導入
In today’s competitive manufacturing landscape, precision is more critical than ever before. Whether it’s in aerospace, medical devices, or automotive parts, the need for high-precision manufacturing has never been greater. But how can manufacturers achieve this high level of accuracy? Enter CNC machining, a process that has revolutionized industries by delivering remarkable precision in production. As businesses demand higher-quality products, CNC machining provides the necessary tools and techniques to meet these stringent requirements. In this article, we’ll dive deep into CNC machining essentials, explaining how this process ensures the precision that businesses need to stay ahead in the market.
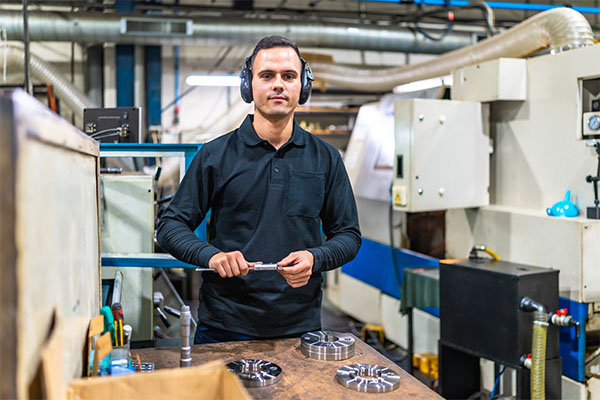
What is CNC Machining? A Brief Overview
CNC加工の定義
CNC machining, or Computer Numerical Control machining, refers to a manufacturing process where computers control machine tools to produce precise parts and components. This process is highly automated, which means it can operate with minimal human intervention. By following pre-programmed software instructions, CNC machines execute tasks with exact precision, cutting and shaping materials like metals, plastics, and composites. From simple cuts to intricate designs, CNC machines offer unrivaled accuracy.
How CNC Works: Basic Principles and Machinery Involved
At the core of CNC machining is its automation. Machines like lathes, mills, routers, and grinders are all equipped with computer-controlled systems that carry out specific tasks with precision. A design is first created using CAD (Computer-Aided Design) software, which is then converted into a set of instructions through CAM (Computer-Aided Manufacturing). These instructions are read by the CNC machine, guiding it to execute the design with incredible accuracy. By utilizing various cutting tools, the machine can manipulate the material in a way that human hands cannot replicate, offering a level of consistency and repeatability that’s vital for high-precision manufacturing.
Key Benefits of CNC Machining: Accuracy, Repeatability, and Versatility
One of the primary advantages of CNC machining is its ability to deliver high accuracy. CNC machines can perform operations with tolerances as tight as 0.0001 inches, a level of precision that is nearly impossible to achieve with manual machining methods. Additionally, CNC machining is highly repeatable, ensuring that each part produced is identical to the last. This consistency is crucial in industries where precision is non-negotiable, such as in the manufacturing of medical devices or aerospace components. Moreover, CNC machines are versatile, capable of producing a wide range of parts and products from various materials, making them indispensable for modern manufacturing.
The Importance of Precision in Manufacturing
Why Precision Matters: Impact on Product Quality and Customer Satisfaction
Precision plays a pivotal role in ensuring the quality and reliability of products. In industries like aerospace and medical devices, even the smallest deviation can lead to catastrophic failures. For example, a component in an aircraft engine that isn’t precisely manufactured can compromise the safety of an entire flight. Similarly, in the medical field, parts like surgical instruments and implants need to be manufactured with impeccable accuracy to ensure they function properly and meet safety standards. Inaccurate products can lead to customer dissatisfaction, product recalls, and a loss of business reputation.
Industries That Rely on Precision
Several industries depend on high-precision manufacturing to produce their products. Aerospace manufacturers require parts that meet stringent safety and quality standards. The automotive industry relies on CNC machining to produce engine components, body parts, and intricate assembly elements that meet strict tolerances. Medical device manufacturers need exact measurements to ensure the effectiveness and safety of devices like pacemakers, surgical instruments, and prosthetics. As technology continues to advance, precision is increasingly demanded across many fields, including electronics, robotics, and energy.
