소개
Medical device machining is a crucial part of producing high-quality healthcare products. With the growing demand for precision in the medical field, ensuring that medical devices are manufactured with the utmost accuracy and reliability is vital. The demand for expert machining services has surged as companies and healthcare providers alike seek devices that meet rigorous standards. Medical device machining isn’t just about crafting parts – it’s about ensuring those parts function seamlessly, comply with stringent regulations, and contribute to better health outcomes. This article will dive deep into why expert machining is the foundation of the medical device industry, exploring the key features, processes, challenges, and solutions associated with this critical field.
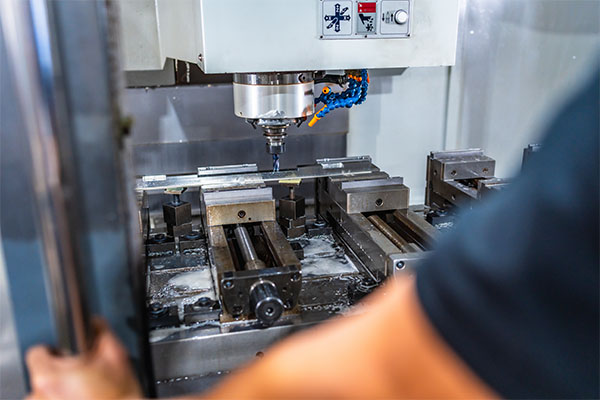
Understanding the Role of Machining in the Medical Industry
Overview of the Medical Device Industry
The medical device industry plays a significant role in the healthcare system, providing tools, equipment, and instruments that are essential for diagnostics, treatment, and care. From life-saving implants to critical surgical instruments, the variety of medical devices is vast. These devices are made from high-performance materials designed to interact safely and efficiently with the human body. The global market for medical devices is expected to continue expanding, driven by advancements in technology, an aging population, and increasing health awareness. This surge in demand creates both challenges and opportunities for manufacturers, particularly in the field of medical device machining.
With growing innovation in medical technology, manufacturers need to ensure that the devices they produce meet the highest standards of precision and performance. Strict regulations govern the production of medical devices, and failure to comply with these standards can result in severe consequences, from financial penalties to safety risks for patients. As such, the demand for expert machinists who can meet these standards continues to rise.
What Makes Medical Device Machining Unique?
Machining medical devices is vastly different from manufacturing standard industrial products. The focus is on precision, biocompatibility, and adherence to strict regulatory guidelines. The materials used in medical devices must meet specific medical standards, such as being non-reactive with body tissues and able to withstand sterilization processes. Medical device machining requires a deeper understanding of materials science, medical regulations, and advanced machining technologies.
Unlike traditional machining, which may focus on high-volume production, medical device machining often involves low-volume, high-precision work. This is especially true when designing custom or patient-specific devices, such as implants or prosthetics. Each part must be crafted to strict tolerances, ensuring both functionality and safety. Regulatory bodies like the FDA and ISO have clear guidelines that all manufacturers must follow, and expert machinists are well-versed in these requirements to ensure compliance.
Key Features of Expert Medical Device Machining
Precision and Accuracy in Medical Devices
Precision is arguably the most critical feature in medical device machining. When manufacturing medical devices, even the smallest errors can lead to product failure, which could have serious consequences for patient safety. Medical devices must meet highly specific measurements to ensure that they fit, function, and perform as expected. From tiny components, such as screws or joints, to complex geometries for implants, expert machining ensures that every part is manufactured to exact specifications.
Advanced techniques like Computer Numerical Control (CNC) machining play a significant role in achieving this level of precision. CNC machines use pre-programmed software to control the movement of the tool, ensuring that every cut, hole, or contour is done with extreme accuracy. For complex designs, machinists may use multi-axis machines to handle intricate shapes or produce devices with multiple features, ensuring the highest quality output.
