Perkenalan
Copper CNC machining has become a crucial service in many industries due to the unique properties of copper. This versatile metal, known for its conductivity, corrosion resistance, and ease of machining, is essential in creating high-precision, durable parts. If you’re in need of custom copper parts for your business, understanding the ins and outs of copper CNC machining can help you make informed decisions and ensure you get the best results.
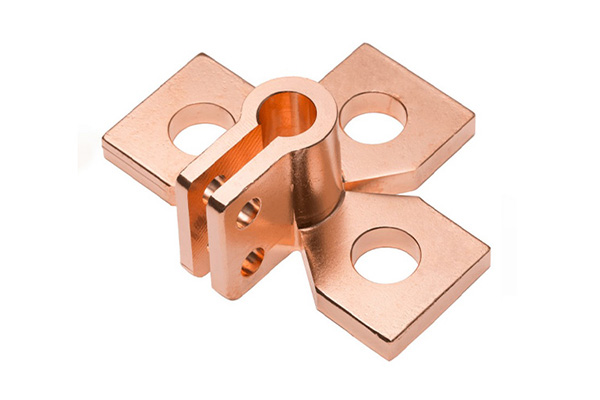
1. What is Copper CNC Machining?
Copper CNC machining refers to the process of using computer-controlled machines to shape and fabricate copper into specific parts and components. This method allows for precision cutting, drilling, and milling, ensuring that the parts are made to exact specifications.
Ready for the good part? The machining of copper presents unique challenges due to its material properties. Unlike other metals, copper is relatively soft, which can cause it to deform easily. However, when properly machined, copper provides excellent conductivity, making it a popular choice in the electrical and electronics industries.
In CNC machining, copper is typically fed into a machine that uses a cutting tool to remove material. The process is highly automated, and the exact movements of the tool are controlled by a computer program. This allows for consistent, high-quality results, even for complex or intricate designs.
Copper’s malleability also makes it easier to machine compared to harder metals like steel. However, this can lead to issues like burrs or excessive wear on tools. As a result, the selection of cutting tools and machining parameters is critical in achieving optimal results.
Incorporating the right techniques and using specialized tools can help mitigate some of the challenges associated with copper machining. The result is a high-quality, precise copper part that is ready for use in a variety of applications.
Proses | Keterangan |
---|---|
Copper Machining | Using computer-controlled tools to cut and shape copper |
Challenges | Copper’s softness can lead to tool wear and deformation |
Manfaat | Copper provides excellent conductivity and is easy to machine |
2. Why Choose Copper for CNC Machining?
When it comes to choosing a material for CNC machining, copper stands out for several reasons. One of the primary benefits of copper is its excellent electrical conductivity. This makes it an ideal material for electrical components such as connectors, wires, and circuit boards.
But here’s the kicker—copper is also highly corrosion-resistant. It doesn’t rust like steel or other metals, making it perfect for applications where durability is key. Whether it’s used in outdoor settings or in harsh environments, copper parts can withstand the elements, offering a long-lasting solution.
In addition, copper is known for its high thermal conductivity, which is important in applications where heat dissipation is crucial, such as in heat exchangers or electrical components. This property helps prevent overheating, ensuring the reliability and performance of devices or machinery that use copper components.
Another major reason to choose copper for CNC machining is its versatility. Copper is highly malleable, allowing it to be formed into a wide range of shapes and sizes. This makes it suitable for a variety of applications, from small electronic components to large machinery parts.
Moreover, copper’s ease of machining reduces manufacturing costs. Since it’s a relatively soft material, it requires less force and energy to machine, making the process more cost-effective compared to harder metals.
Property | Keuntungan |
---|---|
Electrical Conductivity | Ideal for electrical components like connectors and wires |
Corrosion Resistance | Copper doesn’t rust, ensuring long-lasting durability |
Thermal Conductivity | Prevents overheating in applications like heat exchangers |
Malleability | Easily formed into various shapes, reducing manufacturing costs |
3. What Are the Different Types of Copper Used in CNC Machining?
Copper comes in several different types, each with its own set of properties and uses. The most commonly used types of copper in CNC machining are pure copper and copper alloys.
