Perkenalan
Stainless Steel 420 is a versatile and durable material often used in CNC machining for various industrial applications. This article delves into the key characteristics of Stainless Steel 420, its CNC machining process, benefits, and common uses. If you’re looking to understand how this material stands out in the machining industry, you’ve come to the right place. Siap untuk bagian yang bagus? Let’s dive into the fascinating details of Stainless Steel 420 and how it enhances CNC machining capabilities.
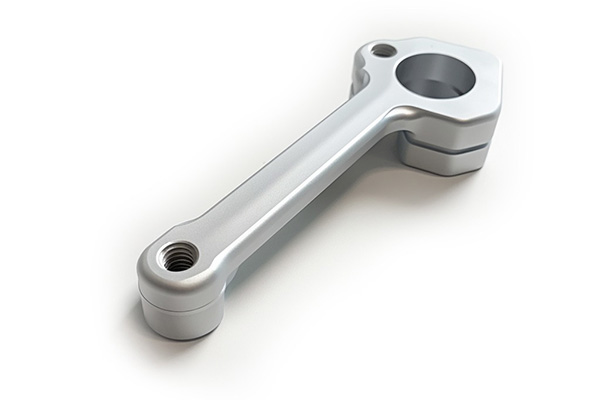
1. What is Stainless Steel 420?
Stainless Steel 420 is a high-carbon, martensitic steel alloy known for its excellent hardness, corrosion resistance, and strength. This material is often used in manufacturing applications where wear resistance and durability are critical. But here’s the kicker: Stainless Steel 420 is also magnetic, making it an ideal choice for industries that require magnetic properties in their components.
Stainless Steel 420 is composed primarily of iron, chromium (12-14%), carbon (0.15-0.4%), and small amounts of other elements such as manganese, silicon, and nickel. This composition grants it its unique properties, including resistance to oxidation and corrosion. Apa cerita sebenarnya? It’s the high carbon content that makes Stainless Steel 420 harder than other stainless steel alloys, such as 304 or 316. The steel is usually hardened through heat treatment, which results in a material that is both strong and wear-resistant.
Common uses of Stainless Steel 420 include surgical instruments, valve components, and automotive parts. These applications benefit from its corrosion resistance and strength. However, it’s important to note that while Stainless Steel 420 is resistant to corrosion, it’s not as corrosion-resistant as austenitic steels like 304 and 316. So, it’s suitable for environments that don’t involve harsh chemicals or high temperatures.
Table 1: Key Properties of Stainless Steel 420
Property | Value |
---|---|
Hardness | High (up to 58 HRC) |
Corrosion Resistance | Sedang |
Magnetism | Yes |
Common Uses | Surgical instruments, valve components, automotive parts |
Composition | 12-14% Chromium, 0.15-0.4% Carbon |
2. Why is Stainless Steel 420 Popular in CNC Machining?
Stainless Steel 420’s popularity in CNC machining is attributed to its unique combination of strength and machinability. This is where it gets interesting: While it is a harder steel, it can still be processed efficiently using CNC machines, making it suitable for high-precision components. The material’s ability to be heat-treated allows it to meet the specific hardness and toughness requirements for different applications.
CNC machining of Stainless Steel 420 presents several advantages, such as its high strength, which makes it ideal for creating durable, long-lasting parts. In the aerospace industry, for instance, components like turbine blades or structural parts benefit from Stainless Steel 420’s ability to withstand wear and corrosion over time.
However, machining Stainless Steel 420 is not without its challenges. The high hardness can lead to excessive tool wear, requiring the use of high-quality, wear-resistant cutting tools. Additionally, the material’s toughness can lead to issues with chip formation during machining. Tapi tunggu, masih ada lagi… Using the right coolant and cutting speeds can mitigate these challenges, ensuring that the machining process is smooth and efficient.
