Introduction to CNC Machining
Mesin CNC, or Computer Numerical Control machining, is the backbone of modern manufacturing, offering unparalleled precision, efficiency, and versatility. This advanced process involves the use of computers to control machine tools such as lathes, mills, routers, and grinders. CNC technology has revolutionized the way parts and products are created, automating processes that once required manual labor and expertise. In a world where manufacturing demands ever-increasing accuracy and speed, CNC machining provides a solution that meets these challenges head-on. Whether in aerospace, automotive, medical, or consumer products, CNC machining enables the production of parts that are both intricate and durable, with repeatable precision.
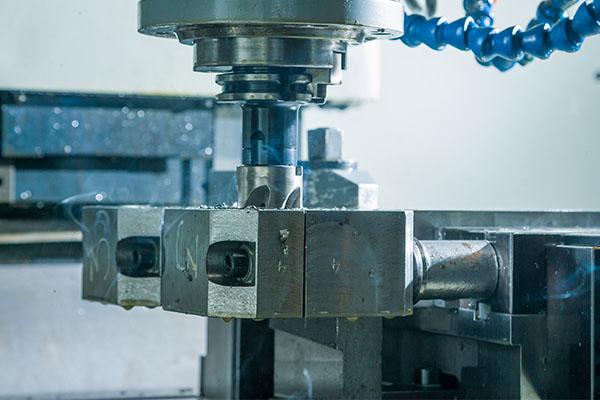
Historical Evolution of CNC Technology
The journey of CNC machining began in the 1940s and 1950s with the advent of the first numerical control machines. These machines were initially developed to help manufacturers automate processes such as drilling and milling, which were traditionally done manually. The breakthrough came in 1952 when the Massachusetts Institute of Technology (MIT) developed the first true CNC machine, which used punched paper tape to store machine instructions. This was a significant leap from the earlier mechanical methods.
By the 1960s, CNC technology began to gain traction in the manufacturing industry, thanks to advancements in computers and electronics. The introduction of computers allowed for more complex and precise control over machining processes. In the 1970s and 1980s, as microprocessors and digital controls became more affordable, CNC machines became widely accessible to manufacturers of all sizes. The development of CNC software made it possible to create digital models of parts and programs that controlled machining processes with even greater accuracy and efficiency.
Today, CNC machining has evolved into a highly sophisticated process, with machines capable of creating parts with micron-level precision. The integration of automation, advanced sensors, and artificial intelligence is further enhancing the capabilities of CNC machines, allowing them to operate autonomously and produce complex geometries that were once unimaginable.
Fundamental Principles of CNC Machining
At the core of CNC machining is the ability to translate a digital design into precise, physical parts. This process begins with the creation of a 3D computer-aided design (CAD) model, which serves as the blueprint for the part to be manufactured. Once the CAD design is complete, it is converted into a set of machine-readable instructions using computer-aided manufacturing (CAM) software. These instructions, known as G-code, dictate the movement of the CNC machine’s tool along different axes to shape the material into the desired part.
CNC machining relies on a range of machine tools, such as mills, lathes, and drills, which are capable of performing various operations like cutting, shaping, drilling, and grinding. Each machine tool is controlled by a computer, which receives the G-code and translates it into commands that control the movement of the machine’s toolhead. The machine’s tool is typically a rotating cutter, which removes material from the workpiece with high speed and precision.
The key to CNC machining’s success lies in its ability to perform these operations with extreme accuracy. A CNC machine can repeat the same process thousands of times, ensuring that each part produced is virtually identical to the last. The precision of CNC machining is what makes it ideal for industries that require exact specifications, such as aerospace and medical device manufacturing.
Key Components of CNC Machines
CNC machines are complex pieces of equipment made up of several key components that work together to ensure the precise operation of the system. These components include the machine control unit (MCU), the drive system, the feedback system, and the tooling.
- Machine Control Unit (MCU): The MCU is the brain of the CNC machine. It interprets the G-code instructions from the CAM software and converts them into signals that control the movement of the machine’s tool. The MCU is responsible for managing the entire machining process, ensuring that the tool moves to the correct position at the right time.
- Drive System: The drive system includes the motors and actuators that move the machine’s components. These components are responsible for the movement of the tool and the workpiece along the machine’s various axes. The drive system ensures that the tool moves with the precision required to meet the design specifications.
- Feedback System: The feedback system provides real-time information to the MCU about the position of the tool and the workpiece. It ensures that the machine is operating as expected and helps to correct any discrepancies during the machining process. Feedback systems often use encoders and resolvers to monitor the movement of the machine parts.
- Tooling: The tooling refers to the cutting tools and other accessories used in the machining process. These tools are designed to perform specific tasks, such as drilling, milling, or turning. The choice of tooling depends on the material being worked with and the complexity of the part being produced.
