소개
In today’s competitive manufacturing landscape, businesses are always looking for ways to streamline their processes and enhance product quality. Top CNC machining aluminum services for precision parts are one of the most sought-after solutions for industries that need custom parts with high tolerances and fast production times. Whether you are in aerospace, automotive, or any other sector requiring precision parts, CNC machining has become a reliable choice. This article delves into the various aspects of CNC machining services for aluminum, highlighting key benefits, challenges, and factors to consider when selecting a service provider.
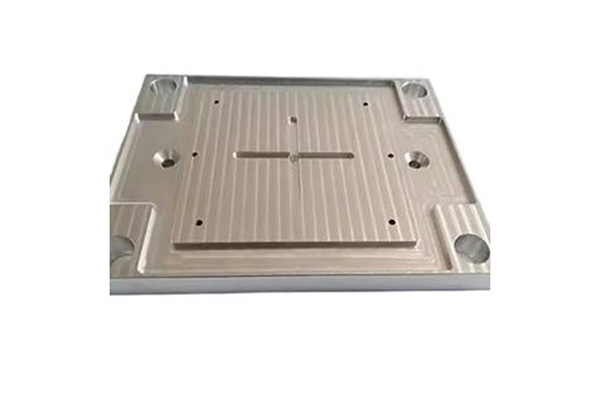
1. Why Choose CNC Machining for Aluminum Parts?
Let’s kick things off by discussing why CNC machining is often the go-to choice for creating aluminum parts. 여기 거래가 있습니다—aluminum is a lightweight, durable, and versatile material, and CNC machining allows manufacturers to cut, shape, and form it with high precision. Aluminum’s properties, including its excellent strength-to-weight ratio and resistance to corrosion, make it an ideal candidate for CNC machining, especially in industries like aerospace, automotive, and electronics. But here’s the kicker—it’s not just about material properties. CNC machining provides high repeatability, which means you can produce large volumes of identical parts with tight tolerances. This consistency is critical when manufacturing precision parts that need to fit and function within specific parameters.
Aluminum’s flexibility doesn’t stop at its mechanical properties. It also has excellent machinability, which means it can be shaped and formed with minimal difficulty. What’s the real story? In CNC machining, precise programming of cutting tools allows for exact specifications to be met, which makes it perfect for complex and intricate designs. Whether you need small, intricate components or larger parts, CNC machining can handle both.
Table 1: Benefits of CNC Machining for Aluminum
혜택 | 설명 |
---|---|
Lightweight | Aluminum is lightweight, making it ideal for applications where weight is a concern, such as aerospace. |
Durability | Offers excellent resistance to wear and corrosion, which is vital for long-lasting parts. |
정도 | CNC machines can manufacture highly accurate parts with minimal human error. |
다재 | Suitable for a wide range of industries, including automotive, aerospace, and electronics. |
2. What Are the Different Types of CNC Machining Services for Aluminum?
You might be wondering, what exactly are the different types of CNC machining services available for aluminum? Well, here’s the thing—CNC machining encompasses a variety of services that each have their specific use cases and advantages. Whether you’re looking for milling, turning, or drilling, understanding which type of service is best suited to your project is essential.
CNC milling is one of the most commonly used machining services for aluminum. This process involves using rotary cutters to remove material from a workpiece, creating shapes like slots, holes, and contours. This is where it gets interesting—milling machines can handle both small and large components with high precision, making them ideal for industries that need quick, custom parts in high volumes.
Turning services are another popular option for CNC machining aluminum parts. During turning, the workpiece is rotated while a cutting tool is applied to it. 당신은 궁금할 수도 있습니다, why is turning such an essential service? Turning is particularly useful for cylindrical parts or parts with circular geometry, like shafts, bushings, and pins. It allows for fine detail and high-speed production with minimal errors.
Drilling, on the other hand, is often used for creating holes in aluminum parts. This process is indispensable in the creation of custom components where precise holes are required for assembly. So, why does this matter? Without accurate drilling, the final product can’t function as intended.
