導入
When it comes to CNC milling, one of the most critical aspects of achieving precision and efficiency is choosing the right workholding device. The workholding device secures your workpiece during the machining process, ensuring it stays stable while the CNC machine performs its operations. But what about the devices that move in and out of the machining area? These devices are designed to provide greater flexibility and accessibility, helping to reduce setup time and improve overall workflow. In this article, we’ll explore the different types of CNC mill workholding devices, particularly those that move in and out of the machining area, and how they can enhance your machining operations.
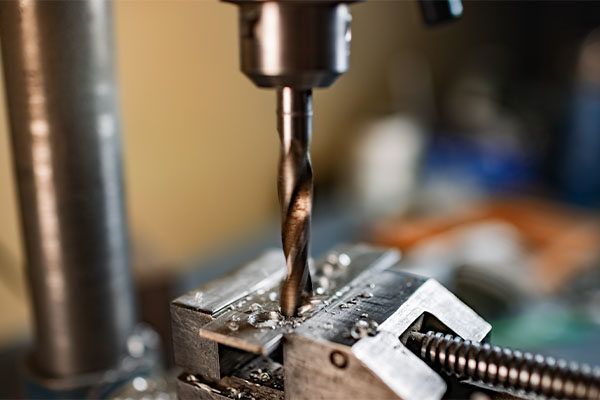
1. Why is Workholding Important in CNC Milling?
Workholding is one of the cornerstones of CNC machining. Without a solid workholding device, even the most accurate CNC machines can struggle to deliver precise results. Here’s the deal: without proper workholding, the part can shift during machining, leading to inaccuracies, increased cycle times, and a higher rate of part rejection.
So, what makes workholding so crucial? First off, a secure workpiece prevents any movement during the cutting process. This allows the machine to focus on its task, rather than compensating for the part shifting. The type of workholding used also affects the efficiency of the operation. Using devices that move in and out of the machining area can save significant time, particularly for parts that need to be reoriented or repositioned frequently.
What’s the real story? Proper workholding also helps ensure that the machining environment remains safe. A securely held part reduces the risk of the workpiece becoming dislodged, which could lead to machine damage or accidents.
Let’s dive deeper into how workholding devices work, and what sets those that move in and out of the machining area apart from their stationary counterparts.
2. What Are the Different Types of CNC Mill Workholding Devices?
When choosing a CNC mill workholding device, there’s a wide variety of options to consider. Ready for the good part? Let’s break it down into a few of the most common devices you’ll encounter on the shop floor.
The most basic workholding device is the vise, which uses a clamping mechanism to hold a workpiece in place. Vises are available in different sizes and styles, such as horizontal and vertical, and are used for a wide range of CNC operations. What makes them so effective? Vises are relatively simple to set up, provide excellent clamping power, and are ideal for holding flat or moderately complex parts.
Moving to the more advanced options, hydraulic and pneumatic workholding devices provide adjustable pressure to securely hold a part. These are used in applications where more clamping force is required, or where rapid clamping and release are necessary. They are often employed in high-volume machining jobs where precision and speed are key.
Then we have magnetic clamping systems, which use a magnetic field to hold ferrous materials in place. These systems provide even clamping force across the part and are excellent for parts with irregular shapes.
But here’s the kicker… what sets movable workholding devices apart? These devices not only secure the workpiece but also allow the part to be easily repositioned within the machining area. This is particularly beneficial when dealing with large parts or jobs that require multiple operations.
Type of Workholding Device | Main Features | Ideal Use Case |
---|---|---|
Vise | Simple, mechanical clamping | Holding flat, regular shapes |
Hydraulic Workholding | Adjustable pressure, fast setup | High precision, heavy-duty clamping |
Pneumatic Workholding | Quick release, adjustable force | Rapid clamping and positioning |
Magnetic Clamping | Even force distribution | Irregular or complex part shapes |
3. What is a Device That Moves In and Out of the Machining Area?
So, what’s a workholding device that moves in and out of the machining area? The term refers to devices that are not fixed in one location within the machining setup. These devices are typically used when the part needs to be reoriented or when different operations need to be performed at various stages of the machining process.
Take, for example, a rotary table with an integrated workholding system. This device rotates the workpiece as the machining operation progresses, allowing different faces of the part to be worked on without manual repositioning. This reduces setup time and minimizes the chance of errors.
