Introduzione alle tolleranze di lavorazione CNC
La lavorazione CNC è uno dei metodi di produzione più precisi, in grado di produrre parti con elevata accuratezza e ripetibilità. Tuttavia, un fattore critico nella lavorazione CNC è il concetto di tolleranze, che definiscono le variazioni consentite nelle dimensioni delle parti. Le tolleranze sono essenziali per garantire che le parti si adattino e funzionino correttamente nel loro assemblaggio finale, soprattutto quando si tratta di ordini personalizzati. Comprendere i diversi tipi di tolleranze e il modo in cui influenzano il processo di lavorazione è fondamentale sia per i produttori che per i clienti. In questa guida, esploreremo gli aspetti chiave di Tolleranze di lavorazione CNC, comprese le tipologie, i fattori che le influenzano e come ottimizzarle per ottenere efficienza dei costi e precisione.
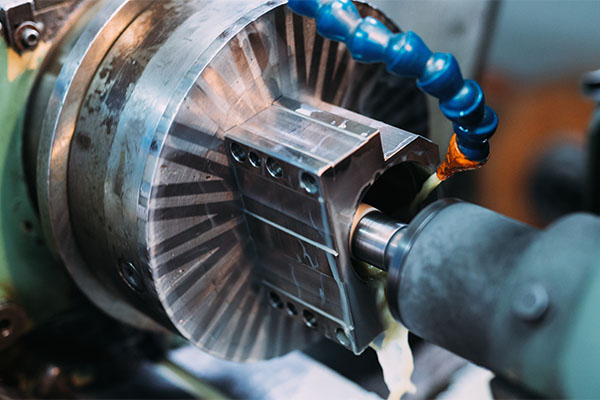
Cosa sono le tolleranze di lavorazione CNC?
Definizione delle tolleranze nella lavorazione CNC
Le tolleranze sono i limiti ammissibili di variazione nelle dimensioni di una parte. Nella lavorazione CNC, questo si riferisce a quanto le dimensioni effettive di una determinata parte possono differire dalle dimensioni di progettazione previste pur essendo accettabili per la funzione. In sostanza, le tolleranze definiscono l'intervallo entro cui la parte può variare e garantiscono che la parte possa ancora adattarsi correttamente al suo assemblaggio previsto.
Esistono due tipi principali di tolleranze nella lavorazione CNC: tolleranze dimensionali E tolleranze geometriche. Le tolleranze dimensionali si riferiscono alla deviazione ammissibile da una misurazione specificata (come lunghezza, larghezza e altezza), mentre le tolleranze geometriche descrivono le deviazioni accettabili nella forma o nella forma di una parte (come rettilineità, planarità o rotondità). Queste tolleranze sono fondamentali per garantire che le parti funzionino correttamente e siano compatibili con altri componenti.
Perché le tolleranze sono fondamentali nella lavorazione CNC
La precisione di una macchina CNC è in gran parte determinata dalla sua capacità di mantenere tolleranze strette. In settori come l'aerospaziale, l'automotive o i dispositivi medici, dove i componenti devono adattarsi perfettamente, le tolleranze diventano ancora più significative. Specificando tolleranze precise, i produttori possono garantire che le parti soddisfino la funzionalità richiesta e siano affidabili in condizioni operative.
Al contrario, se le tolleranze sono troppo larghe, la parte finale potrebbe non soddisfare i criteri di prestazione previsti, portando a costosi errori o guasti. D'altro canto, tolleranze eccessivamente strette possono aumentare i costi di produzione e prolungare inutilmente i tempi di consegna. Raggiungere il giusto equilibrio è essenziale per ottenere sia qualità che efficienza dei costi.
Tipi di tolleranze di lavorazione CNC che dovresti conoscere
Tolleranze dimensionali
Le tolleranze dimensionali definiscono quanto le dimensioni di una parte possono variare dalla misurazione prevista. Queste sono le tolleranze più comunemente specificate nella lavorazione CNC. Ad esempio, un albero potrebbe dover avere una lunghezza di 100 mm, con una tolleranza di ±0,1 mm. Ciò significa che la lunghezza effettiva potrebbe variare da 99,9 mm a 100,1 mm ed essere comunque accettabile.