Table 2: Types of CNC Machining Services for Aluminum
Type of Service | 응용 프로그램 |
---|---|
Milling | Used for creating flat surfaces, slots, and other custom shapes. Ideal for complex geometries. |
Turning | Suitable for cylindrical parts, such as shafts and pins. Excellent for high-speed production of round components. |
Drilling | Focused on creating holes in parts for fasteners, alignment, or assembly. |
3. How Does CNC Machining Work for Aluminum?
What’s the real story? CNC machining for aluminum works by using a computer-controlled machine to automate the cutting process. The CNC machine follows a detailed set of instructions provided by a computer program, ensuring that the part is cut to the exact specifications. Let’s break it down—first, a design or blueprint of the part is created, typically in CAD (Computer-Aided Design) software. The design is then translated into a format that the CNC machine can read.
Once the program is loaded, the aluminum block is securely positioned on the machine, and the cutting tools begin to remove material from the block. 즐거운 부분을 볼 준비가 되셨나요? As the machine operates, it continually checks the position and size of the part to ensure it matches the required design. This continuous feedback loop allows for precise cuts and adjustments throughout the process.
Aluminum’s unique properties make it relatively easy to machine, but here’s the kicker—CNC machines still need to be calibrated properly. Accuracy in cutting tools, feed rates, and spindle speed all play a major role in the final outcome. This is why expert operators are needed to ensure the part is machined to perfection.
Table 3: CNC Machining Process Overview
단계 | 설명 |
---|---|
Design | Create a blueprint or 3D model of the part using CAD software. |
Programming | Convert the CAD model into machine-readable G-code for precise instructions. |
Material Placement | Position the aluminum block on the CNC machine for cutting. |
Cutting Process | CNC machine cuts the material based on the programmed instructions to form the desired shape. |
Quality Check | Continuous monitoring ensures the part meets the required specifications. |
4. What Are the Advantages of Aluminum in CNC Machining?
But here’s the kicker—aluminum is one of the most favored materials in CNC machining, and for good reason. Let’s start with its strength-to-weight ratio—aluminum is light yet strong, which makes it perfect for applications that need to reduce weight without sacrificing durability. Take aerospace, for example, where reducing weight is crucial for fuel efficiency.
This is where it gets interesting—aluminum is also corrosion-resistant, especially when compared to other metals like steel. This is important because it ensures that the parts you create will last longer, even in harsh environments. In fact, aluminum is often used for products that need to withstand exposure to water or chemicals, like marine components or automotive parts.
So, why does this matter? Aluminum’s ability to resist corrosion means less maintenance and replacement over time, which can save businesses significant costs in the long run. Combine this with its excellent machinability, and you have a material that offers both performance and cost efficiency.
Table 4: Aluminum Properties for CNC Machining
Property | 설명 |
---|---|
Lightweight | Ideal for weight-sensitive applications, especially in aerospace and automotive industries. |
Corrosion Resistance | Withstands rust and corrosion, ideal for outdoor and marine components. |
Machinability | Aluminum can be easily cut and shaped, allowing for precise and efficient production. |
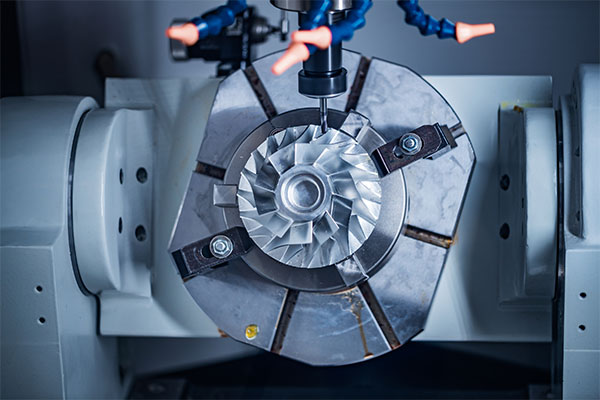
5. How Do CNC Machining Services Ensure Precision in Aluminum Parts?
당신은 궁금할 수도 있습니다, how do CNC machining services ensure that aluminum parts are made with such precision? The secret lies in the high-tech equipment and expert operators involved in the process. What’s the real story? CNC machines are equipped with advanced sensors and feedback mechanisms that constantly monitor and adjust the machining process in real-time, ensuring that parts remain within specified tolerances.
Precision is further achieved by using high-quality cutting tools made from carbide or diamond, which can withstand the demands of cutting aluminum. These tools can maintain sharpness over longer periods, ensuring clean cuts and minimizing the need for tool changes. 즐거운 부분을 볼 준비가 되셨나요? CNC machines also allow for multiple cutting passes, each one refining the part until it reaches the exact specifications. This multi-step process is key to producing highly detailed and accurate components.