What makes these devices so valuable is the ability to keep the part in a constant state of readiness. Whether you’re using a hydraulic workholding system with a movable base or a pneumatic device with automatic positioning, these workholding devices provide flexibility. They help ensure that each machining step is done at the right angle, without the need for manual intervention.
Ready for the good part? Moving workholding devices not only enhance accuracy but also increase throughput by reducing downtime between machining steps.
4. How Do Movable Workholding Devices Improve Efficiency?
Efficiency in CNC milling often comes down to time and precision. What’s the real story? Movable workholding devices can dramatically reduce the amount of time spent repositioning parts or adjusting workholding setups between operations.
Let’s dive deeper into how these devices achieve this. One of the main advantages of movable workholding is the ability to quickly and accurately reposition parts without the need for manual intervention. This can save a lot of time when working on complex parts that require multiple operations at different angles. For example, a rotary table combined with hydraulic clamping can automatically adjust the part’s position, reducing the need for a machinist to manually reposition the part between machining steps.
But here’s the kicker: using movable workholding devices can also improve the overall accuracy of your machining process. Why? Because the part remains securely clamped throughout the entire operation, eliminating the risk of errors caused by shifting or misalignment during manual repositioning. In other words, these devices keep the process moving smoothly, with fewer mistakes.
Device Type | 利点 | Time Saved |
---|---|---|
Hydraulic Workholding | Fast, adjustable clamping force | Less time spent on setup |
Pneumatic Workholding | Quick clamping and release | Faster tool changes |
Magnetic Clamping | Secure and uniform holding | Reduced part repositioning |
5. When Should You Use a Movable CNC Mill Workholding Device?
Understanding when to use a movable workholding device is key to optimizing your CNC operations. So, when should you use one? The decision largely depends on the nature of the machining job and the type of part being worked on.
If you’re working with a large part or one that needs to be rotated or repositioned multiple times during the machining process, then movable workholding devices are a must. For example, a complex aerospace part with intricate contours might require the use of a rotary table combined with a hydraulic workholding system to keep the part stable while machining different faces.
Let’s not forget, movable workholding devices are also invaluable when dealing with high-precision jobs. These devices reduce the chances of errors due to part shifting, ensuring that each machining step is performed with the utmost accuracy.
Now, what about jobs that don’t require frequent repositioning? In those cases, a stationary workholding device might be the better option. The key is to assess the complexity of the job and determine whether repositioning or reorienting the part will be required.
Workholding Device | Best Use Case | Reason |
---|---|---|
Rotary Table | Parts requiring multi-axis machining | Allows easy repositioning during operations |
Hydraulic Systems | High-precision and heavy-duty jobs | Provides adjustable pressure and speed |
Pneumatic Systems | High-speed machining | Quick setup and tool changes |
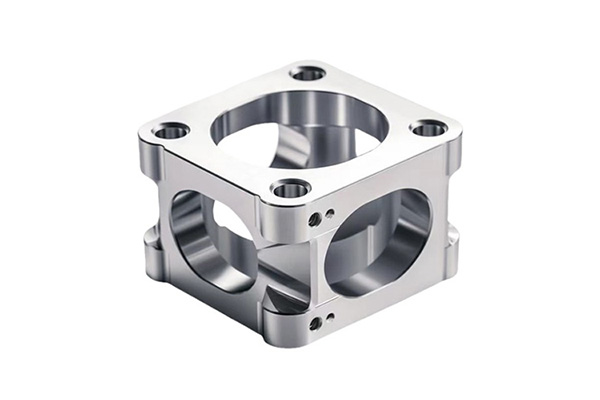
6. How Does a CNC Mill Workholding Device Affect Part Stability?
Stability is essential when it comes to CNC milling, and workholding devices play a major role in maintaining this stability throughout the machining process. What’s the real story? If a workholding device isn’t up to the task, the workpiece can shift or vibrate during machining, leading to inaccuracies, poor surface finishes, or even damage to the part or tooling.
A workholding device that moves in and out of the machining area can greatly affect the stability of the workpiece. For example, a hydraulic system with a movable base allows for precise adjustments to keep the part stable throughout the machining operation. These devices are particularly effective when working with parts that are large or have irregular shapes.
The key takeaway here is that a stable part leads to better results. The tighter the grip, the more accurately the CNC machine can operate. By using a workholding device that keeps the part firmly in place, you can expect better precision and a higher-quality final product.
