Introduzione
ABS (Acrylonitrile Butadiene Styrene) is a versatile plastic material used in a variety of manufacturing processes, particularly in CNC machining. The material is popular because of its toughness, ease of processing, and relatively low cost, making it suitable for both prototyping and end-use parts. In this guide, we will walk you through the various aspects of machining ABS material—from understanding its properties and benefits to mastering the right techniques for machining it.
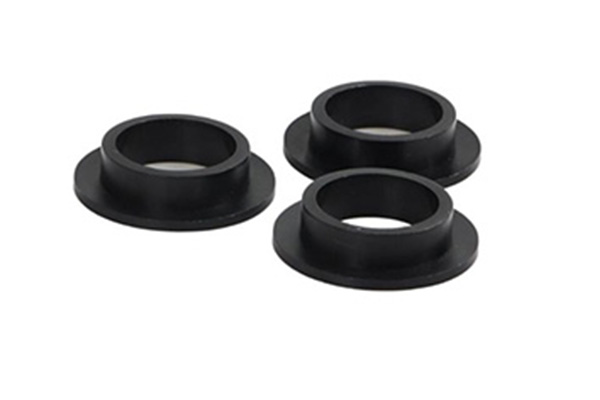
1. Why is ABS Material Popular in CNC Machining?
ABS material is widely used in CNC machining due to its combination of physical and mechanical properties. But here’s the kicker: ABS offers a unique balance of strength, durability, and flexibility, making it a top choice for a range of industries. It’s used in everything from consumer electronics to automotive parts, medical devices, and even toys. Why? Because it is impact-resistant, easy to machine, and relatively affordable compared to other engineering plastics.
The material is most commonly used in prototyping, where precision and fast turnaround are essential. Its excellent machinability makes it ideal for CNC milling and turning, allowing manufacturers to create complex designs with relative ease. ABS also exhibits high-temperature resistance, making it useful in automotive and electronic applications, where heat dissipation is necessary.
Now, let’s take a look at a table to highlight some of the key reasons ABS is favored for CNC machining.
Key Advantages of ABS Material
Property | Descrizione |
---|---|
Impact Resistance | ABS is highly resistant to impact and shock. |
Ease of Machining | ABS is easy to mill, cut, and turn. |
Temperature Resistance | ABS can withstand higher temperatures without losing strength. |
Cost-Effectiveness | ABS is one of the more affordable engineering plastics. |
ABS material is used in applications across various sectors like automotive, electronics, and even medical industries. So, why does it keep coming up as the material of choice for many? It’s simply the combination of these attributes that makes ABS material so attractive for CNC machining.
2. How Do You Choose the Right ABS Material for Machining?
Not all ABS materials are created equal, so it’s important to choose the right type for your machining process. Ready for the good part? The correct ABS grade can dramatically affect the performance, cost, and durability of your final product. When choosing ABS material for CNC machining, several factors come into play, including the grade of ABS, thickness, and whether the material is unmodified or reinforced.
For example, standard ABS is often used for non-structural applications, but when higher strength is required, reinforced grades, such as ABS/PC (polycarbonate) blends, are more suitable. ABS/PC blends offer better impact resistance and are often used in automotive parts where the material needs to endure harsh conditions. Moreover, the thickness of ABS material can impact machining time and the tools required. Thicker ABS may take longer to cut and might require more specialized equipment to ensure a smooth finish.
So, what’s the real story when it comes to selecting the right ABS? It’s about aligning the material’s properties with your specific machining needs and expected product performance. Check out this table to summarize the different types of ABS grades and their applications.
Types of ABS Material and Their Applications
ABS Grade | Applicazione | Properties |
---|---|---|
Standard ABS | Consumer electronics, household items | General-purpose, easy to machine |
ABS/PC Blend | Automotive parts, safety equipment | Improved strength and heat resistance |
Flame-Retardant ABS | Electrical and electronic housings | Flame-resistant, stable at high temperatures |
Glass-Filled ABS | Structural components, automotive applications | Increased strength, heat resistance |
Choosing the right grade of ABS material is critical to ensuring that your final product performs well and meets all necessary standards. In CNC machining, this decision will impact both the speed of production and the quality of the finished product.
