Introduzione
Machining brass is a crucial process in many industries, from automotive to electronics. The material itself offers a combination of strength, corrosion resistance, and ease of machinability, making it ideal for various components. In this guide, we’ll explore everything you need to know about machining brass, including the tools, techniques, and tips that can help you get the most out of this versatile material. Whether you’re new to machining or looking to refine your skills, this article will provide valuable insights and practical advice.
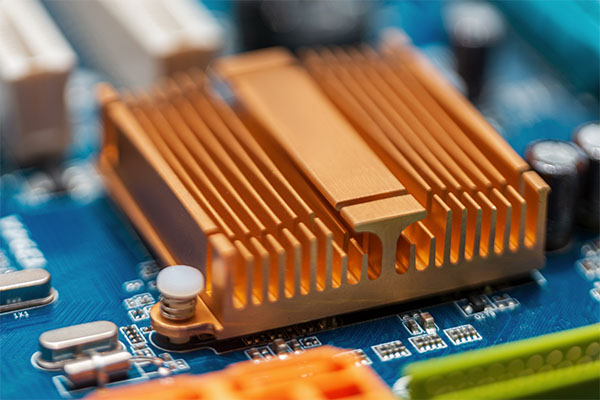
1. What is Machining Brass?
Machining brass is the process of using mechanical tools and equipment to shape brass materials into finished components. Brass is an alloy made primarily of copper and zinc, with varying amounts of other metals added to achieve specific properties. But here’s the kicker: while brass is an excellent material for many applications, it requires careful machining to achieve the desired results.
Brass is a popular choice for manufacturing because of its machinability. It’s easier to work with compared to other metals like steel or iron. This is because brass has a low melting point, which allows it to be easily shaped, drilled, or turned. It also provides excellent resistance to corrosion and is relatively soft compared to other materials, which means it won’t cause excessive wear on cutting tools. So, whether you’re making plumbing fittings, electrical connectors, or decorative parts, brass is often the go-to material.
Now, you might be wondering, how does brass compare to other metals when machining? Brass stands out due to its high machinability index, which means it can be worked with more easily and at higher speeds without compromising tool life. It’s also more forgiving than harder materials, making it a great choice for both experienced machinists and beginners.
Table: Comparison of Machining Brass vs. Steel
Property | Ottone | Acciaio |
---|---|---|
Machinability | Alto | Moderate to Low |
Resistenza alla corrosione | Excellent | Good |
Usura degli utensili | Basso | Alto |
Costo | Moderate | Alto |
2. Why is Brass Popular in Machining?
Brass has gained widespread popularity in machining, especially for high-precision and high-performance applications. But why is it so favored in the industry? Ready for the good part? Brass combines the best of both worlds: strength and ease of machinability. It’s both durable and easy to shape, making it ideal for a wide range of products.
For starters, brass is a versatile material that can be used in a variety of industries. Whether it’s in the manufacturing of musical instruments, plumbing fixtures, or electrical components, brass plays an important role. The alloy’s unique composition allows it to be formed into a variety of shapes without cracking or breaking, which is especially important for items that need to withstand high pressure or friction.
The ability to machine brass at high speeds with relatively low wear on tools makes it a top choice in mass production environments. But here’s where it gets interesting: brass is also a highly corrosion-resistant material. When exposed to moisture or chemicals, it won’t degrade as quickly as other metals, such as iron. This makes brass an excellent choice for outdoor applications or environments where parts are exposed to harsh conditions.
Whether you are machining brass for aesthetic or functional purposes, the combination of machinability, strength, and corrosion resistance makes it an all-around excellent material.
Table: Applications of Brass in Machining
Area di applicazione | Example Products |
---|---|
Electrical | Connectors, switches |
Plumbing | Faucets, valves |
Automobilistico | Cuscinetti, ingranaggi |
Music | Wind instruments |
3. What Are the Challenges in Machining Brass?
Machining brass comes with its own set of challenges, but don’t worry—there are solutions to every problem. What’s the real story? While brass is relatively easy to machine, it’s not without its issues. These challenges typically revolve around controlling heat, managing chips, and preventing tool wear.
One of the primary challenges when machining brass is the heat generated during cutting. Brass has a high thermal conductivity, which means it heats up quickly during machining. If not controlled, this heat can lead to tool wear, poor finish quality, and even material distortion. So, how can this be avoided? Using the right cutting speeds and coolants is crucial. Cutting at the appropriate speeds will help manage heat buildup, while using the right coolant will keep the workpiece and the tool cool.