Device Type | Stability Benefit | Ideal Use Case |
---|---|---|
Hydraulic Workholding | Strong clamping force, consistent pressure | Heavy or large parts |
Pneumatic Workholding | Quick repositioning, consistent clamping | Complex parts requiring fast adjustments |
Magnetic Clamping | Even force distribution | Irregular shapes or thin materials |
7. What Are the Pros and Cons of Movable Workholding Devices?
As with any technology, movable CNC mill workholding devices come with their own set of pros and cons. Let’s break it down. Ready for the good part?
One of the major advantages of movable workholding devices is their ability to enhance flexibility. They allow the part to be repositioned easily within the machining area, saving time and increasing throughput. Additionally, these devices help improve part stability by securely holding the workpiece in place during multiple machining steps.
On the downside, movable workholding devices can be more complex and expensive than their stationary counterparts. They often require additional setup time and maintenance, particularly for hydraulic or pneumatic systems. However, the benefits they offer in terms of speed, precision, and overall efficiency often outweigh these drawbacks.
But here’s the kicker: if you’re working with high-precision parts or complex operations, movable workholding devices are almost always the better choice. In contrast, stationary devices might be sufficient for simpler operations where repositioning is minimal.
長所 | 短所 |
---|---|
Flexible, quick adjustments | Higher initial cost |
Improved part stability | Requires more maintenance |
Faster cycle times | Setup time can be longer |
8. How Do Pneumatic Workholding Devices Move In and Out of the Machining Area?
Pneumatic workholding devices are a popular choice for their ability to provide quick clamping and release. But how do they move in and out of the machining area? Here’s the scoop: pneumatic workholding devices use compressed air to activate clamping mechanisms, allowing the part to be securely held in place. When the job is complete or when a new operation requires the part to be moved, the system quickly releases and repositions the workpiece.
What makes pneumatic systems so valuable? They are fast, efficient, and can be integrated into automated systems. This makes them ideal for high-speed machining operations where time is of the essence. Additionally, because these devices operate on compressed air, they are relatively low-maintenance and offer a high degree of flexibility.
Let’s look at some examples of when pneumatic workholding systems would be used. For instance, if you’re machining a series of identical parts that require rapid tool changes, a pneumatic workholding system would allow you to quickly release and reposition the parts without stopping the entire process.
Device Type | 利点 | Ideal Use |
---|---|---|
Pneumatic Systems | Fast clamping, low maintenance | High-speed, automated machining |
9. How Do Hydraulic Workholding Devices Move In and Out of the Machining Area?
Hydraulic workholding devices are another popular option in CNC machining, known for their ability to deliver adjustable clamping force. So, how do these devices work in the machining area? Hydraulic workholding systems operate by using fluid pressure to move the clamping elements, securing the workpiece. These systems are ideal for parts that require a lot of force to hold securely, such as large, heavy, or high-precision components.
The key benefit of hydraulic systems is their ability to provide consistent, adjustable clamping force, which helps maintain stability during machining. Whether you’re cutting a large part or working with a delicate material, hydraulic workholding devices ensure the workpiece stays in place.
But here’s the kicker: hydraulic systems can also be used in applications that require multiple machining operations. These devices move the workpiece in and out of the machining area seamlessly, allowing for quick changes between operations without compromising on stability or precision.
Device Type | 主な利点 | Best Use Case |
---|---|---|
Hydraulic Workholding | Adjustable clamping force | Heavy-duty, multi-operation machining |
10. What is the Role of Vises in CNC Milling?
Vises are among the oldest and most commonly used workholding devices in CNC milling. These mechanical clamping devices work by using a pair of jaws to secure the workpiece, which is tightened through a screw or hydraulic mechanism. So, what makes them so useful? The simplicity of vises makes them easy to set up and ideal for holding smaller or less complex parts.
But here’s where it gets interesting: while vises are great for simple applications, they might not be as effective for more complex or larger parts that require frequent repositioning. That’s where movable workholding devices come in. Vises can hold the part securely in place, but they lack the flexibility needed for jobs that require multiple machining angles or reorientation.

11. What Are Magnetic Clamping Systems in CNC Milling?
Magnetic clamping systems have become increasingly popular in the CNC milling world. But what exactly makes them so effective? The answer lies in their ability to hold parts securely without physical clamps or fixtures. These systems use a magnetic field to attract ferrous materials, providing a stable grip on the workpiece throughout the machining process.
What’s the real story? Magnetic clamping systems offer several benefits over traditional mechanical clamping methods. First off, they reduce setup time. Unlike manual clamping systems that require adjustments and tightening, magnetic systems hold the part in place instantly. This means less downtime between operations, making it a great choice for high-speed or high-volume machining.
