소개
CNC (Computer Numerical Control) machining is a revolutionary process that allows manufacturers to produce precise and complex parts. One of the most commonly used types of CNC machining is 3 Axis CNC. But what exactly is 3 Axis CNC machining? It’s a process that uses three axes of motion (X, Y, and Z) to shape materials like metals, plastics, and wood. You might be wondering how this system can create such detailed components. Well, in this article, we’ll break down everything you need to know about 3 Axis CNC machining, from its basic mechanics to its applications in various industries.
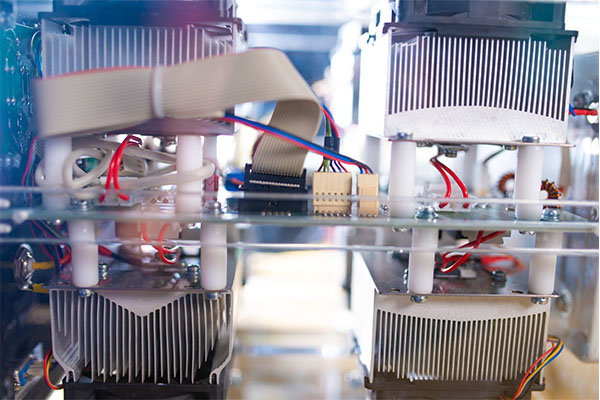
What is 3 Axis CNC Machining?
Defining the 3 Axis CNC System
At its core, a 3 Axis CNC machine is a computer-controlled tool that uses three different movements—along the X, Y, and Z axes—to shape a workpiece. These three axes allow the machine to carve and cut materials with exceptional precision. The X-axis moves the tool left and right, the Y-axis moves the tool forward and backward, and the Z-axis moves the tool up and down. Together, these axes give the machine the ability to handle complex tasks like drilling, milling, and engraving.
Basic Components of a 3 Axis CNC Machine
The key components that make up a 3 Axis CNC machine are quite simple but powerful. First, there’s the tool holder where different cutting tools are attached, and these tools perform the actual machining. The spindle, which is powered by a motor, rotates the tools. Then, the machine’s computer system controls the movement of the entire machine. Lastly, the workpiece is clamped onto a table, where it stays stationary as the cutting tool moves around it. All of these parts work together seamlessly to create precise components.
How Does a 3 Axis CNC Machine Work?
The main advantage of 3 Axis CNC machining lies in its ability to move along three planes of motion to manipulate a workpiece into intricate designs. Each of the three axes is responsible for moving the tool or workpiece in a specific direction. By combining these movements in real time, the machine can produce parts with an incredible level of accuracy. This system works well for a variety of parts, especially those with relatively simple geometries and moderate levels of complexity.
Key Benefits of 3 Axis CNC Machining
When it comes to manufacturing precision components, 3 Axis CNC machining offers numerous advantages. The machine delivers high accuracy and consistency, making it ideal for industries that demand repeatability and precision. It’s also a cost-effective solution for many types of projects, particularly those involving less intricate designs. In addition, it’s a highly versatile machine that can handle a variety of materials, from metals to plastics, making it suitable for a wide range of applications.
The Mechanics Behind 3 Axis CNC Machines
Movement and Coordinate System
A 3 Axis CNC machine operates using a coordinate system that helps guide its movements. The X, Y, and Z axes work together to create a 3D space where the tool can move along different paths. This system allows for the precise positioning of tools relative to the workpiece, ensuring accurate cuts and consistent results. Each movement is carefully controlled by the CNC software, which interprets commands from the operator and translates them into specific actions performed by the machine.
Types of Movement: Linear and Rotational
In addition to the primary linear movements along the X, Y, and Z axes, 3 Axis CNC machines can also perform rotational movements, although this is typically more common in advanced machines. For example, the spindle itself can rotate to allow for different types of cutting and machining techniques. This ability to combine both linear and rotational movements increases the flexibility and precision of the machine.
G-code: The Language of CNC Machines
The movement of a 3 Axis CNC machine is directed by G-code, a programming language that specifies the machine’s actions. G-code tells the machine where to move, what speed to move at, and what cutting tools to use. Every 3 Axis CNC operation begins with the creation of a design, which is then translated into G-code by CAD/CAM software. This allows for automation of the process, reducing human error and increasing production efficiency.
Common Applications of 3 Axis CNC Machining
Manufacturing Industries
3 Axis CNC machining is widely used across various industries, such as aerospace, automotive, electronics, and medical manufacturing. These industries rely on the precision and efficiency offered by 3 Axis CNC machines. For example, in the aerospace industry, CNC machines are used to create critical components for aircraft that must meet stringent quality and safety standards.