Table 2: Advantages and Challenges of CNC Machining Stainless Steel 420
Advantage | Challenge |
---|---|
High strength and durability | High tool wear |
Excellent for precision parts | Difficult chip formation |
Good corrosion resistance | Requires precise machining parameters |
3. What Makes Stainless Steel 420 Different from Other Grades?
Stainless Steel 420 stands out due to its balance of hardness, wear resistance, and corrosion resistance. Anda mungkin bertanya-tanya how it compares to other stainless steel grades like 304 and 316. Well, the primary difference lies in its chemical composition, particularly its higher carbon content. This gives Stainless Steel 420 its distinctive hardness and ability to be heat-treated, but at the cost of slightly lower corrosion resistance compared to 304 and 316 stainless steels.
Unlike 304 and 316 grades, which are austenitic and non-magnetic, Stainless Steel 420 is martensitic and magnetic. This magnetic property makes it suitable for applications where magnetism is essential, such as in certain electrical and mechanical components.
While Stainless Steel 420 is a more cost-effective option compared to higher grades like 316, it’s less resistant to corrosion in more aggressive environments. This makes it unsuitable for use in marine environments or highly corrosive industrial settings where 316 would be a better choice. So, why does this matter? Choosing the right stainless steel alloy depends on the specific requirements of your project, such as the need for magnetism, hardness, or resistance to corrosion.
Table 3: Comparison of Stainless Steel Grades
Property | Stainless Steel 420 | Stainless Steel 304 | Stainless Steel 316 |
---|---|---|---|
Magnetic | Yes | No | No |
Corrosion Resistance | Sedang | Tinggi | Sangat Tinggi |
Hardness | Tinggi | Sedang | Sedang |
Common Applications | Surgical tools, automotive parts | Food processing, kitchenware | Marine, medical devices |
4. How is Stainless Steel 420 Machined?
CNC machining of Stainless Steel 420 requires careful consideration due to its hardness and toughness. Here’s the deal: To achieve precise results, the right cutting tools and machining conditions must be selected. Machining Stainless Steel 420 is typically done using carbide tools, as these are able to withstand the high forces involved in cutting through hardened material.
The machining process often begins with rough cutting, followed by finer machining steps to achieve the desired shape and finish. Apa cerita sebenarnya? Heat treatment is commonly used to further harden Stainless Steel 420 before machining. This makes it more challenging to cut, but it also increases the material’s strength and wear resistance.
In addition to using the proper tools, choosing the right cutting speed and feed rate is crucial for minimizing heat generation and preventing tool damage. The cooling system used in the machining process is just as important. High-quality coolant helps maintain optimal cutting conditions and extends tool life. Siap untuk bagian yang bagus? Using high-pressure coolant systems can significantly improve the machining process by reducing heat buildup and improving chip removal.
Table 4: Key Considerations for CNC Machining Stainless Steel 420
Consideration | Recommendation |
---|---|
Cutting tools | Use carbide or CBN tools |
Cutting speed | Slow to moderate |
Feed rate | Medium to high |
Coolant type | High-pressure coolant recommended |
Heat treatment before machining | Optional, but improves hardness and wear resistance |
5. What Are the Benefits of Using Stainless Steel 420 in Manufacturing?
Stainless Steel 420 offers several benefits, making it a popular choice for manufacturing durable and precise components. But here’s the kicker: Its combination of hardness, corrosion resistance, and wear resistance makes it ideal for applications that require both strength and longevity.
In manufacturing, Stainless Steel 420 is used to produce parts that need to endure significant wear and tear, such as valve components, cutting tools, and surgical instruments. Its ability to be heat-treated allows manufacturers to customize the material’s hardness for specific applications, making it a versatile choice for a wide range of industries.
Another major benefit is Stainless Steel 420’s cost-effectiveness. Apa cerita sebenarnya? While it’s more affordable than higher-grade stainless steels like 316, it still offers impressive strength and corrosion resistance for most applications, making it a cost-effective solution for industries with tight budgets.
Table 5: Benefits of Using Stainless Steel 420
Keuntungan | Keterangan |
---|---|
High hardness and durability | Ideal for wear-resistant components |
Good corrosion resistance | Suitable for various industrial applications |
Cost-effective | Offers strength and resistance at a lower cost than other grades |
6. How Does Stainless Steel 420 Perform in Different Environments?
Stainless Steel 420 is known for its versatility, but its performance in different environments can vary. But here’s the kicker: While it’s resistant to many forms of corrosion, it is not as resistant as austenitic stainless steels like 304 or 316 in extremely harsh environments.