But here’s the kicker: magnetic clamping isn’t just fast. It’s also incredibly precise. The even force distribution across the part minimizes the risk of distortion or movement during the machining process. For parts that are thin or have irregular geometries, magnetic clamping provides a much more stable alternative to traditional workholding methods.
So, when should you consider using magnetic clamping systems? These devices are ideal when machining irregularly shaped parts or thin materials that require uniform clamping force. They are also perfect for jobs where time is critical, as they speed up the clamping process significantly.
Type of Clamping | 主な利点 | Best Use Case |
---|---|---|
Magnetic Clamping | Fast, uniform holding | Thin or irregularly shaped parts |
Mechanical Clamping | Strong, secure hold | Standard parts with regular shapes |
Hydraulic Clamping | Adjustable force | High-precision, heavy-duty tasks |
12. Can CNC Mill Workholding Devices Be Automated?
Automation has become a driving force in CNC milling, transforming everything from part manufacturing to workholding. But can CNC mill workholding devices be automated? The answer is yes, and it’s a game-changer for efficiency and accuracy.
Ready for the good part? Automated workholding devices integrate seamlessly with CNC machines, allowing the workholding setup to adjust automatically during the machining process. This is particularly beneficial for high-volume production environments where part handling needs to be as fast and accurate as possible. Automated systems use sensors, actuators, and robotic arms to handle part loading, unloading, and repositioning without human intervention.
The major advantage of this system is that it reduces human error. Automation ensures that the part is always positioned correctly, making every cycle more consistent and improving part quality. Plus, it allows for continuous production, with minimal downtime for part changes.
So, how does this work in practice? Let’s say you’re running a production run of hundreds of identical parts. Automated workholding devices can ensure that each part is clamped in the same precise position every time, even as the workpiece moves between machining steps. This increases throughput and helps maintain high standards of quality across all parts.
Device Type | 主な利点 | Best Use Case |
---|---|---|
Automated Workholding | Increased speed, precision | High-volume production |
Manual Workholding | Flexibility, control | Low to medium volume machining |
Hydraulic/Pneumatic Systems | Adjustable pressure, fast setup | Versatile for different parts |
13. What Factors Should Be Considered When Choosing a Workholding Device?
Choosing the right workholding device is a crucial decision that depends on several factors. So, how do you make the best choice? Let’s break it down.
The first consideration is the material and size of the part you’re machining. If you’re working with a large, heavy part, you’ll need a workholding device that can withstand high forces without compromising stability. Hydraulic or pneumatic systems are ideal for these jobs because they offer adjustable pressure and can securely clamp large parts.
But here’s the kicker—precision also plays a big role. For high-precision machining, such as in the aerospace or automotive industries, you’ll need a workholding device that provides maximum accuracy. In these cases, hydraulic or magnetic clamping systems are preferable due to their even clamping force and ability to hold the part securely throughout the machining process.
Another important factor to consider is the type of operation you’re performing. If you’re dealing with a part that requires multi-axis machining, a rotary table with a movable workholding device may be the right choice. On the other hand, if your part only needs simple clamping, a vise may suffice.
The last consideration is ease of use. Workholding devices can vary greatly in complexity, so it’s important to consider how easy it will be to set up and use. Complex systems like hydraulics may take longer to set up, but they offer flexibility for more demanding jobs.
要素 | 考慮 | Best Device |
---|---|---|
Part Material | Heavy or dense material | Hydraulic/Pneumatic Systems |
Part Size | Large or oversized parts | Hydraulic/Pneumatic Systems |
精度 | High-precision needs | Hydraulic or Magnetic Clamping |
Operation Type | Multi-axis machining | Rotary Table with Movable Workholding |
14. How to Maintain Your CNC Mill Workholding Devices?
To ensure that your CNC mill workholding devices last for years and continue to perform at their best, regular maintenance is essential. Let’s dive into how you can keep your workholding devices in top condition.
Here’s the scoop: routine maintenance involves cleaning, inspecting, and lubricating the parts of the workholding system. This is particularly important for devices that move in and out of the machining area, as dirt or debris can impair their functionality. Pneumatic systems, for example, need to be regularly cleaned to prevent air blockages, while hydraulic systems require periodic checks to ensure there are no leaks.
