Industrial CNC routers are essential tools for businesses involved in manufacturing, offering incredible precision and versatility. Whether you’re in the woodworking, metalworking, or plastics industries, understanding what a CNC router is, how it works, and why it’s so crucial for modern production processes can help you make better decisions. This guide will walk you through the ins and outs of industrial CNC routers, covering everything from their functionality to the types available, and how they can benefit your business.
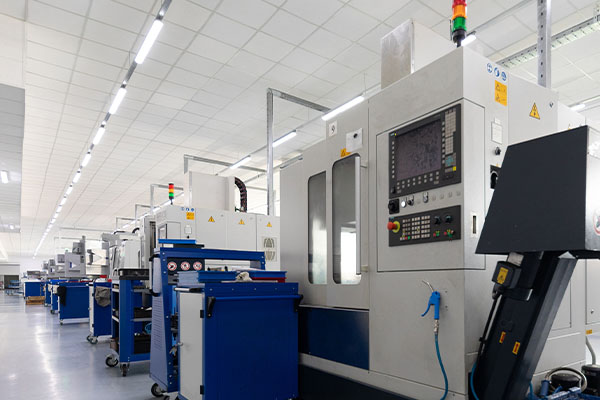
1. What is an Industrial CNC Router?
So, what exactly is an industrial CNC router? Simply put, it’s a computer-controlled machine that cuts, shapes, and engraves materials with high precision. The term CNC stands for “Computer Numerical Control,” which means the router follows a specific program or set of instructions generated by a computer to perform its tasks.
But here’s the kicker: CNC routers can handle a wide range of materials, including wood, metal, plastic, and composites, making them incredibly versatile. For businesses, this translates into the ability to perform multiple types of manufacturing tasks with a single machine.
Industrial CNC routers are typically used for cutting, engraving, and milling, with applications ranging from simple part cutting to more complex, intricate designs. They are commonly found in industries like woodworking, automotive, aerospace, and electronics.
Here’s where it gets interesting: CNC routers are also used for tasks that would be nearly impossible with manual machinery. The precision of a CNC router is so high that it can repeat the same cut hundreds or even thousands of times without error. This makes them invaluable for businesses that require consistent results with minimal deviation.
Now that you know what they are, let’s look at the different types of industrial CNC routers.
Table 1: Types of CNC Routers
Type of CNC Router | Application | Advantages |
---|---|---|
3-axis CNC router | Simple cutting tasks | Cost-effective, simple design |
4-axis CNC router | More complex cuts | Increased precision, ability to work on more materials |
5-axis CNC router | Complex shapes | High precision for intricate designs |
Gantry CNC router | Large-scale cutting | Can handle large workpieces, high stability |
2. How Does an Industrial CNC Router Work?
Ready for the good part? Let’s break down how an industrial CNC router works. It starts with a design, often created with CAD (Computer-Aided Design) software. This design is then converted into a code that the router understands, typically in the form of G-code. The G-code contains all the instructions the machine needs, such as how fast to move, where to cut, and at what depth.
The CNC router follows these instructions to move the router head and cutting tool along multiple axes. The most common setups are 3-axis, 4-axis, and 5-axis machines, each offering varying degrees of complexity and precision.
But here’s the thing: CNC routers aren’t just “set it and forget it” machines. They require regular monitoring to ensure everything is running smoothly. The operator might need to adjust the speed or position of the cutting head or make sure that the material is properly aligned.
Here’s the real story: the CNC router’s ability to automate tasks significantly reduces the risk of human error. The result is more accurate cuts, quicker production times, and less waste. In industries like aerospace or automotive, where every detail counts, this accuracy can make or break a project.