In high-temperature applications, Stainless Steel 420 performs well due to its ability to maintain strength at elevated temperatures. It’s commonly used in gas turbine blades and heat exchangers, where components need to withstand high heat and pressure. Apa cerita sebenarnya? Its resistance to oxidation is also noteworthy, making it suitable for applications in environments where frequent heat cycling is expected.
When it comes to marine environments, however, Stainless Steel 420 can struggle. The material’s resistance to saltwater corrosion is moderate, so it is not ideal for marine applications where higher corrosion resistance is required. For instance, if you’re looking to use Stainless Steel 420 in marine pumps or seawater applications, you might want to consider other alloys like 316. Siap untuk bagian yang bagus? Despite its limitations in highly corrosive environments, Stainless Steel 420 holds up well in more moderate industrial environments, including automotive and industrial machinery.
For food processing industries, Stainless Steel 420’s resistance to corrosion allows it to be used in some applications. However, it is typically avoided in environments where direct food contact occurs due to concerns over the material’s slight corrosion potential. The same goes for pharmaceutical industries, where a higher grade of stainless steel may be required for hygienic standards.
Table 6: Environmental Performance of Stainless Steel 420
Environment Type | Performance of Stainless Steel 420 |
---|---|
High-temperature environments | Good performance, retains strength |
Marine environments | Moderate corrosion resistance |
Food processing | Suitable for some applications |
Pharmaceutical applications | Not ideal for direct contact |
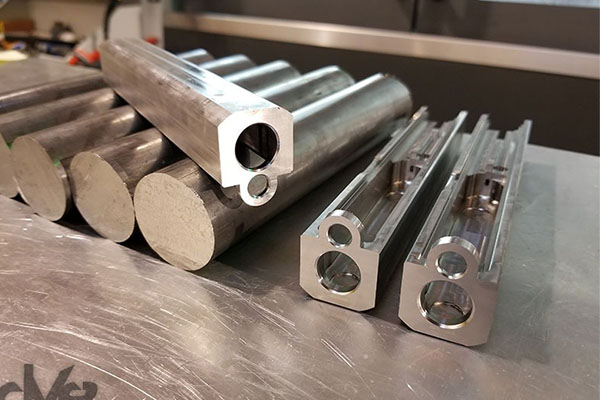
7. What Are the Common Applications of Stainless Steel 420?
Stainless Steel 420 is utilized in a variety of applications where strength, hardness, and resistance to wear are critical. Apa cerita sebenarnya? Its use spans industries such as aerospace, automotive, and medical devices. Let’s take a closer look at some of its most common applications.
In the aerospace industry, Stainless Steel 420 is used to manufacture turbine blades, compressor blades, and other high-stress components. Here’s the kicker: The material’s excellent strength-to-weight ratio and ability to withstand high temperatures make it a valuable choice in these applications. Similarly, in the automotive industry, Stainless Steel 420 is often found in engine components, brake discs, and gears, where durability and high strength are essential.
The medical industry is another major user of Stainless Steel 420. Tapi tunggu, masih ada lagi… Surgical instruments such as scalpels, scissors, and forceps are commonly made from this alloy due to its ability to maintain sharpness and resistance to corrosion. Stainless Steel 420’s high hardness also makes it ideal for manufacturing parts like dental tools, where precision and wear resistance are crucial.
Finally, Stainless Steel 420 is widely used in valve components, pumps, and other industrial machinery that require strength and durability. Siap untuk bagian yang bagus? Its ability to resist wear and tear makes it the go-to material for these applications, where machinery parts face constant stress and friction.
Table 7: Common Applications of Stainless Steel 420
Industry | Application |
---|---|
Ruang angkasa | Turbine blades, compressor blades |
Otomotif | Engine components, brake discs, gears |
Medis | Surgical instruments, dental tools |
Industrial machinery | Valve components, pumps, gears |
8. How to Choose Between Stainless Steel 420 and Other Materials?
When choosing between Stainless Steel 420 and other materials, several factors must be considered to ensure the right material is selected for your application. Apa cerita sebenarnya? It’s not just about strength and durability; corrosion resistance, cost, and machinability also play a big role.
