Perkenalan
In the world of manufacturing, achieving precision is paramount, especially when working with complex projects. Pemesinan presisi CNC offers manufacturers the ability to create intricate designs with remarkable accuracy. But mastering CNC machining, especially for intricate and complex projects, requires more than just having the right equipment. It demands a deep understanding of machine functionality, design considerations, material choices, and the best techniques for fine-tuning precision. Ini kesepakatannya—if you want to take your machining capabilities to the next level, mastering these elements will make a world of difference in your end products.
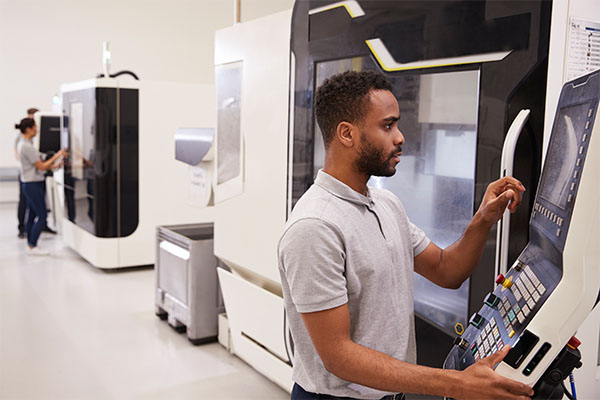
1. What is CNC Precision Machining?
Defining CNC Precision Machining
CNC (Computer Numerical Control) precision machining refers to the automated control of machining tools such as drills, lathes, and mills using computers. It allows for high levels of accuracy, ensuring that complex parts are made with exact dimensions and tight tolerances. Anda mungkin bertanya-tanya, how does it achieve such fine precision? The answer lies in the combination of digital control and advanced machinery, which makes it possible to produce designs that would be almost impossible to replicate manually.
CNC vs. Conventional Machining
In contrast to traditional machining, which requires manual operation of tools, CNC machining utilizes a computer to guide the movement of tools and machines. This is a game-changer for complex projects as CNC machines can work tirelessly and with extreme precision. Moreover, CNC machines can run continuously for long hours, ensuring that large volumes of complex parts are produced efficiently and with minimal human intervention.
Why CNC for Complex Projects?
CNC machines are particularly suited for complex projects that involve intricate designs, multiple operations, and tight tolerances. Unlike conventional machining, which can be prone to human error, CNC precision machining ensures consistent results, part after part. With CNC, you’re not just getting high precision; you’re also optimizing production processes and reducing waste, which is key when dealing with intricate, complex parts.
2. The Basics of CNC Machines: Key Components and Functions
Key Components of a CNC Machine
At the heart of any CNC machine is the controller, which is responsible for guiding the machine’s movements. This controller is programmed with instructions, often from CAD (Computer-Aided Design) software, to dictate the machine’s operations. The CNC machine’s performance is dependent on several core components working in unison: the spindle, tool holder, and workpiece setup. The spindle rotates the tools at high speeds, while the tool holder ensures the cutting tool is held securely. Meanwhile, the workpiece setup ensures that the material being machined remains in place throughout the entire process.
The Importance of Machine Setup and Calibration
Proper machine setup is essential for ensuring the desired accuracy in machining. Ini kesepakatannya—if the machine isn’t calibrated correctly, even the most advanced machine will fail to achieve the required precision. For example, if the machine’s tool offset isn’t adjusted properly, the cutting tool will not reach the right location, resulting in inaccurate parts. Proper calibration checks need to be made before starting any project, particularly when machining complex designs that require fine tolerances.
How CNC Machines Achieve Precision
CNC machines are equipped with high-performance motors and control systems, allowing them to achieve the desired precision levels. These machines can make minute adjustments to cutting speeds, tool positioning, and material handling to ensure that every cut is made to the exact specifications required. This level of control makes CNC machining ideal for high-precision tasks, such as those found in aerospace, automotive, and medical device manufacturing.
3. Understanding Precision in CNC Machining
What is Precision in CNC Machining?
Precision refers to how accurately a CNC machine can replicate a design or part. In CNC machining, this involves adhering to exact dimensions, measurements, and tolerances, often down to the micrometer level. Precision is critical, especially when manufacturing parts that will fit together in a larger assembly or need to perform specific functions, such as components in medical devices or aerospace technology.
