導入
In this article, we will discuss the best practices in medical device CNC manufacturing, including essential processes, materials, and quality control measures. CNC machining plays a critical role in the production of high-precision medical devices, and understanding how to leverage it effectively can make a significant difference. We’ll dive into how medical device manufacturers can ensure quality, maintain regulatory compliance, and keep up with the latest trends.
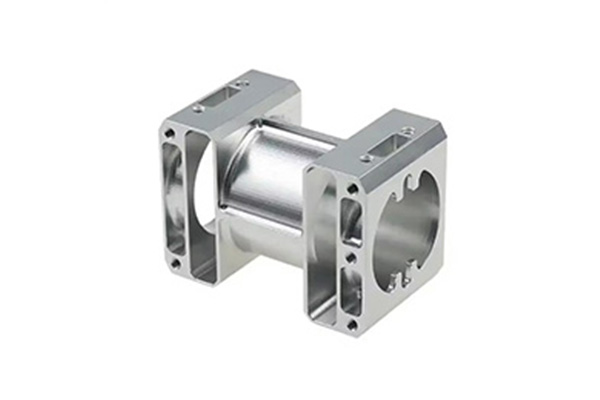
1. What is Medical Device CNC Manufacturing?
Medical device CNC manufacturing refers to the use of computer numerical control (CNC) machines to produce precise, custom parts for medical devices. These devices can range from simple components to complex machinery, all of which require high accuracy and reliability. CNC machining is widely used in the medical field due to its ability to create intricate designs with high precision, critical for ensuring patient safety and device effectiveness.
But here’s the kicker—CNC machining for medical devices isn’t just about creating components; it’s about meeting stringent regulatory requirements. The medical industry is one of the most regulated sectors globally, and manufacturers must comply with standards like ISO 13485, which ensures that quality management systems meet the necessary standards for medical devices.
Additionally, CNC machines can be programmed to manufacture a wide range of materials commonly used in the medical field, such as stainless steel, titanium, and medical-grade plastics. The versatility of CNC allows for the production of devices that are not only functional but also safe and reliable.
Table: Materials Commonly Used in Medical Device CNC Manufacturing
材料 | Common Uses | 長所 | 短所 |
---|---|---|---|
ステンレス鋼 | Surgical instruments, implants, and tools | High strength, corrosion resistance | Expensive, difficult to machine |
チタン | Prosthetics, bone screws, dental implants | Biocompatible, lightweight | Costly, difficult to machine |
Medical-Grade Plastics | Disposable devices, tubing, connectors | Lightweight, cost-effective | Limited strength, durability |
2. Why is CNC Machining Critical for Medical Devices?
CNC machining is crucial in medical device manufacturing for a few key reasons. First, the need for precision in medical devices cannot be overstated. Whether it’s a pacemaker or a surgical tool, even the smallest deviations can have serious consequences. CNC machines provide the precision necessary to meet these stringent requirements.
What’s the real story? CNC machines enable manufacturers to create complex parts that would otherwise be nearly impossible to make manually. With the ability to produce components with micrometer-level precision, CNC machining allows manufacturers to meet the unique demands of the medical industry, which requires highly accurate, customized solutions.
Another reason CNC machining is essential for medical device manufacturing is the ability to handle a wide variety of materials. From biocompatible materials like titanium to flexible plastics, CNC machines can work with an array of materials that are crucial for creating safe and reliable medical devices. This adaptability makes CNC machining indispensable for the industry.
Table: Types of CNC Machining Processes for Medical Devices
CNC Process | 説明 | アプリケーション |
---|---|---|
フライス加工 | Removes material using rotating cutters | Implants, surgical tools |
旋回 | Uses a rotating workpiece and stationary cutter | Tubing, valves, and fittings |
Grinding | Abrasive process for fine surface finishing | High-precision instruments |
3. How Does CNC Machining Benefit Medical Device Manufacturing?
One of the most significant benefits of CNC machining for medical devices is the ability to produce parts with a high degree of accuracy. But here’s the kicker—this is not just about creating parts that fit together. CNC machining ensures that each part meets the required standards for functionality, reliability, and safety.
What’s the big deal? By utilizing CNC machines, medical device manufacturers can maintain consistent quality across large production runs. Once a machine is programmed, it can produce identical parts with minimal variation, which is essential for mass production. This is crucial when dealing with medical devices that need to be identical to ensure patient safety.
Additionally, CNC machining can significantly reduce production time. Traditional methods of manufacturing often involve many manual processes, which can slow down production. CNC machining automates much of this, allowing for faster turnaround times without compromising quality. This efficiency also translates into lower production costs, which is a significant benefit for manufacturers in a competitive market.
