Introduzione
CNC machining has become an essential technology in the manufacturing world, streamlining processes and providing manufacturers with unmatched precision. From creating intricate parts to increasing efficiency in mass production, CNC machines have revolutionized industries. Whether you are new to the field or looking to expand your knowledge, this guide will help you understand the basics of CNC machining, the different types of machines, and how they function. By the end of this article, you’ll have a solid understanding of what CNC machining is, its processes, and why it is vital in today’s manufacturing landscape.
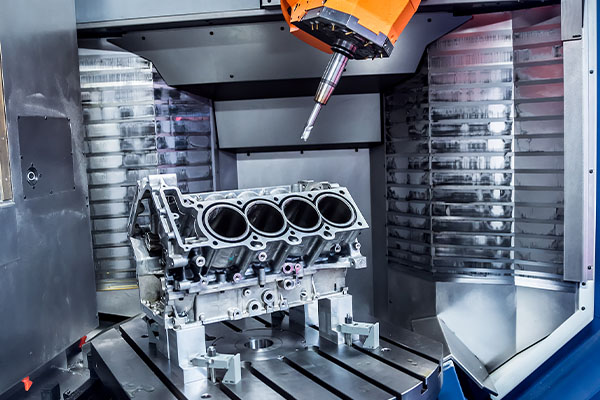
Che cosa è la lavorazione CNC?
CNC machining stands for Computer Numerical Control machining, a process where pre-programmed software controls the movement of tools and machines. Unlike traditional manual machining, where human operators use hands-on control, CNC machining allows for precision and automation in the creation of complex parts. Here’s how it works: CNC machines receive input in the form of coded instructions (G-code), which guides the machine to make exact cuts, turns, and movements needed for the part.
In CNC machining, the machine’s movements are controlled by computers, allowing for higher precision, repeatability, and automation. This level of control means that CNC machining can produce detailed and complex parts with consistent results. The key components of a CNC machine include the controller, which interprets the code; the drive system, which powers the machine’s motions; and the motor, which gives it physical movement. With these components working together, CNC machines can produce high-quality products with minimal human intervention.
The History of CNC Machining
The origins of CNC machining date back to the 1940s and 1950s when the idea of controlling machines via computer programming started to emerge. The first forms of numerical control (NC) were designed to automate the mechanical process of machine tools. However, it wasn’t until the 1960s that CNC technology evolved significantly, as advances in computing and electronics allowed for machines to be fully controlled by computer programs.
The introduction of CNC transformed manufacturing processes by replacing manual labor with automation. This shift led to enhanced precision, speed, and repeatability. The 1980s saw the widespread adoption of CNC in various industries, including automotive and aerospace, where the demand for complex, high-precision parts was growing. Over time, the development of more sophisticated controllers and software further increased the capabilities of CNC machines.
Today, CNC machining is a standard tool in many industries, allowing manufacturers to produce parts that meet the highest standards for precision, quality, and cost-effectiveness. The technology continues to evolve, with advancements in automation, machine learning, and artificial intelligence further improving the efficiency and capabilities of CNC machines.
Types of CNC Machines
CNC machines come in various types, each designed for specific tasks in the machining process. CNC milling machines are some of the most commonly used types, where rotating tools are used to cut and shape the material. Milling machines are versatile and can handle a variety of tasks, from drilling holes to producing intricate shapes.
CNC lathes, on the other hand, are used for turning operations. These machines rotate the workpiece against a cutting tool to create cylindrical parts. Lathes are ideal for producing parts such as shafts, rods, and rings. CNC routers are also widely used, primarily in the woodworking industry, for cutting and shaping wood, plastics, and other soft materials.
Inoltre, CNC EDM (Electrical Discharge Machining) is used to cut hard metals by using electrical sparks to erode material. This method is highly precise and can create complex geometries. CNC plasma and laser cutters offer precision cutting for materials like metals and plastics, often used in industries such as automotive and construction.