Consequences of Low Precision: Financial and Reputational Damage
The consequences of poor precision are severe. Subpar parts can lead to product failure, which can result in costly repairs, warranties, and recalls. In some cases, it can even lead to safety hazards. When precision is compromised, manufacturers risk damaging their reputation and losing the trust of customers. As customers become more aware of the importance of precision, they expect the highest standards. A single mistake in manufacturing can tarnish a brand’s image and lead to significant financial losses, making precision not just a requirement but a competitive advantage.
The Different Types of CNC Machines
CNC Milling Machines: Functions and Applications
CNC milling machines are one of the most commonly used types of CNC machines in high-precision manufacturing. These machines use rotary cutters to remove material from a workpiece and create the desired shape. CNC milling machines are highly versatile and can perform a wide range of tasks, including drilling, boring, and threading. With the ability to operate in multiple axes (2, 3, 4, or even 5 axes), they can create complex shapes and fine details with exceptional accuracy. These machines are used extensively in industries like aerospace, automotive, and electronics, where precision is paramount.
CNC Lathes: When and Why They’re Used
CNC lathes are another important tool in high-precision manufacturing. Unlike milling machines, which primarily remove material from a stationary workpiece, CNC lathes rotate the workpiece itself while cutting tools shape the material. This is ideal for creating cylindrical or conical shapes with high precision. Lathes are often used in industries that require components like shafts, gears, and pulleys. With advancements in CNC technology, lathes can now perform multiple operations, such as drilling, threading, and facing, all while maintaining tight tolerances.
CNC Routers and EDM Machines: How They Differ from Traditional CNC
CNC routers are designed for cutting softer materials like wood, plastics, and foam. They operate similarly to CNC milling machines but are specifically designed for handling larger, less dense materials. Electrical Discharge Machines (EDM), on the other hand, are used for machining hard materials like tungsten and titanium. EDM works by using electrical discharges to erode material from the workpiece, enabling manufacturers to create precise, intricate details even in tough materials. Both CNC routers and EDM machines are essential for high-precision tasks that require specialized machinery.
Other Specialized Machines: CNC Grinders, Laser Cutters, etc.
In addition to the primary types of CNC machines, several specialized machines are used in high-precision manufacturing. CNC grinders are employed to achieve high-precision surface finishes, while laser cutters provide precision cutting for both thin and thick materials. Each of these machines has its unique capabilities, enabling manufacturers to choose the right equipment for their specific needs.
Key Elements of CNC Machining That Ensure Precision
Tolerances and Specifications: Understanding Precision Measurements
Precision machining is all about meeting specific tolerances and specifications. Tolerances refer to the allowable variation in a part’s dimensions. For example, a tolerance of ±0.001 inches means that the actual dimension of the part can be up to 0.001 inches larger or smaller than the desired measurement. In high-precision machining, these tolerances are often extremely tight, sometimes as small as 0.0001 inches. Understanding these measurements is essential for both machinists and clients to ensure that the final product meets the required standards.
High-Quality Materials: The Role of Selecting the Right Materials for Machining
The materials used in CNC machining play a significant role in achieving precision. Different materials have unique properties that affect their machinability, such as hardness, density, and thermal expansion. Selecting the right material ensures that the machining process can be completed accurately without material deformation. For example, harder materials like titanium require specialized cutting tools and more precise machine settings. By choosing the best material for the job, manufacturers can improve the overall quality of the part.
Cutting Tools and Tooling Quality: How They Affect Precision and Performance
The quality of the cutting tools used in CNC machining directly impacts the precision of the finished product. High-quality tools are essential for achieving the desired tolerances and surface finishes. Over time, tools wear down, and regular maintenance or replacement is required to maintain accuracy. By using top-notch tools and regularly inspecting them, manufacturers ensure that their CNC machines continue to produce parts that meet the highest standards of precision.