Measuring Precision in CNC
CNC precision is typically measured using tolerance levels, which define how much deviation from the ideal design is allowed. The tighter the tolerance, the more precision the machine must achieve. The beauty of CNC is that it allows manufacturers to create parts with extremely tight tolerances, often within fractions of a millimeter. This precision is essential for complex projects where even the smallest variation can compromise the performance of the final product.
Why Precision Matters for Complex Projects
Complex projects often require parts that must fit together perfectly, with no room for error. Whether it’s assembling a piece of machinery or manufacturing a critical medical component, achieving precision is vital for ensuring that every piece performs as expected. By mastering CNC precision machining, you ensure the parts will fit seamlessly and function properly, providing long-term reliability and performance.
4. Types of CNC Machines for Complex Projects
Different Types of CNC Machines
CNC machines come in various forms, each designed for specific applications. The most common types include CNC milling machines, CNC lathes, and CNC routers. What’s the deal with these machines? CNC milling machines are excellent for making complex parts that require multi-axis operations, such as intricate curves or surfaces. CNC lathes are ideal for producing cylindrical parts, such as shafts and rods, while CNC routers are commonly used for cutting and shaping softer materials like plastics or wood.
Choosing the Right CNC Machine
Selecting the appropriate CNC machine for your project depends on the complexity of the design, the material being used, and the production volume. Anda mungkin bertanya-tanya, how do you pick the right machine? For example, a 5-axis CNC milling machine might be necessary for parts with complex geometries that require cuts from multiple angles. On the other hand, if you’re working with large volumes of simpler parts, a CNC lathe might be more cost-effective.
How CNC Machines Support Precision for Complex Parts
Regardless of the machine type, all CNC machines are designed to deliver high precision. Multi-axis machines, in particular, can achieve complex cuts and angles with exceptional accuracy, making them ideal for intricate projects. The advanced control systems in these machines ensure that each cut is made to the exact specifications, reducing the chance of errors and minimizing the need for post-production adjustments.
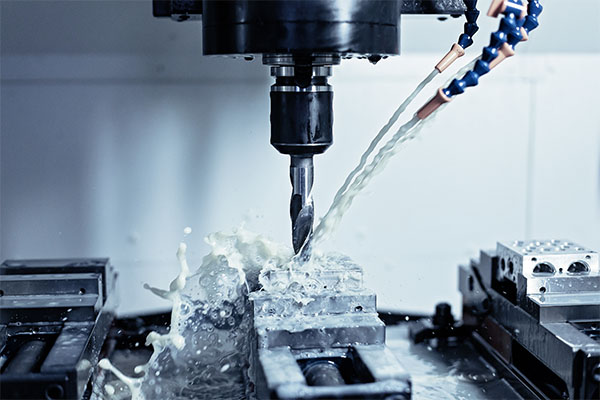
5. Selecting the Right Materials for CNC Machining
Material Choices for CNC Machining
Material selection is a critical aspect of CNC machining. Different materials behave differently during the machining process and can affect the accuracy, surface finish, and durability of the final product. When it comes to precision machining, metals such as aluminum, stainless steel, and titanium are commonly used. These materials are strong, durable, and capable of maintaining tight tolerances. However, CNC machining can also be applied to plastics, composites, and even exotic materials, depending on the requirements of the project.
Impact of Material Properties on Precision
The properties of the material you choose can have a significant impact on how the machine cuts and shapes it. Ini kesepakatannya—harder materials like titanium require slower cutting speeds and more precise tool control, while softer materials such as aluminum can be machined faster and more easily. The key is selecting the material that best suits the specific demands of your project while ensuring that the CNC machine can handle it with the required precision.
Choosing Materials for Complex Projects
For complex projects, it’s essential to choose a material that not only meets the design requirements but also works well with the machining tools and techniques being used. Understanding how materials interact with CNC machines allows for better planning and optimization of the machining process. For example, aerospace components often require lightweight, high-strength materials like titanium, while automotive parts may require different steel alloys that can handle high stress and temperature variations.
6. Understanding CNC Machining Tolerances and Fits
What Are Tolerances in CNC Machining?
Tolerances are a fundamental aspect of CNC machining and define the allowable deviation from the specified measurements of a part. The tighter the tolerance, the more precise the machining must be. In precision machining, tolerances are often measured in microns or millimeters, and even small deviations can have significant impacts on performance. For example, a tolerance of ±0.005mm might be acceptable for some parts, while others may require a tolerance as tight as ±0.001mm.
