Introduction: The Growing Demand for CNC Machining in the Medical Industry
CNC 가공 has revolutionized manufacturing across various sectors, but its role in the medical industry is particularly significant. Medical devices and components often require the utmost precision, durability, and customization to meet stringent health and safety standards. Whether it’s the creation of surgical tools, implants, or prosthetics, CNC machining ensures that these items are produced with extreme accuracy and repeatability. As medical technologies advance, the demand for CNC-machined parts is rapidly increasing, driven by the need for faster, more reliable production methods that can meet the growing global healthcare needs. In this article, we’ll explore how CNC machining plays a critical role in the medical sector, highlighting its benefits, challenges, and future potential.
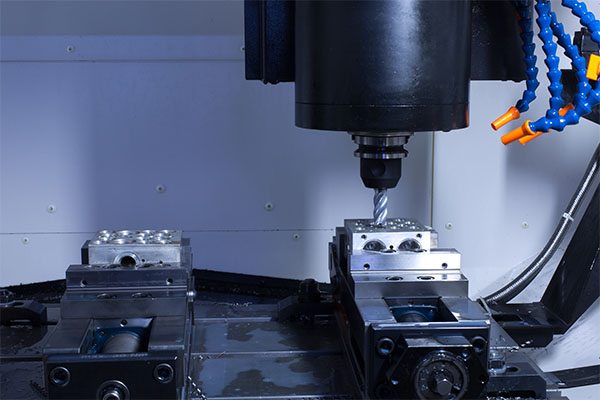
What is CNC Machining? A Quick Overview for Medical Manufacturers
CNC machining, or Computer Numerical Control machining, is a manufacturing process that utilizes pre-programmed computer software to control the movement of machinery tools. These tools are used to remove material from a workpiece to create the desired shape or form. CNC machines are precise, efficient, and capable of producing complex geometries that are impossible or highly difficult to achieve with manual methods.
How CNC Machines Work
CNC machines are automated tools that execute precise movements based on the instructions provided by a computer program. The machine moves along several axes, such as the X, Y, and Z axes, to manipulate a cutting tool (such as a drill or lathe) that removes material from the workpiece. These movements are guided by a 3D model or CAD design, which ensures high precision and consistency.
In the medical sector, CNC machining is used to create a wide range of parts, including surgical instruments, dental implants, and prosthetic devices. The process allows manufacturers to produce high-quality components with exceptional dimensional accuracy and repeatability, meeting the exacting standards required in healthcare applications.
Why CNC Machining is Crucial for the Medical Industry
The medical industry often involves the creation of components that must fit within strict tolerance limits, as they are used in critical applications such as surgery or patient care. CNC machining is uniquely suited to meet these requirements. With its ability to produce parts that are both highly precise and reproducible, CNC machining ensures that medical components are safe, reliable, and effective in their intended use.
Moreover, CNC machining supports the customization of parts, allowing manufacturers to create unique components based on individual patient needs, improving patient outcomes. As the medical field continues to innovate, the demand for CNC machining will likely increase as healthcare providers strive for even greater precision and efficiency in their medical devices and instruments.
Why the Medical Industry Chooses CNC Machining
The medical industry faces unique challenges when it comes to manufacturing, including strict regulations, high-quality standards, and the need for rapid production. CNC machining has emerged as the preferred method for creating high-precision, reliable medical components due to its many advantages.
High Precision and Accuracy
CNC machines are capable of producing parts with micron-level precision, making them ideal for medical applications where accuracy is critical. For example, a surgical tool must be precisely shaped and finished to function correctly. CNC machining ensures that these tools are produced with the highest degree of accuracy, reducing the likelihood of errors during surgery.
Repeatability and Consistency
Another key benefit of CNC machining is its repeatability. Once a machine is programmed with the specifications for a particular part, it can produce identical copies with minimal variation. This is especially important in the medical industry, where even small deviations from design can affect the safety and functionality of a device. CNC machining ensures that every part produced meets the same high-quality standards.
Customization and Complex Geometries
The medical field often requires custom components that are tailored to the specific needs of patients or healthcare providers. CNC machining excels at producing complex geometries and custom designs that are difficult or impossible to achieve with traditional manufacturing methods. Whether it’s a one-off prototype or a small batch of parts, CNC machines can quickly adapt to changing specifications and produce highly detailed and intricate components.
Reduced Lead Times
In today’s fast-paced medical industry, speed is essential. CNC machining offers faster production times compared to traditional methods, especially when combined with modern technologies like rapid prototyping. This is particularly beneficial when manufacturing custom parts or when a quick turnaround is required for a medical device. As a result, CNC machining helps manufacturers meet deadlines and respond to urgent needs more effectively.