Le tolleranze dimensionali possono essere applicate a misure lineari (come la lunghezza, la larghezza o l'altezza di una parte) e misure angolari (come gli angoli tra le caratteristiche). Più stretta è la tolleranza, più precisa deve essere la misurazione, il che spesso richiede macchine CNC avanzate e più tempo per la produzione.
Tolleranze geometriche
Le tolleranze geometriche vengono utilizzate per controllare la forma, l'orientamento e la posizione delle caratteristiche su una parte. Queste tolleranze sono fondamentali per garantire che le parti si adattino come previsto. Ad esempio, un foro potrebbe dover essere perfettamente rotondo o posizionato in una posizione precisa rispetto ad altre caratteristiche sulla parte. Le tolleranze geometriche includono:
- rettilineità: Garantisce che una caratteristica, come un bordo o un asse, sia perfettamente dritta.
- Planarità: Garantisce che una superficie sia livellata entro una tolleranza specificata.
- Rotondità: Garantisce che un foro o una caratteristica cilindrica siano perfettamente circolari.
- Posizione: Definisce la posizione esatta di una caratteristica rispetto alle altre.
Specificando queste tolleranze geometriche, i progettisti possono garantire che i componenti soddisfino i criteri funzionali richiesti.
Tolleranze di finitura superficiale
Le tolleranze di finitura superficiale specificano la levigatezza della superficie di una parte. In molte applicazioni, la qualità della superficie può essere critica per le prestazioni della parte, specialmente per i componenti che si muovono o entrano in contatto con altre parti. La finitura superficiale è spesso specificata utilizzando misure di rugosità come Ra (rugosità media), Rz (altezza massima media) e Ry (altezza massima del profilo).
Perché le tolleranze sono importanti: l'impatto sulla qualità e sulla funzionalità delle parti
Il ruolo delle tolleranze nella funzionalità delle parti
Quando si tratta di funzionalità delle parti, le tolleranze applicate durante il processo di lavorazione possono avere un impatto significativo sul fatto che la parte si adatti e funzioni come previsto. Ad esempio, nei componenti automobilistici o aerospaziali, piccole deviazioni nelle dimensioni delle parti possono influire sul modo in cui interagiscono le parti, portando a problemi come adattamenti scadenti, inefficienze o persino guasti sotto stress.
In alcuni casi, una leggera deviazione di dimensioni o forma potrebbe non essere un problema critico. Tuttavia, per applicazioni ad alte prestazioni come componenti di motori, dispositivi medici o strumenti ad alta precisione, anche le più piccole violazioni di tolleranza potrebbero portare a costosi errori e guasti del prodotto. Pertanto, è essenziale capire come scegliere la tolleranza giusta per ogni parte.
Tolleranze e controllo qualità delle parti
Le tolleranze hanno un impatto diretto sul processo di controllo qualità. Tolleranze strette richiedono attrezzature più sofisticate e livelli di ispezione più elevati, assicurando che le parti soddisfino standard rigorosi. Metodi di controllo qualità come macchine di misura a coordinate (CMM) o sistemi di misurazione ottica sono spesso impiegati per verificare che le parti siano entro l'intervallo di tolleranza specificato. Maggiore è la tolleranza, più rigoroso diventa il processo di ispezione.
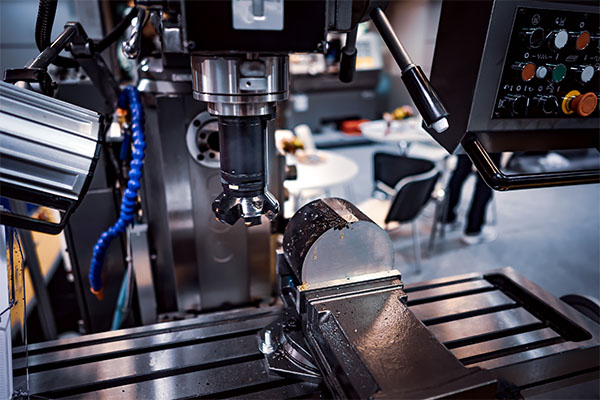
Fattori che influenzano le tolleranze di lavorazione CNC
Proprietà e tolleranze dei materiali
Il materiale scelto per la parte ha un'influenza significativa sulle tolleranze che possono essere raggiunte. Alcuni materiali, come i metalli, possono essere più stabili e più facili da lavorare con tolleranze strette, mentre altri, come la plastica o i compositi, possono subire una maggiore deformazione durante la lavorazione. La durezza del materiale, l'espansione termica e la resistenza svolgono tutte un ruolo nella facilità con cui un materiale può mantenere tolleranze strette.