Another issue is the brass chips produced during machining. Because brass is a relatively soft material, the chips it produces can be long and stringy, making it harder to clear them from the work area. These chips can also damage the surface finish or cause clogs in the machinery if not managed properly. To avoid this, you’ll need to use an efficient chip management system and regularly clear away debris from the work area.
Lastly, despite its machinability, brass is still prone to tool wear. The material can cause friction and wear on cutting edges, so using high-quality cutting tools that are specifically designed for brass machining is essential. Maintaining sharp tools and regularly inspecting them for damage will help ensure better results and longer tool life.
Table: Common Challenges in Brass Machining
Sfida | Soluzione |
---|---|
Heat Buildup | Use proper cutting speeds, apply coolants |
Chip Management | Use chip removal systems, clear debris regularly |
Usura degli utensili | Use high-quality tools, maintain sharpness |
4. What Tools Are Used for Machining Brass?
When machining brass, the right tools make all the difference. Let’s dive into the tools you’ll need and how they contribute to the process. You might be asking, what’s the best equipment to use when working with brass? The answer depends on the type of machining you’re doing.
For turning, CNC lathes are widely used. These machines can accurately cut and shape brass into precise components, whether you’re producing a small batch or mass production runs. Milling machines are another critical tool in brass machining, especially for cutting complex shapes. These machines can handle detailed, intricate designs with ease, making them indispensable for brass machining.
Drill presses are often used for making holes in brass. They allow for accurate hole placement, whether you’re drilling small or large holes. But here’s where it gets interesting: when machining brass, it’s essential to use tools that are specifically designed to work with the material. High-speed steel (HSS) tools are a popular choice, but carbide-tipped tools are often recommended for extended tool life.
Finally, you’ll need a proper measuring tool. Calipers and micrometers are often used to ensure that the final product is within the required tolerance.
Table: Tools for Machining Brass
Attrezzo | Applicazione |
---|---|
CNC Lathe | Turning and shaping brass |
Milling Machine | Complex cutting and shaping |
Drill Press | Drilling holes |
Calipers | Measuring dimensions |
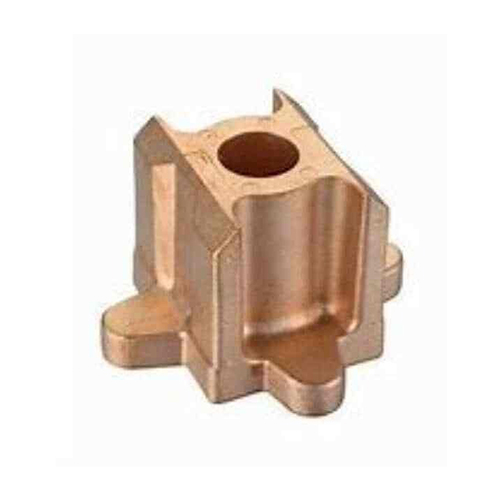
5. How to Choose the Right Brass Alloy for Your Project?
Choosing the right brass alloy is key to ensuring the success of your machining project. Ready for the good part? Brass comes in a variety of alloys, each with unique characteristics that make it suited to different applications. The alloy you choose will depend on factors like strength, corrosion resistance, and machinability.
The most common brass alloys are yellow brass, red brass, and leaded brass. Yellow brass, composed of 60% copper and 40% zinc, is the most commonly used type and is ideal for general-purpose applications. Red brass, which contains more copper and a small amount of tin, is stronger and more resistant to corrosion. Leaded brass, which includes a small percentage of lead, is known for its excellent machinability, making it a good choice for high-precision machining.
What’s the real story here? The alloy you select will directly affect the cost and performance of your parts. For example, if you need a high-strength component that’s exposed to harsh chemicals, red brass may be the best choice. On the other hand, if you’re focused on machinability and cost-effectiveness, yellow brass or leaded brass could be the better option.
Table: Comparison of Common Brass Alloys
Brass Alloy | Composition | Key Benefits |
---|---|---|
Yellow Brass | 60% Copper, 40% Zinc | General-purpose, cost-effective |
Red Brass | 85% Copper, 5% Tin, 5% Zinc | Corrosion-resistant, stronger |
Leaded Brass | 60-65% Copper, 3-5% Lead | Excellent machinability |
6. What Are the Different Machining Processes for Brass?
Machining brass involves several different processes, each suited to specific tasks. You might be wondering, what are the best processes for working with brass? The most common machining processes for brass include turning, milling, drilling, and grinding.
