導入
In today’s fast-paced manufacturing world, precision and efficiency are crucial, and that’s where advanced CNC machining comes into play. CNC, or Computer Numerical Control, has revolutionized the way we produce complex, high-precision parts across a variety of industries. But what sets advanced CNC machining apart? It’s not just about making parts; it’s about making them better, faster, and more cost-effectively. This article will explore the world of advanced CNC machining, diving deep into what it is, the key benefits it offers, and how it’s transforming industries like aerospace, automotive, and healthcare. Let’s explore how this technology is setting the stage for the future of manufacturing.
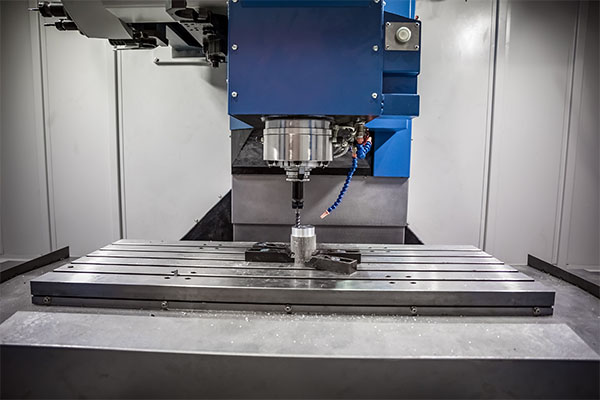
1. Understanding CNC Machining
The Basics of CNC Machining
CNC machining involves the use of computers to control machine tools that cut, shape, and form material into precise parts. This technology has been a game-changer for manufacturers, offering consistent and reliable results. Unlike manual machining, where operators control the tools by hand, CNC machining relies on pre-programmed software to guide the tools through various movements, making the process highly automated and precise. The primary machines used in CNC machining include mills, lathes, routers, and grinders, each designed for specific types of tasks.
What makes CNC machining so beneficial is its ability to automate repetitive tasks with extreme accuracy. Once the machine is programmed, it can operate without human intervention, leading to faster production times and reduced chances of errors. CNC machines can handle a range of materials, from metals and plastics to wood and composites, making them versatile across multiple industries.
The Role of Software in CNC Machining
At the heart of CNC machining is the software used to control the machines. CAD (Computer-Aided Design) and CAM (Computer-Aided Manufacturing) software are essential for designing and programming parts. CAD software is used to create detailed 3D models of parts, while CAM software translates these models into instructions that guide the CNC machine. This integration ensures that parts are manufactured exactly as designed, with a high degree of accuracy and efficiency. The process eliminates much of the human error found in manual machining and streamlines production from start to finish.
2. What Makes CNC Machining “Advanced”?
Technological Innovations in CNC Machines
Advanced CNC machining goes beyond traditional CNC to incorporate cutting-edge technologies that enhance precision, speed, and automation. One of the major advancements is the use of multi-axis machining, which allows the machine to operate on multiple axes simultaneously. This technology makes it possible to create more complex parts in fewer steps, reducing production time and increasing accuracy.
Another key innovation is the integration of robotics and artificial intelligence (AI) into CNC systems. Robots can assist in loading and unloading parts, while AI algorithms optimize machining parameters in real-time. These advancements allow for quicker setups, higher throughput, and better utilization of machine time. Moreover, some modern CNC machines are capable of self-correction, meaning they can adjust their movements to account for minor deviations in material properties or tool wear, ensuring optimal performance.
Advanced Materials and CNC Machining
The ability to work with advanced materials is another hallmark of advanced CNC machining. Materials like titanium, high-performance alloys, and specialized polymers require precise machining techniques to maintain their integrity and properties. CNC machines are capable of handling these materials with ease, allowing manufacturers to produce parts that meet the stringent demands of industries such as aerospace, medical devices, and automotive.
Advanced CNC machining enables manufacturers to create parts that are both lightweight and strong, meeting the needs of industries that require high-performance materials. This ability to work with a wide range of materials expands the potential applications of CNC machining, making it an essential tool for innovation across various fields.
3. Key Benefits of Advanced CNC Machining
Unmatched Precision and Accuracy
One of the standout benefits of advanced CNC machining is its ability to achieve extreme levels of precision and accuracy. CNC machines can work within tolerances as small as a few microns, making them ideal for industries that require highly detailed and exact components. For example, the aerospace industry relies on CNC machining to produce parts with extremely tight tolerances, where even the slightest deviation could lead to failure. Similarly, medical device manufacturers use CNC machining to create custom implants and surgical tools that must fit the human body with precision.