Table 5: CNC Machining Precision and Tools
Tool Type | Usage |
---|---|
Carbide Tools | Durable and resistant to wear, perfect for high-speed machining of aluminum. |
Diamond Tools | Ultra-hard tools used for extremely precise cutting and extended tool life. |
Cutting Passes | Multiple cutting passes ensure high precision and reduce errors during machining. |
6. What Are the Common Applications of CNC Machining Aluminum Services?
What’s the real story? CNC machining for aluminum isn’t just a one-size-fits-all solution. The versatility of aluminum makes it applicable in a wide variety of industries. 즐거운 부분을 볼 준비가 되셨나요? Let’s explore some of the most common applications of CNC-machined aluminum parts and why they are so popular.
In the aerospace industry, lightweight yet durable materials are essential. Aluminum is often used for aircraft parts, from structural components to engine parts, due to its ability to withstand the rigors of high-altitude flights without adding excessive weight. But here’s the kicker—the demand for precision in this field makes CNC machining essential. The ability to produce aluminum parts that meet strict safety and performance standards is a key factor for this sector.
Automotive applications are another area where CNC machining for aluminum shines. From engine blocks to transmission parts, aluminum is commonly used to reduce the weight of vehicles, improving fuel efficiency and performance. So, why does this matter? By using CNC machining, manufacturers can achieve the exact specifications needed for these complex components while also reducing production costs.
In the electronics industry, aluminum is often used for heat sinks and enclosures. Its excellent thermal conductivity makes it an ideal material for dissipating heat in electronic devices. Here’s the kicker—CNC machining allows for the precise cutting of intricate heat sinks and custom enclosures that protect sensitive components, ensuring the reliability of electronics.
Table 6: Common Applications of CNC Machining Aluminum
산업 | Application |
---|---|
항공우주 | Aircraft parts, structural components, and engine components made from lightweight, durable aluminum. |
자동차 | Engine blocks, transmission parts, and lightweight components for improved fuel efficiency and performance. |
Electronics | Heat sinks and enclosures for dissipating heat in electronic devices, ensuring longevity and performance. |
7. How to Choose the Right CNC Machining Service Provider for Aluminum?
Choosing the right CNC machining service provider is no small task. 여기 거래가 있습니다—whether you’re working on a one-time project or a long-term partnership, there are key factors to consider. But here’s the kicker—choosing the wrong service provider can lead to delays, increased costs, or poor-quality parts.
Experience is paramount. Look for a CNC machining service with a track record of producing high-quality aluminum parts. What’s the real story? Experienced providers understand the nuances of working with aluminum and can deliver precise and durable parts, no matter how complex the design is. Check their portfolio, case studies, and client testimonials to gauge their expertise in CNC machining aluminum.
능력 are another crucial factor. So, why does this matter? Different service providers may specialize in different types of CNC machining, such as milling, turning, or drilling. Make sure the provider you choose has the specific capabilities needed for your project.
Cost-effectiveness is another factor to weigh. While price shouldn’t be the only consideration, it’s important to ensure that the service provider offers competitive rates without compromising quality. 즐거운 부분을 볼 준비가 되셨나요? Get quotes from multiple providers and compare them to see which offers the best value for your needs.
Table 7: Key Factors in Choosing a CNC Machining Service Provider
요인 | Consideration |
---|---|
Experience | Look for a service provider with a proven track record of CNC machining aluminum parts. |
능력 | Ensure the provider has the necessary CNC machining capabilities, such as milling, turning, or drilling. |
Cost-effectiveness | Compare quotes and ensure you get competitive pricing without compromising quality. |
8. What Are the Costs Involved in CNC Machining Aluminum Parts?
But here’s the kicker—while CNC machining offers high precision and efficiency, the costs can vary depending on multiple factors. What’s the real story? Let’s dive into what influences the cost of CNC machining for aluminum parts.
The complexity of the part plays a significant role in the cost. More intricate designs with tighter tolerances require more time, effort, and precision, which can increase the price. 즐거운 부분을 볼 준비가 되셨나요? Parts that involve more machining operations—such as milling, turning, and drilling—will naturally cost more than simpler designs.