Table 2: CNC Router Axes and Their Functions
Axis | Function |
---|---|
X-axis | Horizontal movement (left to right) |
Y-axis | Horizontal movement (front to back) |
Z-axis | Vertical movement (up and down) |
A-axis | Rotational movement (around the X-axis) |
B-axis | Rotational movement (around the Y-axis) |
3. Why Should You Use an Industrial CNC Router?
What’s the big deal? Why should businesses invest in industrial CNC routers? Well, these machines offer a range of benefits that make them highly valuable for a variety of industries.
First, there’s the issue of speed. CNC routers can complete tasks far more quickly than manual processes, allowing businesses to meet tight deadlines and keep production lines moving smoothly. Plus, they reduce the need for skilled labor, which can be costly and hard to find.
Another huge advantage is the precision. CNC routers can replicate the same design repeatedly with an almost perfect degree of accuracy. Whether you need to make hundreds or thousands of identical parts, a CNC router will do it with minimal variation.
But here’s the kicker: industrial CNC routers aren’t just about speed and accuracy. They also allow for greater design flexibility. Because the router is controlled by software, it can easily adapt to changes in design or production needs without the need for physical adjustments.
Let’s not forget that CNC routers help reduce waste. By automating the cutting process and using advanced software, these machines minimize material wastage. For industries where every piece of raw material is expensive, this can translate into significant savings over time.
Table 3: Benefits of Using CNC Routers
Benefit | Explanation |
---|---|
Speed | Faster than manual machining |
Precision | High accuracy with minimal deviation |
Flexibility | Can easily adjust designs based on needs |
Waste reduction | Less material waste due to precision |
4. What Are the Different Types of Industrial CNC Routers?
Now, let’s talk about the different types of industrial CNC routers. There isn’t just one “CNC router” – there are multiple types designed for different applications.
- 3-axis CNC routers are the most common, providing basic movement along the X, Y, and Z axes. These are ideal for simpler tasks such as cutting and engraving flat materials like wood, plastic, and metal.
- 4-axis CNC routers add another layer of flexibility by allowing rotation along the A-axis. This enables the machine to work on parts that need to be rotated during processing, such as cylindrical parts.
- 5-axis CNC routers take things up a notch by adding two additional axes, allowing for more intricate and complex cuts. These routers are commonly used in industries like aerospace and automotive, where precision is critical.
And this is where it gets interesting: some CNC routers are designed specifically for large-scale projects, like gantry-style routers. These routers can handle extremely large pieces of material and are typically used in industries that require heavy-duty machinery for massive workloads.
Let’s not forget that the size and capabilities of the router should align with your production needs. The right router for your business depends on the materials you work with, the complexity of your designs, and the scale of your operation.
Table 4: Comparison of CNC Router Types
Type | Features | Common Uses |
---|---|---|
3-axis CNC | Basic movement along X, Y, Z axes | Woodworking, basic metal cutting |
4-axis CNC | Adds A-axis rotation for flexibility | Automotive parts, cylindrical shapes |
5-axis CNC | Additional axes for intricate cuts | Aerospace, precision parts |
Gantry CNC | Large-scale cutting capabilities | Furniture, large-scale manufacturing |
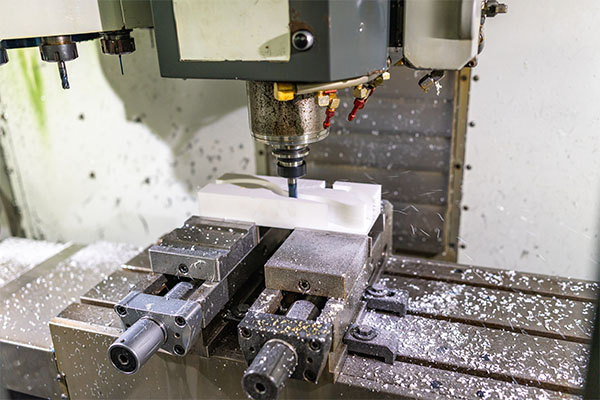
5. How to Choose the Right Industrial CNC Router for Your Business?
What’s the best way to choose the right CNC router for your needs? It’s all about understanding your business requirements and matching those with the capabilities of the router.