Each type of CNC machine offers unique advantages and is chosen based on the specific needs of the project.
CNC Machining Processes
CNC machining encompasses several processes, each suited for different manufacturing needs. Milling is one of the primary processes, involving the use of rotary cutters to remove material from a workpiece. This process can create flat surfaces, grooves, and complex shapes with high precision.
Turning, used primarily in CNC lathes, is a process where the workpiece is rotated against a fixed cutting tool. This is commonly used to make cylindrical components such as shafts, tubes, and rings. Drilling is another critical CNC process that involves creating round holes in a material, with the ability to drill at varying depths and sizes.
In some cases, grinding and polishing are necessary to finish the product to a smooth and precise surface. CNC grinding machines are used to grind parts to exact specifications, while polishing can improve surface quality for aesthetic or functional purposes.
Each of these CNC processes plays an integral role in the production of high-quality parts, ensuring that every component meets the required specifications.
Materiali utilizzati nella lavorazione CNC
The materials used in CNC machining play a significant role in determining the outcomes of the process. Common metals such as aluminum, steel, and titanium are frequently machined due to their strength, durability, and versatility. Aluminum, for instance, is widely used in aerospace and automotive industries because it is lightweight yet strong. Acciaio is often preferred for its toughness and resistance to wear and corrosion, making it suitable for heavy-duty parts.
Plastica such as ABS, nylon, and polycarbonate are also commonly used in CNC machining. These materials are lightweight, easy to machine, and cost-effective, making them ideal for prototypes and consumer products. Composites, including materials like carbon fiber and fiberglass, are used in industries requiring lightweight yet high-strength components.
Wood and foam are also machined with CNC routers for applications in construction, interior design, and prototyping. The choice of material largely depends on the application and the properties required for the final product.
Vantaggi della lavorazione CNC
CNC machining offers numerous benefits that have made it a crucial part of modern manufacturing. One of the most significant advantages is its precision and accuracy. CNC machines are capable of producing parts with extremely tight tolerances, ensuring that each part matches the original design specifications. This level of precision is essential in industries such as aerospace and medical device manufacturing, where safety and performance are critical.
Another advantage is increased productivity. CNC machines can run continuously, often without the need for human intervention, which leads to faster production times. Additionally, complexity of designs is no longer a limitation with CNC machining. The ability to execute intricate and complex shapes is one of the reasons why CNC is preferred over traditional machining.
Automation and efficiency are also key benefits. With CNC machines, the production process becomes more streamlined, reducing manual labor and human error. This not only leads to cost savings but also ensures that production can scale quickly.
Understanding G-code and M-code
G-code and M-code are integral parts of CNC machining, serving as the instructions that control the machine’s movements. G-code, or geometric code, provides instructions for the machine’s motions, including movement along different axes, tool changes, and more. It tells the machine how to move the cutting tool to achieve the desired shape and finish.
M-codes are used to control auxiliary functions, such as turning the spindle on or off, controlling coolant systems, and pausing the machine. These codes work together to give the CNC machine its full range of capabilities. Writing and understanding G-code is a crucial skill for anyone operating CNC machines, as it allows operators to customize the machining process for specific needs.
Programs are written in a text format and then loaded into the CNC machine’s controller, where they are interpreted and executed. Creating an accurate CNC program is essential for ensuring that the machine operates efficiently and produces high-quality parts.