For example, if your project requires high corrosion resistance, you may want to consider austenitic stainless steels like 304 or 316, which offer superior performance in more aggressive environments, including marine and chemical applications. However, if wear resistance and high hardness are key priorities, Stainless Steel 420 would be an excellent choice. But here’s the kicker: Stainless Steel 420 offers a cost-effective alternative to higher-end alloys like 316, making it ideal for industries with budget constraints.
In addition to performance and cost, machinability is another crucial factor. While Stainless Steel 420 is harder than 304, it’s still machinable with the right equipment. If ease of machining is a priority, you might choose a material with less hardness, such as 304 stainless steel, but this might come at the expense of strength and wear resistance. Here’s where it gets interesting: The ability to heat treat Stainless Steel 420 makes it highly adaptable for various applications, giving it a distinct advantage over materials that cannot be heat treated.
Table 8: Factors to Consider When Choosing Stainless Steel 420
Faktor | Consideration |
---|---|
Corrosion resistance | Stainless Steel 420 offers moderate resistance |
Wear resistance | Stainless Steel 420 excels in wear resistance |
Biaya | More cost-effective than 316 stainless steel |
Machinability | Requires carbide tools for machining |
Heat treatment | Can be heat treated for enhanced hardness |
9. What Are the Key Challenges in CNC Machining Stainless Steel 420?
Machining Stainless Steel 420 presents several challenges due to its hardness and toughness. Apa cerita sebenarnya? While its high hardness makes it ideal for many applications, it can also lead to tool wear and difficulty in chip removal during the machining process.
One of the main challenges in CNC machining Stainless Steel 420 is its high carbon content, which makes it harder than other stainless steel grades like 304. Tapi tunggu, masih ada lagi… The high hardness increases the potential for tool wear, meaning that higher-quality, wear-resistant tools, such as carbide or cubic boron nitride (CBN) tools, are needed to achieve the best results. Without the proper tools, the material can cause excessive tool wear and reduce the efficiency of the machining process.
Another challenge is the toughness of Stainless Steel 420. Its toughness means that chips can be difficult to break and remove, leading to poor surface finishes or even tool breakage if not properly handled. Here’s the kicker: Using the right coolant, along with optimal cutting parameters, can help mitigate these challenges by keeping the workpiece cool and ensuring better chip removal.
Table 9: Challenges in CNC Machining Stainless Steel 420
Challenge | Larutan |
---|---|
Tool wear | Use carbide or CBN cutting tools |
Chip removal | Optimize cutting parameters |
Surface finish | Use high-pressure coolant |
10. How to Improve CNC Machining Efficiency with Stainless Steel 420?
Improving CNC machining efficiency when working with Stainless Steel 420 requires optimizing various aspects of the machining process. But here’s the kicker: The right combination of cutting tools, coolant, and machining parameters can significantly enhance machining efficiency, reduce tool wear, and improve overall results.
One of the most effective ways to improve machining efficiency is to use carbide or CBN cutting tools. These tools are designed to withstand the high forces and temperatures generated during machining. Apa cerita sebenarnya? Using the right tool materials ensures that the machining process remains smooth, even when dealing with hard materials like Stainless Steel 420.
Optimizing cutting speeds and feed rates is also essential for improving machining efficiency. What’s the good part? Running the CNC machine at optimal cutting speeds reduces the generation of excess heat, prevents premature tool wear, and minimizes the risk of part distortion. Additionally, using high-pressure coolant systems can help keep the workpiece cool and maintain efficient chip removal, both of which are critical for minimizing tool wear and ensuring consistent results.
Table 10: Tips for Improving CNC Machining Efficiency with Stainless Steel 420
Tip | Keuntungan |
---|---|
Use carbide or CBN cutting tools | Minimizes tool wear |
Optimize cutting speeds and feed rates | Reduces heat generation |
Use high-pressure coolant | Enhances chip removal and tool life |
11. What Are the Best Practices for Maintaining CNC Machines When Machining Stainless Steel 420?
Maintaining CNC machines is essential for achieving high-quality results when machining Stainless Steel 420. Apa cerita sebenarnya? Proper maintenance ensures that the machine performs at its best, reducing the risk of unexpected downtime and extending its lifespan.
