導入
If you’re considering CNC machining for your manufacturing needs, understanding the costs involved is essential. あなたは疑問に思うかもしれない: why is it important to understand CNC machining costs? Well, knowing the factors that influence pricing can help you make more informed decisions. Whether you’re a factory looking to outsource or an individual looking for custom parts, knowing what goes into the final price tag is crucial. In this article, we will break down the factors that affect CNC machining costs, provide you with strategies for minimizing expenses, and answer some frequently asked questions to make sure you have everything you need to succeed.
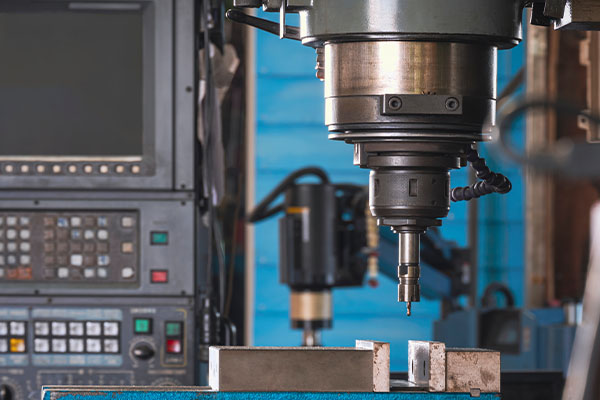
CNC 加工とは何ですか?
CNC machining is a computer-controlled process that uses various cutting tools to remove material from a solid block or workpiece to create specific shapes and parts. It’s widely used in manufacturing industries for precision and efficiency. There are several types of CNC machines, including CNC mills, CNC lathes, and CNC routers. Each machine serves a different purpose, but the principle remains the same: a computer program dictates the movement of the machine tools to achieve the desired cut
Understanding the basics of CNC machining can help you better grasp the cost factors. Machine types, cutting tools, and material choices all come into play when determining the price of a CNC job. The process is highly customizable, which is why pricing can vary so much depending on the job specifications.
Another key aspect to understand is the relationship between the design of the part and the choice of machine. Complex designs with tight tolerances might require specialized tools and longer machining times, leading to increased costs. On the other hand, simpler designs with more generous tolerances can often be machined quickly and at a lower cost.
Key Factors Affecting CNC Machining Costs
Several factors influence the costs of CNC machining, including material selection, machine time, labor, and setup time. Understanding how these factors work together will allow you to get a more accurate estimate for your project.
Material Costs
Materials are one of the most significant cost drivers in CNC machining. Different materials come with varying price tags based on their hardness, availability, and machining complexity. For example, aluminum and steel are commonly used in CNC machining, but steel tends to be more expensive and harder to work with, which can drive up the machining costs. Specialty materials like titanium or high-performance plastics can increase costs even further due to their unique properties and the specialized equipment needed to machine them.
Machine Time
The more complex the design, the more machine time is required. CNC machines are typically charged on an hourly basis, and more intricate parts require more time to process. The hourly rate depends on the type of machine, its age, and its complexity. For example, a CNC milling machine with advanced capabilities may have a higher hourly rate than a simple CNC lathe.
Labor and Expertise
The skill level of the operator is also a significant cost factor. CNC machining requires precision, and experienced machinists are essential for ensuring the best possible results. The more skilled the technician, the higher the cost of the operation, but this ensures that the job is done right and efficiently, reducing the risk of errors and rework.
Setup Time
The setup time involved in preparing the CNC machine for the job can also add to the overall cost. Setting up a machine involves aligning the workpiece, installing tooling, and programming the machine to execute the specific design. The more complicated the design, the longer the setup time, which in turn increases the cost.
Types of CNC Machining Services
The costs of CNC machining services can vary depending on whether you’re ordering a single prototype or placing a large production run. For one-off prototypes, the costs tend to be higher due to the time and effort required to set up the machine for a unique design. Production runs, on the other hand, benefit from economies of scale, as the same setup can be used to produce multiple parts, significantly reducing the cost per unit.