Why Tolerances Are Critical for Complex Parts
When working on complex projects, maintaining tight tolerances is essential for ensuring that all the components fit together perfectly. For example, if a CNC-machined part is too large or too small, it could cause assembly issues or affect the part’s performance. Here’s the deal—tolerances impact everything from ease of assembly to the functionality of the final product.
Achieving Precision with Tight Tolerances
Achieving the desired tolerances requires careful machine setup, tool selection, and cutting strategies. Anda mungkin bertanya-tanya, how do machinists ensure the required precision? They rely on high-quality tools, accurate machine calibration, and the latest technology to achieve consistent, repeatable results. Additionally, post-machining processes such as inspection and measurement are crucial to confirm that the part meets the tolerance requirements.
7. Tooling and Cutting Strategies for Complex Projects
Selecting the Right Tools
Choosing the right cutting tools is vital for achieving precision when machining complex parts. Tool selection depends on several factors, including the material being machined, the required surface finish, and the complexity of the part’s geometry. For example, carbide tools are often used for high-precision cuts due to their durability and sharpness, while high-speed steel tools might be suitable for softer materials.
Optimizing Cutting Strategies
Optimizing cutting strategies is essential for maintaining precision while also maximizing efficiency. Ini kesepakatannya—using the right cutting speed, feed rate, and depth of cut ensures that the material is removed efficiently without compromising the integrity of the part. In complex projects, this means balancing speed with precision to achieve the best results.
Managing Tool Wear
Tool wear is a significant factor in precision machining. As cutting tools wear down, they can lose sharpness and accuracy, leading to poor finishes and deviations from the desired specifications. To prevent this, machinists often use tools with longer wear life, monitor cutting conditions closely, and replace tools regularly to maintain consistent results.
8. CAD and CAM: The Power of Software in Precision Machining
Role of CAD in CNC Machining
Computer-Aided Design (CAD) software allows engineers to create detailed, 3D models of parts before they are machined. These digital models are then fed into the CNC machine’s controller. CAD plays a crucial role in ensuring that every aspect of the part is carefully considered before the machining process begins.
CAM Software for Programming CNC Machines
Computer-Aided Manufacturing (CAM) software is used to generate the toolpaths and G-code necessary for operating CNC machines. Here’s the deal—CAM software helps convert the CAD design into machine-readable code, ensuring that the CNC machine follows the exact path required to produce the part accurately.
Integrating CAD and CAM
Integrating CAD and CAM software allows manufacturers to streamline the entire design-to-production process. This integration helps reduce errors, speed up production times, and ensure that the final product is machined exactly as designed. With advanced software, it’s possible to simulate the machining process, catch errors early, and fine-tune the design before the machining begins.
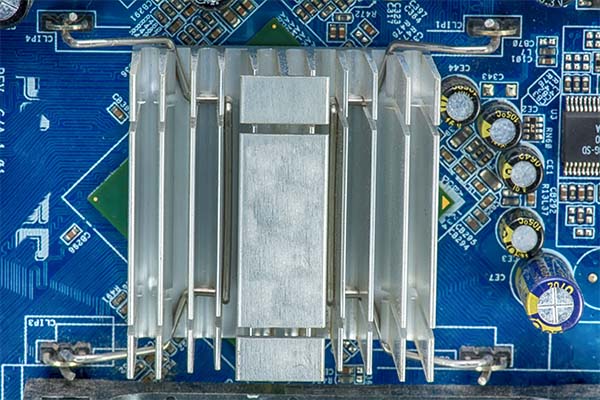
9. The Importance of Proper Workholding in CNC Machining
Workholding Methods for Complex Projects
In CNC machining, workholding refers to the methods used to secure the workpiece in place during machining. Proper workholding is critical for maintaining precision, especially when machining complex parts that require multiple cuts from different angles. Common workholding methods include vices, clamps, fixtures, and magnetic chucks.
How Workholding Affects Precision
Improper workholding can lead to shifting or vibration of the workpiece, which can compromise the accuracy of the machining process. This is a game-changer when working with complex parts, as even the slightest movement can lead to defects. Ensuring that the workpiece is securely fixed in place is essential for achieving the required precision.