Together, these components enable CNC machines to operate with a high degree of accuracy, producing parts that meet strict tolerances and specifications.
Types of CNC Machines
CNC machines come in a variety of types, each designed for specific machining operations. Some of the most common types of CNC machines include CNC mills, CNC lathes, CNC routers, and CNC grinders. Each machine type has its unique capabilities and is suited for different manufacturing applications.
- CNC Mills: CNC milling machines are used for cutting and shaping materials like metal, plastic, and wood. The machine’s tool rotates to remove material from the workpiece, which is held in place by a vice or clamping system. CNC mills are versatile and can perform a wide range of operations, including drilling, boring, and tapping.
- CNC Lathes: CNC lathes are used to create cylindrical parts by rotating the workpiece while a stationary tool removes material. Lathes are ideal for turning operations, where the workpiece is shaped into precise cylindrical or conical forms. They are commonly used in industries like automotive and aerospace for producing parts such as shafts and bolts.
- CNC Routers: CNC routers are similar to milling machines but are typically used for cutting and shaping softer materials like wood, plastic, and foam. These machines are often used in industries like furniture manufacturing, signage, and packaging.
- CNC Grinders: CNC grinding machines are used to remove material from the workpiece using a rotating abrasive wheel. These machines are often used to achieve high-precision finishes on parts that require a smooth surface, such as engine components and aerospace parts.
Each type of CNC machine has its strengths and weaknesses, and the choice of machine depends on the specific requirements of the manufacturing process.
CNC Machining Processes
CNC machining encompasses a variety of processes designed to shape materials into finished products. Some of the most common machining processes include milling, turning, drilling, and grinding. Each process serves a unique purpose and is used to create parts with specific geometries and features.
- Milling: Milling is one of the most widely used CNC machining processes. In milling, the workpiece is held in place while a rotating cutter removes material from it. Milling machines can perform both horizontal and vertical operations, allowing them to create a wide variety of shapes and features.
- Turning: Turning is used to shape cylindrical parts by rotating the workpiece while a cutting tool removes material. CNC lathes are primarily used for turning operations, which are ideal for creating parts like shafts, rings, and cones.
- Drilling: Drilling is the process of creating holes in a workpiece using a rotating drill bit. CNC drilling machines are highly precise and can create holes with exact diameters and depths. This process is often used in conjunction with milling and turning operations.
- Grinding: Grinding is used to smooth the surface of a workpiece or to remove small amounts of material. CNC grinders are capable of producing parts with very fine finishes, making them ideal for applications in industries like aerospace and automotive manufacturing.
These machining processes can be used alone or in combination to create complex parts with precise dimensions.
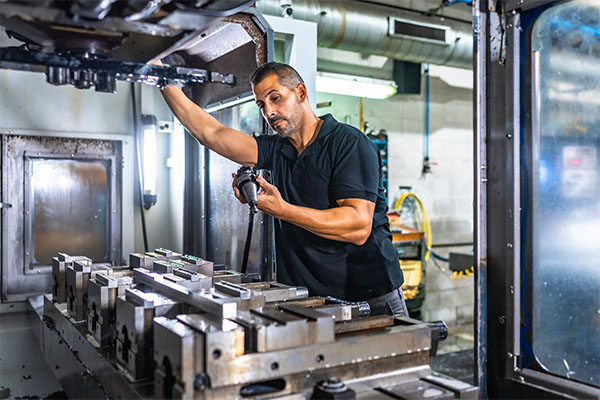
Bahan yang Digunakan dalam Pemesinan CNC
CNC machining is highly versatile and can be used to work with a wide range of materials. The choice of material depends on the part’s intended application, the desired properties, and the specific machining process being used. Some of the most common materials used in CNC machining include metals, plastics, and composites.
- Logam: Metals like aluminum, steel, titanium, and brass are commonly used in CNC machining. These materials are known for their strength, durability, and resistance to wear and corrosion. CNC machining can produce metal parts with tight tolerances and precise features, making metals ideal for industries like aerospace, automotive, and medical devices.
- Plastik: Plastics such as acrylic, polycarbonate, and nylon are also commonly used in CNC machining. These materials are lightweight, cost-effective, and easy to machine. CNC machining allows for the creation of plastic parts with intricate designs and smooth surfaces, making plastics ideal for applications in consumer products and electronics.
- Composites: Composite materials, such as carbon fiber and fiberglass, are increasingly being used in CNC machining. These materials offer a combination of strength and lightweight properties, making them ideal for applications in aerospace and automotive industries. CNC machining allows for precise shaping of composite materials, enabling the creation of complex parts with high strength-to-weight ratios.
The ability to work with such a wide variety of materials makes CNC machining a versatile option for manufacturers in virtually every industry.