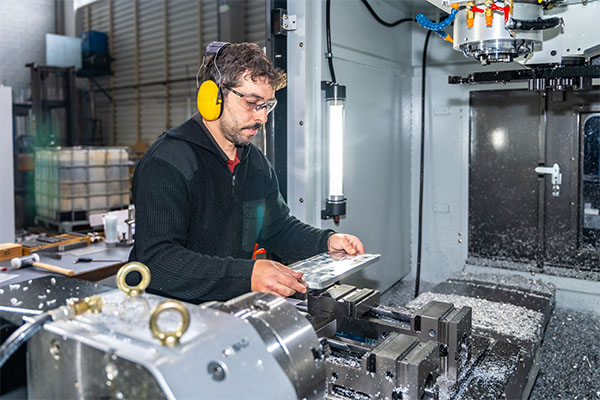
How CNC Machines Achieve High Precision
Advanced Computer Programming: The Software Driving CNC Machines
The software that controls CNC machines is central to achieving high precision. Advanced CNC programming ensures that machines follow precise instructions to cut, mill, or shape materials accurately. Modern CNC machines are equipped with sophisticated software that can handle complex designs and geometries, ensuring that each part is manufactured exactly as specified. This programming also includes features like automatic tool changes, part repositioning, and compensation for tool wear, further enhancing the precision of the process.
Automation and Repeatability: Ensuring Consistency in Production
One of the greatest advantages of CNC machining is automation. Once the program is set, CNC machines can run autonomously, performing the same task repeatedly with the same level of accuracy. This repeatability ensures that every part produced is consistent, which is essential for industries that require high-quality products at scale. Automation also reduces the chances of human error, making CNC machining ideal for tasks where precision is non-negotiable.
Monitoring and Calibration: Keeping Machines and Parts in Top Condition
Regular monitoring and calibration are crucial for maintaining the precision of CNC machines. Over time, machines may experience minor shifts or misalignments that can affect their accuracy. By performing routine checks and recalibrating machines as needed, manufacturers ensure that their equipment continues to deliver precise results. Additionally, monitoring systems can track factors like temperature and vibration, helping to prevent any issues before they affect production.
The Role of CAD/CAM Software in High-Precision CNC Machining
What Is CAD (Computer-Aided Design)?
CAD software is essential for designing parts that will be machined using CNC technology. It allows engineers to create detailed 2D or 3D models of parts, specifying exact measurements and geometries. These designs are then used to guide the CNC machine during the manufacturing process. By using CAD, designers can quickly make adjustments and test their designs before moving to production, which helps save time and costs while ensuring precision.
What Is CAM (Computer-Aided Manufacturing)?
CAM software takes the designs created in CAD and translates them into machine-readable instructions. It determines the best way to manufacture a part, including selecting the appropriate tools, cutting paths, and machining operations. By integrating CAD and CAM, CNC machining processes become more efficient and accurate, as the software can optimize every step of the process, reducing the chance of errors and improving the overall quality of the finished product.
How CAD/CAM Integration Enhances Precision: Streamlining the Design and Production Process
By integrating CAD and CAM systems, manufacturers can streamline the entire design and production workflow. This integration allows for quicker transitions from design to manufacturing, reduces errors, and enhances the overall precision of the parts produced. Designers and machinists can easily collaborate, ensuring that the final product meets the desired specifications and tolerances. In high-precision manufacturing, this synergy between CAD and CAM is invaluable in achieving the level of accuracy that modern industries demand.
Material Selection for Precision CNC Machining
Common Materials for CNC Machining: Aluminum, Steel, Plastics, Titanium
Choosing the right material is a key factor in achieving high precision in CNC machining. Materials like aluminum, steel, plastics, and titanium are commonly used in CNC machining, each offering unique properties. For instance, aluminum is lightweight and easy to machine, making it ideal for industries like aerospace and automotive. Steel, on the other hand, is known for its strength and durability, making it perfect for high-stress applications like engine components. Materials like titanium are often used in specialized fields like medical devices, where strength and biocompatibility are critical.
How Material Properties Impact Precision: Hardness, Density, Thermal Expansion, etc.
The properties of the material being machined directly affect its behavior during the CNC process. For example, materials with high hardness can be difficult to machine and may require specialized tools to achieve precise results. Similarly, the density of the material can impact cutting speeds and tool wear, while thermal expansion can cause slight dimensional changes during machining. Understanding these properties is essential for selecting the right material and ensuring high-precision results.
Choosing the Right Material for Your Project
When selecting a material for CNC machining, it’s important to consider both the material properties and the specific requirements of the part being produced. Factors like strength, weight, cost, and machinability all play a role in determining the best material for your project. Manufacturers must work closely with designers and engineers to ensure that the selected material meets the necessary precision standards while also being cost-effective and efficient to machine.