CNC machines can replicate the same process repeatedly with no loss of accuracy, ensuring that every part produced is identical. This consistency is crucial for industries where quality control and uniformity are paramount.
Increased Efficiency and Productivity
Advanced CNC machining significantly boosts production efficiency. One of the ways this is achieved is through automation. Once a CNC machine is programmed and set up, it can run continuously, requiring minimal human intervention. This allows for high-volume production without sacrificing quality. Additionally, advanced CNC machines can perform multiple operations in one cycle, further reducing production time. For example, multi-axis CNC machines can cut, drill, and mill a part all in one go, eliminating the need for multiple setups and tool changes.
Furthermore, CNC machines can run at high speeds without compromising quality, thanks to advances in high-speed machining technology. This means manufacturers can produce more parts in less time, reducing lead times and increasing throughput. The efficiency gains from advanced CNC machining translate directly to cost savings, making it an attractive investment for businesses looking to scale production.
Complex Geometries and Designs
Another significant benefit of advanced CNC machining is its ability to create complex geometries that would be difficult or impossible to achieve with traditional machining methods. With multi-axis CNC machines, manufacturers can produce parts with intricate shapes, curves, and features that require multiple angles of approach. This capability is especially important in industries like aerospace and automotive, where components often have highly complex designs for aerodynamics, strength, and functionality.
The ability to create complex designs also opens the door to more innovative and custom solutions. Manufacturers can push the boundaries of design and create parts that meet very specific requirements. This flexibility in design is one of the main reasons why advanced CNC machining is so widely used across industries.
Cost Savings in the Long Run
Although the initial investment in advanced CNC machinery may be high, the long-term savings are significant. The automation of machining processes reduces labor costs, as fewer operators are needed to monitor and adjust the machines. Additionally, the high precision of CNC machining minimizes material waste, ensuring that raw materials are used efficiently.
The ability to produce parts faster and with fewer errors also contributes to cost savings. Manufacturers can reduce scrap rates and avoid costly rework, leading to a more streamlined production process. Over time, these savings can offset the initial investment in CNC machines, making them a worthwhile expenditure for businesses looking to improve their manufacturing capabilities.
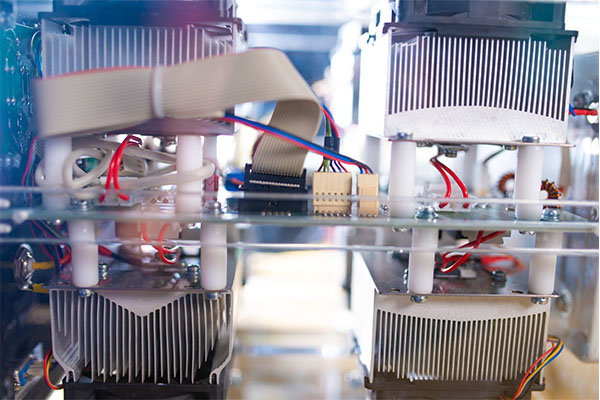
4. Industries That Benefit from Advanced CNC Machining
Aerospace and Aviation
The aerospace industry is one of the biggest beneficiaries of advanced CNC machining. CNC machines play a critical role in the production of aerospace components, where precision, durability, and reliability are essential. CNC machining is used to manufacture engine parts, landing gear components, and structural elements, all of which must meet rigorous standards for safety and performance.
In aerospace, CNC machines are used to create lightweight yet strong components that can withstand extreme conditions, such as high speeds and temperatures. Advanced CNC machining allows for the production of complex geometries, which are often required for parts that need to meet aerodynamic or structural demands. Additionally, CNC machining improves consistency and quality control, ensuring that parts meet the exact specifications necessary for high-performance aviation.
Automotive and Electric Vehicles
The automotive industry has embraced advanced CNC machining to produce high-precision parts used in vehicles. CNC machines are employed to manufacture everything from engine components to suspension parts. The ability to create complex, high-performance parts with precision is crucial in a competitive market where manufacturers are constantly striving to improve vehicle performance, safety, and fuel efficiency.
With the rise of electric vehicles (EVs), CNC machining is also being used to produce custom parts for battery packs, electric motors, and other essential EV components. The versatility of advanced CNC machining makes it an ideal choice for manufacturers looking to innovate and stay ahead in the rapidly evolving automotive market.