3. What Are the Key Properties of ABS Material?
Understanding the key properties of ABS material is crucial to mastering its machining. But here’s where it gets interesting—ABS offers a mix of physical, chemical, and thermal properties that make it uniquely suited for CNC machining. Its versatility is unparalleled.
One of the key properties of ABS is its impact resistance, making it ideal for applications requiring durability and toughness. ABS can withstand significant force and is less likely to crack or break compared to other materials like acrylic or polystyrene. Additionally, ABS has excellent chemical resistance, meaning it won’t degrade easily when exposed to a variety of chemicals, oils, and other substances.
What’s more, ABS has excellent thermal stability. This means that it retains its strength and shape even when exposed to relatively high temperatures, making it useful for parts exposed to heat. However, ABS can soften at temperatures above 100°C, which is why it’s not ideal for extreme temperature environments.
Let’s look at the following table, which summarizes the main properties of ABS and their relevance in CNC machining.
Properties of ABS Material
Property | Descrizione |
---|---|
Impact Resistance | ABS is highly resistant to physical impact. |
Chemical Resistance | ABS can resist a wide range of chemicals. |
Thermal Stability | ABS performs well under moderate temperature conditions. |
Ease of Processing | ABS is easy to machine, shape, and mold. |
ABS material’s combination of these key properties makes it a popular choice for CNC machining in a variety of industries.
4. What Are the Common ABS Machining Techniques?
ABS material can be processed using a variety of machining techniques. But here’s the kicker—knowing which technique to use is the key to achieving precise results. The most common ABS machining techniques include CNC milling, CNC turning, and 3D printing. Each technique offers its own set of advantages depending on the specific requirements of the project.
Fresatura CNC is widely used for machining ABS, particularly for creating complex geometries and fine details. The process involves using rotary cutters to remove material from a workpiece, allowing manufacturers to produce highly detailed parts. CNC turning, on the other hand, is used for creating cylindrical parts. This process involves rotating the workpiece while a cutting tool removes material to achieve the desired shape. ABS is particularly well-suited for both CNC milling and turning due to its ease of cutting and shaping.
Then, there’s Stampa 3D, which is growing in popularity for ABS material. ABS filament is used in many 3D printers to create prototypes and even end-use parts. The material’s ability to be layered and shaped without the need for complex tooling makes it ideal for 3D printing applications.
So, what’s the real story with ABS machining? The choice of technique depends on the specific application and design complexity. Here’s a comparison table of the different machining methods used for ABS.
ABS Machining Techniques
Tecnica | Ideal Application | Key Benefits |
---|---|---|
Fresatura CNC | Detailed geometries, high-precision parts | Precise and versatile, great for complex designs |
Tornitura CNC | Cylindrical parts, automotive components | Great for high-volume production |
Stampa 3D | Prototyping, custom small-run parts | Fast prototyping, no tooling required |
Each machining method has its own strengths, and understanding which one to use for your ABS project is essential to ensuring optimal results.
5. How Do You Prevent Common Machining Problems with ABS?
ABS machining can come with its challenges, and understanding how to prevent these issues is key to producing quality parts. Ready for the good part? Let’s dive into the common problems you might encounter while machining ABS, along with tips on how to avoid them.
One of the most common issues in ABS machining is warping, which occurs when the material deforms due to uneven cooling or stress. To prevent warping, make sure to evenly distribute heat during the machining process and use the correct tooling. Usura degli utensili is another issue that can arise, especially when machining ABS at high speeds. Using the right cutting tools and maintaining them regularly can help avoid this issue.
Another issue is burring, which is the creation of rough edges or shavings during the cutting process. Burrs can interfere with the finished product’s quality, so it’s essential to address this by using proper tool geometry and adjusting cutting speeds.
So, how do you handle these issues? It’s about understanding the material and adjusting your machining methods accordingly. Here’s a table to help summarize the most common ABS machining problems and solutions.
Common ABS Machining Issues and Solutions
Problem | Cause | Soluzione |
---|---|---|
Warping | Uneven cooling or stress during machining | Use consistent cooling methods and support the material during processing |
Usura degli utensili | High machining speeds and dull cutting tools | Regularly replace and sharpen tools, adjust cutting speeds |
Burring | Incorrect tool geometry and cutting speeds | Use appropriate tools, adjust feeds and speeds |
By knowing these common problems and how to prevent them, you’ll be better equipped to tackle ABS machining projects with confidence.
