導入
When it comes to manufacturing high-quality custom parts, ABS CNC machining is one of the most reliable processes available. Acrylonitrile Butadiene Styrene (ABS) is a versatile plastic that offers numerous advantages in both functional and aesthetic applications. This blog post will explore the ins and outs of ABS CNC machining, from its definition to its various applications in multiple industries. By the end, you’ll have a clear understanding of why ABS is such a popular choice and how it can benefit your next machining project.
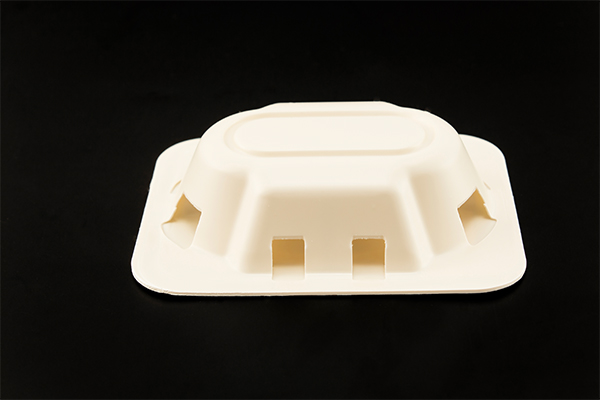
1. What is ABS CNC Machining?
ABS CNC machining refers to the use of コンピュータ数値制御 (CNC) machinery to manufacture parts from Acrylonitrile Butadiene Styrene (ABS) plastic. It involves a highly automated process where a computer controls the tools to shape and cut ABS materials with precision.
But here’s the kicker – CNC machining is favored for its high accuracy, repeatability, and versatility. ABS, being a thermoplastic, is easy to machine, making it an ideal material for various applications, from automotive to consumer electronics.
CNC machining allows manufacturers to achieve precise shapes and dimensions with minimal waste. Whether you need a simple prototype or complex parts, ABS CNC machining can handle it. The versatility of ABS allows manufacturers to design and produce parts that meet exact specifications, making it an excellent choice for industries that demand precision.
The role of CNC machining in manufacturing is pivotal as it significantly reduces human error and improves efficiency in production. ABS is often used in industries requiring a combination of strength, flexibility, and ease of machining. The ability to machine ABS into precise, custom shapes ensures that parts can be tailored to the exact needs of the application.
Common applications of ABS in machining include automotive components, medical devices, consumer goods, and electronic parts. This material’s balance of strength, cost-effectiveness, and ease of use makes it the go-to choice for a wide range of CNC machining projects.
2. Why Choose ABS for CNC Machining?
What makes ABS a top contender for CNC machining? The material properties of ABS make it incredibly versatile and cost-effective.
ABS stands out because of its strength, durability、 そして impact resistance. This plastic can withstand significant stress and force, which is why it’s used in automotive and industrial applications. But wait, there’s more – ABS is also flexible, making it suitable for a wide range of shapes and sizes.
In terms of durability, ABS holds up well under impact, heat, and certain chemicals. This makes it suitable for both functional and aesthetic applications. Whether you’re designing a part that needs to endure wear and tear or something more intricate and decorative, ABS can handle it.
When it comes to cost-effectiveness, ABS machining is ideal for mass production. It’s a relatively low-cost material, and the machining process is efficient, which means lower production costs. For companies that need to balance 品質 そして budget, ABS provides an affordable solution without sacrificing performance.
This versatility is one of the reasons why ABS is used in industries ranging from automotive to consumer electronics. By choosing ABS for CNC machining, manufacturers can deliver parts that perform well under pressure without the need for costly materials.
3. How Does ABS CNC Machining Work?
Ready for the good part? Let’s dive into how ABS CNC machining works.
The process begins by creating a CAD(コンピュータ支援設計) model of the part to be machined. This model is then fed into a CNC machine, which uses precise instructions to cut, drill, and shape the ABS material according to the design specifications.
The first step in the machining process is milling, where rotating cutting tools remove material from the ABS block. This is followed by turning, which is used to machine cylindrical parts, and drilling, which creates holes in the part. Each of these steps requires specific tools, speeds, and feeds to ensure that the part is machined to exact specifications.