Regular inspection of the cutting tools is crucial, as tools that are worn or damaged can lead to poor results and reduced efficiency. But here’s the kicker: Inspecting and replacing tools at regular intervals can prevent unnecessary downtime and keep the machining process running smoothly. The same goes for ensuring that the machine’s coolant system is functioning properly. A high-quality coolant system can help reduce the buildup of heat and ensure that the material is cut smoothly without causing tool wear.
Additionally, it’s important to monitor and adjust the CNC machine’s settings to optimize machining parameters. Regular calibration and maintenance of the machine ensure that it continues to produce high-quality parts and avoid unnecessary repairs. Here’s where it gets interesting: The long-term investment in proper CNC machine maintenance pays off in terms of productivity, part quality, and reduced downtime.
Table 11: Best Practices for CNC Machine Maintenance
Practice | Keuntungan |
---|---|
Regular tool inspection | Prevents tool wear and poor machining |
Maintain coolant system | Ensures efficient cooling and chip removal |
Machine calibration | Maintains accuracy and reduces downtime |
12. How Does Stainless Steel 420 Compare to Other CNC Materials for Precision Work?
Stainless Steel 420 has certain advantages and limitations compared to other materials used in CNC machining for precision work. Apa cerita sebenarnya? Its high hardness and wear resistance make it a top choice for parts that must endure stress and high wear. However, it falls short in terms of corrosion resistance compared to higher-grade alloys like 316.
When compared to materials like aluminum, Stainless Steel 420 offers greater strength and durability but is harder to machine. Aluminum, for instance, is much easier to machine due to its lower hardness, which leads to faster processing times and reduced tool wear. However, aluminum does not offer the same level of strength and wear resistance as Stainless Steel 420, making it unsuitable for certain high-stress applications.
In industries such as automotive or aerospace, where components must withstand significant stress, Stainless Steel 420’s hardness and resistance to wear make it the ideal choice. Siap untuk bagian yang bagus? While it may not be the easiest material to machine, its long-term performance and durability in demanding applications make it well worth the extra effort.
Table 12: Comparison of CNC Materials for Precision Work
Bahan | Strength | Machinability | Wear Resistance | Corrosion Resistance |
---|---|---|---|---|
Stainless Steel 420 | Tinggi | Sedang | Bagus sekali | Sedang |
Aluminium | Sedang | Bagus sekali | Rendah | Bagus sekali |
Stainless Steel 316 | Sedang | Sedang | Bagus | Bagus sekali |
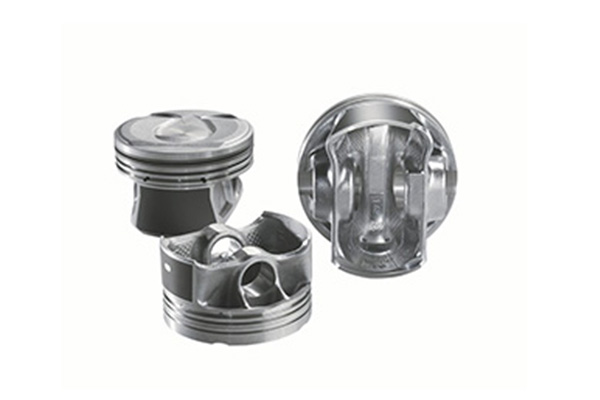
13. What are the Challenges in Welding Stainless Steel 420?
Welding Stainless Steel 420 can present several challenges due to its high carbon content and martensitic structure. Apa cerita sebenarnya? The main issue when welding Stainless Steel 420 is the potential for cracking, especially if the material is not properly heat treated before welding.
Siap untuk bagian yang bagus? Preheating the material to around 400°F (204°C) before welding can help reduce the likelihood of cracking. Post-weld heat treatment is also essential to relieve stresses and ensure the welded area maintains its strength. Additionally, care must be taken when selecting the right filler material for welding Stainless Steel 420 to prevent dilution of the base metal’s properties.
Despite these challenges, welding Stainless Steel 420 can be achieved successfully with the right technique and preparation. Here’s the kicker: By following proper welding procedures and post-weld treatments, Stainless Steel 420 can be welded with minimal issues, making it suitable for high-performance applications.