Prototyping vs. Production Runs
Prototypes are typically more expensive than mass production runs because each piece requires individual attention. Custom designs may also require specialized tooling, adding to the cost. However, once a prototype is designed, manufacturers can use the same setup for production runs, making each unit significantly cheaper.
Custom vs. Standard Parts
Custom parts are often more expensive than standard parts because of the time and complexity involved in designing and machining them. Standard parts, which follow industry-standard designs, are cheaper to produce because they can be made in bulk with minimal setup.
Material Selection
The material you choose for your CNC parts has a significant impact on the overall cost. Standard materials like aluminum are usually more affordable, while exotic materials like titanium or carbon fiber will cost more due to their unique properties and the specialized tools required to machine them.
Machine Hourly Rates
CNC machining is usually priced on an hourly rate, which varies depending on the type of machine, its capabilities, and the complexity of the job. Milling machines tend to be more expensive to run than lathes, as they require more intricate movements and adjustments. A high-end CNC machine with advanced capabilities may also come with a higher hourly rate, but it can deliver more precise results in less time, potentially reducing the overall cost of the project.
How Machine Rates are Calculated
Machine rates are determined by several factors, including the machine’s operating costs, the cost of consumables like cutting tools, and the overall efficiency of the machine. In general, more advanced machines with greater capabilities will have higher hourly rates. However, they can often produce parts more quickly and with greater precision, leading to cost savings in the long run.
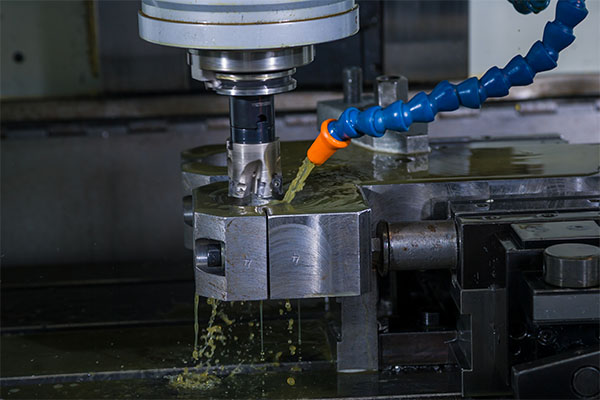
Hourly Rates for Different Machines
CNC milling machines, which are used to cut and shape materials in multiple directions, typically have higher hourly rates than CNC lathes, which are used for turning parts. CNC routers and other specialized machines also have varying rates depending on their complexity and use case
How Machine Downtime Affects Cost
Machine downtime, which can occur due to maintenance or repairs, can significantly impact the cost of CNC machining. When machines are not operational, production slows down, and costs rise due to lost time. Regular maintenance is crucial to minimize downtime and ensure that machines are running at peak efficiency.
Design Complexity and Its Cost Impact
The complexity of your design plays a significant role in determining CNC machining costs. Simple, straightforward designs with generous tolerances are typically cheaper to produce than intricate, highly detailed parts with tight tolerances. The more complex the design, the more time the machine will need to cut and shape the material, which increases costs
Simple vs. Complex Designs
Design complexity often determines the number of cuts, tool changes, and overall machine time required to complete the part. Simple designs may only require basic cutting and shaping, while complex designs often need more detailed programming, additional tool changes, and increased time for precision cuts.
Geometries and Tool Paths
The geometry of the part and the tool paths required to create it can also affect machining time. More intricate geometries with more complex tool paths require more machine time and specialized tools, which increases the overall cost of the job.
3D Printing vs. CNC Machining
While 3D printing can offer a lower-cost alternative for creating complex parts, CNC machining still remains the preferred method for high-precision parts. The cost of 3D printing is generally lower for simple designs, but for highly detailed, high-performance parts, CNC machining is often more cost-effective in the long run due to its superior material properties and durability.