CNC Machining Tolerances: What You Need to Know
Understanding Tolerances: What Does Tight Tolerance Mean?
In high-precision machining, tolerances are critical. A tolerance refers to the acceptable deviation from a part’s nominal dimensions. For example, a part with a tolerance of ±0.005 inches can vary by up to 0.005 inches from the target measurement, and still be considered acceptable. Tighter tolerances mean that the part must be within a much smaller range of deviation, often down to thousandths of an inch or even microns.
Standard Tolerances vs. High-Precision Tolerances
Standard machining tolerances typically range from ±0.001 to ±0.005 inches, suitable for most applications. However, high-precision CNC machining requires much tighter tolerances, often in the range of ±0.0001 inches or even better. These tight tolerances are necessary for critical parts that will be used in high-stress environments, such as aerospace, medical, and automotive industries. Achieving these tolerances requires specialized tools, meticulous calibration, and a great deal of expertise.
How to Measure Tolerances: Tools and Methods for Precision Measurement
Measuring tolerances accurately is an integral part of CNC machining. Precision tools like micrometers, calipers, and coordinate measuring machines (CMM) are used to measure parts to a high degree of accuracy. CMMs, for example, can scan and measure parts using laser or touch-probe technology, providing incredibly detailed information about a part’s dimensions. Regular inspections ensure that parts meet the required tolerances, ensuring quality and consistency in high-precision manufacturing.
Common Challenges in Achieving High Precision in CNC Machining
Heat Expansion and Material Deformation: How Temperature Affects Precision
One of the key challenges in achieving high precision in CNC machining is managing heat expansion. As a machine tool operates, it generates heat that can cause the material being machined, as well as the machine itself, to expand. This expansion can lead to slight shifts in the dimensions of a part, affecting its precision. Materials such as metals are particularly susceptible to thermal expansion, which is why temperature control is essential in high-precision machining. To mitigate this, many high-precision machining facilities incorporate cooling systems or work in controlled environments to maintain a stable temperature, ensuring that the parts remain within their tolerance limits.
Tool Wear and Dulling: Preventing and Managing Tool Degradation
CNC machining relies heavily on cutting tools that wear down over time. As tools become dull, their ability to maintain precise cuts diminishes, leading to deviations in part dimensions. This is especially problematic in high-precision machining, where even minor tool degradation can affect the accuracy of the final product. To address this, manufacturers use high-quality, durable cutting tools, and implement regular maintenance schedules to ensure tools remain sharp and effective. Some machines are also equipped with automatic tool changers, which can replace worn-out tools mid-production to maintain consistency and precision.
Machine Calibration and Maintenance: Keeping Your Machines in Top Condition
For CNC machines to maintain high levels of precision, regular calibration and maintenance are crucial. Even the most advanced CNC machines require periodic checks to ensure they are aligned and functioning correctly. Over time, small misalignments or mechanical issues can arise, impacting the machine’s ability to produce parts to exact specifications. By investing in routine maintenance and calibration, manufacturers ensure that their machines continue to produce high-quality parts with minimal deviations. This practice is essential for industries where the margin for error is extremely small, such as in medical device manufacturing or aerospace.
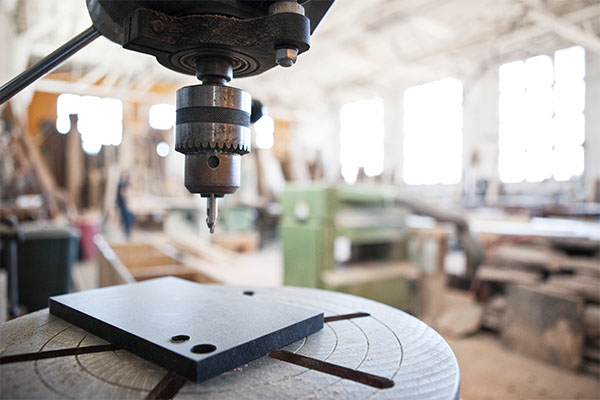
Cutting-Edge Technologies in CNC Machining
5-Axis CNC Machining: Benefits and Applications for High Precision
5-axis CNC machining is a significant advancement in the field of precision manufacturing. This technology allows the cutting tool to move along five different axes simultaneously, enabling it to approach the part from virtually any angle. This added flexibility makes it possible to machine complex geometries with remarkable accuracy, especially in industries like aerospace, where intricate parts are common. The benefits of 5-axis CNC machining include reduced setup time, improved surface finishes, and the ability to create more complex designs in a single operation, which ultimately enhances precision and productivity.