Table: Benefits of CNC Machining for Medical Devices
利点 | 説明 | Impact on Manufacturing |
---|---|---|
精度 | Ability to create parts with micrometer accuracy | Ensures device reliability |
Consistency | Automated processes ensure uniformity | Reduces defects and variation |
Speed | Faster production times due to automation | Reduces lead time and costs |
Flexibility | Ability to work with various materials | Accommodates custom designs |
4. What Materials Are Used in Medical Device CNC Manufacturing?
When it comes to manufacturing medical devices, the materials used are critical to the performance and safety of the devices. CNC machining allows manufacturers to work with a variety of materials that meet the stringent standards required for medical applications.
Ready for the good part? CNC machines can handle a wide range of materials, from metals like titanium and stainless steel to high-performance plastics and ceramics. These materials are chosen not only for their strength and durability but also for their biocompatibility, ensuring that they do not cause adverse reactions when used in the human body.
For example, titanium is commonly used for implants due to its biocompatibility and strength. Stainless steel, on the other hand, is often used for surgical tools and instruments because it is highly resistant to corrosion. Medical-grade plastics, such as PEEK (Polyetheretherketone), are frequently used for disposable items like syringes and tubing because they are lightweight and flexible.
Table: Common Materials for CNC Machining in Medical Devices
材料 | Common Uses | 利点 |
---|---|---|
チタン | Implants, prosthetics, surgical tools | Biocompatible, durable |
ステンレス鋼 | Surgical instruments, implants, medical tools | Strong, corrosion-resistant |
PEEK (Polyetheretherketone) | Disposable devices, connectors, surgical instruments | Biocompatible, flexible |
5. How Are Medical Devices Designed for CNC Machining?
The design process for medical devices begins with a concept, which is then transformed into a precise digital model using CAD (Computer-Aided Design) software. Once the design is complete, CNC machines can take over, using CAM (Computer-Aided Manufacturing) software to guide the machine in creating the part.
But here’s where it gets interesting—medical device design often requires custom solutions. Because each device must meet very specific requirements, design must account for not only the functional aspects of the device but also how it will interact with the human body. CNC machining enables manufacturers to create complex geometries that are essential for medical devices like surgical tools and implants.
Additionally, prototyping plays a vital role in the design process. Before mass production begins, prototypes are created to ensure the design works as intended. CNC machining allows for rapid prototyping, meaning that designs can be tested and refined quickly before moving to full-scale production.
Table: Steps in the Design Process for CNC Machining Medical Devices
ステップ | 説明 | Tools/Processes Involved |
---|---|---|
Design | Create a digital representation of the device | CAD software |
プロトタイピング | Produce a physical model to test design functionality | CNC machines, 3D printing |
Production | Manufacture the device based on the final design | CNC machining, quality control |
6. What Are the Key Quality Standards in Medical Device CNC Manufacturing?
Quality standards in medical device CNC manufacturing are non-negotiable. The medical industry is heavily regulated to ensure that every device produced meets the highest standards for safety and effectiveness. But here’s the kicker—compliance with these standards isn’t just about meeting regulatory requirements; it’s about ensuring patient safety.
What are the critical standards, you ask? The International Organization for Standardization (ISO) 13485 is one of the most important. It outlines the requirements for a quality management system where an organization must demonstrate its ability to provide medical devices that meet customer and regulatory requirements.
Additionally, devices must comply with FDA regulations in the United States, which set standards for the production and marketing of medical devices. These regulations require that manufacturers follow strict guidelines for testing, record-keeping, and labeling.
Table: Key Quality Standards for Medical Device CNC Manufacturing
Standard | 説明 | Compliance Requirements |
---|---|---|
ISO 13485 | Quality management system for medical devices | Must meet regulatory standards for medical device production |
FDA Regulations | Standards for medical device manufacturing in the U.S. | Testing, traceability, and documentation are mandatory |
CE Marking (EU) | Ensures products meet European health, safety, and environmental protection standards | Applies to manufacturers selling in the EU |
7. How Are Medical Devices Tested and Validated?
Testing and validation are critical steps in ensuring that medical devices meet the necessary standards for functionality and safety. But here’s the kicker—these devices aren’t just tested for performance; they must undergo rigorous validation to prove that they are safe for human use. This is where precision and quality control become even more important.
What’s the real story? Medical devices must be tested at every stage of the production process. Pre-production testing involves evaluating the design and prototype to ensure that the concept works as intended. Once the device is produced, in-process quality checks are performed to monitor consistency and precision during manufacturing. And finally, post-production validation ensures that the device meets all safety, regulatory, and performance requirements.