Material Costs and Considerations
Material costs are a significant portion of CNC machining expenses. The choice of material greatly influences both the machine time and the cost of production. For example, softer materials like aluminum are easier and cheaper to machine, while harder materials like titanium require more specialized tools and take longer to process, increasing costs.
Common Materials Used in CNC Machining
Aluminum, steel, plastics, and composites are some of the most commonly used materials in CNC machining. Each material comes with its own set of advantages and challenges. For example, aluminum is lightweight and easy to machine, making it a popular choice for many applications. Steel, on the other hand, is much harder and requires more powerful machinery to work with.
Impact of Material Choice on Pricing
The material you select for your CNC job has a direct impact on both the price and the lead time of your project. Specialty materials, such as high-performance plastics or titanium, are often more expensive and take longer to machine due to their strength and rigidity.
Material Wastage
In CNC machining, material wastage is often inevitable. The process involves cutting away material to achieve the desired shape, and some of it is discarded as scrap. However, this material loss can be minimized through careful design and optimization of the machining process, helping reduce costs.
Labor and Expertise Costs
Skilled labor is essential in CNC machining, as it requires a deep understanding of machine operation and programming. Highly skilled machinists are necessary to ensure that the parts are produced to specification and without defects. The more experienced the machinist, the higher the labor costs will be.
Skilled Operators and Technicians
Machinists must be trained to understand the intricacies of CNC machines, tool selection, and programming. A skilled operator can produce parts more quickly and accurately, reducing the risk of costly errors and rework. This expertise comes at a price, but it ensures that your parts meet the highest standards of quality.
Programming and Design Time
In addition to machine operation, programming the CNC machine to perform the necessary cuts can also take significant time. The complexity of the part design will determine how long it takes to create the program. More intricate designs may require custom programming, which can add to the overall cost of the job.
Training and Certifications
Ensuring that your operators are properly trained and certified is crucial for maintaining quality and efficiency in CNC machining. However, training programs and certifications often come at a cost, which can add to the overall expense of your CNC project. Proper training is an investment that can pay off in the form of better quality and reduced waste.
CNC Machining Setup Costs
The setup phase of CNC machining involves preparing the machine and workpiece, as well as installing tooling and programming the machine. These setup costs can vary depending on the complexity of the design and the specific requirements of the job. For example, simple parts may require minimal setup, while custom designs may need more time and specialized equipment.
Pre-production Setup
Setting up a CNC machine for production involves aligning the workpiece, installing tools, and programming the machine. The setup time can vary depending on the complexity of the part and the type of machine being used. A well-planned setup process can help reduce costs by ensuring that the machine is ready to run efficiently.
Tooling Setup
Tooling setup involves selecting the correct tools for the job and making sure they are installed properly. This can take additional time, especially if the part requires specialized tools. The more tools that need to be changed throughout the machining process, the higher the setup cost will be.
Time Spent on Trial Runs
Trial runs are often necessary to ensure that the machine is set up correctly and that the part will meet specifications. These runs help identify any issues before production begins, but they can also add to the overall cost of the project.
Quality Control and Inspection
Quality control and inspection are essential to ensuring that CNC-machined parts meet the required specifications. These processes are often factored into the overall cost of the project, as they require additional time and resources. The level of quality control needed will depend on the part’s intended use and industry requirements
How Inspection Affects Pricing
Parts that require high levels of precision and strict tolerances will need to undergo more detailed inspections. These inspections can include visual checks, measurements with coordinate measuring machines (CMM), and other testing procedures. The more inspections that are required, the higher the cost of the project will be.
Types of Inspections
Quality control checks may include visual inspections, dimensional checks, or non-destructive testing methods, depending on the application. For high-precision industries like aerospace or medical devices, inspection processes are often more stringent and frequent.