Medical and Healthcare Devices
In the medical field, advanced CNC machining is used to create parts for a variety of healthcare applications, including surgical instruments, implants, and prosthetics. Precision and customization are critical in medical device manufacturing, and CNC machining is capable of producing parts that fit the exact specifications required by healthcare professionals.
CNC machines are particularly useful in creating custom implants, such as joint replacements or dental implants, as they can be tailored to the unique anatomy of the patient. This level of customization ensures a better fit and faster recovery times, making CNC machining a crucial tool in modern medicine.
家電
Advanced CNC machining is also widely used in the production of consumer electronics, where the demand for precision and quality is high. CNC machines are used to create parts like casings, connectors, and internal components for smartphones, computers, and other electronic devices. The ability to produce intricate, durable, and aesthetically pleasing parts is vital in the highly competitive consumer electronics market.
CNC machining enables manufacturers to produce high-quality parts with tight tolerances, ensuring that the finished product meets the desired specifications. As electronic devices continue to evolve, CNC machining will play a key role in producing the next generation of technology.
5. Types of Advanced CNC Machining Techniques
Multi-Axis CNC Machining
Multi-axis CNC machining is one of the most significant advancements in CNC technology. Traditional CNC machines typically work along three axes (X, Y, and Z), but multi-axis machines can move along additional axes, such as the A, B, and C axes. This allows the machine to approach the workpiece from different angles, making it possible to produce more complex parts in a single setup.
The benefits of multi-axis machining are clear. It reduces the need for multiple setups, which in turn reduces the potential for errors and increases efficiency. Parts that would have previously required multiple machines or setups can now be produced with greater accuracy and in less time. Multi-axis machining also allows manufacturers to work with more complex geometries, opening up new possibilities for design and innovation.
High-Speed Machining
High-speed machining (HSM) is a technique that focuses on using CNC machines at faster speeds without compromising on the quality of the finished product. HSM utilizes advanced materials and tooling to cut parts at a much higher rate than traditional machining. This process is particularly useful for industries that require quick turnaround times, such as automotive or consumer electronics manufacturing.
High-speed machining allows manufacturers to significantly reduce production times, enabling them to meet tight deadlines without sacrificing precision. The speed of the process also leads to greater throughput, which ultimately translates to cost savings for manufacturers. By optimizing the machining process for speed, high-speed CNC machines can handle larger production runs without a drop in quality.
Electro-Discharge Machining (EDM)
Electro-discharge machining (EDM) is a specialized process used for creating extremely precise holes and intricate shapes in hard materials. Unlike traditional CNC machining, which uses cutting tools to remove material, EDM uses electrical discharges to erode the material and create the desired shape. This process is particularly useful for creating parts with complex geometries that are difficult to machine using traditional methods.
EDM is commonly used in industries that require high-precision components, such as aerospace, automotive, and medical device manufacturing. The key advantage of EDM is its ability to produce features that are hard to achieve with conventional cutting tools, such as small holes, sharp corners, and fine details. EDM also has the ability to work with materials that are too hard for traditional machining, such as tungsten carbide and hardened steel.
6. Advanced CNC Machining vs. Traditional Machining
Key Differences
When comparing advanced CNC machining to traditional machining, the differences are clear. Traditional machining relies heavily on manual labor, with operators controlling machines by hand to cut, shape, and form materials. While this method can still be effective for certain tasks, it often lacks the precision, consistency, and speed offered by CNC machines.
Advanced CNC machining uses computer control to guide machine tools through precise movements, ensuring that parts are manufactured to exact specifications. The automation involved in CNC machining reduces the risk of human error and allows for faster production times. Additionally, CNC machines can work with a wide range of materials, offering greater flexibility compared to traditional machining.
Cost Comparison: CNC vs. Traditional
Although the upfront cost of CNC machines can be higher than traditional machining tools, the long-term savings are significant. CNC machines require less manual labor, leading to lower labor costs over time. Additionally, CNC machines can operate for longer periods without supervision, increasing productivity. The precision of CNC machining also reduces material waste, which further contributes to cost savings. In the long run, CNC machining offers a more cost-effective solution compared to traditional methods, particularly for high-volume production.
7. The Role of Automation in Advanced CNC Machining
Automation Benefits in CNC Machining
One of the major advantages of advanced CNC machining is the level of automation it introduces. Automation refers to the use of technology to perform tasks without human intervention. In CNC machining, automation is used to control machine tools, load and unload parts, and even monitor the machining process in real-time.