Choosing the Right Workholding Method
Choosing the appropriate workholding method depends on several factors, including the material, the geometry of the part, and the type of machine being used. Anda mungkin bertanya-tanya, how do machinists decide which method to use? They assess the requirements of the project and select the method that will ensure the workpiece remains stable throughout the machining process.
10. Achieving High-Quality Finishes in CNC Machining
Surface Finishing Techniques
Achieving a high-quality finish is a critical aspect of CNC machining, especially for parts that need to meet specific aesthetic or functional requirements. Surface finishing techniques like polishing, grinding, and deburring are used to remove imperfections and achieve the desired surface quality.
How Surface Finish Affects Part Functionality
The finish of a part can have a significant impact on its functionality. For example, rough surfaces can cause friction, wear, and other issues that reduce the longevity of the part. Achieving a smooth finish is particularly important for parts that will be in constant motion or exposed to harsh conditions, such as bearings or gears.
The Role of CNC Machines in Surface Finishing
CNC machines are equipped with various attachments and accessories that enable them to perform precision finishing operations. Ini kesepakatannya—CNC machines can be programmed to perform finishing operations automatically, ensuring that every part has a uniform, high-quality surface finish.
11. Handling Complex Geometries and Tight Tolerances
Multi-Axis CNC Machining
Complex geometries often require multi-axis CNC machining, which allows the cutting tool to move along several axes simultaneously. This advanced capability enables the machine to cut intricate shapes, curves, and angles that would be impossible with traditional machining methods.
Challenges of Machining Complex Geometries
Machining complex geometries presents several challenges, including maintaining tight tolerances, ensuring tool access to all parts of the workpiece, and minimizing the risk of errors. Anda mungkin bertanya-tanya, how are these challenges overcome? By utilizing advanced CNC technology, experienced machinists can make precise cuts on even the most complex designs.
Maintaining Tight Tolerances
Maintaining tight tolerances on complex parts requires advanced machining strategies, regular calibration, and careful monitoring throughout the process. Ini kesepakatannya—if a CNC machine isn’t calibrated correctly or if the toolpath is not optimized, the tolerances will be compromised, leading to inaccurate parts.
12. CNC Machining for High-Volume and Custom Projects
Benefits of CNC for High-Volume Production
One of the key advantages of CNC machining is its ability to produce high volumes of parts with consistent precision. Anda mungkin bertanya-tanya, how does this work? CNC machines are capable of running continuously for long periods, often without the need for human intervention. This is ideal for high-volume manufacturing, where large batches of identical parts are required. CNC machining ensures that every part is produced with the same level of precision, which is crucial for industries like automotive and electronics where uniformity is key.
Custom CNC Machining for Unique Designs
While CNC machines are great for high-volume production, they are also highly effective for custom machining. Ini kesepakatannya—whether you’re making a prototype, custom parts for a small batch, or a one-off component, CNC machining can handle a variety of designs and material types. The flexibility of CNC machines allows manufacturers to switch from mass production to custom jobs without compromising quality or precision.
How CNC Machines Support Both High-Volume and Custom Projects
The versatility of CNC machining makes it ideal for both mass production and custom, one-off parts. Whether you’re producing thousands of parts or just a handful, CNC machining delivers exceptional precision and repeatability. This flexibility makes CNC machining an indispensable tool for companies that need to serve both high-volume and custom project needs.
13. Troubleshooting Common CNC Machining Problems
Common Issues in CNC Precision Machining
Like any manufacturing process, CNC machining comes with its challenges. Common issues include tool wear, machine calibration errors, and material defects. Ini kesepakatannya—even small issues can affect the overall quality of the final product, so it’s important to identify and resolve these problems as quickly as possible.
Resolving Tool Wear and Calibration Problems
Tool wear is a significant issue in CNC machining, as worn-out tools can result in poor finishes and inaccurate cuts. Anda mungkin bertanya-tanya, how do machinists deal with tool wear? Regular tool inspection, monitoring cutting conditions, and replacing tools as needed are essential to prevent wear from affecting machining precision. Similarly, ensuring that the CNC machine is properly calibrated is critical for maintaining the necessary tolerances and accuracy.
Handling Material Defects
Material defects can also cause problems during CNC machining, leading to imperfections in the final product. This is a game-changer when working with complex parts, as even minor imperfections in the material can affect machining accuracy. By inspecting materials before use and choosing high-quality materials, these issues can be minimized.