This process is essential for preventing device failures, ensuring patient safety, and complying with regulatory standards. Without this comprehensive testing and validation, manufacturers risk creating devices that could fail in the field, which could have serious consequences for patients and the manufacturer’s reputation.
Table: Stages of Testing and Validation in Medical Devices
Stage | 説明 | 目的 |
---|---|---|
Pre-production | Test the design and prototype | Ensure the design is functional |
In-process | Continuous monitoring of the manufacturing process | Maintain consistency and quality |
Post-production | Final checks to ensure compliance with regulations | Ensure safety and efficacy of the product |
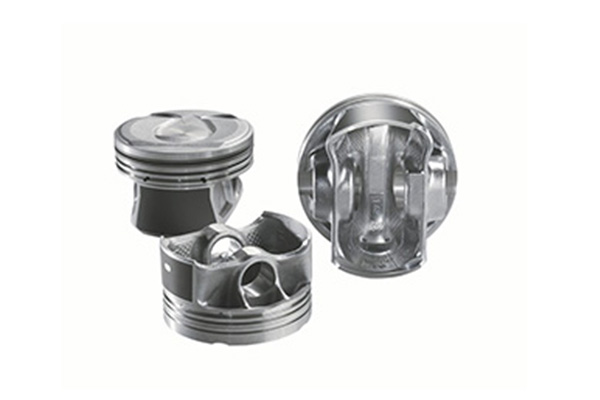
8. What Challenges Are Faced in Medical Device CNC Manufacturing?
Medical device CNC manufacturing offers many benefits, but it also presents unique challenges. Ready for the good part? The challenges aren’t just technical—they are regulatory, material-related, and even logistical.
One of the primary challenges is ensuring high precision across complex designs. With medical devices, even minor errors can lead to safety risks, so CNC machines must be finely calibrated to produce components with high accuracy.
Another hurdle is compliance with regulations. Manufacturers must adhere to strict regulatory standards, including ISO 13485, FDA regulations, and local laws. These regulations often require extensive documentation, which can be time-consuming and complex.
Additionally, manufacturers face material complexity. Many medical devices require the use of specialized, biocompatible materials, which may be difficult to machine. These materials, while essential for safety and performance, often require advanced machining techniques and tools.
But here’s where it gets interesting—CNC machining can help mitigate some of these challenges. By employing high-tech, precise machines, manufacturers can reduce human error, maintain consistency, and improve production efficiency, making it easier to meet these complex challenges.
Table: Common Challenges in Medical Device CNC Manufacturing
チャレンジ | 説明 | ソリューション |
---|---|---|
精度 | High tolerance is required for safety | Use advanced CNC machines with high accuracy |
Regulatory Compliance | Strict regulations in every market | Adhere to ISO 13485, FDA, and CE standards |
Material Complexity | Use of specialized, biocompatible materials | Invest in specialized tools for advanced materials |
9. How Does CNC Machining Improve Efficiency in Medical Device Manufacturing?
CNC machining improves manufacturing efficiency in medical device production by automating and streamlining many processes. But here’s the kicker—this doesn’t just save time; it also ensures that every device produced meets the same high-quality standards.
What’s the big deal? By automating the machining process, manufacturers reduce the need for manual intervention, which means fewer opportunities for error. This increases production speed and reduces labor costs. Additionally, CNC machines can run continuously, meaning they can produce large quantities of components in a shorter time frame.
Automation also improves consistency. With CNC machining, once a design is programmed into the system, the machine can replicate it with high accuracy for every unit produced. This is especially important in the medical industry, where uniformity across all parts is critical to device functionality and patient safety.
But that’s not all. CNC machining helps optimize material usage. It can minimize waste by cutting exactly to the desired dimensions, making the process more efficient and environmentally friendly.
Table: How CNC Machining Improves Manufacturing Efficiency
利点 | 説明 | Impact on Manufacturing |
---|---|---|
Speed | Automation and continuous operation reduce production time | Faster turnaround and lower costs |
Consistency | Precise replication of designs across all parts | Ensures quality control and safety |
Waste reduction | Minimizes material wastage during production | Reduces production costs and environmental impact |
10. What Are the Advantages of Using CNC for Small Batch Medical Devices?
CNC machining is particularly advantageous when it comes to producing small batches of medical devices. Ready for the good part? Small batch production allows manufacturers to offer more customized solutions without sacrificing quality or increasing costs.
One of the biggest advantages is the flexibility CNC offers in terms of design changes. With traditional manufacturing methods, altering designs after production has started can be costly and time-consuming. But with CNC machining, design adjustments can be made quickly and easily, making it an ideal solution for low-volume, customized medical devices.