Start by considering the size and type of materials you’ll be working with. Larger materials may require a bigger machine, while smaller jobs can be handled by compact, more affordable models.
Another factor is precision. If your business deals with intricate designs, you’ll need a router that can handle more detailed work, such as a 5-axis CNC router.
Here’s the deal: it’s also essential to consider the long-term cost. While you may be tempted to go for the cheapest option, investing in a more expensive model might save you money in the long run due to increased efficiency, precision, and fewer maintenance needs.
Now, let’s look at some key factors when making your decision.
Table 5: Key Factors in Choosing a CNC Router
Factor | Considerations |
---|---|
Material type | Choose based on materials you work with most often |
Precision | Higher precision for intricate designs |
Budget | Consider long-term investment vs. initial cost |
6. What Materials Can an Industrial CNC Router Work With?
Ready for the good part? One of the greatest strengths of industrial CNC routers is their versatility in working with different materials. While wood and metal are the most common, these machines can handle an impressive range of materials. But here’s the kicker: the material you choose depends entirely on the type of router and its specific capabilities. Let’s take a closer look.
Wood is perhaps the most widely used material in CNC routers, especially in the furniture industry. Whether you’re crafting intricate designs or cutting large panels, CNC routers provide the precision needed to handle wood with ease. From hardwoods to softwoods, CNC routers can accommodate a variety of types, including plywood, MDF, and particleboard.
Metalworking is another major application. CNC routers can process metals like aluminum, steel, and brass. These materials require more power, which is why certain CNC routers are built specifically to handle harder and denser materials. For example, in the automotive industry, CNC routers are used to cut and shape metal components for vehicle assembly.
What’s the real story? CNC routers can also be used for non-traditional materials, such as plastics and composites. These materials are commonly found in industries like aerospace, where lightweight and durable materials are needed. CNC routers can also cut stone, ceramics, and glass, making them incredibly versatile.
With the variety of materials these machines can handle, it’s clear that industrial CNC routers are designed to meet the demands of many industries. Let’s look at the specific material considerations that can affect the machining process.
Table 6: Materials CNC Routers Can Work With
Material | Application | Considerations |
---|---|---|
Wood | Furniture, cabinetry, decorative items | Requires proper dust collection system |
Metal | Automotive, aerospace, machinery | Requires more powerful routers, coolant systems |
Plastics | Signage, packaging, prototypes | Precision cutting needed to avoid warping |
Composites | Aerospace, automotive parts | Can be tough on tools, needs high-quality bits |
Stone & Glass | Engraving, custom designs | Requires specialized bits and slow speeds |
8. What Industries Benefit Most from Industrial CNC Routers?
So, who benefits most from industrial CNC routers? The truth is, almost every industry that relies on precise manufacturing can take advantage of these powerful machines. Let’s dive into some of the sectors where CNC routers are most commonly used.
The woodworking industry is by far the most well-known user of CNC routers. These machines are used to create everything from custom furniture to cabinetry and intricate carvings. With the ability to automate complex cutting processes, woodworking businesses can increase their output, reduce waste, and improve precision.
The automotive industry also sees significant benefits from CNC routers. CNC machines are used to produce metal components for vehicles, such as engine parts, chassis, and brackets. These machines offer high precision, which is essential when working with the tight tolerances required in automotive manufacturing.
Aerospace is another sector where industrial CNC routers have made a significant impact. The high level of precision required in the design and production of aerospace components can only be achieved with the advanced capabilities of CNC routers. From cutting metal and composites to producing lightweight parts, CNC routers are invaluable in this industry.
And this is where it gets interesting: CNC routers are also used in the electronics industry for cutting and engraving parts like enclosures, connectors, and circuit boards. The ability to work with different materials like plastics and metals makes CNC routers highly adaptable to the needs of this fast-paced industry.