Material costs are another factor that affects overall pricing. While aluminum is relatively affordable compared to other metals like titanium, the specific grade of aluminum you choose can impact the price. So, why does this matter? Higher-grade alloys with better strength or corrosion resistance might be more expensive, but they may offer better performance in the long run.
Production volume is another important consideration. CNC machining is often most cost-effective for medium-to-large batch runs. Smaller runs tend to be more expensive per unit because setup times and machine calibration costs are spread over fewer parts. What’s the real story? To lower unit costs, businesses often opt for larger production volumes.
Table 8: Factors Affecting CNC Machining Aluminum Costs
요인 | 설명 |
---|---|
Complexity of Design | More intricate designs and tighter tolerances require more time and effort, increasing the overall cost. |
Material Type | Higher-grade aluminum alloys typically cost more, but they offer enhanced performance in specific applications. |
Production Volume | Larger production volumes reduce per-unit cost, while smaller runs are generally more expensive. |
9. How Can CNC Machining Improve the Production Process for Aluminum Parts?
Here’s the kicker—CNC machining isn’t just about creating individual parts; it can also improve the entire production process. What’s the real story? By using CNC technology, manufacturers can achieve faster production times, higher precision, and better overall efficiency.
CNC machines are highly automated, which reduces the need for manual labor and minimizes the potential for human error. This automation results in faster turnaround times, especially in high-volume production runs. So, why does this matter? Faster production times mean products can be brought to market more quickly, giving businesses a competitive edge.
CNC machining also minimizes material waste. The precision of CNC machines ensures that only the exact amount of material needed is used, resulting in fewer offcuts and scraps. But here’s the kicker—this not only saves money on material costs but also reduces environmental impact, making CNC machining a more sustainable option.
즐거운 부분을 볼 준비가 되셨나요? CNC machines also provide flexibility in terms of design and materials. If a part needs to be reworked or adjusted, changes can be made quickly and efficiently without the need for retooling, making it easier to adapt to new designs.
Table 9: How CNC Machining Improves Production Efficiency
혜택 | 설명 |
---|---|
오토메이션 | Reduces manual labor and human error, resulting in faster production and fewer mistakes. |
Material Waste Reduction | Precision in cutting minimizes waste, saving money and reducing environmental impact. |
Design Flexibility | Easy adjustments to designs and materials without retooling, improving adaptability. |
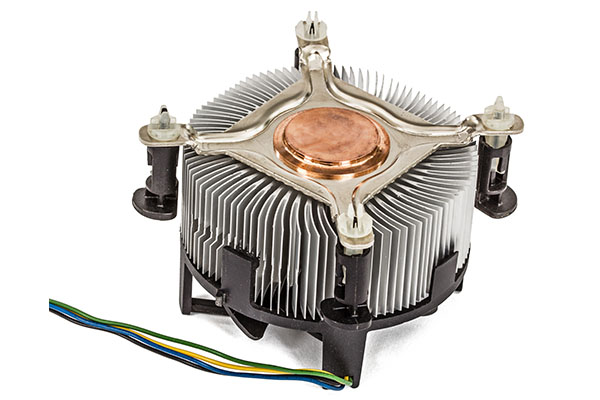
10. What Are the Limitations of CNC Machining for Aluminum?
So, why does this matter? While CNC machining is a powerful and efficient process, it does have its limitations. Here’s the kicker—understanding these limitations is crucial for determining whether CNC machining is the right choice for your project.
One of the main limitations is material constraints. While aluminum is relatively easy to machine, certain grades may be more difficult to work with, especially when dealing with harder materials. 즐거운 부분을 볼 준비가 되셨나요? High-strength alloys may require special tools or longer machining times, which can increase costs.
Another limitation is the tolerance that can be achieved. Although CNC machining offers high precision, there are still practical limits to how fine the tolerances can be. But here’s the kicker—if your project requires ultra-fine tolerances, CNC machining may not be the best choice. Other methods, such as additive manufacturing or EDM (Electrical Discharge Machining), may be more suitable.
What’s the real story? CNC machining is typically limited by the size of the machine and the workpiece. Very large parts may require specialized equipment, which could be more expensive or less readily available.