Common Materials Machined
A broad range of materials can be machined with a 3 Axis CNC machine, from metals like aluminum and steel to plastics and composite materials. For metalworking, CNC machines excel at creating complex geometries with excellent tolerance levels. Plastics such as ABS and PVC are also commonly machined for industries that require parts with low weight and good strength properties. Some CNC machines can even handle wood and softer materials, expanding their versatility.
Precision Parts and Complex Geometries
One of the greatest strengths of 3 Axis CNC machining is its ability to handle complex geometries. From intricate designs to parts with multiple features, a 3 Axis CNC machine can mill and drill with precision. It is especially effective in industries like electronics, where parts need to be both lightweight and durable while maintaining highly specific tolerances.
Understanding the Process of 3 Axis CNC Machining
Step 1: Designing the CAD Model
The first step in any CNC machining process is designing the part using Computer-Aided Design (CAD) software. The CAD model serves as the blueprint for the entire machining process. By designing the part in digital space, you can plan out the specific features, dimensions, and tolerances required for the part. This design can then be shared with the CNC machine for production.
Step 2: Converting CAD to G-code
Once the CAD model is complete, it is converted into a G-code format using Computer-Aided Manufacturing (CAM) software. This conversion ensures that the CNC machine understands the design and can execute the necessary movements. The G-code file tells the CNC machine everything it needs to know—where to cut, the order of operations, and which tools to use.
Step 3: Setting Up the CNC Machine
After the G-code is generated, the next step is to set up the CNC machine. This involves attaching the cutting tools and securing the workpiece on the machine’s table. During setup, the operator will also input any necessary settings, such as spindle speed, feed rates, and tool paths, which ensures that the machining process goes smoothly.
Step 4: The Machining Process
With everything in place, the CNC machine begins its machining process. Using the G-code as a guide, the machine moves the tool across the workpiece to shape it according to the design. The tool removes material by cutting, drilling, or milling, leaving behind the desired part. The machine continuously adjusts its movements based on the G-code instructions, ensuring each cut is precise.
Step 5: Post-machining and Finishing
Once the machining process is complete, the part may require post-processing. This could include polishing, cleaning, or further machining to meet exact specifications. The final part is then inspected for quality and precision. In some cases, additional steps like heat treatment or coating may be necessary, depending on the material and application.
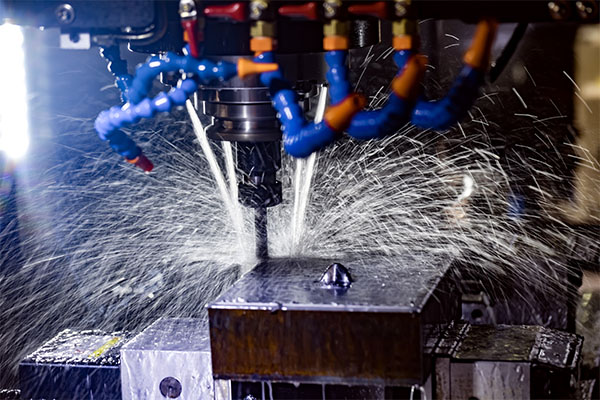
Key Advantages of 3 Axis CNC Machining
High Precision and Accuracy
3 Axis CNC machines are known for their exceptional precision and accuracy. By controlling the position of the tool along three axes, the machine can make extremely fine cuts and produce parts to within tight tolerances. This level of accuracy is essential for industries that demand the highest quality, such as aerospace and medical device manufacturing.
Faster Production and Reduced Errors
Unlike manual machining, CNC machines can operate autonomously, producing parts faster and with fewer errors. This increased efficiency allows for quicker turnaround times, reducing production costs and meeting tight deadlines. Moreover, CNC machining helps reduce human error, ensuring a more reliable and consistent production process.
Versatility in Producing Complex Parts
3 Axis CNC machines can handle a wide range of parts, from simple designs to more intricate shapes. The flexibility of CNC machines makes them suitable for a variety of applications across industries. They can create complex shapes and detailed designs that would be nearly impossible to achieve with manual methods.
Automation Benefits
3 Axis CNC machines can operate autonomously, allowing manufacturers to run operations with minimal oversight. This automation eliminates much of the labor-intensive work associated with traditional machining methods, resulting in cost savings and higher productivity.
Challenges in 3 Axis CNC Machining
Limited Ability to Reach Certain Angles
One of the main limitations of 3 Axis CNC machining is its inability to access certain angles. For highly complex geometries, a 5 Axis CNC machine may be required. This limitation is particularly problematic when working with parts that need to be cut at multiple angles or require intricate, multi-axis milling.
Tool Accessibility
In some cases, the cutting tool may have difficulty reaching certain parts of the workpiece due to tool accessibility issues. This can slow down production and result in a need for special tooling solutions. However, with careful planning and setup, many of these challenges can be mitigated.