Material Selection for Medical Devices
Choosing the right material is paramount when machining medical devices. Materials must be durable, biocompatible, and able to withstand various stresses, such as wear and tear, thermal extremes, or chemical exposure. Common materials used include titanium, stainless steel, and high-performance plastics. Titanium, for example, is known for its strength, corrosion resistance, and biocompatibility, making it a popular choice for implants. Similarly, certain medical-grade plastics are used for disposable devices or parts that need to be lightweight yet durable.
The material chosen can also affect the machining process. Harder materials like titanium may require specialized tools or additional cooling during machining to prevent wear or distortion. Expert machinists are skilled in selecting and working with these materials, ensuring that they are machined to the required specifications and meet industry standards for safety and performance.
Advanced Technology in Medical Device Machining
Machining medical devices requires advanced technology to achieve the level of precision and reliability demanded by the industry. CNC machining, laser cutting, and 3D printing are just a few of the technologies used to manufacture medical devices. These technologies allow for the creation of complex shapes and parts with minimal human intervention, reducing the risk of errors.
CNC machines, for example, can produce high-precision components in a variety of materials, making them a staple in the medical device industry. 3D printing, or additive manufacturing, is also increasingly used for prototyping and producing custom parts, particularly for implants or patient-specific devices. This technology allows for quick iteration of designs and the ability to produce complex geometries that would be difficult or impossible to achieve with traditional machining methods.
The Machining Process for Medical Devices
The Step-by-Step Process of Machining Medical Devices
The process of machining medical devices typically begins with the design and prototype phase. During this stage, machinists work closely with engineers to ensure that the design is feasible and meets regulatory requirements. Once the design is finalized, the manufacturing process begins. This involves selecting the appropriate material, programming the machining equipment, and carefully executing each step to produce the parts.
The machining process often involves multiple stages, including rough machining to remove bulk material, followed by precision machining to achieve the final shape and dimensions. Some parts may also require additional operations, such as polishing or coating, to improve their functionality or appearance. Each step of the process is carefully monitored, with quality checks performed to ensure that the parts meet the required standards.
Quality Control and Testing During Machining
Quality control is a crucial part of the machining process for medical devices. Each part is thoroughly tested and inspected to ensure that it meets the required tolerances and performs as expected. This testing may include visual inspections, dimensional checks, and functional tests. In addition to standard inspections, machinists also use advanced technologies such as Coordinate Measuring Machines (CMM) to measure the precise dimensions of parts and ensure accuracy.
The regulatory bodies that govern medical device production require extensive documentation to prove that all quality control checks have been performed. Expert machinists understand the importance of thorough testing and documentation to ensure that the devices are compliant with industry standards and regulations.
Post-Machining Considerations
Once the machining process is complete, medical device manufacturers must consider additional steps such as surface finishing and packaging. Surface finishing involves processes like polishing or coating to ensure that the device is smooth, durable, and free from defects. For some devices, especially those that will be implanted or inserted into the body, sterilization is a critical post-machining step. Devices must be sterilized to ensure that they are safe for use in medical procedures.
Packaging is another key consideration in the post-machining process. Medical devices must be carefully packaged to prevent damage during shipping and ensure that they remain sterile until they reach their destination. Packaging materials must meet specific regulations to prevent contamination and maintain the integrity of the device.
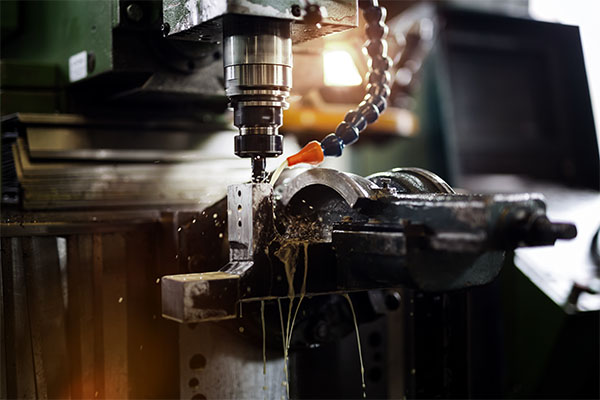
Common Challenges in Medical Device Machining
Regulatory Compliance
One of the biggest challenges in medical device machining is ensuring regulatory compliance. Manufacturers must follow strict guidelines set by regulatory bodies like the FDA and ISO. These guidelines cover everything from design and production to testing and documentation. Non-compliance with these standards can lead to costly delays, fines, or even the inability to market the device.