What’s the real story here? The choice of CNC machinery and tools plays a critical role in achieving precision and efficiency when machining ABS. Standard CNC mills and lathes are commonly used, but specialized equipment may be required for more complex designs. Advanced CNC systems can handle multi-axis operations, which is especially useful for intricate geometries.
One of the key advantages of CNC machining ABS is the minimal waste produced during the process. The precision of the tools means that the parts can be machined with high accuracy, reducing the need for additional finishing operations.
The cooling systems used during machining are also critical in maintaining optimal tool performance and ensuring high-quality finishes on ABS parts.
4. What Are the Benefits of ABS CNC Machining?
Here’s where it gets interesting – ABS CNC machining offers a wealth of benefits that make it a popular choice in many industries.
First, let’s talk about 精度. ABS CNC machining ensures high-precision parts that meet tight tolerances. Whether you’re making a prototype or a large batch of parts, the ability to manufacture with pinpoint accuracy is a game-changer. It allows for perfect fits, optimal function, and reduced errors during assembly.
Next, we have quick turnaround times. One of the main advantages of CNC machining is the speed at which parts can be made. Once the design is finalized, parts can be manufactured in a fraction of the time it would take with traditional methods, making it ideal for fast-paced industries like automotive and electronics.
Another standout benefit is customization. ABS CNC machining allows for tailored solutions that meet specific design requirements. Whether you need a part with unique dimensions, colors, or finishes, CNC machining can deliver the exact specifications you need, giving you the flexibility to innovate.
The mechanical properties of ABS also contribute to its strength. Parts produced through CNC machining are not only precise but also durable. With its high impact resistance, ABS parts can withstand a wide range of stressors, making them ideal for demanding applications.
5. What Are the Common Uses of ABS CNC Machining?
Now, let’s dive into some real-world applications of ABS CNC machining. This material is used across various industries, thanks to its balance of cost, strength, and versatility.
In the automotive industry, ABS is used to create custom components like dashboard parts, engine components, and exterior body parts. The material’s impact resistance makes it perfect for parts that must withstand heavy use.
For electronics, ABS is commonly used for housings and enclosures for devices like smartphones, computers, and televisions. The ability to machine ABS into precise shapes and integrate custom designs is crucial in this industry, where aesthetics and functionality are paramount.
Household appliances also benefit from ABS CNC machining. ABS parts are often found in kitchen gadgets, vacuum cleaners, and other everyday items that need to be durable and cost-effective.
Lastly, the medical industry relies on ABS CNC machining for prototypes and production parts. ABS is ideal for medical devices due to its combination of durability, strength, and ease of use in machining.
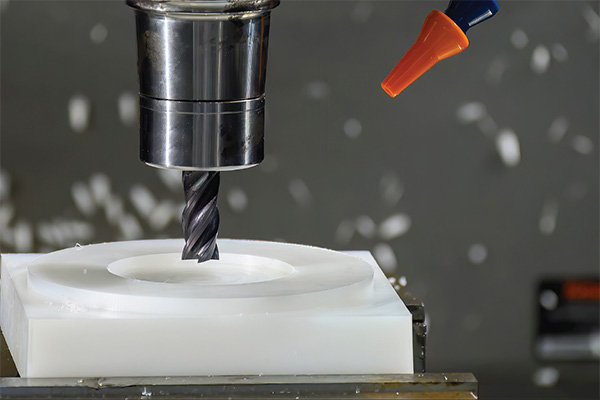
6. What Are the Challenges of Machining ABS?
Of course, no process is without its challenges. When machining ABS, there are a few hurdles to overcome.
One of the main challenges is the potential for cracking そして warping. ABS can be sensitive to temperature changes during the machining process, which can cause the material to expand or contract unevenly. This can lead to part deformation, especially for intricate shapes. But here’s the kicker – choosing the right machining parameters, such as speed, feed rates、 そして cooling methods, can help minimize these risks.
Another challenge is achieving the right surface finish. ABS can be prone to rough edges or marks left by the cutting tools. This requires additional finishing processes, such as sanding or polishing, to ensure a smooth, professional finish.
Lastly, tool wear is an issue to consider. ABS is a relatively hard material, and as a result, machining tools can wear down faster than when working with softer materials. It’s important to monitor the tool condition regularly and replace them when necessary to maintain part quality.