Machine Setup Time and Cost
While CNC machining is efficient during operation, the setup process can be time-consuming and costly. This includes programming the G-code, setting up the machine, and ensuring everything is in alignment. For small batches, the initial setup cost can be a significant factor to consider.
Wear and Tear on Tools
As with any machining process, tools experience wear and tear over time. Cutting tools need to be regularly maintained or replaced to ensure optimal performance. This ongoing maintenance can add to the operational costs and downtime of the machine.
When to Use 3 Axis CNC Machining
Best Applications for 3 Axis Machining
3 Axis CNC machining is best suited for parts with relatively simple geometries and moderate complexity. It is ideal for high-volume production of components that do not require excessive multi-angle cuts. For example, basic components such as brackets, housings, and plates are well-suited to 3 Axis CNC machining.
Factors to Consider When Choosing 3 Axis CNC
When deciding whether 3 Axis CNC machining is the right choice, consider factors such as material type, design complexity, and tolerance requirements. If the part can be produced with just three axes of movement and the required tolerances are achievable, then 3 Axis CNC is a great choice.
Alternatives to 3 Axis CNC Machining
For highly complex parts with intricate angles or curved surfaces, you might need to consider 4 or 5 Axis CNC machining. These machines can handle more advanced cuts and greater precision, making them better suited for certain applications, especially those in the aerospace and medical industries.
3 Axis CNC vs 4 Axis and 5 Axis CNC Machining
Key Differences Between 3 Axis, 4 Axis, and 5 Axis
The main difference between 3 Axis CNC machining and its more advanced counterparts lies in the number of axes used. A 4 Axis machine adds a rotational axis, which allows for machining parts that require multi-sided cutting. A 5 Axis machine takes it a step further by allowing both rotational and tilting movements, making it perfect for very complex parts.
When to Choose a 4 Axis or 5 Axis CNC Machine
If you’re working with parts that require multiple angles or intricate, curved surfaces, a 4 or 5 Axis machine will be necessary. However, for simpler designs, 3 Axis CNC machining can still deliver high-quality results at a lower cost.
Comparing Cost Efficiency
While 4 and 5 Axis CNC machines offer more flexibility, they are also significantly more expensive to operate and maintain. If your parts do not require the advanced capabilities of these machines, 3 Axis CNC machining remains the most cost-effective option.
CNC Milling vs CNC Turning: Which Is Best for Your Project?
Differences Between Milling and Turning
CNC milling and CNC turning are two common machining processes used in the industry. CNC milling involves moving a rotating tool across a workpiece, while CNC turning involves rotating the workpiece against a stationary tool. The choice between these methods depends on the shape and features of the part you are creating.
Which Process Is Suitable for Your Parts?
CNC milling is generally better for parts with flat surfaces or irregular shapes, while CNC turning is ideal for parts that are cylindrical in shape. For many parts, a combination of both processes might be required to achieve the desired result.
Choosing the Right 3 Axis CNC Machine for Your Business
Factors to Consider
When selecting a 3 Axis CNC machine, consider factors such as machine size, precision, and tooling options. Think about your specific production needs and the types of materials you plan to machine. A well-suited machine will ensure maximum efficiency and cost savings.
Evaluating the Machine Manufacturer
Choose a reputable manufacturer with a track record of high-quality machines. Make sure the manufacturer offers good customer service, including training, support, and maintenance.
Maintenance and Support
Regular maintenance is essential to keeping your machine in optimal working condition. Be sure to work with a supplier who offers comprehensive after-sales support. This will help minimize downtime and keep your machine running smoothly.
How 3 Axis CNC Machining Is Revolutionizing Modern Manufacturing
Impact on Small and Large Manufacturers
Both small and large manufacturers benefit from the precision, speed, and cost-effectiveness of 3 Axis CNC machining. Small businesses can access advanced machining technology without incurring the huge costs associated with manual machining or more complex CNC systems.
Adoption of CNC Machining in Emerging Markets
As CNC technology becomes more affordable, it is being adopted by manufacturers in emerging markets to increase efficiency and produce high-quality parts. This has led to a global surge in CNC machining, particularly in industries like automotive and aerospace.
The Role of Automation and AI in CNC Machining
Automation and artificial intelligence (AI) are increasingly being integrated into CNC machining. These technologies help optimize production processes, improve machine precision, and reduce human error.
Common Materials Used in 3 Axis CNC Machining
Metal Alloys
3 Axis CNC machines can work with a variety of metal alloys, including aluminum, steel, and titanium. Each material has its unique properties that make it suitable for different applications. For example, titanium is used in aerospace due to its strength-to-weight ratio, while aluminum is often chosen for its lightweight and corrosion-resistant properties.