Ad esempio, metalli come acciaio inossidabile e alluminio sono comunemente usati per la lavorazione CNC perché forniscono un'eccellente stabilità dimensionale e possono raggiungere tolleranze strette senza un'usura eccessiva degli utensili. Tuttavia, materiali più morbidi come plastica o gomma possono richiedere considerazioni speciali per garantire una lavorazione precisa.
Capacità della macchina CNC
Anche il tipo di macchina CNC utilizzata gioca un ruolo cruciale nel determinare il livello di precisione che può essere raggiunto. Le macchine CNC hanno diversi gradi di accuratezza e ogni macchina ha i suoi limiti quando si tratta di mantenere tolleranze strette. Le macchine ad alta precisione come quelle utilizzate nella produzione aerospaziale possono mantenere tolleranze di ±0,001 mm o anche più strette, mentre le macchine per uso generico possono essere in grado di raggiungere tolleranze di ±0,05 mm.
Quando si sceglie una macchina, è essenziale adattare le sue capacità ai requisiti della parte specifica che si sta producendo. Comprendere i limiti della tua attrezzatura CNC ti aiuterà a selezionare la giusta tolleranza per la parte ed evitare regolazioni non necessarie che potrebbero far aumentare i costi.
Utensili e usura
La qualità degli utensili e la loro usura nel tempo possono anche influenzare le tolleranze ottenute nella lavorazione CNC. Quando gli utensili si usurano, possono causare leggere variazioni nelle dimensioni delle parti. Una manutenzione regolare e la sostituzione degli utensili sono essenziali per mantenere una precisione costante.
Per ridurre l'impatto dell'usura degli utensili, molti produttori utilizzano rivestimenti avanzati o utensili in carburo progettati per durare più a lungo e mantenere la loro affilatura. Inoltre, la regolazione dei parametri di lavorazione quali velocità, velocità di avanzamento e profondità di taglio può aiutare a migliorare la precisione del pezzo finito.
Intervalli di tolleranza comuni per la lavorazione CNC per vari materiali
Tolleranze per parti metalliche
Le parti metalliche devono spesso rispettare tolleranze molto strette, soprattutto in settori come quello aerospaziale e automobilistico. Ad esempio, le parti realizzate in acciaio inossidabile possono essere lavorate con una tolleranza di ±0,05 mm, mentre le parti realizzate in alluminio possono raggiungere tolleranze strette fino a ±0,025 mm. Queste tolleranze assicurano che le parti metalliche si adattino correttamente e funzionino bene in condizioni difficili.
Tolleranze per parti in plastica
Le parti in plastica, d'altro canto, sono generalmente più difficili da lavorare con le stesse tolleranze strette dei metalli. La tolleranza per le parti in plastica varia in genere da ±0,1 mm a ±0,5 mm, a seconda del tipo di plastica e della complessità della parte. Le plastiche possono essere soggette a deformazioni, restringimenti o dilatazioni a causa delle variazioni di temperatura, il che può rendere più difficile mantenere tolleranze coerenti.
In alcuni casi, per applicazioni critiche possono essere utilizzate plastiche ad alte prestazioni come PEEK o PTFE. Questi materiali possono raggiungere tolleranze più strette ma richiedono tecniche di lavorazione più avanzate.
Tolleranze per materiali compositi
I materiali compositi, spesso utilizzati in applicazioni aerospaziali e automobilistiche, presentano le proprie sfide quando si tratta di lavorazione CNC. I compositi sono spesso stratificati e possono avere proprietà diverse a seconda della direzione delle fibre, il che può causare variazioni nella resistenza e nella stabilità dimensionale della parte. Le tolleranze per le parti composite variano in genere da ±0,1 mm a ±0,3 mm, a seconda del materiale specifico e della geometria della parte.
Selezione delle tolleranze giuste per i tuoi pezzi lavorati su misura
Identificazione dei requisiti di tolleranza
La scelta delle tolleranze giuste per le tue parti lavorate personalizzate inizia con la comprensione della funzione specifica della parte. Ad esempio, le parti che devono adattarsi insieme o interagire con altri componenti richiedono tolleranze più strette per garantire un allineamento e una funzionalità adeguati. D'altro canto, le parti che non richiedono un montaggio preciso possono essere progettate con tolleranze più ampie per ridurre i costi di produzione.