So, what’s the real story? Pure copper, known as C110, is one of the most widely used forms in CNC machining. It has high conductivity and is often used in electrical applications where optimal performance is required. C110 copper is also highly ductile, which means it can be easily shaped without cracking or breaking.
However, pure copper isn’t always the best choice for every application. Copper alloys, such as C260 brass and C360, offer a balance between conductivity, strength, and machinability. These alloys are often used when a higher level of durability is needed, such as in mechanical parts or heavy-duty applications.
Copper alloys can be created by mixing copper with other metals, such as zinc, tin, or nickel. The result is a material that offers enhanced strength and resistance to wear, without compromising too much on conductivity. These alloys are often chosen for applications in the automotive, aerospace, and manufacturing industries.
Each type of copper has its strengths and weaknesses, and the choice of material depends on the specific requirements of the project. Understanding the differences between these types can help you make the best decision for your CNC machining needs.
Copper Type | Composition | Best Use |
---|---|---|
Pure Copper (C110) | 99.9% copper | Electrical components, high conductivity |
Copper Alloy (C260 Brass) | Copper and zinc | Mechanical parts, increased strength |
Copper Alloy (C360) | Copper and zinc | Precision machining, durability |
4. How Does CNC Machining Work for Copper Parts?
CNC machining for copper parts follows the same basic principles as CNC machining for other metals. The main difference is the need to account for copper’s specific properties, such as its softness and tendency to work-harden.
What’s the real story? The process begins by programming a CNC machine with a specific design for the copper part. The machine is then set up with the appropriate cutting tools, and the copper material is fed into the machine. As the machine cuts away material, it shapes the copper into the desired form.
One of the challenges with copper is that it tends to work-harden when exposed to high temperatures, which can make machining more difficult. This means that cooling methods, such as using cutting fluids or air jets, are often employed to keep the material from hardening during the machining process.
Another important consideration is tool selection. Since copper is relatively soft, it’s important to use tools that are designed to handle the material’s specific characteristics. High-speed steel (HSS) and carbide tools are commonly used for machining copper, as they provide the necessary strength and durability to cut through the material effectively.
It’s also essential to maintain the right cutting speed and feed rate. Too fast of a speed can cause the copper to heat up and work-harden, while too slow of a speed can result in excessive tool wear and a poor-quality finish.
Melangkah | Keterangan |
---|---|
Langkah 1 | Program CNC machine with copper part design |
Langkah 2 | Set up cutting tools and load copper material |
Langkah 3 | Machine copper to desired shape, using cooling methods |
Langkah 4 | Ensure proper cutting speed and feed rate to prevent issues |
5. What Are the Key Benefits of Copper CNC Machining?
Copper CNC machining offers a range of benefits that make it a preferred choice for a variety of applications. First and foremost, copper’s high conductivity makes it ideal for electrical and electronic components. Whether it’s a connector, switch, or circuit board, copper’s conductivity ensures optimal performance.
Ready for the good part? Copper also offers excellent corrosion resistance. Unlike steel, which can rust over time, copper forms a protective patina that shields it from the elements. This makes it perfect for applications in outdoor or harsh environments where exposure to moisture and air is common.
Copper’s malleability is another significant benefit. It can be easily shaped into complex designs without cracking or breaking. This allows manufacturers to create intricate, high-precision parts that would be difficult to achieve with other materials.
In addition, copper is relatively easy to machine compared to harder metals. Its softness means that less energy is required to cut and shape it, which can result in lower manufacturing costs. Furthermore, the ability to machine copper at a high level of precision ensures that parts are made to exact specifications, reducing the need for post-machining work.
Finally, copper’s ability to dissipate heat efficiently makes it an excellent choice for components that require thermal management, such as heat exchangers, radiators, and cooling systems.