6. How Do You Achieve the Best Surface Finish When Machining ABS?
Achieving the best surface finish when machining ABS material can be tricky, but with the right approach, it’s absolutely possible. What’s the real story here? The surface finish of ABS parts plays a crucial role in their aesthetic appeal and functionality, especially in industries like consumer electronics and automotive. Surface imperfections can affect the part’s performance and its ability to fit seamlessly with other components.
To get a smooth finish, it’s essential to pay attention to the choice of tooling, cutting speeds, and cooling methods. Sharp cutting tools are key in reducing roughness. Dull tools can lead to excessive friction, creating heat that can cause ABS to melt or deform, leading to a poor surface finish. Also, appropriate spindle speeds are crucial—too fast or too slow can both result in an uneven finish. Moderate speeds that match the material’s properties will help achieve a finer surface.
Another aspect to consider is cooling. ABS tends to soften when exposed to heat, so controlling the temperature during machining is essential. Using air or mist cooling systems can help minimize heat buildup and maintain the integrity of the material during the process.
Let’s dive into a table that sums up the key factors affecting surface finish and ways to address them.
Factors Affecting Surface Finish
Fattore | Descrizione | Soluzione |
---|---|---|
Tool Sharpness | Dull tools create rough surfaces | Regularly sharpen or replace tools |
Spindle Speed | Incorrect speeds can cause uneven surfaces | Use moderate, material-specific speeds |
Cooling | Excessive heat can soften ABS and affect finish | Use air or mist cooling to maintain stability |
Achieving the best surface finish on ABS requires careful attention to these details. If you follow these guidelines, your machined ABS parts will not only perform better but also look better, giving your products a professional appearance.
7. How Do You Handle ABS Material During Post-Processing?
Post-processing is an often overlooked but crucial step when working with ABS material. This step can have a huge impact on the final appearance, function, and quality of the part. So, what’s the real story here? Post-processing helps refine the finished part and removes any imperfections caused during the machining process. It can involve processes like cleaning, deburring, polishing, and assembly.
Pulizia is the first post-processing step. ABS can accumulate debris, oils, or residue from the machining process, which needs to be removed for the part to function properly. Using gentle solvents like isopropyl alcohol and a soft cloth can help clean the surface without damaging the material.
Deburring follows cleaning. During machining, ABS parts can develop rough edges or burrs, which can affect the fit or function of the part. You can remove burrs using manual tools, such as deburring knives or a fine-grit sanding block. For larger production runs, vibratory finishing O abrasive blasting may be used for faster results.
Polishing is often the final step to improving the aesthetics of the ABS part. It’s especially important when working with parts that will be visible, such as automotive components or consumer electronics. Using a polishing wheel and appropriate abrasive compounds can give the surface a smooth, glossy finish.
Here’s a table to summarize the different post-processing steps for ABS.
Post-Processing Steps for ABS
Fare un passo | Descrizione | Tools/Methods Used |
---|---|---|
Pulizia | Removes oils, debris, and residue | Isopropyl alcohol, soft cloth |
Deburring | Eliminates rough edges and burrs | Deburring knives, fine-grit sandpaper, vibratory finishing |
Lucidatura | Improves the surface finish and aesthetics | Polishing wheel, abrasive compounds |
Post-processing ensures that the ABS part meets the required specifications and is ready for use. It enhances both the look and function of the finished product, improving overall quality.