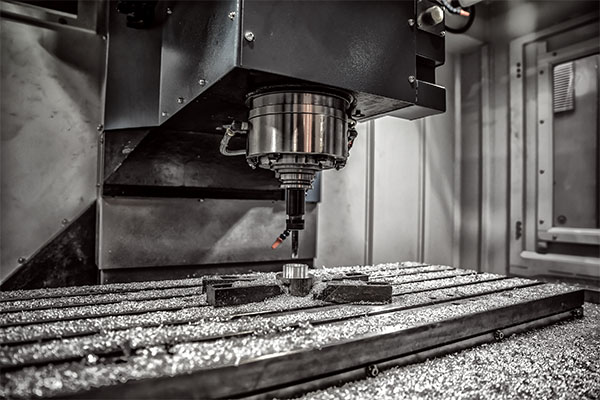
How to Set Up a CNC Machine
Setting up a CNC machine involves several important steps to ensure that the process runs smoothly. Preparing the machine is the first step, which involves checking the machine’s functionality, ensuring that all components are working correctly, and verifying that the tools are in good condition.
Loading the material is another critical step. Workpieces must be carefully secured in the machine’s fixture or chuck to prevent movement during machining, which could lead to inaccuracies. Proper tool selection and calibration are also vital. Tools must be chosen based on the material being machined, and they should be calibrated for accuracy to ensure the right cuts are made.
Once everything is in place, the CNC program is loaded into the machine’s controller. Verifying the program ensures that it’s correct and that the machine will perform the desired operations without issues.
Common CNC Machining Tools
CNC machining requires a variety of tools to perform different tasks. End mills are one of the most commonly used tools. These rotating cutters are used to cut through materials and can handle a range of operations, from shaping to drilling. There are several types of end mills, each designed for specific applications, such as flat mills, ball end mills, and corner radius mills.
Drills and reamers are used for creating holes, with reamers being particularly useful for smoothing and refining holes to exact dimensions. In turning operations, lathes and turning tools are essential for shaping cylindrical parts. These tools are designed to provide precise cuts, helping create parts like shafts and rings.
Taps and dies are used for creating threaded holes and other threaded features. These tools are essential for machining parts that require threaded components, such as bolts and screws.
Lavorazione CNC in diversi settori
CNC machining plays a vital role in various industries, producing parts that require high precision and quality. In the aerospace industry, CNC machining is used to create components that must meet strict specifications for safety and performance. Parts such as turbine blades, landing gear, and structural components are all produced using CNC technology.
Nel automotive industry, CNC machining is used to create parts such as engine blocks, chassis components, and transmission parts. The high precision and efficiency of CNC machines make them ideal for mass production, as well as for creating prototypes for new designs.
Dispositivi medici require the highest levels of precision, and CNC machining is used to create everything from surgical instruments to implants. CNC is also used in produzione elettronica, where it produces components such as circuit boards and connectors.
Challenges in CNC Machining
Despite its many advantages, CNC machining does come with its challenges. One of the limitazioni materiali involves machining harder materials, which can be difficult for some CNC machines to handle. Certain materials, such as superalloys and composites, require specialized tooling and machining techniques.
Usura degli utensili is another issue that can affect the quality of parts. Over time, cutting tools wear down, which can lead to inaccuracies in machining. Regular monitoring and tool replacement are necessary to maintain machining quality.
Managing the complexity of designs can also be challenging. As parts become more intricate, the risk of errors increases, requiring careful programming and monitoring. Additionally, the costs of CNC machining can be high, especially for small-scale production runs, though these costs are often justified by the benefits of precision and automation.
CNC Machining vs. 3D Printing
CNC machining and Stampa 3D are both manufacturing processes, but they operate very differently. CNC machining is a subtractive process, where material is removed from a solid block, whereas 3D printing is an additive process, where material is built up layer by layer.
Lavorazione CNC is better suited for producing parts from a wide range of materials, including metals and composites, with high precision. Stampa 3D is often used for prototyping and creating more complex shapes that may be difficult to achieve with traditional methods.
However, Lavorazione CNC is generally more precise and faster for production runs that require high-quality finished products. Both technologies can be used together, with CNC machining handling parts of high complexity or that require high strength, while 3D printing is used for rapid prototyping.
CNC Machining and Automation
Automation in CNC machining refers to integrating the machines with robotics and computer systems to streamline the production process. CNC machines integrated with automation can run for long periods with minimal human intervention, improving efficiency and reducing labor costs.
