s performance. This is why it’s important to use advanced CNC machines with high precision capabilities, ensuring that parts meet stringent industry standards.
चुनौती | समाधान |
---|---|
उपकरण का घिसाव | Use specialized cutting tools like carbide or ceramic |
Heat management | Employ cooling systems or lubrication during machining |
Machining accuracy | Use advanced CNC machines with precision capabilities |
8. How to Choose the Right CNC Machine for PEEK Machining?
What’s the best CNC machine for machining PEEK? The answer depends on the complexity of the part and the precision required. CNC machines come in various types, from simple mills to highly specialized 5-axis machines. For basic CNC milling, a 3-axis CNC machine might suffice, especially for parts with simple geometries. However, when working with more complex shapes or when high precision is required, a 5-axis CNC machine is often necessary.
The machine’s rigidity is another critical factor when choosing a CNC machine for PEEK. PEEK is a strong material, and machining it can generate a significant amount of force. A machine with high rigidity helps ensure that the cutting tools maintain the correct position, reducing vibrations that can lead to errors in the machining process. A machine with high-speed spindles is also essential, as it allows for faster cutting, reducing overall machining time and improving productivity.
Additionally, the cooling system integrated into the machine should be considered. Some CNC machines are equipped with cooling systems specifically designed for high-performance plastics like PEEK. These cooling systems help manage the heat produced during the machining process, ensuring the material does not deform and maintaining part quality.
कारक | सोच-विचार |
---|---|
Complexity | 3-axis vs. 5-axis CNC machines |
Rigidity | Choose machines with high rigidity to prevent vibration |
रफ़्तार | High-speed spindles improve productivity |
Cooling | Integrated cooling systems to manage heat |
9. What Are the Costs Involved in PEEK CNC Machining?
Let’s talk about costs. PEEK CNC machining is not the cheapest option available, but it offers superior performance that can justify the higher initial expense. The costs involved can be broken down into several key areas:
First, material costs. PEEK is a high-performance polymer, and its price reflects that. Typically, PEEK costs more than standard plastics like PTFE or polycarbonate. However, its durability, resistance to chemicals, and high-temperature capabilities make it a worthwhile investment for industries that require these attributes.
Next, machining costs. The cost of machining PEEK is generally higher than that of machining more common materials due to its hardness and the tools required to process it. The use of specialized cutting tools, high-speed spindles, and advanced CNC machines all contribute to the increased machining costs. Additionally, the need for coolant and lubrication systems during machining can add to operational costs.
Lastly, labor and overhead costs should be factored in. While PEEK machining does require specialized knowledge, it also requires experienced machinists who can handle the material’s challenges and ensure the final part meets the required standards. The more complex the part, the higher the labor costs, as intricate machining requires more time and expertise.
Cost Category | Estimated Cost |
---|---|
माल की लागत | High due to the performance characteristics of PEEK |
Machining Costs | Higher due to specialized tools and advanced machinery |
श्रम लागत | Increased for skilled machinists handling complex parts |
Overhead Costs | Coolants, lubrication, and machine maintenance |
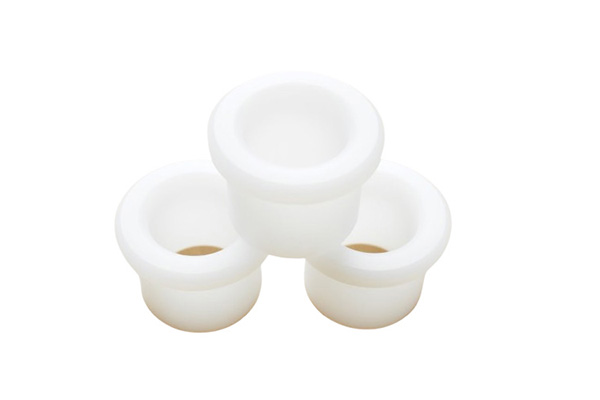
10. How Does CNC Machining Enhance the Properties of PEEK?
CNC machining is more than just a method for shaping PEEK; it actually enhances its properties. PEEK is known for its impressive strength, chemical resistance, and temperature stability, but CNC machining takes it a step further by ensuring these properties are perfectly realized in the final product.