The benefits of automation in CNC machining are numerous. First, it significantly reduces the need for manual labor, which can help lower operational costs. Automation also improves the consistency and quality of production, as machines can perform the same task repeatedly with minimal variation. By automating certain processes, manufacturers can increase production speed, reduce human error, and maintain high levels of precision.
Collaborative Robots (Cobots)
Collaborative robots (cobots) are a recent innovation in CNC machining. Unlike traditional industrial robots that work in isolation, cobots are designed to work alongside human operators, assisting them with tasks like loading and unloading parts, measuring finished products, and even adjusting machine settings. Cobots are an excellent solution for small-batch production and custom orders, where flexibility and quick setup times are essential.
The integration of cobots into CNC machining operations has the potential to increase productivity and reduce the strain on operators. Cobots are easy to program and can be reconfigured for different tasks, making them ideal for manufacturers looking to adapt to changing production needs.
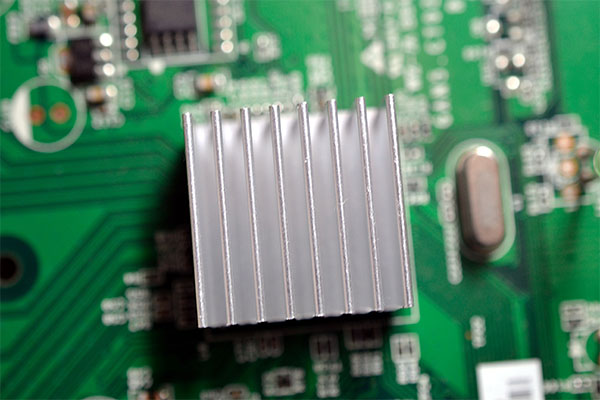
8. The Impact of AI and Machine Learning on CNC Machining
Predictive Maintenance and Real-Time Monitoring
AIと機械学習 have a significant impact on CNC machining, particularly in the area of predictive maintenance. AI systems can analyze data from CNC machines in real-time, predicting when a machine is likely to fail or require maintenance. By identifying potential issues before they become critical, manufacturers can schedule maintenance and repairs proactively, reducing downtime and increasing machine availability.
Real-time monitoring powered by AI also helps operators monitor the health of the machines during production. If a machine starts to deviate from its optimal performance, AI algorithms can send alerts to operators, allowing them to make adjustments before a problem becomes serious. This proactive approach to machine management helps keep production running smoothly and efficiently.
Enhancing Precision Through Machine Learning
Machine learning algorithms are used to fine-tune machining processes for greater precision and consistency. As CNC machines collect more data, machine learning models can analyze this information to identify patterns and optimize machining parameters automatically. This means that over time, CNC machines become more efficient and accurate, producing higher-quality parts with less human intervention.
By utilizing machine learning, manufacturers can ensure that their CNC machines are continuously improving and adapting to new challenges. This enhances the overall quality of the finished product and reduces the likelihood of errors during production.
9. Overcoming Challenges in Advanced CNC Machining
High Initial Investment
One of the main barriers to adopting advanced CNC machining is the high initial investment required to purchase and set up the machinery. Advanced CNC machines are expensive, and the costs associated with software, training, and maintenance can add up quickly. However, the long-term benefits of CNC machining often outweigh the initial costs, particularly for businesses that require high-volume production or need to produce complex parts with high precision.
For manufacturers looking to overcome the cost barrier, financing options and leasing programs are often available. Additionally, the return on investment from increased productivity and reduced operational costs can help justify the initial expense.
Skilled Workforce and Training
Another challenge associated with advanced CNC machining is the need for skilled operators and programmers. CNC machines are highly sophisticated and require operators who understand both the technology and the materials they are working with. As machines become more advanced, the skill set required to operate them increases.
To overcome this challenge, manufacturers must invest in training programs for their workforce. Providing ongoing education and support for CNC operators ensures that they are able to use the machines effectively and safely. This investment in training also helps reduce errors and improve overall productivity.
Material Handling and Waste Reduction
Material handling is another challenge faced by manufacturers using advanced CNC machining. Managing materials efficiently is critical to reducing waste and improving the overall sustainability of the production process. Advanced CNC machines can help minimize material waste by optimizing cutting paths and using less material during the machining process.
Manufacturers can also use more efficient material handling systems, such as robotic arms and conveyor belts, to improve the flow of materials to and from the machines. This reduces bottlenecks and helps ensure that parts are produced quickly and accurately, with minimal waste.