What’s the real story? If you neglect maintenance, you risk reducing the lifespan of your devices and compromising machining accuracy. Regular inspections allow you to catch minor issues before they turn into major problems. For example, checking the seals in a hydraulic system can help prevent fluid leaks, which could disrupt your operations.
But here’s the kicker—keeping your devices clean and well-maintained will not only extend their life but also improve their performance. Proper maintenance reduces the likelihood of errors during machining and increases the efficiency of your operations. The bottom line? Don’t wait for a problem to arise before addressing it. Stay ahead of the game with regular checks.
Maintenance Task | Frequency | 利点 |
---|---|---|
Clean Workholding Devices | Weekly | Prevents debris buildup |
Inspect Hydraulic Systems | Monthly | Prevents leaks and pressure loss |
Lubricate Moving Parts | Monthly | Ensures smooth operation |
Check Pneumatic Systems | Bi-weekly | Ensures air pressure consistency |
15. What Are Some Innovations in CNC Mill Workholding Devices?
As technology continues to advance, CNC milling workholding devices are also evolving. What’s the real story? Recent innovations are making these devices faster, more efficient, and even more precise.
Take, for example, the development of intelligent workholding systems. These devices are integrated with sensors that allow for real-time monitoring of the part’s stability. What does that mean for you? It means less time spent troubleshooting and more time spent machining. The sensors track any potential shifting of the part, alerting the machine operator before any errors occur.
But here’s the kicker: we’re also seeing the rise of smart automation, where workholding devices can automatically adjust their clamping force based on the part’s material or size. This dynamic adjustment ensures that the workpiece remains securely held throughout the entire machining process, without requiring manual input from the operator.
Let’s not forget the impact of 3D printing in workholding device production. 3D-printed workholding devices are becoming more common, allowing for customized solutions that are designed specifically for the unique geometry of each part. This has the potential to significantly reduce setup times and improve efficiency, especially for low-volume, high-mix production runs.
Innovation | 説明 | 利点 |
---|---|---|
Intelligent Workholding | Sensors monitor part stability | Reduces errors, improves accuracy |
Smart Automation | Clamping force adjusts automatically | Optimizes part stability during machining |
3D Printed Workholding | Custom workholding devices | Faster setup, better customization |
結論
In CNC milling, choosing the right workholding device is crucial for achieving precision, efficiency, and safety. Devices that move in and out of the machining area offer unique benefits, including faster setup times, greater flexibility, and improved part stability. Whether you choose hydraulic, pneumatic, or magnetic clamping systems, movable workholding devices can significantly enhance your operations. Remember, maintenance and innovation also play key roles in maximizing the performance and lifespan of your equipment.
With a variety of workholding devices to choose from, understanding your needs and making the right selection will ultimately determine the success of your CNC milling operations. Keep exploring the latest innovations in the field, and you’ll always stay ahead of the curve.
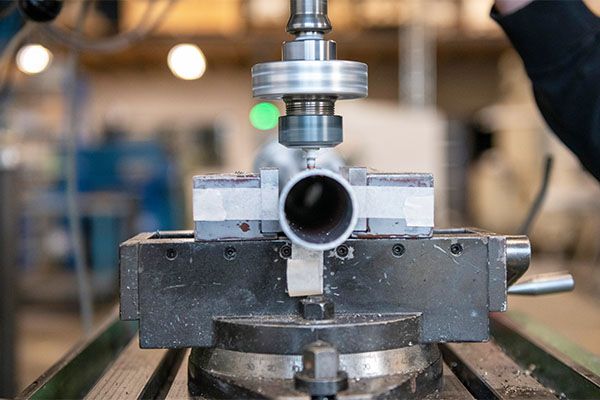
FAQセクション
質問1: What is a CNC mill workholding device?
A CNC mill workholding device is a tool used to secure a workpiece during machining, ensuring it remains stable and accurately positioned.
質問2: How does a movable CNC mill workholding device work?
Movable workholding devices allow the workpiece to be repositioned within the machining area for different operations, improving efficiency and precision.
質問3: What are the benefits of using a movable CNC mill workholding device?
Movable workholding devices enhance flexibility, reduce setup times, and improve part stability, resulting in more efficient and accurate machining operations.
質問4: When is it necessary to use a movable workholding device in CNC milling?
Movable workholding devices are ideal for complex or large parts that require frequent repositioning or multi-axis machining.
質問5: How do I choose the right workholding device for my CNC mill?
Consider factors such as part material, size, precision requirements, and the type of machining operation when selecting the appropriate workholding device.