Table 7: Industries Benefiting from CNC Routers
Industry | Common Applications | Key Benefits |
---|---|---|
Woodworking | Furniture, cabinetry, intricate designs | Increased speed, precision |
Automotive | Engine parts, chassis, brackets | High tolerance, cost efficiency |
Aerospace | Lightweight components, metal cutting | Precision, complex designs |
Electronics | Circuit boards, enclosures, connectors | Versatility with materials |
9. How Do You Maintain an Industrial CNC Router?
Let’s talk about maintenance. What’s the best way to keep your CNC router running smoothly for years to come? Here’s the deal: proper maintenance is essential to ensuring the longevity and efficiency of your equipment. Regular upkeep can prevent costly repairs and keep your business running smoothly.
Routine cleaning is a crucial part of CNC router maintenance. Dust and debris can quickly build up on the machine, causing parts to wear out prematurely. Using compressed air to blow out dust and wiping down surfaces with a clean cloth can help keep things running smoothly.
Another critical maintenance task is checking the mechanical components of the router, such as the motors, bearings, and drive systems. Over time, these parts can wear down, leading to inefficiency or even failure. Regular lubrication and inspections can help identify any potential issues before they become major problems.
What’s the real story? Software maintenance is just as important as physical maintenance. Ensuring that the router’s software is up to date helps avoid potential glitches and ensures the router is running the latest cutting-edge programs.
By performing routine maintenance and addressing issues early, you can extend the lifespan of your CNC router and avoid unexpected downtime. After all, the more consistent your machine’s performance, the better your business will operate.
Table 8: Routine Maintenance Tasks for CNC Routers
Task | Frequency | Benefits |
---|---|---|
Cleaning machine parts | Weekly | Prevents build-up of dust |
Lubricating moving parts | Monthly | Reduces wear and tear |
Inspecting software | Quarterly | Keeps the machine updated |
Checking mechanical parts | Bi-annually | Identifies wear before failure |
10. What Are the Costs Associated with Industrial CNC Routers?
Let’s dive into the costs. What should you expect when purchasing and maintaining an industrial CNC router? Here’s where it gets interesting: the cost of CNC routers varies widely depending on the size, complexity, and brand of the machine. But here’s the kicker: while the initial cost might seem high, the return on investment (ROI) can be significant.
The upfront cost of a CNC router typically ranges from $10,000 to $150,000 or more. Smaller machines designed for basic tasks tend to be more affordable, while larger, multi-axis machines can cost significantly more. But that’s not the end of the story. When you factor in maintenance costs, software updates, and tooling, you could be looking at additional ongoing expenses.
Another factor to consider is energy costs. Industrial CNC routers are powered by electricity, so businesses should account for the cost of running the machines. However, the speed and efficiency of CNC routers can offset these costs over time by reducing labor costs and increasing production speed.
Now, let’s not forget about financing options. Many companies offer leasing options or financing plans for CNC routers, making it easier for businesses to invest in high-end equipment without paying everything upfront.
Table 9: CNC Router Costs and Considerations
Cost Factor | Estimated Cost | Considerations |
---|---|---|
Initial Purchase | $10,000 – $150,000+ | Based on size and capabilities |
Maintenance | $500 – $5,000/year | Includes parts and labor |
Energy Consumption | $0.10 – $0.20 per hour | Depends on machine power |
Software Updates | $500 – $2,000/year | Keeps machine up to date |
11. How Can Industrial CNC Routers Improve Production Efficiency?
What if you could produce parts faster and with more accuracy? Well, here’s the kicker: industrial CNC routers can significantly improve your production efficiency. Whether you’re manufacturing hundreds of identical parts or creating custom prototypes, these machines provide speed, precision, and repeatability.
For starters, CNC routers automate many of the tasks that would otherwise require manual labor. With the machine doing most of the work, businesses can reduce the time spent on each task. In industries like automotive and aerospace, where deadlines are tight, this speed can be the difference between meeting client expectations and falling behind.