7. How Do You Optimize ABS CNC Machining?
Ready to optimize your ABS CNC machining process? Here are a few strategies that will take your production to the next level.
First, it’s essential to choose the right CNC tools for ABS. The type of tool used, along with its coatings and material, will impact the efficiency and finish of your parts. For example, carbide tools are known for their durability and performance when machining ABS.
Next, adjusting the speed and feed rates can make a big difference in the machining process. Too high of a feed rate can lead to excessive tool wear, while too low can result in inefficient production. It’s all about finding that sweet spot for optimal performance.
Cooling methods are also crucial in ABS CNC machining. Using liquid coolant または air cooling can help prevent the material from overheating, which reduces the risk of cracking and warping. Proper cooling extends tool life and enhances overall part quality.
Finally, avoid some common mistakes when machining ABS. This includes improper tool selection, not adjusting speeds correctly, or failing to use adequate cooling. Avoiding these mistakes will ensure a more efficient and effective machining process.
8. How Does ABS Compare to Other Materials in CNC Machining?
When considering CNC machining, it’s important to compare ABS to other materials to understand its advantages and limitations. ABS vs. Polycarbonate: Polycarbonate is a stronger material than ABS, offering better impact resistance and transparency. However, it’s also more expensive and harder to machine. ABS, on the other hand, is more cost-effective and easier to work with, making it a better option for less critical applications. ABS vs. Acrylic: Acrylic offers better optical clarity and rigidity than ABS but lacks the impact resistance ABS provides. Acrylic is ideal for displays and signage, while ABS is better suited for applications requiring durability and toughness. ABS vs. Nylon: Nylon has higher wear resistance and better chemical stability than ABS, making it ideal for moving parts and harsh environments. ABS is cheaper, easier to machine, and provides good impact resistance but may not perform as well in high-stress environments. When choosing between these materials, you need to weigh factors like cost, durability, and the complexity of the machining process. But here’s the kicker: ABS often offers the best balance of these factors for many everyday applications.
材料 | Cost | Strength | Impact Resistance | Machining Ease |
---|---|---|---|---|
アブソリュート | 低い | Medium | 高い | Easy |
Polycarbonate | 高い | 非常に高い | 非常に高い | Difficult |
Acrylic | Medium | Medium | 低い | Medium |
ナイロン | Medium | 高い | Medium | Medium |
9. What Are the Different Types of ABS Used in CNC Machining?
Not all ABS materials are created equal, and understanding the different types can help you select the best material for your project. Standard ABS vs. High-impact ABS: Standard ABS offers good strength, impact resistance, and heat resistance, making it ideal for many standard machining applications. High-impact ABS, however, is designed to withstand greater force and impact without cracking or breaking, making it ideal for more demanding environments. Reinforced ABS Materials: Reinforced ABS, often combined with glass fibers, offers enhanced strength and rigidity, making it suitable for applications that require extra durability and structural integrity. It’s often used in automotive and industrial applications where additional reinforcement is necessary. Color and Finish Options in ABS Materials: ABS is available in a variety of colors and finishes, allowing for customization to meet specific aesthetic or functional needs. Whether you need a high-gloss finish for an electronic casing or a matte finish for mechanical parts, ABS can be tailored to suit your design requirements. What’s the real story here? Understanding these variations in ABS can help you select the right material based on the specific demands of your application.