Table 10: Limitations of CNC Machining for Aluminum
한정 | 설명 |
---|---|
Material Constraints | Some aluminum alloys may require specialized tools or additional machining time, increasing costs. |
Tolerance Limits | CNC machining can only achieve a certain level of precision, making it unsuitable for parts that require ultra-fine tolerances. |
Size Constraints | Very large parts may require specialized CNC equipment, which can increase cost and availability. |
11. How Do Different Aluminum Grades Affect CNC Machining?
Here’s the kicker—the grade of aluminum used can significantly impact the CNC machining process. What’s the real story? Different aluminum grades have varying strengths, hardness, and machinability, which can influence how easily they can be processed and the final quality of the part.
So, why does this matter? For example, 6061 aluminum is one of the most common grades used in CNC machining. It’s known for its good strength-to-weight ratio and corrosion resistance. It’s also relatively easy to machine, making it a favorite in industries like aerospace and automotive.
On the other hand, 7075 aluminum is much stronger but harder to machine. 즐거운 부분을 볼 준비가 되셨나요? While it’s ideal for applications that require high strength, like military and aerospace components, it may require more advanced equipment and longer machining times, which can drive up costs.
But here’s the kicker—understanding the properties of different aluminum grades is essential for choosing the right material for your project. It ensures you get the right balance between machinability, strength, and cost.
Table 11: Aluminum Grades and Their Effects on CNC Machining
Aluminum Grade | 속성 | Machinability |
---|---|---|
6061 | Good strength-to-weight ratio, corrosion-resistant, versatile for many applications. | Easy to machine, ideal for a wide range of applications. |
7075 | High strength, excellent for aerospace and military components. | Harder to machine, requires specialized tools and longer machining time. |
2024 | Known for its high strength and excellent fatigue resistance, commonly used in aircraft. | Requires more advanced equipment and care during machining. |
12. What Are the Sustainability Considerations for CNC Machining Aluminum?
What’s the real story? Sustainability is a hot topic, and CNC machining is no exception. Here’s the kicker—aluminum is one of the most sustainable materials you can use for CNC machining because it’s highly recyclable. In fact, aluminum can be recycled without losing its properties, making it an excellent choice for companies looking to reduce their environmental footprint.
So, why does this matter? When machining aluminum, scrap material is often produced, but instead of being discarded, it can be melted down and reused for future projects. 즐거운 부분을 볼 준비가 되셨나요? This closed-loop system reduces waste and minimizes the need for raw materials, lowering both environmental impact and costs.
In addition to recycling, CNC machining can also reduce energy consumption. What’s the real story? Advanced CNC machines are designed to be energy-efficient, using less power and generating fewer emissions compared to older manufacturing methods.
Table 12: Sustainability in CNC Machining for Aluminum
Sustainability Aspect | 설명 |
---|---|
Recycling | Aluminum is highly recyclable, reducing waste and the need for new raw materials. |
Energy Efficiency | Modern CNC machines are designed to minimize energy usage, contributing to lower carbon emissions. |
Reduced Material Waste | CNC machining’s precision reduces scrap material, contributing to less waste in the production process. |
13. How to Maintain and Care for Aluminum CNC Machining Tools?
So, why does this matter? Proper maintenance of CNC machining tools is essential to ensure the longevity of your equipment and the quality of your aluminum parts. 즐거운 부분을 볼 준비가 되셨나요? Regular cleaning, proper lubrication, and periodic inspections can go a long way in preventing downtime and ensuring optimal machine performance.
What’s the real story? One of the key aspects of maintaining CNC machines is ensuring the cutting tools are sharp and free from any debris that can affect their performance. Here’s the kicker—using the right lubricants can also help reduce friction and prevent overheating, which can lead to tool wear and tear.
But here’s the kicker—operators should be trained to identify signs of wear and take appropriate action to replace or sharpen tools before they start affecting the quality of the parts being produced.
Table 13: CNC Machining Tool Maintenance Tips
Maintenance Tip | 설명 |
---|---|
Regular Cleaning | Prevents debris buildup, ensuring smooth operation and better precision during machining. |
Proper Lubrication | Reduces friction, prevents overheating, and prolongs the life of cutting tools. |
Tool Inspection | Periodic checks for tool wear and tear to ensure high-quality machining and prevent defects in parts. |
14. What Are Some Common Issues in CNC Machining Aluminum Parts?
Here’s the kicker—while CNC machining offers numerous benefits, there are a few common issues that can arise during the process. What’s the real story? One of the biggest challenges is tool wear, which can affect the quality of the final part. As the tools wear down, they can cause imperfections in the machining process, such as rough surfaces or incorrect dimensions.