What’s the real story? CNC routers also reduce human error, ensuring that each cut or shape is replicated with high accuracy every time. This reduces the need for rework, cutting down on both time and material costs.
Let’s not forget about scalability. As your business grows, CNC routers can handle increased production without sacrificing quality. With the ability to quickly adjust to different designs or materials, these machines can scale production to meet your needs.
By investing in an industrial CNC router, you’ll not only improve efficiency but also enhance your ability to meet customer demands with precision and speed.
Table 10: Key Factors in Improving Production Efficiency
Factor | Benefit |
---|---|
Automation | Reduces manual labor, increases speed |
Precision | Decreases human error, improves consistency |
Scalability | Adapts to growing production needs |
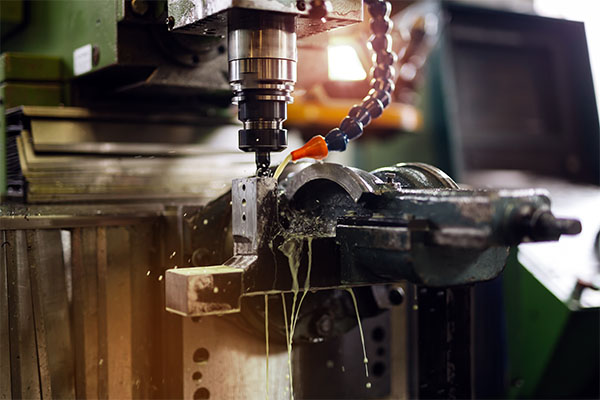
12. What Are the Latest Trends in Industrial CNC Routers?
Let’s take a look at some of the latest trends in industrial CNC routers. What’s new in the world of CNC routing? Well, this is where it gets exciting.
One major trend is the integration of AI and machine learning into CNC systems. These technologies help optimize cutting paths and predict potential failures before they happen, improving both efficiency and machine lifespan.
Another trend is the development of multi-material CNC routers, which can handle a wider variety of materials at once. This makes it easier for businesses to handle complex jobs that involve multiple materials without needing to switch between different machines.
What’s the real story? Robotics is also making waves in the CNC router world. Robots are being integrated into CNC systems to automate material handling and assist with part placement, reducing human labor and increasing efficiency.
As these technologies continue to evolve, the future of industrial CNC routers looks even more promising, offering businesses even more ways to improve efficiency, precision, and production capabilities.
Table 11: Emerging Trends in CNC Routers
Trend | Description | Benefit |
---|---|---|
AI Integration | Machine learning for optimized paths | Increases efficiency, reduces errors |
Multi-material Routers | Ability to work with various materials | Streamlines production, reduces need for multiple machines |
Robotics Integration | Robots assist with material handling | Automates labor, increases speed and efficiency |
13. Can Small Businesses Afford Industrial CNC Routers?
So, you might be wondering: can small businesses afford industrial CNC routers? Here’s the kicker: while the initial cost may seem high, there are options that can make CNC routers accessible for smaller businesses.
Leasing is one option that allows businesses to get started with a CNC router without a large upfront investment. Leasing companies often offer flexible terms, making it easier for small businesses to access high-end equipment. The leasing cost typically includes maintenance and support, which can save on additional expenses.
What’s the real story? Small businesses can also look for more affordable, smaller-scale CNC routers that still provide impressive capabilities. These machines might not have the advanced features of larger models, but they can still handle a wide range of tasks, helping businesses save money while maintaining efficiency.
Table 12: CNC Router Financing Options
Financing Option | Description | Benefit |
---|---|---|
Leasing | Rent a CNC router for a fixed period | Lower initial cost, includes support |
Small-Scale Machines | More affordable models with basic features | Lower upfront investment, still efficient |
Loans | Financing through banks or lenders | Allows for machine purchase without upfront cash |
14. How Do Industrial CNC Routers Contribute to Sustainability?
Sustainability is on everyone’s mind, and industrial CNC routers are no exception. So, how do these machines contribute to a greener future? Let’s dive in.