Per determinare la tolleranza ottimale per una parte, è essenziale considerare sia i requisiti di progettazione sia le capacità del processo di produzione. Tolleranze eccessivamente strette possono aumentare i tempi di produzione, i costi di attrezzaggio e la probabilità di errori, mentre una tolleranza troppo ampia può compromettere la funzionalità o la qualità della parte.
Bilanciamento di precisione e costo
Sebbene possa essere allettante specificare le tolleranze più strette possibili per garantire il massimo livello di precisione, questo spesso comporta un costo più elevato. Ottenere tolleranze più strette richiede in genere macchinari più avanzati, tempi di lavorazione più lunghi e costi di ispezione maggiori. Per molte parti, è più conveniente specificare tolleranze adeguate alla funzione prevista della parte senza esagerare con la precisione.
Trovare il giusto equilibrio tra tolleranza e costo è fondamentale per ottenere sia qualità che efficienza nella lavorazione meccanica personalizzata.
Come le tolleranze influenzano i costi di lavorazione CNC
La relazione tra tolleranze e costi di produzione
Nella lavorazione CNC, esiste una correlazione diretta tra la strettezza della tolleranza e il costo complessivo di produzione. Tolleranze più strette richiedono generalmente una tecnologia più avanzata, una precisione maggiore e più tempo per garantire che la parte rispetti le specifiche. Di conseguenza, i costi di produzione tendono ad aumentare con la necessità di tolleranze più strette. Questo perché è richiesta una maggiore attenzione ai dettagli in ogni fase del processo, dalla progettazione iniziale all'ispezione finale.
Ad esempio, quando si lavora una parte con una tolleranza di ±0,1 mm, la macchina potrebbe dover fare più passaggi o usare utensili specializzati per garantire che vengano raggiunte le dimensioni desiderate. Ciò può aumentare il tempo di lavorazione e l'utilizzo del materiale, entrambi fattori che contribuiscono a costi più elevati. D'altro canto, una parte con una tolleranza di ±0,5 mm potrebbe non richiedere tanto tempo o attrezzature specializzate per essere prodotta, riducendo i costi di produzione.
Inoltre, le parti con tolleranze più strette spesso richiedono un controllo di qualità e un'ispezione più rigorosi. A seconda dell'applicazione, questo può comportare l'uso di strumenti sofisticati come macchine di misura a coordinate (CMM), scansione laser o altri dispositivi di misurazione ad alta precisione. Il costo di questi strumenti, insieme al tempo impiegato per ispezionare ogni parte, può aumentare rapidamente quando si producono componenti con tolleranze molto strette.
Come le tolleranze influenzano i tempi di consegna
Le tolleranze influiscono anche sui tempi di consegna per i progetti di lavorazione CNC. Le parti con tolleranze più strette richiedono una pianificazione più attenta e tempo aggiuntivo per il processo di lavorazione. Ad esempio, una parte che richiede una tolleranza di ±0,01 mm può richiedere diverse ore in più per essere lavorata rispetto a una parte simile con una tolleranza di ±0,5 mm.
Il tempo aggiuntivo necessario per soddisfare tolleranze più strette può anche ritardare la tempistica di produzione complessiva, specialmente in progetti con più parti o geometrie complesse. Inoltre, se si verificano errori di lavorazione durante il processo, potrebbe essere necessario correggerli, portando a ulteriori rilavorazioni e prolungando ulteriormente i tempi di consegna.
Per ridurre al minimo l'impatto delle tolleranze strette sui tempi di consegna, i produttori spesso devono pianificare e ottimizzare attentamente il processo di lavorazione. Ciò può comportare la selezione delle macchine giuste, la regolazione dei parametri di taglio e l'utilizzo dei percorsi utensile più efficienti per garantire che la parte venga completata nei tempi previsti.