Plastics and Composites
In addition to metals, plastics and composites can be machined using 3 Axis CNC machines. Materials like ABS, PVC, and carbon fiber are common choices for industries like automotive and electronics, where lightweight, durable materials are needed.
Wood and Other Materials
Wood is another material that can be machined using 3 Axis CNC. CNC machining allows for precise cuts and detailed carvings on wood products, making it ideal for creating furniture, cabinetry, and decorative items.
Choosing the Right Material for Your Project
When selecting materials for CNC machining, consider the specific requirements of your project, including strength, durability, weight, and cost. The right material choice will help ensure that the final product meets your needs.
Tips for Optimizing Your 3 Axis CNC Machining Process
Speed and Feed Rate Adjustments
Adjusting the speed and feed rates is essential for optimizing your machining process. The speed at which the tool moves and the feed rate can significantly impact the quality and efficiency of the cut. Proper adjustments will ensure that your tools last longer and that the parts are made efficiently.
Reducing Tool Wear and Extending Machine Life
Over time, tools experience wear and tear, which can affect machining quality. Regular maintenance, proper tool selection, and optimal feed rates can extend the life of your tools and help keep your CNC machine operating at peak performance.
Improving Surface Finish Quality
Achieving a smooth surface finish is often essential in CNC machining, especially for parts that will be used in high-end products. Using the right cutting tools, optimizing speed and feed rates, and choosing the correct material will help you achieve the desired finish.
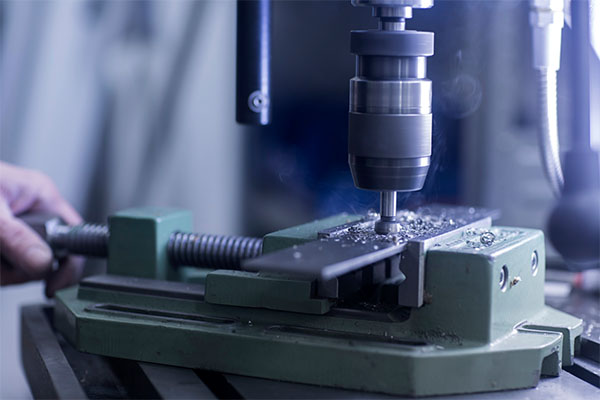
Future Trends in 3 Axis CNC Machining
Integration with 3D Printing
One of the biggest trends in CNC machining is the integration of CNC with 3D printing. This combination allows for more flexible designs and faster production times, as parts can be 3D printed first and then finished with CNC machining for a perfect final product.
Growth of IoT and Smart CNC Machines
The rise of Internet of Things (IoT) technologies is transforming the CNC machining industry. Smart machines equipped with sensors and connectivity features can provide real-time data on machine performance, enabling manufacturers to optimize their processes.
The Rise of Collaborative Robots (Cobots) in CNC Machining
Collaborative robots, or cobots, are increasingly being used in CNC machining. These robots work alongside human operators, enhancing efficiency and safety by performing repetitive or dangerous tasks while allowing the operator to focus on higher-level tasks.
결론
3 Axis CNC machining is an indispensable part of modern manufacturing. From precision to versatility, this process enables industries across the world to produce high-quality, complex parts with ease. If you’re considering using CNC machining for your project, it’s important to understand its capabilities and limitations. Whether you’re a small business or a large manufacturer, 3 Axis CNC machining offers the perfect balance of efficiency, cost-effectiveness, and precision.
자주 묻는 질문 섹션
What materials can be machined with a 3 Axis CNC machine?
A wide range of materials, including metals (aluminum, steel, titanium), plastics (ABS, PVC), and composites, can be machined with 3 Axis CNC machines.
How accurate is 3 Axis CNC machining?
3 Axis CNC machines are highly accurate and can achieve tight tolerances, often within a few microns, depending on the machine and material.
How much does a 3 Axis CNC machine cost?
The cost of a 3 Axis CNC machine can vary greatly depending on factors like machine size, features, and precision. Prices typically range from $10,000 to $100,000 or more.
Can 3 Axis CNC machines handle large parts?
Yes, 3 Axis CNC machines can handle a variety of part sizes, including large components. However, very large parts may require larger machines or specialized setups.
What are the most common issues faced in 3 Axis CNC machining?
Common challenges include tool wear, machine calibration issues, and limited access to certain angles or surfaces in complex parts.
How often should a 3 Axis CNC machine be serviced?
Regular maintenance is essential to keep CNC machines in good working condition. Typically, routine maintenance should be performed every few hundred hours of operation, but more frequent checks may be necessary for high-usage environments.