Type | Strength | Impact Resistance | Common Use |
---|---|---|---|
Standard ABS | Medium | 高い | General-purpose |
High-impact ABS | 高い | 非常に高い | Automotive, industrial |
Reinforced ABS | 非常に高い | 高い | Structural parts, automotive |
Custom-colored ABS | Medium | 高い | Consumer products |
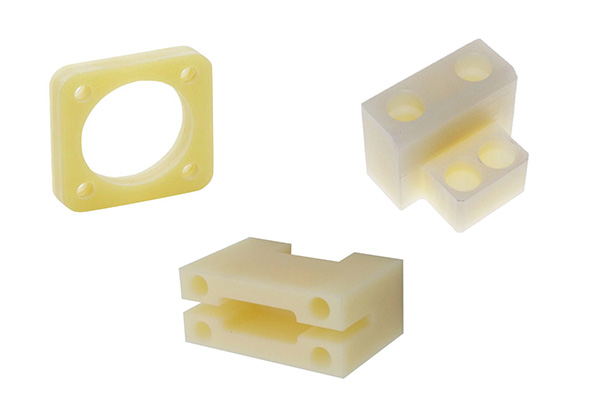
10. How to Ensure Quality in ABS CNC Machining?
Quality control in ABS CNC machining is essential to ensuring that parts meet the required specifications and perform reliably. Quality control methods for ABS parts: Common quality control measures include visual inspections, dimensional checks, and material testing. Ensuring that the right tolerances are maintained during the machining process can avoid costly errors and rework. Testing and inspection techniques: The use of Coordinate Measuring Machines (CMMs) and laser scanners helps verify the precision of machined ABS parts. These tools measure the actual part dimensions and compare them with CAD models to check for any deviations. Certification and standards for ABS machining: Compliance with international standards like ISO 9001 can ensure that ABS CNC machining processes meet industry requirements for quality. Certified manufacturers often follow established guidelines to ensure the highest level of consistency and reliability. This is where it gets interesting—implementing robust quality control measures can drastically improve the final product, ensuring it meets or exceeds expectations.
Quality Control Method | 説明 | Tools Used |
---|---|---|
Visual Inspection | Basic check for defects | Microscopes, magnifiers |
Dimensional Checks | Verify part dimensions against CAD model | Calipers, micrometers |
Material Testing | Ensure material properties meet standards | Tensile testers, hardness testers |
CMM Inspection | Detailed, automated inspection | CMM machines, 3D scanners |
11. How Much Does ABS CNC Machining Cost?
Understanding the factors that influence the cost of ABS CNC machining can help you better budget for your project. Factors affecting the cost of ABS CNC machining: Costs are influenced by the complexity of the design, the volume of parts required, and the level of precision needed. More intricate designs will take longer to machine and require more expensive tooling. Cost comparison with other materials: While ABS is generally cheaper than materials like polycarbonate and nylon, the cost can increase when using high-impact or reinforced ABS due to the need for specialized machinery or longer processing times. Budgeting for large-scale ABS machining projects: For large production runs, cost reductions are possible through optimized designs and material savings. Bulk orders can also benefit from reduced per-part costs. Ready for the good part? ABS CNC machining offers an excellent balance of affordability and functionality, making it an ideal choice for many businesses.
要素 | Impact on Cost | Example |
---|---|---|
デザインの複雑さ | Higher complexity = higher cost | Intricate, detailed parts |
Volume | Larger volume reduces per-part cost | Mass production runs |
Material Type | High-impact or reinforced ABS cost more | Automotive, industrial parts |
精度 | High precision increases cost | Tight tolerances, exact measurements |
12. What Are the Environmental Considerations for ABS CNC Machining?
Environmental impact is a growing concern in all areas of manufacturing, including ABS CNC machining. Recycling ABS waste from machining: ABS plastic is fully recyclable, and waste materials from the CNC machining process can be repurposed for new products, reducing waste and minimizing environmental impact. Eco-friendly alternatives to ABS: While ABS is recyclable, there are eco-friendly alternatives such as PLA or bioplastics that may offer reduced environmental footprints. These materials, however, may not provide the same strength or durability in certain applications. Reducing environmental impact in CNC machining processes: Manufacturers can also reduce energy consumption by optimizing machining processes and using advanced technologies that minimize material waste and energy use. But here’s the kicker—by incorporating sustainable practices and using alternative materials, companies can significantly lower their environmental footprint in the long term.
考慮 | 解決 | 利点 |
---|---|---|
Waste Recycling | Reuse ABS plastic waste | Reduce landfill, save costs |
Eco-friendly Materials | Use PLA, bioplastics | Lower environmental impact |
Process Optimization | Minimize material waste | Reduce energy consumption |
13. What Industries Benefit from ABS CNC Machining?
ABS CNC machining serves a wide range of industries due to its durability and versatility. Automotive and transportation: ABS is used in automotive parts like dashboards, trim pieces, and interior components. Its durability and cost-effectiveness make it ideal for mass production in this industry. Consumer goods and electronics: In the consumer goods sector, ABS is used for everything from home appliances to mobile phone cases due to its strength and versatility. Medical and healthcare products: ABS is used in medical devices and equipment due to its biocompatibility and ease of sterilization. Industrial machinery and equipment: ABS is also used for custom machine parts, housings, and enclosures in industrial applications. What’s the real story? ABS is a top material choice across numerous sectors, providing both performance and cost-efficiency.