Turning is used to shape the material into cylindrical forms, while milling is ideal for cutting complex shapes. Drilling is commonly used to create holes, and grinding is used to achieve a fine finish. Each process requires different equipment and tooling, and the choice of process depends on the desired final product.
So, here’s where it gets interesting: understanding which process to use for each part is crucial. For example, if you’re making a round part, turning is the way to go. However, if you need to cut intricate shapes, milling may be the better choice. The key is to match the process to the desired outcome.
Table: Common Brass Machining Processes
Processo | Best For |
---|---|
Turning | Shaping cylindrical parts |
Milling | Cutting complex shapes |
Drilling | Creating holes |
macinazione | Achieving fine surface finishes |
7. How Does Cutting Speed Affect Brass Machining?
Cutting speed plays a significant role in the machining process, especially when working with brass. You might be thinking, how can cutting speed influence the quality and efficiency of my machining? Well, the cutting speed directly impacts both the heat generated during machining and the tool’s longevity.
Brass, due to its high thermal conductivity, tends to heat up quickly during machining. If the cutting speed is too high, it can cause excessive heat, which may lead to premature tool wear and subpar surface finishes. Conversely, cutting too slowly can result in inefficient machining and increased production time.
The key is to find the optimal cutting speed for your specific brass alloy. For example, yellow brass typically requires a cutting speed range of 100 to 300 feet per minute (fpm), while red brass may need a slower speed due to its higher copper content. You should also consider the type of tool you’re using—carbide tools can withstand higher cutting speeds compared to high-speed steel (HSS) tools.
Here’s the real story: fine-tuning the cutting speed for each job is essential for maximizing tool life and producing high-quality parts. For high-volume production, adjusting cutting speeds to match the material’s properties will help achieve consistency and efficiency.
Table: Optimal Cutting Speeds for Different Brass Alloys
Brass Alloy | Recommended Cutting Speed (fpm) | Ideal Tool Material |
---|---|---|
Yellow Brass | 100-300 | High-speed Steel (HSS) |
Red Brass | 50-200 | Carbide |
Leaded Brass | 150-400 | Carbide |
8. What Are the Best Coolants for Machining Brass?
Coolants are vital when machining brass, especially given the heat generated during cutting. What’s the real story here? Using the right coolant can dramatically improve both the quality of the finish and the life of your tools.
There are several types of coolants that work well with brass, each offering different benefits depending on the machining process. Water-soluble coolants are commonly used because they offer excellent heat dissipation. These coolants help lower temperatures by providing a barrier between the tool and the material, thereby reducing friction.
Oil-based coolants, on the other hand, offer superior lubrication, which is beneficial when working with tougher brass alloys. They create a thin film that reduces wear and tear on cutting tools. But here’s the kicker: while oil-based coolants are effective, they can be harder to clean and may require additional steps to maintain.
In recent years, synthetic coolants have gained popularity due to their ability to provide both lubrication and cooling without the need for oils. These coolants are often biodegradable, making them more environmentally friendly.
Table: Types of Coolants for Brass Machining
Coolant Type | Key Benefits | Caso d'uso ideale |
---|---|---|
Water-soluble | Excellent cooling, cost-effective | General machining |
Oil-based | Superior lubrication | Lavorazione ad alta velocità |
Synthetic | Biodegradable, dual-function | Environmentally conscious machining |
9. How to Prevent Brass from Overheating During Machining?
Overheating is one of the primary challenges when machining brass. But here’s where it gets interesting: controlling the temperature not only extends the life of your tools but also ensures that you achieve the best surface finish.
One effective way to prevent overheating is by controlling the cutting speed. As mentioned earlier, adjusting the speed ensures that the brass doesn’t heat up excessively during machining. Using the correct cutting parameters is essential to avoid material deformation, tool wear, or poor-quality finishes.
Another important step is to maintain proper coolant flow. Coolants not only keep the tool cool but also remove the heat generated by the cutting process. Choosing the right coolant for the job and applying it consistently is essential. Additionally, using the correct tool material can help reduce heat buildup. Carbide tools, for example, are much more resistant to heat than HSS tools.
So, what’s the solution? By fine-tuning these elements—cutting speed, coolant application, and tool choice—you can keep brass cool and machined to perfection.