Keuntungan | Keterangan |
---|---|
High Conductivity | Ideal for electrical and electronic components |
Corrosion Resistance | Forms a protective patina to prevent rust |
Malleability | Easily shaped into complex designs without cracking |
Cost-Effective | Requires less energy to machine compared to harder metals |
Pembuangan Panas | Excellent thermal management properties for cooling systems |
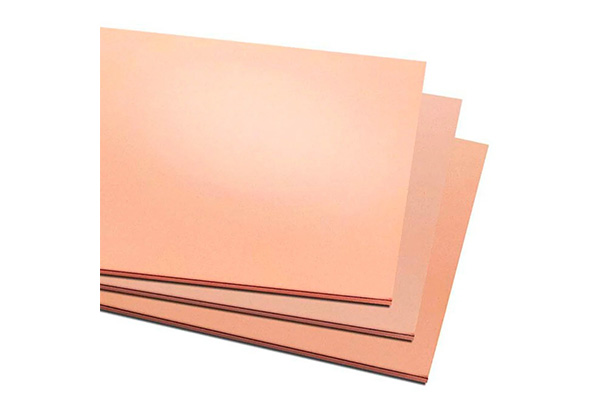
6. How Do You Achieve Precision with Copper CNC Machining?
Achieving precision in copper CNC machining is no simple task. Copper, being a relatively soft material, can be challenging to work with because it tends to deform easily under pressure. So, what’s the real story? The key to ensuring precise copper machining lies in the right combination of cutting tools, machine settings, and operator skill.
First, let’s talk about the importance of the cutting tools. Since copper is a softer material compared to metals like steel, it’s crucial to choose the right tools to avoid excessive wear and tear. Carbide tools, for example, are commonly used in copper machining. These tools are durable, heat-resistant, and provide a smooth finish, which is essential when machining copper to tight tolerances.
Next up is the cutting speed. Too fast, and the copper will overheat, leading to work hardening and tool wear. Too slow, and you risk an inefficient process. The ideal cutting speed for copper typically falls between 100 and 200 meters per minute, depending on the tool and machine.
The feed rate also plays a crucial role in maintaining precision. A slower feed rate allows for better control over the cutting process and minimizes tool deflection, which can lead to dimensional inaccuracies. Alongside this, cooling methods are employed to reduce heat buildup during machining. The use of coolants or air jets is common in copper machining, ensuring that the material doesn’t work-harden during the cutting process.
Lastly, CNC machines themselves are critical to achieving precision. Advanced machines with high-quality controls allow for tighter tolerances and a higher level of accuracy in the final product.
Faktor | Importance |
---|---|
Cutting Tools | Carbide tools are commonly used to avoid wear and ensure smooth finishes |
Cutting Speed | Ideal speeds range from 100-200 meters per minute to avoid overheating |
Feed Rate | A slower feed rate minimizes tool deflection and ensures accuracy |
Cooling Methods | Using coolants or air jets prevents work hardening during machining |
CNC Machine Quality | High-quality machines offer better precision and tighter tolerances |
7. What Are the Best Practices for Copper CNC Machining?
When it comes to copper CNC machining, there are several best practices that can ensure high-quality results and optimize the efficiency of the process. These practices are essential in mitigating common issues, such as tool wear, material deformation, and low production rates. Ready for the good part? By following these best practices, manufacturers can save both time and money.
First, the proper selection of cutting tools is vital. As we mentioned earlier, carbide tools are typically the best choice for machining copper, thanks to their durability and sharpness. It’s also essential to regularly inspect tools for wear. Worn-out tools can lead to poor-quality parts and increased scrap rates.
Next, managing heat is crucial when machining copper. Copper’s tendency to work-harden makes it susceptible to heat buildup, which can cause it to become brittle and difficult to machine. This is where cooling methods come into play. Using water-based coolants or air jets helps dissipate heat, keeping the material soft and easy to work with.
In addition to this, maintaining the correct cutting parameters—such as the cutting speed, feed rate, and depth of cut—is essential. For copper, the cutting speed should be kept moderate, and the feed rate should be adjusted to avoid excessive material buildup on the cutting tool. This ensures smooth cutting and high-quality finishes.
Another best practice is to ensure proper chip removal. Copper, being a relatively soft material, tends to form chips that can clog up the machine. Regular chip removal prevents these blockages, ensuring that the cutting process remains smooth and consistent.