業界 | Application Examples | 利点 |
---|---|---|
自動車 | Dashboards, trim, interior parts | Durability, cost-effective |
Consumer Goods & Electronics | Appliances, phone cases | Customization, strength |
Medical & Healthcare | Medical devices, tools | Biocompatibility, ease of sterilization |
Industrial Machinery | Custom parts, enclosures | Durability, precision |
14. What Are Some Real-Life Examples of ABS CNC Machining Projects?
ABS CNC machining has been used in various industries to create innovative and custom solutions. Case studies from various industries: In the automotive industry, ABS was used to create lightweight, durable trim pieces that met strict design specifications. Examples of custom ABS parts: Custom ABS parts for electronics include protective enclosures for sensitive devices, offering both impact resistance and a sleek finish. Success stories in ABS machining: A notable example comes from the medical field, where ABS was used to manufacture durable, lightweight housing for medical equipment, reducing overall weight without compromising on strength. This is where it gets interesting—real-world applications of ABS CNC machining highlight its adaptability across industries.
業界 | Project Example | Result |
---|---|---|
自動車 | Custom trim pieces | Lightweight, durable |
Electronics | Protective enclosures | Impact resistance |
医療機器 | Equipment housing | Lightweight, strong |
15. How to Get Started with ABS CNC Machining?
Getting started with ABS CNC machining is easy when you know what to consider. Finding the right CNC machining provider: Researching and selecting a reliable CNC machining provider is key. Look for a provider with experience in working with ABS and a proven track record of quality work. Key considerations for first-time clients: For first-time clients, it’s important to clearly communicate the design requirements, including tolerances, material specifications, and finishes. Steps to take when placing an ABS machining order: When placing an order, provide detailed CAD files, specify quantities, and discuss lead times and cost expectations. Ready for the good part? Starting your ABS CNC machining project is straightforward with the right knowledge and preparation.
ステップ | アクション | Considerations |
---|---|---|
Find a CNC provider | Research and choose wisely | Experience, reliability |
Communicate requirements | Provide design specs, materials | Tolerances, finishes |
Place order | Submit CAD files, agree on terms | Quantities, lead time |
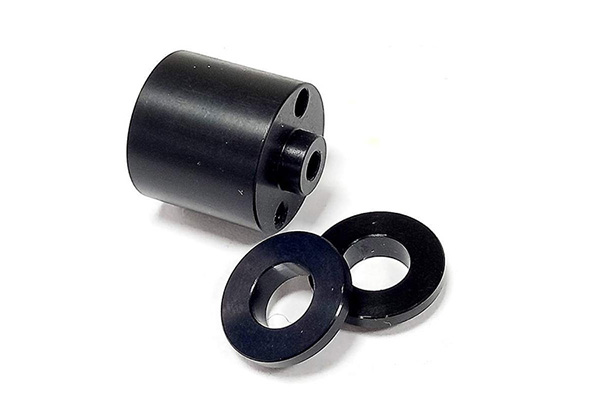
FAQセクション
- Q1: What is ABS CNC machining?
ABS CNC machining is the process of using computer numerical control (CNC) machinery to create precise parts and components made from Acrylonitrile Butadiene Styrene (ABS) plastic. It is widely used due to its strength, flexibility, and ease of machining. - Q2: How does ABS CNC machining work?
ABS CNC machining works by using a CNC machine to shape ABS material into the desired part or component through processes such as milling, turning, and drilling. The machine is programmed with specific instructions to cut and shape the ABS with high precision. - Q3: What are the benefits of ABS CNC machining?
ABS CNC machining offers several advantages, including high precision, quick turnaround times, cost-effectiveness, and the ability to produce durable and customized parts that meet specific design requirements. - Q4: How much does ABS CNC machining cost?
The cost of ABS CNC machining depends on factors such as part complexity, volume, material choice, and the specific machining processes involved. Custom parts or complex designs will typically incur higher costs. - 質問5: What industries benefit from ABS CNC machining?
ABS CNC machining is beneficial for industries such as automotive, electronics, consumer goods, medical devices, and industrial machinery, where precision, customization, and material durability are essential.