Laser and Waterjet Cutting: Accuracy in Non-Traditional Methods
In addition to traditional CNC milling and lathing, technologies like laser cutting and waterjet cutting have become valuable tools for high-precision machining. Laser cutting uses a focused beam of light to vaporize material with extreme precision, making it ideal for cutting thin sheets of metal or other materials with tight tolerances. Waterjet cutting, on the other hand, uses a high-pressure stream of water mixed with abrasive particles to cut through materials. This method is particularly useful for cutting materials that are heat-sensitive or would warp under conventional methods. Both techniques offer unique advantages for precision cutting, allowing manufacturers to achieve accuracy without compromising material properties.
Additive Manufacturing Integration: How 3D Printing Complements CNC Machining
While CNC machining is known for its subtractive process, additive manufacturing, or 3D printing, can complement CNC machining by offering capabilities for producing intricate shapes that would be difficult or impossible to achieve through traditional methods. 3D printing allows manufacturers to create parts layer by layer, offering precision in the construction of complex geometries. By combining CNC machining with 3D printing, manufacturers can optimize the production process, using machining for the initial shaping and additive manufacturing for fine details or more intricate structures. This integration ensures that manufacturers can meet the precision requirements of even the most demanding projects.
Cost Considerations in High-Precision CNC Machining
How Precision Affects Cost: High-Precision Machines and Tools
Achieving high precision in CNC machining often comes at a higher cost due to the need for advanced machinery and specialized tools. Machines capable of producing tight tolerances and intricate designs are often more expensive to purchase and maintain. Additionally, high-precision tools, which are necessary for maintaining accuracy, tend to be more costly than standard tools. The materials used in high-precision machining, such as hardened steels or aerospace-grade alloys, can also drive up costs due to their difficulty in machining. While these expenses may be higher, the end result is a product that meets the most stringent specifications and quality standards, which is often a necessity for industries like aerospace, medical devices, and electronics.
Balancing Cost and Quality: Making High-Precision Machining Affordable
While high-precision machining can be expensive, it is essential to balance cost with quality. Manufacturers can optimize production by carefully selecting the right materials, tools, and machines that offer the best value for the specific project requirements. By implementing efficient machining processes and reducing waste, it’s possible to lower production costs without sacrificing precision. Additionally, collaborating with experienced CNC service providers can help companies get the most out of their investments, ensuring that the end product is both high-quality and cost-effective.
Investing in the Right CNC Machine: Factors to Consider When Choosing Machinery
When investing in CNC machinery, manufacturers must consider a variety of factors, such as the types of materials to be machined, the complexity of the parts, and the required tolerances. Selecting the right CNC machine for the job can help ensure that precision is achieved while keeping costs in check. Machines with advanced features, like multi-axis capabilities and automated tool changers, can increase efficiency and reduce manual intervention, leading to cost savings over time. However, it’s important to assess the machine’s capabilities against the specific requirements of the project to ensure that it provides the right level of precision at an affordable cost.
CNC Machining and Quality Control
Inspection Methods for Precision Parts: CMM, Laser Scanning, etc.
Quality control is critical in high-precision CNC machining to ensure that parts meet the required specifications. Coordinate Measuring Machines (CMM) are commonly used to inspect parts for dimensional accuracy, with probes that measure physical characteristics of the part at multiple points. Laser scanning is another method used to measure and inspect parts by creating a 3D digital model of the part. These methods help detect any deviations from the desired tolerances, allowing for quick corrections before the part moves to the next stage of production.
Quality Assurance Standards: ISO Certifications, Industry-Specific Standards
To ensure that parts meet the highest standards of quality, many manufacturers adhere to ISO certifications and industry-specific quality assurance standards. ISO 9001 is a widely recognized standard for quality management systems, helping companies maintain consistent quality in their products. Industry-specific standards, such as AS9100 for aerospace or ISO 13485 for medical devices, outline the specific requirements for products used in these sectors. By following these guidelines, manufacturers can ensure that their CNC machining processes meet global standards for precision and reliability.