Expert machinists are familiar with these regulations and work closely with manufacturers to ensure that their products meet all necessary requirements. They play a crucial role in ensuring that the devices are safe for use and meet the required performance standards.
Complexity in Design and Manufacturing
Medical device designs are often highly complex, requiring intricate machining processes to achieve the desired results. Machinists must work with tight tolerances and be able to handle intricate designs that include complex geometries, small parts, or specialized features. Managing these complex designs while maintaining high standards of precision is a significant challenge in medical device machining.
Advanced machining techniques, such as multi-axis CNC machining and additive manufacturing, are often used to handle these complex designs. Expert machinists are adept at overcoming these challenges, ensuring that even the most complex designs are produced accurately and efficiently.
Time and Cost Management
Time and cost management are essential factors in medical device machining. Manufacturers must balance the need for precision with cost-effectiveness and timely delivery. While high-quality machining often requires significant time and resources, expert machinists know how to optimize the production process to reduce costs without sacrificing quality.
Working with an experienced machining partner can help streamline the manufacturing process, ensuring that the devices are produced on time and within budget. Efficient time management and cost control are crucial to ensuring that medical devices are delivered to the market quickly and at an affordable price.
Benefits of Choosing Expert Medical Device Machining Services
Expertise and Experience in the Industry
Choosing a machining partner with extensive experience in the medical device industry is one of the most important decisions a manufacturer can make. Experienced machinists bring a wealth of knowledge to the table, allowing them to navigate complex designs, regulatory requirements, and the challenges of manufacturing medical devices. They understand the nuances of working with medical-grade materials and know how to optimize the machining process to achieve the highest quality results.
In addition, experienced machinists can provide valuable insights and recommendations during the design and prototyping stages. This can help manufacturers avoid costly mistakes and ensure that the final product meets both functional and regulatory requirements.
Improved Accuracy and Precision
When it comes to medical device machining, accuracy and precision are non-negotiable. Expert machinists have the skills and experience needed to deliver parts with exact tolerances and specifications. By using advanced technologies and quality control measures, they can minimize defects and ensure that each part performs as expected.
Expert machining also allows manufacturers to produce devices that fit seamlessly into medical procedures. This level of precision is essential for devices that need to function in the human body, such as implants or surgical instruments.
Customization for Specific Needs
Medical devices are not one-size-fits-all, and often need to be tailored to specific patient needs or medical procedures. Expert machinists are able to provide customized solutions, whether it’s designing a device for a specific anatomical requirement or creating a part with unique features. This level of customization is particularly important in fields like orthopedics, where personalized implants are becoming more common.
Working with an expert machining service ensures that manufacturers can meet the unique needs of their clients, creating devices that are both functional and reliable.
How to Choose the Right Machining Partner for Your Medical Device Needs
Evaluating Expertise and Capabilities
When selecting a machining partner for medical devices, it’s important to evaluate their expertise and capabilities. Look for a partner with a proven track record in medical device manufacturing, particularly in the specific types of devices you need to produce. Ask for case studies or examples of similar projects they have completed successfully.
It’s also important to assess the technologies and equipment they use. Advanced machining technologies such as CNC machines, 3D printers, and laser cutters are essential for achieving the level of precision required in medical device manufacturing. Ensure that your machining partner has access to the necessary tools and resources to meet your production needs.
Importance of Communication and Collaboration
Clear communication is key to the success of any machining project. Ensure that your machining partner is responsive and communicative, keeping you updated on progress and addressing any concerns promptly. Collaboration is also important to ensure that the design and manufacturing process goes smoothly. A strong working relationship with your machining partner will help ensure that your medical device is produced to the highest standards.