14. The Future of CNC Precision Machining: Innovations and Trends
Kemajuan Teknologi dalam Pemesinan CNC
The future of CNC machining looks bright, with continuous advancements in technology. What’s the deal? We’re seeing more automation, advanced sensors, and AI integration in CNC machines, which will significantly enhance precision and efficiency. The latest trends include 5-axis machining, robotic integration, and adaptive machining, where the machine automatically adjusts parameters based on real-time data.
Peran AI dan Otomasi dalam Pemesinan CNC
AI and machine learning are playing a key role in revolutionizing CNC machining. Here’s the deal—AI can help optimize machining processes by adjusting cutting speeds, feed rates, and tool paths based on feedback from sensors. This leads to better precision, reduced waste, and faster production times. Moreover, automation in CNC machining is improving production efficiency and reducing the need for manual intervention.
The Future of Materials in CNC Machining
In addition to technological advancements in machinery, there are also innovations in materials used for CNC machining. Anda mungkin bertanya-tanya, how will material technology evolve? New composites, alloys, and lightweight materials are being developed to meet the demands of industries like aerospace, automotive, and medical device manufacturing. These materials offer improved strength, durability, and machinability, allowing CNC machining to achieve even higher levels of precision in complex projects.

15. Conclusion: Mastering CNC Precision Machining for Complex Projects
Recap of Key Points
In this article, we’ve explored the fundamentals of Pemesinan presisi CNC, from its components and techniques to its advantages for complex projects. We’ve covered how to select the right materials, tools, and machines for precision work, and we’ve discussed how to handle complex geometries and tight tolerances. CNC machining is an essential tool for any manufacturer looking to produce high-precision, complex parts with consistency.
The Importance of CNC Precision
Mastering CNC precision machining is essential for ensuring that complex parts are manufactured to the highest standards. Here’s the deal—when CNC machining is done right, it results in parts that fit together seamlessly, perform reliably, and meet strict tolerance requirements. The key to success is continuous learning, optimizing processes, and keeping up with technological advancements.
Ajakan untuk Bertindak
Ready to take your CNC machining to the next level? Hubungi kami today for expert advice on how to master CNC precision machining for your complex projects. Whether you’re working on a high-volume production run or a custom part, we have the expertise to help you achieve your goals. Don’t settle for less when precision matters most—let’s build something great together!
Bagian FAQ
What are the key differences between CNC and traditional machining?
CNC machining uses computers to control machining tools, allowing for much higher precision and automation compared to traditional manual machining. This makes CNC machining ideal for complex, high-precision parts.
How can I ensure the precision of my CNC machining projects?
To ensure precision, it’s essential to calibrate your CNC machine regularly, choose the right tools, optimize cutting speeds and feed rates, and use high-quality materials. Additionally, using software like CAD and CAM can help optimize the design and machining process.
What are the common causes of precision errors in CNC machining?
Common causes include tool wear, machine calibration issues, incorrect tool paths, and material defects. Regular maintenance, proper tool selection, and thorough inspections can help prevent these errors.
Can CNC machines handle large or extremely intricate projects?
Yes, CNC machines are capable of handling both large and intricate projects. Multi-axis machines can handle complex geometries, and advancements in CNC technology allow for greater precision on larger parts.
How does material hardness affect CNC machining precision?
Harder materials require slower cutting speeds and more careful tool control, but they can be machined with high precision using the right tools and techniques. Softer materials are easier to machine but may require different considerations to maintain accuracy.
How do I optimize CNC machine settings for different materials?
Optimizing CNC machine settings for different materials involves adjusting cutting speeds, feed rates, and tool selection based on the material’s properties. Softer materials may require faster speeds, while harder materials need slower speeds and more durable tools.
What industries benefit the most from precision CNC machining?
Industries like aerospace, automotive, medical devices, and electronics benefit greatly from CNC precision machining due to the need for high-quality, precise components.
Is CNC machining cost-effective for custom, small-batch production?
Yes, CNC machining is cost-effective for custom, small-batch production due to its ability to quickly produce high-precision parts without the need for expensive molds or tooling.
How long does a typical CNC machining project take?
The duration of a CNC machining project depends on the complexity of the part, material choice, and production volume. Small, simple parts may take just hours to complete, while more intricate projects could take days.