The Role of Tolerances in Quality Control
Tighter tolerances require more precise machining and more frequent inspections. This increases the cost of production, as it requires more machine time and additional checks throughout the process. However, maintaining tight tolerances is critical for parts used in industries that require high levels of performance and safety.
The Importance of Tolerances in CNC Machining Costs
Tolerances are the allowable variations in a part’s dimensions. The tighter the tolerance, the more time and effort are needed to machine the part accurately. Parts with looser tolerances are quicker and easier to produce, resulting in lower costs. Tight tolerances require specialized machines, tools, and quality checks, which increase the price.
What are Tolerances?
Tolerances are the acceptable limits of deviation from the nominal dimensions of a part. For example, a part with a tolerance of ±0.01 mm means that the actual size of the part can vary by up to 0.01 mm from the intended measurement. Tight tolerances require more precise machining processes and higher-quality tools, which add to the cost.
How Tighter Tolerances Increase Costs
Tighter tolerances mean that the part must be machined with more precision, which often requires slower cutting speeds, specialized tools, and more frequent inspections. All of these factors add to the cost of the project, making tight tolerances a significant cost driver in CNC machining.
When Can Tolerances Be Relaxed to Reduce Costs?
Relaxing tolerances can significantly reduce the time and effort required to machine a part, which in turn reduces costs. If the part does not require extreme precision, it may be possible to relax the tolerances, thereby saving on machining time and reducing the overall cost.
Managing Waste in CNC Machining
Waste management is an important factor in reducing the costs of CNC machining. Material waste occurs naturally during the machining process, but careful planning and design can help minimize this waste, ultimately saving you money.
Material Waste
CNC machining involves cutting away material to achieve the desired part shape. This means that some of the material will be discarded as waste. While material waste is inevitable, reducing it through efficient design and machining strategies can help lower overall costs.
Minimizing Scrap
Minimizing scrap requires careful planning and the use of precise cutting techniques. By optimizing the tool paths and cutting strategies, it’s possible to reduce material loss and make the machining process more cost-effective. Scrap can also be minimized by reusing leftover materials for other projects, which helps cut down on waste disposal costs.
Recycling and Reusing Materials
In some cases, leftover materials from the CNC process can be recycled and reused in future projects. This reduces both waste disposal costs and material costs, making the overall machining process more sustainable and affordable.
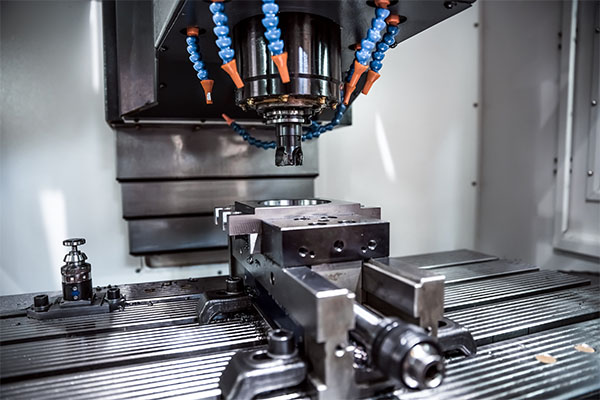
CNC Machining Costs and Different Industries
CNC machining is used in many different industries, each with unique requirements and cost factors. Understanding how CNC costs differ across industries can help you better plan your machining projects.
Automotive and Aerospace
The automotive and aerospace industries require highly precise parts that must meet strict safety and performance standards. As a result, CNC machining costs in these industries tend to be higher due to the need for specialized machines, materials, and inspections.
医療機器
Medical devices often require parts that are made to tight tolerances and need to meet regulatory standards. This increases the cost of CNC machining, as additional inspection and quality control are necessary to ensure that the parts are safe for use in medical applications.
Consumer Goods
CNC machining is also used in the production of consumer goods, including electronics and household items. For high-volume, low-cost production, manufacturers often use CNC machining to produce parts efficiently and at a lower cost per unit.