비용 효율성
While CNC machining may initially seem costly due to the need for advanced equipment, it often proves more cost-effective in the long run. This is because it reduces material waste, minimizes the need for manual labor, and lowers the risk of production errors. As a result, manufacturers can deliver high-quality parts at competitive prices, making CNC machining a viable option for medical manufacturers seeking both quality and cost efficiency.
Key Materials Used in Medical CNC Machining
CNC machining in the medical industry requires specific materials that can withstand the demanding conditions of medical applications. These materials must be biocompatible, durable, and capable of withstanding high levels of stress, corrosion, and sterilization. Below are some of the most commonly used materials in medical CNC machining:
스테인리스 스틸
Stainless steel is one of the most widely used materials in medical CNC machining due to its strength, corrosion resistance, and biocompatibility. It is commonly used in the production of surgical instruments, implants, and medical hardware. Stainless steel alloys, such as 316L, are especially favored for their resistance to pitting, cracking, and other forms of corrosion, making them ideal for applications that involve exposure to bodily fluids or harsh sterilization processes.
티탄
Titanium is another essential material in medical CNC machining, particularly for applications that require high strength-to-weight ratios. It is commonly used in orthopedic implants, dental implants, and surgical instruments. Titanium’s biocompatibility makes it suitable for long-term implantation in the human body, and its resistance to corrosion ensures that the materials maintain their integrity over time.
Medical-Grade Plastics
In addition to metals, medical-grade plastics are frequently used in CNC machining for medical devices. Materials such as PEEK (Polyether ether ketone), POM (Polyoxymethylene), and PTFE (Polytetrafluoroethylene) are popular choices due to their chemical resistance, low friction properties, and biocompatibility. These plastics are commonly used in the production of components like housings for medical devices, tubing, and even some surgical instruments.
알류미늄
Aluminum is used in CNC machining for medical parts that require a combination of strength and lightness. It is commonly found in diagnostic equipment, surgical tools, and assistive devices. Although aluminum is not as biocompatible as stainless steel or titanium, it is often used for non-implantable components that do not come into direct contact with the human body.
Ceramics
Ceramics, including zirconia and alumina, are used in some highly specialized medical applications, such as dental implants, prosthetics, and wear-resistant components. These materials offer excellent strength, durability, and biocompatibility, making them ideal for long-term use in the human body.
The ability to work with a wide range of materials is one of the reasons why CNC machining is so versatile and well-suited to the medical industry. Manufacturers can select the best material for each specific application, ensuring that the parts meet the necessary performance and safety standards.
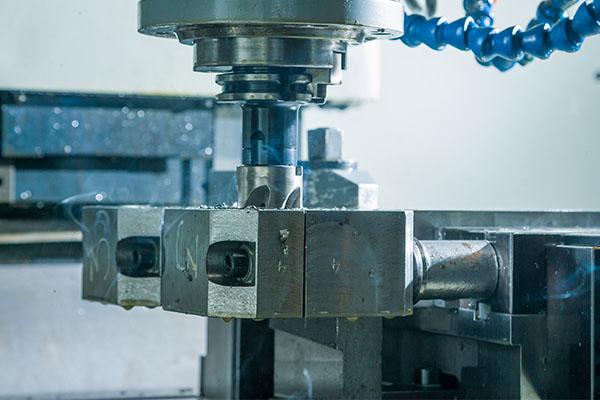
Precision and Tolerances: Meeting Medical Industry Standards
One of the primary reasons CNC machining is so highly valued in the medical industry is its ability to produce parts with extremely tight tolerances. In medical device manufacturing, tolerances refer to the allowable deviations from a part’s intended dimensions. Tight tolerances are crucial in the medical sector because even minor deviations can result in a malfunctioning device or pose a safety risk.
The Importance of Tolerances in Medical Devices
Medical devices are often required to function in highly controlled environments and must operate under extreme precision. For example, implants must fit seamlessly with surrounding tissues or bones to ensure effective healing and long-term durability. Surgical instruments must be finely tuned to ensure they perform as expected during procedures. Any deviations from design specifications can compromise the device’s functionality, safety, or patient comfort.
How CNC Machining Meets These Demands
CNC machining is inherently capable of achieving tight tolerances, often as low as 0.001 mm (1 micron), depending on the machine and material used. This level of precision is essential when working with parts that must fit perfectly within the human body, such as implants or prosthetics.
Furthermore, CNC machining ensures that parts are produced consistently, meaning that even large batches of components will adhere to the same high-quality standards. This repeatability is a major advantage when manufacturing medical devices in large quantities, where uniformity is paramount.
Advanced CNC Technologies for Tight Tolerances
Modern CNC machines are equipped with advanced features that enable them to meet the stringent tolerance requirements of the medical industry. Features like 5-axis machining allow for the production of complex geometries that require precise control over multiple axes. Additionally, advancements in CAD/CAM software make it possible to design and simulate parts with intricate details before they are even manufactured, ensuring that the final product adheres to the required tolerances.