Additionally, shorter lead times are possible due to the rapid prototyping capabilities of CNC machining. In the medical field, this can be particularly beneficial when developing new devices or responding to urgent market demands.
Furthermore, CNC machines offer cost-effectiveness in small batch production. Traditional manufacturing methods often require large initial investments and tooling, but CNC machines can be quickly reprogrammed to handle different projects, making small batch runs much more feasible.
Table: Advantages of CNC Machining for Small Batch Production
Advantage | 説明 | Impact on Medical Devices |
---|---|---|
Customization | Easy to modify designs for small batches | Accommodates unique medical requirements |
Speed | Faster lead times due to rapid prototyping | Shorter development times for new devices |
Cost-effectiveness | Reduced upfront costs compared to traditional methods | Lower production costs for small batches |
11. How Can Manufacturers Ensure CNC Machining Precision for Medical Devices?
Precision is paramount in medical device manufacturing, and CNC machining plays a vital role in ensuring that parts meet the required standards. What’s the big deal? Even the smallest variation in a medical device component can have severe consequences.
The first step in ensuring precision is machine calibration. CNC machines must be regularly calibrated to ensure that they maintain accuracy over time. This involves checking the alignment of the machine’s tools and making adjustments as needed.
Tool maintenance is another critical factor. Over time, cutting tools can wear out, leading to reduced accuracy. Manufacturers must regularly inspect and replace tools to maintain high precision during production.
Additionally, manufacturers use advanced CNC technologies such as multi-axis machining and high-speed cutting to achieve greater accuracy. These technologies allow for the creation of complex shapes and geometries with very tight tolerances, essential for medical devices.
But here’s the kicker—implementing strict quality control measures, including in-process checks and final inspections, ensures that every part meets the required specifications, further reducing the risk of errors.
Table: Methods to Ensure CNC Machining Precision
方法 | 説明 | 利点 |
---|---|---|
Calibration | Regularly calibrating CNC machines for accuracy | Maintains precision over time |
Tool Maintenance | Inspecting and replacing worn-out tools | Ensures consistent cutting quality |
Advanced CNC Technology | Using multi-axis machining and high-speed cutting | Allows for complex, high-precision designs |
12. How Do Medical Device Manufacturers Ensure Regulatory Compliance with CNC Machining?
Regulatory compliance is a critical aspect of medical device manufacturing. Manufacturers must ensure that their products meet all necessary standards to ensure patient safety and effectiveness. What’s the real story? The medical device industry is one of the most heavily regulated industries in the world, and compliance is non-negotiable.
To meet regulatory requirements, manufacturers must adhere to standards such as ISO 13485 and the FDA regulations for medical devices. These standards outline the necessary quality management systems, documentation, and testing procedures to ensure the safety and reliability of medical devices.
Manufacturers must also maintain traceability throughout the production process. This means that every part produced must be traceable to its source, ensuring that if an issue arises, the faulty part can be identified and removed from the production line.
But here’s the kicker—CNC machining can actually help manufacturers maintain compliance. By automating much of the production process, CNC machines ensure consistency and accuracy, making it easier to meet regulatory standards.
Table: Key Regulatory Standards for Medical Device Manufacturing
Standard | 説明 | Compliance Requirements |
---|---|---|
ISO 13485 | Quality management system for medical devices | Required for certification and audit |
FDA Regulations | U.S. standards for medical device manufacturing | Testing, documentation, and traceability |
CE Marking (EU) | Certification for medical devices sold in the EU | Safety, health, and environmental standards |
13. What Trends Are Shaping the Future of CNC Machining in Medical Device Manufacturing?
The world of CNC machining is constantly evolving, and the medical device industry is no exception. Ready for the good part? The future of CNC machining in medical device manufacturing is being shaped by several key trends.
One major trend is the increasing integration of automation and artificial intelligence (AI). AI can optimize CNC machine settings for greater efficiency and precision, while automation can streamline the entire manufacturing process, reducing the need for manual intervention.
Another trend is the use of additive manufacturing (3D printing). CNC machining and 3D printing are increasingly being used together to create more complex, customized devices. For example, 3D printing can be used for rapid prototyping, while CNC machining ensures that the final product meets stringent quality standards.
Additionally, the use of advanced materials is revolutionizing the medical device industry. New materials are being developed that offer superior strength, biocompatibility, and functionality. CNC machining plays a critical role in working with these advanced materials, enabling manufacturers to create cutting-edge devices.