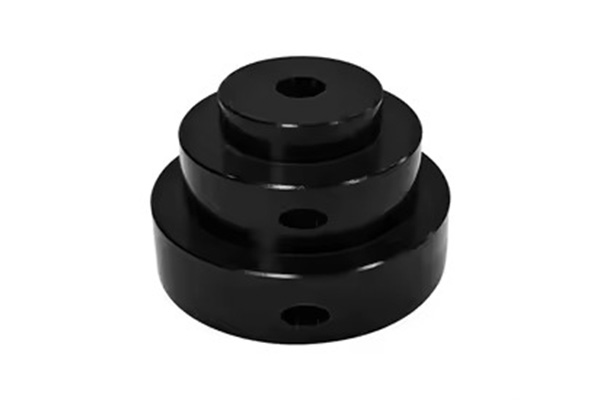
8. What Are the Environmental Considerations for ABS Material Machining?
Sustainability is becoming an increasingly important consideration in the manufacturing world, and ABS material machining is no exception. What’s the real story? ABS is a synthetic plastic, and while it has great advantages, its environmental impact can’t be ignored. However, with proper planning and responsible practices, the environmental footprint of ABS machining can be minimized.
Recycling ABS is a viable option. ABS can be melted down and reformed, allowing manufacturers to reuse the material in new products. This process can save on raw material costs and help reduce waste. In fact, many companies today use recycled ABS in their manufacturing processes, especially in non-critical applications where absolute precision isn’t required.
Un'altra considerazione importante è waste management. During machining, ABS parts can generate scrap material. Minimizing this waste by optimizing the machining process can help reduce environmental impact. Many companies are turning to more efficient cutting strategies to minimize waste and increase material utilization.
Let’s take a look at a table summarizing some of the environmental considerations when machining ABS.
Environmental Considerations
Fattore | Descrizione | Soluzione |
---|---|---|
Recycling | ABS can be recycled to create new products | Implement recycling programs for ABS scraps |
Waste Generation | ABS machining creates scrap material | Optimize cutting strategies to reduce waste |
Energy Use | Energy-intensive processes may have environmental impacts | Use energy-efficient equipment and practices |
By being mindful of these environmental considerations, ABS machining can be made more sustainable without compromising quality.
9. How Does ABS Material Compare to Other Plastics in Machining?
When it comes to CNC machining, ABS is often compared to other common plastics like polycarbonate, acrylic, and nylon. But here’s the kicker—ABS offers distinct advantages and drawbacks compared to these materials. It’s essential to understand how it stacks up in order to make an informed decision when choosing a material for a project.
For example, polycarbonate is another tough material, but it has superior impact resistance compared to ABS. However, polycarbonate is more difficult to machine and requires more careful handling. On the other hand, acrylic is easier to machine than ABS but lacks the same toughness and is more prone to cracking under stress.
Nylon, a widely used material in industrial applications, offers better wear resistance and strength in high-load situations. However, ABS is often preferred for parts that require high aesthetic quality and ease of machining. When comparing ABS to these materials, it’s clear that ABS offers a unique balance of ease of machining, impact resistance, E rapporto costo-efficacia that makes it ideal for many applications.
Let’s look at a table to compare ABS material with some other commonly used plastics in machining.
ABS vs Other Plastics
Materiale | Key Properties | Ideal Applications |
---|---|---|
addominali | Impact-resistant, easy to machine, cost-effective | Consumer goods, automotive, electronics |
Polycarbonate | Superior impact resistance, more difficult to machine | Automotive parts, safety equipment |
Acrylic | Easy to machine, clear, brittle | Signage, displays, lighting covers |
Nylon | Excellent wear resistance, strong, durable | Bearings, gears, industrial components |
Choosing the right material depends on the specific requirements of your application, including strength, machining ease, and final appearance. ABS stands out for its balance of these qualities.
10. What Are Some Common Applications of Machined ABS Parts?
ABS material is used in a wide range of industries due to its versatility and machinability. But here’s the kicker—ABS can be found in everyday objects, as well as critical components in industries like automotive, medical, and consumer electronics.
Nel automotive industry, ABS is used for making parts like dashboards, interior trims, and bumpers. The material’s ability to absorb impact and resist heat makes it ideal for these applications. In elettronica di consumo, ABS is used to produce housings for devices such as televisions, smartphones, and computers. Its smooth finish and durability are essential for protecting sensitive electronics.
In medical devices, ABS is used for creating diagnostic equipment housings, surgical tools, and other instruments that require strength and precision. The material’s ability to be easily machined into complex shapes makes it particularly useful in these applications.
Check out the following table for a summary of common applications for ABS material.