Keuntungan dari Mesin CNC
Mesin CNC offers numerous advantages that make it a popular choice for modern manufacturing. Some of the most significant benefits of CNC machining include precision, repeatability, efficiency, and flexibility.
- Precision: CNC machines can produce parts with extremely tight tolerances, often within fractions of a millimeter. This high level of precision is essential for industries that require exact specifications, such as aerospace and medical device manufacturing.
- Repeatability: Once a CNC program has been created and tested, it can be used to produce an unlimited number of identical parts. This repeatability ensures that each part meets the same quality standards, making CNC machining ideal for mass production.
- Efficiency: CNC machines operate much faster than manual machines, reducing the amount of time required to produce a part. The automation of the machining process also minimizes the need for manual labor, which helps to lower costs and increase production speed.
- Flexibility: CNC machines can be easily reprogrammed to produce different parts, making them highly versatile. This flexibility allows manufacturers to switch between different products without needing to invest in new equipment.
These advantages have made CNC machining the preferred choice for many industries, offering manufacturers a cost-effective and efficient way to produce high-quality parts.
Challenges and Limitations
Despite its many benefits, CNC machining does have its challenges and limitations. Some of the most common issues associated with CNC machining include high initial costs, limited material compatibility, and the need for skilled operators.
- High Initial Costs: CNC machines are expensive to purchase and set up. Additionally, the software and training required to operate these machines can add to the overall cost. However, the long-term benefits, such as increased efficiency and precision, often outweigh these initial expenses.
- Limited Material Compatibility: While CNC machining is versatile, it is not suitable for all materials. Some materials, such as certain ceramics or composite materials, can be difficult to machine with traditional CNC tools. However, advances in tooling and technology are continuously improving the ability to work with a broader range of materials.
- Skilled Operators Required: Operating a CNC machine requires specialized knowledge and training. Skilled operators are needed to set up the machines, program the tools, and monitor the machining process. This can increase the cost of labor and may require ongoing training to keep up with technological advancements.
Despite these challenges, CNC machining remains one of the most effective and efficient methods for producing high-quality parts.
Applications Across Industries
CNC machining is used across a wide range of industries due to its precision, versatility, and efficiency. Some of the most common industries that rely on CNC machining include aerospace, automotive, medical devices, and consumer electronics.
- Ruang angkasa: CNC machining is essential in the aerospace industry, where parts need to meet strict safety and performance standards. CNC machines are used to manufacture components like turbine blades, engine parts, and structural components with tight tolerances and high strength-to-weight ratios.
- Otomotif: The automotive industry uses CNC machining to produce components like engine blocks, transmission parts, and suspension components. CNC machining allows for the production of parts with high precision and low cost, making it ideal for mass production.
- Medical Devices: In the medical field, CNC machining is used to produce surgical instruments, implants, and diagnostic equipment. The precision of CNC machining is critical in medical device manufacturing, where small tolerances can have a significant impact on performance and safety.
- Elektronik Konsumen: CNC machining is also used in the production of parts for consumer electronics, including casings, connectors, and components for devices like smartphones, tablets, and computers.
The versatility of CNC machining allows it to serve a broad range of industries, offering manufacturers the ability to create high-quality, customized parts for a variety of applications.
Design Considerations for CNC Machining
Designing a part for CNC machining requires careful consideration of factors like material selection, geometry, tolerances, and the specific machining process to be used. By optimizing the design for CNC machining, manufacturers can reduce production time and costs while ensuring that the final product meets all specifications.
- Material Selection: The choice of material has a significant impact on the machining process. Some materials are easier to machine than others, and the material’s hardness, strength, and thermal properties can affect tool wear and machining time.
- Geometry: The geometry of the part plays a crucial role in the CNC machining process. Parts with complex shapes or intricate features may require special tooling or longer machining times. It’s important to design parts that are easy to machine while still meeting the functional requirements.
- Toleransi: Tight tolerances require greater precision in the machining process and may result in longer production times. It’s essential to balance the desired tolerance with the overall design and cost constraints.
- Machining Process: Different machining processes have different capabilities and limitations. Designers must choose the most appropriate process for the part, taking into account factors such as material type, complexity, and production volume.
By carefully considering these factors, manufacturers can create parts that are optimized for CNC machining, ensuring high-quality results and efficient production.
Quality Control and Precision in CNC Machining
Quality control is critical in CNC machining to ensure that each part meets the required specifications and tolerances. CNC machines are highly accurate, but it’s essential to monitor the machining process to catch any potential errors or deviations.
- Inspection Techniques: Various inspection techniques are used to verify the quality of CNC-machined parts. These include visual inspection, dimensional measurement, and non-destructive testing. Advanced measurement tools like coordinate measuring machines (CMMs) are often used to check the accuracy of parts.