Table: Emerging Trends in CNC Machining for Medical Devices
Trend | 説明 | Impact on Manufacturing |
---|---|---|
Automation and AI | Using AI and automation to optimize machining processes | Improves efficiency and precision |
Additive Manufacturing | Combining CNC machining and 3D printing for complex designs | Enables rapid prototyping and custom designs |
Advanced Materials | Developing new materials for improved performance | Expands design possibilities and enhances functionality |
14. What Are the Cost Considerations in Medical Device CNC Manufacturing?
Cost is always a significant factor in manufacturing, but in medical device production, it’s particularly critical. What’s the real story? Balancing cost and quality is a fine line, especially when it comes to medical devices, where safety and precision are paramount.
One of the major costs involved in CNC machining for medical devices is the upfront cost of equipment. High-quality CNC machines can be expensive, and manufacturers must factor in the cost of purchasing and maintaining these machines.
Additionally, there are costs associated with 材料. Medical-grade materials like titanium and specialized plastics can be expensive, and waste during production can add to the overall cost.
Finally, there are labor and operational costs. While CNC machines can help reduce labor costs by automating the process, skilled technicians are still required to program and operate the machines. The more complex the devices being manufactured, the higher the labor costs.
But here’s the kicker—by optimizing production and reducing errors, CNC machining can actually help reduce long-term costs, making it a wise investment for medical device manufacturers.
Table: Cost Considerations in CNC Machining for Medical Devices
Cost Factor | 説明 | Impact on Manufacturing |
---|---|---|
Equipment | Purchase and maintenance of CNC machines | High upfront investment |
材料 | Cost of biocompatible and specialty materials | Expensive raw materials |
Labor and Operations | Skilled technicians and machine operators | Ongoing operational costs |
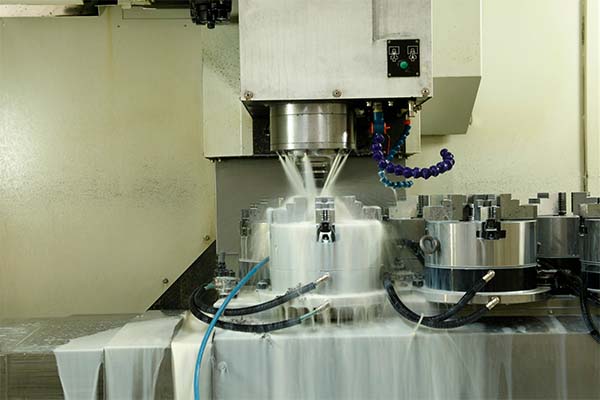
15. What Are the Future Prospects for CNC Machining in Medical Device Manufacturing?
The future of CNC machining in medical device manufacturing looks promising. Ready for the good part? Advancements in technology, materials, and automation will continue to drive innovation in this space, ensuring that CNC machining remains a key player in the production of high-quality medical devices.
As the demand for customized devices increases, CNC machining will be crucial in delivering tailored solutions for specific patient needs. Additionally, as technologies like AIと機械学習 continue to evolve, CNC machines will become even more precise and efficient, opening up new possibilities for medical device manufacturing.
In the coming years, we can expect to see even greater collaboration between CNC machining and other technologies, such as 3D printing, to create innovative, cost-effective, and patient-friendly solutions.
Table: Future Prospects of CNC Machining in Medical Device Manufacturing
Trend | 説明 | Impact on the Industry |
---|---|---|
Customization and Tailored Solutions | Growing demand for personalized devices | More accurate, patient-specific devices |
AI and Automation | Integration of AI and machine learning for optimization | Increased precision and efficiency |
Collaboration with 3D Printing | Using CNC and 3D printing together for complex designs | Expands design capabilities and reduces lead times |
FAQセクション
Q1: What is CNC machining in medical device manufacturing?
CNC machining in medical device manufacturing involves using computer-controlled machines to produce highly accurate parts for medical devices, ensuring precision and compliance with safety standards.
Q2: How does CNC machining benefit the production of medical devices?
CNC machining offers significant advantages, including high precision, consistency, and the ability to work with a wide range of materials, making it ideal for manufacturing medical devices.
Q3: What are the most common materials used in CNC machining for medical devices?
Common materials include stainless steel, titanium, and medical-grade plastics, all of which are chosen for their strength, durability, and biocompatibility.
Q4: What are the key quality standards in medical device CNC manufacturing?
The key standards include ISO 13485, FDA regulations, and CE marking, all of which ensure that medical devices meet rigorous safety and quality requirements.
質問5: How does CNC machining improve efficiency in medical device manufacturing?
CNC machining improves efficiency by automating the production process, reducing manual labor, speeding up production times, and ensuring high-quality output consistently.