Importance of Consistency in Production
Maintaining consistency in production is vital for industries that rely on high-precision parts. Even slight variations in product dimensions can lead to significant issues, particularly when parts must fit together or operate in a precise environment. By implementing rigorous quality control measures and maintaining precise calibration of CNC machines, manufacturers can ensure that every part produced meets the same high standards, minimizing variation and enhancing product reliability.
The Future of High-Precision CNC Machining
Automation and Artificial Intelligence: Impact on Production Speed and Precision
The future of high-precision CNC machining is undoubtedly tied to automation and artificial intelligence (AI). Automated systems and AI-powered tools are transforming the industry by optimizing machining processes, reducing human error, and improving overall efficiency. With AI, CNC machines can continuously adapt and optimize their settings based on real-time data, ensuring that precision is maintained throughout the production process. This level of automation will drive faster production speeds while maintaining the high standards of precision required for industries like aerospace, medical, and electronics.
The Rise of Smart Factories: How IoT and Data Integration Are Changing CNC Machining
The rise of smart factories is revolutionizing CNC machining by integrating Internet of Things (IoT) technology into manufacturing processes. By connecting CNC machines to a central data network, manufacturers can monitor and analyze machine performance in real-time. This integration allows for predictive maintenance, reducing downtime, and ensuring that machines operate at peak efficiency. As factories become more interconnected, the precision of CNC machining will continue to improve, with real-time adjustments and data-driven insights leading to better-quality products.
Sustainability in CNC Machining: Reducing Waste While Maintaining Precision
Sustainability is becoming an increasingly important factor in CNC machining. With growing environmental concerns, manufacturers are seeking ways to reduce waste while still achieving high precision. Implementing energy-efficient practices, recycling materials, and optimizing cutting tools to minimize material waste are just a few strategies that CNC machining companies are using to promote sustainability. By incorporating these practices, manufacturers can not only reduce their environmental impact but also lower production costs, making precision machining more affordable and eco-friendly.
How CNC Machining Benefits Specific Industries
Aerospace: Meeting Stringent Tolerance Requirements for Critical Parts
In the aerospace industry, precision is paramount. Parts used in aircraft, satellites, and spacecraft must meet extremely tight tolerances to ensure they function correctly and safely under demanding conditions. CNC machining is the ideal solution for producing these complex, high-precision components, as it allows for the creation of parts with extremely tight dimensional requirements. From turbine blades to structural components, CNC machining ensures that aerospace manufacturers can meet these stringent standards while maintaining reliability and safety.
Medical Devices: The Need for Flawless, Reliable Precision
In the medical device industry, precision is crucial for both functionality and patient safety. Surgical instruments, implants, and diagnostic devices must be manufactured to the highest standards of accuracy to ensure they perform effectively and safely. CNC machining allows manufacturers to create parts with the precision required for these life-saving devices, ensuring that they meet the exact specifications needed for safe use. Whether it’s producing tiny components for pacemakers or large surgical instruments, CNC machining offers the precision necessary for high-quality medical products.
Automotive: High-Volume Production Without Sacrificing Quality
The automotive industry demands high-precision machining for a wide range of parts, from engine components to suspension systems. CNC machining allows manufacturers to produce parts at scale while maintaining tight tolerances and consistent quality. High-precision machining also ensures that parts fit together seamlessly in assembly lines, reducing the risk of defects and costly rework. As the automotive industry shifts toward electric vehicles and autonomous systems, the demand for precise, high-quality parts continues to rise, making CNC machining an essential part of the manufacturing process.
Electronics: Small, Intricate Parts That Demand Tight Tolerances
In the electronics industry, precision is necessary for producing small, intricate parts like circuit boards and connectors. As devices become more compact and feature-packed, the need for high-precision machining increases. CNC machining allows manufacturers to produce parts with the fine details required for modern electronic devices, ensuring that components work together seamlessly and reliably. From smartphone components to semiconductors, CNC machining ensures that the tiny parts inside electronics function as intended.