The combination of high-precision machines and advanced software ensures that CNC machining is a reliable and efficient method for producing medical components that meet or exceed industry standards for quality and performance.
Rapid Prototyping: Accelerating Innovation in Medical Device Development
The healthcare industry is continually evolving, with new medical devices and technologies emerging at an ever-increasing pace. Rapid prototyping has become an essential tool for medical device manufacturers to keep up with this demand for innovation. CNC machining plays a critical role in this process by enabling quick and cost-effective prototyping of medical components.
What is Rapid Prototyping?
Rapid prototyping refers to the process of quickly creating a physical model or prototype of a design, often using the same materials and processes that will be used in full-scale production. This allows manufacturers to test and refine their designs before committing to full production, reducing the risk of errors and costly revisions later on.
How CNC Machining Supports Rapid Prototyping
CNC machining is particularly well-suited for rapid prototyping because of its flexibility and precision. Using a computer-aided design (CAD) file, manufacturers can quickly create a prototype of a medical device or component in a matter of hours or days. This is significantly faster than traditional methods, such as casting or molding, which can take much longer.
Additionally, CNC machines can produce prototypes in a wide variety of materials, including metals and plastics, which makes them ideal for testing different design options. This ability to quickly produce and test prototypes allows medical manufacturers to iterate on designs more efficiently and bring products to market faster.
The Benefits of Rapid Prototyping in Medical Device Development
Rapid prototyping enables medical manufacturers to streamline their product development processes, resulting in quicker time-to-market for new devices. It also reduces the risk of manufacturing defects and ensures that the final product meets the necessary functional and regulatory requirements. Furthermore, the ability to test prototypes in real-world conditions allows manufacturers to identify potential issues early on, saving both time and money in the long run.
Customization: How CNC Machining Supports Tailored Medical Solutions
One of the most significant advantages of CNC machining in the medical industry is its ability to create customized, patient-specific parts. Whether it’s a custom implant, prosthetic, or surgical tool, CNC machining offers unparalleled flexibility in terms of design and production. This customization is particularly valuable in the medical field, where the needs of each patient can vary significantly.
Personalized Implants and Prosthetics
CNC machining allows manufacturers to create custom implants and prosthetics that are specifically tailored to the individual patient’s anatomy. For example, in orthopedic surgery, custom joint implants can be designed to fit a patient’s unique bone structure, improving the likelihood of a successful outcome and reducing the risk of complications.
By using advanced imaging techniques such as CT or MRI scans, manufacturers can create highly detailed 3D models of a patient’s anatomy. These models can then be used to design and manufacture personalized implants or prosthetics using CNC machining, ensuring a perfect fit and optimal performance.
Custom Surgical Instruments
In addition to implants, CNC machining is also used to create custom surgical instruments designed for specific procedures. Surgeons often require specialized tools to perform complex operations, and CNC machining allows for the creation of tools that are perfectly suited to the surgeon’s needs. This level of customization ensures that medical professionals have the right tools to perform their jobs with precision and confidence.
Adapting to Changing Patient Needs
The ability to quickly produce customized components also enables manufacturers to respond more effectively to changes in patient needs. For example, a patient may require a new implant due to changes in their condition or anatomy. CNC machining allows manufacturers to quickly produce a new implant with minimal lead time, ensuring that patients receive the best possible care.
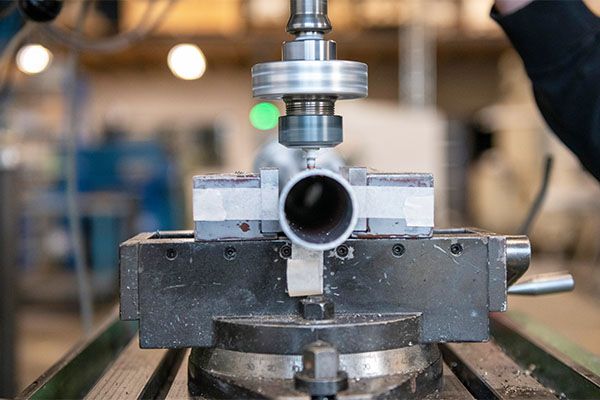
Quality Control: Ensuring Consistency and Compliance in Medical Manufacturing
Ensuring the quality and consistency of medical components is of utmost importance, as even small defects can lead to serious consequences for patient health and safety. CNC machining plays a critical role in maintaining the high-quality standards required in the medical industry.