Table: Ways to Prevent Overheating During Brass Machining
Metodo | Beneficio | Key Consideration |
---|---|---|
Control Cutting Speed | Reduces friction and heat buildup | Adjust based on brass alloy |
Use Proper Coolants | Keeps temperature low, enhances finish | Choose between water-soluble, oil-based, or synthetic |
Use Carbide Tools | Better heat resistance than HSS | Ideal for high-speed machining |
10. What Is the Role of Tool Wear in Brass Machining?
Tool wear is an inevitable part of machining, but what does it really mean for brass machining? Well, the wear and tear on your tools can significantly affect both the quality and cost-effectiveness of your machining process.
As tools wear down, they become less effective at cutting brass, which can lead to rougher finishes, dimensional inaccuracies, and even material damage. So, how do you keep your tools in top condition? Regular monitoring of tool wear is key. This includes checking for signs of dullness, chipping, or uneven wear patterns. When tools wear out, they also generate more heat, which exacerbates the problem.
Another factor to consider is the material of the tool. High-quality carbide tools typically have a longer lifespan compared to HSS tools. Carbide tools also retain their sharpness better, ensuring consistent performance over time. But here’s the kicker: even carbide tools will wear out eventually, especially when machining tougher alloys.
To minimize the impact of tool wear, it’s essential to use the right tool for each job, regularly inspect tools, and replace them before they become too worn.
Table: Tool Materials and Wear Resistance
Tool Material | Durability | Miglior caso d'uso |
---|---|---|
High-speed Steel (HSS) | Moderate | General-purpose machining |
Carbide | Alto | High-speed, tough materials |
Ceramic | Very High | Extremely abrasive materials |
11. How to Achieve a Smooth Finish on Brass?
Achieving a smooth finish on brass is an essential aspect of machining, especially for parts that require high precision or aesthetic appeal. Ready for the good part? A smooth finish not only improves the appearance of the part but also enhances its function, especially in applications like electrical connectors or fittings.
The first step in achieving a smooth finish is to ensure that the machining parameters—such as cutting speed and feed rate—are set correctly. Higher cutting speeds generally lead to a finer finish, but if set too high, they can cause roughness. Additionally, using the right cutting tools with sharp edges ensures that the brass is cut cleanly without leaving marks or burrs.
Polishing is another critical step to achieve a smooth finish. After the initial machining process, brass parts can be polished using abrasive wheels or rotary tools to remove any minor surface imperfections. Another option is electroplating, where a thin layer of metal is applied to the surface for added smoothness and protection.
So, how do you ensure a flawless finish? It’s a combination of using the right settings, tools, and post-machining processes. The right approach guarantees that the brass component meets the desired specifications.
Table: Techniques for Achieving a Smooth Brass Finish
Tecnica | Descrizione | Best for |
---|---|---|
Lucidatura | Removes surface imperfections | Final finish |
Galvanotecnica | Adds a thin layer of metal for smoothness | High-precision parts |
Abrasive Finishing | Uses abrasive wheels to smooth surfaces | Removing burrs and scratches |
12. What Are the Common Mistakes to Avoid in Brass Machining?
When machining brass, there are several common mistakes that can negatively impact the quality of your work. But here’s the kicker: avoiding these mistakes is the key to achieving better results and reducing production costs.
One of the most common mistakes is using the wrong cutting speed. As we’ve seen, if the speed is too high, it leads to overheating, tool wear, and poor-quality finishes. Conversely, cutting too slowly can result in inefficient machining.
Another mistake is failing to manage brass chips effectively. Brass tends to produce long, stringy chips that can clog machines and ruin surface finishes. Using an efficient chip removal system and frequently clearing the chips from the machine helps avoid this issue.
Finally, using worn-out or inappropriate tools can lead to poor results. Dull tools can cause excessive heat buildup and increase the likelihood of inaccurate cuts. Regularly checking and replacing tools ensures consistent results.
So, what’s the solution? Stay aware of these common pitfalls and take proactive steps to avoid them. By doing so, you’ll improve the efficiency and quality of your brass machining projects.
Table: Common Brass Machining Mistakes and Solutions
Mistake | Soluzione |
---|---|
Incorrect Cutting Speed | Adjust based on material and tooling |
Ineffective Chip Management | Use chip removal systems and clear regularly |
Using Worn Tools | Regular tool inspections and replacements |
13. What Are the Benefits of Using CNC Machines for Brass Machining?
CNC machines offer numerous advantages when machining brass. What’s the real story here? The key benefits include precision, efficiency, and repeatability, making CNC machines ideal for high-volume production runs.