Best Practice | Explanation |
---|---|
Cutting Tool Selection | Use carbide tools and inspect them regularly for wear |
Heat Management | Use water-based coolants or air jets to prevent work hardening |
Cutting Parameters | Adjust cutting speed, feed rate, and depth of cut to suit copper |
Chip Removal | Regularly remove copper chips to prevent clogging and ensure smooth operation |
8. How Does Copper CNC Machining Compare to Other Machining Methods?
Copper CNC machining offers numerous advantages over other machining methods, especially when it comes to precision and the ability to produce complex parts. But here’s the kicker—while CNC machining is incredibly efficient, it’s not the only option for working with copper. So, what’s the real story?
When compared to traditional machining methods, CNC machining stands out for its ability to produce high-precision parts with minimal manual labor. Traditional machining methods, such as manual turning or milling, often require skilled operators to guide the tool, leading to more variability in the final product. CNC machines, on the other hand, are automated and programmed, ensuring consistency and precision.
But CNC machining isn’t always the best option for every application. In some cases, other machining methods like die casting or injection molding may be more appropriate, especially when producing large quantities of parts with a simpler design. These methods can be more cost-effective in high-volume production scenarios because they eliminate the need for extensive setup times.
However, when it comes to custom or low-volume runs of complex copper parts, CNC machining is the clear winner. Its versatility allows manufacturers to produce intricate designs that would be difficult or impossible to achieve with traditional machining. Additionally, CNC machines can handle a variety of copper alloys, making them suitable for diverse applications across different industries.
Method | Advantage | Disadvantage |
---|---|---|
Mesin CNC | High precision and versatility for custom parts | Higher setup costs for low-volume runs |
Traditional Machining | Lower setup costs for simple designs | Requires skilled operators and can be less precise |
Pengecoran Mati | Cost-effective for high-volume production | Not suitable for complex designs or custom parts |
9. What Industries Use Copper CNC Machining?
Copper CNC machining is used across a wide variety of industries, thanks to the unique properties of copper. So, why is copper so widely used? The material’s excellent electrical and thermal conductivity, combined with its corrosion resistance, makes it essential in many industries, particularly those requiring high precision and reliability.
One of the largest industries that rely on copper CNC machining is the electrical industry. Copper is the go-to material for wiring, connectors, and other electrical components due to its superior conductivity. CNC machining ensures that these parts are produced with high precision, which is critical for the functionality of electrical devices.
The automotive industry also makes use of copper CNC machining, particularly for parts that need to conduct electricity or manage heat, such as radiators and electrical contacts. Copper’s durability and thermal conductivity are valuable in these applications.
The aerospace industry is another major user of copper CNC machining. Parts like heat exchangers, fuel lines, and electrical connectors often need to be made from copper to ensure optimal performance in extreme conditions. The precision and ability to handle complex geometries in CNC machining make it ideal for these applications.
Industry | Application |
---|---|
Electrical | Wiring, connectors, electrical components |
Otomotif | Radiators, electrical contacts, heat management parts |
Ruang angkasa | Heat exchangers, fuel lines, electrical connectors |
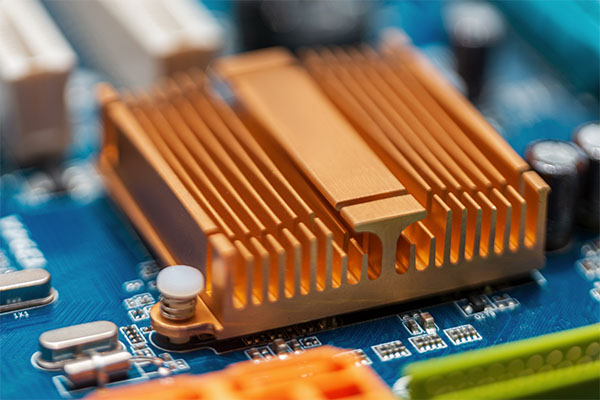
10. How to Ensure the Quality of Copper CNC Machined Parts?
Ensuring the quality of copper CNC machined parts is a critical step in the manufacturing process. So, what’s the real story? Quality assurance starts right from the initial design phase and continues through to the final inspection of the parts.
First, the design phase plays a crucial role in the quality of the final product. Using precise CAD drawings and ensuring that the design is optimized for machining can prevent many common issues later on in the process. Inadequate design details or incorrect tolerances can lead to poorly machined parts that don’t meet the required specifications.