Stringent Quality Control Measures
CNC machining is an inherently precise process, but additional quality control measures are still necessary to ensure that each part meets the required standards. These measures can include visual inspections, dimensional checks, and tests for material properties. For highly critical components, such as implants or surgical tools, additional non-destructive testing (NDT) methods may be employed to ensure the integrity of the parts.
Compliance with Industry Standards
Medical manufacturers must comply with strict regulations, such as ISO 13485, which outlines the requirements for a quality management system in the production of medical devices. CNC machining can help meet these standards by ensuring that parts are consistently produced to the required specifications. In addition, CNC machining processes can be easily documented and traced, which is essential for compliance with regulatory agencies such as the FDA.
Minimizing Human Error
The automation of CNC machining significantly reduces the potential for human error, which is a common risk factor in traditional manufacturing processes. By using computer-controlled machines, manufacturers can achieve higher levels of accuracy and consistency in their production processes. This is particularly important in the medical field, where even small deviations from specifications can have serious consequences.
Case Study: Successful Medical CNC Machining Projects
In this section, we will explore several real-world examples of how CNC machining has been used to produce critical medical components, demonstrating the advantages of the process in action. These case studies highlight the precision, customization, and speed that CNC machining brings to the medical industry.
The Cost Benefits of CNC Machining for Medical Manufacturers
CNC machining is often considered an investment, but it offers numerous long-term cost benefits, particularly when it comes to producing high-quality, complex parts for the medical industry. By reducing material waste, increasing production speed, and improving consistency, CNC machining helps manufacturers lower overall production costs.
Speed and Scalability: CNC Machining for High-Volume Medical Production
CNC machining not only excels at producing custom parts, but it also supports large-scale production runs. The scalability of CNC machining allows manufacturers to produce both small and large volumes of medical components with equal precision and speed, ensuring that demand is met efficiently.
Challenges in CNC Machining for the Medical Sector
Despite its many benefits, CNC machining for medical applications does present some challenges, such as material limitations, complex geometries, and the need for highly skilled operators. However, with advances in technology and expertise, these challenges can be overcome, ensuring that CNC machining remains a top choice for medical device manufacturers.
The Role of Technology in Enhancing CNC Machining for Medical Parts
Advancements in CNC machining technology, including 5-axis machining, CAD/CAM software integration, and automation, are driving innovation in the medical sector. These technologies enable manufacturers to achieve even greater precision, efficiency, and customization in the production of medical components.
How to Choose the Right CNC Machining Partner for Medical Manufacturing
Choosing the right CNC machining partner is critical for medical manufacturers. Factors such as experience, certifications, and technological capabilities should be considered when selecting a partner to ensure that your medical components meet the necessary quality and regulatory standards.
Conclusion: Why CNC Machining is the Future of Medical Manufacturing
CNC machining is at the forefront of medical device manufacturing, offering precision, customization, and efficiency that is unmatched by traditional methods. As the medical industry continues to innovate, the role of CNC machining will only become more integral, helping to drive the development of new, safer, and more effective medical devices and solutions.
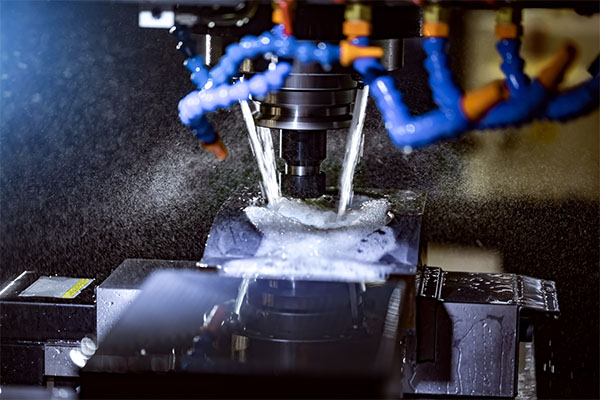
자주 묻는 질문
- What are the main advantages of CNC machining in the medical field? CNC machining offers high precision, repeatability, and the ability to produce complex parts. It also supports customization, rapid prototyping, and reduces lead times for medical devices.
- What materials are typically used for CNC machining medical components? Common materials include stainless steel, titanium, medical-grade plastics (PEEK, POM), aluminum, and ceramics, each selected for their strength, durability, and biocompatibility.
- How does CNC machining ensure consistency in medical manufacturing? CNC machines are computer-controlled, ensuring that parts are produced to exact specifications with minimal variation. This repeatability is crucial for maintaining high-quality standards.
- Can CNC machining produce customized medical devices? Yes, CNC machining excels at producing custom components, including implants, prosthetics, and surgical instruments, tailored to the specific needs of individual patients.
- What challenges do medical manufacturers face when using CNC machining? Challenges include material limitations, the need for highly skilled operators, and the complexity of machining intricate geometries for medical devices. However, these challenges can be addressed with advanced technology and expertise.