CNC (Computer Numerical Control) machines are automated, which means they can produce highly precise components without the need for constant operator input. This is especially important when machining brass, where maintaining consistency is crucial for producing high-quality parts. CNC machines also offer high cutting speeds and can perform multiple operations in a single pass, improving overall efficiency.
But here’s where it gets interesting: CNC machines can handle complex geometries and intricate details that would be difficult to achieve with manual machines. Whether you’re making decorative items or highly technical components, CNC machines offer the versatility needed for a wide range of brass machining projects.
Table: Advantages of CNC Machines in Brass Machining
Beneficio | Descrizione |
---|---|
Precisione | High accuracy and consistency in machining |
Efficiency | Faster production with less manual labor |
Versatility | Can handle complex shapes and designs |
14. How Can You Improve Efficiency in Brass Machining?
Improving efficiency is crucial for any machining operation, especially when working with a material like brass. Ready for the good part? Efficiency boosts not only reduce costs but also ensure that production timelines are met.
One way to improve efficiency is by optimizing machine settings. Adjusting cutting speeds, feed rates, and tool paths ensures that you’re maximizing the potential of your machines while avoiding unnecessary delays. Additionally, regular maintenance of equipment helps prevent breakdowns that can slow down production.
Another method is to automate certain aspects of the machining process. Automating repetitive tasks, such as part loading and unloading, reduces downtime and human error. For example, using a robot arm to load and unload brass components while the CNC machine continues cutting will keep the operation running smoothly.
So, the solution lies in combining optimization, automation, and maintenance to achieve maximum efficiency in brass machining.
Table: Methods to Improve Brass Machining Efficiency
Metodo | Beneficio |
---|---|
Optimize Machine Settings | Reduces production time and increases tool life |
Automate Processes | Reduces downtime and human error |
Regular Maintenance | Prevents breakdowns and ensures smooth operation |
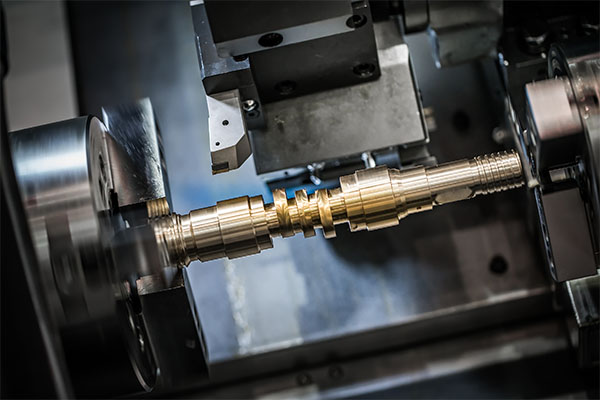
15. How to Maintain and Care for Brass Machining Tools?
Proper tool maintenance is essential for achieving high-quality brass machining. What’s the real story? By keeping tools in good condition, you can improve machining efficiency and extend tool life.
Routine cleaning and inspection are key components of tool maintenance. Tools should be regularly cleaned to remove any chips, dust, or coolant residue that can cause damage or affect performance. Additionally, inspecting tools for signs of wear or damage allows you to replace or sharpen them before they impact the quality of your work.
Another important aspect of tool maintenance is storage. Storing tools in a dry, clean environment helps prevent corrosion, which is especially important when working with brass, a material prone to oxidation. Finally, sharpening tools regularly ensures that they remain sharp and effective.
So, by staying on top of these practices, you can ensure your tools stay in great condition and continue to perform at their best.
Table: Tool Maintenance Practices
Pratica | Beneficio |
---|---|
Regular Cleaning | Removes debris and maintains tool performance |
Routine Inspection | Identifies wear and damage early |
Proper Storage | Prevents rust and prolongs tool life |
Sezione FAQ
Domanda 1: What is machining brass?
Machining brass is the process of shaping brass into parts using tools such as lathes, drills, and mills.
D2: How does machining brass work?
Machining brass involves cutting, drilling, turning, or milling to create specific shapes or parts.
D3: What tools are best for machining brass?
The best tools for machining brass include CNC lathes, milling machines, drill presses, and calipers.
D4: How can I prevent overheating during brass machining?
To prevent overheating, use proper cutting speeds and ensure the use of coolants to maintain optimal temperatures.
D5: Why is brass used in machining?
Brass is used because it offers excellent machinability, corrosion resistance, and versatility for a wide range of applications.