Table 13: Welding Stainless Steel 420 Considerations
Consideration | Recommendation |
---|---|
Preheating | Preheat to 400°F to prevent cracking |
Filler material | Choose compatible filler material |
Post-weld heat treatment | Apply to relieve stress and prevent cracks |
14. What Are the Environmental Considerations When Using Stainless Steel 420?
Stainless Steel 420 is a durable and reliable material, but like all metals, its environmental impact should be considered. Apa cerita sebenarnya? While Stainless Steel 420 is recyclable, its manufacturing process does have an environmental footprint.
The energy-intensive process of mining, refining, and fabricating Stainless Steel 420 contributes to carbon emissions and other environmental impacts. But here’s the kicker: Despite these challenges, Stainless Steel 420’s longevity and resistance to corrosion make it a more sustainable option in the long run. By choosing Stainless Steel 420, industries can reduce the frequency of replacements and decrease material waste over time.
Siap untuk bagian yang bagus? Stainless Steel 420 can be fully recycled, making it an environmentally friendly material choice in comparison to other non-recyclable materials. As industries move toward more sustainable practices, recycling Stainless Steel 420 helps reduce environmental impacts.
Table 14: Environmental Considerations of Stainless Steel 420
Environmental Factor | Dampak |
---|---|
Carbon emissions from manufacturing | Energy-intensive process, contributes to pollution |
Recyclability | Fully recyclable |
Long-term sustainability | Durable material, reduces frequent replacements |
15. How Can Stainless Steel 420 Impact the Future of CNC Machining?
Stainless Steel 420 is a key material in the evolving world of CNC machining. Apa cerita sebenarnya? As industries demand more durable, high-performance parts, Stainless Steel 420 will continue to play a crucial role due to its unique balance of strength, hardness, and machinability.
With advancements in CNC technology and cutting tools, machining Stainless Steel 420 will become even more efficient and precise. But here’s the kicker: As machine tools become more advanced, the limitations of Stainless Steel 420, such as its difficulty to machine, will be mitigated, making it even more popular in high-performance applications.
The future of Stainless Steel 420 in CNC machining looks bright, as new innovations in materials and machining processes continue to improve the capabilities and efficiency of this versatile alloy. Siap untuk bagian yang bagus? The continued demand for precision parts across industries like aerospace, automotive, and medical devices will keep Stainless Steel 420 at the forefront of CNC machining for years to come.
Table 15: Future of Stainless Steel 420 in CNC Machining
Faktor | Dampak |
---|---|
CNC technology advancements | Improves machining efficiency and precision |
Demand for high-performance parts | Increases use in aerospace, automotive, and medical industries |
Material innovation | Increases versatility and adaptability for future applications |
Bagian FAQ
Pertanyaan 1: What is Stainless Steel 420?
Stainless Steel 420 is a high-carbon, martensitic steel known for its hardness, corrosion resistance, and durability. It’s commonly used in manufacturing surgical instruments, automotive parts, and valve components.
Pertanyaan 2: How does CNC machining work for Stainless Steel 420?
CNC machining for Stainless Steel 420 involves using computer-controlled tools to shape and cut the material. The hardness of the steel requires carbide tools and precise cutting speeds, as well as high-quality coolant systems.
Pertanyaan 3: What are the main applications of Stainless Steel 420?
Stainless Steel 420 is used in surgical tools, valve components, automotive parts, and industrial machinery due to its strength and corrosion resistance. It’s particularly suited for applications where wear resistance is key.
Pertanyaan 4: How do I choose between Stainless Steel 420 and other grades?
When choosing between Stainless Steel 420 and other grades, consider factors such as the required hardness, corrosion resistance, and cost. Stainless Steel 420 is more cost-effective than grades like 316 but offers slightly lower corrosion resistance.
Pertanyaan 5: What are the challenges of machining Stainless Steel 420?
Machining Stainless Steel 420 can be challenging due to its hardness, which can cause excessive tool wear. To mitigate this, carbide tools and high-pressure coolant systems are recommended for efficient machining and extended tool life.