Comprendere i limiti delle apparecchiature e degli utensili CNC
Precisione delle macchine CNC e il suo impatto sulle tolleranze
Le capacità delle apparecchiature CNC utilizzate sono un fattore cruciale nel determinare il livello di precisione che può essere raggiunto durante il processo di lavorazione. Diversi tipi di macchine CNC hanno diversi gradi di accuratezza ed è importante comprendere i limiti delle macchine in uso per evitare di stabilire aspettative di tolleranza non realistiche.
Ad esempio, le fresatrici o i torni CNC di fascia alta utilizzati nei settori aerospaziale o medico possono raggiungere tolleranze strette fino a ±0,001 mm. Queste macchine utilizzano tecnologie avanzate come la fresatura multiasse, la calibrazione laser e i sistemi di feedback in tempo reale per mantenere un'estrema precisione.
D'altro canto, le macchine CNC per uso generico potrebbero non essere in grado di mantenere tolleranze così strette e la precisione ottenibile potrebbe essere solo di ±0,05 mm o ±0,1 mm. È essenziale adattare le tolleranze richieste della parte alle capacità dell'attrezzatura CNC disponibile per garantire che la produzione sia fattibile e conveniente.
Scegliere la macchina CNC giusta per il lavoro
Selezionare la macchina CNC giusta per il lavoro è fondamentale per ottenere la tolleranza desiderata. Ad esempio, se la tolleranza richiesta è stretta e la parte ha geometrie complesse, potrebbe essere necessario investire in macchine ad alta precisione, come torni CNC Swiss o fresatrici a 5 assi. Queste macchine offrono la possibilità di lavorare parti complesse con errori minimi, ma comportano costi iniziali più elevati e tempi di produzione più lunghi.
Tuttavia, per parti più semplici con tolleranze più ampie, una fresatrice CNC standard potrebbe essere sufficiente. Scegliere la macchina giusta in base alle tolleranze richieste può aiutare a semplificare la produzione, ridurre i costi e garantire che la parte soddisfi gli standard di qualità.
Utensili e usura degli utensili
Anche la qualità e le condizioni degli utensili utilizzati nella lavorazione CNC svolgono un ruolo significativo nella precisione del prodotto finale. Nel tempo, gli utensili possono usurarsi, con conseguenti variazioni dimensionali e deviazioni dalle tolleranze specificate. Pertanto, una manutenzione regolare e una sostituzione tempestiva degli utensili sono fondamentali per mantenere risultati costanti, soprattutto quando si lavorano parti con tolleranze strette.
Inoltre, il materiale e il rivestimento degli utensili possono influenzare la loro longevità e precisione. Gli utensili in carburo, ad esempio, tendono a mantenere la loro affilatura e stabilità dimensionale nel tempo, rendendoli una scelta preferita per la lavorazione CNC ad alta precisione. Gli utensili rivestiti, come quelli con rivestimenti in nitruro di titanio (TiN) o carbonio simile al diamante (DLC), possono anche aiutare a ridurre l'usura e prolungare la durata dell'utensile, il che è particolarmente importante quando si lavorano materiali difficili o si producono parti con tolleranze strette.
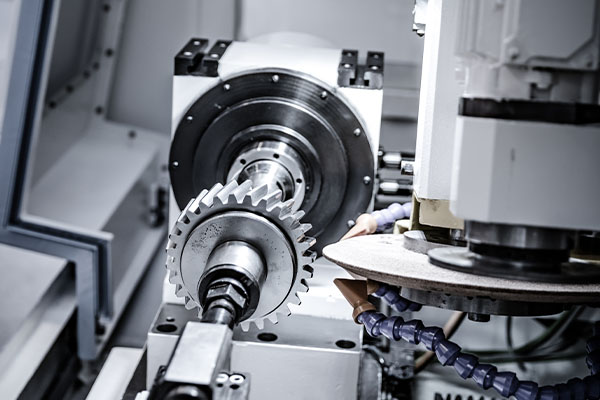
Ottimizzazione delle tolleranze per tempi di consegna più rapidi e costi ridotti
Equilibrio tra precisione ed efficienza
Sebbene tolleranze strette siano necessarie per alcune applicazioni, possono comportare tempi di consegna più lunghi e costi di produzione più elevati. Pertanto, una delle sfide principali nella lavorazione CNC è trovare il giusto equilibrio tra precisione ed efficienza. Ottenere le tolleranze richieste mantenendo bassi i costi di produzione e mantenendo tempi di consegna rapidi è essenziale per soddisfare le richieste dei clienti e rimanere competitivi sul mercato.