10. How Advanced CNC Machining Supports Customization
Tailored Products for Niche Markets
One of the main advantages of advanced CNC machining is its ability to produce highly customized parts for niche markets. With traditional manufacturing methods, creating custom parts often requires extensive tooling and setup. However, with CNC machining, manufacturers can quickly reprogram the machines to produce parts with different shapes, sizes, and materials. This capability is invaluable for industries that require tailored solutions, such as medical device manufacturing or aerospace.
CNC machines are capable of producing low-volume, custom parts quickly and efficiently. Manufacturers can work directly with customers to design and produce components that meet specific needs, whether it’s a custom implant for a patient or a specialized part for a research project. This flexibility allows businesses to cater to unique market demands without incurring the high costs typically associated with custom manufacturing.
Benefits for OEMs and Custom Manufacturers
OEMs (original equipment manufacturers) and custom manufacturers benefit greatly from advanced CNC machining. By using CNC machines, they can produce components that meet their exact specifications without the need for new tooling or extensive rework. This allows manufacturers to offer a wide range of custom options without significantly increasing production costs.
For example, CNC machining allows OEMs to produce replacement parts or low-volume custom orders with high precision. This capability is particularly important in industries like automotive, aerospace, and medical devices, where OEMs need to provide high-quality, custom components for their customers.
11. Sustainability and Environmental Impact of Advanced CNC Machining
Reducing Material Waste
Advanced CNC machining is also contributing to sustainability efforts by reducing material waste. Unlike traditional machining methods, which often result in significant material waste due to excessive cutting and reshaping, CNC machines can work with high precision and minimize the amount of material that is discarded during production.
By optimizing cutting paths and tool movements, CNC machines ensure that as much material as possible is used in the finished product. This is particularly important in industries that use expensive materials like aerospace alloys or medical-grade metals, where reducing waste can lead to significant cost savings.
Energy Efficiency in CNC Machines
In addition to reducing material waste, advanced CNC machines are becoming more energy-efficient. Many modern CNC machines are designed to consume less power while delivering the same level of performance. Energy-efficient motors, intelligent cooling systems, and optimized cutting strategies all contribute to a reduction in energy consumption during machining.
The move towards energy-efficient CNC machines is an important step in the push for more sustainable manufacturing practices. As manufacturers continue to adopt more energy-efficient technologies, they will contribute to reducing the carbon footprint of the manufacturing industry as a whole.
12. Future Trends in Advanced CNC Machining
Additive Manufacturing and CNC Integration
One of the exciting trends in advanced CNC machining is the integration of additive manufacturing (3D printing) with traditional CNC machining. While CNC machining excels at creating solid, durable parts, additive manufacturing allows for the creation of complex geometries that would be difficult to achieve with traditional subtractive methods.
The combination of these two technologies creates new possibilities for manufacturers, enabling them to produce hybrid parts that leverage the benefits of both processes. For example, a part could be 3D printed with intricate internal structures and then CNC machined to add precise outer features or improve surface finish.
Integration of IoT in CNC Machines
Another future trend is the integration of IoT (Internet of Things) in CNC machines. IoT-enabled machines can communicate with each other and with a central system, providing real-time data on machine performance, inventory levels, and production progress. This connectivity allows manufacturers to optimize their operations and improve efficiency by monitoring the performance of machines remotely and making adjustments as needed.
By utilizing IoT technology, manufacturers can achieve better insights into machine utilization, predictive maintenance, and overall system performance. This data-driven approach helps reduce downtime, optimize workflows, and improve the overall performance of CNC machining operations.
13. Case Studies of Advanced CNC Machining Success
Case Study 1: Aerospace Industry
The aerospace industry has seen remarkable success with advanced CNC machining. One example is the use of CNC machines to manufacture lightweight, high-strength components for aircraft. CNC machining has enabled manufacturers to produce complex, precise parts for the aerospace sector, ensuring that aircraft perform at optimal levels. One case study highlights the use of CNC to create engine components for a commercial airliner, where precision was critical for the engine’s performance and reliability.
Case Study 2: Automotive Industry
In the automotive industry, advanced CNC machining has transformed the way manufacturers produce high-performance car parts. One notable example is the production of lightweight, strong components for electric vehicles (EVs). CNC machining allows for the precise manufacturing of battery housings, motor parts, and chassis components, all of which require high-performance materials and exact specifications. The use of advanced CNC machines has helped EV manufacturers meet stringent design and production requirements while maintaining cost efficiency.