How to Choose the Right CNC Machining Service for Your Project
Evaluating Capabilities: What to Look for in a CNC Machining Service Provider
When choosing a CNC machining service provider, it’s essential to evaluate their capabilities. Look for a provider with experience in your specific industry and a track record of delivering high-precision parts. Make sure they have the necessary equipment, such as multi-axis CNC machines, and that they can handle the materials and tolerances required for your project. A reliable provider will also offer flexible services, including prototyping, short runs, and full-scale production.
Ensuring Consistent Quality: How to Check for Certifications and Past Work
Ensuring the quality of CNC machining services is crucial for high-precision work. Look for certifications such as ISO 9001 or industry-specific certifications like AS9100 for aerospace or ISO 13485 for medical devices. These certifications indicate that the provider adheres to rigorous quality management standards. Additionally, ask for samples of previous work or case studies to assess the provider’s capabilities and the quality of their products.
Communication and Customer Service: Ensuring a Smooth Collaboration
Clear communication is vital when working with a CNC machining service provider. Make sure that the provider is responsive and willing to collaborate with you throughout the project. A good service provider will keep you informed about the progress of your project and address any concerns that arise. By working closely with your provider and establishing open lines of communication, you can ensure that your project runs smoothly and meets the necessary precision standards.
Conclusion: Why CNC Machining is Essential for Modern Manufacturing
CNC machining has revolutionized the way we approach manufacturing, enabling the creation of high-precision parts that meet the most demanding specifications. From aerospace to medical devices, the benefits of CNC machining extend across various industries, providing a competitive edge for companies that rely on precision to deliver top-quality products. Whether you’re producing a small batch of parts or a high-volume run, CNC machining offers the precision, repeatability, and versatility necessary to meet modern manufacturing demands. By choosing the right CNC service provider, manufacturers can ensure that their products meet the highest standards of quality and precision.
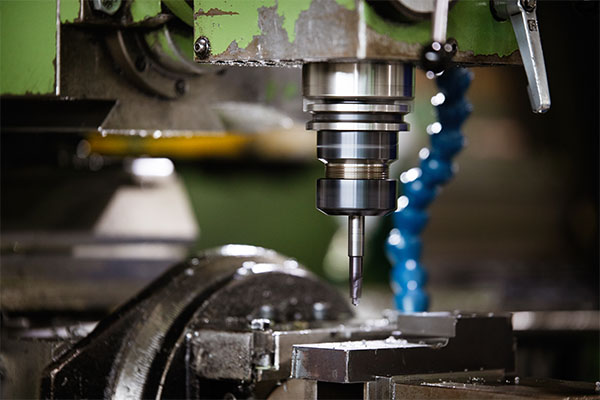
FAQセクション
- What is the difference between CNC machining and traditional machining?
- CNC machining involves the use of computer-controlled machines to create precise parts, whereas traditional machining is done manually, which can introduce more variability and less accuracy.
- How do I ensure my parts meet precise specifications?
- Work closely with your CNC service provider to establish clear specifications and utilize quality control methods like CMM inspection to measure parts against your requirements.
- What is the most common material used in CNC machining?
- Common materials include aluminum, steel, titanium, and various plastics, each chosen based on the part’s requirements for strength, machinability, and cost.
- How do CNC machines ensure consistency in production?
- CNC machines follow pre-programmed instructions that ensure the same operations are repeated with high accuracy, reducing the chances of human error.
- What are the costs associated with high-precision CNC machining?
- The cost of high-precision CNC machining varies depending on the complexity of the part, materials, and tooling required. High-precision parts typically require more advanced machinery and tools, which can increase costs.
- Can CNC machining handle both small and large production runs?
- Yes, CNC machining is suitable for both small and large production runs, offering flexibility and precision for both types of projects.
- What maintenance is required to keep CNC machines precise?
- Regular calibration, tool maintenance, and checks for wear are essential to maintain the precision of CNC machines.
- How do I know if my CNC machining service provider is reliable?
- Check for certifications, review past projects, and ask for references from other clients to evaluate the reliability of a service provider.
- What are the limitations of CNC machining?
- CNC machining may have limitations with extremely hard materials, certain intricate shapes, or very thin parts, which may require specialized processes.
- Can CNC machining be used for prototyping?
- Yes, CNC machining is often used for prototyping, allowing manufacturers to create accurate models and parts before full-scale production.