One way CNC machining enhances PEEK is through precision cutting, which ensures that each part is manufactured to tight tolerances. This means that the final parts will have the desired properties without any inconsistencies, ensuring that the PEEK retains its strength and durability. The smooth surface finish achieved through CNC machining also plays a significant role in the material’s overall performance. A well-machined surface can reduce wear and tear, increase resistance to corrosion, and improve the part’s longevity.
Moreover, customization is a huge benefit of CNC machining. With the flexibility to design parts with complex geometries, CNC machining allows manufacturers to tailor PEEK parts to specific requirements, whether they need to fit into a small, precise space or withstand particular operational conditions. This level of customization ensures that PEEK is used to its full potential in various industries.
फ़ायदा | Enhancement |
---|---|
शुद्धता | Ensures tight tolerances for consistent material performance |
सतह खत्म | Smooth surfaces reduce wear and corrosion |
अनुकूलन | Allows for tailored geometries to meet specific needs |
11. What Are the Best Practices for Machining PEEK?
To achieve the best results in PEEK CNC machining, manufacturers must follow some best practices that help ensure efficiency, quality, and cost-effectiveness. Let’s explore some of these practices:
First, always use sharp cutting tools. Since PEEK is a tough material, dull tools can cause unnecessary heat buildup, which could lead to material deformation. Sharp tools ensure cleaner cuts and better surface finishes. Also, consider tool coatings that are specifically designed for high-performance polymers like PEEK, as these coatings can enhance tool life and performance.
Another best practice is to optimize cutting speeds and feed rates. Machining PEEK too quickly can lead to excessive heat generation, while machining too slowly can cause the process to take longer than necessary. Finding the optimal cutting speed and feed rate ensures that the material is machined efficiently without compromising its properties.
Lastly, don’t forget about heat management. PEEK can be sensitive to excessive heat, which is why using coolant or lubrication during machining is crucial. Proper cooling will not only prevent deformation but also extend the life of both the material and the cutting tools.
Best Practice | कारण |
---|---|
Sharp Cutting Tools | Reduces heat buildup and improves cutting quality |
Optimized Cutting Speeds | Balances efficiency and material integrity |
Heat Management | Prevents deformation and extends tool life |
12. What Industries Benefit the Most from PEEK CNC Machining?
So, where exactly is PEEK CNC machining most beneficial? PEEK’s unique combination of properties makes it a perfect fit for industries that require high-performance materials capable of withstanding harsh environments. Here are some key industries that benefit from PEEK CNC machining:
In the medical industry, PEEK is used to create implants, surgical instruments, and prosthetics. Its biocompatibility and ability to withstand repeated sterilization processes make it a go-to material for these critical applications. PEEK’s resistance to wear and corrosion also ensures the longevity of medical devices.
In the aerospace industry, PEEK’s lightweight yet durable nature is critical for manufacturing parts that need to perform under extreme conditions. From structural components to connectors and seals, PEEK parts help improve fuel efficiency and reduce maintenance costs.
The automotive industry also benefits from PEEK CNC machining, especially for high-performance parts like bushings, bearings, and seals. PEEK’s ability to withstand high temperatures and resist wear makes it ideal for these applications, ensuring that automotive components remain functional even in the harshest conditions.
उद्योग | आवेदन |
---|---|
चिकित्सा | Implants, surgical instruments, and prosthetics |
एयरोस्पेस | Structural components, connectors, and seals |
ऑटोमोटिव | Bushings, bearings, and seals |
13. What Innovations Are Being Made in PEEK CNC Machining?
PEEK CNC machining is constantly evolving as new technologies and innovations emerge. One notable advancement is the use of 3D printing technologies to create PEEK components. While traditional CNC machining is still the primary method for machining PEEK, 3D printing has opened new doors for producing complex parts with reduced material waste. This technology can be particularly useful for prototyping or creating small batches of parts.
Another innovation is the development of advanced cutting tools designed specifically for high-performance plastics like PEEK. These tools are more durable and capable of maintaining their sharpness longer, improving machining efficiency and reducing costs in the long run.
Additionally, the introduction of smart CNC machines that are equipped with sensors and data analytics capabilities is transforming the way PEEK parts are machined. These machines can monitor parameters such as temperature, cutting speed, and tool wear in real-time, allowing for better process control and ensuring consistent quality.