Un modo per ottimizzare le tolleranze mantenendo l'efficienza è concentrarsi sulle dimensioni critiche della parte. Non tutte le caratteristiche di una parte devono soddisfare le tolleranze più strette. Identificando quali dimensioni sono più importanti per la funzionalità della parte e applicando tolleranze più strette solo dove necessario, i produttori possono ridurre i tempi e i costi di lavorazione senza compromettere le prestazioni della parte.
Semplificazione del processo di lavorazione
Per ottimizzare i tempi di lavorazione e ridurre i costi, i produttori dovrebbero anche considerare di semplificare il processo di lavorazione. Ciò può essere ottenuto selezionando le giuste strategie di lavorazione, come l'utilizzo degli utensili da taglio più appropriati, la regolazione delle velocità di avanzamento e l'ottimizzazione dei percorsi utensile. Le macchine CNC dotate di funzionalità di automazione avanzate, come i cambiautensili o i sistemi di caricamento automatizzati, possono anche aiutare a ridurre il tempo dedicato a compiti non produttivi, velocizzando ulteriormente il processo.
Un altro modo efficace per ottimizzare le tolleranze è impiegare tecniche di produzione avanzate come la produzione additiva o la lavorazione ibrida. Questi metodi possono spesso raggiungere lo stesso livello di precisione della lavorazione CNC tradizionale, riducendo al contempo lo spreco di materiale, l'usura degli utensili e i tempi di produzione.
Esempi concreti di sfide e soluzioni alla tolleranza
Caso di studio 1: componente aerospaziale con tolleranze strette
Nella produzione aerospaziale, parti come componenti di motori ed elementi strutturali devono rispettare tolleranze estremamente strette per garantire sicurezza e prestazioni. Un esempio concreto riguardava una staffa in alluminio lavorata su misura utilizzata nel sistema di carrello di atterraggio di un aereo. La tolleranza richiesta per questa parte era di ±0,01 mm, il che rappresentava una sfida a causa del potenziale di espansione termica del materiale e della geometria intricata del design.
Per soddisfare i severi requisiti di tolleranza, il produttore ha utilizzato una macchina CNC a 5 assi ad alta precisione con calibrazione laser. Inoltre, ha implementato un processo di lavorazione multi-step che includeva operazioni di sgrossatura di precisione, semi-finitura e finitura. La parte è stata inoltre sottoposta a diversi cicli di controllo qualità utilizzando una macchina di misura a coordinate (CMM) per garantire che soddisfacesse le specifiche richieste.
Caso di studio 2: componente di dispositivo medico con geometrie complesse
Nel settore dei dispositivi medici, componenti come strumenti chirurgici e impianti richiedono un'elevata precisione per garantire il corretto e sicuro funzionamento. Un esempio ha coinvolto la lavorazione di un impianto al ginocchio in titanio, che ha richiesto tolleranze geometriche complesse, tra cui rotondità precisa e tolleranze di posizione per i fori che avrebbero ospitato le viti.
Per ottenere queste tolleranze, il produttore ha utilizzato un tornio svizzero CNC con capacità di utensili motorizzati. Ciò ha consentito loro di lavorare la parte in un'unica configurazione, riducendo il rischio di errori causati dal riposizionamento. La parte è stata quindi ispezionata utilizzando un sistema di misurazione ottica ad alta precisione per garantire che tutte le tolleranze geometriche fossero rispettate.
Controllo di qualità: garantire accuratezza e coerenza nella lavorazione CNC
L'importanza di un'ispezione rigorosa
Il controllo qualità svolge un ruolo fondamentale nell'assicurare che le parti siano entro le tolleranze specificate e soddisfino gli standard richiesti. Nella lavorazione CNC, l'ispezione inizia durante il processo di configurazione e continua durante tutto il ciclo di produzione. Molti produttori utilizzano macchine di misura a coordinate (CMM) e sistemi di scansione laser per misurare le parti in modo accurato e rilevare eventuali deviazioni dalle specifiche desiderate.
L'ispezione può anche comprendere controlli visivi, valutazioni della finitura superficiale e test funzionali, a seconda dell'uso previsto della parte. Per parti con tolleranze particolarmente strette, potrebbero essere necessari ulteriori passaggi di ispezione per garantire che non si verifichino variazioni durante il processo di lavorazione.