Robotics in CNC machining enables machines to handle tasks such as loading and unloading parts, allowing for continuous operation. This integration of automation also leads to fewer errors and faster turnaround times.
IL benefits of automation in CNC machining include improved consistency, reduced setup times, and a decrease in human errors. By automating processes, manufacturers can increase production capacity while ensuring that quality standards are consistently met.
Future Trends in CNC Machining
The future of CNC machining is shaped by smart technology, where machines with AI and machine learning capabilities are becoming more common. These machines can learn from their operations, detect problems before they occur, and optimize the machining process for efficiency.
Another trend is the integration of produzione additiva into traditional CNC machining. Hybrid systems that combine CNC’s subtractive capabilities with 3D printing’s additive abilities are allowing for more complex and customized parts.
Innovations in materials are also on the horizon, with CNC machines being developed to work with stronger, more versatile materials. As CNC machining continues to evolve, it will enable manufacturers to create even more sophisticated parts with greater efficiency.
Conclusione
In conclusion, CNC machining is an essential tool in modern manufacturing, offering precision, efficiency, and versatility across various industries. Whether you’re looking to create a simple part or a complex, high-precision component, CNC machines have the ability to meet these needs with unparalleled accuracy. By understanding the basics of CNC, from the machines to the processes and materials, you are better equipped to navigate the world of manufacturing. If you’re considering implementing CNC machining into your own business, it’s crucial to understand its capabilities and challenges to make informed decisions and optimize your production processes.
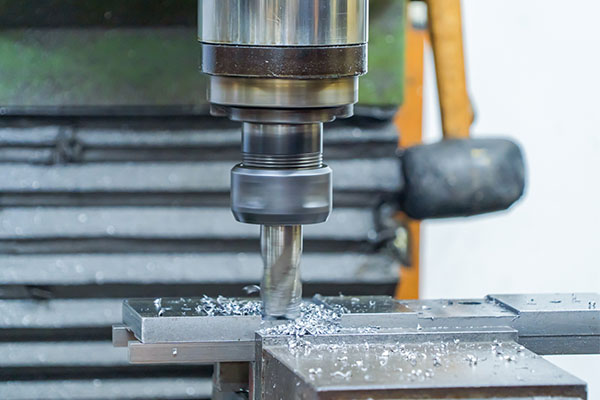
Sezione FAQ
- What is the difference between CNC and manual machining? CNC machining uses a computer program to control machine movements, offering higher precision, repeatability, and automation compared to manual machining, which relies on human operators.
- How accurate are CNC machines? CNC machines are highly accurate, capable of achieving tolerances as tight as a few microns, depending on the machine and tooling used.
- What are the most commonly used CNC machines? Common CNC machines include CNC milling machines, CNC lathes, CNC routers, and CNC laser cutters, each suited for specific tasks.
- Can CNC machines handle all types of materials? CNC machines can work with a wide variety of materials, including metals, plastics, composites, wood, and foam. However, some materials may require specialized tools or machines.
- How do I get started with CNC programming? Learning CNC programming typically involves understanding G-code, the language used to control CNC machines, and learning how to write and edit programs for specific operations.
- What are the costs involved in CNC machining? CNC machining costs depend on several factors, including material, machine type, complexity of the part, and production volume. Higher complexity and lower volumes typically result in higher costs.
- How do I maintain a CNC machine? Regular maintenance of CNC machines involves cleaning, checking for wear, and calibrating tools to ensure continued precision and prevent machine breakdowns.
- Can CNC machining be used for prototyping? Yes, CNC machining is often used for prototyping due to its ability to create precise parts from a range of materials, allowing for functional testing before mass production.
- What’s the lifespan of a CNC machine? The lifespan of a CNC machine depends on usage, maintenance, and the type of machine, but many can last for several decades if properly maintained.