नवाचार | प्रभाव |
---|---|
3डी प्रिंटिंग | Enables complex designs with less material waste |
Advanced Cutting Tools | Improve efficiency and reduce tool wear |
Smart CNC Machines | Enhance process control and consistency |
14. What Are the Safety Considerations When Machining PEEK?
When machining PEEK, safety is paramount. The process involves the use of high-speed tools, which can pose risks if not handled properly. One safety concern is heat generation, which can cause burns or other injuries if not carefully managed. To mitigate this risk, operators should use cooling systems to keep temperatures under control and wear appropriate protective equipment, such as gloves and safety goggles.
Another safety consideration is dust and fumes. When cutting or grinding PEEK, it can produce fine dust particles that are harmful if inhaled. This is why it’s important to use dust extraction systems and to wear respiratory protection when machining PEEK. Proper ventilation and safety protocols should always be followed to minimize these risks.
Finally, machine operators should always be properly trained in handling high-performance materials like PEEK. The toughness of the material requires specialized knowledge, and using the right techniques and equipment is essential for maintaining both safety and product quality.
Safety Consideration | कार्रवाई |
---|---|
Heat Generation | Use cooling systems and protective gear |
Dust and Fumes | Use dust extraction systems and wear respiratory protection |
Machine Handling | Ensure operators are properly trained in PEEK machining |
15. How Can PEEK CNC Machining Contribute to Sustainability?
PEEK CNC machining is often viewed as a sustainable choice for manufacturing high-performance parts. Why? For one, PEEK’s durability ensures that the parts made from it last much longer than components made from other materials. This longevity means that parts don’t need to be replaced as frequently, leading to less waste in the long run.
Moreover, recycling opportunities for PEEK are increasing. While it’s still a relatively new area, research into recycling PEEK materials is ongoing, and it’s becoming easier to reuse scrap material from the machining process. This could lead to a future where PEEK components can be reused or repurposed, further reducing waste.
Additionally, energy efficiency in PEEK CNC machining is another contributing factor to its sustainability. Advanced machining techniques allow for reduced energy consumption during the machining process, helping to lower the carbon footprint associated with manufacturing.
Sustainability Aspect | फ़ायदा |
---|---|
Durability | Long-lasting parts that require fewer replacements |
Recycling | Opportunities for reusing scrap PEEK material |
ऊर्जा दक्षता | Reduced energy consumption during machining |
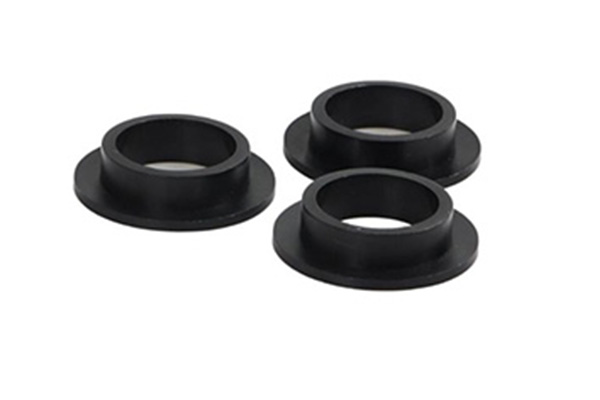
अक्सर पूछे जाने वाले प्रश्न अनुभाग
प्रश्न 1: What is PEEK?
PEEK (Polyetheretherketone) is a high-performance thermoplastic polymer known for its strength, durability, and resistance to high temperatures and chemicals.
प्रश्न 2: How does PEEK CNC machining work?
PEEK CNC machining involves using CNC machines to precisely cut, shape, and finish PEEK materials into components with high accuracy, suitable for various demanding industries.
प्रश्न 3: Why is PEEK used in the medical industry?
PEEK is biocompatible, strong, and resistant to sterilization processes, making it ideal for medical implants, surgical instruments, and prosthetics.
प्रश्न 4: What are the benefits of using PEEK in aerospace applications?
PEEK is lightweight, strong, and resistant to high temperatures, making it perfect for aerospace components where weight and strength are crucial for performance.
प्रश्न 5: What are the challenges of machining PEEK?
Machining PEEK can be difficult due to its toughness. Specialized tools and cooling methods are required to avoid tool wear and manage heat during the machining process.