- Standards and Certifications: To ensure that parts meet industry standards, CNC machining facilities often adhere to certifications such as ISO 9001. These certifications ensure that the facility follows established quality management practices and meets stringent manufacturing standards.
- Feedback Loops: Feedback loops are built into the CNC machining process to monitor tool wear, machine performance, and material conditions. These loops ensure that any deviations are caught early and corrected before they affect the final product.
By implementing effective quality control processes, manufacturers can ensure that CNC-machined parts meet the highest standards of precision and reliability.
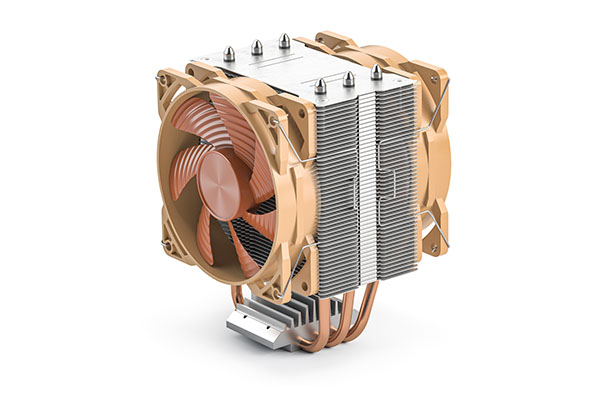
Future Trends in CNC Machining
CNC machining is an ever-evolving field, with continuous advancements in technology and processes. Some of the most promising future trends in CNC machining include the integration of automation, artificial intelligence, and advanced materials.
- Automation: The use of robotic arms and automated loading and unloading systems is increasing in CNC machining. These automation systems help to reduce human error, increase production speed, and lower labor costs.
- Artificial Intelligence: AI is being integrated into CNC machines to optimize machining processes, predict tool wear, and automate decision-making. AI-powered CNC machines can analyze data in real-time to adjust machining parameters for optimal performance.
- Advanced Materials: CNC machining is becoming increasingly capable of working with advanced materials like carbon fiber, ceramics, and composite materials. These materials offer superior performance but require specialized machining techniques.
As technology continues to advance, CNC machining will become even more efficient, accurate, and versatile, opening up new possibilities for manufacturers in a wide range of industries.
Selecting a CNC Machining Service Provider
Memilih yang tepat CNC machining service provider is critical to ensuring the quality and cost-effectiveness of your manufacturing process. When selecting a provider, consider factors like capabilities, certifications, experience, and customer service.
- Kemampuan: Ensure that the provider has the capabilities to meet your specific requirements. This includes the types of materials they can work with, the machining processes they offer, and the tolerances they can achieve.
- Certifications: Look for CNC machining service providers that are certified to industry standards such as ISO 9001. These certifications demonstrate that the provider follows strict quality control processes and meets industry standards.
- Experience: A service provider with experience in your industry will be better equipped to handle the unique challenges of your project. Look for a provider with a proven track record of success in your sector.
- Customer Service: Strong customer service is essential for a smooth and efficient manufacturing process. Choose a provider that communicates effectively, offers support throughout the process, and is responsive to your needs.
By carefully evaluating potential CNC machining service providers, you can ensure that your manufacturing process is efficient, cost-effective, and produces high-quality parts.
Kesimpulan
CNC machining is a powerful and versatile manufacturing technology that offers unmatched precision, efficiency, and flexibility. With its ability to produce parts from a wide variety of materials, CNC machining is essential in industries ranging from aerospace to medical devices. By understanding the principles of CNC machining, the different types of machines and processes involved, and the design considerations required for success, manufacturers can take full advantage of this technology to create high-quality products. As CNC machining continues to evolve, its potential to revolutionize manufacturing will only grow, offering new opportunities for innovation and advancement across industries.

Tanya Jawab Umum
What is CNC machining?
CNC machining is a manufacturing process where a computer controls the movement of machine tools to create precise parts. It is used to machine materials like metals, plastics, and composites into finished products.
Industri apa yang menggunakan permesinan CNC?
CNC machining is used across various industries, including aerospace, automotive, medical devices, and consumer electronics, to produce parts with high precision and complex geometries.
What are the benefits of CNC machining?
The main benefits of CNC machining include high precision, repeatability, efficiency, and the ability to work with a wide range of materials.
Can CNC machining be used for prototyping?
Yes, CNC machining is commonly used for prototyping due to its ability to quickly produce high-quality, accurate parts.
What is the difference between CNC milling and CNC turning?
CNC milling uses a rotating tool to remove material from a stationary workpiece, while CNC turning rotates the workpiece while a stationary tool removes material. Both processes are used to create different types of parts.