So, why does this matter? Another common issue is burr formation, which occurs when excess material is left around the edges of the machined part. Burrs can affect the functionality and aesthetics of the part, especially if it needs to fit into another component.
But here’s the kicker—CNC machines can also face issues with alignment. If the machine is not properly calibrated, the part may not be produced to the correct specifications, leading to waste or rework.
Table 14: Common Issues in CNC Machining Aluminum
Issue | 설명 |
---|---|
Tool Wear | Tools lose sharpness over time, leading to rough surfaces and incorrect dimensions. |
Burr Formation | Excess material left around the edges of the part, affecting its functionality and appearance. |
Alignment Issues | Misalignment can cause inaccuracies in machining, leading to defective parts. |
15. How to Ensure Quality Control in CNC Machining Aluminum?
But here’s the kicker—quality control is crucial when it comes to CNC machining aluminum parts. What’s the real story? A robust quality control process ensures that parts meet the required specifications and perform as intended.
CNC machining centers are equipped with quality inspection tools, such as coordinate measuring machines (CMM), that help check the dimensions and features of the machined parts. 즐거운 부분을 볼 준비가 되셨나요? In addition to these automated inspections, manual inspections are often performed to verify tolerances and ensure the part meets the design requirements.
So, why does this matter? With the right quality control measures in place, manufacturers can prevent defective parts from reaching customers and ensure that only the highest quality components are delivered. What’s the real story? Quality control is essential for maintaining customer satisfaction and preventing costly rework or returns.
Table 15: Quality Control in CNC Machining for Aluminum
Quality Control Measure | 설명 |
---|---|
CMM Inspections | Automated measurements ensure that parts meet precise dimensional specifications. |
Manual Inspections | Manual checks are done to verify that parts meet tolerances and functionality requirements. |
Defect Prevention | Quality control procedures help detect issues early, preventing defective parts from being delivered to clients. |
결론
To sum it up, top CNC machining aluminum services for precision parts offer exceptional value for industries that require custom parts made from a lightweight, durable, and versatile material. From its excellent strength-to-weight ratio to its corrosion resistance, aluminum is an ideal material for CNC machining. By choosing the right CNC machining service, businesses can ensure they receive high-quality, precise components for their operations. Whether you’re looking for milling, turning, or drilling services, CNC machining guarantees accuracy, repeatability, and efficiency.
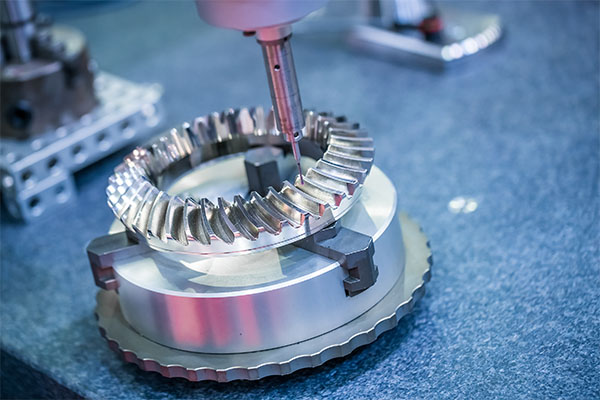
자주 묻는 질문 섹션
질문 1: What is CNC machining?
CNC machining is a process that uses computer-controlled machines to precisely cut and shape materials into specific parts or components based on a digital design.
질문 2: How does CNC machining work?
CNC machining works by translating a digital design into a set of instructions for a machine to follow, allowing it to cut, mill, or turn materials into custom parts with high precision.
질문 3: What types of aluminum are commonly used in CNC machining?
Common aluminum grades include 6061, 7075, and 2024. These grades offer a combination of strength, corrosion resistance, and machinability, making them ideal for various industries.
질문 4: How accurate is CNC machining for aluminum?
CNC machining for aluminum can achieve high precision, with tolerances as tight as ±0.0005 inches, depending on the machinery and tools used.
질문 5: Can CNC machining be used for both small and large aluminum parts?
Yes, CNC machining can accommodate both small, intricate parts and larger components, offering flexibility for a wide range of applications.