Common Applications of Machined ABS Parts
Industria | Applicazione | Example Products |
---|---|---|
Automobilistico | Interior parts, bumpers, trim | Dashboards, door panels, bumpers |
Electronics | Housings, enclosures | Smartphones, television housings, computer cases |
Medico | Medical device parts | Diagnostic equipment, surgical instruments |
Consumer Goods | Household items, toys | Kitchen appliances, children’s toys |
As you can see, ABS material’s strength, machinability, and cost-effectiveness make it a top choice for many industries.
11. How Do You Troubleshoot Issues in ABS Material Machining?
Machining ABS material can come with its fair share of challenges. But here’s the kicker—knowing how to troubleshoot common problems can save you time and improve the quality of your work.
One common issue is overheating, which can cause ABS to soften, warp, or even melt during the machining process. To avoid this, ensure that you are using the correct cutting speeds and feeds for ABS. Cooling systems like air or mist cooling can help manage the temperature and prevent overheating.
Another issue to look out for is usura degli utensili, which can lead to rough finishes and inaccuracies. Regular maintenance of your cutting tools is essential to ensuring a smooth machining process. Also, if you notice poor surface finishes, it may be due to incorrect cutting speeds or dull tools. Adjusting these factors can often resolve the issue.
Let’s take a look at a table that outlines some common issues and troubleshooting tips.
Troubleshooting ABS Machining Issues
Issue | Cause | Soluzione |
---|---|---|
Overheating | Incorrect cutting speeds, lack of cooling | Use correct speeds, apply cooling methods |
Usura degli utensili | Excessive use, dull tools | Regular tool maintenance, use sharp tools |
Poor Surface Finish | Incorrect speeds, tool wear | Adjust cutting parameters, replace dull tools |
By following these troubleshooting tips, you can resolve common issues and ensure that your ABS parts are machined to perfection.
12. How Does ABS Material Perform in CNC Turning?
CNC turning is one of the most common methods for machining ABS material, and understanding how to maximize the effectiveness of this process is key. What’s the real story? CNC turning is ideal for producing cylindrical parts, such as gears, rods, and shafts, all of which are commonly used in a variety of industries.
ABS performs well in CNC turning because of its impact resistance E easy machinability. The material holds up well during the cutting process, allowing for smooth, precise parts to be produced. The key to successful CNC turning of ABS is to ensure that the workpiece is supported properly during rotation. Vibration can cause inaccuracies and surface imperfections, so proper tooling and support are crucial.
Let’s dive into a table to summarize the best practices for CNC turning with ABS material.
Best Practices for CNC Turning ABS
Best Practice | Descrizione |
---|---|
Use Sharp Tools | Ensure tools are sharp to avoid surface defects |
Maintain Proper Speed | Set appropriate spindle speeds to avoid overheating |
Support the Workpiece | Use supports to minimize vibration and ensure accuracy |
By following these best practices, you can achieve high-quality ABS parts using CNC turning, ensuring both precision and durability.
13. How Does ABS Material Perform in CNC Milling?
CNC milling with ABS material is another popular technique, and for good reason. So, why does this matter? CNC milling allows for the creation of complex shapes, making it ideal for a wide range of applications, from prototyping to end-use parts. ABS’s machinability makes it an excellent material for CNC milling, offering smooth finishes and precise geometries.
ABS’s heat resistance E durability are particularly beneficial during milling, especially when cutting complex or intricate designs. The material’s toughness helps prevent chipping or cracking, which can be a concern with other materials like acrylic. However, usura degli utensili is still an issue, especially during high-volume milling, so regular tool maintenance is essential.
Check out the following table to summarize the key considerations when milling ABS.
Key Considerations for CNC Milling ABS
Considerazione | Descrizione |
---|---|
Usura degli utensili | Regular maintenance of cutting tools is essential |
Spindle Speed | Proper speed settings reduce heat buildup and improve quality |
Vibration | Minimize vibrations for smoother cuts and higher precision |
By keeping these considerations in mind, you’ll be able to achieve the best possible results when milling ABS material.
14. How Do You Maintain Quality and Consistency in ABS Machining?
Maintaining quality and consistency in ABS machining is essential for ensuring that each part meets the required specifications. But here’s where it gets interesting—achieving consistency requires attention to every detail, from choosing the right material to adjusting machine settings. Quality control processes, such as regular tool inspection, machine calibration, E process monitoring, are crucial to maintaining consistency in ABS machining.