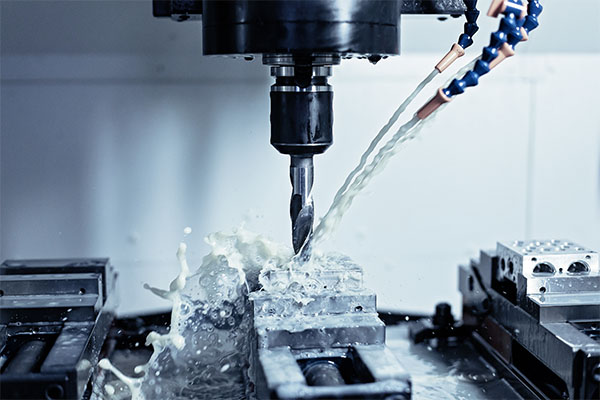
14. Choosing the Right Advanced CNC Machining Service
考慮すべき要素
When selecting an advanced CNC machining service, several factors should be taken into account. First, the machining service should have the necessary expertise and equipment to handle the specific materials and designs required. Look for a provider that specializes in your industry and has experience working with the types of parts you need to produce.
Additionally, consider the service’s quality control processes. A reliable CNC machining service should have stringent quality control measures in place to ensure that every part meets the required specifications. The provider should also offer flexibility and the ability to adapt to changing production needs, whether it’s scaling up for high-volume runs or producing custom parts for specific applications.
Outsourcing CNC Machining: Pros and Cons
For some manufacturers, outsourcing CNC machining can be a cost-effective solution. Outsourcing allows businesses to access state-of-the-art machinery without the need for a large initial investment. It also offers flexibility, as outsourcing partners can handle large orders or handle rush production runs.
However, outsourcing also comes with its challenges. Communication and coordination can sometimes be difficult when working with remote suppliers, and quality control can become an issue if the machining provider does not meet the required standards. When outsourcing CNC machining, it’s crucial to choose a reputable partner that has a proven track record of delivering high-quality parts on time.
15. Conclusion
In conclusion, advanced CNC machining is a powerful tool that has revolutionized manufacturing across various industries. By providing unmatched precision, efficiency, and the ability to work with advanced materials, CNC machining has become indispensable in industries like aerospace, automotive, and healthcare. While the initial investment can be high, the long-term benefits, including cost savings and increased productivity, make CNC machining a worthwhile investment for businesses looking to stay competitive in today’s fast-paced market.
As the technology continues to evolve, we can expect even greater advancements in machine learning, automation, and energy efficiency. The future of CNC machining looks bright, and it will continue to drive innovation across the manufacturing sector. For companies looking to enhance their manufacturing capabilities, embracing advanced CNC machining is the key to staying ahead of the curve.
FAQセクション
What is the difference between CNC machining and traditional machining?
CNC machining uses computer-controlled tools to automate the production process, allowing for higher precision, consistency, and speed. Traditional machining, on the other hand, involves manual operation of tools, which can be more prone to human error and slower production times.
How accurate is advanced CNC machining?
Advanced CNC machining can achieve tolerances as small as a few microns, making it highly accurate. This level of precision is essential for industries that require complex and high-performance parts, such as aerospace and medical devices.
What are the costs involved in using advanced CNC machines?
While the initial investment in advanced CNC machines can be high, the long-term savings from increased productivity, reduced labor costs, and minimized material waste often outweigh the costs. Pricing varies depending on the complexity of the machine and the production requirements.
CNC マシンはどんな材料でも扱えますか?
CNC machines can handle a wide variety of materials, including metals, plastics, composites, and ceramics. The choice of material depends on the type of part being produced and the requirements of the industry.
What are the main industries using advanced CNC machining?
Industries such as aerospace, automotive, healthcare, consumer electronics, and military manufacturing widely use advanced CNC machining due to its precision and ability to handle complex parts.
How long does it take to program a CNC machine for a new part?
The time it takes to program a CNC machine for a new part depends on the complexity of the part and the experience of the programmer. Simple parts may take only a few hours to program, while more complex parts could take several days.
What is the future of CNC machining with AI and automation?
The future of CNC machining is moving towards increased integration of AI and automation. These technologies will enhance the precision, efficiency, and flexibility of CNC machines, allowing for even faster production times and more accurate parts. AI-powered machines will also be able to optimize machining parameters in real-time for continuous improvement.