Once the copper material is machined, it’s important to perform regular inspections throughout the process. This includes checking for dimensional accuracy, surface finish, and other critical parameters. Using advanced measuring tools, such as coordinate measuring machines (CMM), can help ensure that the parts meet the required tolerances.
Another important quality control step is testing the copper parts for functionality. For example, if the part is intended for electrical use, testing the conductivity is crucial. Similarly, parts that will be exposed to high temperatures should be tested for thermal conductivity and heat resistance.
By integrating quality control measures at every stage of production, manufacturers can ensure that the final copper CNC machined parts meet the necessary performance standards.
Quality Control Step | Keterangan |
---|---|
Design Phase | Ensure accurate CAD drawings and proper design details |
Inspection | Regular checks for dimensional accuracy and surface finish |
Testing | Test for functionality, such as conductivity and heat resistance |
11. What Are the Challenges in Copper CNC Machining?
While copper is a great material for CNC machining, it’s not without its challenges. One of the primary difficulties in copper CNC machining is managing the material’s softness. Copper is relatively soft compared to other metals, which makes it more prone to deformation during machining.
But here’s the kicker—copper’s softness also makes it more difficult to maintain precision, especially when working with thin or intricate parts. This means that CNC operators must carefully manage cutting speeds, feed rates, and cooling methods to prevent any deformation or tool wear.
Another challenge is work hardening. Copper tends to harden when it is exposed to high heat during machining. This can make it more difficult to machine over time, and if not managed properly, it can lead to tool damage or even part failure. To prevent work hardening, it’s important to maintain proper cooling and use the right cutting tools.
Lastly, chip removal can be a challenge when machining copper. Since copper is soft and tends to produce long chips, these chips can get caught in the machine and cause blockages. This can lead to delays and additional maintenance if not properly managed.
Challenge | Larutan |
---|---|
Softness | Use appropriate cutting tools and manage cutting parameters |
Work Hardening | Apply proper cooling and select suitable cutting speeds |
Chip Removal | Regularly remove chips to prevent machine blockages |
12. How Much Does Copper CNC Machining Cost?
The cost of copper CNC machining can vary widely depending on several factors, including the complexity of the part, the type of copper used, and the quantity of parts being produced. Ready for the good part? The more complex the part, the higher the cost will be due to the increased machining time and the need for specialized tools.
For simple copper parts, the cost tends to be relatively low. However, for more complex components with intricate designs, the cost increases. The price can also be affected by the material itself. For example, high-purity copper tends to be more expensive than copper alloys due to its superior conductivity.
Other factors that influence cost include the number of parts being ordered. For large orders, manufacturers can often offer volume discounts, making the cost per part lower. On the other hand, low-volume or custom runs may have a higher per-part cost due to the increased setup time and tooling requirements.
When budgeting for copper CNC machining, it’s essential to consider all of these factors. By working with a reliable CNC machining service, you can ensure that you’re getting the best value for your investment.
Cost Factor | Explanation |
---|---|
Complexity | More complex parts require more time and specialized tools |
Bahan | High-purity copper is more expensive than copper alloys |
Quantity | Larger orders typically result in lower per-part costs |
13. How to Choose the Right Copper CNC Machining Service?
Choosing the right copper CNC machining service can make a significant difference in the quality and cost of your final product. So, what’s the real story? The key to selecting the best service provider is understanding your specific needs and looking for a company that aligns with them.
First, consider the company’s experience with copper machining. Copper is a specialized material, and working with a provider that has experience machining copper parts can help ensure the quality and precision of your components. A company with experience will be familiar with the challenges associated with copper and can help guide you through the process.
Next, look at the company’s equipment and technology. CNC machining has advanced significantly in recent years, and a company with the latest equipment will be able to provide higher precision and faster turnaround times. Additionally, modern machines allow for greater flexibility in terms of the types of copper alloys that can be machined.
Finally, consider the company’s customer service and communication. A good CNC machining service will be responsive to your needs, transparent about pricing, and willing to collaborate with you throughout the process. Look for companies with strong reputations and positive customer reviews.