Il ruolo dei sistemi di ispezione automatizzati
Con l'avanzare della tecnologia, molti produttori ora si affidano a sistemi di ispezione automatizzati per monitorare la precisione delle parti lavorate tramite CNC. Questi sistemi utilizzano laser, telecamere o altri sensori per controllare continuamente le dimensioni delle parti mentre vengono prodotte. L'ispezione automatizzata non solo migliora la precisione, ma velocizza anche il processo di controllo qualità, consentendo ai produttori di rilevare gli errori in anticipo e prevenire errori costosi.
Miglioramento continuo e cicli di feedback
Oltre alle ispezioni formali, i produttori dovrebbero implementare programmi di miglioramento continuo per monitorare le prestazioni di lavorazione nel tempo. Tracciando parametri chiave come usura degli utensili, prestazioni della macchina e precisione di produzione, i produttori possono identificare aree di miglioramento e apportare le modifiche necessarie per mantenere tolleranze strette in modo coerente.
Il ruolo delle tolleranze negli ordini di lavorazione personalizzati
Specifiche di lavorazione e tolleranza personalizzate
Quando si effettuano ordini di lavorazione personalizzati, i clienti devono comunicare chiaramente i requisiti di tolleranza per evitare incomprensioni o costosi errori. Fornire disegni dettagliati che specifichino le tolleranze desiderate per ogni caratteristica della parte aiuterà a garantire che il processo di lavorazione proceda senza intoppi. I clienti devono anche collaborare con i loro partner di produzione per determinare se le tolleranze specificate sono realizzabili entro i tempi e il budget stabiliti.
Collaborazione con i fornitori di lavorazioni CNC
La collaborazione tra cliente e fornitore è fondamentale per garantire che le tolleranze siano chiaramente comprese e rispettate. Ciò può comportare la discussione delle scelte dei materiali, la revisione delle capacità dell'attrezzatura CNC e la garanzia che la progettazione della parte sia ottimizzata sia per i requisiti di producibilità che di tolleranza.
I fornitori possono spesso fornire preziose informazioni su come adattare i progetti dei pezzi per renderli più facili da lavorare, pur rispettando le specifiche di tolleranza. Lavorando insieme, produttori e clienti possono raggiungere il miglior equilibrio possibile tra precisione, costi e tempi di consegna.

Domande frequenti
Quali sono le tolleranze più comuni per la lavorazione CNC?
Il più comune tolleranze per lavorazioni CNC variano da ±0,05 mm a ±0,5 mm, a seconda della complessità e del materiale della parte. Tolleranze più strette, come ±0,01 mm, sono in genere richieste per applicazioni ad alta precisione come dispositivi aerospaziali o medici.
In che modo le tolleranze influiscono sui costi della lavorazione CNC?
Le tolleranze più strette generalmente aumentano i costi di lavorazione CNC, poiché richiedono attrezzature più avanzate, tempi di lavorazione più lunghi e ispezioni più rigorose. Le tolleranze più larghe possono aiutare a ridurre i costi e i tempi di produzione.
La lavorazione CNC può raggiungere tolleranze strette per tutti i materiali?
Mentre molti materiali, come i metalli, possono raggiungere tolleranze strette con la lavorazione CNC, alcuni materiali, come la plastica e i compositi, sono più difficili da lavorare con elevata precisione a causa delle loro proprietà intrinseche. È importante selezionare il materiale appropriato per la tolleranza richiesta.
Come posso ridurre i costi di lavorazione di pezzi con tolleranze strette?
Per ridurre i costi, concentrati sull'ottimizzazione del design per la producibilità. Specifica le tolleranze solo dove sono necessarie per la funzione della parte e scegli il processo di lavorazione e l'attrezzatura giusti per il lavoro. Collaborare con il produttore può anche aiutare a identificare le aree in cui i costi possono essere ridotti senza sacrificare la qualità.
Quali sono gli utensili migliori per ottenere tolleranze strette nella lavorazione CNC?
Gli utensili in carburo e quelli rivestiti, come quelli con rivestimenti in nitruro di titanio (TiN), sono ideali per ottenere tolleranze strette. Questi utensili mantengono la loro affilatura più a lungo, riducendo il rischio di usura dell'utensile e variazioni dimensionali.