Custom Machining for Other Industries
CNC machining is used across a wide range of industries, from electronics to robotics to defense. In each case, the machining process is tailored to meet the specific requirements of the industry, whether that means custom parts, specialized materials, or high-quality standards.
How to Calculate CNC Machining Costs
Calculating the cost of CNC machining can be complex, but understanding the various factors that influence pricing can help you make more accurate estimates.
Breakdown of the Pricing Formula
CNC machining costs are calculated by taking into account factors like material costs, machine time, labor, and tooling. The more detailed and complex the part, the more factors there are to consider when estimating the cost.
Cost per Part
The cost per part is influenced by the complexity of the design, the material used, and the time required to machine the part. Simple parts tend to cost less per unit, while complex designs with tight tolerances may cost more.
Examples of Cost Calculations
For example, a simple part made of aluminum might cost $5 per unit, while a more complex steel part with tight tolerances could cost $50 or more per unit. These prices vary depending on the specifics of the project, but understanding how each factor impacts the cost can help you make more informed decisions.
Tips for Reducing CNC Machining Costs
There are several strategies that manufacturers can use to reduce CNC machining costs without sacrificing quality.
Design Optimization
Designing parts with fewer complexities and tighter tolerances can reduce machining time and material waste. By simplifying designs and optimizing them for CNC machining, manufacturers can cut down on production costs.
Choosing the Right Material
Selecting the right material for your part is crucial for keeping costs down. Materials like aluminum are easier to machine and more affordable than materials like titanium or hardened steel. Choosing a material that’s appropriate for the part’s intended use can save both time and money.
Batch Production
For larger runs, producing parts in batches can help reduce the cost per unit. By using the same setup for multiple parts, manufacturers can take advantage of economies of scale and reduce the overall cost of production.
Outsourcing vs. In-house Production
Deciding whether to outsource CNC machining or produce parts in-house depends on several factors, including cost, equipment availability, and expertise. Outsourcing can often be more cost-effective for smaller projects, but in-house production may be more efficient for larger, ongoing orders.
結論
Understanding CNC machining costs is crucial for anyone involved in the manufacturing process. By considering factors such as material selection, machine time, labor, and design complexity, you can better estimate costs and make informed decisions for your project. これが取引だ: reducing costs isn’t about cutting corners—it’s about optimizing the design and manufacturing process to ensure efficiency and high-quality results.
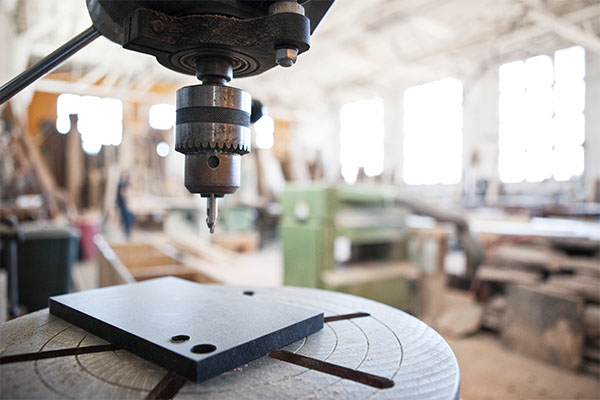
FAQセクション
How much does CNC machining cost per hour?
CNC machining costs are typically calculated by the hour, with rates varying depending on the machine type and complexity of the job.
What factors should I consider when choosing a CNC machine?
When selecting a CNC machine, consider the material you’ll be working with, the required tolerances, and the complexity of the part.
Can I reduce CNC machining costs by changing the design?
Yes, simplifying the design and reducing tolerances can lower machining time and material waste, ultimately cutting costs.
What is the difference in cost between different CNC machines (milling vs. lathe)?
CNC milling machines tend to be more expensive to run than lathes, as they require more complex movements and tooling.
How can I estimate the cost of a CNC machining project?
To estimate the cost, consider material costs, machine time, labor, and setup time based on the complexity of the part and the chosen machining method.