Cost and Delivery Considerations
Cost and delivery timelines are always important factors in any manufacturing process. Choose a machining partner that offers competitive pricing without compromising on quality. It’s also important to ensure that they can meet your deadlines and deliver the devices on time. A reliable partner will work with you to establish realistic timelines and ensure that the devices are delivered as promised.
Case Studies: Successful Medical Device Machining Projects
Real-World Examples
Case studies offer valuable insights into the success of medical device machining projects. Successful examples demonstrate the importance of expertise in delivering high-quality devices that meet regulatory requirements and perform as needed. By showcasing real-world examples, manufacturers can see how expert machinists have helped bring innovative medical devices to life.
Lessons Learned and Outcomes
In many cases, lessons learned from past projects can help inform future manufacturing decisions. By analyzing successful projects, manufacturers can identify best practices and avoid common mistakes. Whether it’s understanding material selection, machining techniques, or regulatory compliance, these lessons can lead to better outcomes in future machining projects.
Future Trends in Medical Device Machining
The Role of Automation and AI
Automation and artificial intelligence (AI) are becoming increasingly important in the field of medical device machining. Automation helps streamline the production process, reducing errors and improving efficiency. AI is being used to analyze large sets of data, predict equipment failures, and optimize machining processes.
The use of automation and AI is likely to increase in the coming years, offering even greater precision and efficiency in the manufacturing of medical devices.
Advancements in Materials and Technology
As technology advances, new materials and machining techniques continue to emerge. Additive manufacturing and biocompatible materials are opening up new possibilities for the medical device industry. These advancements will lead to more personalized, effective devices, as well as improvements in device durability and performance.
결론
Medical device machining plays a crucial role in ensuring the safety and effectiveness of healthcare products. By working with expert machinists who understand the complexities of medical device manufacturing, manufacturers can create high-quality devices that meet regulatory standards and perform as needed. Whether you’re producing implants, diagnostic tools, or surgical instruments, choosing the right machining partner is essential to the success of your medical device projects.
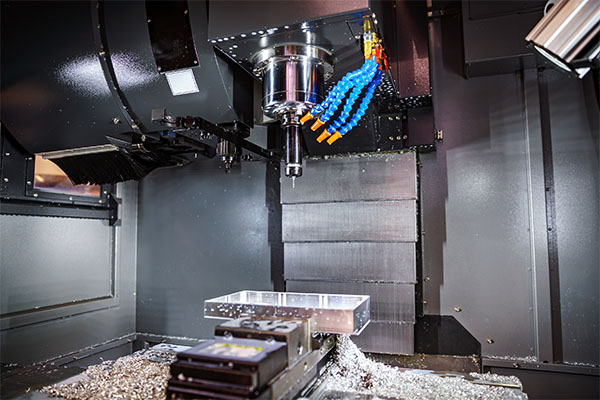
자주 묻는 질문 섹션
What types of materials are typically used in medical device machining?
- Materials like titanium, stainless steel, and medical-grade plastics are commonly used in medical device machining due to their durability, biocompatibility, and resistance to wear and tear.
How do I ensure that my medical device meets regulatory standards?
- Work closely with machinists who are familiar with FDA regulations and ISO certifications to ensure that your devices meet safety, performance, and quality standards.
What is the difference between CNC machining and 3D printing for medical devices?
- CNC machining is best for producing high-precision, complex parts from solid materials, while 3D printing is ideal for rapid prototyping or creating custom parts with intricate geometries.
How can I reduce the cost of machining without compromising quality?
- Focus on optimizing the design and production process to reduce waste, use cost-effective materials, and streamline manufacturing without sacrificing precision or safety.
How long does the machining process for medical devices typically take?
- The machining process can take anywhere from a few days to several weeks depending on the complexity of the design, materials used, and production volume.
What are the most common challenges in medical device machining?
- Some challenges include ensuring regulatory compliance, managing complex designs, and maintaining quality control throughout the production