For starters, CNC routers reduce material waste. By using software to program precise cuts, the machines minimize the amount of scrap material produced. This is particularly important in industries like woodworking, where raw materials can be costly.
What’s the kicker? CNC routers are also more energy-efficient than other machines, helping businesses reduce their overall energy consumption. Many modern CNC routers are designed with energy-saving features, like variable speed motors, that adjust power usage based on the task at hand.
Let’s not forget that by automating production processes, CNC routers reduce the need for human intervention, which can help lower the environmental impact of manufacturing.
Table 13: Sustainability Benefits of CNC Routers
Benefit | Explanation |
---|---|
Reduced material waste | Precise cuts minimize scrap material |
Energy efficiency | Power-saving features reduce energy consumption |
Lower environmental impact | Automation reduces human labor and waste |
15. What Are the Potential Challenges of Using Industrial CNC Routers?
Finally, let’s look at the challenges. While industrial CNC routers offer significant benefits, they are not without their potential drawbacks. But here’s the kicker: understanding these challenges allows businesses to better prepare and mitigate issues as they arise.
One of the biggest challenges is the need for skilled operators. While CNC routers are automated, they still require expertise to operate, maintain, and troubleshoot. Training employees to use these machines can take time and resources.
Another potential challenge is the initial cost. While CNC routers offer excellent ROI in the long run, the upfront investment can be significant, especially for smaller businesses.
What’s the real story? There are also maintenance costs to consider. Although CNC routers are generally low-maintenance, routine upkeep is necessary to keep the machines running smoothly. For businesses that don’t have in-house technicians, outsourcing maintenance can be an additional expense.
Table 14: Common Challenges of CNC Routers
Challenge | Explanation | Solution |
---|---|---|
Skilled labor | Operators need training and expertise | Offer in-house training or hire experts |
High upfront cost | CNC routers can be expensive to purchase | Consider financing options or leasing |
Ongoing maintenance | Machines require regular upkeep | Create a routine maintenance schedule |
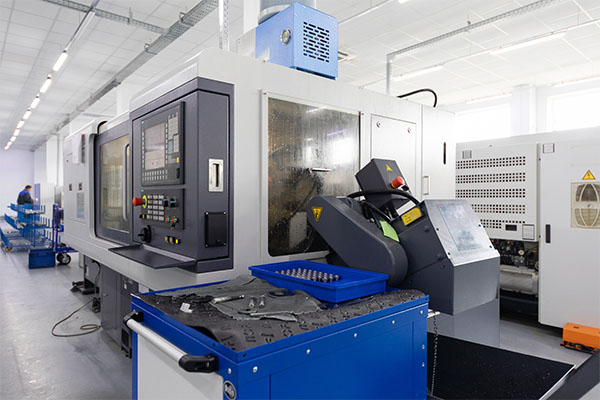
FAQ Section
Q1: What is an industrial CNC router?
An industrial CNC router is a computer-controlled machine used for cutting, shaping, and engraving various materials like wood, metal, and plastics with precision.
Q2: How does an industrial CNC router work?
An industrial CNC router works by following instructions from a computer, which tells it how to move along different axes to perform tasks like cutting, milling, and engraving.
Q3: Why should I invest in an industrial CNC router?
Investing in an industrial CNC router increases production speed, reduces labor costs, ensures high precision, and provides flexibility in design, which ultimately improves your bottom line.
Q4: What industries use industrial CNC routers?
Industries like woodworking, metalworking, automotive, aerospace, and electronics frequently use CNC routers for precise, repeatable, and cost-effective production.
Q5: How can I maintain an industrial CNC router?
Routine maintenance for a CNC router includes cleaning, checking mechanical parts, calibrating the machine, and ensuring the software is updated to ensure optimal performance and longevity.