Faktor | Importance |
---|---|
Experience | A company with experience in copper machining ensures high-quality parts |
Equipment | Advanced machinery results in better precision and faster turnaround |
Customer Service | Responsive communication ensures a smooth collaboration |
14. What is the Lead Time for Copper CNC Machining Services?
Lead time for copper CNC machining varies depending on several factors, including the complexity of the part, the type of material used, and the volume of the order. Generally, the lead time for custom copper parts ranges from a few days to several weeks.
Ready for the good part? Lead times can be shortened with effective communication and preparation. If you provide your CNC machining service with accurate specifications and clear CAD drawings, they can prepare for your order in advance, reducing delays. Additionally, working with a supplier who has access to the necessary copper material and a reliable supply chain can also help minimize wait times.
For small orders or prototyping, lead times are typically shorter. However, for large orders that require custom tooling or more complex designs, the lead time may be longer. It’s always a good idea to request an estimated timeline upfront so that you can plan accordingly.
Lead Time Factor | Explanation |
---|---|
Complexity | More intricate designs require longer lead times |
Material Availability | Access to copper materials can affect lead time |
Order Volume | Larger orders may take longer to process |
15. How Can You Order Custom Copper CNC Machined Parts?
Ordering custom copper CNC machined parts is a straightforward process, but it’s important to provide your service provider with all the necessary details upfront. Here’s how you can get started.
First, you’ll need to supply your CNC machining service with your part specifications. This typically includes providing a detailed CAD drawing, specifying material requirements (e.g., pure copper or alloy), and outlining the desired finish or tolerance levels.
Once your specifications are clear, the service provider will assess the feasibility of the project and provide you with an estimate, including pricing, lead times, and any additional details. Be sure to review the estimate thoroughly and communicate any changes or adjustments as needed.
Finally, once everything is agreed upon, the CNC machining service will begin the production process. During production, it’s a good idea to maintain communication with the service provider to address any potential issues or questions that arise.
Order Step | Keterangan |
---|---|
Provide Specifications | Send detailed CAD drawings and material requirements |
Receive Estimate | Review pricing, lead times, and any additional details |
Begin Production | Maintain communication throughout the production process |
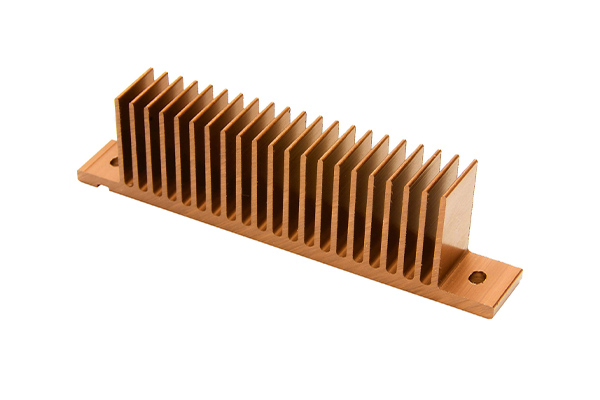
Bagian FAQ
Pertanyaan 1: What is Copper CNC Machining?
Copper CNC machining is the process of using computer-controlled tools to shape and fabricate copper into specific parts. It is widely used for creating high-precision components for industries like electronics, automotive, and aerospace.
Pertanyaan 2: How does CNC Machining work for Copper?
CNC machining for copper involves programming a CNC machine with the design of the copper part. The machine then uses cutting tools to remove material, shaping the copper into the desired form, while cooling methods prevent work-hardening.
Pertanyaan 3: Why is Copper preferred for CNC machining?
Copper is preferred for CNC machining due to its excellent electrical conductivity, corrosion resistance, and malleability. These properties make it ideal for electrical components, as well as for applications that require heat dissipation.
Pertanyaan 4: How do you ensure precision in Copper CNC machining?
Precision in copper CNC machining is achieved through careful programming, tool selection, and maintaining the right cutting speed and feed rate. Cooling methods also play a crucial role in maintaining accuracy during the machining process.
Pertanyaan 5: How much does Copper CNC machining cost?
The cost of copper CNC machining varies depending on factors like the complexity of the part, the material used, and the manufacturing process. Generally, copper machining is cost-effective compared to harder metals due to its malleability and ease of machining.