Un altro fattore importante è machining environment. Controlling factors like temperature and humidity can significantly affect the quality of the final product. Inconsistent temperatures can lead to expansion and contraction of the material, resulting in machining inaccuracies. By maintaining a stable environment and ensuring regular machine maintenance, manufacturers can avoid these issues and ensure consistency across production runs.
Let’s break down the key actions required for maintaining quality and consistency in ABS machining.
Maintaining Quality and Consistency in ABS Machining
Azione | Descrizione |
---|---|
Regular Tool Inspection | Check tools for wear and replace them as necessary |
Machine Calibration | Regularly calibrate machines to ensure accurate results |
Environment Control | Maintain consistent temperature and humidity for stable machining |
By taking these actions, you can ensure that every ABS part produced meets the required quality standards.
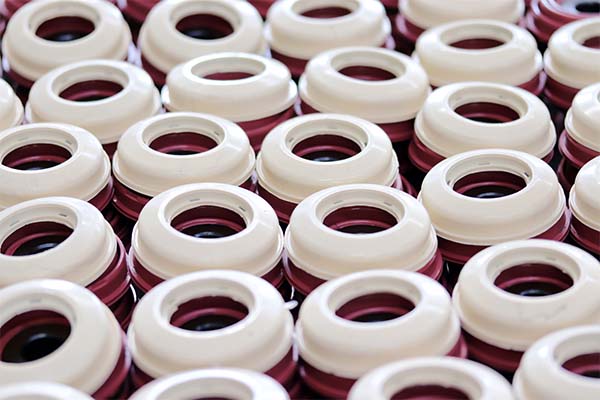
15. How Do You Troubleshoot ABS Material Machining?
Troubleshooting ABS machining issues requires a combination of skill, knowledge, and experience. What’s the real story here? Often, the solution to machining problems can be found by identifying the root cause and adjusting parameters accordingly.
The most common issues in ABS machining include warping, usura degli utensili, E poor surface finish. If you’re facing warping, ensure that the material is being cooled properly during machining and that cutting speeds are adjusted to reduce heat buildup. If tool wear is causing issues, check the condition of your tools and replace them as needed. Poor surface finish can often be attributed to incorrect spindle speeds or dull tools—adjusting these parameters can help improve the final result.
Here’s a summary of troubleshooting steps for ABS machining.
Troubleshooting ABS Machining
Issue | Soluzione |
---|---|
Warping | Use appropriate cooling methods and control heat buildup |
Usura degli utensili | Inspect tools regularly and replace them when necessary |
Poor Surface Finish | Adjust spindle speed, use sharp tools, and ensure proper cooling |
By identifying and addressing these common issues, you can improve the quality and efficiency of your ABS machining projects.
Conclusione
In conclusion, machining ABS material is an essential process for producing durable, high-quality parts used across various industries. From understanding the properties of ABS to mastering the right machining techniques, this guide has provided a comprehensive overview. By choosing the right material grade, applying effective machining techniques, and addressing common issues, you can ensure the success of your ABS machining projects. Ready to get started with your next ABS project? Keep these tips in mind and achieve optimal results.
Domande frequenti
Domanda 1: What is ABS material?
ABS is a versatile thermoplastic material known for its impact resistance, ease of machining, and thermal stability. It is widely used in industries ranging from automotive to electronics.
D2: How does CNC machining work with ABS material?
CNC machining involves using automated machines to shape ABS material into specific designs. It is ideal for creating precise, durable parts with complex geometries.
D3: What causes ABS to warp during machining?
ABS can warp due to uneven cooling, stress, or improper tooling. Ensuring consistent cooling and using proper machining techniques can help prevent warping.
D4: Can ABS be used for high-stress applications?
ABS is durable, but it is not suitable for extremely high-stress applications. For such applications, stronger materials like polycarbonate may be more appropriate.
D5: How can I improve the surface finish of machined ABS parts?
To improve the surface finish, use sharp tools, adjust machining speeds, and consider post-processing techniques like polishing or coating for a smooth, professional result.